环氧陶材质是什么(固态电池,必经之路这是解析最全面的一篇文章)
Posted
篇首语:最关情,折尽梅花,难寄相思。本文由小常识网(cha138.com)小编为大家整理,主要介绍了环氧陶材质是什么(固态电池,必经之路这是解析最全面的一篇文章)相关的知识,希望对你有一定的参考价值。
环氧陶材质是什么(固态电池,必经之路这是解析最全面的一篇文章)
作为下一代电池技术的代表,固态电池引发市场高度关注。本期我们详细阐述固态电池的原理、发展历程以及产业现状。
一、固态电池—后锂电时代必经之路
固态电池具有发展的必然性。固态电池采用不可燃的固态电解质替换了可燃性的有机液态电解质,大幅提升了电池系统的安全性,同时能够更好适配高能量正负极并减轻系统重量,实现能量密度同步提升。在各类新型电池体系中, 固态电池是距离产业化最近的下一代技术,这已成为产业与科学界的共识。
固态电池产业化阶段尚处早期,但有望在未来超速发展。我们对固态电池各体系的开发进度进行了详细的梳理并比较了不同的技术路径现状。当前已实现小部分商业化的固态电池产品对比传统锂电暂未形成足够的竞争优势,而未来固态电池将走阶段发展的路线,从特殊领域逐渐往动力电池过渡, 并且随着国际巨头的加速布局,固态电池将进入发展的快速轨道。
传统液态锂电不会是动力电池的技术终点
1 传统动力电池体系难以满足10年后的能量密度需求
众所周知,动力电池直接对应新能车产品的性价比,而能量密度是动力电池的关键指标。我国电动车市场正经历由“政策驱动”向“政策助跑”的转换,政策对于锂电产业能量密度提升的导向已经明确,补贴直接与能量密度挂钩并不断提高门槛。工信部颁布的《中国制造2025》指明:“到2025年、 2030年,我国动力电池单体能量密度分别需达到400Wh/kg、500Wh/kg。” 指标分别对应当前乘用车动力电池单体平均水平170Wh/kg的2-3倍。
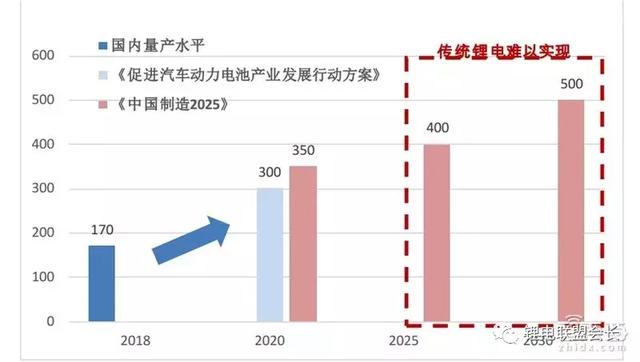
当前动力电池单体能量密度与各项政策指标有较大差距
为了理清400-500Wh/kg 对于动力电池能量密度的概念,我们对锂离子电池技术的迭代路径进行了梳理,我国正位于第二代向第三代锂电发展的过程中。正极材料的选择上,我国已由磷酸铁锂转向三元,并逐渐向高镍三元发展。负极材料当前产业化仍集中于石墨材料,未来也在向硅碳负极进行过渡。据推算,当前采用的高电压层状过渡金属氧化物和石墨作为正负极活性材料所组成的液态锂离子动力电池的重量能量密度极限约为280Wh/kg左右。引入硅基合金替代纯石墨作为负极材料后,锂离子动力电池的能量密度有望做到 300Wh/kg以上,其上限约为 400Wh/kg。
2 安全问题关乎行业健康发展,难以彻底根除
可燃的液态有机电解液是电池自燃的幕后元凶。新能源汽车销量逐年增长却伴随着安全事故的增加,其中,电池自燃占比事故原因的31%。自燃的原因是由于锂电池发生内部或者外部短路后,短时间内电池释放出大量热量,温度极剧升高,导致热失控。而易燃性的液态电解液在高温下会被点燃,最终导致电池起火或者爆炸。
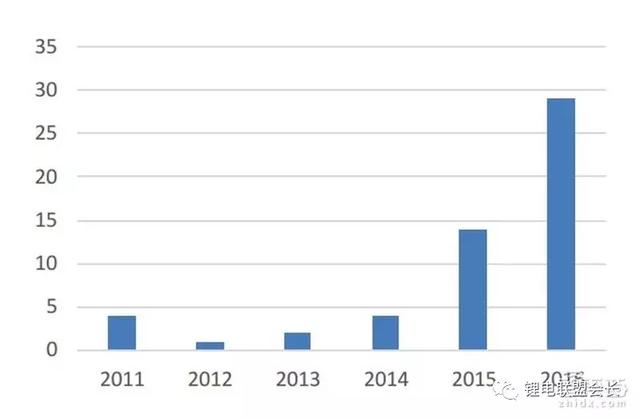
国内新能源汽车安全事故年发生次数(例)

国内新能源汽车起火事故原因分布
起火事件的频发挫伤公众对于新能源车信心,政策相继出台加强行业监管,企业方面,近年来也从不同方向对安全问题进行优化。
