热处理高频加工(常用钢材热处理方法及目的)
Posted
篇首语:一寸光阴一寸金,寸金难买寸光阴。本文由小常识网(cha138.com)小编为大家整理,主要介绍了热处理高频加工(常用钢材热处理方法及目的)相关的知识,希望对你有一定的参考价值。
热处理高频加工(常用钢材热处理方法及目的)
常用钢材热处理方法
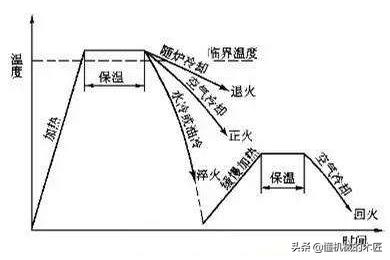
一.淬火
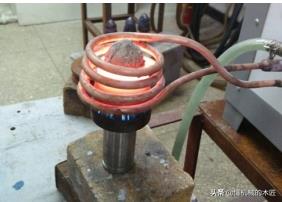
将钢件加热到临界温度以上40~60℃,保温一定时间,急剧冷却的热处理方法,称为淬火。常用急剧冷却的介质有油、水和盐水溶液。淬火的加温温度、冷却介质的热处理规范,见表<常用钢的热处理规范>.
淬火的目的是:使钢件获得高的硬度和耐磨性,通过淬火钢件的硬度一般可达HRC60~65,但淬火后钢件内部产生了内应力,使钢件变脆,因此,要经过回火处理加以消除。钢件的淬火处理,在机械制造过程中应用比较普遍,它常用的方法有:
1.单液淬火:将钢件加热到淬火温度,经保温一定时间后,在一种冷却液中冷却,这种热处理方法,称为单液淬火。它适用于形状简单、技术要求不高的碳钢或合金钢,工件直径或厚度大于5~8mm的碳素钢,选用盐水或水中冷却;合金钢选用油冷却。在单液淬火中,水冷容易发生变形和裂纹;油冷容易产生硬度不够或不均的现象。
2.双液淬火:将钢件加热到淬火温度,经保温后,先在水中快速冷却至300~400℃,在移入油中冷却,这种处理方法,称为双液淬火。形状复杂的钢件,常采用此方法。它既能保证钢件的硬度,又能防止变形和裂纹。缺点是操作难度大,不易掌握。
3.火焰表面淬火:用乙炔和氧气混合燃烧的火焰喷射到工件表面,并使其加热到淬火温度,然后立即用水向工件表面喷射,这种处理方法,称为火焰表面淬火。它适用于单件生产、要求表面或局部表面硬度高和耐磨的钢件,缺点是操作难度大。
4.表面感应淬火:将钢件放人感应器内,在中频或高频交流电的作用下产生交变磁场,钢件在磁场作用下产生了同频率的感应电流,使钢件表面迅速加热(2-10s)至淬火温度,立即把水喷射到钢件表面。这种热处理方法,称为表面感应淬火。经表面感应淬火的零件,表面硬而耐磨,而内部有较好的强度和韧性。这种方法适用于中碳钢和中等含碳量的合金钢件。
表面感应淬火根据所采用的电流频率的不同,可分为高频、中频和工频淬火三种。高频淬火电流频率为100~150kHz,淬硬层深1~3mm,它适用于齿轮、花键轴、活塞和其它小型零件的淬火;中频淬火电流频率为500~10000Hz,淬硬层深3—10mm,它适用于曲轴、钢轨、机床导轨、直径较大的轴类和齿轮等;工频淬火电流频率为50Hz,淬硬层一般大于10mm,适用于直径在300mm以上的大型零件的淬火,如冷轧辊等。
二.回火
将淬火后的钢件加热到临界温度以下某一温度性(见表),保温一段时间,然后在空气中或油中冷却的过程,称为回火。回火的目的是:消除钢件淬火时所产生的内应力,使钢件组织趋于稳定;降低淬火中的脆性,增加塑性和韧性。回火是继淬火后进行的热处理工序,也是热处理的最终工序,它对产品最终所需要得到的性能和组织起着决定性的影响。钢淬火后,硬度和强度虽有很大的提高,但塑性、韧性却有明显的降低,这就是淬火脆性。为了取得回火后所要求的机械性能,选择好回火温度是很重要的。根据回火温度的不同,回火可分为低温、中温和高温回火三种。
1.低温回火:将淬火后的钢件加热到150~29℃,并保温一定时间,然后在空气中冷却,称为低温回火。目的在于保持钢件淬火后所得到的高硬度和耐磨性的条件下,降低淬火脆性和内应力。低温回火适用于各种刃具、量具和模具等的处理。
2.中温回火:将淬火后的钢件加热到350~450℃,经保温一段时间,随炉冷却下来。这种处理方法,称中温回火。它的目的是为了使钢件保持一定硬度,从而得到较高的弹性。中温回火适用于弹簧、锻模的处理。
3.高温回火:将淬火后的钢件加热到500~650℃,经保温后冷却下来,称为高温回火。它的目的是完全消除淬火内应力,使工件得到高强度和高韧性。高温回火主要用于要求强度、韧性高的重要结构零件,如传动主轴、曲轴、凸轮、齿轮等。
三.退火
将钢件加热到临界温度以上40~60℃,在此温度下停留一段时间(保温),然后缓慢冷却,这种热处理方法称为退火。碳钢的临界温度是随含碳量多少而变化,一般是750~800℃,有些合金钢是在800~900℃之间。
退火的目的是:降低硬度、提高塑性、改进切削性能、消除内应力,如消除锻压、铸造的内应力,防止加工后的变形、细化晶粒、均匀组织、改进机械性能。上面指出的退火目的,不是所有钢材都能达到的,而只能满足一个或几个目的。
