热管煤气加热器(《热管技术大全》—热管技术在合成氨工业中的应用)
Posted
篇首语:我自横刀向天笑,去留肝胆两昆仑。本文由小常识网(cha138.com)小编为大家整理,主要介绍了热管煤气加热器(《热管技术大全》—热管技术在合成氨工业中的应用)相关的知识,希望对你有一定的参考价值。
热管煤气加热器(《热管技术大全》—热管技术在合成氨工业中的应用)
合成氨工业是一项基础化学工业,在化学工业中占有很重要的地位。
合成氨生产从造气开始直到氨的合成都伴随着热的过程。合理地利用和控制合成氨生产过程中放出的热量,不仅可以节约生产中的能源消耗,降低生产成本,而且可以提高 CO 变换率及氨的合成率,前者属于余热利用,而后者属于化学反应的热控制,热管技术在这两方面都存在很大的开发潜力。
根据我国工业发展的特殊情况,我国的合成氨工业从生产规模上可分为小合成氨、中合成氨和大合成氨生产。
生产的原料路线有煤、油及天然气。由于原料路线不同,因而生产工艺路线及采用的设备也不尽相同。针对不同工艺路线设备的特点,热管技术在合成氨工业生产中有以下几种应用类型。
① 回收低温余热预热助燃空气,或生产低压蒸汽作为生产原料;
② 回收高温余热产生中压蒸汽作原料蒸汽的补充,或生产高压蒸汽作为生产的动力源;
③ 控制固定床催化反应器的化学反应温度,使其向最佳反应温度曲线无限逼近,从而提高 CO 变换反应器的 CO 变换率及合成氨塔内氨的合成率。
以上三种应用类型,在不同的生产规模及不同的原料工艺路线中应用的方式及设计思路均不同,必须针对不同的实际条件采用不同的结构设计才能收到良好的效果。
1.上、下行煤气余热回收
上、下行煤气是指以煤或煤球为原料的生产路线中煤造气炉所产生的上吹半水煤气及下吹半水煤气。由于生产原料不同,上、下行煤气气体中所含尘粒及温度也不相同。
1.1小合成氨上、下行煤气余热回收
小合成氨生产大都使用煤球为原料造气。其特点是出煤造气炉的上、下行煤气的温度较低,气体成分复杂含有大量粉尘及水蒸气,容易引起低温腐蚀及灰尘堵塞等一系列问题。
在设计此类设备中应重点考虑以下问题
① 由于气体温度低,可利用的传热温差很小,要回收一定热量必须要有很大的传热面积,传热面积过大不仅占地大、金属耗量大,成本也高;
② 上、下行煤气含有大量粉尘和水蒸气,特别是下行煤气含尘量更多。每标准立方米气体的含尘量估算在 30g 以上;
③ 这种成分的气体温度不宜降得过低,否则易达到露点。一旦达到露点不仅产生露点腐蚀,而且灰尘会堵死气体通路使设备不能使用;
④ 对于以碳化煤球为原料的煤气中所含粉尘既细又黏,要使设备能长期稳定可靠运行,除能保证自清灰外,设备结构必须能考虑定期清灰以清除附着于管壁及翅片上的灰尘。
根据以上具体要求,设计出的热管换热设备首先应保证长期可靠运行,不堵塞、体积紧凑、占地面积小,设备气体出口热管的管壁温度应高于气体露点温度(约 120℃),以防气体中的有害成分结露。
