热压罐质量(国外空天往返飞行器用先进树脂基复合材料研究与应用进展)
Posted
篇首语:等不到的晚安就别等了,挤不进的世界就别挤了。本文由小常识网(cha138.com)小编为大家整理,主要介绍了热压罐质量(国外空天往返飞行器用先进树脂基复合材料研究与应用进展)相关的知识,希望对你有一定的参考价值。
热压罐质量(国外空天往返飞行器用先进树脂基复合材料研究与应用进展)
随着航天航空技术的不断发展,具备运送有效载荷、在轨和再入飞行、安全水平着陆滑跑返回地面等融合特点的新型可重复使用飞行器成为研究热点。相比单次使用的运载火箭,空天往返飞行器是一种新型可重复使用的运载器,具有发射周期短、发射成本低、超强机动、灵活进出空间等鲜明特点。可重复使用的飞行器结构设计、材料评估、制造工艺及试验验证等先进技术,是新型空天往返飞行器研制的关键,也是航空航天技术的融合发展方向。
先进树脂基复合材料具有高比强度、高比刚度、抗疲劳性能好及多功能集成等特点,在航空、航天、电子等领域的应用越来越广泛,已经发展成为一类可设计的重要结构材料。在新型空天飞行器结构系统上,由于树脂基复合材料可设计性强、减重效果显著,应用部位由次承力结构向主承力结构逐步增加。此外,复合材料可实现复杂机体结构整体制造,减少连接和装配工作,降低结构件制造成本,提高结构件制造效率。
欧美等国家自上世纪50年代开始,竞相开展这类新型空天飞行器的基础理论、工程研制及飞行试验。以美国国家航空航天局(NASA)为代表的科研机构,系统研究了空天往返飞行器的轻量化结构设计与制造,特别是先进复合材料结构设计、制造及试验技术,并将突破的关键技术用于机体结构的进一步优化设计和制造,推动可重复使用空天往返飞行器结构系统的升级发展。我国在这方面研究起步较晚,正在全面研究飞行器结构设计及制造技术,特别是复合材料结构及制造工艺;目前取得了不错的技术进展,但与国外相比还有较大差距。
本文系统总结了国外空天往返飞行器用先进树脂基复合材料种类、性能及典型结构制造工艺,然后介绍了世界主要国家空天往返飞行器的复合材料结构研制应用进展情况,包括美国X系列飞行器、日本H-Ⅱ轨道验证飞行器(HOPE-X)的复合材料应用情况,最后介绍了飞行器复合材料结构的技术发展趋势。
一、国外空天往返飞行器用先进树脂基复合材料
空天往返飞行器的服役环境比大气层内航空飞机更加苛刻,力热耦合作用会加剧结构和材料的微形变扩展,甚至引发结构失效。飞行器结构材料必须具备密度低,弹性模量高的特性,满足耐高低温交变、辐照、原子氧等太空环境要求及真空质损、可凝挥发物等真空逸气要求;还必须满足耐湿热老化、耐腐蚀、耐损伤疲劳等性能要求。
目前,空天飞行器结构材料主要有金属材料和复合材料两大类。飞行器结构上应用的结构复合材料包括碳纤维复合材料、玻璃纤维复合材料和金属基复合材料,其中纤维增强树脂基复合材料的应用最为广泛。
国外报道中提到的空天飞行器用复合材料,大多数为碳纤维增强树脂基复合材料(CFRP),部分典型复合材料牌号、玻璃化转变温度、材料力学性能等材料体系信息如表1所示。可见,国外空天往返飞行器用先进树脂基复合材料的增强体包括碳纤维、玻璃纤维,碳纤维是主要增强材料;树脂基体包括酚醛树脂、环氧树脂、双马来酰亚胺树脂及聚酰亚胺树脂等常用热固性树脂,环氧树脂和双马来酰亚胺树脂是机体结构制造用复合材料的主要树脂基体。
表 1 国外空天往返飞行器用典型树脂基复合材料信息
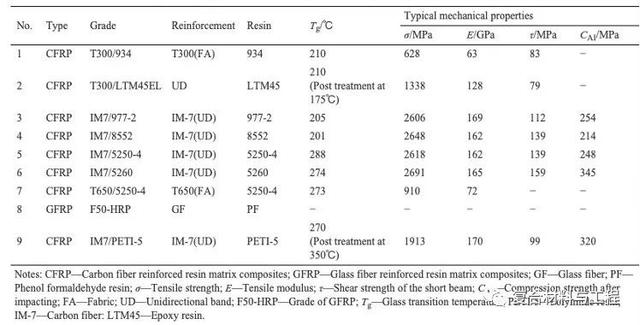
T300、T650碳纤维是日本Toray公司生产的聚丙烯腈(PAN)基碳纤维,T300碳纤维的拉伸强度为3 655 MPa,拉伸模量228 GPa,T650碳纤维的拉伸强度为4 482 MPa,拉伸模量241 GPa。IM7碳纤维为美国Hexcel公司生产的标准中模碳纤维,拉伸强度为5 309 MPa,拉伸模量为289 GPa;该纤维力学性能与Toray公司生产的T800碳纤维相当,是目前报道航空飞行器、空天飞行器轻质复合材料结构制造常用的增强相材料。
