热流道温度怎么设置合理温度(塑胶模具设计基本知识提升)
Posted
篇首语:莫道桑榆晚,为霞尚满天。本文由小常识网(cha138.com)小编为大家整理,主要介绍了热流道温度怎么设置合理温度(塑胶模具设计基本知识提升)相关的知识,希望对你有一定的参考价值。
热流道温度怎么设置合理温度(塑胶模具设计基本知识提升)
摘要 简述塑料模具设计中已经成熟的经验及原则,提高对塑胶模具的认知,进而在结构设计时能更好的符合模具要求。
关键词 模具,浇注系统,顶出系统,温控系统,排气系统,抽芯系统等
1 引言一套完整的模具,它涵盖有多个相关系统,它们之间相辅相成.只有当各系统达到最佳组合,
才能保证模具的正常使用和精度.因模具的结构必须符合产品的要求,不同的产品有不同的要
求,而产品存在变化性和多样性,这就决定了模具的多样性.一般来说,典型之塑料模具包括:
浇注系统,顶出系统,冷却系统,排气系统,抽芯系统等.本文将针对模具的各个系统作简要
说明。
2.模具设计相关要素
2.1 分模面
为使产品从模具中取出,模具必须分成公母模侧两部分,此分界面称之为分模面.它有分模和排气
的作用,但因模具精度和成型之差异,易产生毛边,结线,有碍产品外观及精度,选择分模面时注意:
1 不可位于明显位置而影响产品外观.
2 开模时应使产品留在有脱模机构的一侧.
3 位于模具加工和产品后加工容易处.
4 对于同轴度要求高的产品,尽可能将型腔设计在同一侧.
5 避免长抽芯,考虑将其放在公模开模方向,如一定要有应将抽芯机构尽量设在公模侧.
6-般不采用圆弧部分分模,这样会影响产品外观.
7 对于流动性好易溢边之塑料,应采用插破方式分型可防治毛边产生.
8 对于高度高,脱模斜度小之产品,可取中间分模,型腔分两边以有利于脱模.
2.2 脱模斜度
为使产品容易从模具中脱出,模具上必须设置脱模斜度.其大小视产品形状,塑料,模具结构,表
面精度和加工方式不同而异.一般为1-3°,在不影响产品外观和性能之情形下,脱模斜度愈大愈好

.
格形状,尺寸及肉厚不同应有不同的脱模斜度,经验公式如下:
0.5(A---B)/H =1/12—1/14
A=大端尺寸B=小端尺寸H=高度
栅格节距在 4mm 以下之场合,脱模斜度为 1/10 左右,栅格肉厚超过8mm,斜度不可过份加大,可
在母模侧多留胶位处分模,如栅格段胶位加大,可考虑加大斜度.
3.加强筋(可改善料流,防止应力变形,并起补强作用)
a.纵肋:0.5(A-B)/H=1/500—1/200
b.底肋:0.5(A-B)/H=1/150—1/100
c.凸柱:0.5(大端直径 – 小端直径)/H=1/30—1/20 (内外孔在模具同一侧)
母模侧:0.5(大端直径 – 小端直径)/H=1/50—1/30
公模侧:0.5(大端直径 – 小端直径)/H=1/100—1/50 (内外孔在模具两侧)
注: 母模侧脱模斜度可较公模侧大些,以利于脱模.
2.3 肉厚
产品的肉厚会直接影响到成型周期和生产效率,并会因肉厚不均引起缩收下陷和应力产生,设计模
具时,决定肉厚应注意:
1.产品机械强度是否充分.
2.能否均匀分散冲击力和脱模力,不发生破裂.
3.有埋入件时,须防止破裂,是否会因肉薄产生结合线而影响强度.
4.尽可能肉厚一致,以防缩收下陷.
5. 肉太薄是否会引起充填不足或阻碍料流.


一般为产品上凸出之圆柱,它可增强孔的周边强度,装配孔及局部增高之用.必须防止因肉厚增加
造成缩水和因聚集空气造成充填不满或烧焦现象,设计时注意点:
1.其高度以不超过本身直径之两倍为宜,否则须增设加强筋.
2.其位置不宜太接近转角或侧壁,以利于加工.
3.优先选择圆形,以利于加工和料流,如在底部可高出底面 0.3—0.5mm.
2.5 孔
在多数产品上都有孔的存在,其主要有三种方法来取得:
1. 在产品上直接成型
2.在产品上先成型预留孔,再机加工完成.
3.成型后完全由机加工钻孔.
设计时须注意以下几点:
1.孔与孔之间距离须孔径 2 倍以上.
2.孔与产品边缘之距离应为孔径之 3 倍以上.
3.孔之周边宜增加肉厚.
4.孔与产品侧壁之距离应为孔径 0.75 倍以上.
5.孔之直径在 1.5mm 以下时,很容易产生弯曲变形,须注意孔深不宜超过孔径 2 倍以上.
