液压泵柱塞加工(高精铜转子柱塞孔珩磨加工及调试方法)
Posted
篇首语:月与灯依在,不见去年人本文由小常识网(cha138.com)小编为大家整理,主要介绍了液压泵柱塞加工(高精铜转子柱塞孔珩磨加工及调试方法)相关的知识,希望对你有一定的参考价值。
液压泵柱塞加工(高精铜转子柱塞孔珩磨加工及调试方法)
液压柱塞泵铜转子上有9个柱塞孔,9个柱塞孔与转子中心轴之间成14°夹角均布,为满足转子柱塞孔与柱塞外圆的高精度间隙配套关系,因此,转子上9个柱塞孔的加工精度要求特别高。
9个柱塞孔的一致性0.005max,每个柱塞孔圆柱度(圆柱度由锥度、椭圆度、直线度组成)0.002max,柱塞孔粗糙度要求为Ra0.1。现有柱塞孔的研磨是采用手工加工,手工加工难度大,对加工者的操作技术要求高,不能很好的保证零件的加工质量,加工效率低。
高精度铜转子柱塞孔的珩磨加工方法,该方法是利用自制夹具,将转子倾斜14°固定在立式珩磨的工作台上,使转子上的其中一个柱塞孔位于立式珩磨的珩磨杆底部并与珩磨杆同轴,利用珩磨杆上的圆柱形W20油石作为加工刀具,对该柱塞孔进行珩磨加工;加工过程中使用立式珩磨专用珩磨油进行冷却和润滑;圆柱形W20油石在加工过程中通过改变转速和上下运动速度在柱塞孔的孔壁上产生夹角为40~45°的交叉细网纹,以获得柱塞孔良好的动态滑动性能。加工过程包括粗珩、半精珩、精珩和抛光过程;粗珩时,主轴速度为20~40rpm,进刀量为0.08~0.1mm/min;半精珩时,主轴速度不变,进刀量为0.06~0.08mm/min;精珩时,主轴速度不变,进刀量为0.04~0.06mm/min;抛光时,在无进刀量的情况下,轴向反复走刀2秒。加工完一个柱塞孔后,松开夹具将转子旋转一定角度后固定,再加工另一个柱塞孔,直至完成转子上的所有柱塞孔的加工。
以材料牌号为ZQSb3.5-20的转子零件加工为例,该型号转子的硬度为HB≤68。如要加工的零件将转子固定在自制的夹具上。转子首件加工对刀采取的过程和措施转子首次首件加工时,需要修整油石,用标准件对刀定义出油石的加工初始直径,并对刀给出一个冲程周期的顶端位置和底端位置,通过调整刀具向下和向上运动速度来调整网纹角度,并编程给出小余量光磨时间,以保证粗糙度要求。
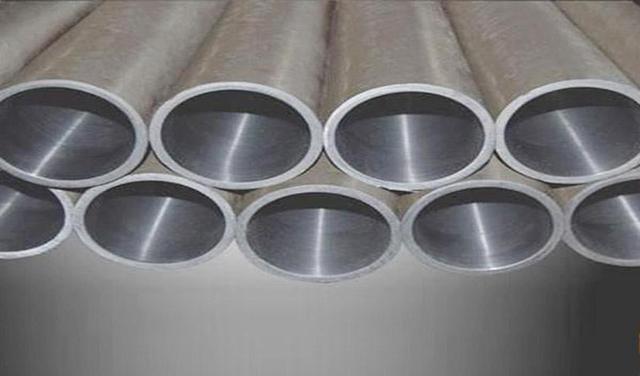
转子的加工过程介绍:机床以停止状态时珩磨油石所在位置为机床的坐标零点,机床开始运转时,定点探头快速弹出,刀具快速移动到探头位置短暂停下,等探头快速缩回后,刀具以相对缓慢的速度进入转子内,并开始从油石的程序中对刀时所给定的初始直径位置,油石的加工直径逐渐变大,并开始接触转子柱塞孔,开始实质性加工过程。
加工方式的控制因转子柱塞孔与转子中心所形成的角度为14°,转子采用立珩加工方式进行加工时,需保证所加工的柱塞孔与冲程方向相同,因此需采用自制的专用夹具,保证转子孔加工的方向,转子珩磨加工过程经过一段时间的摸索,得出锥度主要靠调整程序来实现,椭圆度主要靠合理的装夹定位来实现,因此转子的装夹过程就显得至关重要。