934环氧树脂是美国Fiberite公司生产的180℃高温固化树脂,具有高流动性和良好耐湿热性能,满足NASA对复合材料真空逸气要求。LTM45环氧树脂是美国ACG公司研制的低温固化树脂,可在60℃固化,175~180℃后固化处理,长期使用温度为120℃;其复合材料制备成本低,适用于大尺寸、形状复杂的复合材料构件研制生产。
977-2环氧树脂是美国Cytec公司生产的180℃高温固化树脂,是一款典型的高韧性树脂,具有良好的耐高低温(−196~160℃)性能,在航空航天领域应用广泛。8552环氧树脂是美国Hexcel公司生产的低流动性增韧改进环氧树脂,具有高韧性和高损伤容限。
美国Narmco公司设计开发出多种商品化的共聚改性双马来酰亚胺树脂,5250-3、5250-4高韧性双马来酰亚胺树脂是典型代表;5250-4双马来酰亚胺树脂是一种耐湿热、抗冲击、耐高温树脂,拉伸强度达到68.9 MPa,断裂伸长率达到2.7%,与AS-4碳纤维和IM-7碳纤维搭配的复合材料在F-22战斗机外蒙皮、框梁及骨架等结构件上大量应用。Cytec公司并购Narmco公司后开发出的5260双马来酰亚胺树脂,具有近似5250-4树脂的使用温度,又比5250-4树脂高出50%的抗损伤能力;其复合材料CAI值为345 MPa,最高使用温度达177℃。
Cytec公司之后开发的5270双马来酰亚胺树脂具有良好耐高温性能,高温状态性能已接近聚酰亚胺PMR-15;其复合材料湿热性能优于5250-4,连续工作温度达250℃。IM-7/5250-4、IM-7/5260系列碳纤维增强双马来酰亚胺树脂复合材料的耐高温性能、冲击后压缩等性能良好,可满足飞行器机身结构对结构材料韧性和抗冲击性的要求。
机体结构承受温度每提高28℃,可使热防护层厚度减少5.08~6.35 mm,因此耐高温复合材料的研制应用显得尤为必要。PETI-5聚酰亚胺树脂是美国NASA兰利研究中心研制的耐高温树脂,具有良好的热稳定性及力学性能;其耐温等级高于双马来酰亚胺树脂,可以减少构件外层热防护系统的用量,从而减少整机质量,保存结构余量。测试IM7/5250-4和IM7/PETI-5两种复合材料力学性能,结果表明:在−54~177℃温度范围内IM7/5250-4复合材料力学性能比IM7/PETI-5略微有优势;IM7/PETI-5准各向同性复合材料层压板的开孔拉伸强度和开孔压缩强度优于IM7/5250-4。IM7/PETI-5复合材料力学强度在204℃开始出现下降,但力学保持率相对较好;一般情况下飞行器在232℃温度附近的载荷很低,因此IM7/PETI-5复合材料在232℃温度下的剩余强度满足设计要求。
综上,空天往返飞行器结构用先进树脂基复合材料选材考虑树脂基体因素更多,基体性能决定了复合材料主要性能的上限。如图1~2所示,随着飞行器结构性能要求的不断提高,先进复合材料的树脂基体对高韧性、高耐温性能的需求越来越高。环氧树脂从5208、3501发展至977、3900、LTM45系列,树脂韧性不断提高;这些树脂都是采用热压罐固化和真空袋固化工艺,从2000年开始逐渐研发出电子束固化、非热压罐固化及树脂膜熔渗(RFI)工艺用环氧树脂体系。复合材料的应用从DC10、737等飞行器的承力结构逐渐增加至B-2、B777等大型飞行器的承力结构,应用部位也逐渐增加;并在民用和军用飞机、航空发动机冷结构上应用逐渐增加。
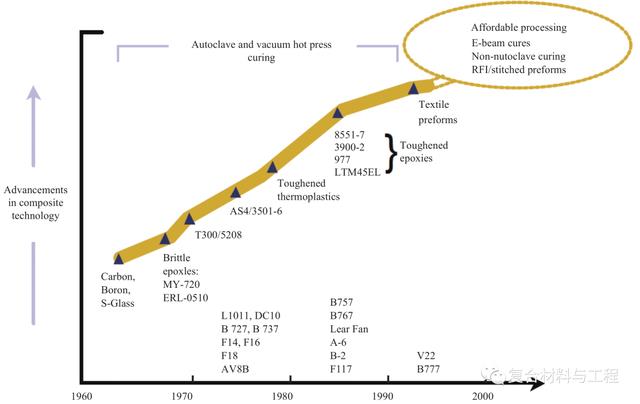
图 1 树脂基复合材料的树脂基体发展演变:环氧树脂
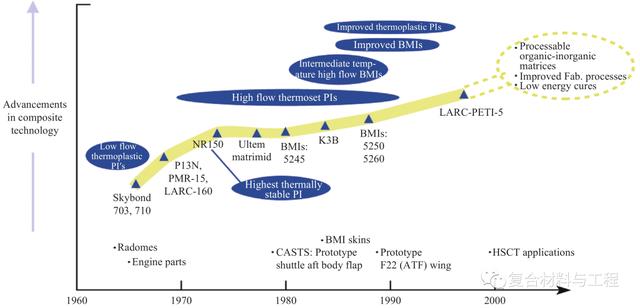
图 2 树脂基复合材料的树脂基体发展演变:耐中温和高温树脂
双马来酰亚胺树脂由5245发展至5250、5260系列,树脂韧性、流动性等性能得到明显的优化提高;聚酰亚胺树脂由PMR-15、LARC-160发展至LARC-PETI-5,从低流动性热塑聚酰胺发展到高流动性热固性聚酰亚胺及进一步的改性聚酰亚胺树脂及其复合材料耐高温性能得到提高,综合力学性能也有所改善。耐高温树脂材料的发展也更加关注工艺性、低能耗固化工艺及优化的制造工艺等技术方面;耐高温复合材料应用由雷达天线罩、航空发动机零件发展到飞机体襟翼、F-22战斗机机翼等领域,拓展应用至高速民用飞行器构件上。
