深孔钻怎样加工s136H的材料(基于Moldflow的汽车方向盘内饰件注射模设计)
Posted
篇首语:春衣少年当酒歌,起舞四顾以笑和。本文由小常识网(cha138.com)小编为大家整理,主要介绍了深孔钻怎样加工s136H的材料(基于Moldflow的汽车方向盘内饰件注射模设计)相关的知识,希望对你有一定的参考价值。
深孔钻怎样加工s136H的材料(基于Moldflow的汽车方向盘内饰件注射模设计)
随着汽车行业的飞速发展,消费者对汽车内饰件的要求越来越高,不仅对装饰性的外观要求高,同时对内饰件的功能性、安全性及工程属性的要求也越来越高,专注汽车模具设计模流分析技术分享,这些知识都是本人10多年汽车模具设计模流分析的相关经验的总结和摘取,如有想了解这方面技术的朋友,可以私聊我,发一些关于这方面资料给您。
为了满足汽车内饰件日益增长的要求,必须从模具设计阶段开始优化,采用Moldflow等CAE软件对塑件在成型过程中可能存在的缺陷进行分析,制定解决方案,提前预防缺陷的产生,然后通过调节进料方式、更改塑件结构或采用3D打印等新兴制造工艺提高塑件的成型质量。
//
塑件工艺分析
//
塑件为某轿车方向盘上的内饰件,与另一产品装配在一起固定在方向盘下方,在车内可直接看到该塑件的外表面,故外观要求及精度要求高。

图1 汽车方向盘内饰件
塑件结构如图1所示,外形尺寸为126.3mm×141.7mm×57.6mm,体积为29.78cm3,材料为PC+ABS,采用1模1腔结构成型,收缩率根据塑件尺寸、壁厚及材料物理性能推荐设置为0.5%,表面镀铬。塑件壁厚均匀,主壁厚为2.5mm。