四.正火
将钢件加热到临界温度以上40~60℃,保温一定时间,然后在空气中冷却的热处理方法,称为正火。正火的加热、保温温度都与退火相同,不同的只是冷却速度不一。正火是在空气中冷却,冷却速度快,时间短,操作方便,效率高。
正火的目的是:细化晶粒,均匀组织,提高钢件的机械性能,消除内应力,改善钢件的切削性能。正火常用于碳钢代替退火
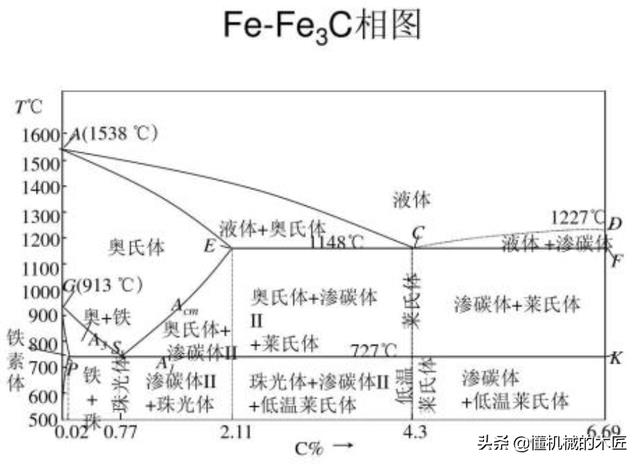
退火与回火的区别在于:(简单地说,退火就是不要硬度,回火还保留一定硬度)。

五.调质
将钢件淬火后,再进行高温回火的热处理方法,称为调质。其目的是细化晶粒,使钢件得到高韧性和足够强度。调质一般是在粗加工后进行的,它适用于各种重要结构零件,特别是交变载荷下工作的传动轴、齿轮、丝杠等精密零件的预先热处理,经过调质后,再进行加工的工艺过程。
调质和高温回火处理方法是相同的,目的都是细化晶粒、均匀组织、消除应力,使钢件得到良好的机械性能,不同的是高温回火是热处理的最终工序,而调质处理则是精加工前的预备工序,是对半成品而作的热处理操作。
六.时效
它是长时间消除零件在制造过程中所产生内应力的工艺方法。时效处理有人工时效和自然时效。
1.人工时效:将钢件(或铸铁件)加热到100—150℃或更低的温度,长时间(5~10h)保温,然后在空气中冷却的方法,称为人工时效。时效处理也是一种低温补充回火,其目的是消除淬火后钢件内部组织的微观应力和机械加工后的残余应力,以达到高精度零件的变形小和尺寸的稳定性。如对量具、铸铁件消除内应力的人工时效处理。
2.自然时效:将粗加工后的零件,长期放置在露天,受自然温度的调节,逐渐消除内应力的处理方法,称为自然时效。如铸件放在露天、丝杠放在海水中、长轴悬吊挂起等。
七.化学热处理
将钢件放到含有某些活性原子,如碳、氮、铬、铝等的化学介质当中,借助高温时原子扩散的能力,使介质中的某些原子渗入到钢件表面层里,达到改变钢的表面层的化学成分,使钢件的表面层具有特殊的性能,这种方法称为钢的化学热处理。它的目的是提高钢件表面的硬度、耐磨性、耐蚀性、耐热和抗疲劳等性能。化学热处理使零件表面层和内部都得到不同的组织和性能,从而大大地提高零件的质量和寿命。常用的方法有
渗碳、渗氮、氰化等。
1.渗碳:渗碳是碳原子渗入钢件表面的过程。渗碳用于低碳钢和低合金钢(0.1~0.25%C)。钢件经过渗碳淬火后具有较高的表面硬度(HRC60—65)和耐磨性,而内部仍保持较高的韧性。一些受冲击的耐磨零件、如轴、齿轮、凸轮、活塞销等都要进行渗碳处理。按渗碳剂的不同,渗碳可分为固体渗碳、液体渗碳和气体渗碳。其方法是将钢件碳处理。按渗碳剂的不同,渗碳可分为固体渗碳、液体渗碳和气体渗碳。其方法是将钢件放人渗碳剂中,加热至930℃左右,经保温使碳原子扩散到钢件表面,钢件表面含碳量可达0.8~1%,渗碳厚度为0.5~2mm。
2.渗氮:渗氮是把氮原子渗入钢件表面的过程。渗氮多于含铝、铬、钼等元素的中碳合金结构钢。渗氮可使钢件表面得到比渗碳更好的硬度和耐磨性,特别是提高了钢件的耐蚀性。渗氮方法是将钢件放人含氮的介质或利用氨气加热分解后的氮气中,加热至500-620℃,保温一定时间,使氮原子扩散到钢件表面,然后随炉温冷却至200℃以下,停止供氮。取出钢件在空气中冷却。由于渗氮温度低,因而渗氮速度缓慢,如得到0.3—0.5mm厚的渗氮层,就要经过20~50h的渗氮过程。

3.氰化:在钢件表面同时渗入碳原子和氮原子的过程叫氰化。它的目的是为了提高钢件表面层的硬度和耐磨性,同时氰化又是提高疲劳强度极限最有效的方法,特别是对中、小型零件,如齿轮,小轴最适宜。氰化还适用于碳钢和合金结构钢,也适合于高
速钢等切削工具。
氰化是将钢件放在熔融的氰盐溶液中加热,在加热过程中,由氰盐[NaCl、KCl、K4Fe(CN)6]氰化分解而形成活性的碳、氮原子,渗入钢件表面。根据加热温度不同,氰化可分为高温氰化(900-950℃)、中温氰化(800—840℃)和低温氰化。氰盐是剧毒物质,因此,要特别防止中毒。
八.发黑
发黑处理是属氧化处理的方法。它的作用是使钢件表面生成一层保护膜,以增强钢件表面防锈和耐蚀能力,同时可使钢件表面光泽美观,对淬火零件还有消除淬火应力的作用。
发黑又叫煮黑,是将钢件放在很浓的碱和氧化剂的溶液(苛性钠和过氧化钠)中加热煮沸,使钢件表面生成一层黑色的Fe3O4薄膜的工艺处理过程。发黑主要用于碳素结构钢和低合金工具钢,发黑层厚度约为0.6—0.8mm。