近年来,在高韧性和高抗冲击损伤容限(冲击强度≥315 MPa)复合材料研制及性能研究方面取得持续的技术突破。高韧性的M91、X850环氧树脂,兼具耐湿热与韧性的3960环氧树脂,耐超低温环氧树脂,耐高温F655-2、5270、5280双马来酰亚胺树脂,均与高强碳纤维具有良好的匹配性,且这些改性树脂基体进一步提高了复合材料韧性和耐湿热性,可为新一代高性能空天往返飞行器结构的研制提供坚实的材料技术支撑。
空天飞行器机体结构材料根据构件尺寸、使用温度(150~400℃范围)、耐疲劳性能、损伤容限等综合要求而匹配;选用材料经过综合试验考核验证,材料相对成熟,性能稳定。高韧性高损伤容限环氧树脂复合材料、耐高温增韧双马来酰亚胺树脂复合材料及耐更高温的聚酰亚胺复合材料是飞行器轻量化机体结构选用的主要材料。
二、国外空天往返飞行器复合材料结构制造工艺
欧洲空间局(ESA)在重复使用飞行器用先进复合材料技术方面研究表明:复合材料凭借轻质高强,可设计性强,良好减振性能和低膨胀系数等鲜明特点,显著减少了飞行器零件和紧固件数量,从而采用更少原材料、更少装配时间实现飞行器整体装配技术的变革。先进复合材料技术在以F-22、F-35、B787、A350、B-2系列飞机,Delta、Titan、Ariane、Falcon系列火箭等众多型号为代表的航空航天飞行器结构上的工程应用,证明了复合材料在飞行器结构上应用的可靠性和技术优势。因而,采用复合材料设计和制造是空天往返飞行器先进性的典型体现,也是其结构技术的发展趋势。
空天往返飞行器具有与航空飞行器相似的外形设计,其机体结构主要分为机身结构、翼面结构两大类,机身结构主要包括前机身、中机身、后机身,翼面结构主要包括机翼、尾翼和体襟翼。机身包括壁板、框架、加强框、梁、口盖、起落架舱及舱门等零组件,翼面结构包括翼梁、翼盒、副翼、方向舵等零组件。机体零组件结构形式包括层合结构、蒙皮加筋结构、桁架结构、夹层结构等。碳纤维复合材料在飞行器蒙皮加筋壁板、框架、梁等结构上具有鲜明优势,如图3所示;复合材料具有可设计性,可设计实现复杂结构三维编织、多轴大尺寸经编、缝合及复杂机身结构整体制造。
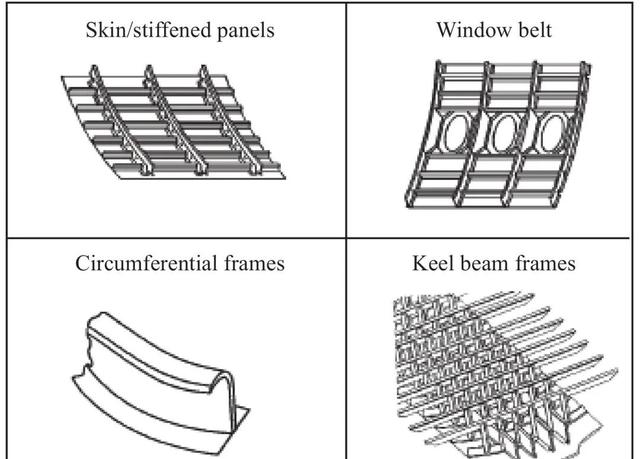
图 3 碳纤维复合材料在空天飞行器机身上的应用结构形式
在国外飞行器机体结构发展过程中,机身、翼面结构形式上几乎没有变化,结构材料由金属替换为比强度、比模量更高的纤维增强树脂基复合材料,包括碳纤维和玻璃纤维。飞行器复合材料结构发展追求更高减重效率,更高整体化程度;机体结构制造工艺的高效化和低成本化。
复合材料结构的制造工艺包括基于预浸料的热压罐固化、模压固化工艺,铺放方式包括手工铺放与自动铺放工艺;基于纤维预制体的树脂传递模塑(RTM)成型、RFI成型工艺;基于低温固化预浸料的袋压成型工艺及整体化成型工艺等。国外典型空天往返飞行器复合材料结构及其制造方案汇总见表2。
表 2 国外空天往返飞行器典型复合材料结构及其制造方案
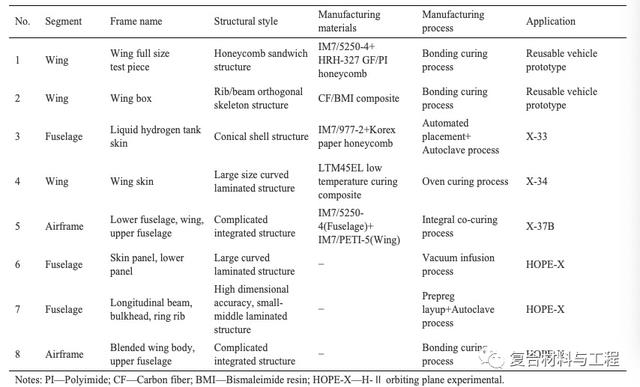
空天飞行器大型上/下半壳、机翼采用整体胶接固化或共固化工艺成型,壁板蒙皮、贮箱铺放工艺采用真空导入的树脂传递模塑工艺、自动铺放工艺。固化方式采用加热固化,包括热压罐固化、烘箱固化两种方式。
其中,X-37B飞行器结构采用了与空天环境相适应的复合材料整体化结构设计,并使用高精度成型模具技术实现了大尺寸构件整体结构成型;同时各零件之间大量采用共固化/共胶接工艺技术,实现复合材料结构整体制造,提高了结构效率,降低了装配工作量;基于全复合材料结构/防热一体化设计,采用了复合材料结构与热防护结构匹配的连接技术。这些创新制造技术的应用,使X-37B飞行器具有鲜明的先进性和机动性,成为现阶段最成功的可重复使用空天往返飞行器,从而助推了空天往返飞行器复合材料结构制造技术发展。
典型飞行器复合材料构件在制造工艺上,机身蒙皮基于IM7碳纤维复合材料采用自动铺放工艺实现,环向框架采用基于二维三向编织物RTM工艺或模压成型工艺实现,地板梁和等截面加强件采用拉挤工艺实现,桁条和其他加强件采用模压成型或热压罐成型工艺实现,低温燃料箱采用缠绕工艺实现;贮箱间结构采用IM7/8552复合材料制造的蒙皮、纵梁和面板组成(图4),上面板采用低温固化复合材料制成,下面板采用自动铺放工艺成型,框、梁采用RTM工艺成型实现。
