深孔钻油用过后应该变混浊吗(PCB板,图形电镀参数)
Posted
篇首语:第一个青春是上帝给的;第二个的青春是靠自己努力的。本文由小常识网(cha138.com)小编为大家整理,主要介绍了深孔钻油用过后应该变混浊吗(PCB板,图形电镀参数)相关的知识,希望对你有一定的参考价值。
深孔钻油用过后应该变混浊吗(PCB板,图形电镀参数)
作者简介:
长期从事PCB工艺维护、改进及技术研发工作,现任职于一家上市公司研发总监;对高端PCB制造颇有研究。
Chapter 1 电镀原理
一 电镀基础
1 电镀的基本过程:
电镀是一种电化学过程,也是一种氧化还原过程,由电镀得到的金属镀层结晶细致,化学纯度高,结合力好。电镀时,将金属制体作为阴极,所镀金属或合金作为阳极,分别挂于铜或黄铜制成的阴极棒上而浸入含有镀层成分的电镀液中,并通入直流电。
以镀镍为例:将零件浸入含有镍的金属盐溶液中作为阴极,金属镍作为阳极,接通电源后在零件上即可沉积出金属镀镍层,其氧化还原过程如下:
阴极:Ni2++2e——Ni (主) 2H++2e——H2 (副)
阳极:Ni-2e——Ni2+ (主) 4OH--4e——2H2O+O2 (副)
对镀层的基本要求是:①与基体结合牢固,附着力好。
②镀层完整,结晶细致紧密,孔隙率小。
③具有良好的物理、化学、力学性能。
④具有符合标准的厚度,而且均匀。
2 电镀的结晶过程及影响结晶粗细的因素:
2.1 电镀的结晶过程:
在形成金属晶体的同时进行着结晶核心的生成和成长过程,这两个过程的速度决定了金属结晶的粗细程度。一般地,当晶核生成的速度大于晶核的成长速度,就能获得结晶细致,排列紧密的镀层;晶核的生成速度大于晶核成长速度的程度越大,则镀层的结晶越细致紧密;否则结晶粗大。
实践证明:提高金属电结晶时阴极极化作用,可以提高晶核的生成反应,便于获得结晶细致的镀层;但阴极极化作用不是越大越好,当阴极极化作用超过一定范围时,会导致氢气的大量析出,从而使镀层变得多孔、粗糙、疏松、烧焦、甚至呈粉末状,质量反而下降。
2.2 影响电镀结晶粗细的主要因素:
2..2.1主盐特性:一般地,如果主盐是简单的盐,其镀液的阴极极化作用很小,因此镀层结晶晶体较粗。而如果是络盐,由于络离子在溶液中的离解作用小,络合作用使金属离子在阴极上的还原过程变得困难,从而提高了阴极的极化作用,因此镀层的结晶较细。
2.2.2主盐浓度:在其它条件一定时,提高主盐浓度,则阴极极化作用下降,结晶核心的生成速度变慢,所得的镀层结晶变粗,稀溶液的阴极极化作用虽比浓溶液大,但其导电性差,不能采用大的阴极Dk,同时阴极电流效率低,所以不能用此因素来改善镀层结晶的细致程度。
2.2.3 附加盐:电镀溶液中除主盐外,有时还要加入某些盐类,其作用是提高溶液的导电性,有时还能提高阴极极化作用,使镀层结晶更为细致紧密。
2.2.4 添加剂:为了改善电镀溶液的性能和镀层质量,往往在电镀溶液中加入少量的某些有机物质的添加剂,其能吸附在阴极表面或与金属离子形成络合体,从而大大提高金属离子在阴极还原时的极化作用,使镀层细致、均匀、平整、光亮。但必须注意有机添加剂是有选择性的,不可乱用。
2.2.5 阴极电流密度DK:一般地,DK过低,则阴极极化作用小,镀层结晶较粗,随着DK的增大,阴极极化作用增大,镀层结晶变得细致紧密,但DK不能超过镀液允许的Dk上限值,否则阴极附近的金属离子严重缺乏,在阴极的尖端和凸出地方会产生形状如树枝状的镀层,或在整个阴极表面产生海绵状的镀层。