主要手段包括: (1)采用功能性电解液,于电解液中添加阻燃剂; (2)优化 BMS 热管理系统,减少过冲过放等易引发热失控的场景发生; (3)采用陶瓷涂覆与耐高温的电池隔膜等等。 但这些手段在技术层面并没能取代可燃性有机电解质的使用,电池系统的安全隐患没有得到彻底根除。零自燃风险,将是未来电动车实现燃油车全面替代需要迈出的关键一步。
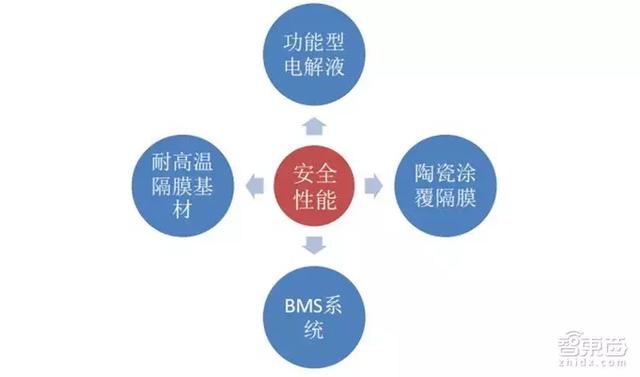
现有动力电池安全问题解决路径
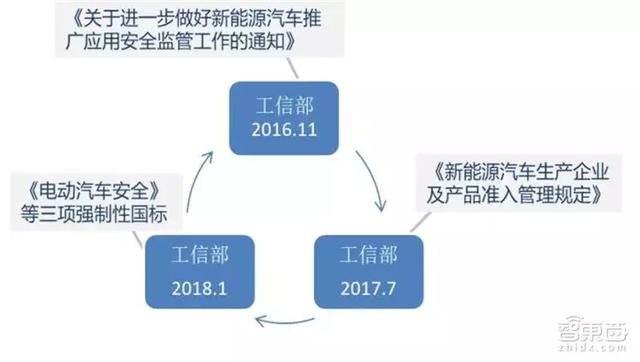
新能源汽车安全监管相关政策
面对能量与安全两座大山,下一代锂电的风口在哪?回望电动车电池技术发展史,从早期的铅酸电池,到丰田等日本企主打的镍氢电池,再到08年特斯拉roaster使用的锂离子电池,传统液态锂离子电池已统治动力电池市场十年。未来,能量与安全需求与传统锂电技术的矛盾将越来越凸显,在下一代锂电技术中,固态电池获得了最高的关注度,已引发全球范围的企业进行提前卡位。
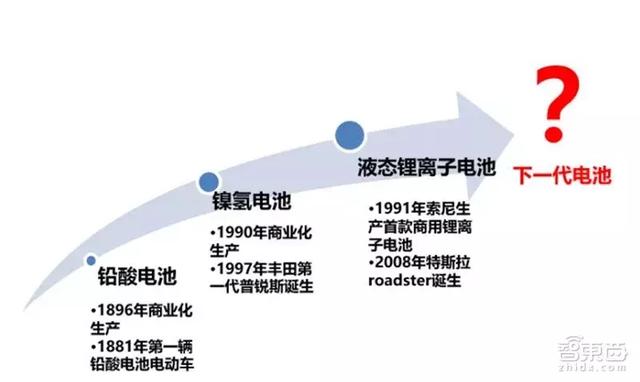
动力电池发展历史沿革
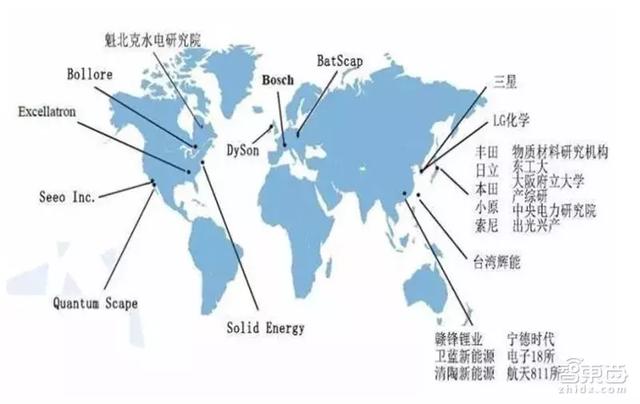
全球多家企业与科研机构已投入固态电池研究
二、为什么一定是固态电池
1 不燃烧,根除安全隐患
固态电池是采用固态电解质的锂离子电池。工作原理上,固态锂电池和传统的锂电池并无区别:传统的液态锂电池被称为“摇椅式电池”,摇椅的两端为电池的正负两极,中间为液态电解质,锂离子在电解液中迁移来完成正负极间的穿梭实现充放电,而固态电池的电解质为固态,相当于锂离子迁移的场所转到了固态的电解质中。固态电解质是固态电池的核心。
固态电解质不可燃烧,极大提高电池安全性。与传统锂电池相比,全固态电池最突出的优点是安全性。固态电池具有不可燃、耐高温、无腐蚀、不挥发的特性,避免了传统锂离子电池中的电解液泄露、电极短路等现象,降低了电池组对于温度的敏感性,根除安全隐患。同时,固态电解质的绝缘性使得其良好地将电池正极与负极阻隔,避免正负极接触产生短路的同时能充当隔膜的功能。
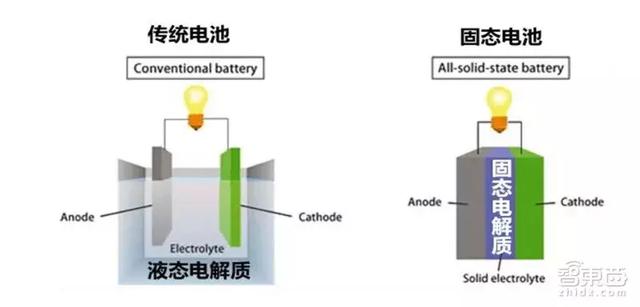
固态电解质是固态电池的核心
2 兼容高容量正负极+轻量化电池系统,推动能量密度大飞跃
更宽的电化学窗口,更易搭载高电压正极材料:提高正极材料容量需要充电至高电压以便脱出更多的锂,目前针对钴酸锂的电解质溶液可以充电到4.45V,三元材料可以充电到4.35V,继续充到更高电压, 液态电解液会被氧化,正极表面也会发生不可逆相变,三元811电池的推广目前便受到了耐高压电解液的制约。而固态电解质的电化学窗口更宽,可达到5V,更加适应于高电压型电极材料。随着正极材料的持续升级,固态电解质能够做出较好的适配, 有利于提升电池系统的能量密度
兼容金属锂负极,提升能量密度上限:高容量与高电压的特性,让金属锂成为继石墨与硅负极之后的“最终负极”。为了实现更高的能量密度目标,以金属锂为负极的电池体系已成为必然选择。因为:
(1)锂金属的克容量为3860mAh/g,约为石墨(372mAh/g)的10倍,(2) 金属锂是自然界电化学势最低的材料,为-3.04V。同时其本身就是锂源,正极材料选择面更宽,可以是含锂或不含锂的嵌入化合物,也可以是硫或硫化物甚至空气,分别对应能量密度更高的锂硫和锂空电池,理论能量密度接近当前电池的10倍。