6.分模面在中间之通孔,为防止偏心,可将不重要一侧之孔径加大.
2.6 螺纹
为装配之用,产品上有时会有螺纹设计,它可以直接成型,也可以在成型后再机械加工.对于经常
拆卸或受力大之螺纹,则采用金属螺纹镶件,设计时注意如下原则:
1.螺距小于 0.75mm 之螺纹避免使用,最大可使用螺距 5mm 之螺纹.
2.因塑料收缩原因,避免直接成型长螺纹,以防螺距失真.
3.螺纹公差小于塑料收缩量时,避免使用.
4.如内外螺纹配合,须留 0.1—0.4mm 之间隙.
5.螺纹部分应有 1--3°脱模斜度.
6.螺牙不可延长至产品末端,须设 0.8mm 左右之光杆部位.以利于模具加工和螺纹寿命.
7.在一些类似瓶盖产品上,它会设一些竖琨纹,其间距宜大,最小为 1.5mm,一般为 3.0mm,在分模
面设至少 0.8mm 平坦部位.
2.7 镶嵌件
为了防止产品破裂,增加机械强度或作为传导电流之媒体及装饰之用,在产品成型时常埋入镶嵌件,
注意要点:
1. 保证镶件牢靠性,镶件周围胶层不能太薄.
2.镶件和镶件孔配合时须松紧合适,不影响取放.
3.为使镶件与塑料结合紧密,埋入部分常设计成粗糙或凹凸之形状(压花.钻孔.冲弯.切槽.倒扣
等).
2.8 其它要点
1.加强筋不可太厚,一般不超过肉厚的一半,以防缩水.
2.只要不影响外观和功能,光面尽量改为咬花面,这样可减少模具加工难度,增加美感,也可防止缩
水产生.
3.在凸柱周边,可除去部分肉厚,以防止收缩下陷.
4.肉厚较薄之孔,应将孔边及高度增加,以便补强.
5.心芯梢受收缩力影响,产品顶出时易造成破裂,可设置凸边,承受顶出力.
6.转角设R,可改善强度,防止应力集中有利于料流.
7.避免锐角,薄肉部份易使材料充填不足.
8.外边有波纹之产品,为方便后加工,可改为加强边缘.
9.分模面有阶段形时,模具加工不易,考虑改为斜线或曲线分模.
10.贯穿之抽芯易发生故障,改为两侧抽芯为佳.
11.因圆形比其它形状加工更易,可降低成本,优先选用.
12.在产品上加蚀文字或图案时,如无特殊要求,尽量设计凹字,便于模具加工.
3. 浇注系统设计
浇注系统是塑模设计中一重要环节,常分为普通和无流道浇注系统.它跟所用塑料产品形状,尺寸,
机台,分模面有密切关系.设计时注意以下原则:
1.流道尽量直,尽量短,减少弯曲,光洁度在 Ra=1.6—0.8um 之间.
2.考虑模具穴数,按模具型腔布局设计,尽量与模具中心线对称.
3.当产品投影面积较大时,避免单面开设浇口,以防注射受力不均.
4.浇口位置应去除方便,在产品上不留明显痕迹,不影响产品外观.
5.主流道设计时,避免塑料直接冲击小型芯或小镶件,以免产生弯曲或折断.
6.主流道先预留加工或修正余量,以便保证产品精度.
3.1 主流道设计
主流道是连接机台喷嘴至分流道入口处之间的一段通道,是塑料进入模具型腔时最先经过的地
方.其尺寸,大小与塑料流速和充模时间长短有密切关系.太大造成回收冷料过多,冷却时间增长,包
藏空气增多.易造成气泡和组织松散,极易产生涡流和冷却不足;如流径太小,热量损失增大,流动性
降低,注射压力增大,造成成型困难.一般情况下,主流道会制造成单独的浇口套,镶在母模板上.但
一些小型模具会直接在母模板上开设主流道,而不使用浇口套.主流道设计要点:
1.浇口套内孔为圆锥形( 2--6°),光洁度在 Ra=1.6—0.8um.锥度须适当,太大造成压力减少,产生
濣流,易混进空气产生气孔,锥度过小会使流速增大,造成注射困难.
2.浇口套口径应比机台喷嘴孔径大 1—2mm,以免积存残料,造成压力下降,浇道易断.
3.一般在浇口套大端设置倒圆角(R=1—3mm),以利于料流.
4.主流道与机台喷嘴接触处,设计成半球形凹坑,深度常取 3—5mm.特别注意浇口套半径比注嘴半
径大 1—2mm,一般取 R=19—22mm 之间,以防溢胶.
5.主流道尽量短,以减少冷料回收料,减少压力和热量损失.
6.主流道尽量避免拼块结构,以防塑料进入接缝,造成脱模困难.
7.为避免主流道与高温塑料和射嘴反复接触和碰撞造成损坏,一般浇口套选用优质钢材加工,并热处
理.
