涡流测厚仪的工作原理(MBD技术在设计与制造协同过程中的实践)
Posted
篇首语:天才就是百分之九十九的汗水加百分之一的灵感。本文由小常识网(cha138.com)小编为大家整理,主要介绍了涡流测厚仪的工作原理(MBD技术在设计与制造协同过程中的实践)相关的知识,希望对你有一定的参考价值。
涡流测厚仪的工作原理(MBD技术在设计与制造协同过程中的实践)
以MBD技术为核心,以PMI报表数据为纽带的数字化产品设计制造的实践方法,在数字化工厂的广泛应用,特别是在复杂产品的研发、生产中,形成全局的信息管理和决策树,将为企业节省大量工期和费用。
作者:张文祥 张宝 | 来源:e-works
0 前言
随着工业与信息化的快速融合与发展,高效数字化生产日渐成为企业发展趋势。MBD为第三代制造设计语言,其基于文档的过程驱动和基于特征的三维表达,与知识库、过程模拟有机结合,读写方便,使设计和制造的一体化成为可能。设计和制造信息共同定义的产品数字模型,其三维参数技术保证了海量设计数据的唯一性、准确性、共享性,为数字化车间实施提供了参数保障。国内对MBD各子系统的单独应用已较普遍,但对MBD协同的应用还不成熟,尚处于技术研究阶段,亟需对MBD在设计与制造的辩证关系和实践策略进一步加深研究。
1 MBD概述
MBD技术是指将产品信息定义到产品数字模型中,产出数字孪生产品,形成保证产品数据唯一性的数字化设计与管理体系,如图1。早在1997年,波音公司就开始研究MBD技术的标准,其数字化设计与制造方法的使用大幅减少关联模型重构耗时,限制或消除因重构引起的出错,实现工艺过程的虚拟验证和装配仿真,大幅提升数据重用,为智能制造奠定数据支撑。
在我国数字化技术相关政策支持下,MBD技术逐步应用,但设计与制造协同并不能有效实施。主要表现为:
MBD规范未统一。行业规范尚处于研究阶段,上下游协作成员在信息交流、共享等方面存在很大偏差,使得设计无法完全按照需求进行定义。
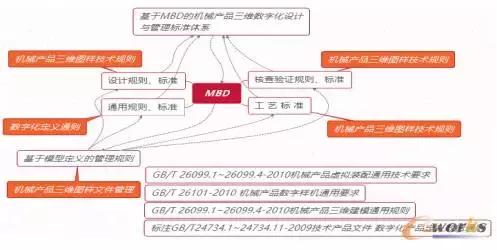
图1 MBD技术标准体系
短时间无法形成基于MBD的生产体系。制造数据的信息化是伴随PLM(Product Life-Cycle Management)出现的生产方式。由于其颠覆了传统生产方式,专业MBD技术人员的严重缺乏致企业无法全面实施该技术。
2 PMI协同
产品制造信息PMI,即所有尺寸、公差与配合等制造信息,按规范直接标注在三维模型上的标注方式(图2),使产品团队能够直接创建、查询和读取制造信息,并使信息数据能够在上下游协作成员间快速调度。
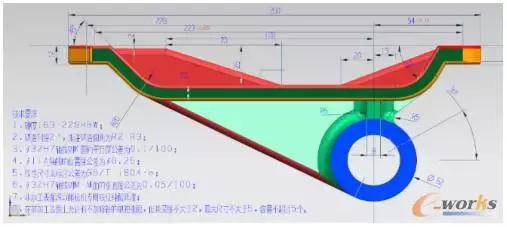
图2 机油泵传动轴支架的PMI三维标注
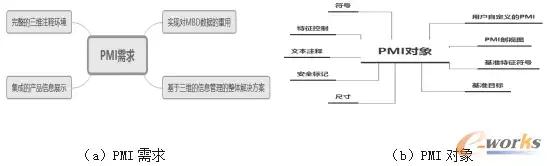
图3 PMI
制造部门对PMI的需求十分迫切,随着产品的精度、复杂度、能效等要求的提高,产品团队对产品设计数据的共享也进一步凸显。如图3(a),包括完整的基于三维的信息管理整体解决方案、注释环境、集成信息展示和数据重用。产品团队能够快速对PMI对象【图3(b)】的编辑,实现全面的设计、制造、装配过程数据的快速重用和直观体现,便是基于PMI协同实现的。
3 容差分析,关键特性识别与关键特定义
3.1 容差分析及模拟