2.2.6 温度: 其它条件一定时,升高温度,会加快阴极反应速度和金属离子的扩散,降低阴极极化作用,因而镀层结晶变粗;另一方面,温度的升高可提高允许的DK的上限值,DK的增加可增大阴极极化作用,综合两方面的因素,镀层结晶不会变粗而且会加快沉积速度,提高生产效率。
2.2.7搅拌:一方面,搅拌会加速溶液的对流,降低阴极的浓差极化,从而使镀层的结晶较粗,另一方面,搅拌可以提高允许的DK上限值,在较高的DK和电流效率下得到细致的镀层。搅拌必须进行定期或连续的过滤,以除去杂质。搅拌的方式有机械法,阴极移动,压缩空气搅拌等,使用较多的有阴极移动和空气搅拌。
2.2.8 换向电流:能周期的改变电流方向,被镀零件在每个周期内均有一段时间为阴极,从而限制结晶成长的速度,同时还能溶解镀层上的显微凸出部分,具有整平作用。采用换向电流可以使用较大的电流密度,提高生产效率,并可使镀层结晶排列得更为紧密。
3 分散能力、覆盖能力及其影响因素:
常用均镀能力和深镀能力来评定镀层在零件上分布的均匀性和完整性。
3.1在电镀时,即使是形状简单的平板零件,由于电流的边缘效应,电力线容易在零件的尖角和边缘处集中,DK比较大,因而镀层较厚,而在中部电力线少,DK小,镀层较薄。对于凹凸不平的或有深孔的零件,除有边缘效应外,还由于凹凸两处与阳极的距离不同,使它们彼此间的电阻不同,因而DK在凹凸处的分布不同,凸处与阳极距离近,电阻小,DK大,镀层厚,反之亦然,甚至在口径较小的深孔处,由于电力线达不到内壁表面,而沉积不
上镀层。
3.2影响均镀能力和深镀能力的因素:
3.2.1 阴极极化度:表示阴极电极电位随DK变化而变化的程度。
dф/dDk即极化曲线上每一点的斜率,如果没有阴极极化,阴极表面不同处的DK的分布主要取决于它们与阳极间的距离,距离近则DK大,距离远则DK小,此称为初始电流分布,但实际上有极化存在,电流流过电极相当于一溶液界面间串联了一个电阻,其与dф/dDk相当,当距离近时,DK大,阴极极化值大,阴极极化引起的电压降大,这样就使整个阴极表面上各处的Dk趋于均匀,从而获得均匀的镀层,因此提高阴极极化度可提高均镀能力和深镀能力,但必须在允许使用的Dk范围内。
3.2.2 镀液的电导率:也即导电性,在其它条件一定时,电导率大,则导电性强,阴极与阳极间溶液的电压降的的差别就小,就比较容易通过阴极极化来调整,使Dk在阴极上分布均匀,但当极化度很小时,增大电导率,对均镀能力和深镀能力无太大改善。
3.2.3 电流效率η: η=m/kit *100% k为电化当量,单位为g/A*h。电流效率对均镀性和深镀能力的影响取决于η与Dk的变化关系:当η与Dk反向变化时,Dk大则η低,金属沉积就小,DK小则η大,金属沉积大,这样就使阴极各处的实际DK分布得更均匀,相应均镀性就提高。
3.2.4 电极和镀槽的几何因素:电镀槽的的形状,电极的形状,尺寸,电极间的距离,电极在镀槽中的位置等均会影响阴极上的电流的均匀程度,适当增大电极间距离可改善镀层的均匀性。
3.2.5 基体金属:
3.2.5.1 氢过电位:当氢在基体金属上的过电位小于在镀层金属上的过电位,则在刚入电镀缸时,有大量的氢气析出,会影响镀层的均匀性,另当金属中含有氢过电位小的杂质,则在杂质表面有大量氢气放出,也不容易均匀,为获得均匀连续的镀层,常在最初通电时采用短时间的大电流进行冲击,在基体表面先镀上一层氢过电位大的金属,然后按正常的Dk电镀。