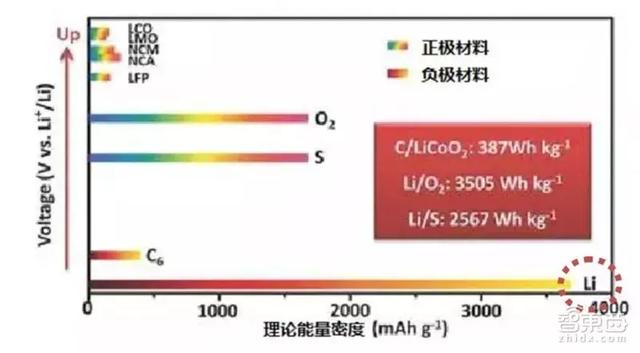
锂金属是负极材料的最终形态
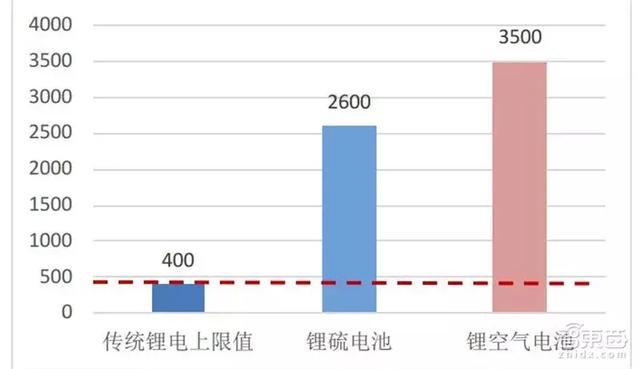
锂金属负极体系能量密度远超传统锂电
锂金属负极在当前传统液态电池体系难以实现。锂金属电池的研究最早可追溯到上世纪60年代,并在20世纪70年代已成功开发应用于一次电池。而在可充放电池领域,金属锂负极在液态电池中存在一系列技术问题至今仍缺乏有效的解决方法,比如金属锂与液态电解质界面副反应多、 SEI膜分布不均匀且不稳定导致循环寿命差,金属锂的不均匀沉积和溶解导致锂枝晶和孔洞的不均匀形成。
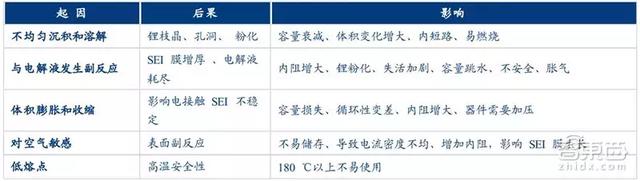
锂金属负极在液态电池中存在的应用难题
固态电解质在解决锂金属负极应用问题上被科学界寄予厚望。研究者把解决金属锂负极的应用问题寄希望于固态电解质的使用,主要思路是避免液体电解质中持续发生的副反应,同时利用固体电解质的力学与电学特性抑制锂枝晶的形成。此外,由于固态电解质将正极与负极材料隔离开,不会产生锂枝晶刺破隔膜的短路效应。总而言之, 固态电解质对于锂金属负极拥有更好的兼容性,锂金属材料将在固态电池平台上率先应用。
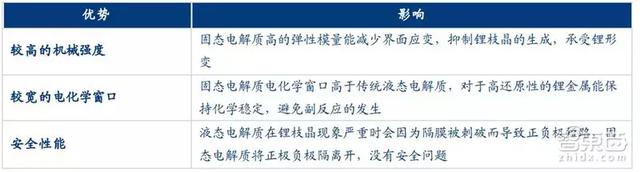
固态电解质在锂金属负极应用上的优势
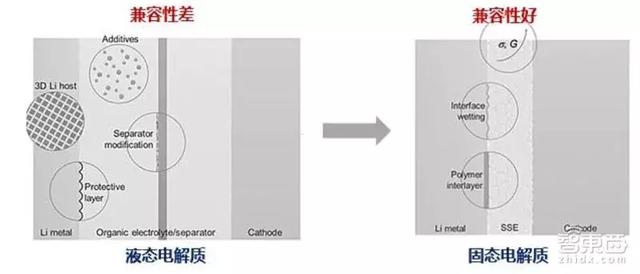
固态电解质对锂金属负极兼容性更好
减轻系统重量,能量密度进一步提升。固态电池系统重量减少进一步提升能量密度。动力电池系统需要先生产单体,单体封装完成后将单体之间进行串联组装。若先在单体内部进行串联,则会导致正负极短路与自放电。固态电池电芯内部不含液体,可实现先串并联后组装,减少了组装壳体用料, PACK设计大幅简化。此外,由于彻底的安全特性, BMS等温控组件将得以省去,并可通过无隔膜设计进一步为电池系统“减负”。
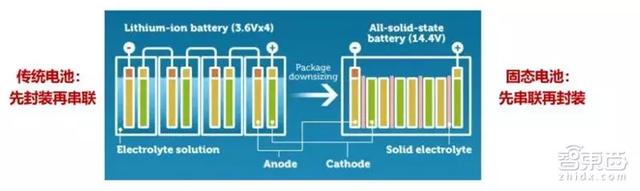
固态电池封装更加灵活
3 固态电池是最有希望率先产业化的下一代电池技术
固态电池体系革命更小。锂硫电池、锂空气等体系需更换整个电池结构框架,难题更多也更大,而固态电池主要在于电解液的革新,正极与负极可继续沿用当前体系,实现难度相对小。锂金属负极兼容,通过固态电解质实现。锂硫、锂空气均需采用锂金属负极,而锂金属负极更易在固态电解质平台实现。固态电池作为距离我们最近的下一代电池技术已成为科学界与产业界的共识,是后锂电时代的必经之路。
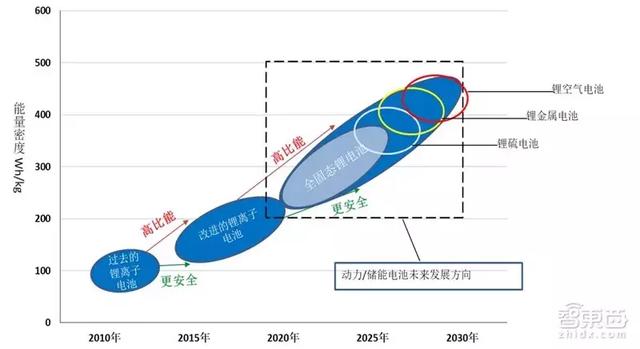
固态电池是动力电池必经之路
三、固态电池距离我们还有多远
1 高阻抗、低倍率的核心难题
当前固态电解质体相离子电导率远低于液态电解质的水平,往往相差多个数量级。 按照材料的选择,固态电解质可以分为聚合物、氧化物、硫化物三种体系,而无论哪一种类别,均无法回避离子传导的问题。电解质的功能在于电池充放电过程中为锂离子在正负极之间搭建锂离子传输通道来实现电池内部电流的导通,决定锂离子运输顺畅情况的指标被称为离子电导率,低的离子电导率意味着电解质差的导锂能力,使锂离子不能顺利在电池正负极之间运动。聚合物体系的室温电导率约10-7-10-5S/cm,氧化物体系室温下电导率为10-6-10-3S/cm,硫化物体系电导率最高,室温约10-3-10-2S/cm,而传统液态电解质的室温离子电导率为10-2S/cm 左右, 比任意固态电解质类型的离子电导率都要高。