经过一段时间的经验总结得到如下装夹定位需要注意的地方:需保证转子装夹定位端面无任何异物,加工前用手感触转子定位大端面上应无毛刺高点,并用棉花等蘸上干净的汽油将转子定位大端面和定位孔清洗干净,并将夹具上与相贴合的定位面和定位圆柱销擦拭干净,将转子放入夹具上后,应转动转子使其充分和夹具贴合;将夹具上的限位锥度销放入转子柱塞孔进行定位时,既要旋转锥度销使其与转子柱塞孔充分贴合定位,又不能使用较大力气压锥度销,否则会使转子倾斜导致椭圆度不能满足要求;转动定位销至销子与转子内孔更好的接合,以保证珩磨杆与孔的位置的垂直度;将转子固紧在夹具上时,力量必须对称和均匀,先用手工两边同时逐步拧紧之后,用扳手单边分至少5次逐步两边拧紧压紧螺钉,不可以单边用扳手使用较大的力拧紧一边螺钉后,再拧紧另一边,否则会导致转子往一边相对倾斜,并造成9个内孔圆柱度0.002max不合格,每个内孔加工后的圆柱度不一致,大部分孔圆柱度会不能满足图纸要求;
转子装上后,注意检查珩磨油是否对准所加工孔,因珩磨油对减少机床磨损、并保证加工粗糙度等有至关重要的作用;总而言之,合理装夹转子是保证其椭度合格的最重要的因素,而以上5点是装夹时容易出错并很重要的装夹因素,而这些因素需要一个有经验的操作者才能实现。
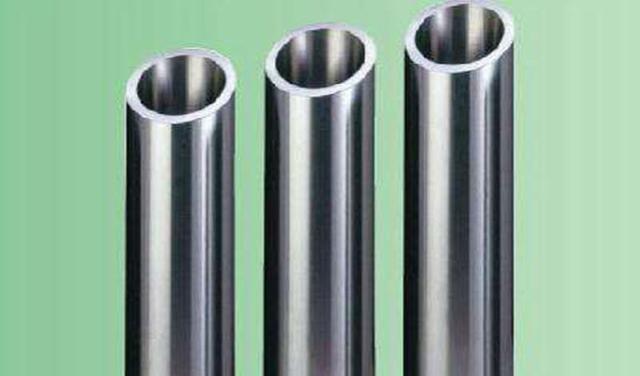
程序调试经过较长一段时间的现场试验加工探索,得出珩磨加工转子时目前较为优化的参数组合,能够稳定地保证转子珩磨加工的尺寸精度、形状精度和表面质量。在程序中,给定的相关主要参数简介:工具连接器型号选择:FAM-0515加工起始直径为:φ15.98主轴转速:300rpm(即每分钟珩磨刀具随主轴旋转300转)冲程长度:26.5(即珩磨油石在转子孔中作单边行程为26.5mm的往复运动)冲程速度:110spm(即每分钟的冲程次数为110次)珩磨交叉网纹角度:42.2度粗珩速度:0.088毫米/分钟粗珩停止直径:15.985毫米(即加工到φ15.985毫米时切换到半精珩模式)半精珩速度:0.04毫米/分钟半精珩停止直径:16.008毫米(即加工到φ16.008毫米时切换到抛光模式)精珩余量:0.002(即加工到φ16.01毫米时切换到抛光模式)精珩进给速度:0.025毫米/分钟抛光时间:2秒抛光进给速度:0(即抛光的过程就是空走的过程)珩磨加工过程中珩磨油石对加工效率和表面质量的影响至关重要,由于长时间的磨削,珩磨油石中晶体面间距不同,在外力作用下晶体沿着面间距大的结晶面被劈开,会使磨粒的强度大幅度降低,导致磨粒的碎裂,从而降低了珩磨油石的磨削性能,最终导致转子内孔出现喇叭形孔、腰鼓形孔等现象,不满足设计要求。
转子珩磨网纹的理论分析加工后的零件表面具有微观网纹结构,实践证明,仅以表面粗糙度来定义承受高摩擦负荷表面的质量是远远不够的,物体表面需具有两个特性功能,一个是物体表面的良好支承性,也就是说尽可能使物体的表面达到一个光滑的平台表面,由此而获得一个良好的动态滑动性能,但是一旦表面太光滑,也就意味着在两个运动物体间需要有足够的润滑油层作为一个滑动媒体。珩磨网纹可起到这个滑动媒体。因此,珩磨网纹对产品工作状态的润滑性和储油性时很有利的。
经过反复的工艺试验及技术探索,使立式珩磨加工在转子柱塞孔的加工过程中得到了首次突破,保证铜转子内孔的高精度加工要求;其生产效率可由原来50台/每月扩大到250~300台/每月,经过批量投入的加工验证。
使用立式珩磨实现柱塞孔的研磨加工,加工完成后的柱塞孔壁上形成的交叉细网纹,有利于润滑油的储存和油膜的保持,从而延长了工件的使用寿命,很好的改善了柱塞孔的动态滑动性能。