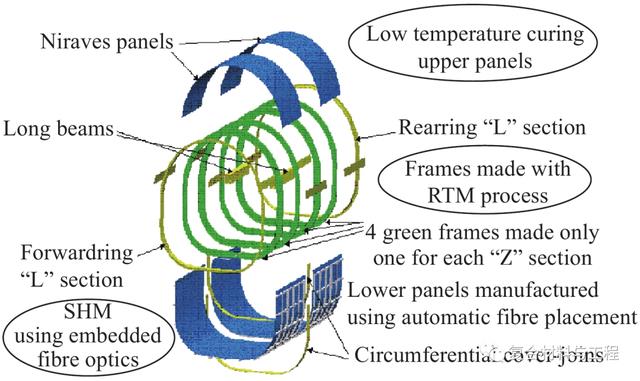
图 4 典型贮箱间结构组成分布
可见,国外研究机构依据空天飞行器机体复合材料结构特点和使用工况,选用合适的增强纤维及编织形式、匹配树脂基体制成复合材料,并选择相应的制造工艺实现不同结构部件的制造。飞行器结构件制造工艺设计时,主要考虑二个方面:一是充分利用复合材料可设计性特性,大尺寸构件采用一体化壁板结构设计并整体固化工艺制造,以减少机体零件数量和装配紧固件;二是采用低成本成型工艺制造非主承力件,包括采用低温固化预浸料成型工艺、非热压罐固化工艺(如真空袋压固化、模压固化、RTM成型工艺)。
图5为飞行器结构复合材料制造技术发展演变。可见,随着树脂基复合材料应用构件逐渐从小型次承力结构件、大型次承力结构件向大型主承力件的发展,国外复合材料制造工艺也随之深入研究,手工制造由手工铺贴发展为RTM工艺、热压工艺、RFI工艺等,自动化制造由纤维缠绕工艺发展为热固性预浸料自动铺带与自动铺丝、基于加热铺放头的热塑性预浸丝/带自动铺放工艺及面向大尺寸构件的高质量非热压罐成型工艺。可见,复合材料制造工艺发展趋势是制造工艺的自动化和低能耗,进而提高复合材料制造工艺的规范化和低成本化。一方面是高铺放精度、高一致性的自动化制造工艺,如研究使用基于粉末浸渍预浸带的干法自动铺放、具有加热加压铺丝头的自动铺放工艺;另一方面是低温、低能耗的非热压罐固化工艺,如研究环氧树脂基复合材料的电子束固化、感应固化,聚酰亚胺的液态浸渍工艺HT-VARTM等技术。
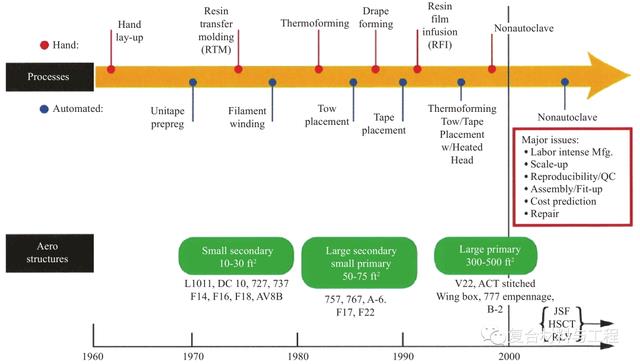
图 5 飞行器结构复合材料制造技术发展演变
为满足空天往返飞行器轻量化复合材料结构的最优化制造实现,需要结合飞行器机体结构特点、使用工况,做到结构/制造一体化,综合考虑结构设计及其可制造性、制造材料及基础性能数据、制造工艺、制造成本及制造周期等因素,迭代优化机体结构及实现方案,确定最优的结构模型、制造材料及制造工艺。
三、国外空天往返飞行器复合材料结构研制应用进展
空天往返飞行器相对于一次使用的运载火箭,大幅降低发射成本,缩短发射周期,灵活完成进出空间任务,满足天地多次往返的使用需要。美国、英国、俄罗斯及日本等国家自上世纪50年代都先后投入大量人力和物力开展这类新型飞行器的研究,取得了不同阶段的研究成果。其中研究最突出的是NASA主导研发的X系列验证机计划(又名“探路者”计划),突破众多关键技术,研制出不同试验任务的飞行器,并成功完成多次飞行试验,提高了重复使用运载器的技术水平,为重复使用空天飞行器工程应用奠定了良好基础。表3为国外空天往返飞行器典型复合材料应用情况汇总,包括了飞行器应用结构、材料体系及制造工艺等。
表 3 国外空天往返飞行器典型复合材料应用情况
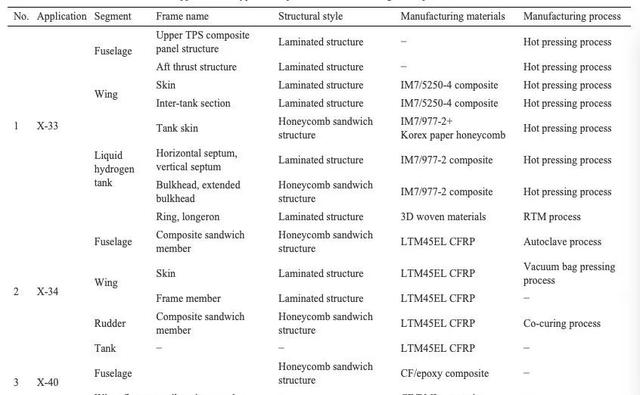
3.1、美国空天往返飞行器复合材料研制应用进展
自上世纪50年代起,美国着手开展先进空天飞行器的技术基础研究工作;80年代中期,启动了“国家空天飞机(NASP)”计划,但因目标过于超前,1994年被迫中止。随后,美国采取分阶段的发展策略,继续研发和验证先进空天飞行器相关技术。空天飞行器计划由美国空军和NASA共同提出,1996年项目开始实施,进行轨道机动可重复使用飞行相关技术的验证。美国NASA主导研发的X系列验证飞行器,如X-30、X-33、X-37、X-43等项目,都将轻质碳纤维增强树脂基复合材料作为必选的先进结构材料之一。碳纤维复合材料在X系列飞行器结构上的应用部件和比例逐渐增加。
(1) X-33飞行器项目
X-33项目是NASA与洛克希德·马丁公司于1996年启动的可重复使用运载器技术验证项目,目的是为研制可完全重复使用的实用型运载器进行技术准备。该项目研究推进为后续空天飞行器研究工作提供了研制基础,但在技术难度过大和资金短缺的双重压力下,X-33项目于2001年取消。