3.2.5.2 表面状态:不干净的表面(如氧化或油污),即使在最有利的电化学和几何条件下,金属的沉积是不均匀的,而且结合力会显著降低,又因氢在粗糙面上的过电位小于光滑表面,粗糙面上的氢容易析出,金属不易沉积,因此提高基体金属的光洁度,往往可以改善深镀能力。
二 镀铜原理
1 镀液的种类及选择:
镀铜液的种类很多,氰化镀铜、焦磷酸盐镀铜、氟硼酸盐镀铜、氨基磺酸盐镀铜、硫酸盐镀铜等,其中酸性硫酸盐镀铜为PCB行业的首选,原因如下:
①高分散能力:包括板面的均镀能力和孔内的深镀能力,对于PCB来说,对于板厚径比小于4:1的PCB,表铜:孔铜小于1:0。85,否则此镀液不可用。上述镀液中,焦磷酸盐镀液和氟硼酸盐镀液的分散能力最好,硫酸盐镀液次之。但焦磷酸盐镀液抗污染能力差,稳定性差,维护困难,如粘度大不易维护,含有氨水难维护,而氟硼酸盐体系有较强的腐蚀性,对PCB基材,抗蚀剂膜,设备和环境有很强的腐蚀和污染,所以焦磷酸盐镀液和氟硼酸盐液不被选用。
②镀液性能的稳定性:稳定性取决于镀液成分的稳定和添加剂作用性能稳定,硫酸盐镀液成分较稳定,随着温度的变化不会发生副反应,PH值的控制也简单,而添加剂也较稳定,一般室温下不会发生较多的副反应产物,而镀液受污染之后较易处理,通常采用分极电解除去金属杂质及进行碳处理除去有机污染,而其它镀液在稳定性上都存在控制困难和副产物难以除去的问题。
③抗污染能力:是指镀液体系对杂质影响的忍耐程度,它决定着镀液的实用工艺性的好坏,在各种镀铜液体系中,硫酸盐体系对杂质的影响最不敏感,而焦磷酸盐体系抗杂质污染能力最差。
④操作维护的难易度:如果镀液体系成分过多、复杂,原材料供应狭窄、添加剂品种多的话,则操作维护都要求较频繁,同时镀液的分析,调整麻烦,这样实际生产应用也就困难,而硫酸盐镀液相对地在维护保养上相对简单。
⑤要获得高分散能力和高厚径比的电镀效果,必须选择高酸低铜镀液,同时,要获得高韧性的镀层,也必须选择高酸低铜及中低电流密度的条件,才能得到细致的沉积铜层,使沉积铜层拥有高韧性。
2 酸性硫酸铜镀液的电极反应:
①阴极:主反应:Cu2++2e→Cu 副反应:Cu2++e→Cu+ 2Cu+→Cu2++Cu 2Cu++H2O→-Cu2O+2H+ Cu2O 、铜粉分散在镀液中,通电时易沉积在阴极表面及镀层中,使镀层粗糙呈海绵状,毛刺。
②阳极:可溶性阳极 Cu-2e—Cu2+(主反应)
3 CuSO4 的作用及影响趋势:
①溶液中Cu2+的有效浓度:Cu-2e→Cu2+ CuSO4 →Cu2++SO42- H2SO4 →2H++SO42- 从上三式可看出,Cu2+的有效浓度取决于CuSO4的浓度,H2SO4的含量,阳极溶解状况及溶液温度,一般地,阳极溶解快,H2SO4含量低,CuSO4含量高,则Cu2+的有效浓度就高。
②Cu2+ 的影响; 当Cu2+的有效浓度低,则允许的Dk上限值低,沉积速度慢,电流效率低,镀层结晶细致,抗蚀性好,镀液的分散能力和深镀能力好,但镀层易烧焦,光亮度,整平性稍差。当Cu2+的有效浓度高,则允许的Dk上限值高,沉积速度快,电流效率高,镀层光亮整平性好, 但镀层粗糙,抗蚀性差,镀液的分散能力和深镀能力差,低电流区易无镀层,且可能有CuSO4结晶析出。
4 H2SO4的作用和影响趋势:
①作用: 降低溶液的电阻,提高镀液的导电性
降低Cu2+的有效浓度,提高镀液的分散能力
抑制Cu2+,Cu+的水解
促进阳极的化学溶解
②影响趋势:含量低时,则Cu2+的有效浓度高,镀液的分散能力差,Cu2+、Cu+的水解趋势增大,镀层易粗糙,疏松,毛刺,溶液的导电性差,含量高时,溶液的导电性好,阳极的化学溶解性好,镀层细致,但光亮度整平性下降。
