泰州线切割厂家有哪些(机械行业策略报告:紧抓通用设备自主可控,把握专用设备景气加速)
Posted
篇首语:休言女子非英物,夜夜龙泉壁上鸣。本文由小常识网(cha138.com)小编为大家整理,主要介绍了泰州线切割厂家有哪些(机械行业策略报告:紧抓通用设备自主可控,把握专用设备景气加速)相关的知识,希望对你有一定的参考价值。
泰州线切割厂家有哪些(机械行业策略报告:紧抓通用设备自主可控,把握专用设备景气加速)
(报告出品方:中国银河证券)
一、2023 年投资关键词:疫后复苏、自主可控、新技术 落地
(一)2022 年回顾
我们在 2022 年度机械行业策略报告《硬科技+新能源,引领装备升级新征程》中提出 2022 年投资关键词为“硬科技”“新能源”“专精特新”,认为 2022 年机械设备制造业的投资机 会依然将来源于与制造业投资相关的板块,特别是符合时代发展趋势的科技革命&能源革命下 的制造升级。在 2022 年机械行业春季策略报告《把握稳增长主线,自下而上精选α》中提出 2022 年稳增长主线凸显,稳增长重在稳投资,稳投资重在基建投资和制造业投资,机械设备 板块多角度受益。
回顾 2022 年机械行业基本面以及行情表现:
从投资层面看,2022 年 1-11 月份固定资产投资累计同比增速为 5.3%,其中增长主要 受益于基建投资和制造业投资的拉动,1-11 月基建投资累计增速为 11.65%,制造业 投资累计增速为 9.3%,房地产开发投资形成拖累,累计增速为-9.8%。
从机械行业上市公司业绩层面看,2022 年前三季度机械行业整体收入增速转正 (+0.55%),净利润降幅收窄(-14.18%),虽整体盈利能力仍承压(净利率 6.75%, 同比-1.16pct),但受益于原材料价格回落因素,毛利率逐季环比改善(毛利率 22.22%, 同比-0.72pct,2022Q3 单季度环比+1.87pct)。细分子行业中,锂电设备、光伏设备、 油服装备、煤机矿机、半导体设备实现收入和净利润双增长。
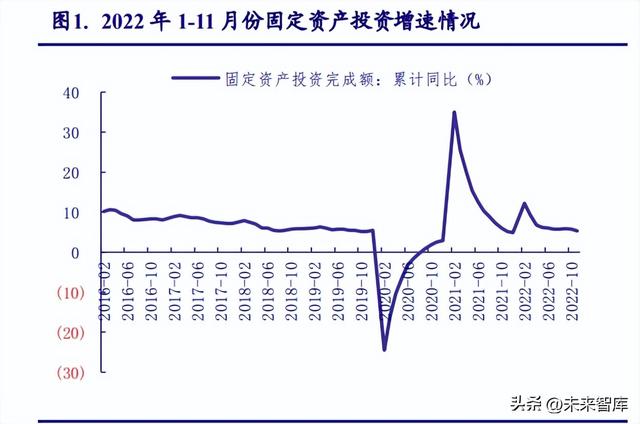
从机械设备板块行情表现层面看,整体走势与大盘基本一致,年初至今累计涨幅为11.82%,其中仅油服装备、机床工具、光伏设备三个细分子行业从全年维度来看取得 了正收益。2022 年市场总体波动较大,投资机会较难把握,且主题性投资机会大于 基本面投资机会,机械板块典型代表为“人型机器人”及“钙钛矿设备”等主题性投 资机会。我们认为,2022 年结合基本面与市场风格,机械设备板块中可把握的投资机会包括油服(个股迪威尔年初至今涨幅 129.29%)、光伏设备中 Topcon 招标超预 期(个股捷佳伟创年初至今涨幅-2.82%,但从 4 月份底部起年内最高涨幅达 257%)、 新技术复合铜箔(个股东威科技年初至今涨幅 99.41%)、四季度通用设备底部复苏 (个股纽威数控年初至今涨幅 32.58%)等。
(二)2023 年投资关键词:疫后复苏、国产替代、新技术落地
展望 2023 年,从宏观层面看,面临最大的变化是疫情防控政策的调整从动态清零到全面 放开,随着放开第一波冲击过去,生产生活逐步恢复正常,复苏可期,全年 GDP 目标在中国 潜在经济增速和稳就业考虑下有望在 5%上下,其中消费由于低基数和放开后复苏以及政策鼓 励扩大内需等因素影响下预计增速高于5%,出口在高基数以及外需收缩压力下预计低于5%, 实现 5%的增速目标,仍需投资发力。投资方面,我们认为制造业投资仍是政策发力的方向, 地产虽出现拐点但投资在 2022 年拿地和新开工面积大幅下降的基础上难以转正,基建投资预 计保持韧性但增速低于 2022 年。 因此,2023 年机械板块的投资机遇,我们依然看好与制造业投资相关的板块。但 2023 年 制造业投资受出口增速放缓以及汽车销量增速放缓等因素影响受到一定压制,增长将主要来 源于政策对于高技术制造业的支持、国际形势不确定增强下的产业链自主可控,以及设备更新 周期等。从通用设备和专用设备对比的角度看,我们看好 2023 年通用设备整体投资机遇大于 专用设备,且均存在结构性机会,通用设备的投资机会更多来源于进口替代,如数控机床、数 控刀具、工业机器人等,专用设备的投资机会更多来源于新技术的落地,如光伏高效电池、复 合铜箔、4680 大圆柱电池、一体压铸等渗透率提升带来的设备投资机会。长期来看,这一轮 制造业投资的典型特征将为“制造升级”,具体体现在高端产品占比提升,自动化智能化改造 比例提升,国产化程度提升三大趋势。
二、紧抓通用设备复苏+自主可控投资主线
(一)通用设备有望底部复苏,推荐受益政策支持下自主可控品种
1、以机床、机器人、注塑机、激光为代表的通用自动化行业体现出类似的周 期性特征
机床、工业机器人、注塑机、激光等通用自动化设备由于景气度均与制造业投资相关,历 史上主要受汽车制造业投资、3C 制造业投资及其他一般制造业投资波动影响,景气趋势上体 现出方向上的一致性(幅度有差别)。
机床:由于我国机床产业大而不强,中高端机床进口为主,相较国内产量数据,进口 数据可以更好地体现产业升级下的需求变动趋势,因此我们选取机床进口数据作为 指标。从过去 26 年的机床进口数据来看,机床行业有其 10 年左右的大周期性的特 征,但也镶嵌 3-4 年小周期,从增速低谷到下一个周期低谷的时间段分别为:1998- 2001 年,2001-2005 年,2005-2009 年,2009-2013 年,2013-2016 年,2016-2019 年, 虽个别年份有领先或滞后,整体也体现出与机器人、激光、注塑机较为一致的变动趋 势。
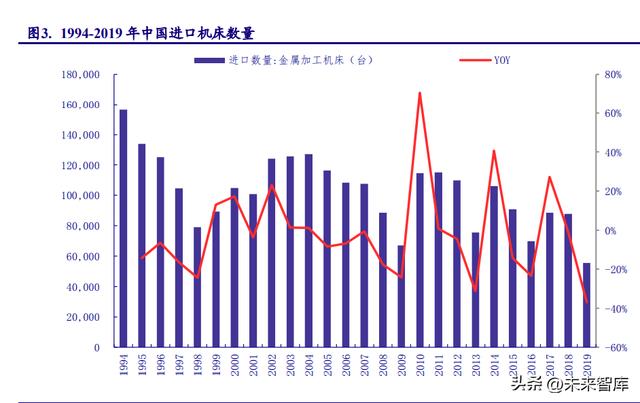
工业机器人:通过复盘 IFR 公布的 1999 年至 2021 年的工业机器人销量历史数据, 全球工业机器人和中国工业机器人的销量增速有着较为相似的变化趋势,表现出 3-4 年左右的周期性。
注塑机:由于注塑机行业缺乏行业性统计数据,我们以行业龙头海天国际的营收数据 为代表说明行业的变化趋势。从海天国际过去 19 年的营收增速变化趋势来看,同样 体现出 3 年左右的周期性特征,从增速低谷到下一个周期低谷的时间段分别为:2005- 2008 年,2008-2012 年,2012-2015 年,2015-2019 年,整体体现出与机器人较为一致 的变动趋势。
激光:我们以武汉文献中心公布的历年中国激光产业发展报告中的中国激光设备销 售规模为指标,可以看出,激光设备行业同样体现出 3 年左右的周期性,过去 10 年 出现过 2013-2016 年,2016-2019 年两轮周期,激光作为一个新兴产业链,数据较短, 从这近两轮的数据来看,近 3 年变化趋势与机器人一致,上一轮较机器人滞后一年。
2、背后是库存周期影响下的制造业投资小周期
通用自动化各个细分行业显现出的 3-4 年的小周期特征,背后是库存周期影响下的制造业 投资小周期。从工业企业产成品库存数据来看,2000 年 5 月、2002 年 10 月、2006 年 5 月、 2009 年 8 月、2013 年 8 月、2016 年 6 月、2019 年 11 月为每一轮小周期低点,平均周期约 39 个月,其中上行期约 23 个月,下行期约 17 个月。此轮库存周期的高点出现在 2022 年 4 月份,按历史周期规律推演,库存周期见底回升将出现在 2023 年 9 月。