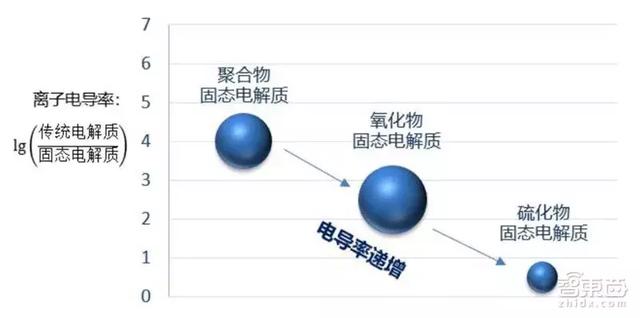
三大体系固态电解质离子电导率高低顺序
此外, 固态电解质拥有高界面阻抗。 在电极与电解质界面上,传统液态电解质与正、负极的接触方式为液/固接触,界面润湿性良好,界面之间不会产生大的阻抗,相比较之下,固态电解质与正负极之间以固/固界面的方式接触,接触面积小,与极片的接触紧密性较差,界面阻抗较高,锂离子在界面之间的传输受阻。
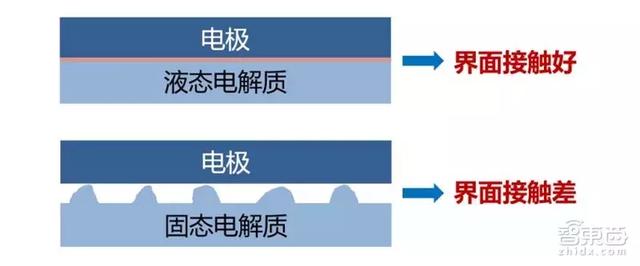
固态电解质界面阻抗高于传统液态电解质
低离子电导率与高界面阻抗导致了固态电池的高内阻, 锂离子在电池内部传输效率低,在高倍率大电流下的运动能力更差,直接影响电池的能量密度与功率密度。
2 三大技术路线产业化进展
固态电池的三大体系各有优势,其中聚合物电解质属于有机电解质,氧化物与硫化物属于无机陶瓷电解质。纵览全球固态电池企业,有初创公司,也不乏国际厂商,企业之间独踞山头信仰不同的电解质体系,未出现技术流动或融合的态势。欧美企业偏好氧化物与聚合物体系,而日韩企业则更多致力于解决硫化物体系的产业化难题,其中以丰田、三星等巨头为代表。
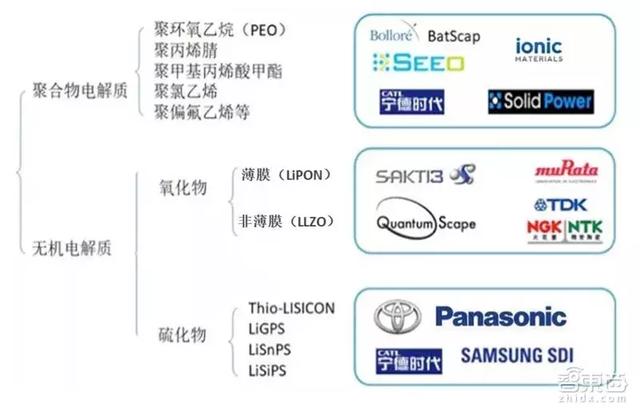
全球固态电池企业在技术路线
聚合物体系:率先小规模量产,技术最成熟,性能上限低。聚合物体系属于有机固态电解质,主要由聚合物基体与锂盐构成,量产的聚合物固态电池材料体系主要为聚环氧乙烷(PEO) -LiTFSI(LiFSI),该类电解质的优点是高温离子电导率高,易于加工,电极界面阻抗可控。因此成为最先实现产业化的技术方向。但其室温离子电导率为三大体系中最低,严重制约了该类型电解质的发展。电导率过低+低容量正极意味着该材料的较低的能量与功率密度上限。 在室温下,过低的离子电导率(10-5S/cm 或更低)使离子难以在内部迁移,在 50~80℃的环境下利用才勉强接近可以实用化的10-3S/cm。此外, PEO 材料的氧化电压为3.8V,难以适配除磷酸铁锂以外的高能量密度正极,因此,聚合物基锂金属电池很难超过300Wh/kg 的能量密度。
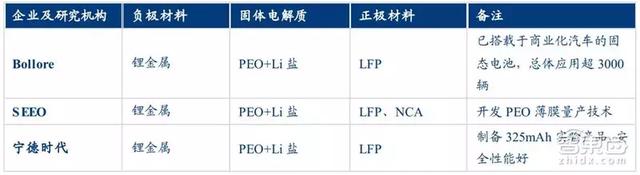
聚合物体系研发机构
法国博洛雷公司率先将此类固态电池商业化。 2011年12月其生产的以30kwh固态聚合物电池+双电层电容器为动力系统的电动车驶入共享汽车市场,这也是世界上首次用于EV的商业化固态电池。据资料显示,该公司共投入约2900辆EV,设立了约900座服务站和约4500台充电器,服务用户合计达到18万人以上,其中近4成的约7万人为活跃用户,每天的利用次数约为1.8万次。该产品为后来者提供了参考与指导,但并不具备商业价值。 博洛雷公司的聚合物固态电池采用了 Li-PEO-LFP的材料体系,能量密度为110Wh/kg,对比传统电池系统没有密度优势。由于聚合物电解质在室温下难以工作,博洛雷为此电池系统搭配了200W的加热器,发动前需通过加热元件将电池系统升至60-80℃。而在面对长时间停车时,加热器也需要一直处于工作状态,停车时需要连接充电器。加热器的存在,增加能耗,对电池包壳体设计增加了诸多限制,安全性也有待考究。此外,由于聚合物体系功率密度低,应对紧急起步、紧急加速等场景需配载双电层电容器弥补输出。
