热压烧结石墨模具脱模剂(全新热锻环保工艺模式)
Posted
篇首语:不飞则已,一飞冲天;不鸣则已,一鸣惊人。本文由小常识网(cha138.com)小编为大家整理,主要介绍了热压烧结石墨模具脱模剂(全新热锻环保工艺模式)相关的知识,希望对你有一定的参考价值。
热压烧结石墨模具脱模剂(全新热锻环保工艺模式)

前言
石墨或来自石墨的产品,因其优良的润滑脱模性能及低廉的价格,仍然是锻造工业生产中最常用的脱模润滑剂,但这类产品对人员和环境的伤害不可估量(职业病伤害、粉尘伤害、设备伤害、环境后处理伤害等),在此社会环境条件下,引进环保型白色脱模剂替代石墨脱模剂势在必行。白色脱模剂的价格是石墨系列脱模剂的5倍左右,但其润滑脱模性能远低于石墨产品,为了保证生产过程稳定运行及产品品质就需要加大用量,因此白色脱模剂的使用成本将是石墨脱模剂的10倍左右。那么,如何把节能降耗和环境保护有机结合起来,就成为摆在我们面前亟待解决的重大课题。
目前,国内部分锻造企业已经开始探寻绿色锻造的道路,为了实现高效低耗、节能环保的目标,致力于开发新的锻造工艺,选用新型的锻造设备或者对现有的设备及工艺进行改进。
该热锻环保工艺模式就是在这样的行业环境中应运而生,为了将整个热锻生产对环境的影响降到最小并尽可能的提升资源利用效率,本文从脱模剂循环再生使用和含油废水油水分离处理两个方面入手,以提升物料能源利用效率、杜绝有害排放为目标,研究并应用了包含脱模剂回收再生技术和含油废水油水分离技术的全新的热锻环保工艺模式,这也是一种低熵的生产制造模式。
脱模剂回收再生技术
脱模剂循环再生系统是利用荷电凝聚原理,通过荷电凝聚将混入脱模剂中的固体垃圾、杂油有效的分离出去,使脱模剂达到可循环再利用的状态。
通过脱模剂再生系统实现脱模剂的回收、再生、循环使用,达到配合锻造生产线进行自动化生产并实现节约能耗的目的。本系统将锻造使用过后落入地坑水槽中的已经稀释过的白色脱模剂泵吸到脱模剂处理前槽,随后通过磁力分离器、油水分离装置、细微浮游物去除装置去除脱模剂中混杂的铁粉、油分及细微杂质,然后泵到浓度调整槽进行浓度自动调整,并将其供应至脱模剂供应箱内循环使用。
地坑浮油收集
地坑水槽内设置液位开关,当浮油达到上限位传感器位置时用浮动式抽吸机将浮油泵到废油桶中,另外用泵将使用过的脱模剂泵入处理前槽。浮油处理能力为300L/h。
磁力铁粉分离