几种零件的热处理实例
内容介绍>>
齿轮热处理实例
一、工作条件以及材料与热处理要求
1.条件: 低速、轻载又不受冲击
要求: HT200 HT250 HT300 去应力退火
2.条件: 低速(<1m/s)、轻载,如车床溜板齿轮等
要求: 45 调质,HB200-250
3.条件: 低速、中载,如标准系列减速器齿轮
要求: 45 40Cr 40MnB (5042MnVB)调质,HB220-250
4.条件: 低速、重载、无冲击,如机床主轴箱齿轮
要求: 40Cr(42MnVB)淬火 中温回火 HRC40-45
5.条件: 中速、中载,无猛烈冲击,如机床主轴箱齿轮
要求: 40Cr、40MnB、42MnVB 调质或正火,感应加热表面淬火,低温回火,时效,HRC50-55
6.条件: 中速、中载或低速、重载,如车床变速箱中的次要齿轮
要求: 45 高频淬火,350-370℃回火,HRC40-45(无高频设备时,可采用快速加热齿面淬火)
7.条件: 中速、重载
要求: 40Cr、40MnB(40MnVB、42CrMo、40CrMnMo、40CrMnMoVBA)淬火,中温回火,HRC45-50.
8.条件: 高速、轻载或高速、中载,有冲击的小齿轮
要求: 15、20、20Cr、20MnVB渗碳,淬火,低温回火,HRC56-62.38CrAl 38CrMoAl 渗氮,渗氮深度0.5mm,HV900
9.条件: 高速、中载,无猛烈冲击,如机床主轴轮.
要求: 40Cr、40MnB、(40MnVB)高频淬火,HRC50-55.
10.条件: 高速、中载、有冲击、外形复杂和重要齿轮,如汽车变速箱齿
轮(20CrMnTi淬透性较高,过热敏感性小,渗碳速度快,过渡层均匀,渗碳
后直接淬火变形较小,正火后切削加工性良好,低温冲击韧性也较好)
要求: 20Cr、20Mn2B、20MnVB渗碳,淬火,低温回火或渗碳后高频
淬火,HRC56-62.
18CrMnTi、20CrMnTi(锻造→正火→加工齿轮→局部镀同→渗碳、
预冷淬火、低温回火→磨齿→喷丸)渗碳层深度1.2-1.6mm,齿轮硬度
HRC58-60,心部硬度HRC25-35.表面:回火马氏体+残余奥氏体+碳化物.
中心:索氏体+细珠光体
11.条件: 高速、重载、有冲击、模数<5
要求: 20Cr、20Mn2B 渗碳、淬火、低温回火,HRG56-62.
12.条件: 高速、重载、或中载、模数>6,要求高强度、高耐磨性,如立车重要螺旋锥齿轮
要求: 18CrMnTi、20SiMnVB 渗碳、淬火、低温回火,HRC56-62
13.条件: 高速、重载、有冲击、外形复杂的重要齿轮,如高速柴油机、
重型载重汽车,航空发动机等设备上的齿轮.
要求: 12Cr2Ni4A、20Cr2Ni4A、18Cr2Ni4WA、20CrMnMoVBA(锻造→
退火→粗加工→去应力→半精加工→渗碳→退火软化→淬火→冷处理
→低温回火→精磨)渗碳层深度1.2-1.5mm,HRC59-62.
14.条件: 载荷不高的大齿轮,如大型龙门刨齿轮
要求: 50Mn2、50、65Mn 淬火,空冷,HB≤ 241
15.条件: 低速、载荷不大,精密传动齿轮.
要求: 35CrMO 淬火,低温回火,HRC45-50
16.条件: 精密传动、有一定耐磨性大齿轮.
要求: 35CrMo 调质,HB255-302.
17.条件: 要求抗磨蚀性的计量泵齿轮.
要求: 9Cr16Mo3VRE 沉淀硬化
18.条件: 要求高耐磨性的鼓风机齿轮.
要求: 45 调质,尿素盐浴软氮化.
19.条件: 要求耐、保持间隙精度的25L油泵齿轮。
要求: 粉末治金(生产批量要大).
20.条件: 拖拉机后桥齿轮(小模数)、内燃机车变速箱齿轮(m6-m8).
要求: 55DTi或60D(均为低淬透性中碳结构钢)中频淬火,回火,
HRC50-55,或中频加热全部淬火.可获得渗碳合金钢的质量,而工艺简
化,材料便宜.
二、备注:
1.机床齿轮按工作条件可分三组:
(1).低速:转速2m/s,单位压力350-600N/mm^2.
(2).中速:转速2-6m/s,
单位压力100-1000N/mm^2,冲击负荷不大.
(3).高速:转速4-12m/s,弯曲力矩大,单位压力200-700N/mm^2.
2.机床常用齿轮材料及热处理:
(1).45 淬火,高温回火,HB200-250,用于圆周速度<1m/s中等压力,高频
淬火,表面硬度HRC52-58,用于表面硬度要求高、变形小的齿轮.