结合历史传导规律,企业盈利周期领先于库存周期约一个季度,市场股价表现又领先于企 业盈利周期约一个季度。 从工业机器人和金属切削机床产量数据来看,2022 年三季度见底,四季度起有所回暖, 工业机器人 10 月单月产量增速 14.4%,金属切削机床 10 月单月产量增速-8.5%(有所收窄), 但 11 月受疫情影响数据均有所下滑。从草根调研反馈信息来看,9 月起机床、刀具等通用设 备需求边际改善。
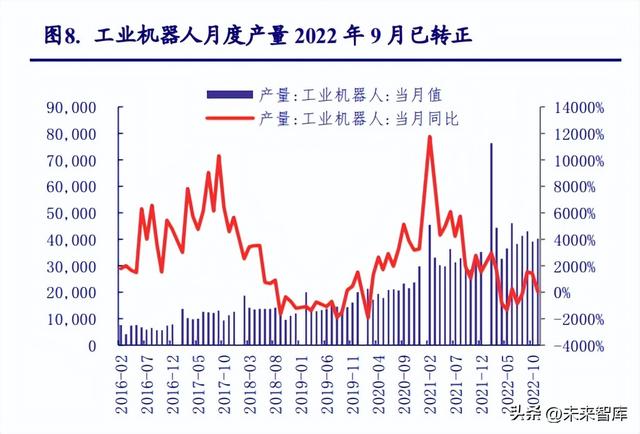
3、本轮制造业投资体现“弱复苏+自主可控”特征
当前工业企业库存仍处于较高水平,本轮去库存或需要更长的时间,背后的原因是需求较 弱,或需等到疫情冲击对经济的影响减弱,生产生活逐步恢复正常,预计在 2023 年 Q2 前后, 另外,要结合此轮制造业投资的特征,也就是政策支持下的自主可控选取投资赛道。
通用自动化细分行业包括机床产业链(数控刀具、数控机床、机床核心零部件)、机器人 产业链(机器人本体、机器人核心零部件)、注塑机、激光产业链(激光器、激光设备、激光 控制系统)、叉车、通用减速器、自动化零部件等细分子行业。通过以上分析,我们重点看好 数控刀具、数控机床以及机器人三大细分子行业,以及受益于商业模式创新或进口替代的其他 通用零部件领域。
(二)重点看好数控机床、数控刀具、机器人三大细分子行业
1、数控机床 (1)机床行业周期性特征明显,目前处于逐步回升阶段
机床行业是一个典型的周期性行业,当前大周期(更新周期)向上,小周期(库存周期) 逐步见底回升。机床的一般产品寿命约为 10 年,因此行业大约每 7-10 年为一个商业周期,历 史上全球消费规模 1983 年、1993 年、2003 年、2013 年均为阶段性低点。从 10 年的大周期来 看,2020 年全球机床总消费 668.17 亿美元,中国机床消费金额 213.16 亿美元,处于近 10 年 最低位,中国及全球市场从 2021 年开始复苏,2021 年机床消费显著提升,分别同比增长 19.73% 和 31.46%,目前仍处于底部回升阶段。中国机床消费占全球比重在 2019 年下降到低位 27.16% 后,近两年稳步上升,2021 年达到 35%。
从小周期维度来看,与注塑机、机器人、激光、工控、通用减速机等通用自动化行业一致, 背后是制造业投资的小周期。小周期维度 3-4 年一轮周期,2019 年、2015 年、2012 年、2009 年均为小周期低点。中国金属切削机床 2022 年以来当月产量增速不断下降,库存压力逐渐释 放,2022 年 1-11 月累计产量 52 万台,同比下降 12.50%,较于往年同期水平也处于地位。 目前中国机床行业处于大、小周期底部回升的交织阶段,另外中国疫情政策逐步宽松,中 国制造业有望在 2023 年稳步回暖。展望未来 3-5 年,中国机床消费市场不仅将全面恢复到疫情前水平,而且借力国家十四五规划,以高端制造业为导向进一步扩大国内的机床消费市场。
(2)需求端:疫情后时代经济全面恢复,高端制造业为核心驱动
金属切削机床需求稳步上升,金属成形机床需求逐步恢复
金属切削机床的需求主要分为两种,第一是更新需求,金属切削机床的设备更换周期一般 是 10 年,我们通过将之前 10 年-15 年每年机床产量进行加权计算得出;第二是新增需求,每 年中国制造业的扩张都需要新机床设备的购入,我们预计未来 3 年中国制造业投资平均增速 为 5%,因此未来 3 年带动的新增需求为 14.01 万台、11.77 万台、12.36 万台。以上加总,得 到未来三年金属切削机床需求分别为 71.47 万台、76.43 万台、79.83 万台。金属成形机床我们 则认为会稳步恢复到疫情前水平,以更换需求为基本逻辑,预计未来三年金属成形机床需求分 别为 15.17 万台、23.39 万台、21.28 万台。
工业现代化建设持续推进,数控机床占比稳步提升
随着政策对高端制造业的倾斜,数控机床占比稳步提升,2021 年中国机床数控化率为 45%, 预计在政策加持和制造业需求下,假设每年提升 3 个百分点,中国数控机床 2023-2025 年的需 求为 36.45 万台、41.27 万台、45.50 万台。
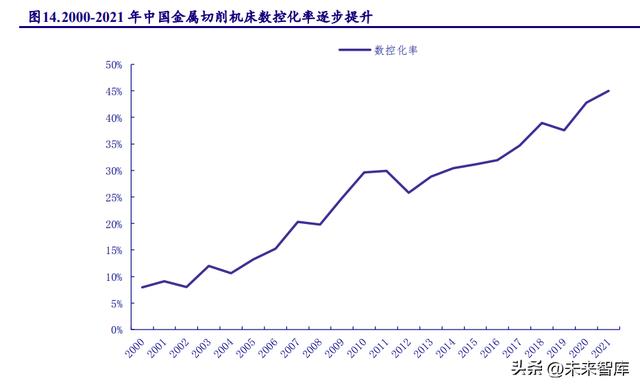
(3)供给侧:核心零部件、中高端机床依赖进口,但国产化率在提升,国产产能在提升
机床产业链:中游位置承接结合上下游工业产业
机床行业技术水平和产品质量是衡量一个国家装备制造业发展水平的重要标志。机床是 对金属或其他材料的坯料或工件进行加工,使之成为所要求的几何形状、尺寸精度和表面质量 的机器,机械产品的零件通常都是用机床加工出来的。机床与其他机器的主要区别在于,机床 是制造机器的机器,同时也是制造机床本身的机器,因此机床又被称为母机或工具机。 整个机床产业链上中下游清晰,包括上游基础材料和零部件生产商、中游机床制造商和下 游终端用户。上游基础材料和零部件生产商主要为机床制造商提供结构件(铸铁、钢件等)、 数控系统、传动系统(导轨、丝杠、主轴等)、刀库等组成,涉及企业主要包括发那科、西门 子、海德汉、三菱等等公司;中游是机床制造商,负责向终端用户提供满足其要求的各种机床 或成套的集成产品;终端用户主要是汽车、消费电子、航天航空、船舶、工程机械等领域的公 司。
机床零部件占比与供应情况
上市机床公司核心零部件占比
从机床行业上游来看,上游零部件可以分为结构件、数控系统、传动系统、功能部件等, 这几部分占据了机床的最主要成本。 分公司来看,海天精工机床零部件占比前三为结构件、控制系统和传动系统,分别占比 34.92%、21.60%、20.35%;纽威数控机床零部件占比前三为功能部件、电气件和铸件,分别占 比 25.58%、22.33%、20.86%;国盛智科机床零部件占比前三为机床其他材料、数控系统及配件 和钣焊类原材料,分别占比 22.73%、20.17%、20.05%;科德数控机床零部件占比前三为结构 件、传动类和控制系统,分别占比 39.26%、17.26%、13.11%;浙海德曼机床零部件占比前三为 导轨、数控系统和铸件,分别占比 26.69%、24.05%、14.82%。
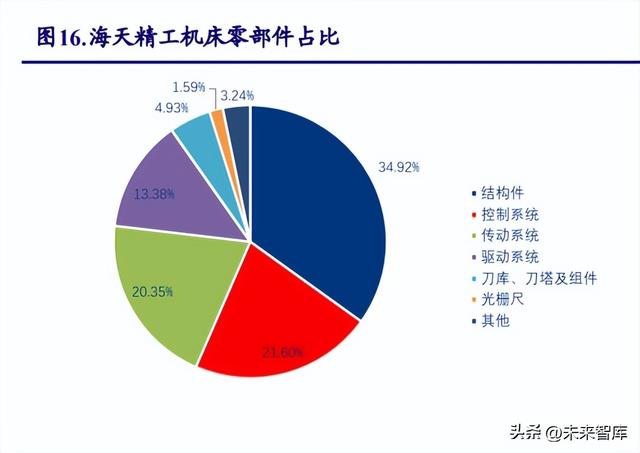
零部件供应商
公司集中在发那科、西门子、HIMIN 和台湾银泰等;核心功能部件如转台、刀库、刀塔等是部分进口,部分使用国产品牌,公司集 中在台湾宝嘉成、旭阳、常州德速、北钜等。结构件和铸件、钣焊件以国产品牌为主,如光洋 科技、云科晟数控等。 总的来说,机床的上游核心部件以进口日本、德国的公司为主,非核心部件正在逐步使用 国产品牌。
(4)机床中高端划分及竞争格局
机床中高端划分
目前我国的机床消费市场按照档次分大致呈金字塔结构,底部是低档机床,占比 50-60%, 由国内厂商占领,主要通过打价格战来竞争,产能过剩;中部是中档机床,占比 30-40%,是目 前中外企业竞争的主要领域;而顶部是高端机床,占比 10%,基本来源于进口,长期被欧日企 业垄断。