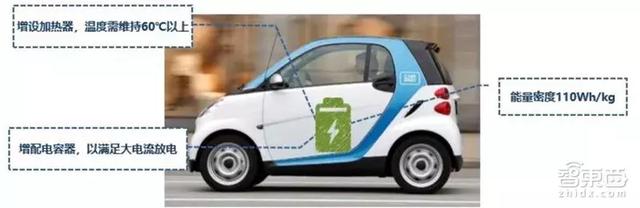
博洛雷生产的固态电池汽车的局限
聚合物体系可卷对卷生产, 量产能力最好。 由于聚合物薄膜拥有弹性和粘性,博洛雷与SEEO公司的电解质均可由卷对卷的方式量产。卷对卷印刷技术在薄膜太阳能电池、印刷等领域已有较广泛应用,其技术相对成熟,成本低廉。因此, 聚合物体系是当前量产能力最强固态电池。与无机固态电解质复合是潜在的发展方向。 将聚合物体系与其他无机固态电解质体系复合能改善聚合物体系的电导率,并能较好结合两者优势,实现“刚柔并济。
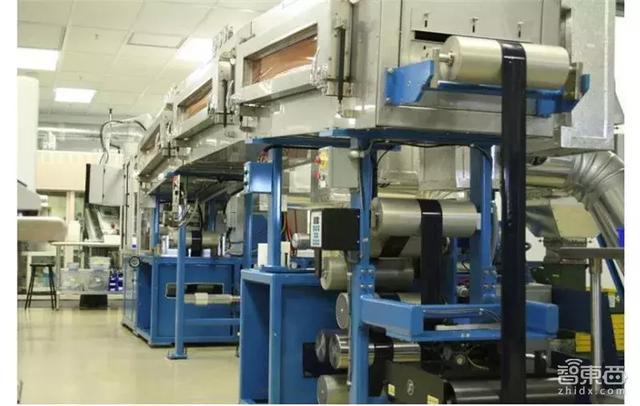
公司的卷对卷固态电池产线
氧化物体系: 分为薄膜型与非薄膜型,薄膜型适用于微型电子, 非薄膜型综合性能优异。对比有机固态电解质,无机固态电解质包括氧化物体系与硫化物体系,无机材料的锂离子电导率在室温下要更高,但电极之间的界面电阻往往高于聚合物体系。 其中氧化物体系开发进展更快,已有产品投入市场。氧化物体系主要分为薄膜型与非薄膜型两大类。 薄膜型主要采用 LiPON 这种非晶态氧化物作为电解质材料,电池往往薄膜化;而非薄膜型则指除 LiPON 以外的晶态氧化物电解质,包括LLZO、LATP、LLTO等,其中LLZO是当前的热门材料,综合性能优异。
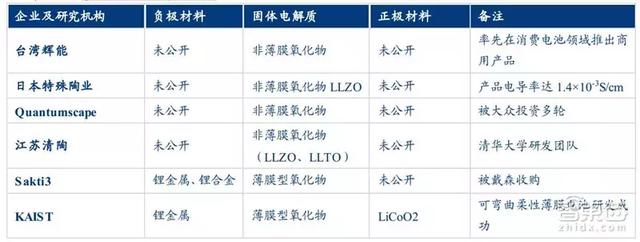
氧化物体系研发机构
薄膜型产品性能较好,但扩容困难。 锂离子的流动与电流一样,遵循某种“欧姆定律”,如果传导距离缩短,则可以减小电阻值, 通过使电解质层变薄可以在一定程度上弥补低离子传导率。除了LiPON等少数几种固体电解质,大多数材料难以制备成薄膜。已经小批量生产的以无定形 LiPON 为电解质的氧化物薄膜电池,在电解质层较薄时( ≤2μm),面电阻可以控制在50~100Ωcm2。同时薄膜化的电池片电池倍率性能及循环性能优异,可以在50C下工作, 循环45000次后,容量保持率达95%以上。 但是薄膜化带来较好性能的同时也面对着扩充电池容量的困境。单体薄膜电池的容量很小,往往不到mAh级别,在微型电子、 消费电子领域勉强够用, 可对于Ah级别的电动车领域则需要串并联大量的薄膜电池来增加电池组容量,工艺困难且造价不菲。从涂布到真空镀膜, 薄膜型产品多采用真空镀膜法生产。 由于涂布法无法控制粒子的粒径与膜厚,成膜的均匀性比较低,真空镀膜法能够较好保持电解质的均匀性。但是真空镀膜的生产效率低下,成本高昂,不利于大规模生产。为了改善材料与电极的界面阻抗,目前为止的应对措施是通过在1000℃以上的高温下烧结电极材料来增加界面的接触面积,对工艺要求较苛刻。薄膜型氧化物固态电池厂家Sakti3于2015年被英国家电巨头戴森收购, 可受制于薄膜制备的成本与规模化生产难度大,迟迟没有量产产品。
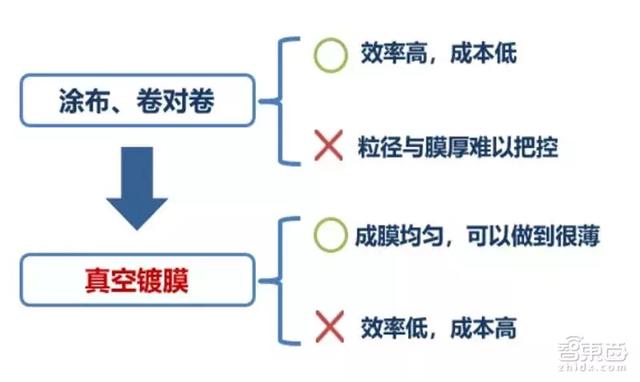
真空镀膜法的特点