加工过程中发热量小,加工表面基本没有热损伤和变质层,不仅能去除较大的加工余量,还能提高柱塞孔的几何精度,降低表面粗糙度。使转子内孔加工得到了突破,采用本发明的方法柱塞孔的粗糙度可以达到Ra0.05~0.01效果非常理想。现有手工加工每月只能加工50台,采用珩磨加工后每月可加工250~300台,大幅度提高了产品加工效率。
相关参考
柱塞泵配件大全(PARKER派克PV092L1K1T1NMRK柱塞泵)
前言:PV092L1K1T1NMRK柱塞泵浇注成型,高精密加工中心及磨削加工,具有较高的机械精度,并具有自润滑作用。在液压系统中轴向柱塞泵是利用柱塞在柱塞孔内的往复运动引起的体积变化而工作。因为柱塞泵的柱塞和柱塞孔均为圆...
柱塞泵各零件零件图(浅析柱塞泵件的热处理工艺方法及注意事项)
柱塞泵是依靠柱塞在缸体柱塞孔中作往复运动而产生的容积变化来实现吸油和压油过程。柱塞泵压力高、排量大、效率高,其结构较齿轮泵和叶片泵要复杂,零件加工精度要求高。柱塞泵的主要零件在工作时都承受压应力作用,...
一、液压柱塞杆设备划伤问题怎么会发生顾名思义,是支持活塞做功的连接部件,大部分应用在油缸、气缸运动执行部件中,是一个运动频繁、技术要求高的运动部件。以液压油缸为例,由:缸筒、活塞杆(油缸杆)、活塞、端...
一、液压柱塞杆设备划伤问题怎么会发生顾名思义,是支持活塞做功的连接部件,大部分应用在油缸、气缸运动执行部件中,是一个运动频繁、技术要求高的运动部件。以液压油缸为例,由:缸筒、活塞杆(油缸杆)、活塞、端...
柱塞式液压泵是一种容积式液压泵,通过柱塞在缸孔内的反复运动,改变柱塞缸内的容量,将低压油吸入油箱,压入系统高压油。柱塞泵因其工作输出压力高、效率高、功率大、变量方便、坚固耐用等优点,广泛应用于工程...
一、液压柱塞杆设备划伤问题怎么会发生顾名思义,是支持活塞做功的连接部件,大部分应用在油缸、气缸运动执行部件中,是一个运动频繁、技术要求高的运动部件。以液压油缸为例,由:缸筒、活塞杆(油缸杆)、活塞、端...
一、液压柱塞杆设备划伤问题怎么会发生顾名思义,是支持活塞做功的连接部件,大部分应用在油缸、气缸运动执行部件中,是一个运动频繁、技术要求高的运动部件。以液压油缸为例,由:缸筒、活塞杆(油缸杆)、活塞、端...
...体中作往复运动造成密封容积的变化来实现吸油与压油的液压泵。柱塞泵结构图柱塞泵动态图径向柱塞泵工作原基本上类似于轴向柱塞泵,也是利用柱塞的往复直线运动完成吸油与压油过程的(见图)。柱塞径向排列在油缸体中,...
液压泵流量压力特性(液压泵柱塞数为何常为奇数?什么是流量脉动量、压力脉动量?)
柱塞泵柱塞数为奇数,如:5,7,9这是为什么呢?目的是柱塞泵为减小瞬时理论流量的脉动性。因为油源的进出油管路的规格、连接方式与配制水平,还有油源自身的工作原理、结构尺寸、加工制作方式与精度、材质,以及油液...
液压泵流量压力特性(液压泵柱塞数为何常为奇数?什么是流量脉动量、压力脉动量?)
柱塞泵柱塞数为奇数,如:5,7,9这是为什么呢?目的是柱塞泵为减小瞬时理论流量的脉动性。因为油源的进出油管路的规格、连接方式与配制水平,还有油源自身的工作原理、结构尺寸、加工制作方式与精度、材质,以及油液...