5 Cl-的作用及影响趋势:
①作用: 阳极活化剂,促进阳极溶解
降低加有其它光亮剂所产生的内应力,使镀层具有一定的延展性,韧性。
提高镀层的光亮度和整平性。
②阳极活化的作用机理:通电时,Cu-e→Cu+(快速) Cu+-e→Cu2+(慢速),负电的Cl-聚在阳极表面形成CuCl胶体,其吸附在阳极表面,阻止Cu+的产生,促进Cu2+的形成。
③影响:含量低时,阳极溶解性差,镀层内应力大,镀层表面产生不平且光亮度差,甚至有粗糙,毛刺,含量高时,过多的CuCl胶体膜包在阳极表面,阳极易钝化,同时CuCl胶体进入镀液,Cu+歧化反应,形成的铜颗粒小(但比电解铜结晶大),难以过滤除去,夹杂在镀层中形成粗糙,镀层光亮度下降和低电流区不亮。
6 光剂:
①作用: 有光亮和整平作用。
提高允许的Dk范围。
提高镀液的分散能力和深镀能力。
②含量:含量低时,则镀层的边缘处,凸起处易产生毛刺和烧焦,而低电位处特别是深孔处易无镀层,镀层的光亮度整平性差,含量高则镀层易产生
雾状,电流效率低。
7 阳极:
①阳极采用含Cu99.9%,含磷0.04~~0.3%的铜板(铜球),在通电溶解时,表面生成一层有一定韧性的黑色Cu3P膜,一方面它不影响阳极的导电性能
因而不会影响阳极的正常溶解,另一方面它能限制Cu的过分溶解,限制Cu+的产生。磷含量高,膜厚且坚实,阳极溶解困难,含量少时将有较多的Cu+
在溶液中存在,镀层粗糙,毛刺,且光亮剂消耗也加快。
②铜阳极装入钛篮,并套上阳极袋,以防止阳极泥进入镀液。
③阳极与阴极的面积比为1.5~~2:1时,阳极能正常溶解。
8 杂质:
①由于过量硫酸的存在,且Cu2+的电极电位较其它金属离子为正,其它金属离子不易产生共沉积,因而金属杂质的允许含量可略高一些。
②一般金属杂质离子可采取分级电解,分别除去各个电级电位段的金属离子。
③镀液中的有机物的分解产物过多会影响镀层的光亮度,降低分散能力,可加入5~~7ml/L的双氧水,搅拌1~~2h,加热至60~~70℃,继续搅拌2h,以
驱除过量的双氧水,再加入5~~7g/L的活性炭,搅拌1h后静置8h以上,然后过滤即可。
9 温度:
①受到光剂的作用温度范围限制,镀液的最佳温度范围为15~~300C。
②温度低,则Cu2+的有效浓度低,允许的Dk范围窄,沉积速度慢,电流效率低,镀层结晶相对细致紧密,镀层光亮度,整平性稍差,高电流区易烧焦,低电流区易无镀层。
③温度高,阳极溶解快,Cu2+的有效浓度高,允许的Dk范围宽,沉积速度快,电流效率高,镀层结晶粗糙,光剂的消耗速度快,镀液的分散能力和深镀能力差。
10 电流密度Dk:
①Dk的允许值是由温度,CuSO4含量决定的。
②Dk小,阴极极化作用小,沉积速度慢,电流效率高,低电流区易无镀层。
③Dk高,阴极极化作用大,沉积速度快,电流效率低,镀层结晶相对细致,光剂消耗速度快,但过分的高则高电流区镀层粗糙,有树枝状的条纹和镀瘤。
11 过滤:①作用:除去镀液中的悬浮杂质,包括铜粉,光剂的分解产物。
②设置:出口在槽底,进口在液面下约10cm处,进出口管对应在槽子的对角线上。
③滤芯:聚丙烯(PP)材料,精度在5~~10um,循环量为2~~5循环/h。
12搅拌:
①作用:减轻Cu2+的浓差极化的趋势,提高允许的Dk的上限值,加快沉积速度。
使阴极区的H+得到及时的补充,减少Cu2+,Cu+的水解而使镀层产生毛刺和粗糙的可能。
使镀液中的Cu+氧化成Cu2+,避免铜粉的产生。