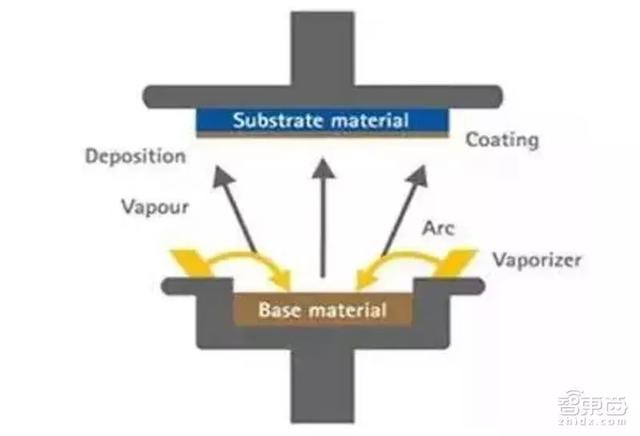
真空镀膜法示意图
非薄膜型氧化物产品综合性能出色,是当前开发热门。 非薄膜型产品的电导率略低于薄膜型产品,但仍然远高出聚合物体系,且其可生产成容量型电池而非薄膜形态, 从而大大减少了生产成本。非薄膜型氧化物固态电池的各项指标都比较平衡,不存在较大的生产难题,已成为中国企业重点开发的方向,台湾辉能与江苏清陶都是此赛道的知名玩家。非薄膜型产品已尝试打开消费电子市场。 台湾辉能科技公司量产的非薄膜型固态电池是在消费电子市场“吃螃蟹”的先行者。公司产品采用软性电路板为基材,厚度可以达到2mm,且电池可以随意折叠弯曲。2014年公司与手机厂商HTC合作生产了一款能给手机充电的手机保护皮套,采用了五片氧化物固态电池共提供了1150mAh容量的电源,通过接口直接为手机充电。同时,产品在可穿戴设备等领域也有应用。
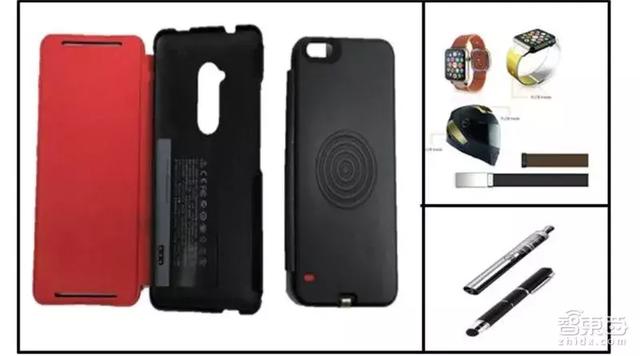
辉能科技的微型电子类氧化物固态电池产品
硫化物体系:开发潜力最大,难度也最大。硫化物电解质是电导率最高的一类固体电解质, 室温下材料电导率可达10-4-10-3S/cm, 且电化学窗口达5V以上,在锂离子电池中应用前景较好, 是学术界及产业界关注的重点。 因为其拥有能与液态电解质相媲美的离子电导率,是在电动汽车方向最有希望率先实现渗透的种子选手,同时也最有可能率先实现快充快放。受日韩企业热捧。 硫化物固态电池的开发主要以丰田、三星、本田以及宁德时代为代表,其中以丰田技术最为领先,其发布了安时级的Demo电池以及电化学性能,同时,还以室温电导率较高的LGPS作为电解质,制备出较大的电池组。
对环境敏感,存在安全问题。 硫化物固态电解质拥有最大的潜力,但开发进度也处于最早期。其生产环境限制与安全问题是最大的阻碍。 硫化物基固态电解质对空气敏感,容易氧化,遇水易产生 H2S 等有害气体,这意味着生产环境的控制将十分苛刻,需要隔绝水分与氧气,而有毒气体的产生也与固态电池的初衷相悖。 对此企业的解决方案主要为:
(1)开发不容易产生硫化氢气体的材料,(2)在全固态电池中添加吸附硫化氢气体的材料, (3)为电池设计抗冲撞构造。
但这些做法会导致电池体积增大以及加大成本。 除此以外, 硫化物固态电池在充放电过程中由于体积变化,电极与电解质界面接触恶化,导致较大的界面电阻,较大的体积变化会恶化其与电解质之间的界面。 因此,硫化物体系是当前开发难度最大的固态电解质。生产工艺上,涂布+多次热压、添加缓冲层改善界面性能。 硫化物固态电池多已实现涂布法进行样品生产,同时,生产环境需要严格控制水分。为了解决界面问题,企业往往采取热压的方式增强电解质与电极材料的接触。此外,通过在电极与电解质之间渡上一层缓冲层,改善界面性能。宁德时代在硫化物体系也进行了前瞻布局,并初步设计了其工艺路线,其工艺路线为:正极材料与硫化物电解质材料的均匀混合与涂覆,经过一轮预热压,形成连续的离子导电通道。经过二次涂覆硫化物之后,再进行热压,固态化之后可以去掉孔隙,再涂覆缓冲层后与金属锂复合叠加。
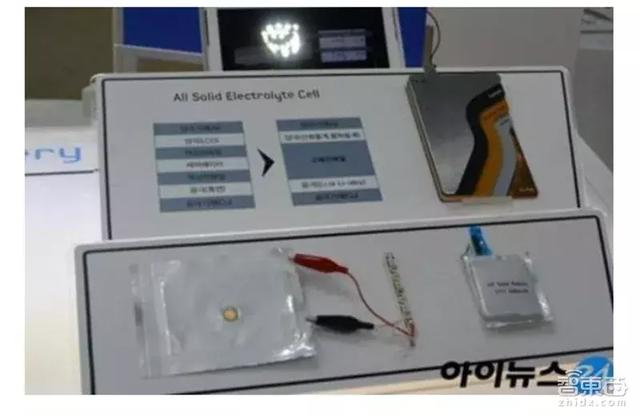
三星硫化物电池
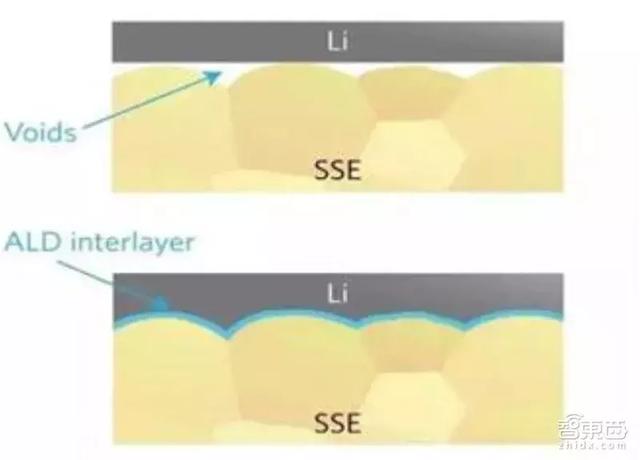
添加缓冲层改善界面性能