根据以上原则,设计并成功运行了多年的适用于煤气造气上、下行煤气余热回收的热管蒸汽发生器如图5-1、图5-2。该设备具有如下特点。
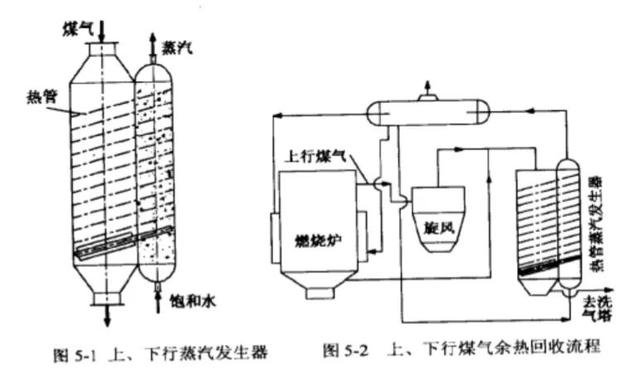
① 气体流动方向为从上到下,减少灰尘附着于管壁的可能性;
② 热管的蒸发段全部采用轴向直翅片。一方面可以扩展传热表面,另一方面可消除热管背部的涡流区,从而不使灰尘在此停聚。同时也减少了流动阻力损耗。
从煤气炉出来的上行煤气先经过旋风除尘器,然后从蒸汽发生器的上部向下流过热管管束,温度从进口的360℃左右降到出口的140℃左右进入下一工段的洗气塔,然后去煤气柜。
下行煤气从煤气炉的底部出来经过旋风除尘器仍然从蒸汽发生器的顶部进入,温度从 300℃以上降至140℃进入洗气塔,然后去煤气柜。
1.2中合成氨上行、下行煤气余热回收
中合成氨与小合成氨生产除在产量规模不同外,主要的区别在于中型合成氨厂的煤造气是以块煤为原料。因此其上行煤气出煤造气的温度远较小化肥高,大约在 600℃左右。中合成氨生产造气工段的流程简图如图 5-3 所示。
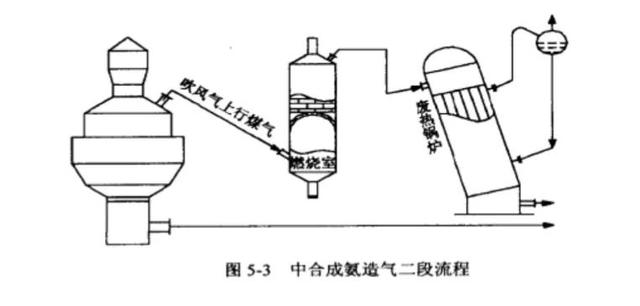
与小合成氨不同之处在于煤造气炉后有一吹风气燃烧室。上行煤气经过燃烧室后再进入列管式废热锅炉。上行煤气与吹风燃烧气合用一个废热锅炉产生低压蒸汽(0.4~0.8MPa)或中压蒸汽(1.9~2.5MPa)供工艺使用。
由于中合成氨煤造气炉的下行煤气温度较低(200℃左右),因而一般不经过废热锅炉而直接去洗气塔。
在上述生产流程中存在着以下几方面的问题。
① 列管式废热锅炉容易损坏
损坏的原因大都由于两方面的原因∶
一是气体流速过高,气体中含有大量煤的灰渣或细煤粒极易将管子磨穿。
二是在产生低压蒸汽时,下管板水进口处的水温过低,造成局部管壁低温过冷,形成露点腐蚀。
二种原因都可能使局部管子破裂漏水,必须停工查漏检修,给生产造成损失。
② 设备利用率不高
在煤造气合成氨生产中,上行煤气制作过程只占一个循环的 24%~27%,吹风气只占一个循环的 25%~28%,亦即在一个循环中只占 49%~55%的时间有气体通过废热锅炉,其余时间无气体通过,设备处于空闲状态。
③ 换热面积设计严重不合理
一般造气工段的废热锅炉均是按瞬间最大吹风气流量设计的,而上行煤气只相当于吹风气量的 30%~50%左右,这样小的气量通过上述按吹风器最大瞬时量设计的废热锅炉,由于传热面积过大,必然形成上行煤气出口温度过低,不仅会产生露点腐蚀,而且易形成灰堵。
④ 低温余热没有充分回收
目前中型合成氨厂都将废热锅炉产生的饱和蒸汽压力提高。其优点是得到高品位的蒸汽,另一方面也提高了传热管壁温度,对防止露点腐蚀有利。
但由于饱和蒸汽压力提高,饱和蒸汽温度也相应提高,为维持一定温差,排出废热锅炉气体的出口温度也相应提高。一般将出口温度设计在 270℃左右。