MBD范畴的容差(Allowance)是指容许的特征值的波动范围。数字化产品的装配过程都严格参数化,因此,如图5,容差积累的主要形成对象——尺寸链,从微观到宏观上都影响到工装的精度。而实际生产的可控误差主要来源于尺寸链公差叠加,因此有必要对容差进行更严格的界定。
容差模拟是对PMI尺寸链的规范和可操作性的论证方法,如极限法、均方根法及蒙特卡洛法等。如图6,通过对PMI工作报表的尺寸链特征值数据进行基于蒙特卡洛模拟的容差分析,由计算机产生随机数,对特征值进行修正,其各尺寸链的容差分布的正态分布函数
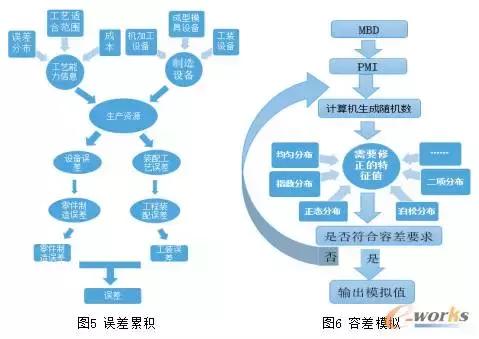
3.2 MBD协同过程中的关键特征
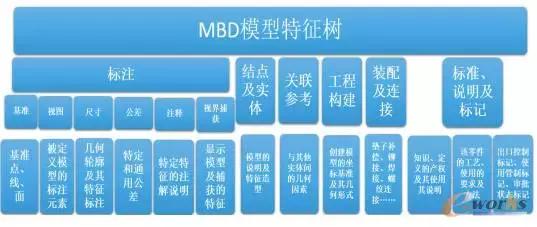
图7 MBD模型特征树
MBD的特征构架是协同的框架和核心。由于手动创建纸质技术数据包TDP(Technical Data papery Package),致使产品与数据严重分离,设计与制造协同脱离数据的支撑,协同的扩展和进程连接十分艰难,时效成本也过高。如图7,工程标注的协同创建、论证、关联表述、装配连接及注释说明等内容作为主要协同对象,因此,基于特征的协同,关键特征在协同过程中处于核心地位。
直接影响工程进度的关键特征参数对PLM起着决定性作用。关键特征在设计制造协同过程作为关键协同目标,包括设计人员与制造人员协同时共同或分别提出的产品生产时需要控制或把握的极限尺寸、配合公差、专用公差、特征关联、干涉、轮廓度公差等。绝大多数MBD系统的PMI标注模块都可以实现对一般尺寸的自动标注,但部分关键特征参数仍需要人工按需求进行判定和定义,设计也不可能对所有尺寸进行标注,部分有公差要求的尺寸、关键的重要尺寸和专用公差也需要选择性抑制。
3.3 基于PMI定义关键特征
PMI报表作为制造信息数据互动核心,将三维模型作为设计协同对象,关键特征参数作为协同目标。PMI提供了详细的产品制造数据,为工程协同提供了全面规范的可靠设计数据源。自动进行的实时数据更新为PMI工作报表提供了时效性,因此将PMI工作报表作为数据重用库,能实现对数据的最大化重用。
基于ASME Y14.36M-1996、ESKD、GB、ISO和JIS等标准,及Teamcenter可行论证结果,进行关键特征的定义创建,如图8,模型PMI的创建和修订立即在PMI工作报表以反馈形式呈现,因此基于PMI实现关键特征在三维模型中定义为MBD协同工程的快速实施奠定了基础。
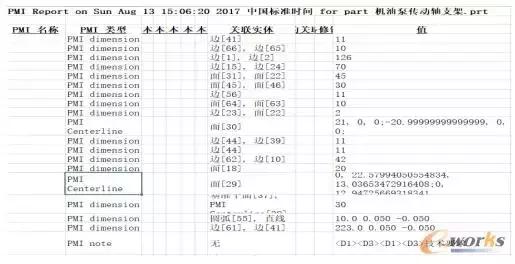
图8 PMI工作报表特征值的反馈呈现
4 基于BOM转换的特征传递
4.1 BOM、EBOM、PBOM与MBOM
BOM(Bill Of Material)是记录项目所用材料的详细信息及其相关属性并作为MRP(Material Requirement Planning)和ERP (Enterprise Resource Planning )的重要文件。对项目来说,即是产品或工程的构成元素的属性明细表及关系清单。
EBOM(Engineering BOM),作为BOM在工程应用中使用的数据结构,它能精确地描述工程的定义和设计指标,及其各子工程之间的关联关系,并以文件形式进行对材料明细表、特征明细表及子构建分类明细表等数据进行详细抽取并规范表达。