综合看来,聚合物体系工艺最成熟,率先诞生EV级别产品, 其概念性与前瞻性引发后来者加速投资研发,但性能上限制约发展,与无机固态电解质复合将是未来可能的解决路径;氧化物体系中, 薄膜类型开发重点在于容量的扩充与规模化生产,而非薄膜类型的综合性能较好,是当前研发的重点方向;硫化物体系是最具希望应用于电动车领域的固态电池体系,但处于发展空间巨大与技术水平不成熟的两极化局面,解决安全问题与界面问题是未来的重点。
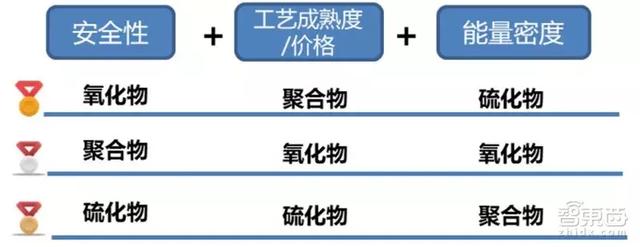
各体系性能指标对比
3 产业化尚处早期,但前景已有保障
市场化产品能量密度较低。 现阶段固态电池量产产品很少,产业化进程仍处于早期。 唯一实现动力电池领域量产的博洛雷公司产品能量密度仅为100Wh/kg, 对比传统锂电尚未具备竞争优势。高性能的实验室产品将为产业化奠基。 从海外各家企业实验与中试产品来看,固态电池能量密度优势已开始凸显,明显超过现有锂电水平。 在我国, 固态锂电的基础研究起步较早, 在“六五”和“七五”期间,中科院就将固态锂电和快离子导体列为重点课题,此外,北京大学、中国电子科技集团天津18所等院所也立项进行了固态锂电电解质的研究,并在此领域取得了不错的进展。 未来,随着产业投入逐渐加大,产品性能提升的步伐也望加速。
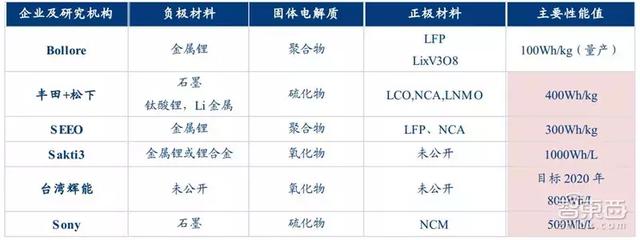
全球主要固态电池企业产品
4 固态电池对锂电产业链的影响
除了电解质,固态电池在其他电池部件上的选择与传统锂电也有一定差异。电极材料采用与固态电解质混合的复合电极。 结构上, 固态电池正负极与传统电极的最大区别在于: 为了增加极片与电解质的接触面积, 固态电池的正负极一般会与固态电解质混合。例如在正负极颗粒间热压或填充固态电解质,或者在电极侧引入液体,形成固-液复合体系,这都与传统锂电单独混合极片浆料并在铝/铜箔上涂布不同。 而在材料选择上,由于固态电解质普遍更高的电化学窗口,高镍高压正极材料更容易搭载,未来也将持续沿用新的正极材料体系,负极材料上,多采用硅、金属锂等高容量负极,充分发挥固态电池的优势。电极与电解质之间存在缓冲层。 缓冲层的加入能起到改善电极与电解质界面性能的作用。其成分可以为凝胶化合物、Al2O3等。
隔膜仍然存在,电池实现全固态后消失。 现阶段的大部分固态电池企业的产品仍需添加少量液态电解液以缓解电极界面问题、增加电导率,因此隔膜仍然存在与电池中以用来阻隔正负极,避免电池短路。这种折中的解决方法同时拥有固态电池的性能优势,在技术难度上也更加易于实现。 而随着技术推进, 未来电解液用量会越来越少,当过渡到完全不含液体或液体含量足够小时, 电池将取消隔膜设计,体系已能满足安全需求。多采用软包的封装技术。 除去液态电解液后,固态电池的封装与 PACK上比传统锂电更灵活、更轻便,因此将采用软包封装。
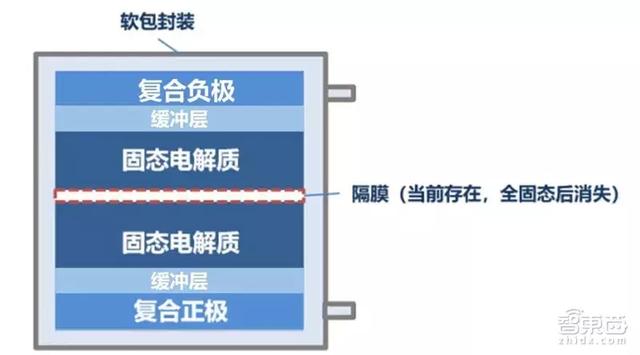
固态电池内部结构透视图
四、未来发展之路: 步步为营,梯次渗透
展望未来发展趋势,技术上步步为营,应用上梯次渗透,固态电池阶段发展之路已经明晰。结构上, 现阶段电池体系包含部分液态电解质以取长补短。 而技术发展过程中将逐渐减少液体的使用,从半固态电池到准固态电池,最终迈向无液体的全固态电池。应用领域上,有望率先发挥安全与柔性优势,应用于对成本敏感度较小的微电池领域,如RFID、植入式医疗设备、无线传感器等;技术进步后,再逐渐向高端消费电池渗透;随着产品的成熟,最终大规模踏入电动车与储能市场,从高端品牌往下渗透, 实现下游需求的全面爆发。