由于中型合成氨生产的气体流量较大,如果将 270℃气体的温度降到 140℃左右,则吹风燃烧气、上行气、下行气的总回收热量相当于一吨蒸汽的热量(φ2700mm 煤气炉),显然这种低温小温差有腐蚀性气体的余热回收采用热管是最合适的。
根据以上情况,对中型合成氨煤造气工段采用热管技术可以有二种途径。
① 在原有废热锅炉后加一台热管低温余热回收装置,将废热锅炉出口 270℃的气体降至 140℃,同时将下行煤气(约 200℃)也经过热管装置,可以回收下行煤气约 60℃温差的热量。
热管装置可以是气-气式的,即用回收的低温余热加热进入煤气炉的空气或过热低压水蒸汽。也可以是热管省煤器的形式,加热废热锅炉的给水。
② 为充分考虑设备利用率及余热回收率,可使每一台煤造气炉后配一台热管蒸汽发生器专供上、下行煤气余热回收,由于上下行煤气的发生量相差不太大,设计的传热面积比较合理。
而将三台煤气炉的吹风气通过一个燃烧室燃烧后进入一台热管废热锅炉,可使设备的利用率达75%~84%。
2 .吹风气燃烧气余热回收
从煤气炉出来的吹风气中含有少量可燃成分如 CO、H,等,为充分回收其热量,一般均首先通过燃烧室,将可燃成分燃尽, 再进废热锅炉回收其热量。
由于块煤造气和煤球造气的吹风气中所含可燃气成分的含量不同,出煤造气炉的温度也不相同,所以在设计二种吹风气余热回收热管蒸汽发生器时应考虑的注意事项也不完全相同。
2.1 小合成氨吹风气燃烧热的利用
在以往的小合成氨生产中吹风气都是直接排放,不仅浪费了能源,而且对环境造成污染和危害。80 年代末期在小合成氨蒸汽自给技术改造中,大多数小合成氨厂均进行了吹风气燃烧热量回收的技术改造。典型的几种流程如图5-6、图5-7、图5-8所示。
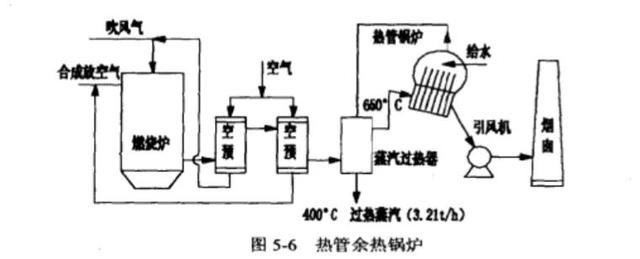
图 5-6 所示流程的热管余热锅炉是一种紧凑式余热锅炉,热管的冷凝段直接插在汽包中。
该流程具有不少优点,如空气预热温度比较高(420℃以上),对燃烧炉稳定燃烧起到良好作用。
过热蒸汽的温度也比较高(400℃),但该设计未能充分发挥热管优势,使高品位热能未能得到充分利用。
本可产生(表压)1.6MPa 以上中压蒸汽,由于采用了低温热管,该流程只能产生 0.4MPa(表)的低压蒸汽。
其次该流程未能发挥热管在低温余热回收中的优势,排烟温度 160℃显得偏高。
热管锅炉的设计未考虑大含尘量气体中灰尘的处理,因之该设备仅适用于以块煤为原料而不适用于以碳化煤球为原料的造气工段。
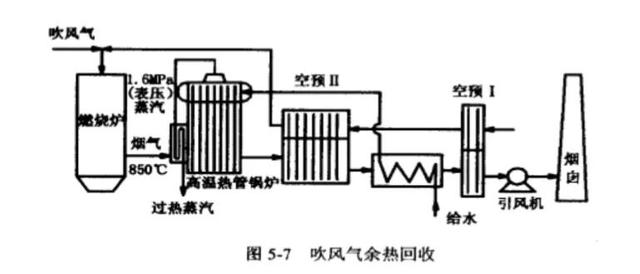
图 5-7 是另一种流程,其特点是吹风气入燃烧炉燃烧后,产生800~900℃的高温烟气,直接进入高温热管余热锅炉。
该锅炉的前一部分采用了以钠、钾为工作介质的不锈钢管材为壳体的高温热管,可以承受 900℃以上的高温。
烟气降温至 400℃左右进入第Ⅱ热管空气预热器,加热来自第 I热管空气预热器的空气,将空气从 140℃左右加热到 320℃左右去燃烧室作为吹风气的助燃空气。