中国机床消费市场的国产化率在经过 2003-2008 年快速提升后,一直在 70%左右的水平波 动,国产化率有待提高,高端设备进口替代空间弹性更大。根据 Gardner Intelligence 的数 据,2021 年中国机床进出口金额为 82.4 亿美元,占消费总量的 29%,整体的国产化率 71%。 而高性能、高精密度的高档数控机床的国产化率更低。由于低档机床主要由国产厂商提供,我 们假设进口机床集中在中高档,则中高档机床国产化率仅为 20%-30%。 近年来,国内中高档数控机床市场亦出现了一批具备核心技术的新兴民营机床企业,其产 品得到市场的广泛认可,综合竞争力大幅提高,民族品牌开始崛起,逐渐形成进口替代趋势。 另外,在中美贸易战的大背景下,由于美国以各种理由,特别是在高科技领域限制中国的全球 化进程,这使得国内行业供应链被迫进行调整,加速了进口替代的进程。
国内机床企业竞争格局
集中度低:我国虽为机床大国,根据 Gardner Intelligence 的数据,2021 年中国机床消 费市场金额是 280 亿美元(1960 亿人民币),但大而不强,行业集中度较低,截至 2021 年, 我国金属切削机床企业仍有 931 家,金属成形机床仍有 544 家,行业内企业普遍规模较小。 中高端国产化率低:我们定义数控金属切削机床销量为中高端,则销量的 45%为中高端, 中高端金额更高,假设 70%的金额占比为中高端,则中高端市场规模约为 900 亿,进口的 82.4 亿美元(约 600 亿)均为中高端,则国产中高端市占率约为 1/3。
重点企业扩产计划
为响应国家十四五规划,我国机床生产企业积极进行以高端数控机床为主的产能扩增计 划。截至目前,纽威数控的三期中高端数控机床产业化项目已经在今年 8 月建成投产,预计年 增产能 2000 台;国盛智科的中高档数控机床生产项目也已大致完成建设阶段,预计 2023 年将达到 50%设计产能,2024 年实现达产;科德数控的面向航空航天高档五轴数控机床产业化能力 提升工程已完成厂房建造与改造装修阶段,正在安装与调试设备;而创世纪、秦川机床和海天 精工的增产项目也均通过股东大会审议和相关批复,正在规划设计阶段。 综上,这些项目达产以后,我们保守预计年增高端机床超 15000 台,将会为国产高端机床 领域注入新的活力。
2、数控刀具
(1)数控刀具作为工业耗材,是典型的顺周期行业
机床刀具指机械制造中用于切削加工的工具,又称切削工具,为工业耗材。2016-2018 年 我国切削刀具市场规模出现快速增长,2018 年刀具消费总额达到 421 亿元,超过 2011 年 400 亿的高点,创造了历史最高纪录。2019 年,汽车等下游制造行业下行,叠加中美贸易摩擦加 剧,我国刀具消费额有所下滑至 393 亿元。2020 年疫情后我国经济快速复苏,刀具行业的年 消费额又一次创新高,达到 421 亿元,2021 年市场规模进一步提升达到 477 亿元。根据 QY Research 数据,2020 年全球切削刀具消费金额达 370 亿美元(约 2680 亿人民币), 2016-2020 复合增长率为 2.82%,预测 2025 年,全球刀具消费额将达到 425 亿美元。
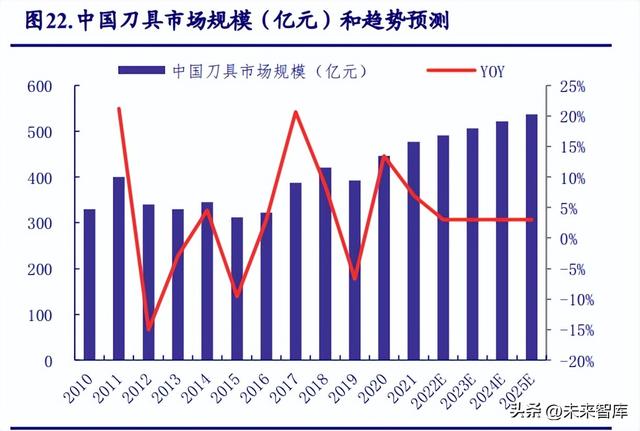
用于金属切削机床加工的刀具按照材料的硬度从低到高主要分为高速钢、硬质合金、陶瓷 以及超硬材料。根据中国机床工具工业协会数据,2021 年国内金属切削机床刀具的市场规模 大约 477 亿元,其中硬质合金约占 51%,达到 243.27 亿元;根据中国机床工具工业协会统计,刀片约占会员企业硬质合金刀具销售额 54%,依此估算国内硬质合金刀片市场规模在 131.4 亿 元左右。硬质合金数控刀具按照结构可大致分为整体硬质合金刀具和可拆分/转位刀具,其中 可转为刀具的使用更便捷,刀片达到寿命后可直接拆卸进行替换。刀片根据加工方式又可分为 车削、铣削、和钻削刀片,其中车削刀片的占比最大。
(2)明年有望迎来周期向上+进口替代+均价提升的量价齐升机会
我国正处于产业结构的调整升级阶段,刀具消费占比有较大提升空间。在工业 4.0 的趋势 下,制造业在积极寻求转型升级补短板,现代切削加工对刀具的稳定性、加工精度、进给速度、 使用寿命等要求也相应的提高。在我国刀具产品占机床的消费结构中,数控刀片占机床消费的 比重从 2012 年的 14.1%提升到 2020 年的 32.1%,可见我国刀具消费在提质升级,但距离传统 制造业强国还有一定差距;根据华锐精密可转债募集说明书显示,德国、美国和日本等制造业 强国注重数控机床和高效刀具互相协调、平衡发展,每年的刀具消费规模为机床消费的 50%左 右。随着国内终端用户生产观念逐渐从“依靠廉价劳动力”向“改进加工手段提高效率”进行 转变,以及制造业的转型升级,我国刀具消费规模仍存在较大提升空间。
疫情只是导火索,从 2017 年起进口刀具的国内市场份额呈现下滑趋势。由于近两年疫情 影响,国外的刀具厂商供货不及时+物流滞后,给国内的企业带来进口替代的机遇。在过去 30 年里,随着国内刀具行业的新兴企业涌现,各企业研发投入加大,叠加专精特新企业补贴和减 税政策支持,刀具技术升级+本土服务优势显现,国产替代的进程不断加速,进口刀具的市场 份额由 2016 年的 37.2%逐步下降至 2019 年的 34.6%。
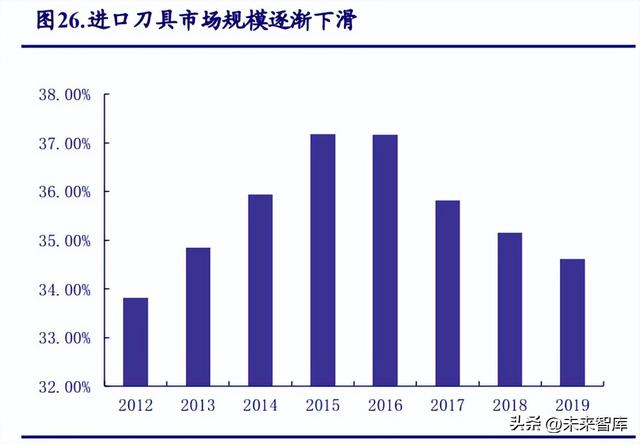
机床数控化是机床行业的升级趋势,降本增效的同时,数控化率提升也为数控刀具市场带 来增量。近几年,我国机床数控化率保持着稳定增长,2021 年金属切削数控机床产量占比达 到 44.85%,同比+40.15%。根据国务院《中国制造 2025》规划,预计到 2025 年我国数字化研 发设计工具普及率达到 72%,关键工序数控化率达到 50%;对比国际上制造业强国机床数控 化率 60%-70%以上的水平,我国机床数控化率还有较大的提升空间。所以无论是存量机床的 更新换代需要,还是每年新增的数控机床的需求,刀具作为机床加工的消耗品,将迎来可观的 消费需求增速。
(3)未来发展趋势是打造刀具综合解决方案提供商以及供应全球
以山特维克为鉴,未来刀具企业的发展路径为拓宽品类、从产品到服务强化品牌效应。自 成立以来,山特维克一直致力于为客户解决实际问题,其产品也根据客户需求不断革新,从硬 质合金刀片逐渐发展到包括涂层刀片和其他各类特殊材料刀片的近 10 万种品类;除产品外, 山特维克还推出了刀具咨询和定制化服务。优质的产品加上全方位的服务,更能拓宽销售渠道、 扩大客户范围、强化品牌效应。 国内头部企业或许也可以走上并购扩张的道路,以扩充产品线为客户提供完整的解决方 案为目标,从硬件到软件,从设备配套到技术储备,未来中国有望出现一个行业龙头占领大部 分市场,并逐步向海外扩张。
3、机器人
(1)工业机器人产量重回正增长区间
2022 年 9 月-11 月,中国工业机器人产量同比重新恢复到正增长区间,受宏观经济因素、 机械子行业周期波动、下游自动化需求乃至疫情等多方因素刺激,我国工业机器人的产量自 2015 年有统计数据以来,年度产量已从 2015 年的 32996 台,增长至 2021 年的 36.6 万台,可 谓是经历了一轮最初的成长。 近两年来,在自动化改造需求升级和疫情压制固定资产投资意愿的冲突下,我国工业机器 人的销量同比数据经历了一轮小波动,而站在当下,我们仍旧对国产工业机器人及其产业链的 前景持有乐观预期。
(2)产业链协同发展有望推动行业新一轮增长