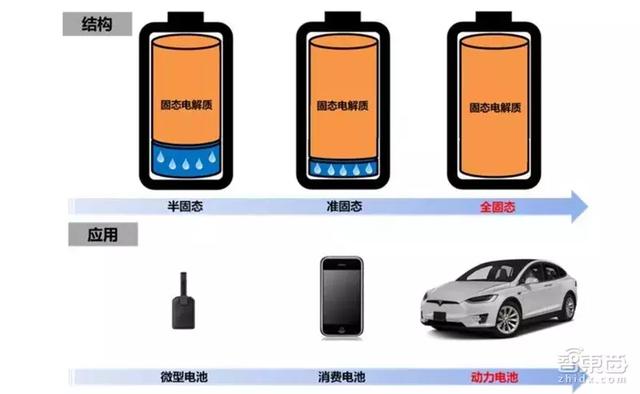
梯次渗透实现固态电池全方位应用
智东西认为,电池已经成为包括新能源汽车在内许多现代电子产品的一大短板。锂电产业链是一个至少还有10年良好前景的行业,而新技术的开发与崛起也将不断强化行业的估值与前景。 在行业看好与多方布局之下,固态电池产业有望获得超速发展。固态电池承载着电池安全与能量全面提升的光荣使命,未来有望成为行业的新爆发点与关键性技术保障。
来源/智东西内参
相关参考
松下电池怎么样(历时一个月,迄今为止我最全面的纽扣电池综合测试)
...好,我是梦想是个猪,今天为大家带来一篇市售主流纽扣电池的横向综合评测。前言之所以会做这个测试,是因为前段时间车友群里有人在问:你们的车钥匙离车多远的时候会被感应到?这种感应解锁的方式是不是比通过遥控器...
...不止一两处,本篇文章,老高从导热灌封胶的角度,整理环氧树脂胶、硅橡胶、聚氨酯三种主要基材对应的导热胶性质和工艺方法。灌封胶是一个广泛的称呼,原来主要用于电子元器件的粘接,密封,灌封和涂覆保护,目前灌封胶尤...
...不止一两处,本篇文章,老高从导热灌封胶的角度,整理环氧树脂胶、硅橡胶、聚氨酯三种主要基材对应的导热胶性质和工艺方法。灌封胶是一个广泛的称呼,原来主要用于电子元器件的粘接,密封,灌封和涂覆保护,目前灌封胶尤...
...不止一两处,本篇文章,老高从导热灌封胶的角度,整理环氧树脂胶、硅橡胶、聚氨酯三种主要基材对应的导热胶性质和工艺方法。灌封胶是一个广泛的称呼,原来主要用于电子元器件的粘接,密封,灌封和涂覆保护,目前灌封胶尤...
...不止一两处,本篇文章,老高从导热灌封胶的角度,整理环氧树脂胶、硅橡胶、聚氨酯三种主要基材对应的导热胶性质和工艺方法。灌封胶是一个广泛的称呼,原来主要用于电子元器件的粘接,密封,灌封和涂覆保护,目前灌封胶尤...
比亚迪固态电池技术(2023年新能源固态电池领跑者,第一个吃螃蟹)
#2月财经新势力#去年,比亚迪固态电池装车量产消息传出,震惊全球!全球媒体争相报道,因为这是电池的技术革命。固态电池领跑者:清陶(昆山)能源发展股份有限公司1.技术来源:中科院,清华大学,工程研究院技术来自...
海参清洗刷(海参泡发方法最全面的图文教程,做法和要点详解,新手一次就成功)
大家好,我是秀厨娘,一个喜欢待在厨房里研究美食的姑娘,每天与大家分享一道营养美味的家常菜做法,如果您也喜欢做美食,欢迎关注,我们可以互相分享自己在做美食时积累的经验,互相学习,为家人和朋友做出更营养健...
海参清洗刷(海参泡发方法最全面的图文教程,做法和要点详解,新手一次就成功)
大家好,我是秀厨娘,一个喜欢待在厨房里研究美食的姑娘,每天与大家分享一道营养美味的家常菜做法,如果您也喜欢做美食,欢迎关注,我们可以互相分享自己在做美食时积累的经验,互相学习,为家人和朋友做出更营养健...
在工业产品向多样化、高档化发展的过程中,如何提高直接影响产品质量的模具质量是一项重要的任务。在模具制造过程中,形状加工后的平滑加工与镜面加工称为零件表面研磨与抛光加工,它是提高模具质量的重要工序。掌握...