PBOM(Process Planning BOM)作为工艺清单,它明确了各零件之间的工艺关联关系,对零件的制造位置、施工方及施工形式等制造信息进行分布式跟踪,以EBOM作为数据支撑,以收集的跟踪数据为依托,制定并修正工艺规划和工序进程,并生成生产计划参考,根据需求预测系列产品的不同组合的产能和产能余量,指导下一步的生产行为。
MBOM(Manufacturing BOM),根据PBOM进行的制造及装配步骤的详细设计,以此描述物料在车间的流动,包括产品的装配信息(方法、顺序等)、工装相关信息(设备、磨具、刀具、卡具等)、工时材料定额、最终产品制造方法等。
基于EBOM、PBOM和MBOM信息流组成的BOM是不可分割的整体构架方案。
4.2 基于PMI工作报表的BOM转换
多协同进程的全生命周期数据链无缝对接,实现构建基于设计、仿真验证、工艺、制造等多领域相结合的MBD主模型数据集,关键在于创建PMI数据映射。在MBD的基础资料库中加入物料信息库,在MBD产品结构树中加入BOM差异分析、物料齐套和汇总,在产品资料中加入成本与模拟模块,并在数据管理库中加入物料资料更改查询模块,将MBD系统特征树与BOM系统进行并行分布,形成以产品资料为核心的BOM系统结构。同理,反向以BOM为核心来看,相当于在BOM特征树中有选择地添加全部或部分制造生产信息,与制造部门ERP和MES系统集成,提供相应信息,达到方便生产管理的目的。
通过对产品进行属性标记(图9),属性作为对应BOM特征树的特征判定依据,计算机抽取产品制造信息生成该模型的制造信息详细报告,PMI工作报表作为BOM系统功能结构中的特征数据关联来源,形成垂直的EBOM功能管理树。
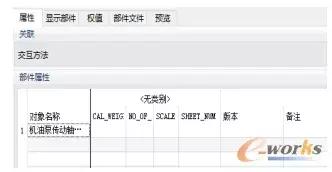
图9 产品属性标记
4.3 基于目录的数据关联与关键特征的传递
各MBD特征与BOM之间的一致性,尤其是关键特征的一致性必须根据MBD结构树上反映的工艺信息快速准确体现,包括工艺层次、分工路线、零件组号、装配大纲、和原材料牌号等。
基于目录的BOM特征分类和基于装配关系的矩阵分布作为数据关联的函数变量,使BOM产品结构各层次的特征值,形成关键控制特征作为一般工程数据传递的分布环境(图10)。既在纵向数据通道,也在横向据通道对各层级的BOM特征实现了基于目录的有效区分,因此关键控制特征的传递,是实现产品全生命周期前期数字化生产的有效方式。
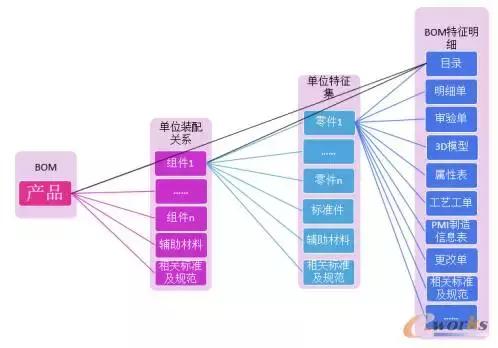
图10 基于目录的BOM产品结构
由此可见,基于PMI工作报表的BOM转换实质为抑制部分简单加工特征、体积加工特征和表面加工特征,将MBD模型转化为MBOM模型的过程。工艺模型的创建实质就是从建模低层语义中收集工艺高层语义,并建立稳定的工艺本体与建模本体之间的映射的过程。
5 结构化工艺与可视化工单
5.1 结构化与可视化
结构本身作为系统内的各组成单元之间的相互作用与联系的整体架构,结构化即为开发该系统而进行元素分解,关系抽象,模块独立的方法。传统的卡片式工艺设计以工序为单位,对某一工艺进行阶段性的详细工艺说明,包括编号、名称、内容及参数、操作要求、辅助设备等。作为阶段进行编制的工艺文件,面对目前制造业企业对协同开发需求的不断强化,难以适应复杂多样的工艺需求。结构化工艺作为一种适应MBD数字化设计的工艺设计模式,是产品制造工艺领域,为达到工艺数据创建、验证、协同提供支持的目的,面向生产资料准备、阶段工艺规划、制造过程管理的应用。MBD结构化工艺实现过程包括:
输入:输入工艺参数,选择加工方法,指定加工要求,收集MBD工艺信息,形成结构化工艺描述;
转换:加工方法、轮廓映射为建模特征,工艺参数映射为建模参数,加工要求映射为PMI,构建建模本体;
应用:创建与建模特征对应的加工特征,抑制建模特征,创建工序模型。判断建模特征包含的几何元素,将建模本体识别为工艺本体,并在不同的工艺文件中重用工艺本体。将建模本体作为前道工序模型进而得到本道工序模型,并附加PMI标注。
作为以表述任务下达、受领、分配与审核,面向工种的人员、任务、物料、工时、作业进程、技术保障、关联厂商和相关说明的管理系统,如图11,工单与制造执行管理之间的传递关系,是可视化工单作为PLM系统任务工作单据的有效形式。
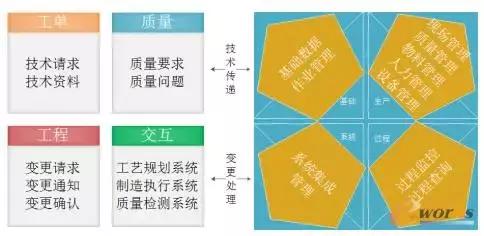
图11 工单与制造执行管理
5.2 结构化工艺与可视化工单
结构化工艺总体构架将模型设计与工艺设计的数据想衔接,继承。如图12,结构化工艺和可视化工单基于MBD的4P(Product 、PMI、Process、plan)系统,结合ERP、MES实现数据运转,交互。
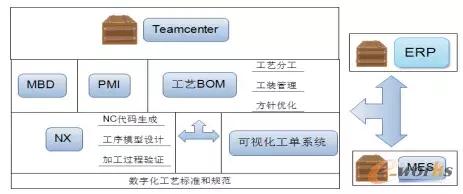
图12 结构化工艺
结构化工艺的闭环功能配置快速输出工艺,可视化工单的闭环功能配置维持PDCA计划和SDCA循环。(如图13~16)
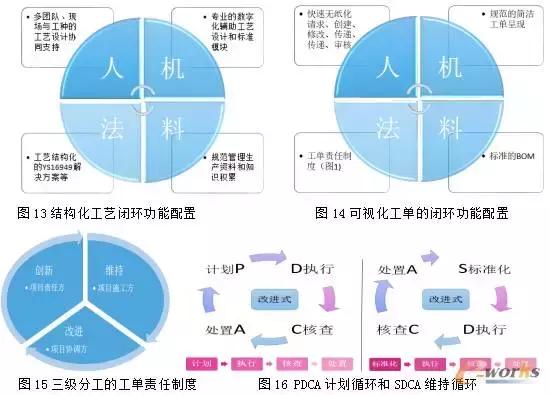
5.3 优越性
相对只能进行局部阶段性的表述的卡片式工艺设计,结构化工艺设计优越性主要体现在:
高效的数字化作业不受设计树结点、设计区域和时间阶段的限制,大幅降低人力需求,缩短工期,降低成本;
垂直的模块化关联设计树,模块化创建、修改、报备、传递、关联等,能对全局管理;
快速联动的工艺设计、管理。
纸质工单作为描述性工作任务单据,只能独立表述单个或几个任务的详细作业,缺乏时间上的阶段性和整体性的规划分析,因此,远不能满足数字化作业对现场指导的时效性需
求。相对纸质工单,可视化工单优越性主要体现在:
根据工艺BOM制定,对工程进行实时跟踪;
如图17,实时场景式表述,可实现基于现场视图的快速管理(创建、修改、报备、反馈、审核等);
更加灵活,可据实际情况进行权限设定,如图18,基于管理员权限进行任务自动分配。
功能模块化,工单数据的重用度大幅提高,可实现关联工序的选择调用;
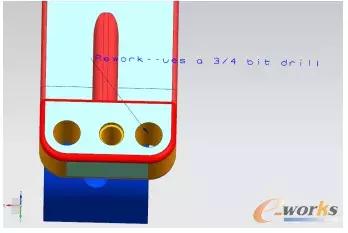
图17 基于MBD可视化工单的现场反馈
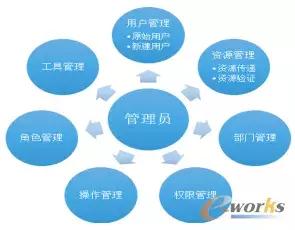
图18 基于权限的工单管理
6 CMM数字化检测与质量控制
6.1 基于MBD的CMM
质量是产品满足用户需求的关键指标。产品性能、使用和储存寿命、产品功能、安全性、外观等,是厂商实施质量检测的核心目标。