脱模剂从地坑水槽泵入处理前槽过程中经过磁力分离器,磁力分离器使用稀土类的永久性磁石将脱模剂中混入的氧化皮等铁粉进行磁力分离,永久性磁石磁力为铁素体磁石的8.3倍,铁粉去除能力可达94%~99%。
荷电凝聚油水分离
铁粉去除后,脱模剂经过处理前槽进入油水分离装置。油水分离从两方面进行,一方面是在液面上采用旋转式刮刀将表面的浮油刮入废油回收装置,另一方面对于液体内部包含油在内的颗粒采用荷电凝聚技术凝聚成较大的颗粒,通过滤网进行过滤。处理后油分浓度为1000ppm以下。
细微悬浮物过滤
采用60网目篮式过滤器过滤细微悬浮物,滤芯规格为25μm,外径φ65mm,内径φ30mm, 长度750mm,为了保证设备的正常稳定运行,采用了双系统设计,一使用一备用,在第一系统网目堵塞时自动切换到第二系统运行,可保证在设备不停机的情况下对第一系统的滤芯进行更换,每个系统设有6个过滤器,处理能力达到1800L/h,过滤后脱模剂内细微物大小小于25μm的数量在500ppm以下。
浓度自动调整
脱模剂去除细微悬浮物后进入浓度调整槽,利用电导率计实时监测脱模剂浓度,当浓度值低于下限或者高于上限时,能够自动补充脱模剂原液以提高浓度或者自动加水以降低浓度,可以实现在�5%精度范围内自动调整,浓度调整完成后脱模剂进入脱模剂供应箱中循环使用。
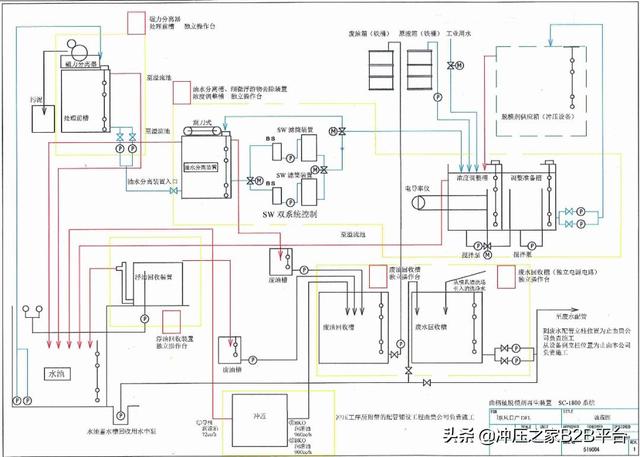
脱模剂再生循环原理图
本技术通过合理选用合适的白色脱模剂替代黑石墨脱模剂消除了脱模剂对环境的污染,减少了对作业者的健康危害,提升了作业现场的5S,达成环保的目标;通过脱模剂循环再生系统,实现了全自动化生产,使脱模剂能够回收、再生、循环利用,脱模剂的消耗降低到每生产1kg锻件仅消耗30g脱模剂原液,达成节能的目标。
含油废水油水分离技术
脱模剂再生循环系统分离出来的含油废水进入油水分离装置,通过油水分离系统的重油分离→曝气分离→气浮分离→浮油浓缩,最终将含油废水分离成工业废水和废油,便于后续进行专业处理。
重油分离
在含油废水收集坑设置一部收油机,初步清理表面浮油。废水提升泵设置一根回流管,延伸至收集坑底部,对底部进行冲刷搅拌,防止过多的杂物沉淀。
曝气分离
经过初步的重油收集,含油废水被提升至隔油池,部分小的油颗粒与水分子结合比较紧密,通过曝气的方式充分搅拌,将油与水分离。
通过曝气后,含油废水流入静置分离池,废水通过底部孔洞进入下一步处理,废油定期进行刮除。
气浮分离