出第 Ⅱ热管空气预热器的烟气约 280℃左右进入热水加热器,将脱氧水加热至 130℃左右,烟气降至 140℃左右再进入第 Ⅰ热管空气预热器,将 25℃左右的常温空气加热至 130℃左右进入第 ⅡI热管空气预热器,最后烟气降温至 120℃左右排入烟囱,这一流程可以产生 1.6~2.5MPa 的中压蒸汽,直接供变换或其他工段使用。
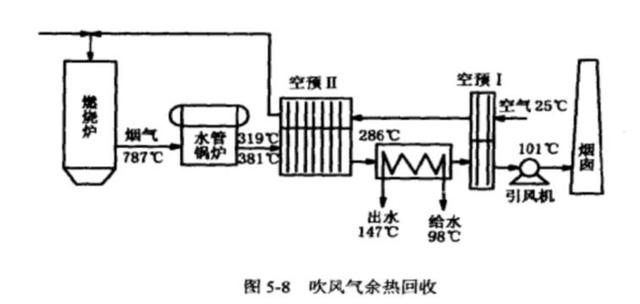
图 5-8 的流程与图 5-7完全一致,只是用普通的水管锅炉代替了热管锅炉,造价比较便宜但占地面积较大。
2.2 中型合成氨吹风气燃烧热的利用
中小合成氨不同之处在于所有中型合成氨厂以煤造气的工段,吹风气都经过燃烧室燃烧后再进入废热锅炉回收余热。
正如前述,原有的列管式废热锅炉都是按瞬时最大吹风气流量设计的,而吹风气在一个循环中只占 25%~28%的时间,所以设备的利用率不高。
即使上行煤气也通过废热锅炉,也只有 50%~60%的利用率,何况上行煤气的流量仅是吹风气瞬时流量的 1/3。所以合理的办法是将三台煤气炉的吹风气通过一个燃烧室燃烧,燃烧后的烟气再进入一个废热锅炉,这就大大提高了设备的利用率。
虽然利用原有的列管式废热锅炉也可做到这一点,但原有的废热锅炉设计的气体流速均相当高,锅炉进口处的流速高达 20m/s 以上。因此,高速磨损经常是管壁破坏的原因之一。
如果三台煤气炉的吹风燃烧气都经过同一锅炉,则磨损速度将增大二倍,因而其磨损破坏几率也将增大二倍。
根据中型合成氨生产的具体特点,在设计吹风气燃烧气余热回收的热管蒸汽发生器时应注意∶
① 应具有很高的可靠性及比较长的使用寿命;
② 体积应紧凑;
③ 金属耗量应少;
④ 注意风速的选择,防止快速磨损。
3 .一段转化炉空气预热器
一段转化炉是 30 万吨/年大型合成氨厂的关键设备。一段转化炉的任务是在外部供热的情况下使烃类与水蒸气的混合物在炉管内转化为 CH4、H2、CO、CO2等气体混合物。其中 H2、CH是合成氨的原料。
一段转化炉有多种结构型式。目前国内主要有顶部烧嘴和侧壁烧嘴二种形式,分别见图 5-9(a),图 5-9(b)。
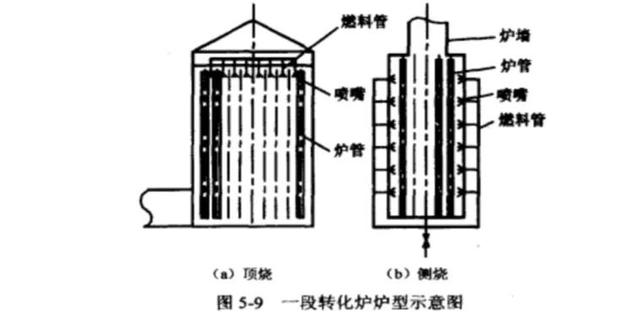
烧嘴喷出的燃料在空气助燃下加热炉内的转化炉管。热量大部分为转化炉管吸收。转化炉管所在区域称为辐射段。
为了充分合理地利用热量还必须使烟道气通过对流段,在对流段内布置有各种吸收烟道气余热的管道。烟气流出对流段的温度设计值在 250℃左右。
但实际上由于对流段内各种热回收管道的表面结垢,经过一段时间运行之后,排出对流段的烟气温度大多在 300℃左右。排出的烟气量(标准状况)达 140000~240000 m²/h。如果将其降温到 140℃排空,则回收的热量可达8400~15000 kW。回收这部分热量最合理的用途是加热助燃空气。
由于一段炉使用的燃料一般为轻柴油或天然气,节约这部分燃料也就更有价值。