8.其形式有多种,可视不同模具结构来选择,一般会将其固定在模板上,以防生产中浇口套转动或被
带出.
3.2 分流道设计
分流道是主流道的连接部分,介于主流道和浇口之间,起分流和转向作用.分流道必须在压力损失
最小的情况下,将熔融塑料以较快速度送到浇口处充模,因在截面积相等的条件下,正方形之周长最长,
圆形最短.面积如太小,会降低塑料流速,延长充模时间,易造成产品缺料,烧焦,银线,缩水;如太
大易积存过多气体,增加冷料,延长生产周期,降低生产效率.对于不同塑料材质,分流道会有所不同,
但有一个设计原则:必须保证分流道的表面积与其体积之比值最小.即在分流道长度一定的情况下,要
求分流道的表面积或侧面积与其截面积之比值最小.
分流道型式有多种,它因塑料和模具结构不同而异,常用型式有圆形,半圆形,矩形,梯形,U形,
正六边形,设计时基本原则:
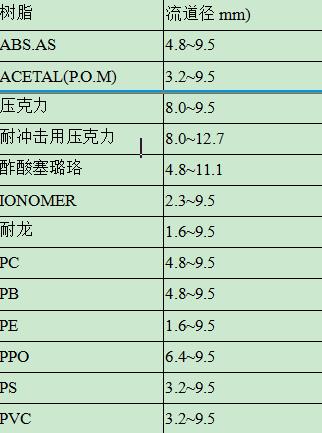
3.3浇口设计


1.在条件允许下,分流道截面积尽量小,长度尽量短.
2.分流道较长时,应在末端设置冷料穴,以容纳冷料和防止空气进入,而冷料穴上一般会设置拉料杆,
以便于胶道脱模.
3.在多型腔模具中,各分流道尽量保持一致,长度尽量短,主流道截面积应大于各分流道截面积之
和.
4.其表面不要求过份光滑(Ra=1.6 左右),有利于保温.
5.如分流道较多时,应考虑加设分流锥,可避免熔融塑料直接冲击型腔,也可避免塑料急转弯使塑料
平稳过渡.
6.分流道一般采用平衡式方式分布,特殊情况可采用非平衡方式,要求各型腔同时均衡进胶,排列紧
凑,流程短,以减少模具尺寸.
7.流道设计时应先取较小尺寸,以便于试模后有修正余量.

3.3 浇口设计
浇口是指流道末端与型腔之间的连接部分,是浇注系统的最后部分.其作用是使塑料以较快速度进
入并充满型腔。它能很快冷却,封闭.防止型腔内还未冷却的热胶倒流.设计时须考虑产品尺寸,截面
积尺寸,模具结构,成型条件及塑料性能有关.浇口尽量短小,与产品分离容易,不造成明显痕迹,其
类型多种多样。主要有
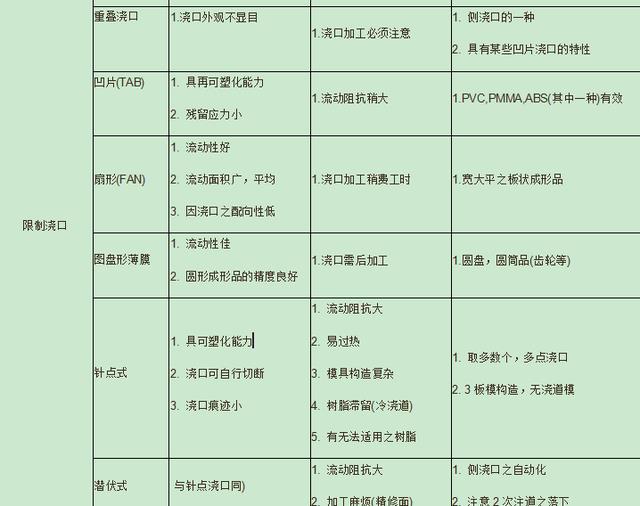

1.胶口应开设在产品肉厚部分,保证充模顺利和完全.
2.位置应选在使塑料充模流程最短处,以减少压力损失,有利于模具排气.
3.通过模流分析或经验,判断产品因浇口位置而产生之结合线处,是否影响产品外观和功能,可加
设冷料穴加以解决.
4.细长型芯附近避免开设浇口,以免料流直接冲击型芯,产生变形错位或弯曲.
5.型或扁平产品,建议采用多点进浇,可防止产品翘曲变形和缺料.
6.量开设在不影响产品外观和功能处,可在边缘或底部处.
7.浇口尺寸由产品大小,几何形状,结构和塑料种类决定,可先取小尺寸再根据试模状况进行修
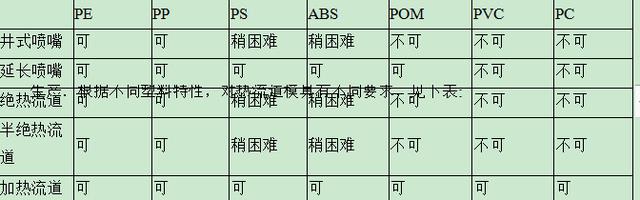
8.模多穴时,相同的产品采用对称进浇方式,对于不\\同产品在同一模具中成型时,优先将最大产品
放在靠近主流道的位置.