传统的人工检测对数据的利用率过低,很难满足PLM对数据的重用需求。仅尺寸检测就会消耗大量时间,信息传递在制造与质检、质检与设计、工艺等部门之间的数据反馈严重滞后,降低了检测效率,影响了产品的PLM的高效实施。CMM(Coordinate Measuring Machining)检测技术,通过软件自动读取产品MBD数据,生成检测设备能自动读取、识别、执行、报备的DMIS等格式文本,作为测量标准值。将实际值与标准值差值与标准公差进行比较,根据差值大小评估该产品质量优劣。如图19,CMM将基于MBD的设计、制造、检验的数据传递链路,完整地统一起来。
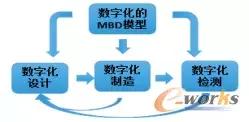
图19 基于MBD的数字化设计、制造与检测
6.2 数字化检测的基本流程
在MBD实施进程中,被测量客体主要集于几何形状、面积、面粗糙度、长度、高程、角度、形位公差等上。由于不同种类、不同数量的几何量的累积,被测量在MBD模型中表现种类繁多的特点,因此要想实现CMM自动化,必须对MBD数据链路进行研究。
配备数字化测头、量具、量仪和数据处理软件的设备,基于计算机辅助检验规划CAIP(Computer Aided Inspection Planning)的MBD检测工艺,集成了检测工艺规划、过程控制、报告生成的数字化检测系统。如图20,基于检测规范及要求,对MBD模型实施关键特征检测并进行数据抽取,生成GD&T;工艺路径规划及CNC程序进行后置处理后,实施基于DMIS等文件的CMM测量,将测量数据和测量要求和数据处理规范组合编制为测量报告。
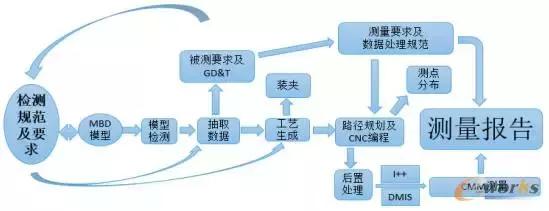
图20 基于MBD的检测信息驱动CMM
CMM作为数字化设计、制造的后期反馈,是实现MBD作为唯一信息驱动的重要环节。
6.3 数字化检测的数据来源
MBD模型作为数字化检测的主要检测依据,模型数据库、结构特征库、标准规范库、检验项目库、检验方法库、检验工具库和检验规划知识库组成数字化检测的数据来源。
MBD模型数据库。
检验结构特征库:点、线、面、孔、筋等。
标准选用规范库:HB5800、HB7552、、企业标准、企业规范、机型通用技术准则等。
检验项目库:高程、筋宽、孔位置、直径、同轴度、型面轮廓度等。
检验方法库:机械测量仪、光学测量、微波测量、气动式测量、声学测量、IGPS扫描等。
检验工具库:坐标测量机、激光扫描系统、涡流测厚仪、室内GPS等。
数字化检测的关键特征主要集中于形位公差(GT&D)。根据要素的单一和关联分类,分为包括集几何元素的单一类型、包括轮廓(Profile)、反向(Orientation)、跳动(Runout)、位置(Location)的关联类型、包括晶粒度等的结构类型。
6.4 检验卡片的关键控制特征生成
关键控制特征的数字化检验依赖于数据的重用,而实现对数据的重用必须对MBD模型的恒定特征要素进行标准划分。基于MBD数据集抽取的检测对象,依据特征的来源(三维模型、技术要求、设备容许参数等)、检验工序划分(时序、坐标、设备、方法等)、检验输出结果(工序生成、排序等)可得出CMM可读取的检验卡片文件(关键特征表、关键特征检验时序表、单一特征检验实现方法等)。
7 结论与展望
以MBD技术为核心,以PMI报表数据为纽带的数字化产品设计制造的实践方法,在数字化工厂的广泛应用,特别是在复杂产品的研发、生产中,形成全局的信息管理和决策树,将为企业节省大量工期和费用。在我国工业2025的战略要求下,MBD技术在设计与制造协同过程的广泛应用将大幅提升我国装备制造整体水平。
相关参考