②方式:通常有压缩空气搅拌和阴极移动。
阴极移动; 与阴极表面成45℃角方向移动,幅度40~~50mm,频率16~~20次/min。
空气搅拌:在槽底设置一与阴极杆平行导气管,开孔方向与垂直成15℃角。空气搅拌必须对空气进行油水分离并过滤,除去油分和机械杂质。
13 开缸操作:
①洗缸:
加入自来水,清洗缸底,排去自来水。
加入2/3体积的自来水,缓慢加入10%的NaOH并充分搅拌使之溶解。
将钛篮及阳极袋浸入NaOH液中浸泡8h。
排掉溶液并用自来水冲洗干净。
加入2/3 体积的自来水,缓慢加入5%的H2SO4,将钛篮和阳极袋浸入4~~8h。
排掉H2SO4液,并用自来水和DI水先后冲洗干净,然后取出钛篮和阳极袋备用。
②加入2/3体积的DI水(在一干净的备用桶中),缓慢加入120ml/L的CP级H2SO4,并升温至60~~70℃。
③缓慢加入70g/L的CuSO4,充分搅拌使之溶解,并补充液位。
④降温至30~~40℃,缓慢加入5~~7ml/l的双氧水,搅拌1~~2h。同时加热。
⑤升温至60~~70℃,加入5~~7g/L的活性炭,并搅拌1~~2h(停止加热)。
⑥静置8h,用沉有助滤粉的新棉芯过滤至合格。(用滤纸过滤溶液无碳粉。)。
⑦用新棉芯抽至铜缸中,同时挂上阳极及阳极袋(阳极清洗按清洗方法进行),补充液位。
⑧由化验室分析并调整成分。
⑨拖缸分级电解:0.5A/dm2*4h 1.0A/dm2*2h 1.5A/dm2*2h
⑩做赫氏槽试验并调整光剂。
试板合格后生产。
三镀镍原理
1 概述:
①镍具有银白色的金属光泽,密度8.9g/cm3,熔点1453℃,原子量为58.7,通常显示的化合价为+2价,标准电极电位为-0.25V,电化当量为1.095g/A*h,在常温下,对水和空气均是稳定的,易溶于稀酸。
②用于PCB的镍镀层在金和铜之间,厚度为3~~6um,阻止铜和金的相互扩散,提高电子互连的可靠性。
③新鲜的镍镀层表面易被空气氧化成一层极薄的氧化层而影响可焊性或电镀时与其它金属的结合力,半光亮镍相对光亮镍,内应力低些,可焊性好些,而光亮镍延展性好些。
2 电极反应:
①阳极: Ni-2e——Ni2+ (主反应),当阳极钝化或阴阳极面积比小于1:1.5时有: 2Cl--2e——Cl2 4OH- -4e——2H2O+O2
②阴极: Ni2+ +2e——Ni (主反应) 2H+ +2e——H2 (副反应)
3 NiSO4·7H2O的作用及影响趋势:
①是溶液中Ni2+的主要来源,其含量一般控制在250~~350g/L。
②含量低,Ni2+的有效浓度低,溶液的分散能力好,镀层结晶细致,但允许的Dk上限值低,沉积速度慢,电流效率低。
③含量高时,Ni2+的有效浓度高,允许使用的Dk高,沉积速度快,含量过高时,阴极极化降低,分散能力差,同时电解液的带出损失大。
4 NiCl2·6H2O的作用及影响趋势:
①该化合物中的Cl-为阳极活化剂,当镀液中的Cl-含量不足时,阳极容易钝化。
②NiCl2还能提高溶液的电导率,从而降低达到额定电流时的槽电压。
③但含量过高时,会使镀层应力增加。
5 H3BO3的作用及影响趋势:
①在镀镍溶液中起缓冲作用,它能稳定溶液的PH值,当其含量低于20g/L时,缓冲作用较差,含量达到28~~35g/L时,缓冲作用较强。
②对于在较低PH值下使用的镀镍液,H3BO3的缓冲作用尤其重要,因为H+浓度高,其放电会引起阴极区的PH值较快的升高,以致于生成