通过溶气水泵特殊的构造在运行中泵的蜗壳产生负压,通过负压吸入一定量的空气泡,气泡在泵叶轮的强力切割作用下,分散成细小的气泡进入气液分离罐,溶气水形成纳米级气泡溶气水,然后进入混合区与含油废水混合,亲油性气泡与水中的细小油颗粒接触并将细小油颗粒吸附在气泡表面,在浮力的作用下上浮到水面,通过刮油机刮除。在气浮清液槽内设置一台在线油测定仪,用于监测最终处理的废水中的含油量是否达标。
浮油浓缩
通过曝气分离和气浮分离出的浮油含有一定量的水分,需要进行浓缩处理后达到废油处理公司的含油量要求,因此需要进一步分离其中的水分。浮油浓缩采用隔板式隔油池,浮油进入隔油池后静置,浮油与水分离,底部水分通过集水管排出。浓缩后的浮油定期进行清理与收集。
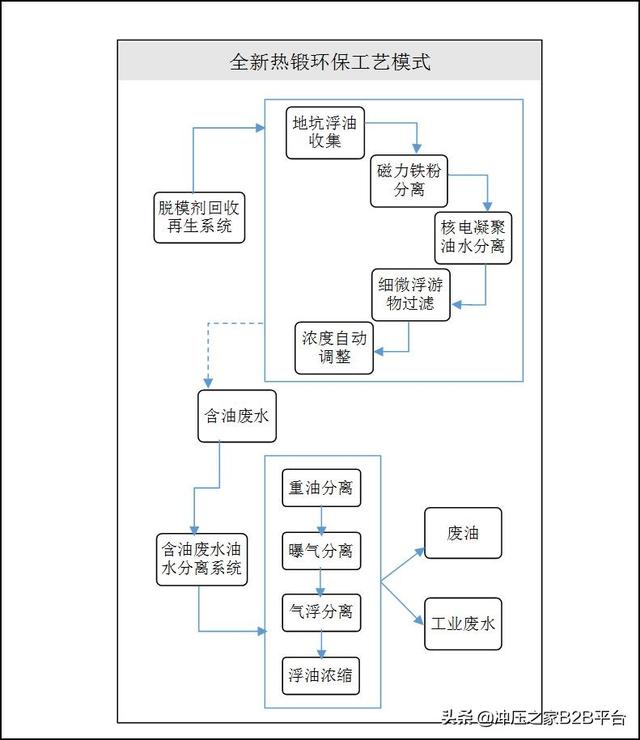
热锻环保工艺系统图
全新热锻环保工艺模式特点
全新热锻环保工艺模式采用了较多的先进工艺及技术,主要特点有以下5个:
⑴采用了稀土类永久磁铁对脱模剂回收液中的铁粉进行高达94%~99%的分离;
⑵采用了荷电凝聚技术对脱模剂回收液进行油水分离;
⑶采用了双系统过滤式细微悬浮物去除装置,使脱模剂回收液中的杂物大小不足25μm的含量低于500ppm;
⑷采用电导率计实现了脱模剂浓度的自动调整,调整精度在�5%范围内;
⑸多种油水分离工艺联合运用,曝气分离、气浮分离、浮油浓缩等,使废油中的含油量≥90%,处理过程中不会产生二次污染。
实施效果及应用
热锻工艺方案的差别,将会导致物料和能源消耗的较大差异,对环境的影响也会完全不一样。全新热锻环保工艺模式的研究就是结合生产线的实际情况,基于环境保护最大化、物料能源消耗最小化研究并应用的最优工艺模式,实现了自动化程度高、物料能源消耗少、废弃物少、对环境污染小的目标。
该工艺模式投入使用后,彻底替代了石墨脱模剂,消除了石墨的严重污染,并且通过脱模剂回收再生技术使脱模剂回收循环使用,大大降低了物料能源消耗成本,取得了较大的经济效益。同时,对脱模剂使用过程中产生的含油废水进行油水分离,后续可有针对的进行处理,彻底避免了将有害废物直接排放到环境中,取得了显著社会效益。
— —END— —
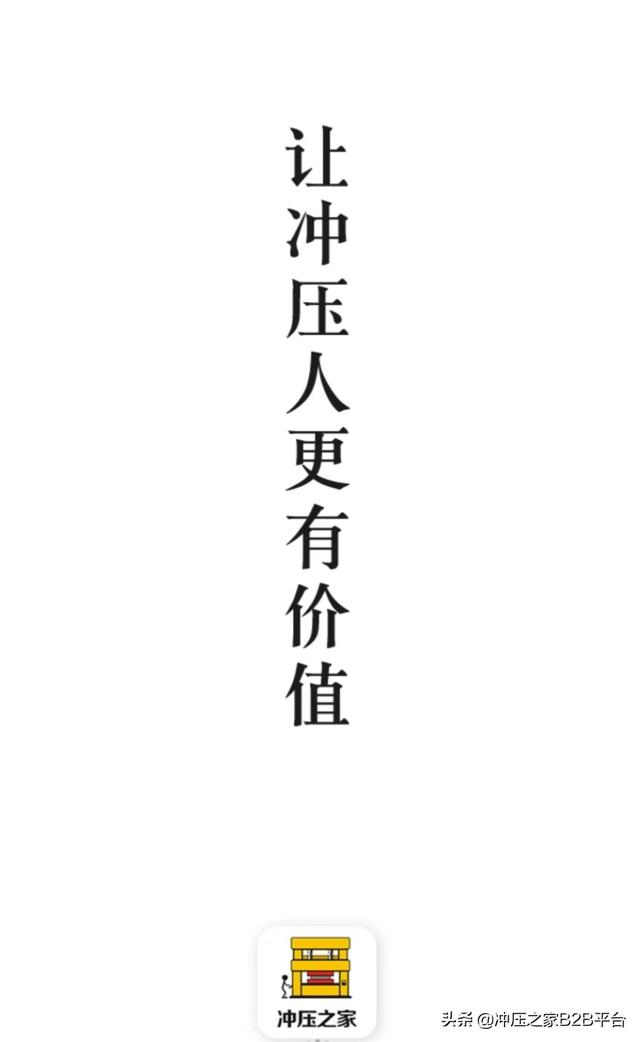
相关参考
...在高温高压下性能要稳定,自身不发生氧化变质,不腐蚀模具和工件。2)有良好的温浸润性(浸润温度为400~550℃).3)具有良好的润滑、脱模性能。4)有良好的冷却及隔热性能,可以防止坯料的温度急剧下降,又可防止模具呈现过热...