主要成型特点如下:①外观面不允许有任何成型缺陷,如浇口痕迹、应力痕、熔接痕、缩痕、推杆痕、飞边等;②塑件形状为“U”形,成型时容易发生内缩变形;③塑件成型后需进行表面镀铬,在设计阶段需考虑电镀时的上挂问题。
//
模流分析制定成型方案
//
在UG软件中先初步观察塑件结构,了解塑件的大致情况和基本参数,然后将3D模型导入CAD Doctor软件中进行圆角去除、缝隙填补等修整工作,接着再将修整好的3D模型导入Moldflow软件中进行网格划分、修整网格、厚度分析和材料选择等分析前的处理操作,然后对塑件进行浇口位置、成型窗口和初步的填充分析,结果如图2所示。
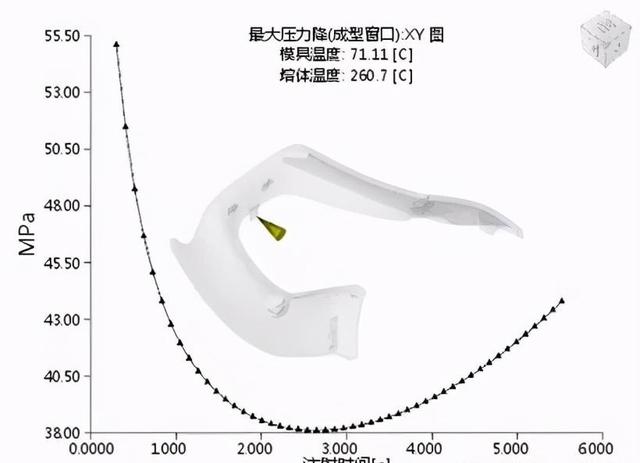
图2 塑件成型窗口-最大压力降
由Moldflow分析结果可知,单点进料可以满足塑件的注射要求,为了保证塑件的成型质量,采用热流道转普通流道的形式。
从塑件的分型线来看,型腔区域都是外观面,不允许有浇口痕迹,无法采用点浇口,而塑件周边结构的原因导致无法放置侧浇口。
考虑到注射后电镀的上挂问题及塑件“U”形形状可能导致内缩变形,在塑件“U”形的开口处增加了一段辅助流道,一是为了撑住塑件“U”形开口减少内缩变形;二是为了电镀时有上挂的位置,同时塑件末端存在尖角,电镀时容易引起电流增加,造成“烧铬”或“堆镀”等现象,可增加两段细长的流道以平衡电流;三是将填充末端移到了辅助流道上,便于排气。
最后通过分析塑件的分型线、外观要求、塑件结构、电镀上挂等需求与Moldflow软件分析的结果进行综合考虑,制定成型方案如下:进料方式为热流道转普通流道单点进料,采用潜伏式浇口,流道截面形状采用“U”形,如图3所示。