9.浇口附近之冷料穴,尽端常设置拉料杆,以利于浇道脱模.
3.4 热流道
目前浇注系统发展和改进的一个重要方向,就是开发热流道模具.它与一般注射模具的主要区别就
是注射成型过程中,浇注系统内之塑料不会冷却拟固,也不会形成浇道与产品一起脱模.因此也称无流
道模具,在大型和精密模具设计中,应用已越来越广泛.
它有以下优点:
1.短成型周期,省去剪浇口,修整产品,破碎回收等工序,节约人力,物力,提高生产效率.
2.无冷胶,可减少材料消耗.
3.生产中温度严格控制,显著提高产品质量,降低次品产生.
4.注系统中塑料始终处于融熔状态,有利于压力传递,可降低注射压力,利于成型.
5.无浇道产生,所以可缩短开模行程,有利于模具和机台寿命.
但热流道模具结构复杂,温度控制要求严格,需要精密的温控系统,制造成本较高,不适合小批量

4.顶出系统设计
产品完成一个成形周期后开模,产品会包裹在模具的一边,必须将其从模具上取下来,此工作必须
由顶出系统来完成.它是整套模具结构中重要组成部分,一般由顶出,复位和顶出导向等三部分组成.
4.1 按动力来分
1.手动顶出: 当模具开模后,由人工操纵顶出系统顶出产品.它可使模具结构简化,脱模平稳,产品
不易变形.但工人劳动强度大,生产率低,适用范围不广.一般在手动旋出螺纹型芯时使用.
2.机动顶出: 通过注射机动力或加设之马达来推动脱模机构顶出产品,它可通过机台上的顶杆推顶针
板,来达到脱模目的.也可在公母模板上安装定距拉杆或链条,靠开模力拖动顶出机构顶出产品,调模
时必须注意控制开模行程,适用于顶出系统在母模侧之模具.
3.液压顶出: 在模具上安装专用油缸,由注射机控制油缸动作,其顶出力速度和时间都可通过液压系
统来调节,可在合模之前顶出系统先回位.
4.气动顶出: 利用压缩空气在模具上设置气道和细小的顶出气孔,直接将产品吹出.产品上不留顶出
痕迹,适用于薄件或长筒形产品.
4.2 按模具结构分
一次顶出机构,二次顶出机构,母模顶出机构,浇注系统顶出机构,螺纹顶出机构等.
设计原则:
1.选择分模面时尽量使产品留在有脱模机构的一边,
2.顶出力和位置平衡,确保产品不变形,不顶破.
3.顶针须设在不影响产品外观和功能处.
4.尽量使用标准件,安全,可靠有利于制造和更换.
顶出系统形式多种多样,它与产品之形状,结构和塑料性能有关,一般有顶杆,顶管,推板,顶出
块,气压,复合式顶出等.
4.3 顶杆
它是顶出机构中最简单,最常见的一种形式,其截面积形式主要有如下:
1.圆形 因圆形制造加工和修配方便,顶出效果好,在生产中应用最广泛.但圆形顶出面积相对较小,
易产生应力集中,顶穿产品,顶变形等不良.在脱模斜度小,阻力大等管形,箱形产品中尽量避免使
用.当顶杆较细长时,一般设置成台阶形的有托顶针,以加强刚度,避免弯曲和折断.
设计要点:
1.顶出位置应设置在阻力大处,不可离镶件或型芯太近,对于箱形类等深腔模具.侧面阻力最大,应
采用顶面和侧面同时顶出方式,以免产品变形顶破.
2.产品阻力均衡时,顶杆应对称设置,使受力平衡.
3.当有细而深之加强筋时,一般在其底部设置顶杆.
4.若模具上有镶件,顶针设在其上效果更佳.
5.在产品进胶口处避免设置顶针,以免破裂.
6.当产品表面不允许有顶出痕迹时,可设置顶出耳再剪除.
7.对于薄肉产品在分流道上设置顶针,即可将产品带出.
8.顶针与顶针孔配合,一般为间隙配合.如太松易产生毛边,太紧易造成卡死.为利于加工和装配,
减少摩擦面,一般在模仁上预留 10—15mm 之配合长度,其余部分扩孔 0.5—1.0mm 成逃孔.
9.为防止顶针在生产时转动,须将其固定在顶针板上,其形式多种多样,须根据顶针大小,形状,位
置来具体确定,在此不一一列举.
10.顶出系统托模以后在进行下一周期生产时,必须退回原处,其形式主要有强制回位,拉杆回位,
弹簧回位,油缸等.