工业机器人产业链主要由原材料、零部件(上游)、机器人本体(中游)、系统集成(下 游)以及行业应用等几个环节组成。工业机器人的生产成本结构中,上游核心零部件占比较高, 伺服系统、控制器与减速器成本占比超 70%,这其中减速器则占到一半,而本体制造仅占 15%。 究其原因,工业机器人的驱动与控制功能均来自核心零部件,与本体制造相比,核心零部件的 技术壁垒更高,因此生产成本占比高。 核心零部件国产化程度低在一定程度导致其生产成本占比高。以减速器为例,减速器国产 化率较低,该市场主要依赖于进口。中国工业机器人制造企业在采购减速器时,由于采购数量 较少,难以产生规模效应,面临国际供应商议价权过高问题,相同型号用减速器,中国企业采 购价格是国际知名企业的两倍。
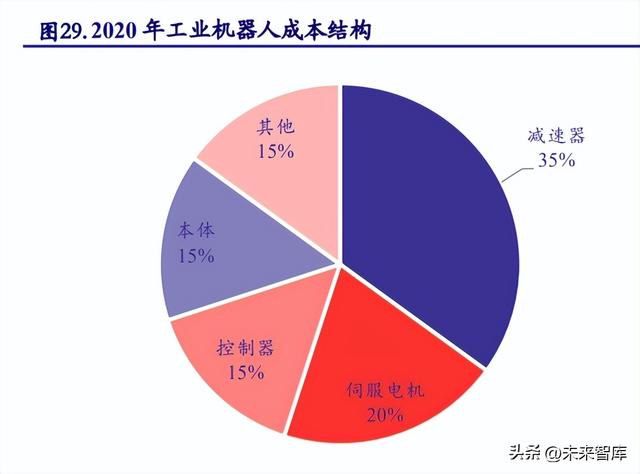
国产减速器市占率逐渐抬头,持续发展未来可期。减速器属于高精密度产品,产品开发周 期长、前期资金投入大、技术复杂度高且生产难度高,减速器行业壁垒也高,是我国工业机器 人领域中相对薄弱的环节。而从市占率来看,减速器行业集中度高,市场一直被少数国际企业 垄断。近年来,中国工业机器人用谐波减速器的市场份额就有较为明显变化,国产速器厂商正 处于不断的技术消化、产品放量、产能扩张的正向成长周期中。我们认为,随着下游需求持续 拓宽,预计未来减速器国产化率将得到大幅提升。
精密减速器作为工业机器人的核心零部件之一,与工业机器人的产销量息息相关。在机械 部底座、肩部起支撑作用的多为 RV 减速器,是多轴工业机器人的重要活动关节,也是“大关 节”;在执行操作的小臂、腕部等部位,则主要以“小关节”的谐波减速器为传动部件。一般 来说,一台六轴机器人共需要使用 6 个减速器,其中底座、肩部使用 2 个 RV 减速器,其余部 分使用谐波减速器 4 个。因此,工业机器人销量与精密减速器的配套需求密切相关。
将减速器主要厂商的销售额与全球工业机器人销售量进行对比发现,两者呈现一个正相 关的趋势。全球工业机器人销量的销量从 2004 年的 9.5 万台增加至 2021 年的 48.6 万台,同 期减速器销售额从 1370 亿日元增长至 3368 亿日元。纳博特斯克和哈默尼克一直在全球工业 机器人的减速器领域占有不可撼动的龙头地位,两家厂商的市占率合计覆盖了大半以上的市 场,从两家公司的营业额来看,确实也与全球机器人销量数据呈现高度的相关性。
从工业机器人的三大主机厂与纳博特斯克的营业收入来看,整个工业机器人整机与零部 件的传导链条清晰明了。回顾日本的工业机器人订单数据、全球机器人销量数据和减速机的销 售额,可以发现订单数据最先到达拐点,随后机器人销量和减速机的配套销量相继呈现相同的 变化趋势。基于这种较强的相关性,我们可以将驱动工业机器人销量增长的三大底层因素,与 订单变化趋势,以及减速机的销量变化趋势联系到一起。 减速器发展成熟并能大批量供货给中游机器人整机厂时,双方毛利都会因彼此的协同而 得以提升。从全球工业机器人产业链的历史发展角度来看,RV 减速器龙头纳博特斯克,作为 工业机器人主机厂安川的一级供应商,双方出货量提升时,双方的毛利率也在逐步提升。理论 上来说,景气度向好的市场以及广阔的市场空间是产业链上下游毛利率整体提升的因素之一, 其次则是产业链主机与零部件在更好的协同之后,降成本控制在更低的区间范围内,为双方都 争取更厚的盈利空间。
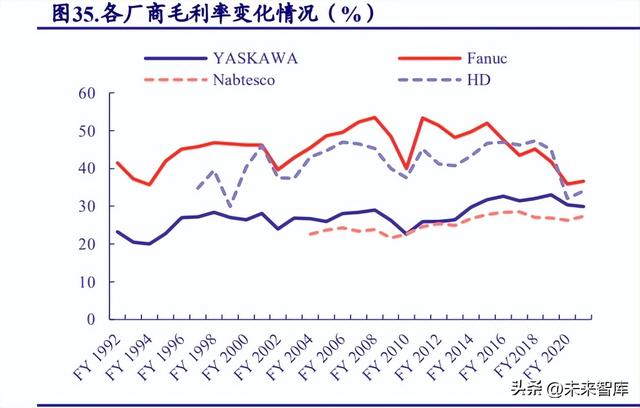
在 2000 年左右,日本的工业机器人销量正处于波动上涨的阶段当中,我们可以看到当时 工业机器人主机厂发那科和减速器的零部件厂商哈默尼克的盈利能力均有的阶段性上行的趋 势。拟合日本的工业机器人历史订单情况和主机厂、零部件厂商的盈利水平后,可也以发现下 游市场快速成长,产业链上下游协同发展,将拉动毛利率逐步提升。 随着中国减速器技术不断突破,国产减速器逐渐放量,与其中游的整机厂进行协同后,双 方毛利也将会跟随国外的趋势得到一个提升。工业机器人产业链联系较为紧密,且传导作用明 显,中国实现核心零部件国产化后,中游机器人本体的成本将大幅下降,产品竞争力可有效提 升,本体成本的降低将带动系统集成解决方案价格的降低,从而缩短应用端工业自动化生产设 备改造投资回收期,使得工业机器人在制造业的渗透率提升,需求也相应增加。终端客户需求 大幅增长将传导至中上游形成规模效应,进一步促进全产业链降本,同时推动中上游技术与质 量双升,促进中国工业机器人企业竞争力进一步加强。
因此,我们认为,一方面三大底层因素,人口老龄化、用劳用工成本以及下游产业汽车电 子行业的蓬勃发展依然会不断的驱动中国工业机器人的销量增长,另一方面,我国工业机器人 主机厂、如埃斯顿等公司已经在市场中崭露头角,瓜分市场份额,我国的核心零部件厂商也不 断进行技术研发与革新,上下游产业链协同发展,互惠共赢,增厚盈利的成长期将不日到来。 此外,进出口价格差距逐渐缩小,机器换人具有较高性价比。我国工业机器人进口均价已 经从 1996 年的 4.76 万美元/台下降到 2019 年间的 1.63 万美元/台,而由于劳动人口下降导致 的制造业人员工资持续上升,两者之间的差距不断缩小,并且工业机器人代替人工所带来的效 率和安全性等方面的提升,使得工业机器人具有越来越高的性价比,机器换人成为越来越多企 业的选择。 利好政策频出,国家大力支持工业机器人发展。如今工业机器人行业处在快速发展阶段, 中国作为未来全球最大的机器人市场,不仅要把机器人水平提高上去,而且要尽可能多地占领 市场。因此,在当今国家制造业处于人口红利逐渐消失的背景下,提升产业智能化升级将助力 企业提高制造效率,国家提出了一系列与机器人相关的发展战略与规划。
中国企业追赶脚步并不慢,且格局优化后有望进一步提速。据 MIR 统计,我国 2021 年工 业机器人市场中内资占有率为 32%,下 2020 年小幅下降后又迅速回升,相比 2019 年提升 1.9 个百分点。2020 年小幅下滑的主要原因是疫情冲击导致一些系抗风险能力弱的内资品牌加速 退出市场所致,但是龙头企业的占有率提升,我国国产工业机器人领军企业保持快速发展;从 绝对值来看,相比于历史沉淀悠久、拥有核心激素的国外机器人企业,我国数控系统以及工业 机器人商业化起步较晚,但领军企业如埃斯顿通过积累底层技术和外延并购优质资产,已经实 现了 80%的零部件自主供应,具备满足通用化和定制化需求的本体自主设计能力,并能够开 发、优化软件算法提升机器人本体质量。从这个角度来看我国工业机器人处于快速替代进口产 品的阶段,并且国内工业机器人龙头企业也在开拓海外市场,包括设立研发中心,收并购海外 企业,和海外公司进行战略合作,产品出口等,国内龙头优势有望进一步放大。
三、把握专用设备景气加速个股掘金
(一)光伏设备
1、光伏设备三大驱动因素:需求提速、供给释放、技术革新
(1)需求端:全球需求持续释放,2023 年全球装机或超 330GW
2023 年国内光伏装机或达 127GW,同比增速 49%。据各省十四五光伏装机规模预计 500GW,对应年均 100GW 以上。从装机先行指标招标规模来看,1-11 月有超过 110GW 光伏 EPC 项目启动招标,近 80GW 光伏 EPC 项目公布中标结果(去年同期仅为 10 余 GW),为 2023 年装机高增长奠定基础。