Ni(OH)2沉淀等杂质,这些杂质与镍一起沉积,夹杂在镀层中。
6 添加剂(光剂):
①改善和细化镀层结晶,使镀层均匀,平整,同时降低镀层的内应力,提高延展性。
②含量过高,则应力增大,脆性变大,结合力变差,加大镀缸污染。
7 PH值:
①镀镍溶液的PH值对电解液性能,镀层外观,力学性能有较大影响。
②PH值高时,Ni2+水解成Ni(OH)2的趋势增大,阴极极化作用增大,镀液的分散能力好,H+浓度低,阴极电流效率高。过高时,则Ni(OH)2沉淀过多,镀液浑浊,且不利于气泡逸出,产生针孔,镀层中也可能夹杂有Ni(OH)2 ,镀层结晶粗糙,并影响镀层的力学性能。
③PH低时,阳极溶解性好,采用较高的Dk和温度,阴极电流效率低,低电流区及凹入处易无镀层,镀层硬度不高,韧性好。
8 润湿剂:
①实质上是一种表面活性剂,它降低液体的表面张力,使氢气泡不易在阴极表面上滞留,从而减少针孔的生成。
②一般使用十二烷基磺酸钠作润湿剂,过多时易使镀层发雾,发花。
9 温度:
①促进盐类溶解,提高Ni2+的有效浓度,从而提高允许的Dk上限值。降低溶液的电阻,提高导电性,降低镀层的内应力,提高镀层的延展性,但盐类水解的趋势增大,镀液混浊,易出现针孔,分散能力下降。
②影响趋势;温度低,则阴极极化作用增强,允许的Dk上限值低,沉积速度慢,电流效率低,镀层结晶细致紧密,高电流区易烧焦,镀层均镀能力和深镀能力好。
温度高,则阴极极化作用小,允许的Dk上限值高,沉积速度快,电流效率高,镀层结晶粗糙,有镀瘤,镀液均镀能力,深镀能力差。
10 电流密度Dk:
①决定因素:Dk是由温度,Ni2+的有效浓度,PH值,搅拌等因素决定,一般地,Ni2+的浓度高,温度高,PH值低,有搅拌时,允许使用的Dk高,反之亦然。
②Dk高,阴极极化强,结晶相对细致,沉积速度快,电流效率低,但过高,则镀层粗糙,烧焦,有镀瘤,针孔多。电流密度低,则阴极极化弱,沉积速度慢,电流效率高,低电流区颜色暗,易无镀层。
11 搅拌:
①作用:加速传质过程,减轻浓差极化,提高允许的Dk上限值,加快沉积速度。使阴极区的H+得到及时的补充,避免PH值升高,产生Ni(OH)2沉淀,夹杂在镀层中,使应力增加,有利于H2从阴极表面逸出,减少针孔。
②设置:阴极移动 与阳极表面成45℃角,幅度25~~50mm,频率16~~20次/min。(还有一种在阴极杆上沿阴极杆方向的移动。)
空气搅拌 空气要洁净,设置在槽底,开口与垂直成15℃角。
12 过滤:
①作用:除去镀液中的悬浮杂质,光剂分解产物等。
②要求:材料PP,精度5~~10um,循环量2~~5循环/h。
13 阳极:
①材料:一般使用含硫镍阳极,镍含量为大于99.99%,其形状有镍饼,镍角,镍球,少量的硫使阳极溶解得更均匀,且以不溶性硫化镍保存在阳极袋中,不会污染镀液,硫化镍残渣可吸附镀液中的Cu2+帮助净化镀液。
②装置:存放在钛篮中,挂在阳极杆上,并套上阳极袋。
③阳极与阴极的面积比:阳:阴=1.5~~2:1。阳极不易钝化。
14 杂质:
①铜:允许含量为0.01g/L,它会使低电流区的镀层变暗,可用电解法除去。
②锌:允许含量为0.02~~0.1g/L,在低电流区产生暗色条纹,甚至形成亮黑条纹,用电解法除去。
③铁:允许含量为0.03g/L,铁易形成Fe(OH)3沉淀,使镀液混浊,易产生针孔,夹杂在镀层中易形成黑点和粗糙的镀层,镀层脆性增加。
15 开缸操作:
①用自来水冲洗缸壁,缸底,然后排去。
②加入2/3体积的自来水,加入10%的NaOH,并补充液位,将钛篮,阳极袋一起浸泡8h。