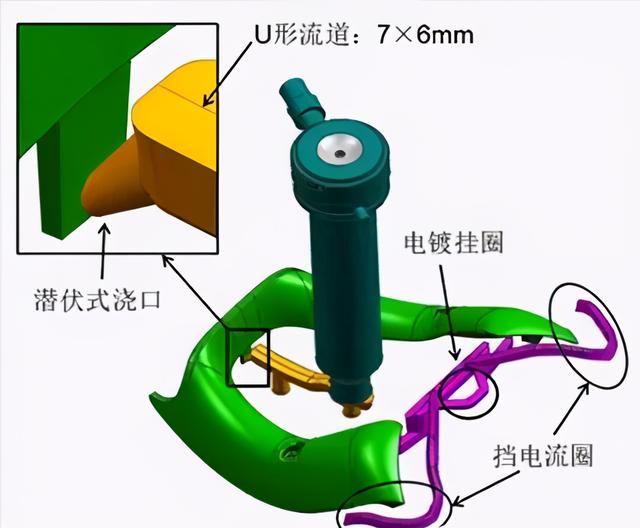
图3 成型方案
成型方案确定后,为降低塑件在成型过程中产生明显缺陷的风险,减少试模修模次数,提高模具生产效率,再次通过Moldflow软件对塑件成型过程进行更全面的分析,包括填充、压力、体积收缩率、气穴、模温及变形等,大部分结果都满足要求,其中填充时间、V/P切换时的压力模拟结果分别如图4和图5所示。
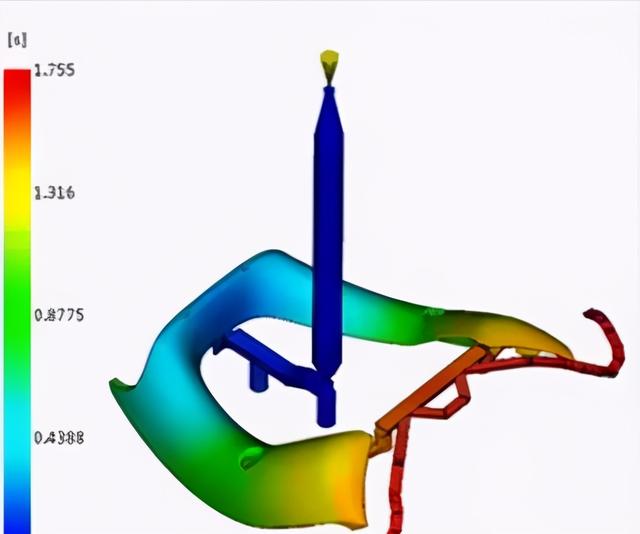
图4 填充时间
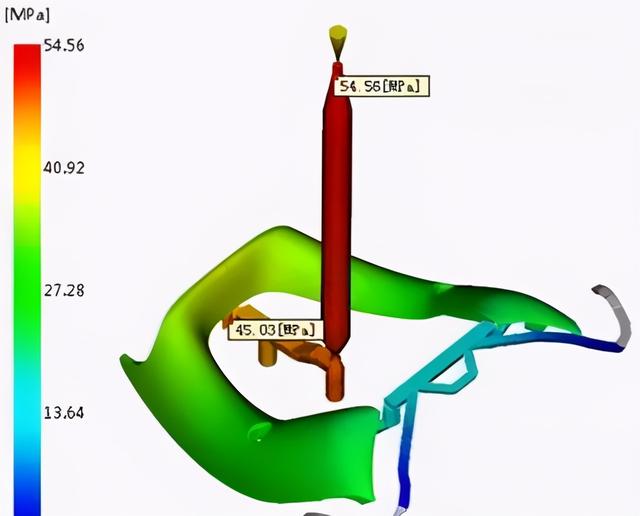
图5 V/P切换时的压力
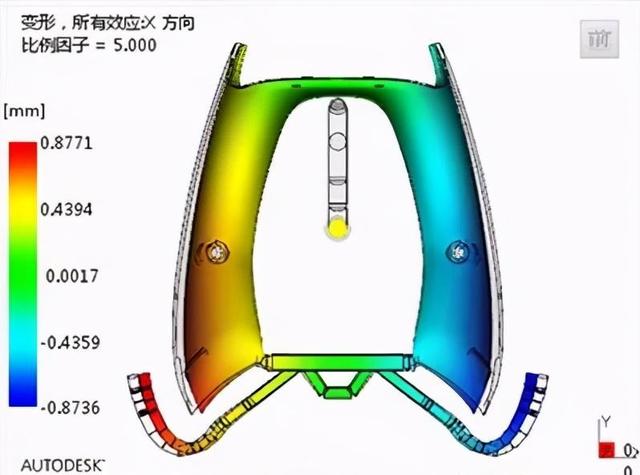
图6 传统水路X方向变形
通过分析发现即使增加了辅助流道,塑件内缩变形依然较大,如图6所示。
//
模具结构设计
//
1 成型系统设计
塑件外观面无特殊结构,成型后不会留在型腔内,为了提高模具制造效率和修模效率,动、定模都采用了镶拼结构。由于塑件后续有电镀工艺,对塑件表面粗糙度要求高。塑件有3处结构无法正常脱模,需要采用辅助脱模结构,其中一处采用动模滑块,另外2处采用斜推杆。塑件要求无困气、黑点、填充不满等缺陷,在定模型腔板镶件分型面上开设多处排气槽用于排气。
定模型腔板镶件材料采用加硬的S136H钢,动模型芯镶件材料采用1.2316钢,滑块和斜推杆都采用8407钢,定模板、动模板及模架的其他板都采用P20钢。

图7 仿形水路