(2).20Cr渗碳、淬火、低温回火
HRC56-62,用于高速、压力、中等、并有冲击的齿轮.
(3).40Cr 调质,HB220-250,用于圆周速度不大,中等单位压力的齿轮,
淬火,回火,HRC40-50,用于中等圆周速度、冲击负荷不大的齿轮.
(4)除上述条件外,如尚要求热处理时变形小,则用高频淬火、
硬度HRC52-58.
3.汽车、拖拉机齿轮的工作条件比机床齿轮要繁重得多,要求耐磨性、
疲劳强度、心部强度和冲击韧性等方面比机床齿轮高.因此,一般是载
荷重、冲击大,多采用低碳合金钢(除左行列出的牌号以外,
尚有20MnMoB、20SiMnVB、30CrMnTi、30MnTiB、20MnTiB等),
经渗碳、淬火、低温回火处理.拖拉机最终传动齿轮的传动扭矩较大,
齿面单位压较高,密封性不好,砂土、灰土容易钻入,工作条件比较差,常
采用20CrNi3A等渗碳。
4.一般机械齿轮最常用的材料是45和40Cr,其热处理方法选择如下:
(1).整体淬火;强度、硬度(HRC50-55)提高,承载能力增大,但
韧性减小,变形较大,淬火后须磨齿或研齿,只适用于载荷较大、无冲
击的齿轮.应用较少.
(2).调质:由于硬度低,韧性也好不太高,不能用于大冲击载荷下工作,
只适用于低速、中载的齿轮,一对调质齿轮的小齿轮面硬度要比大齿
面硬度高出HB25-40.
(3).正火:受条件限制不适合淬火和调质的大直径齿轮用.
(4).表面淬火:45、40Cr高频淬火机床齿轮广泛采用,直径较大用火
焰表面淬火.但对受较大冲击载荷的齿轮因其韧性不够,须用低碳钢
(有冲击、中小载荷)或低碳合金钢(有冲击、大载)渗碳.
轴类热处理实例
一、 工作条件以及材料与热处理要求
1.条件:
在滑动轴承中工作,υ周< 2m/S,要求表面有较高在硬度的小轴,心轴.
如机床走刀箱、变速箱小轴..
要求: 45、50,形状复杂的轴用40Cr、42MnVB.调质,HB228-255,轴
颈处高频淬火,HRC45-50
2.条件: 在滑动轴承中工作,
υ周< 3m/S,要求硬度高、变形小,如中间带传动装置的小轴
要求: 40Cr、42MnVB 调质,HB228-255,轴颈高频淬火,HRC45-50.
3.条件: υ周≥ 2m/S,大的弯曲载荷及摩擦条件下的小轴,如机床变速箱小轴。
要求: 15、20、20Cr、20MnVB 渗碳,淬火,低温回火,HRC58-62.
4.条件: 高载荷的花键轴,要求高强度和耐磨,变形小.
要求: 45 高频加热,水冷,低温回火,HRC52-58.
5.条件: 在滚动或滑动轴承中工作,轻或中等负荷,低速,精度要求不高,
稍有冲击,疲劳负荷可忽咯的主轴,或在滚动轴承中工作,轻载,
υ<1m/s的次要花键轴.
要求: 45 调质,HB225-255(如一般简易机床主轴)
6.条件: 在滚动或滑动轴承中工作,轻或中等负荷转速稍高.
ρυ≤150N.m/(cm^2.s),精度要求高,冲击,疲劳负荷不大.
要求: 45 正火或调质,HB228-255,轴颈或装配部位表面淬火,HRC45-50.
7.条件: 在滑动轴承中工作,中或重载,转速较高ρυ≤400N.m/cm^2.S,
精度较高,冲击、疲劳负荷不大.
要求: 40Cr 调质,HB228-255或HB248-286,轴颈表面淬火,HRC≥54,
装配部位表面淬火HRC≥45.
8.条件: 其他同上,但转速与精度要求比上例高,如磨床砂轮主轴.
要求: 45Cr、42CrMo其他同上,表面硬度HRC≥56.
9.条件: 在滑动或滚动轴承中工作,中载、高速、心部强度要求不高,精
度不太高,冲击不大,但疲劳应力较大,如磨床,重型齿轮铣床等主轴.
要求: 20Cr 渗 碳,淬火,低温回火,HRC58-62.
10.条件: 在滑动或滚动轴承中工作,重载,高速(ρυ≤400N.m/cm^2.s)
冲击,疲劳应力都很高.
要求: 18CrMnTi 20Mn2B 20CrMnMoVA 渗碳 淬火 低温回
火HRC≥59.
11.条件: 在滑动轴承中回转,重载,高速,精度很高≤0.003mm,很高疲
劳应力,如高精度磨床镗床主轴.
要求: 38CrAlMoA 调质 硬度HB248-286:轴颈渗氮,硬度HV≥900.
12.条件: 电动机轴,主要受扭.
要求: 35及45 正火或正火并回火,HB187及HB217.
13.条件: 水泵轴,要求足够抗扭强度和防腐蚀.
要求: 3Cr13及4Cr13 1000-1050℃油液,硬度分别为HRC42及HRC48.
14.条件: C616-416车床主轴,45号钢
(1)承受交变弯曲应力,扭转应力,有时还受冲击载荷.
(2)主轴大端内锥孔和锥度处圆,经常与卡盘,顶针有相对摩擦.
(3)花键部分经常磕碰或相对滑动(4)在滚动轴承中动转,中速,中载.
要求:
(1)整体调质后硬度HB200-230,金相组织为索氏体 .
(2)内锥孔和外圆锥面处硬度HRC45-50,表面3-5mm风金相组织为屈氏体和少量回火马氏体.