4.4 顶管
又叫司筒或套筒顶针,它适用于环形筒形或带中心孔之产品顶出.由于它是全周接触,受力均匀,
不会使产品变形,也不易留下明显顶出痕迹,可提高产品同心度.但对于周边肉厚较薄之产品避免使用,
以免加工困难和强度减弱,造成损坏.
4.5 推板
此形式适用于各种容器,箱形,筒形和细长带中心孔之薄件产品.它顶出平稳均匀,顶出力大,不
留顶出痕.一般会有固定连接,以免生产中或托模时将推板推落.但只要导柱足够长,严格控制托模行
程,推板也可不固定.推板与型芯之间的配合须顺畅,防止摩擦或卡死,也必须防止塑料渗入间隙中,
当产品为盲孔时,会因真空吸附造成脱模困难和产品变形,一般会在公模上设置一菌形阀,在顶出时菌
形阀打开,进入空气,使脱模顺畅.它可用弹簧回位,也可跟顶出装置连在一起兼作顶杆作用.
4.6 顶出块
有些带突缘或尺寸较大之产品,为便于加工和脱模,常设计成顶出块形式顶出.大多其平面为分模
面,下面有两支或数支较大直径顶杆连接,顶出面积较大,平稳.在有成形面和尺寸较大之模具中应用
较广泛.
4.7 气压顶出
当产品为深腔薄肉件时,用压缩空气顶出,简单而有效.可在公模仁上设置一些细小进气孔,也可
设置菌形杆,开模后通入 5—6 个大气压之压缩空气,使弹簧压缩开启阀门,高压空气进入产品与公模仁
之间,使产品脱模.但对于箱形产品,因气体进入会使侧壁横向抠张,而使空气漏掉,这时应配与推板
配合使用.
4.8. 复合顶出
受产品形状影响,多数模具采用两种以上顶出方式,以便达到理想的顶出效果,具体形式须根据产
品和模具结构来定,在此不作具体叙述.
4.9 其它顶出方式
4.9.1 点状进胶浇道自动脱落
点浇口在母模一边,为取出胶道,须加设一分型面.开模后一般由人工取出胶道,造成操作麻烦,
生产率降低,为适应自动化生产,最好设计成自动脱落装置,使胶道在顶出时自动脱落.
a.侧凹拉断 在分流道尽头钻一斜孔,开模后拉出胶道,由中心顶杆顶出.
b.拉料杆拉断 由拉料杆拉出胶道,开模一定行程后限位杆带动推板将胶道推落.
c.母模推板推脱 开模时母模板与母模推板先分型,胶道留在母模板与母模一起移动一定行程后,限
位杆限制推板移动,推板与模板分开,胶道被拉断而自动脱落.
d.顶针拉断 对于细长深腔模具,可在母模设置一顶出系统,开模后以限位杆行程使顶针反向顶出胶
道,产品由推板推出,此方式与开模行程有关,应用较特殊.
4.9.2 母模侧顶出方式
一般的产品都会留在公模侧顶出,但有些产品因形状特殊或产品特殊要求,顶出装置必须设在母
模.因母模是固定的机台,顶杆无法作用在顶板上,必须借助开模力或外力来完成.常见的有油缸,电
动,拉勾等.
4.9.3 螺纹顶出
因螺纹与一般产品形状特殊,必须旋转顶出或侧向脱模,根据产品复杂程度和产量,一般有采用手
动和机动两种方式.
1)强制脱螺纹
a. 对于本身弹性强之塑料(PP . PE),可利用其弹性进行强制脱模而不会损坏螺牙.
b. 用具有弹性的珪橡胶做成螺纹型芯,开模时用弹簧先退出型芯中顶杆,使橡胶型芯产生向内收缩,
再用顶针将产品脱出.此方式能简化模具结构,但橡胶型芯寿命较短,只适用于小批量生产.
c.有些螺纹可通过半圆滑块或型环成形,用两个对半滑块合起来组成完整螺纹或产品顶出后用手,
2)电机将螺纹旋出.

螺纹脱出时必须作相对转动,模具上必须要有止转装置来保证.
a. 外部止动 模具母模设有止转花纹,公模仁回转时产品可自动脱落.
b. 内部止动 有内螺纹之产品在公模仁顶面设置止转形式,脱模时止动模仁旋转并轴向顶出螺纹可脱
出,注意止动模仁螺距必须与产品螺距一致.
c. 产品端面止动 在产品端面设置止动小凸点,型芯旋转时推板将产品顶出.
小型产品有侧浇口时,只顶出胶道也可将产品带出,但对于软性塑料则避免使用.
型芯旋转驱动方式 常用的有人工,电动,油缸,气缸,液压马达及大螺距丝杆螺母驱动等方式,一般来
讲,旋转机构在设计时,产品有几扣螺纹,螺纹型芯就必须转几圈.