对于大型合成氨厂的设备,其运转可靠性属第一。特别是像一段转化炉这样的关键设备,决不能因设备事故而停车,否则造成的停车损失太大,因此热管换热器设计最重要的是防止灰堵。
对于以煤气或天然气、轻柴油为燃料的一段炉的烟气的余热回收比较简单,灰堵的可能性不大。
而对于以重油或渣油为燃料的烟气余热回收则必须慎重考虑,防止灰堵的关键措施有如下几条。
(1)保持合理的风速
在压力降允许的条件下尽量采用高风速,风速高不仅不易积灰,传热系数也高。但风速过高又会引起压力降加大,压力降是由引风机的抽力决定的,所以二者必须兼顾。
为了保证合适的风速,许多设计者采用了等流速的设计方法。即保证烟气通过每一排热管的流速相等。
由于烟气在通过热管管排时,烟气温度不断降低,体积不断缩小,为了保持相等的流速,流道的截面也应该随之相应缩小。因此流体通道沿流动方向呈梯形。
选择最适宜的风速与系统允许的压力降有关,一段炉热管空气预热器的压力降一般小于600Pa。通常最小流通截面工况下的流速可在8~11m/s 的范围内选择。
(2)选择合理的翅片间距
翅片间距密,热管的根数可以减少,但翅片间距过小,不仅容易积灰,而目压力降也大。根据不同的燃料种类,可在6~12mm 之间选择。
(3)调整好末排管壁温度
热管管壁温度的调整始终是设计者应考虑的一个重要问题。
特别是当烟气流出换热器温度降得较低时,在逆流换热情况下,热管的冷侧正是常温空气的进口。这时应当注意热管的管壁温度是否在烟气露点以下。 如管壁温度低于烟气露点,则很容易形成灰堵。
烟气的露点与燃料的含硫量以及燃烧后烟气中的硫酸蒸汽分压有关。设计前应弄清燃料的含硫量,根据资料查询该种燃料烟气的露点。
我国的 30 万吨/年合成氨大型化肥厂大多从国外引进。在这些工厂中的一段转化炉多数未配有空气预热器,有的厂配用了回转式空气预热器,根据实用效果对比,回转式明显不如热管式好。
目前国内的30 万吨/年合成氨厂大多配用了热管式空气预热器。资料表明,回转式空气预热器改为热管式空气预热器后有如下优点。
① 免去了回转式电机的动力消耗;
② 热回收效率提高了18.3%;
③ 减少了维修工作量。
4 .变换工段气-气换热器
在中、小型合成氨厂的变换工段,来自热水饱和塔的半水煤气要与来自变换炉变换气进行热交换。通过换热,水煤气的温度升高,而变换气的温度降低。
半水煤气和变换气的组分都是有毒、易爆、易燃物质(CO、H,)。所有的变换工段的变换热交换器(第一热交换器、第二热交换器)都是采用列管式的,存在易腐蚀、泄漏、串气等问题。
特别是第一热交换器, 由于温度较低,极易腐蚀,维修工作量大。腐蚀还会引起列管管口堵塞,增加系统阻力,致使变换系统压差增大,影响生产的安全正常运行。
在变换系统中应用热管换热器具有如下优点∶
① 可以调整热管管壁温度,控制低温腐蚀的产生;
② 个别热管损坏不会发生二种气体的串混;
③ 设备紧凑,压力降小,对变换生产有利;
④ 使用寿命长,投资省。