(3)花键部分硬度HRC48-53,金相组织同上
15.条件: 跃进-130型载重(2.5吨)
汽车半轴
承受冲击、反复弯曲疲劳和扭转,主要瞬时超载而扭断,要求有足够
的抗弯、抗扭、抗疲劳强度和较好的韧性
要求: 40Cr 35CrMo 42CrMo40CrMnMo 40Cr 调质后中频表面
淬火,表面硬度HRC≥52,深度4-6mm,静扭矩6900N.m,疲劳≥30万次,估
计寿命≥30万km
金相组织: 索氏体+屈氏体(原用调质加高频淬火寿命仅为4万km)
二、备注:
1.(1-8)备注:
主轴与轴类材料与热处理选择必须考虑受力大小、轴承类型和主轴
形状及可能引起的热处理缺陷.在滚动轴承或轴颈上有轴套在滑
动轴承中回转,轴颈不需特别高的硬度,可用45、45Cr,调质,HB220-250,
50Mn,正火或调质HRC28-35.在滑动轴承中工作的轴承应淬硬,可用15、
20Cr,渗碳,淬火,回火到硬度HRC56-62,轴颈处渗碳深度为
0.8-1mm.直径或重量较大的主轴渗碳较困难,要求变形较小时,可用45
或40Cr在轴颈处作高频淬火.高精度和高转速(>2000r/min)机
床主轴尚须采用氮化钢进行渗氮处理,得到更高硬度.在重载下工作的
大断面主轴,可用20SiMnVB或20CrMnMoVBA,渗碳,淬火,回火,HRC56-62.
2.(9)备注:
内心强度不高,受力易扭曲变形表面硬度高,宜作高速低负荷主轴.热处理变形较大.
3.(10)备注:
心部有较高的σb及αk值,表面有高的硬度及耐磨性.有热处理变形.
4.(11)备注:
很高的心部强度,表面硬度极高,耐磨和变形量小.
5.(12)备注:
860-880℃正火
6.(13)备注:
或1Cr13 1100℃油淬,350-400℃回火,HRC56-62.
7.(14)备注:
加工和热处理步骤:
下料→锻造→正火→粗加工→调质→半精车外圆,钻中心孔,精车外
圆,铣键槽→锥孔及外圆锥局部淬火,260-300℃回火→车各空刀槽,粗磨
外圆,滚铣花键槽→花键高频淬火,240-260℃加火→精磨.
曲类热处理实例
一、 工作条件:
1.内燃机曲轴: 承受周期性变化的气体压力,曲柄连杆机械的惯性力,
扭转和弯曲应力以及冲击力等.此外在高速内燃机中还存在扭转振动,
会造成很大应力.
2.要求有高强度及一定的冲击韧性、弯曲、扭转、疲劳强度,和轴颈处高
的耐磨性.
二、材料与热处理实例:
1.低速内燃机,采用正火状态的碳钢、球墨铸铁.
2.中速内燃机,采用调质碳钢或合金钢,如45、40Cr、45Mn2、50Mn2等及
球墨铸铁。
3.高速内燃机,采用高强度合金钢,如35CrMo、42CrMo、18Cr2Ni4WA等.
4.以110型柴油机曲轴为例: QT60-2正火,中频淬火,σb≥650N/mm^2,
αk>15N.m/mm^2,(试样20×20×110mm),轴体HB240-300,轴颈HRC≥55,
珠光体数量:试棒≥75%,曲轴≥70%.
蜗杆蜗轮热处理实例
一、 工作条件以及材料与热处理要求
1.条件: 负荷不大,断面较小的蜗杆
要求: 45 调质,HB220-250
2.条件: 有精度要求(螺纹磨出)而速度<2m/s.
要求: 45 淬火,回火,HRC45-50
3.条件: 滑动速度较高,负荷较轻的中小尺寸蜗杆
要求: 15 渗碳,淬火,低温回火,HRC56-62
4.条件: 滑动速度>2m/s
(最大7-8m/s);精度要求很高,表面粗糙度为0.4的蜗杆,如立车中的主要蜗杆
要求: 20Cr 20Mn2B 900-950℃渗碳,800-820℃油淬,180-200℃低温回火,HRC56-62
5.条件: 要求高耐磨性、高精度及尺寸大的蜗杆
要求: 18CrMnTi、20SiMnVB处理同上,HRC56-62
6.条件: 要求足够耐磨性和硬度的蜗杆
要求: 40Cr、42SiMn、45MnB 油淬,回火,HRC5-50
7.条件: 中载、要求高精度并与青铜蜗轮配合使用(热处理后再加工丝扣)之蜗杆
要求: 35CrMo调质, HB255-303(850-870℃油淬,600-650回火)
8.条件: 要求高硬度和最小变形的蜗杆
要求: 38CrMoAlA、38CrAlA正火或调质后氮,硬度HV>850
9.条件: 汽车转向蜗杆
要求: 35Cr 815℃氰化、200℃回火,渗层深度0.35-0.40mm,表面锉力硬度,心部硬度<HRC35
二、备注:
1.蜗轮材料与热处理:
(1)圆周速度≥3m/s的重要传动;锡磷青铜QSn10-1,QSn-10
(2)圆周速度≤4m/s Al9-4
(3)圆周速度≤2m/s,效率要求不高:铸铁防止蜗轮变形一般进行时效处理
2.蜗杆材料与热处理:
(1)高速重载:15、20Cr 渗碳淬火,HRC56-62;40、45、40Cr淬火,
HRC45-50
(2)不太重要或低载;40 45调质
弹簧热处理实例
一、 工作条件以及材料与热处理要求
1.条件: 形状简单,断面较小,受力不大的弹簧
要求: 65 785-815℃油淬,300℃400℃、500℃。600℃回火,相应的
硬度HB512、HB430、HB369,75,780-800℃油或水淬,400-420℃回火,
HRC42-48.