5.冷却系统
冷却系统之设计规则 设计冷却系统的目的在于维持模具适当而有效率的冷却。冷却孔道应使用标准
尺寸,以方便加工与组装。设计冷却系统时,模具设计者必须根据塑件的肉厚与体积决定下列设计参数:
冷却孔道的位置与尺寸、孔道的长度、孔道的种类、孔道的配置与冷却系统之设计规则。
设计冷却系统的目的在于维持适当而有效率的冷却。冷却孔道应使用标准尺寸,以方便加工与组装。
设计冷却系统时,模具设计者必须根据塑件的肉厚与体积决定下列设计参数:冷却孔道的位置与尺寸、
孔道的长度、孔道的种类、孔道的配置与连接、以及冷却剂的流动速率与热传性质。
5.1 冷却管路的位置与尺寸
要维持经济有效的冷却时间,就应避免塑件肉厚过大。塑件所需的冷却时间随其肉厚增加而急速增
长。塑件肉厚应该尽可能维持均匀,例如图 6-56 的设计。冷却孔道最好设置是在公模块与母模块内,设
在模块以外的冷却孔道比较不易精确地冷却模具。
通常,钢模的冷却孔道与模具表面、模穴或模心的距离应维持为冷却孔道直径的 1~2 倍,经验要求,
钢材冷却孔道要维持 1 倍直径的深度,铍钢合金要 1.5 倍直径的深度,铝材要 2 倍直径的深度。冷却孔
道之间的间距应维持 3~5 倍直径。冷却孔道直径通常为 10~14 mm(7/16~9/16 英吋),如图 6-57 所示。
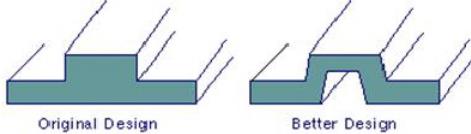
图:应尽可能将塑件设计为均匀肉厚
5.2 流动速率与热传
塑件两侧的温度应维持在最小的差异,紧配塑件温差应维持在 10℃以内。当冷却剂之流动从层流转变为扰流,
热传效果变佳。层流在层与层之间仅以热传导传热;扰流则以径向方向质传,加上热传导和热对流两种方式传热,
结果,热传效率显者增加,如图 6-58 所示。应注意确保冷却管路之各部份的冷却剂都是扰流。
5o/z4E-l#[)h*F1^/P!_
当冷却剂到达扰流流动状态后,流速的增加对于热传的改善很有限,所以,当雷诺数超过 10,000 时,就不须再增加
冷却剂的流动速率,否则,只会小幅地改善热传,却造成冷却管路的高压力,需要更高的帮浦费用。图 6-59 说明了
一旦冷却剂变成扰流后,更高的冷媒流动速率并无法改善热传速率或冷却时间,但是压力降与帮浦成本却显著提高。
冷却剂会向阻力最低的路径流动。有时候可以尝试使用限流塞将冷却剂引导流向热负荷较高的冷却孔道。气隙会降
低热传效率,因此,应尝试消除镶埋件与模板之间的气隙,以及冷却管路内的气泡。
模流分析软件的冷却分析可以协助发现与修正静止冷却管路和快捷方式冷却管路,以及冷却管路的高压力降。
6.排气系统
注塑模的排气是模具设计中的一个重要问题,特别是在快速注塑成型中对注塑模的排气要求就更加严
格。
6.1 注塑模中气体的来源:
1.浇注系统和模具型腔中存有的空气。
2.有些原料含有未被干燥排除的水分,它们在高温下气化成水蒸气。
3.由于注塑时温度过高,某些性质不稳定的塑料发生分解所产生的气体。
4.塑料原料中的某些添加剂挥发或相互发生化学反应所生成的气体
6.2 注塑模的排气不良,将会给塑件的质量等诸多方面带来一系列的危害。主要表现如下:
1.在注塑过程中,熔体将取代型腔中的气体,如果气体排出不及时,将会造成熔体充填困难,造成注
射量不足而不能充满型腔。
2.排除不畅的气体会在型腔内形成高压,并在一定的压缩程度下渗人塑料内部,造成气孔、组织疏松、
空洞、银纹等质量缺陷。
3.由于气体被高度压缩,使得型腔内温度急剧上升,进而引起周围熔体分解、烧灼、使塑件出现局部
碳化和烧焦现象。它主要出现在两股熔体的合流处, 死角及浇口凸缘处。
4.气体的排除不畅,使得进入各型腔的熔体速度不同,因此,易形成流动痕和熔合痕,并使塑件的力
学性能降低。
5.由于型腔中气体的阻碍,会降低充模速度,影响成型周期,降低生产效率。