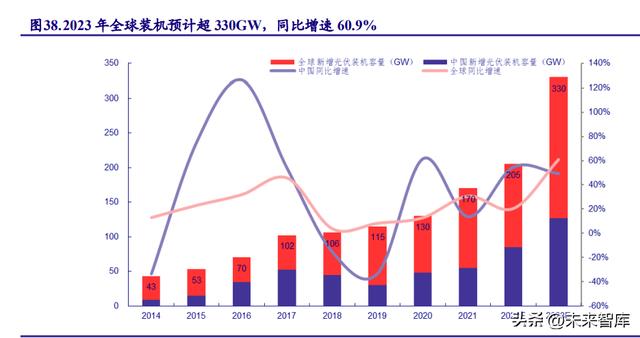
2023 年全球新增装机预计达 330GW,同比增速 60.9%。2022 年 1 到 10 月累积出口组件 达 133.3GW,同比增长 83%。其中欧洲组件进口 74.7GW,俄乌冲突加剧能源紧张局势,欧盟 将 2030 年可再生能源目标从 40%提升至 45%,预计 2023 年欧洲装机接近 75GW,同比增速 35%。 2023 年光伏设备市场空间或达 700 亿元。目前 PERC 生产线单 GW 投资额预计 1.3 亿元, topcon 对应 2.3 亿元,HJT 对应 4 亿元,保守计算,每年全球光伏设备市场空间约 700 亿元。
(2)供给端:硅料长期供不应求的局面将根本扭转
2023 年底硅料产能预计达 200 万吨之上,预计可支撑装机约 600GW。硅料供不应求的局 面得到根本改变,带动组件价格下降将进一步刺激装机需求,设备端将受益。以上数据按照 2.8g/w 及 1.2 倍容配比测算。 供给端相对紧张环节将转移至石英坩埚,非硬性瓶颈,价格具备上涨弹性。石英坩埚是光 伏硅片长晶环节耗材,原材料石英砂在下游需求放量而供给有限的情况下,供需格局趋紧,且 高端石英砂供给相对刚性。23 年年装机若按 350gw 测算,对应石英砂需求 8.8 万吨,预计 2023 年全球供给 9.6 万吨,供需比 1.09,处于紧平衡。
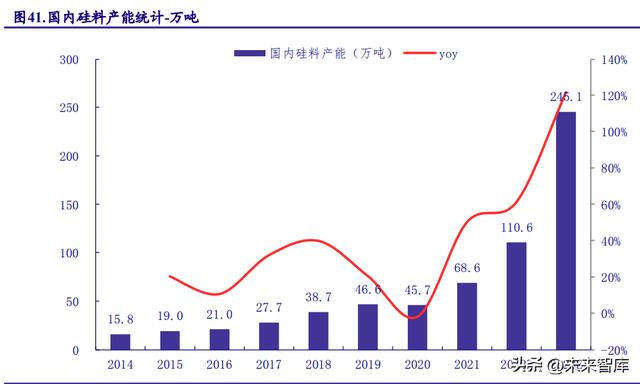
(3)光伏产业链面临的技术变革
降低度电成本、开发高效电池,即降本增效是行业发展趋势和主流方向。硅料环节目前主 流技术路线为改良西门子法(产物为棒状硅),流化床法(产物为颗粒硅)凭借无需破碎、可 连续加料等优势加速渗透;拉棒环节,CCZ 连续直拉法省去了单晶棒冷却时间,大大提升生 产效率;硅片向薄片化、大尺寸方向发展,以有效较少单片硅耗量及硅棒的切割损耗,钨丝作 为母线的金刚线,目前中钨高新已建成 100 亿米光伏钨丝生产线,处于产能爬坡阶段;在开发 高效电池方面,目前主流的 P 型电池向光电转化效率更高的 N 型(TOPcon、HJT、xBC)电池 转变,预计 2023 年 HJT、TOPcon 电池占比进一步提升。在上游环节的技术变革影响下及降本 增效目标驱动下,组件环节技术变革主要围绕适应电池片调整、提高转换效率及单位电池片密 度而进行。
2、光伏设备产业链梳理
(1)硅片设备
硅片连接上游硅料及下游电池片,目前单晶硅片是市场主流
多晶硅片占比快速减少,单晶硅片市占比从 2016 年不足 20%提升至 2021 年 95%。硅片 是实现多晶硅原料向光伏晶硅电池转变的必经阶段。单晶硅片制造企业主要利用单晶硅炉生 产单晶硅棒,多晶硅片企业主要利用铸锭炉生产多晶硅锭,而后再将其加工成单晶硅片或多晶 硅片,最终用于制造晶硅电池片。光伏硅片可分为多晶和单晶硅片,当硅原子以金刚石晶格排 列晶核的晶面取向相同为单晶,否则为多晶。因单晶电池光电转换效率可比多晶电池高 2-3%, 在光伏电池降本增效的目标驱动下,单晶硅片市占比迅速提升。 硅片制造工艺步骤主要包括拉晶、切片,目前设备均已实现国产化,拉晶过程根据掺杂剂 不同分别得到 P 型或 N 型硅片,切片步骤目前主要采用金刚线切割。拉晶工艺主要包括 Fz(悬 浮区熔法)、Cz(直拉法),Fz 法可生产高纯度单晶,但对多晶硅原料的尺寸、设备、技术要 求较为苛刻,生产成本高,目前主要用于对硅片要求更高的半导体领域。光伏领域主要使用 Cz 法,Cz 法过程中掺杂三价硼族得到 P 型硅片,五价磷族得到 N 型硅片。拉晶环节核心设备为 单晶炉,已全面国产化。光伏硅片切割主要采用线锯切割方式,分为游离磨料和固结磨料两种, 前者以砂浆切割为代表,通过钢线、游离液体磨料及待切割硅料三者摩擦作用进行切割;后者 采用金刚线(金刚石粉固定在钢线上)进行切割,具有切割速度快、硅片品质高、成本低的优 点,目前在单晶领域金刚线切割已完全取代砂浆切割。切片环节核心设备为多线切割机,国产 厂商已主导市场。
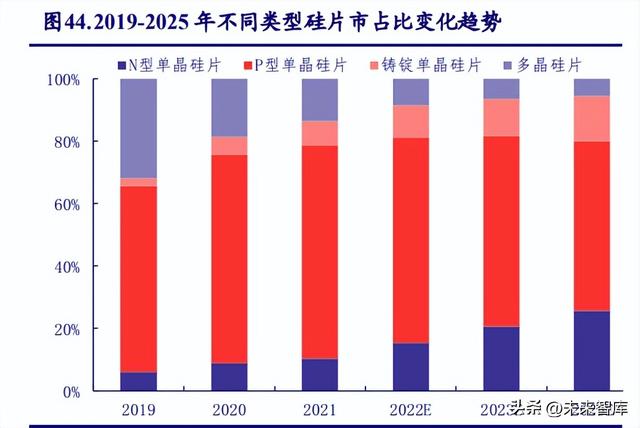
硅片环节迎大尺寸、薄片化、N 型化历史机遇
拉晶环节降本路线主要是大尺寸及优化投料工艺。目前公认大尺寸体系可降低全产业链 生产成本约 0.07-0.09 元/w,拉晶环节老旧单晶炉已无法拉制 210 尺寸硅片对应硅棒,单晶炉 设备迎更新需求。当硅片尺寸在一定范围内增大时,不换设备只改变夹具就可增加产出率,有 效摊薄单位成本。自 2019 年中环 210 和隆基 18X 的相继推出,大尺寸硅片在 2021 年三季度 市占比首次超过 50%并持续增加中。根据 PV InfoLink 预测,到 2022 年末,大尺寸硅片包括 182 和 210 的市占将达 79%。老旧单晶炉设备热屏内径一般不超 300mm,有的仅为 270mm, 而目前 210 硅片对应硅棒外径约 300mm,原单晶炉已无法满足 210 尺寸硅片所需硅棒的拉制 需求。目前8-12 英寸第四代且实现全自动化升级,第四代的 160炉型(210mm 向下兼容 180mm), 热场尺寸达 36 英寸以上,单炉投料量达 2800kg 以上。 RCZ(多次投料复拉法)在拉制单根硅棒时留下部分硅溶液使得坩埚保持高温,可令坩埚 多次利用,目前成为主流技术。CCZ(连续直拉法)可以一边加料一边拉制晶棒,增加了拉晶效 率,单晶电阻率一致性强、品质更高,对硅料要求高,更适合拉制 N 型硅,有望成为下一代拉 棒主流工艺。
切片环节降本路线主要是薄片化及切割细线化。硅片薄片化可以有效减少硅材料消耗, 提高单位产能,目前市场主流的 182、210单晶硅片厚度达到 160um,相比 2016年减薄了 16%。 2021 年以来,受到硅料价格快速上涨影响,硅片厚度有加速减薄的趋势。同时,为减少切片 环节因锯缝造成的硅料损失,金刚线切割呈现细线化趋势,金刚线母线直径已由 2016 年的 80um 降至 2021 年 43um 左右。 N 型电池具有弱光响应好、光致衰减小等优点,有更大的效率提升空间,N 型电池是电池 技术发展主要方向,对应 N 型硅片需求进一步增加,N 型硅片相比 P 型硅片需要纯度更高的 多晶硅料。根据 CPIA 预测,2022 年 N 型硅片市占将达 10%左右,预计 2025 年市占达到 25%。 2022 年以来硅棒/硅片规划及在建规模已超 200GW,带动硅片设备需求。产业链垂直一 体化趋势愈发明显。2021 年硅料硅片涨价潮以来,光伏电池片、组件厂商愈发认识到硅料、 硅片环节重要性,促进部分下游厂商加快垂直一体化的布局,呈现进一步整合趋势。
薄片化推动细线化趋势,钨丝金刚线渐行渐近
硅片环节:薄片化推动细线化趋势,钨丝金刚线渐行渐近。为减少切片环节因锯缝造成的 硅料损失,金刚线切割呈现细线化趋势。根据聚成科技公告,目前行业领先水平钨丝已做到 28 线,且同规格的钨丝线优于碳钢线。 钨丝单价高于碳钢线,盈利能力边际改善。根据聚成科技公告,2022H1,碳钢线和钨丝线 的单价分别为 35.95 元/公里、74.07 元/公里,毛利分别为 35.68%、36.85%,销售分别为 42.25%、 57.75%。除聚成科技外,原轼新材、三超新材、岱勒新材也分别实现钨丝金刚线小批供应。
(2)电池片设备