2.条件: 中等负荷的大型弹簧
要求: 60Si2MnA 65Mn 870℃油淬,460℃回火,HRC40-45(农机座位弹簧
65Mn 淬火 回火 HB280-370)
3.条件: 重负荷、高弹簧、高疲劳极限的大形板簧和螺旋弹簧
要求: 50CrVA、60SiMnA 860℃油淬,475℃回火,HRC40-45
4.条件: 在多次交变负荷下工作的直径8-10mm的卷簧
要求: 50CrMnA 840-870℃油淬,450-480℃回火,HB387-418
5.条件: 机车、车辆、煤水车或板弹簧
要求: 55SiMn、60Si2Mn
HRC39-45(hb363-432)(解放牌汽车板簧:55Si2Mn HB363-441)
6.条件: 车辆及缓冲器螺旋弹簧、汽车张紧弹簧
要求: 55Si2Mn、60Si2Mn、60Si2CrA 淬火,回火,HRC40-47
或HB370-441
7.条件: 柴油泵柱塞弹簧、喷油嘴弹簧、农用柴油机气阀弹簧及中型、
重型汽车的气门弹簧和板弹簧
要求: 50CrVA 淬火,回火,HRC40-47
8.条件: 在高温蒸汽下工作的卷簧和扁簧,自来水管道弹簧和耐海水浸
蚀的弹簧,Φ10-25mm
要求: 3Cr13 HRC39-46 4Cr13 HRC48-50 HRC48-49 HRC47-49
HRC37-40 HRC31-35 HRC33-47
9.条件: 在酸碱介质下工作的弹簧
要求: 2Cr18Ni9 1100-1150℃水淬,绕卷后消除应力,400℃回火60min,HB160-200
10.条件: 弹性挡圈δ4,Φ85
要求: 60Si2 400℃预热,860℃油淬,430℃回火空冷,HRC40-45.
二、备注
1.弹簧热处理一般要求淬透,晶粒细,残余奥氏体少.脱碳层深度每边应符
合:<Φ6mm的钢丝或钢板,应<1.5%直径或厚度;>Φ6mm的钢丝钢板,应
<1.0%直径或厚度.
2.大型弹簧在热状态加工成型随即淬火-回火,中型弹簧在冷态加工成
型(原材料要求球化组织或大部分球化),再淬火-回火.小型弹簧用冷轧
钢带、冷拉钢丝等冷态加工成型后,低温回火
3.处理后可经喷丸处理:
40-50N/cm^2的压缩空气或离心机70m/s的线速度,将Φ0.3-0.5mm(对
于小零件、汽门弹簧、齿轮等)、Φ0.6-0.8mm(对板簧、曲轴、半轴
等)铸铁丸或淬硬钢丸喷射到弹簧表面,强化表层,疲劳循环次数可提高
8-13倍,寿命可提高2-2.5倍以上
机床丝杠热处理实例
一、 工作条件以及材料与热处理要求
1.条件: ≤级精度,受力不大,如各类机床传动丝杠
要求: 45、45Mn2 一般丝杠可用正火,≥HB170;受力较大的丝杠,调质,
HB250;方头,轴颈局部淬硬HRC42
2.条件: ≥7级精度,受力不大,轴颈方头等处均不需淬硬,如车床走刀丝杠
要求: 45Mn易切削钢和45 热轧后σb=600-750N/mm^2,除应力后HB170-207,
金相组织:片状珠光体+铁素体
3.条件: 7-8级精度,受力较大,如各类大型镗床、立车、龙门铣和刨床等
的走刀和传动丝杠
要求: 40Cr、42MnVB、(65Mn)调质HB220-250,σb≥850N/mm^2;方头、
轴颈局部淬硬HRC42,金相组织:均匀索氏体
4.条件: 8级精度,中等负荷,要求耐磨,如平面磨床,砂轮架升降丝杠与滚
动螺线啮合
要求: 40Cr、42MnVB 调质HB250,中频表淬HRC54,, 调质后基体组织:
均匀索氏体+细状珠光体
5.条件: ≥6级精度,要求具有一定耐磨性,尺寸稳定性,较高强度和较
好的切削加工性,如丝杠车床,齿轮机床、坐标镗床等的丝杠
要求: T10、T10A、T12、T12A球化退火,HB163-193,球化等级3-5级,
网状碳化物≤3级,调质HB201-229,金相组织;细粒状珠光体
6.条件: ≥6级精度,要求抗腐蚀、较高的抗疲劳性和尺寸稳定性.如
样板镗床或其他特种机床精密丝杠.