③排去NaOH液,用自来水冲洗干净,加入2/3体积的自来水,加入5%的H2SO4并补充液位,将钛篮一起浸泡4h。
④排去H2SO4液,用自来水,纯水先后冲洗干净缸体,钛篮和阳极袋备用。
⑤将一碳处理好的镀液引入缸中(碳处理见操作要求)。
⑥补充液位,取样分析并调整。
⑦分级拖缸电解。
⑧做赫氏槽并调整光剂。
⑨试板合格后生产。
四 镀锡原理
1 概述:
①锡原子量为118.69,原子价位有+2和+4。标准电位有-0.136V 和0.15V,电化学当量为2.2g/A*h,密度为7.28g/cm3。
②锡为白色金属,无毒,延展性好,镀层致密,孔隙小,在中性和碱性环境中较稳定,不易发生化学反应。
③在PCB中用作印制板碱性蚀刻时的线路抗蚀保护层(镀纯锡)。
2 电极反应:
①阴极: Sn2+ +2e—Sn 2H+ +2e—H2 从标准电位看,应是还原出H2,但H2存在极化超电位,故Sn先被还原出来。
②阳极: 可溶性锡条或锡球 Sn-2e—Sn2+
3 SnSO4:
①提供Sn2+的主盐,纯度要求达99.99%,不能用化学纯的SnSO4。
②Sn2+高,则允许的Dk高,分散能力下降,严重导致Sn2+水解和氧化成Sn4+,镀层粗糙,镀液易变浑浊,Sn2+低,则允许的Dk低,高电流区易烧焦,电流效率低。
4 H2SO4:
①作用:提高溶液的导电性,提高深镀能力 ,抑制Sn2+的水解,抑制Sn2+氧化成Sn4+。
②但H2SO4含量不能过高,否则析氢多,电流效率低,且阳极化学溶解增强,Sn2+高,分散能力和深镀能力变差。
5 添加剂:(主要有两类)
①稳定剂:有甲酚磺酸,对苯二酚,邻苯二酚,抗坏血酸等,可使Sn4+还原成Sn2+。
②光亮剂;有细化结晶,增光作用。
③分散剂:是表面活性剂,促进光亮剂的溶解。
含量低时,光亮效果差,均镀性差,孔隙多,过多则产生较多的有机污染,镀层脆性。
6 电流密度Dk:
①由温度,SnSO4的含量而定,温度高,SnSO4含量高则允许的Dk高。
②Dk高,则沉积速度快,结晶粗糙,孔隙大,抗蚀性差,电流效率低,Dk低,沉积速度慢,低电流区无镀层。
7 温度:
①一般受到所使用添加剂的最佳温度范围限制。
②温度高,阴极极化弱,镀层粗糙,沉积速度快,电流效率高。添加剂消耗快,有机污染快,Sn2+易氧化成Sn4+,产生沉淀,镀液混浊。
③温度低,则允许的Dk低,沉积速度慢。
8 搅拌:
①考虑到Sn2+易氧化成Sn4+,故不能用空气搅拌,只能用阴极移动。
②可以除去阴极表面的浓差极化。使Sn2+得到及时的补充,提高Dk允许的上限值和电流效率。
9 过滤:
①除去镀液中的悬浮杂质,光亮剂的分解产物等。
②出口在槽底,入口在液面下100mm处,出入口成对角设置。
③精度为5~~10um,循环量为2~~5循环/h。
10 阳极:
①锡阳级没有阳级膜,纯度要求99.99%以上。
②外套阳级袋,防止阳极泥进入镀液。
③阳极与阴极的面积比为2~~3:1。
11 杂质:
①锡缸的杂质主要为二价离子和有机污染,用低电流长周期电解,可把杂质金属还原出来(0.2~~0.5A/dm2*8~~10h)。
②阴极采用瓦楞形不锈钢板,瓦楞形状可形成高低电位,有利于阳极的活化及不同金属的还原。
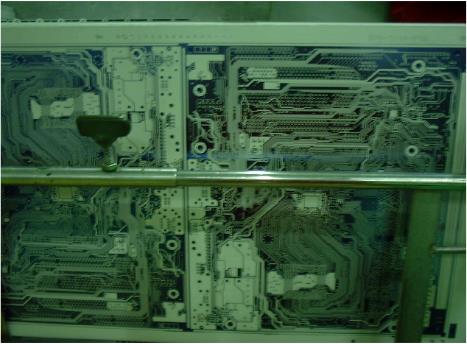
服务生产高端PCB产品
2-40层PCB高可靠制造
盲埋孔(HDI)1,2, 3阶
软硬结合线路板
背钻,金手指以及超厚铜板
相关参考