为进一步解决塑件内缩变形的问题,定模型腔镶件采用了仿形水路,如图7所示,仿形水路是完全仿造塑件形状进行设计的,从水路到塑件的距离基本一致,冷却更均匀,减少塑件因冷却不均匀引起的变形,使定模温控效果更佳。仿形水路无法通过传统的加工方式制造,整块定模型腔板镶件采用3D打印工艺制造。
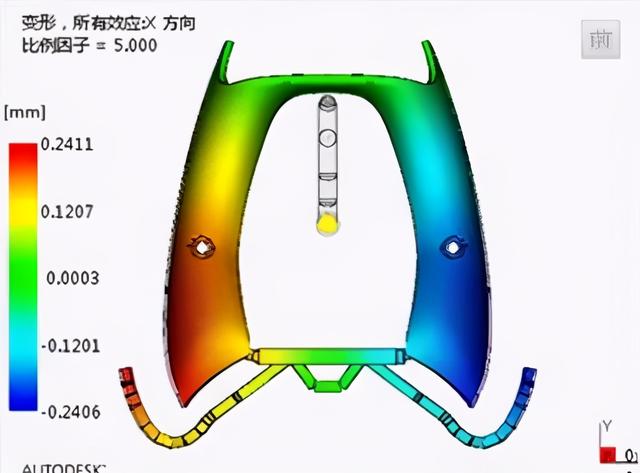
图8 仿形水路X方向变形
在Moldflow软件中将定模水路由之前的传统水路改为3D打印的仿形水路再次分析之后,发现塑件内缩变形有明显改善,如图8所示,与图6对比可见塑件内缩变形明显减少。
2 冷却系统设计
塑件的表面粗糙度与尺寸要求高,所以温控系统必须设计合理,以保证塑件变形小和表面光洁。为节约成本,动模采用传统深孔钻式的冷却水路,且动模型芯面是对应塑件的装配面,表面要求相对定模型腔面要低一些。
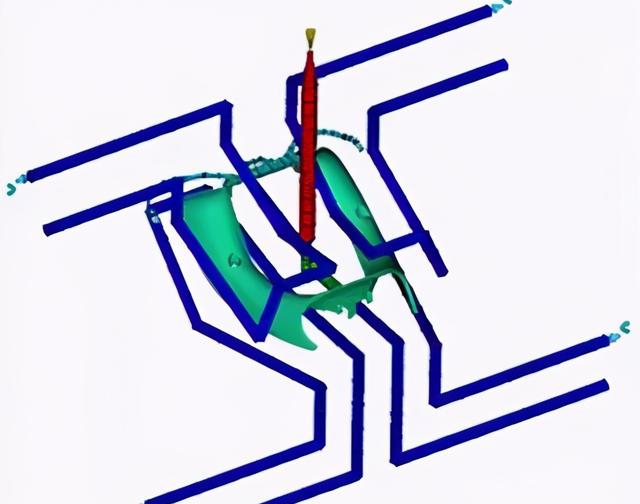
(a)传统冷却水路
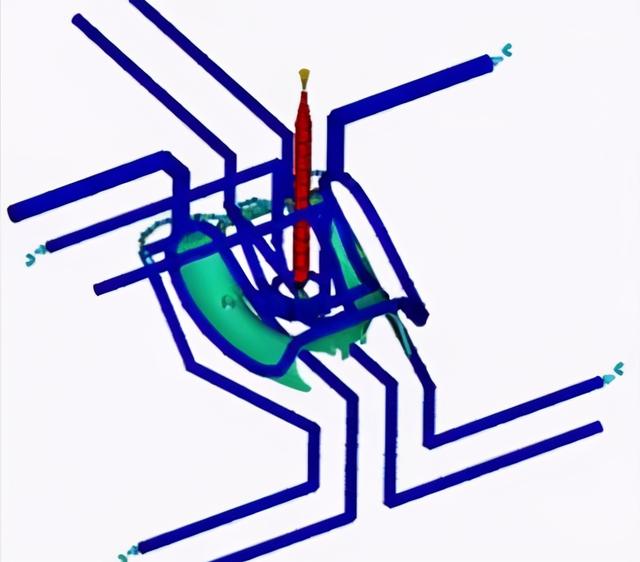
(b)3D打印仿形水路
图9 冷却水路排布
模具定模设计3组水路,动模设计2组水路,其中定模有一组是为防止热流道浇口处产生“拉丝”现象而设计的热流道冷却水路,该组水路直径为ϕ6mm,其余动、定模水路直径均为ϕ8mm,图9(a)所示为优化前的传统水路,图9(b)所示为优化后的3D打印仿形水路。
3 推出系统设计
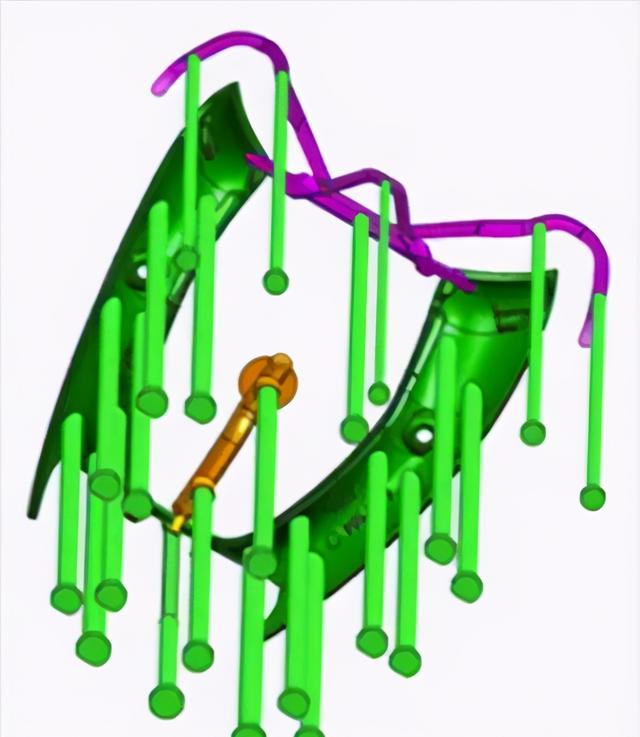
图10 推出系统