X-33空天飞行器是一个大型可重复使用运载器的半尺寸亚轨道验证机,飞行器长21.0 m,宽23.5 m,起飞质量129.27 t,最大飞行马赫数13.8;X-33飞行器内部结构图见图6,机体结构包括机翼、体襟翼、尾翼、航电舱、液氢贮箱和液氧贮箱等。
图 6 X-33飞行器内部结构
为了减轻机体质量,X-33飞行器机体大量采用复合材料制造;机体上部热防护板块结构、后推进结构、液氢贮箱都采用复合材料设计,如图7所示。机翼面板蒙皮和箱间段设计采用了碳纤维增强双马来酰亚胺树脂基复合材料,材料为IM7/5250-4复合材料。
液氢贮箱蒙皮面板为IM7/977-2复合材料+Korex蜂窝结构,蜂窝为杜邦公司生产的芳纶纸蜂窝。如图8所示,垂直隔板、水平隔板都设计采用了IM7/977-2复合材料制造;前/后隔板、前/后扩展端口隔板设计为IM7/977-2复合材料面板+蜂窝夹层结构,蜂窝为美国UlTRACOR公司生产的蜂窝芯;前环、水平纵梁及垂直纵梁设计为三维机织预制件,采用RTM工艺成型获得。
(2) X-34项目
美国轨道科技公司(OSC)为了使空天飞行器研制成本降低、性能提高及可靠性增加,设计并研制了X-34空天飞行器,飞行器长17.6 m,翼展8.5 m,最大飞行马赫数8.0。
该飞行器经过多次技术革新,采用全复合材料机身主结构和推进剂贮箱,机身结构多采用复合材料蜂窝夹层结构形式,蜂窝为铝蜂窝,高度在15.88~34.93 mm之间;中模碳纤维单向带和织物预浸料用于机身蒙皮和机翼梁,蒙皮厚度为0.076~3.05 mm之间,以增加部件的弯曲刚度。
制造工艺方面,创新地引入了复合材料非热压罐固化、低温固化等工艺技术增加制造灵活性,并采用不使用工装的激光定位装配技术降低装配成本。X-34飞行器所有复合材料部件采用ACG公司的LTM45EL预浸料,可在60℃固化,180℃后固化处理(相比于热压罐固化同种复合材料,低温固化复合材料的压缩强度降低22%,层间剪切强度降低28%),从而减小复合材料残余应力,提高零部件尺寸精度。
此外,非热压罐固化复合材料在机体局部修补固化方面具有优势,修补与机体结构使用的是同一树脂体系复合材料,比非同样树脂体系的材料修补得更佳、更耐用;且可以采用加热毯局部真空袋压工艺,即可实现局部复合材料迅速低温加热固化。
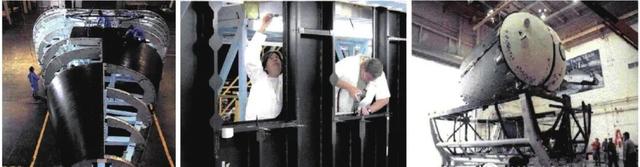
图 7 X-33飞行器复合材料结构
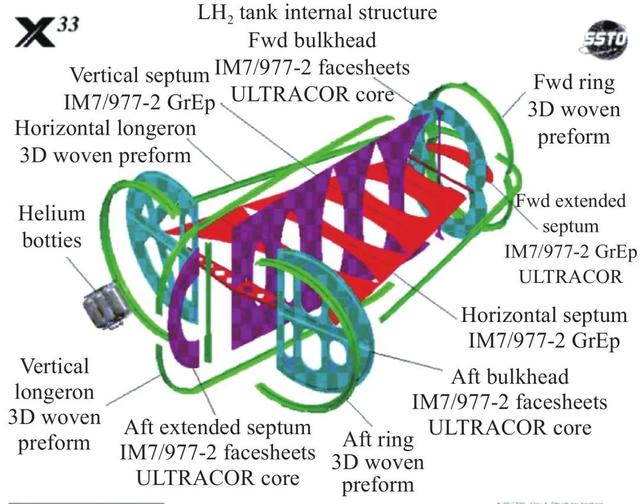
图 8 X-33飞行器液氢贮箱内部结构及材料组成
机身复合材料夹层构件是基于钢质成型模具采用热压罐成型工艺,夹层结构件采用三步固化工艺成型,后固化不依据成型模具执行;机翼蒙皮基于复合材料成型工装采用真空袋压固化,蜂窝夹层结构件采用一步共固化工艺成型,构件后固化在模具上实现;方向舵复合材料夹层结构件是基于铝质模具采用三步固化工艺成型,构件后固化在模具上实现。采用激光跟踪仪进行定位及装配,定位精度控制在0.13 mm;同时为所有零件位置和型面建立数据库,便于风洞或其它试验后数据对比。
(3) X-40飞行器项目
美国波音(Boeing)公司提出X-40(ReFly)空间机动飞行器方案,旨在验证返回末段的自主进场与着陆技术。X-40为复合材料结构无动力飞行器,机身采用碳纤维/环氧树脂复合材料蜂窝夹层结构制造,机翼、襟副翼、全动双斜尾翼、阻力板采用耐高温双马来酰亚胺树脂复合材料制造。
1997年,波音公司与美国空军合作研制的X-40A进场着陆试验飞行器,机体长6.7 m,翼展3.50 m,机身结构采用碳纤维/环氧复合材料与铝蜂窝制造,成功完成7次无动力进场着陆试验。在此基础上设计的全尺寸X-40B飞行器,增加了液体燃料火箭推进系统等,但该机型研制中止,其技术支撑了X-37A飞行器的研制。
(4) X-37飞行器项目
X-37空天飞行器计划是猎鹰(FALCON)计划的一部分,是NASA于1999年启动的空天飞机计划。2002年一度取消,2004年由美国国防高级项目研究局(DARPA)接手,又于2006年由空军快速响应能力办公室(RCO)负责,由主承研方波音公司研制出2架试验机。X-37项目包括两个子项目,进场与着陆试验飞行器(X-37A)和轨道飞行器(X-37B)。X-37A为X-40A飞行器的120%放大型,外形基本相同,主要结构采用耐高温双马来酰亚胺树脂复合材料及其蜂窝夹层结构件制造,完成6次进场着陆试验,为X-37B轨道试验飞行器设计优化及研制提供了重要依据。