...在高温高压下性能要稳定,自身不发生氧化变质,不腐蚀模具和工件。2)有良好的温浸润性(浸润温度为400~550℃).3)具有良好的润滑、脱模性能。4)有良好的冷却及隔热性能,可以防止坯料的温度急剧下降,又可防止模具呈现过热...
热压烧结机电压4v什么意思(氧化锆陶瓷用热等静压烧结有什么特点呢?)
...特点呢?接下来科众陶瓷给大家介绍一下。氧化锆陶瓷用热压烧结工艺可以在比无压烧结低的温度下获得致密的陶瓷烧结体坣壱屲,且烧结时间短得多。但热压烧结是采取单向加压,因而制品的形状和尺寸要受到模具的限制,一...
热压烧结机电压4v什么意思(氧化锆陶瓷用热等静压烧结有什么特点呢?)
...特点呢?接下来科众陶瓷给大家介绍一下。氧化锆陶瓷用热压烧结工艺可以在比无压烧结低的温度下获得致密的陶瓷烧结体坣壱屲,且烧结时间短得多。但热压烧结是采取单向加压,因而制品的形状和尺寸要受到模具的限制,一...
...结时不收缩的无机材料陶瓷。氮化硅的强度很高,尤其是热压氮化硅,是世界上最坚硬的物质之一。具有高强度、低密度、耐高温等性质。Si3N4陶瓷是一种共价键化合物,基本结构单元为[SiN4]四面体,硅原子位于四面体的中心,...
...县五金产品生产中必不可少的工序,如何挑选优良的热锻模具用钢,改善模具的运用寿命,下降生产成本,进步经济效益,已成为各生产企业一起关心的问题.1热锻填具钢的工况条件1.1以东西五金产品为铡,现在国内生产厂企业大多采用...
...县五金产品生产中必不可少的工序,如何挑选优良的热锻模具用钢,改善模具的运用寿命,下降生产成本,进步经济效益,已成为各生产企业一起关心的问题.1热锻填具钢的工况条件1.1以东西五金产品为铡,现在国内生产厂企业大多采用...
...法。与冲压加工工艺基本上一样,冷锻加工也是由材料、模具和设备三要素构成。只是冲压加工中的材料主要是板材,而冷锻加工中的材料主要是圆盘线材。日本(JIS)叫冷间锻造(简称冷锻),中国(GB)叫冷镦,外面螺丝厂...
...法。与冲压加工工艺基本上一样,冷锻加工也是由材料、模具和设备三要素构成。只是冲压加工中的材料主要是板材,而冷锻加工中的材料主要是圆盘线材。日本(JIS)叫冷间锻造(简称冷锻),中国(GB)叫冷镦,外面螺丝厂...
锻造模具是在锻造工艺过程中使用的模具,原材料在外力的作用下在锻模中产生塑性变形,从而得到所需的形状和尺寸的零件。锻造模具可根据锻造温度的不同分为热锻模、温锻模和冷锻模。热锻模因设备的不同还可分为锤锻模...