要求: 38CrMoAlA 调质HB280,渗氮HV850,调质后基体组织,均匀
的索氏体,渗氮前表面应无脱碳层
7.条件: ≥6级精度,要求耐耐磨、尺寸稳定,但负荷不大,如螺纹磨
床、齿轮磨床等高精度传动丝杠(硬丝杠)
要求: 9Mn2V(直径≤60mm)、CrWMn(直径>60mm),球化退火后,
球状珠光体1.5-4级,网状碳化物≤3级,硬度≤HB227,淬火硬度
HRC56+0.5,金相组织,回火马氏体无残余奥氏体存在
8.条件: ≥6级精度,受点负荷的,如螺纹或齿轮磨床、各类数控机床的滚珠丝杠
要求: GCr15(直径≤70mm0)、GCr15SiMn(直径>80mm)球化退火
后,球状珠光体1.5-4级,网状碳化物≤3级,HRC60-62,金相组织;回火马氏体
二、备注:
1.丝杠的选材与处理;
(1)丝杠的主要损坏形式,一般丝杠(≤7级精度)为弯曲及磨损;≥6级
精度丝杠为磨损及精度丧失或螺距尺寸变化
(2)丝杠材料应具有足够的力学性能,优良的加工性能,不易产生磨裂,能
得到低的表面粗糙度和低的加工残余内应力,热处理后具有较高硬度,
最少淬火变形和残余奥氏体常用于不要求整体热处理至高硬
度的材料,有45、40Mn、40Cr、T10、T10A、T12A、T12等.淬硬丝杠材料,
有GCr15、9Mn2V、CrWMn、GCr15、SiMn、38CrMOAlA等
(3)热处理:
一般丝杠:正火(45钢)或退火(40Cr),除应力处理和低温时效,调
质和轴颈、方头高频淬火与回火精密不淬硬丝杠: 除应力处理低
温时效,球化退火,调质球化,如遇原始组织不良等,还需先经900℃(T10、
T10A)-950℃(T12、T12A)正火处理后再球化退火,或直接调质球化
精密淬硬丝杠: 退火或高温正火后退火,除应力处理,淬火和低温时效
2.考虑热加工工艺性,丝杠结构设计注意事项:
(1)结构尽可能简单,避免各中沟槽、突变的台阶、锐角等,尤其是氮化
丝杠更应避免一切棱角
(2)丝杠一端应留空刀槽.凸起台阶或吊装螺钉孔,便于冷热加工中吊挂用
(3)不应有较大的凸阶,以免除局部镦粗的锻造工序.
3.滚珠丝杠副的材料与热处理:
(1)材料选用;滚珠丝杠;L≤2m、Φ40-80mm变形小、耐磨性高的6-8
级丝杠用CrWMn整体淬火
汽车、拖拉机、配件热处理实例
一、 工作条件以及材料与热处理要求1.条件; 推土机用销套: 承受重载、
大冲击和严重磨损
要求: 20Mn、25MbTiB 渗碳,二次淬火,低温回火,HRC59,渗碳层深2.6-3.8mm
2.条件: 推土机履带板: 承受重载、大冲击和严重磨损
要求: 40Mn2Si 调质,履带齿中频淬火或整体淬火,中频回火,距齿顶
淬硬层深30mm
3.条件: 推土机链轨节 承受重载、大冲击和严重磨损
要求: 50Mn、40MnVB 工作面中频淬火,回火,淬硬层深6-10.4mm
4.条件: 推土机支承轮
要求: 55SiMn、45MnB 滚动面中频淬火,回火,淬硬层深6.2-9.1mm
5.条件: 推土机驱动轮
要求: 45SiMn 轮齿中频淬火,淬硬层深7.5mm
6.条件: 活塞销: 受冲击性的交变弯曲剪切应力、磨损大.主要是磨损、断裂
要求: 20Cr 渗碳,淬火,低温回火,HRC59(双面)
7.条件: 刮板弹簧 转子发动机用,要求在高温下保持弹抗疲劳性能
要求: 718耐热合金 1050℃固溶处理,冷变形,690℃真空时效,8h
(或620℃下8小时,500℃下松驰8小时)
8.条件: 受冲击性迅速变化着的拉应力和装配时的预应力作用,在发动
机运转中,连杆螺栓折断会引起严重事故,要求有足够的强度、冲击韧性
和杭疲劳能力
要求: 40Cr调质,HRC31,不允许有块状铁素体:下料→锻造→退火或正
火→加工→调质(回火水冷防止第二类火脆性→加工→装配
二、备注
1.<Φ50mm、耐磨性高、承受较大压力的6-8级,丝杠用GCr15整体或中频淬火
2.>Φ50mm、耐磨性高、6-8级丝杠用GCr15SiMn整体或中频淬火
3.≤Φ40mm、L≤2mm、变形小、耐磨性高的6-8级丝杠用9Mn2V、整淬,冰冷处理.
4.有防蚀要求特殊用途的丝杠用9Cr18,中频加热表面淬火.
矿山机械及其他零件
工作条件以及材料与热处理要求
1.条件: 牙轮钻头 主要是磨坏
要求: 20CrMo渗碳,淬火,低温回火,HRC61
2.条件: 输煤机溜槽(原用16Mn钢板,未处理,仅用3-6个月)
要求: 16Mn钢板中频淬火(寿命可提高一倍)
3.条件: 铁锹(原用低碳钢固体渗碳淬火,回火,质量很差)
要求: 低碳钢 淬火,低温回火,得低碳马氏体,质量大大提高
4.条件: 石油钻井提升系统用吊环(原用35钢)、吊卡(原用40CrNi或
35CrMo) 正火或调质,质量差,笨重.
要求: 20SiMn2MoVA淬火,低温回火,得低碳马氏体,质量大大提高
5.条件: 石油射孔枪 承受火药爆炸大能量高温瞬间冲击,类似于枪
炮.主要是过量塑性变形引起开裂
要求: 20SiMn2MoVA淬火,低温回火,得低碳马氏体,σb=1610N/mm^2,
αk=80N.m/mm^2
6.条件: 煤矿用圆环牵引链,要求高抗拉强度和抗疲劳,主要是疲劳断裂
及加工时冷弯开裂.
要求: 20MnV、25Mn2V 弯曲后闪光对焊,正火,880℃淬火,250℃回火
获得代碳马氏,预变形强化.