X-37B飞行器(图9)总长8.84 m,翼展4.54 m,高2.9 m,机身长7.83 mm,载荷舱长2.1 m、直径1.2 m,其尺寸大约只有美国已退役航天飞机的四分之一,尺寸较小,主要验证飞行器结构材料、在轨道运行、自主返航及水平着陆等关键技术,成为实现可重复使用、小型无人多功能的太空运载器或作战平台。
图 9 X-37B飞行器
X-37B飞行器结构件的设计采用了整体结构(Integrated structure)的概念,设计中将很多零部件装配组成整体结构,设计尽可能保证纤维连续性,提高机体的结构效率。飞行器主结构全部采用轻质复合材料设计与制造,机身结构大量采用先进耐高温复合材料及其蜂窝夹层结构制造(图10),选用的是美国Cytec公司的IM7/5250-4碳纤维增强双马来酰亚胺树脂复合材料;机身上壁板、下壁板、口盖、纵梁等结构为整体结构件,都是复合材料共固化整体结构件。大尺寸部件采用共固化和共胶接等整体成型工艺,显著减少了零件、紧固件及模具数量。
图 10 X-37B飞行器结构碳纤维复合材料组件示意图
机身蒙皮为夹层结构,表层为3~6层的IM7/5250-4碳纤维复合材料,内层为玻璃纤维和酚醛树脂的复合材料F50-HRP,中间层为波纹板(Flexcore)结构形式;表层和中间层之间用胶黏剂粘接,固化后就形成了蒙皮结构。
机翼、体襟翼及阻力板结构采用轻质耐高温结构材料,为NASA兰利研究中心研发的IM7/PETI-5碳纤维增强聚酰亚胺树脂复合材料。引入耐高温PETI-5聚酰亚胺复合材料可以提高热防护系统(TPS)的背温(从204.4℃提高至232.2℃),进而减少TPS的厚度;且可使整个翼面结构(包括TPS)减重2%。较薄厚度的TPS不仅可以减重,还可以加厚翼盒的结构;机翼结构厚度的增加将会直接提高其刚度,特别是仅有25.4 mm厚的外表面根部位置。
机翼上蒙皮、下蒙皮、机翼主梁、翼套梁都为夹层结构,芯层为12.7 mm厚的钛合金蜂窝芯材,其余部件为聚酰亚胺复合材料层压板。减速板面板使用碳纤维/聚酰亚胺复合材料,芯子使用钛合金蜂窝材料。体襟翼由碳纤维/聚酰亚胺复合材料和钛合金蜂窝芯材制造,尺寸约为609.6 mm×508 mm×101.6 mm。
飞行器复合材料框与下半壳壁板胶接连接,在框、梁等零件与部件接合处采用紧固件机械连接,机体整体部段装配如图11所示。2003年,X-37B飞行器成功地完成了结构验证试验,试验过程中,对飞行器施加了飞行和着陆时典型载荷。试验成功后,飞行器机身运回波音公司的试验厂房,如图12所示,进行后续组装和系统集成工作。
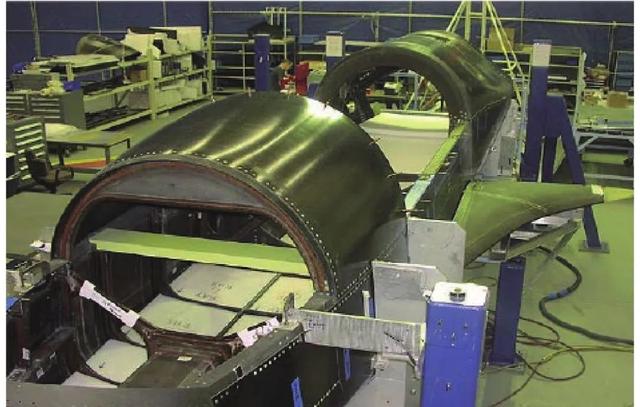
图 11 装配中的X-37B飞行器机身

图 12 成功试验后运回的X-37B飞行器
X-37B飞行器成功地通过了5次空天往返飞行试验,先后创造了674天、718天、780天在轨运行纪录后安全返航,目前仍在第6次太空飞行试验中;飞行器轻质复合材料结构系统不仅能够满足机体结构动、静、疲劳强度的要求,还能在近地轨道环境、再入大气层气动加热的高温环境保持设计要求的力热性能。
正是通过X-33、X-34、X-37等一系列X飞行器试验计划,美国掌握了可重复使用空天飞行器的大量关键技术;先进复合材料结构技术的发展和应用验证,是保证下一代空天飞行器研制的重要基础支撑。
3.2、国外其他国家空天往返飞行器复合材料研制应用情况
在先进重复使用空天飞行器研究方面,英国设计了“霍托尔”、“云霄塔”空天飞行器方案、德国设计了“桑格尔”空天飞行器方案,日本提出了“HOPE-X”空天飞行器方案,俄罗斯、法国、印度和巴西等国也相继提出了各自的空天飞机方案。然而这些国家设计研发的空天飞行器均未见具体实施和飞行试验成功的报道。