变换工段的半水煤气和变换气都具有一定的压力,因此热管换热器的壳体也必须是按压力容器设计标准设计。
5 .二段转化炉高温高压蒸汽发生器
30万吨/年合成氨厂二段转化炉出口的转化气温度约为 975℃,必须使温度降至 360℃左右送入高温变换炉。
为了充分利用这部分热量,故使二段转化炉出口的转化气通过高压废热锅炉,利用这部分废热来产生高压蒸汽作为合成氨厂的动力蒸汽。
我国30万吨/年合成氨厂的高温高压废热锅炉迄今为止都是自国外引进。
目前主要有两种结构形式∶
① U型管式,如图5-12;
② 刺刀管式,如图 5-13。
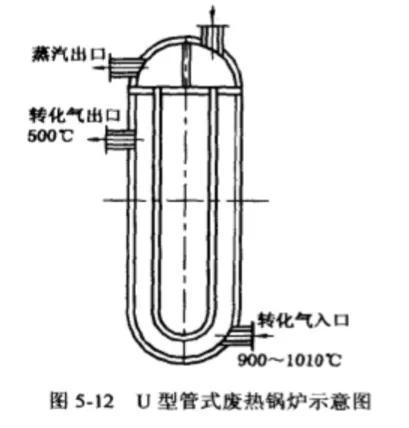
图 5-12 是 U 型管式废热锅炉结构,在高压管箱内用隔板将管板一分为二,管板的一侧进入来自汽包下降管的循环水,由U型管的端口进入管板下方的转化气壳体内。
循环水在 U 型管内接受管外转化气的热量产生蒸汽,汽水混合物向上流动至 U型管的另一端进入高压管箱隔板的另一侧,沿上升管进入汽包。
这种结构有其天生缺陷, 即汽-水循环回路不畅。因为当循环水在 U 型管内被加热成为汽水混合物时,在整个 U型管内都有向上流动的趋势,循环水的下降必然受到汽水混合物向上流动的阻挡。所以它的自然循环很不稳定,严重时形成汽阻使管子过热爆管。
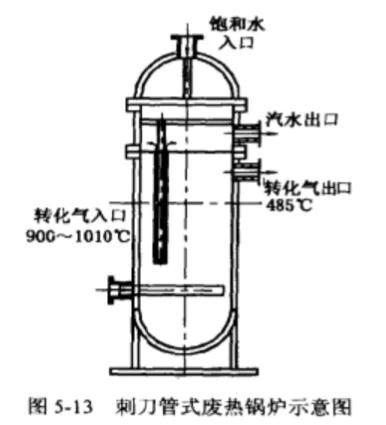
图 5-13 为刺刀管式废热锅炉。循环水从汽包的下降管由顶部进入中心管向下进入外套管的夹层,接受来自转化气的热量,汽水混合物向上流动沿夹层进入上端的汽水室再沿上升管进入汽包。
这种形式的汽水循环较U 型管结构合理。但结构较复杂,中心管下端与外套管端部的距离要求很严,此处是循环水受热最强的部分。
汽水混合物既沿夹层上升也有沿中心管向上流动的趋势,这种趋势也使中心管的循环水下降受到阻力,当上部分水板分水不均时,则有可能造成循环的恶化,部分中心管供水不足引起管壁过热爆管。
以上两种进口技术都存在固有的先天缺陷。在传统的传热技术范围内,只可能产生这些专利技术。然而如采用热管技术,就可以使汽水循环回路非常通畅,结构又非常简单。
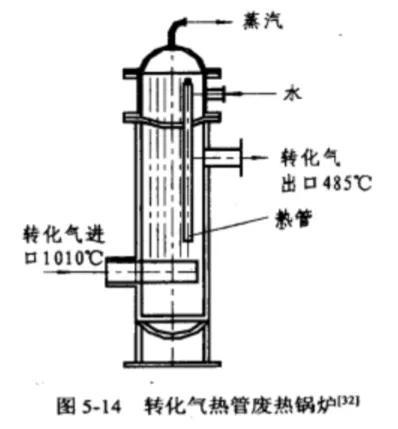
图 5-14 是热管式高温高压废热锅炉的结构示意图。
从汽包下降管来的饱和水从高压管箱的一侧进入高压管箱。饱和水在此接受热管冷却段放出的热量产生汽水混合物,蒸汽从顶部出口,沿上升管进入汽包。这种循环回路是典型的汽水循环回路,因此很容易建立起自然循环,系统的循环阻力也小。
其工作原理是高温的二段炉转化气由壳体的下部通过气体分布器向上流动,分别由环向隔板扫过热管的加热段。热管内部的工作液体受热汽化,向上流动到管板上方的冷却段。工作液体在冷却段放出汽化潜热加热管箱中的饱和水,使饱和水产生蒸汽。
放出汽化潜热后的工作液体沿热管内部管壁下流,在加热段继续受热汽化,工作液体蒸汽再次上升到达冷却段,加热管外的饱和水,使水变为蒸汽进入汽包,如此反复循环。