P 型向 N 型转换,高效电池技术路线引领光伏发展新纪元
高转换效率牵引下,BSF→PERC→N 型电池(主要包括异质结电池和 TOPcon 电池)技 术总路线清晰,2021 年 PERC 新建量产线市占 91.2%,N 型电池市占 3%,随着 N 型电池成 本的降低及良率的提升,市占有望进一步提升。对四年以来的电池片渗透率进行复盘,2017 年 常规 BSF 电池市占率达 83%,随着 PERC 效率得到市场认可,市占率由 2017 年 15%提升至 2020 年 86%,基本全面替代 BSF 电池。2021 年,新建量产产线仍以 PERC 电池产线为主,随 着 PERC 电池片新产能持续释放,PERC 市场占比进一步提升至 91.2%。2021 年 BSF 电池市 场占比下降至 5%,较 2020 年下降 3.8%。N 型电池(主要包括异质结电池和 TOPcon 电池) 量产规模仍较少,市占比 3%,具体而言,TOPcon 产品良率低的关键技术问题仍未完全解决, 异质结电池制造成本端仍比 TOPcon 高 0.2 元/w 左右(目前 PERC、TOPCon、HJT 设备投资 成本分别为 0.12、0.21、0.4 元/w)。根据 CPIA 预测,伴随高效 N 型电池生产成本的降低及 良率的提升,预计 2027 年 N 型电池量产线市占比将超 50%。
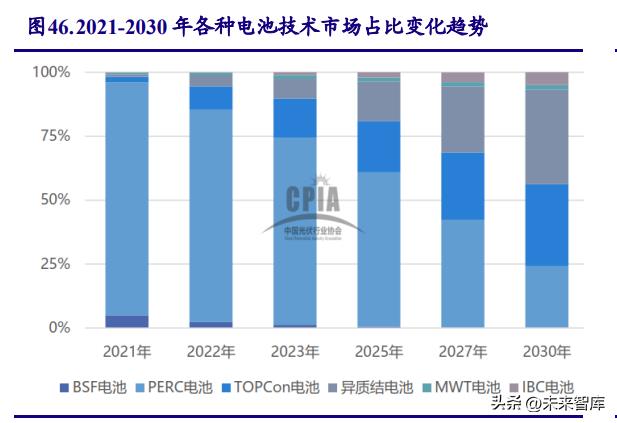
HJT 电池工序简单可控、光致衰减低、效率高,相较其他路线有明显优势,目前单瓦制 造成本高是阻碍 HJT 迅速扩张的重要原因。目前 HJT 电池组件 1GW 的总投资约 7 亿元人民 币左右(其中:电池设备投资接近 4 亿元/GW)。主要降本增效路线:一是微晶技术量产,电 池片平均转换效率显著提升。二是浆料平价,通过引入 12BB 以上多主栅技术、优化网版、银 包铜量产导入等工作,显著降低浆料成本。目前华晟 M6-12BB 电池单片银耗量已降至 150mg 以下,导入银包铜浆料后年内有望将 HJT 电池银浆耗量降至 120mg/片。三是硅片薄片化,异 质结的对称结构、低温或无应力制程可以适应更薄的硅片,100um 厚度超薄 HJT 专用硅片的 量产导入,在当前成本结构下可直接降低 HJT 产业链成本约 0.17 元/w(Solarzoom)。
xBC 技术将 PN 结、基底与发射区的接触电极以交指形状做在电池背面,可最大减少光学 损失,相较于常规电池可以获得更高的电流,目前制程工艺复杂,激光开槽技术可用于背面钝 化层开膜上,可简化工艺流程,大幅降低生产成本。隆基绿能 HPBC 电池泰州 4GW 将于 2022 年 8 月投产。
(3)新技术变革下组件设备(串焊设备)有望迎来量价齐升
组件设备环节主要受上游技术变革及降本增效高效双重因素影响
在上游环节的技术变革影响下及降本增效目标驱动下,组件环节技术进步方向主要包括 适应电池片栅线调整的多主栅串焊工艺、提高光电转换效率的半片等工艺、提高单位面积电池 密度方向的叠瓦、拼片等工艺。 2021 年以来,行业对串焊机的需求基本统一为兼容大尺寸。2020 前的组件设备只可兼容 到 166 尺寸,在硅片大尺寸趋势下,由于组件设备的不兼容性,2020-2021 年行业扩产的重要 驱动力来自于大尺寸设备对小尺寸的替代。光伏组件制备核心设备为串焊机,价值量占组件设 备价值量的三分之一左右,受益于大尺寸组件的占比上升,串焊机更新周期由原来的 3-5 年缩 短至一年半。 薄片化降本的逻辑在于降低单片硅耗,在控制碎片率的前提下实现降本目的。根据爱康科 技测算,硅片厚度每降低 10um,成本可便宜 0.16 元/w,若 HJT 厚度从 170um 下降至 120um, 成本相对于 PERC 具有优势。Topcon 在高温工艺下如果硅片厚度过薄,其钝化层会存在浆料 烧穿的情况,致使良率大幅降低,由于 HJT 为低温工艺,比 TOPcon 更容易实现薄片化。目前 TOPcon 厚度通常在 160um 以上,HJT 可以做到 120um。薄片化对串焊提出更高的要求以控制 碎片率。
N 型电池扩产有望提升组件设备价值量
SMBB 主要通过将细栅变窄实现降低银浆量目标,适用于细栅银浆耗量更大的 TOPcon 电 池。HJT 使用的为低温浆料,其颗粒比高温银浆更大,所以不能降低主栅和细栅的线径,降低 细栅的银浆耗量而增加主栅数量无法吸纳朱降低 HJT 的成本。更细的栅线对定位的精准度、 焊接的精准度等提出更高的要求,有望带动单 GW 设备价值量提升。 0BB 主要针对 HJT 电池,能够完全去除主栅的银浆耗量,该技术对于串焊机放置焊带及 电池片的精准度要求更高,现有的串焊机因无点胶、印刷机、固化的功能而较难改造为 0BB。
3、第三代太阳能电池钙钛矿产业化加速
(1)钙钛矿电池(PSCs)是第三代太阳能电池代表
从晶硅到钙钛矿,钙钛矿材料介绍、光电特性及工作原理
第一代晶硅电池目前最成熟,第二代薄膜电池相比第一代具有质量轻、转换效率高的优势, 但电池活性层材料昂贵且设备成本高等因素限制其大面积制备和商业化,第三代新型太阳能 电池凭借材料成本低、效率高、工艺流程短等优势成为产业界和学术界热点。 广义的钙钛矿其实是指具有 ABX3 型的化学组成的化合物:A 位一般由有机无机杂化,包 括甲氨 Ch3Nh3或者甲醚有机的分子,或无机的铯,B 位一般由硒或者铅,X 位一般都是卤素, ABX 通过化学配位键进行连接,形成 ABX3 结构式,这种结构称为钙钛矿,用在钙钛矿电池 的吸光层。 钙钛矿具有优异的光能吸收性,较高光吸收系数有利于减少光学损失,在 300-800nm 波 长范围均有高吸收系数(大于 3*10-4 cm-1 )。缺陷态密度低使得非辐射复合率很低,电压损失值 小,开路电压损失在 0.3-0.4v 之间。钙钛矿材料可以通过调节组分,使其能带间隙在 1.4~2.3eV 之间连续可调,因此可以衍生出区别于硅基光伏的应用。目前最常用的钙钛矿材料 MAPbI3 和 FAPbI3 的禁带宽度位于 1.5-1.6eV,其理论最大光电转化效率均处于 30%以上。连续可调的带 隙宽度可制备钙钛矿叠层多结电池。通过对钙钛矿进行组分调控,可实现带隙连续调控,通过 调整A、B和X含量可以获得不同组分钙钛矿材料,对应钙钛矿材料的带隙及能级分布也各不 相同。
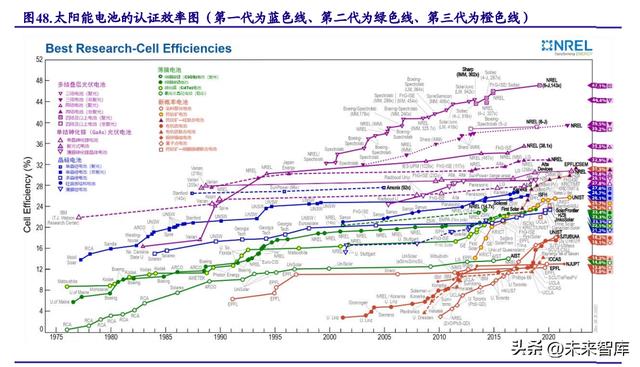
(2)效率提升空间大,降本优势明显
钙钛矿理论极限效率高于晶硅电池,可达 30%以上
钙钛矿太阳能电池(PSCs)单结理论极限效率超 30%,叠层模式下可达 40%以上,相比 晶硅电池效率提升空间大,主要因为人工设计后的钙钛矿材料带隙可以达到或接近 s-q 理论下 吸光层最优带隙(1.3-1.5ev)。钙钛矿电池实验效率从 2009 年的 3.8%提升至目前的 25.7%, 电池效率提升速度远快于晶硅电池的核心原因是钙钛矿电池材料可设计性强。
产业化效率稳步提升,目前已达 16-18%