日本宇宙开发事业团(NASDA)和日本国家航空航天实验室(NAL)共同开展HOPE-X空天飞行器的全复合材料机身结构设计、整体成型技术、连接与装配技术等方面研究工作。该飞行器机体总长13 m、宽9 m,翼身组合结构,主体结构采用全复合材料夹层结构,选用碳纤维环氧树脂、双马来酰亚胺树脂及氰酸酯树脂的先进结构复合材料,蜂窝芯材为铝蜂窝。复合材料的树脂基体为日本最新开发的低温固化环氧树脂,具体牌号未透露;复合材料构件固化温度约为100℃,使用非热压罐固化工艺,后固化(约180℃)后仍保持较高使用温度(高于160℃)。采用低温固化工艺,可以有效降低飞行器复合材料结构内部热应力,提高结构件型面及尺寸精度。
HOPE-X飞行器大型上机身构件成型模具采用金属框架+复合材料工作面的方案,复合材料工作面采用碳纤维复合材料+玻璃纤维复合材料的组合制造,热膨胀系数与复合材料机身一致,保证了固化后构件型面精度。机翼面板和舱门尺寸小、结构简单,可采用钢制成型模具成型;框、梁等零件成型采用非金属模具,模具材料为无机陶瓷与玻璃纤维复合材料组合而成,价格便宜,易于采用数控机床加工;且该模具具有良好精度,热膨胀系数与复合材料零件一致。
HOPE-X飞行器采用自动铺放技术、RTM工艺及热压罐工艺等技术实现全部复合材料构件的制造。真空袋压成型工艺用于制备机身蒙皮壁板和下部机体壁板等大型结构件,热压罐成型工艺制备纵梁、隔框和环形肋等机体内部尺寸精度要求高的中小尺寸结构件。采用整体成型工艺技术实现大型复合材料构件的制造,翼身融合体与上部机身采用二次胶接/共胶接固化工艺组合成整体,复合材料梁与翼身融合体之间及复合材料框与蒙皮壁板之间都采用二次胶接/共胶接固化工艺实现组装,如图13所示。结构件胶接固化在大型固化箱中实现。框架与机身壁板连接采用单侧L形件和湿预浸料铺贴,可显著提高框架与壁板间的胶接强度,图14为飞行器上机身与翼身融合体结构组装过程图。
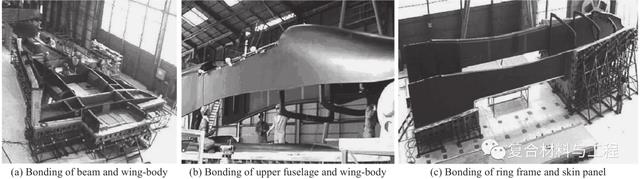
图 13 HOPE-X飞行器机身结构胶接

图 14 HOPE-X飞行器结构组装
欧洲航天局(ESA)开展的过渡性试验飞行器中间试验车辆(IXV,Intermediate experimental vehicle)为技术验证飞行器,总长4.4 m(不含体副翼结构),侧向宽度2.24 m,法向高度1.54 m,验证研究可重复使用滑翔返回式天地往返运载技术。试验成功后,将继续开展更为深入的增加机翼、V尾等结构的创新空间飞行器(ISV,Innovative space vehicle)的研究计划,结构类似于X-37B飞行器。
IXV飞行器结构系统主要包括框、梁、口盖和壁板等,主体结构主要选用碳纤维增强复合材料;其中上、下壁板及侧壁板是复杂曲面结构,为复合材料制造的整体结构件,如图15所示。
图 15 IXV飞行器复合材料结构
结合典型L形构件的固化回弹变形趋势仿真结果,指导零件成型模具及工艺优化。为了控制壁板的固化变形量,大型壁板结构件通过使用试验验证的型面补偿成型模具制造。为了保证夹层结构壁板构件中预埋件定位准确,采用了激光投影辅助定位技术。
英国喷气发动机公司主导研制的云霄塔(SKYLON)飞行器,设计为水平起降、单级入轨的重复使用运载器,如图16所示。机身总长约83 m、翼展25.4 m,主承力结构采用碳纤维复合材料桁架结构,具体材料未透露。机翼的翼梁(可能采用复合材料制造)作为主承载结构穿过机翼,每根翼梁贯穿整个翼展。SKYLON飞行器研制进展缓慢,还未进行验证飞行。
图 16 英国SKYLON飞行器
俄罗斯中央流体力学研究院( TsAGI) 完成了可重复使用空天飞行器的第一阶段可行性研究,飞行器的俄文缩写是МРКН(图17),意为多用途火箭运载器。风洞试验获得了有关飞行器着陆过程中气动特性等数据,TsAGI 将继续对该飞行器进行试验和制造,对于机体结构材料并未报道。
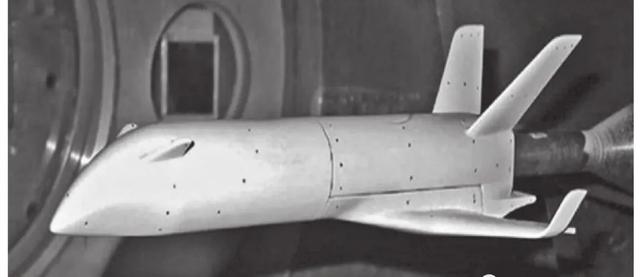
图 17 俄罗斯МРКН飞行器
四、国外空天往返飞行器复合材料结构发展趋势