模具采用推杆推出的形式,如图10所示,其中进料处的浇口凝料有较大的脱模角度,无法在此处设置圆形推杆,只能采用矩形推杆,塑件还有2处需要采用斜推杆推出。模具设置4根推板导柱,采用弹簧复位的形式,同时动模座板安装了复位保护开关,防止撞模。
//
模具结构
//
模具最大外形尺寸(除去热流道接线盒)为400mm×450mm×415mm,属于中型注射模,模具结构如图11所示。
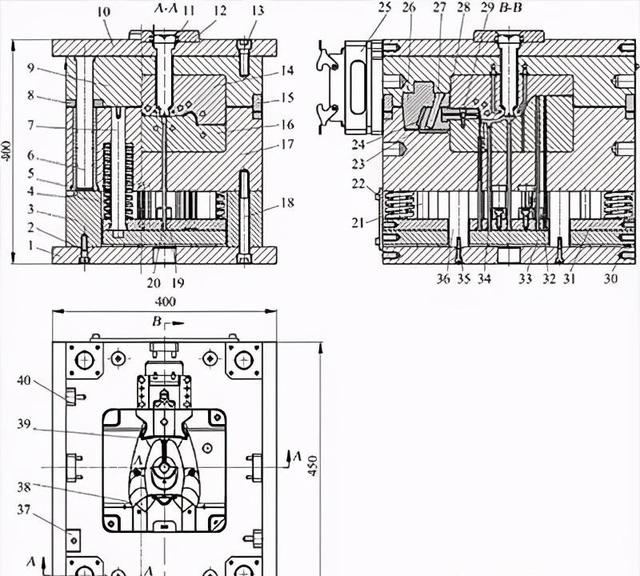
图11 模具结构
1.动模座板 2.螺钉 3.垫块 4.弹簧 5.导套 6.导柱 7.复位杆 8.平衡块 9.定模板 10.定模座板 11.热喷嘴 12.定位圈 13.螺钉 14.型腔板镶件 15.定位块 16.型芯镶件 17.动模板 18.螺钉 19.限位螺钉 20.拉料杆 21.推板导柱 22.挡尘板 23.滑块座 24.耐磨块 25.热流道接线盒 26.楔紧块 27.斜导柱 28.滑块 29.螺钉 30.限位钉 31.推杆固定板 32.斜顶座 33.推板 34.推杆 35.螺钉 36.支撑块 37.计数器 38.斜推杆 39.浇口镶件 40.锁模块
模具浇注系统采用热流道转普通流道潜伏式浇口单点进料的方式,确保塑件的成型质量及后续的功能性达标,同时为了减小塑件结构引起的内缩变形,定模冷却系统采用了3D打印仿形水路,冷却效果更佳,塑件变形小,达到了客户要求,推出系统采用了推杆推出的形式。
该设计方案可为同类塑件因冷却不均引起变形太大的设计案例提供参考,在确保生产成本的基础上可以考虑动、定模都采用3D打印仿形水路的方式,冷却效果更好
相关参考