这种高温高压蒸汽发生器结构的优点非常明显。因为热管的二端均是自由的,没有高温下的热膨胀问题,循环水进入高压管箱后受到热管的均匀加热类似于大容积的池状沸腾,因此没有水分配问题。
热管的内部采用了液态金属(钠、钾)作为工作介质,液态金属的特点是饱和蒸汽压力很低。在大气压力的条件下,钠的沸点是 883℃,钾的沸点是 760℃。故在高温条件下工作的热管内部压力一般处在负压状态,管壁不会爆破。
即使个别热管管壁因某些特殊原因穿孔,内部少量的液态金属在高温转化气中将与水蒸气反应生成氢氧化合物。由于水侧的管壁完好故不会有水漏入转化气中,生产不会受到影响,安全可靠性远较 U 型管式及刺刀式废热锅炉高。
6 .绝热化学反应器级间热管换热器
在合成氨生产中,CO变换反应器和氨合成反应器都属于绝热催化反应器。其化学反应是典型的气固相催化可逆放热反应,从反应热力学和动力学可知,降底温度,移走反应热,增加压力和降低生成物浓度, 都有利于平衡向氨生成方向移动。
对于不可逆放热反应,温度升高,则反应速率常数增大,但平衡常数的数值降低,温度对平衡常数和反应速度的影响是相互矛盾的。因此一定组成条件下存在一个最佳反应温度问题。
这里以合成氨生产为例,其平衡曲线及最适宜温度曲线列于图 5-15。
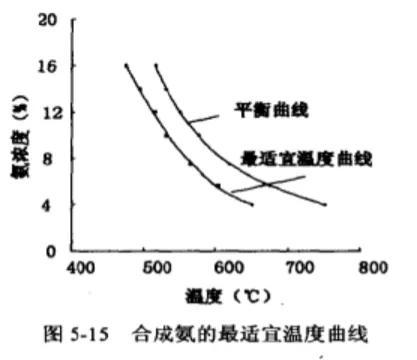
由图 5-15 可见,当氨浓度较高时所需的反应温度宜低;而氨浓度偏低时,则所需的最适宜反应温度较高,因此随着氨反应浓度的增加,触媒床层温度应尽量沿最适宜反应温度线往低温方向移动。
显然这时的反应速度也是逐渐下降的。但只要沿着最佳反应温度曲线移动,就能保持在该温度条件下的最大反应速率。所以如何移走反应热量,使氨的合成反应尽量靠近最佳反应温度进行,已成为氨合成塔内件研制的关键所在,也是评价该反应器优劣的重要标志之一。
但工业生产上要使反应完全按照最适宜反应温度的变化规律进行操作几乎是非常困难的。因为从图可知,随着反应率的提高,最适宜温度是由高逐渐降低的,如要使反应完全沿着最适宜温度曲线进行,就要采取边反应边进行冷却的措施,以移走反应热使气体冷却到最适宜温度,这就要使反应器的结构非常复杂。
国内外所有的合成反应器都围绕着这一目标不断开发新的结构,但遗憾的是迄今为还未能有重大突破,关键问题是在高温高压的有限空间内,常规的换热技术很难实现最佳反应温度的逼近。
结构的复杂性以及结构的不可靠性始终是很难逾越的障碍,热管技术的出现给反应器的内件改造带来了希望。
理论分析热管有可能将绝热反应器中床层的温度控制在最佳范围,如图 5-16 中虚线所示。图中横坐标为反应床层温度,纵坐标为氨合成率。
热管技术用在绝热催化反应器内的基本思想是逐段取出化学反应热以控制反应在最适宜的温度范围内得到最大的反应率,各种具体的化学反应器的操作条件(温度、压力、空速等)均不一致,因而根据不同的操作条件有不同的考虑。此研究工作已在南京化工大学取得阶段性成果。
相关参考