产业化效率稳步提升,目前已达 16-18%,2023 年玻璃基中试组件最高转换效率预计达 19.3%。近年来产业化效率呈现逐步上升趋势,2019 年协鑫光电在实现 1241.16cm2 面积 15.31% 的效率,同年杭州纤纳在 300cm2 尺寸的钙钛矿组件实现 14.3%效率,华能集团 2019 年实现 100cm2 组件效率 18%,2021 年实现 3500cm2 面积电池效率 15.5%。2022 年极电光能在 300cm2 大尺寸组件实现 18.2%转化效率,同年协鑫光电尺寸为 1m*2m 组件下线,据协鑫光电预计在 工艺和产能稳定后,量产组件效率将超 18%。目前产业化效率距离钙钛矿单结电池理论极限效 率(超 30%)还有较大提升空间,产业端、研发端针对钙钛矿电池的研发投入逐年增加,随着 钙钛矿可设计性晶体配方以及工艺逐步优化,产业化效率预计呈现上升趋势。根据 CPIA 预测, 玻璃基中试组件最高转换效率(>900cm2)2022 年达到 18.5%、2025 年 20%、2030 年 22%。
规模化降本优势明显,GW 级产能组件成本可降至 0.6 元/W
从 100MW 级扩大至 GW 级产能,组件成本下降约 50%,由 0.15 美元/W 降至 0.1 美元 /W。目前有三家公司公布过其钙钛矿电池的生产成本。纤纳光电 100MW 生产线组件成本约 0.15 美元/W,扩大至 GW 级产线后组件成本约 0.1 美元/W;协鑫光电 GW 级产线组件成本 可低于 0.1 美元/W。
(3)产业化落地加速,钙钛矿设备显著受益
工艺路线:与材料、配方及电池结构等要素相关(以平面反式为例)
平面结构电池中每层工艺路线与对应材料、配方、电池结构等要素相关,可能涉及的工艺 如下:(一)导电基底一般使用 CVD 或 PVD 法制备 ITO 或 FTO 导电玻璃。若第二层空穴传 输需要温度较高的工艺,则选择 FTO 导电玻璃,因为 ITO 超过 300 摄氏度之后,会容易出现 弯曲形变。(二)空穴传输层 PVD 法或刮涂法制备,不同材料对应不同制备方法。如果选择 氧化镍,它基本上就是喷涂、喷雾热解制备或者是用 PVD 法制备。如果选择 PTAA 等有机物, 就需要刮涂制备或者是喷雾热解制备。(三)钙钛矿吸光层比较流行做的是湿法制备、刮棒制备、狭缝涂布制备以及喷雾热解制备,不同工艺方法各有优缺点,目前使用湿法,尤其是涂布 工艺较多。(四)电子传输层若选择有机材料会使用蒸镀工艺,若为金属氧化物则会涉及气相 沉积等工艺。有机材料,比如富勒烯等,选择的方式可能是蒸镀,尤其是团簇式蒸镀设备。如 果选择二氧化锡或者硫化镉或者是二氧化钛这一部分,则使用 PVD 设备,或是 RPD、磁控电 射等设备。(五)电极层选择金属电极通常对应蒸镀工艺,若选择透明导电电极通常对应磁控 溅射工艺。
设备端:主要为镀膜设备、涂布设备、激光设备、封装设备
产线设备类型主要为镀膜设备、涂布设备、激光设备、封装设备,其中镀膜设备价值量过 半,激光设备确定性需求强,封装设备与晶硅电池相比差别不大。(一)镀膜设备主要涉及 PVD 及 RPD 设备,其中 RPD 设备比传统的 PVD 设备优势在于可以减少对钙钛矿电池的轰击损害, 有利于提高转换效率和良率。相应的设备企业有捷佳伟创、迈为股份、京山轻机、众能光电等, 其中捷佳伟创于 2022 年 7 月获钙钛矿电池量产 RPD 镀膜设备订单,该 RPD 设备具备较高技 术壁垒;蒸镀设备主要涉及京山轻机等,2021 年 5 月京山轻机子公司晟成光伏与协鑫光电开 展叠层技术战略合作,晟成光伏钙钛矿团簇型多腔式蒸镀设备已实现量产并应用于多个客户 端。(二)涂布设备主要用于制作钙钛矿吸光层,主要企业德沪涂膜(未上市)、众能光电等, 德沪涂膜为协鑫光电 100MW 产线供应大尺寸狭缝涂布设备,狭缝涂布可在玻璃、塑料等基片 上沉积液体化合物,精确控制液体流量和移动相对速度,制备所需技术指标的薄膜。众能光电 目前已对外销售刮涂/涂布一体机。(三)目前各种技术路线均需要激光设备,激光设备主要应 用工序为激光划线,把大的面板进行切割,形成子电池,再将电池用串联或者并联的方式连接。 目前供应钙钛矿激光设备的公司包括大族激光、迈为股份、德龙激光、杰普特、帝尔激光、众 能光电等。
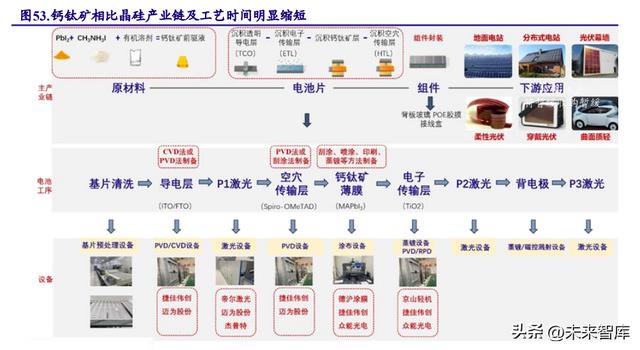
(二)风电设备 1、风电设备:明年是交付大年,关注抗通缩及国产替代主线
(1)2022 年装机并网不及预期,2023 年全球/国内风电新增装机需求有望达到 115/75GW
2022 年前三季度国内风机招标量已达 76.3GW,同比增长 83%;我们预计 2023 年全球/ 国内风电新增装机需求有望达到 115/75GW,同比增长 21%/67%,2022-2025 年全球/国内风电 新增装机 CAGR 有望达到 14%/28%。整体看 2022 年招标量有望达到 100GW,按照招标量年 内与下年 3:7 的比例,预计 70%招标的风机将于 2023 年交付并网,为未来风电装机打下坚实 基础。
(2)风机大型化下关注抗通缩环节及国产替代主线
风机大型化持续推进,招标价格持续下跌,2022 年 9 月月度公开招标均价已降低至 1808 元/kw。平均功率提升及单位成本降低有望带动风电装机量提升。
(三)核电设备
1、核电技术发展助力双碳背景下核电复苏
(1)核电技术快速发展
核电技术的发展从第一代到第四代,甚至第五代也被提出。从核电站技术演变来看,主要 可划分四代核电技术。第一代是实验性的核电站,主要目的是为了通过试验示范形式来验证其 核电在工程实施上的可行性,目前已基本退役;第二代核电技术具有标准化、系列化、批量化 的特点,安全性较、经济性均提高,但应对严重事故的措施仍薄弱;第三代核电技术是主流, 安全性更高,建造周期缩短,寿命延长,目前我国新建均为三代机型,正在逐步取缔二代+机组 成为主力,2021 年 9 月,世界首个钍核反应堆在甘肃成功运行,中国或将于 2030 年前建造一 个为 10 万居民提供电力的 373 兆瓦钍核反应堆;第四代仍在发展阶段,预计 2030 年左右推 出解决核能经济性、安全性、可持续性、废物处理和防止核扩散问题的核能系统。第五代核能 系统是一种“核能协同网络”的概念,具有系统性、灵活性和多能性三大特点。
(2)全国核电机组装机规模持续增长
核电机组核准数量是核电装机规模的先行指标,2022 年核电机组核准数量已达 10 台,是 2008 年以来的最多年份。2011 年日本福岛核事故以来,中国一度暂停新增核电项目审批,直 至 2012 年 12 月才核准江苏田湾核电二期工程,2022 年我国核准 5 个核电项目,共计 10 台核 电机组,是 2008 年以来最多年份。截至 2022 年 9 月,我国在运核电机组数量 54 台,其中中 广核 26 台,中核 25 台,国家电投 2 台,华能 2 台,乐观预计 2030 年我国在运核电机组或达 96 台。我国在建核电机组 23 台,其中中核 10 台,中广核 9 台,华能 2 台,国家电投 2 台。
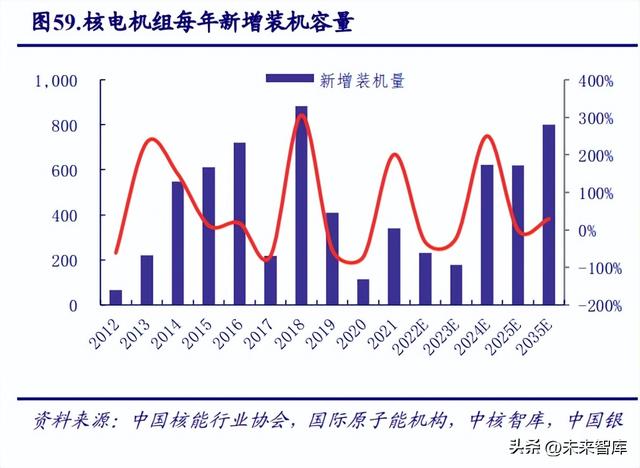
(3)核电装备市场空间或达千亿元
2022-2025 年我国核电装备市场空间或达千亿元。按“十四五”期间我国核电运行装机容 量达 7000 万千瓦,每台核电机组 100 万千瓦装机容量计算,2022-2025 年间,核电建设有望 按照平均每年 7-8 台机组推进。核电站每千瓦建造成本 1.1-1.8 万元,设备市场空间占比约为 建造成本的一半,按平均每年 7-8 台机组推进,2022-2025 年核电设备市场空间或达千亿,约 825-1350 亿元,对应核电设备市场空间 413-675 亿元。