美国X系列飞行器总的发展方向正朝着航空航天结合逐步推进,X-37B的飞行成功意味着美国在空天飞行器研制与应用方面迈出了一大步。进入21世纪以来,NASA先后与诺斯罗普·格鲁门公司合作研发X-43A无人作战飞行器,与湾流公司合作研发X-54未来超声速运输技术验证机,与洛克希德·马丁公司合作研发X-55先进复合材料货运飞行器验证机。NASA还主导新研多次使用的快速反应小型低成本飞行器(RASCL)。美国国防高级项目研究局(DARPA) 主导的“试验性空天飞机”(代号XS-1)项目,将在X-37B飞行器基础上,以二级入轨和完全可重复使用方式大幅度降低进入太空成本。XS-1空天飞机将具有频繁起降的航空器特性,同时兼顾高超声速飞行器和快速进入空间飞行器的技术发展。
随着可重复使用飞行器概念及技术的飞速发展,美国、英国、俄罗斯等国家将会进一步加快空天往返飞行器的深入研究及试验验证工作,对于先进高性能结构复合材料的需求和应用研究相应增加。飞行器轻质复合材料结构系统必然会追求更高比强度与比模量、更佳耐空天环境性能、更好可靠性材料体系以满足服役环境下结构完整性要求,复合材料构件制造将朝着高度集成整合、数字化、规范化、智能化方向发展,以适应服役飞行器高效高质量制造需要。
五、结语
相比于传统材料,先进树脂基复合材料具有鲜明的高比强度、高比刚度等性能优势,可以满足空天往返飞行器的轻量化结构设计与制造需求。从国外空天往返飞行器轻量化结构系统研制进展可见,匹配不同结构部段使用温度的高性能碳纤维增强树脂基复合材料,是飞行器轻质机体主承力、次承力结构选用的主要结构材料;依据飞行器机体结构特点和受力工况,综合考虑不同复合材料制造工艺特点、制造成本等因素,采用合适的制造工艺实现结构件的最优制造。高性能树脂基结构复合材料已经应用到以X-33、X-37B、HOPE-X为代表的空天飞行器机体结构件研制中,验证了空天飞行器用轻量化结构和材料技术,应用成熟度达到较高水平。先进树脂基结构复合材料技术是空天往返飞行器轻质结构件研制的核心技术之一,也是实现飞行器总体性能的关键一环。
相关参考
复合材料成型工艺是复合材料工业的发展基础和条件。随着复合材料应用领域的拓宽,复合材料工业得到迅速发展,一些成型工艺日臻完善,新的成型方法不断涌现,目前聚合物基复合材料的成型方法已有20多种,并成功地用于...
复合材料成型工艺是复合材料工业的发展基础和条件。随着复合材料应用领域的拓宽,复合材料工业得到迅速发展,一些成型工艺日臻完善,新的成型方法不断涌现,目前聚合物基复合材料的成型方法已有20多种,并成功地用于...
一、概况环氧树脂模具又称树脂模具,它具有制造周期短、成本低、特别适合形状复杂的制品和产品更新换代快速的工业领域;因此,在国外先进国家已得到广泛的应用,特别在汽车制造业、玩具制造业、家电制造业、五金行业...
一、概况环氧树脂模具又称树脂模具,它具有制造周期短、成本低、特别适合形状复杂的制品和产品更新换代快速的工业领域;因此,在国外先进国家已得到广泛的应用,特别在汽车制造业、玩具制造业、家电制造业、五金行业...
...而广泛应用于运输车辆、建筑、电子/电气等行业。SMC/BMC复合材料模压控温设备的选择是复合材料在模压过程中需要注
...而广泛应用于运输车辆、建筑、电子/电气等行业。SMC/BMC复合材料模压控温设备的选择是复合材料在模压过程中需要注
复合材料成型工艺是复合材料工业的发展基础和条件。随着复合材料应用领域的拓宽,复合材料工业得到迅速发展,一些成型工艺日臻完善,新的成型方法不断涌现,目前聚合物基复合材料的成型方法已有20多种,并成功地用于...
大|企|业|动|向BigPlayerSABIC推动全球先进回收及生物基材料产量陶氏化学携手LVMH布局生物基材料包装市场Bioweg携手GinkgoBioworks推动细菌纤维素优化生产帝斯曼发布AI颜色预测工具Lucidiris天壤利用扩散模型生成全新蛋白质结构...
...院,国有事业单位,现有透波材料及天线罩技术、树脂基复合材料技术、热防护材料技术、陶瓷基结构复合材料技术、金属材料特种工艺技术、材料理化分析及检测技术六大专业。研究所目前人员规模700余人,承担任务以三院项...
...院,国有事业单位,现有透波材料及天线罩技术、树脂基复合材料技术、热防护材料技术、陶瓷基结构复合材料技术、金属材料特种工艺技术、材料理化分析及检测技术六大专业。研究所目前人员规模700余人,承担任务以三院项...