6.3 排气槽设计要点:
1.排气槽尽量放在分型面的凹模一边,方便模具的制造与清理;
2.尽量设在料流末端和塑件壁厚较大部分;
3.排气方向不应朝向操作人员,并应加工成曲线或折弯状态,以免气体喷射时烫伤工人;
4.排气槽宽度常取 1.5-6mm,槽深 0.02-0.05mm,以塑料不进入排气槽为宜。
6.4 排气系统的方式:
1.开设排气槽
排气槽通常开设在型腔一侧,围绕型腔开设或在熔体最后充满部位。
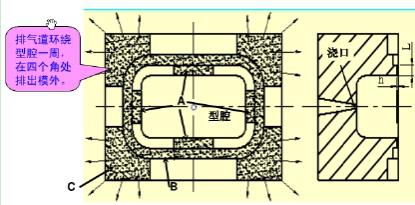



排气通道尺寸:排气道 A 深:0.01~0.02mm 宽:3~5mm 长:一般 3~5mm
排气道 B 深:0.05~0.08mm 宽:3~5mm 或更大 长:根据需要而定
排气道 C 深:可取 1mm 宽:可大于 5mm 长:连通至模板边界
分型面排气
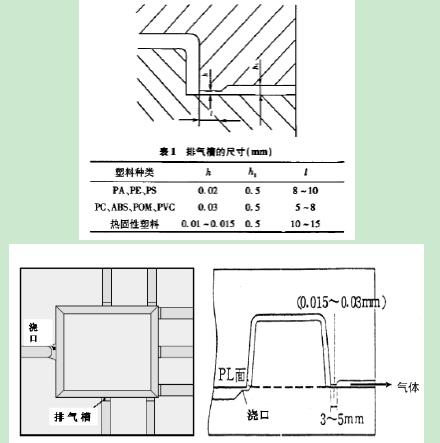
模具流道排气
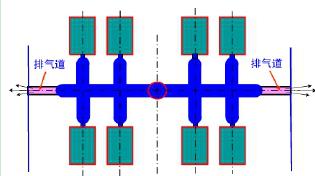


2 抽真空排气
这种方式要求模具的分型面温和要好,通过气孔将模腔内放入气体抽净。但需要配备抽真空设备,
增加模具成本,一般不采用。
3 利用间隙排气
1)镶拼零件的配合面间隙,如型腔、型芯镶块。
2)侧向抽芯零件间隙
3)顶出零件配合间隙(推杆、块)
4)分型面间隙(粗糙度一般)利用间隙排气时,使用时间长了,间隙可能堵塞,应定期清理,保持
畅通。
4 利用多孔金属排气
近年来新发展的一种内部具有均匀的相互连通的孔隙结构的金属材料---多孔金属,对模具型腔的排
气具有很好的效果。当型腔某些部位排气困难时,可循用多孔金属制作型腔镶块,排气效果十分明显。
模具使用时应注意维护与清理,保持气孔畅通。
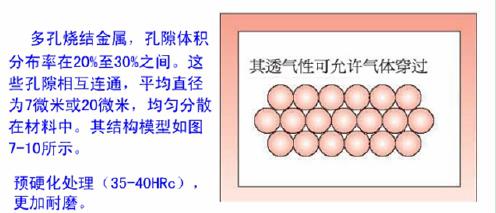
5 混合排气
通常是开设排气通道和间隙排气混用。
塑料的溢边值与排气间隙
排气系统应保证气体顺利逸出,塑料熔体不能流出。
塑料材料的溢边值可分为如下三种:
低粘度材料不产生医疗的间隙为:0.01~0.03mm
中粘度材料不产生医疗的间隙为:0.03~0.05mm


7.抽芯系统
当塑料制品侧壁带有通孔凹槽,凸台时,塑料制品不能直接从模具内脱出,必须将成型孔,凹槽及
凸台的成型零件做成活动的,称为活动型芯。完成活动型抽出和复位的机构叫做抽苡机构。
7.1 抽芯机构的分类
1.机动抽芯
开模时,依靠注射检的开模动作,通过抽芯机来带活动型芯,把型芯抽出。机动抽芯具有脱模力大,
劳动强度小,生产率高和操作方便等优点,在生产中广泛采用。按其传动机构可分为以下几种:斜导柱
抽芯,斜滑块抽芯,齿轮齿条抽芯等。
2.手动抽芯
开模时,依靠人力直接或通过传递零件的作用抽出活动型芯。其缺点是生产,劳动强度大,而且由
于受到限制,故难以得到大的抽芯力、其优点是模具结构简单,制造方便,制造模具周期短,适用于塑
料制品试制和小批量生产。因塑料制品特点的限制,在无法采用机动抽芯时,就必须采用手动抽芯。手
动抽芯按其传动机构又可分为以下几种:螺纹机构抽芯,齿轮齿条抽芯,活动镶块芯,其他抽芯等。
3.液压抽芯
活动型芯的,依靠液压筒进行,其优点是根据脱模力的大小和抽芯距的长短可更换芯液压装置,因
此能得到较大的脱模力和较长的抽芯距,由于使用高压液体为动力,传递平稳。其缺点是增加了操作工
序,同时还要有整套的抽芯液压装置,因此,它的使用范围受到限制,一般很小采用。
7.2 斜导柱抽芯机构设计原则:
1.活动型芯一般比较小,应牢固装在滑块上,防止在抽芯进松动滑脱。型芯与滑块连接有一定的强度
和刚度。
2.滑块在导滑槽中滑动要平稳,不要发生卡住,跳动等 现象。
3.滑块限位装装置要可靠,保证开模后滑块停止在一定而不任意滑动。