σb≥850N/mm^2,σs≥650N/mm^2,αk≥100N.m/mm^2
7.条件: 凿岩机钎尾 受高频冲击与矿石摩擦严重,要求多冲杭力大,耐
疲劳,主要是断裂与凹陷
要求: 30SiMnMoV、32SiMnMoV HRC56,渗碳淬火→650℃回火,二次
加热260-280℃等温淬火→螺纺部分滚压强化
8.条件: 凿岩机钎杆 受高频冲击与矿石摩擦严重,要求多冲抗力大,
耐疲劳和磨损,主要是折断与磨损
要求: 30SiMnMoV HRC59,900-920℃下用 "603"液体渗碳2h,
至880℃空冷25-30s,油冷,230回火3h
9.条件: 中压叶片油泵定子 要求槽口耐磨和抗弯曲性能好.主要是
槽口磨损、折断
要求: 38CrMoAl 渗氮,HV900 调质→粗车→去应力→精车→渗氮
10.条件: 机床导轨 要求轨面耐磨和保持高精度.主要是磨损和精度丧失
要求: HT200 HT300 表面电接触加热淬火,HRC56
11.条件: 化工用阀门、管件等腐蚀大的零件,要求抗腐蚀性高
要求: 普通碳素钢渗硅
12.条件: 锅炉排污阀 主要是锈蚀,要求抗腐蚀性好
要求; 45 渗硼
13.条件:
(1)1t蒸汽锤杆Φ120,L=2345mm 10t模锻锤锤杆
(2)受较剧烈多次冲击和疲劳应力.主要是疲劳断裂
要求;
(1)45Cr 850℃淬火,10%盐冷,450℃回火,HRC45
(2)35CrMo 860-870℃水淬,450-480℃回火,HRC40
14.条件: 电耙耙斗、电铲铲斗的齿部:冲击大、摩擦严重.主要是磨坯.
要求; ZGMn13 水韧处理,HB180-220(工作时在冲击和压力下HB450-550)
15.条件: Φ840及Φ650mm的矿车轮
要求: ZG55、ZGCrMnSi HB280-330
二、备注:
1.L≤1m、变形小、耐磨性高的6-7级丝杠用20CrMoA,渗碳,淬火
2.L≤2.5mm、变形小、耐磨性高、6-7级丝杠用40CrMoA,高频或中频淬火.
3.7-8级的丝杠用55、50Mn,高频淬火.
4.L≤2.5mm、变形小、耐磨性高、5-6级精度的丝杠,38CrMoAlA或
38CrWVAl,氮化.
5.螺母 GCr15、CrWMn、9CrSi,也有用18CrMn Ti 12CrNiA等渗
碳钢的
6.硬度要求 推荐HRC60±2,螺母取上限,当丝杠L≥1.5<,或精度为
5、6级时,硬度可低一些,但须≥HRC56
7.采用表面热处理的淬透层深度,磨削后,应为:中频处理>2mm;
高频渗碳处理>1mm;氮化处理>0.4mm,7级精度以上的丝杠应作消除残余庆力的稳定处理.
相关参考
常用钢材热处理方法一.淬火将钢件加热到临界温度以上40~60℃,保温一定时间,急剧冷却的热处理方法,称为淬火。常用急剧冷却的介质有油、水和盐水溶液。淬火的加温温度、冷却介质的热处理规范,见表<常用钢的热处理...
常用钢材热处理方法一.淬火将钢件加热到临界温度以上40~60℃,保温一定时间,急剧冷却的热处理方法,称为淬火。常用急剧冷却的介质有油、水和盐水溶液。淬火的加温温度、冷却介质的热处理规范,见表<常用钢的热处理...
常用钢材热处理方法一.淬火将钢件加热到临界温度以上40~60℃,保温一定时间,急剧冷却的热处理方法,称为淬火。常用急剧冷却的介质有油、水和盐水溶液。淬火的加温温度、冷却介质的热处理规范,见表<常用钢的热处理...
常用钢材热处理方法一.淬火将钢件加热到临界温度以上40~60℃,保温一定时间,急剧冷却的热处理方法,称为淬火。常用急剧冷却的介质有油、水和盐水溶液。淬火的加温温度、冷却介质的热处理规范,见表<常用钢的热处理...
常用钢材热处理方法一.淬火将钢件加热到临界温度以上40~60℃,保温一定时间,急剧冷却的热处理方法,称为淬火。常用急剧冷却的介质有油、水和盐水溶液。淬火的加温温度、冷却介质的热处理规范,见表<常用钢的热处理...
常用钢材热处理方法一.淬火将钢件加热到临界温度以上40~60℃,保温一定时间,急剧冷却的热处理方法,称为淬火。常用急剧冷却的介质有油、水和盐水溶液。淬火的加温温度、冷却介质的热处理规范,见表<常用钢的热处理...
常用钢材热处理方法一.淬火将钢件加热到临界温度以上40~60℃,保温一定时间,急剧冷却的热处理方法,称为淬火。常用急剧冷却的介质有油、水和盐水溶液。淬火的加温温度、冷却介质的热处理规范,见表<常用钢的热处理...
退火热处理过程:将钢件加热到一定温度,保温一定时间,然后缓慢冷却到室温热处理目的:①降低钢的硬度,提高塑性,以利于切削加工及冷变形加工②细化晶粒,均匀钢的组织,改善钢的性能及为以后的热处理作准备③消除...
退火热处理过程:将钢件加热到一定温度,保温一定时间,然后缓慢冷却到室温热处理目的:①降低钢的硬度,提高塑性,以利于切削加工及冷变形加工②细化晶粒,均匀钢的组织,改善钢的性能及为以后的热处理作准备③消除...
退火热处理过程:将钢件加热到一定温度,保温一定时间,然后缓慢冷却到室温热处理目的:①降低钢的硬度,提高塑性,以利于切削加工及冷变形加工②细化晶粒,均匀钢的组织,改善钢的性能及为以后的热处理作准备③消除...