4.锁紧块要能承受注射时向压力,应选用可靠的连接方式与模板连接。锁紧块和模板可做成一体。锁
紧块的斜角 θ,一般取 θ1-θ>2°-3°,否则斜导柱无法带动滑块运动。
5.滑块完成抽芯运动后,仍停留在导滑槽内,留在导滑槽内的长度不应小于滑块全长的-4、3,否财,
滑块在开始复位时容易倾斜而损坏模具。
6.防止滑块设在定模的情况下,为保证塑料制品留在定模上,开模前必须先抽出侧向型芯,最好采
取定向定距拉紧装置。
7.3 斜滑块抽芯机构设计
塑料制品侧面的凹穴或凸台较浅,所需的抽芯距不大,但所需的脱模力较大时,可选 用斜滑块抽芯
结构。这种斜滑块抽芯结构的特点是:当推杆推动斜滑块时,推杆及抽芯(或分型)动作同时进行。因
斜滑块刚性好,能承受较大的脱模力,因此,斜滑块的斜角比斜导柱的斜 角稍大,一般斜块的 斜角不
能大于 30°,否则易发生故障。斜滑块推出长度一般不超过导长度的 2/3,如果太长,会影响斜滑块的导
滑。因为斜块抽芯结构简单,安全可靠,制造比较方便。因此,在塑料射模具中应用广泛。
1.斜滑块的导滑及组合形式。按导滑部分形状可分为矩形,半圆形和燕尾形。
2.斜滑块的组合形式斜滑块的组合,应考虑抽芯方向,并尽量保持塑料制品的外观美不使塑料制
品表面留有明显的痕迹。同时还要考虑滑块的组合部分有足够的强度。如果塑料制品外形有转折处,则
斜滑块的拼缝线应与塑料制品的折线重合。
8 结论:
上述仅对模具设计时各个系统的注意事项做简要的汇总说明,内容不是很全面,未涉及到设计计算
的具体细节,仅给初学者一个初步的认识,希望对大家有所帮助。
相关参考
热流道的种类:开放式热流道、针阀式热流道、针点式热流道。第一种:开放式热流道。1.开放式热流道在成型中零件表面还会存在一个小点有进胶口,需要人工去除。2.最大的优点,就是进胶量比较大,在设计中基本上使用大...
热流道的种类:开放式热流道、针阀式热流道、针点式热流道。第一种:开放式热流道。1.开放式热流道在成型中零件表面还会存在一个小点有进胶口,需要人工去除。2.最大的优点,就是进胶量比较大,在设计中基本上使用大...
热流道分三种,分流板、喷嘴、温控箱。可以看看我放的图纸,主浇口进料,通过分流板流过喷嘴,温控箱阿诺立是控温的。热流道模具是利用加热装置使流道内熔体始终不凝固的模具。因为它比传统模具成形周期短,而且更节...
热流道分三种,分流板、喷嘴、温控箱。可以看看我放的图纸,主浇口进料,通过分流板流过喷嘴,温控箱阿诺立是控温的。热流道模具是利用加热装置使流道内熔体始终不凝固的模具。因为它比传统模具成形周期短,而且更节...
...三根据产品所用的树脂原材料所需的温度,模具温度(有热流道的也要设定温度)进行合理
...三根据产品所用的树脂原材料所需的温度,模具温度(有热流道的也要设定温度)进行合理
热流道内部实际温度高于控制器设定的温度很多时,产品会出现严重的异色,料花,糊斑;模具浇口会出现流延,拉丝,冒烟,熔体喷出等异常情况。导致热流道内部实际温度超高的原因主要有以下几点:1.不合理的热电偶安装...
热流道内部实际温度高于控制器设定的温度很多时,产品会出现严重的异色,料花,糊斑;模具浇口会出现流延,拉丝,冒烟,熔体喷出等异常情况。导致热流道内部实际温度超高的原因主要有以下几点:1.不合理的热电偶安装...
...的生产成本就成为每个公司要重点考虑的方法之一。使用热流道模具是一个降低成本的不错方法,它不仅减少了水口料的产生(减少对环境的污染)而且还可以缩短注塑产品的生产周期,提高工作效率。并同时还可以提高注塑产...
...的生产成本就成为每个公司要重点考虑的方法之一。使用热流道模具是一个降低成本的不错方法,它不仅减少了水口料的产生(减少对环境的污染)而且还可以缩短注塑产品的生产周期,提高工作效率。并同时还可以提高注塑产...