2、核电发展提速背景下核电新燃料储运的投资机会
(1)我国新燃料运输容器迈入国产化替代
我国核电产业起步较晚,此前新燃料储运容器主要来自国外购入。国际上主要的核电大国 美国、法国、俄罗斯等核能产业发展时间长,于新燃料运输方面积累了丰富的技术经验,其所 产容器为国际所广泛使用。法国主管部门批复 FCC3、FCC4 型运输容器满足新燃料组件安全 运输需求。美国按照 A(F)或 B(F)型货包的要求进行核燃料组件运输容器设计,在力学、临界 安全等方面的考虑充分,而俄罗斯 TK-C5 型、TK-C5-M 型等运输容器结构相对简单。总体上, 国外核燃料组件运输容器装载兼容性和系列化程度较高。
(2)我国新燃料运输容器的市场空间测算
新燃料组件运输需求来自当年新建成和在运核电机组。当年新建成核机组的燃料组件运 输需求为当年新建成核电机组数与单台核电机组对应组件数量的乘积。在运核电机组的燃料 组件运输需求为当年在运核电机组数与单台核电机组对应组件数量乘积的三分之一。由于我 国商用核电站分布于沿海地区,元件制造厂地处内陆,核燃料组件运输路程较长、路况复杂, 考虑元件制造周期和厂内存放周期,一年周转 2 次。此外,一台容器可以装两个燃料组件。因 此,每年的新燃料容器年市场需求为当年新建成和在运核电机组的燃料组件运输需求的四分 之一。
3、核电发展提速背景下核电乏燃料储运的投资机会
(1)乏燃料运输国内外发展进程
乏燃料运输容器的发展历程分为 5 各阶段:第一阶段为研究堆用小型乏燃料运输容器(10 t 左右);第二阶段为商用堆用小型乏燃料运输容器(20 t 左右);第三阶段为商用堆用大型 乏燃料运输容器(100 t 左右);第四阶段为商用堆用系列化大型乏燃料运输容器;第五阶段 为大型多用途乏燃料容器(研究堆、商用堆、存储、运输)。主要核电大国均有了技术成熟、已经形成系列化的乏燃料运输容器,多数处于第四阶段并向第五阶段发展,如法国 TN 系列容 器、美国 NAC 系列容器、德国 Castor 系列容器、日本 MSF 系列容器、俄罗斯 TK 系列容器等。 对比国内与国外发展现状,我国目前已逐步进入第三阶段。1994 年,核二院研制的 RY-I 型研究堆用小型运输容器在大连 523 厂进行小批量生产,标志着我国完成了第一个阶段。齐齐 哈尔重型铸造致力于研制球墨铸铁核乏燃料运输容器,成功研制了 BQH-20 型球墨铸铁乏燃料 运输容器,目前该厂可生产 20 t 级的球墨铸铁乏燃料运输容器。2017 年 12 月中核“龙舟CNSC 乏燃料运输容器研制”项目中原型样机通过验收,并具备了批量化生产能力,这标志着 我国成功自主研制了大型乏燃料运输容器。 2021 年 6 月,我国自主设计制造的百吨级乏燃料 运输容器—CNSC 乏燃料运输容器顺利下线,这标志着我国逐步进入乏燃料运输容器的第三阶 段。
(2)乏燃料后处理需求旺盛
乏燃料产生量高,后处理需求大
我国乏燃料产生量逐年增长,到 2030 年乏燃料年产出 1803 吨,累计产出 23110 吨。我 国核电站设备平均利用率在 2013-2021 年基本在 80%以上,近三年超 90%,这说明核电站机组 运行稳定,基本满负荷运行。此外,对 2013-2021 年核电发电量与乏燃料年产量的数据进行回 归,可得两者呈正相关,据此来预测 2022 及以后的乏燃料年产量与乏燃料累计产生量。根据 《by Energy Outlook:2020edition》,中国核电年均增速为 5.4%至 6.0%,按 5.4%的增速对 乏燃料产出做等比估算,到 2030 年乏燃料年产出为 1803 吨,累计产出 23110 吨。
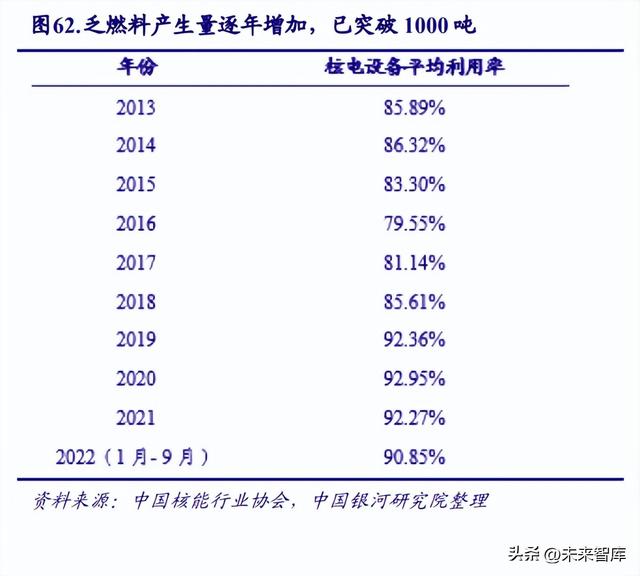
乏燃料组件类别不同刺激乏燃料后处理需求
乏燃料组件类别不同刺激乏燃料处理需求。不同堆型和型号对应的组件尺寸、形状有所区 别。以外形尺寸和燃料特性为划分依据,我国的乏燃料包括标准型四边形组件、加长型四边形 组件、短型四边形组件、六边形组件、圆柱形棒束组件、球形组件。乏燃料组件类别的不同对 乏燃料处理和储存能力提出了更高的要求。
闭式循环管理产生乏燃料暂存需求
中国坚定执行闭式核燃料循环政策。目前,各国主要采取直接进行深地层埋藏、闭式核燃 料循环两种方式处理乏燃料。直接进行深地层埋藏多用于美国、加拿大、北欧国家,成本低、 简单,但后患无穷(自然灾害、恐怖袭击等)。闭式核燃料循环多用于法国、日本、中国、俄 罗斯等国家。闭式核燃料循环指将乏燃料送至后处理厂,从中回收铀、钚,以实现重复利用核 燃料的目的。早在 1983 年,我国就确定了“发展核电必须相应发展后处理”的战略,2021 年我 国进一步明确了坚定执行闭式核燃料循环的政策。 天然铀需求大而产量不足,建立闭式核燃料循环的必要性进一步提升。天然铀是目前普遍 使用的核燃料,核电装机容量的增长增加了对铀的需求。根据世界核协会,天然铀需求量从 2013 年的 6711 吨增长到 2021 年的 9563 吨,增速达 4.5%。然而,我国天然铀不丰富且开采成 本高,2021 年我国铀产量仅占全球总产量的 3.4%,铀资源高度依赖进口,对外依存度常年维持 在 70%以上。根据世界核协会,我国铀产量在 2013-2021 年间仅增长 385 吨。因此,必须建立 核燃料闭式循环体系,这可使铀资源利用率提高 50~60 倍,大幅减少天然铀需求量,降低铀 对外依存度,实现核能可持续发展,这也符合我国建设资源节约、环境友好型社会的发展要求。
(3)乏燃料后处理能力弱
乏燃料产生量逐年增长,但是我国乏燃料后处理能力薄弱,目前乏燃料处理能力只有 50 吨/年,在建处理能力也仅为 200 吨/年。2010 年,我国在甘肃兰州建造了第一座乏燃料后处 理中间试验厂——中核四零四厂,拥有年处理 50t 的乏燃料处理能力。随后,中核集团提出了 在中试厂的技术基础上自主设计建设 200t/a 项目,目前正在建设。相比乏燃料的年产生量, 目前我国的乏燃料处理能力远远不够,需建立乏燃料离堆贮存能力。
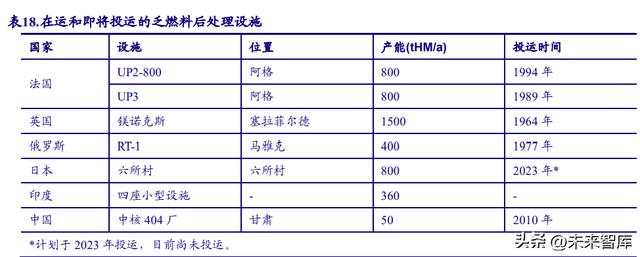
(4)乏燃料运输容器市场空间超千亿
基于乏燃料在堆冷却满 3 年后离堆贮存的前提假设,乏燃料运输容器对应市场空间将破 千亿。根据《田湾核电站乏燃料离堆贮存方案研究》,乏燃料组件在乏燃料水池贮 3 年后,放 射性和余热即可衰减至从反应堆水池运出的条件。所以,按 3 年正常测算乏燃料累计运出需求 量,到 2030 年,乏燃料累计运出需求量约 1.64 万吨,对应市场空间约 492.6 亿元。
(四)电动车仍处发展快车道,重点关注锂电中技术变革及供应 链重构中的设备机遇
1、全球新能源汽车快速放量,锂电技术革新打开设备成长空间
(1)新能源汽车渗透率快速提升,持续超预期
2022 年我国新能源汽车产销持续创新高,渗透率快速提升。中国新能源汽车市场产销两 旺表现突出,2021 年新能源汽车产量为 354.5 万辆,同比增长 159.52%;新能源汽车销量为 352.1 万辆,同比增长 157.57%;连续 7 年位居全球第一。2022 年 1-10 月,新能源汽车延续高 景气,产销量分别达到 548.5 万辆和 528.0 万辆,同比分别增长 113.8%和 107.69%;10 月单月 渗透率提升至 28.49%。
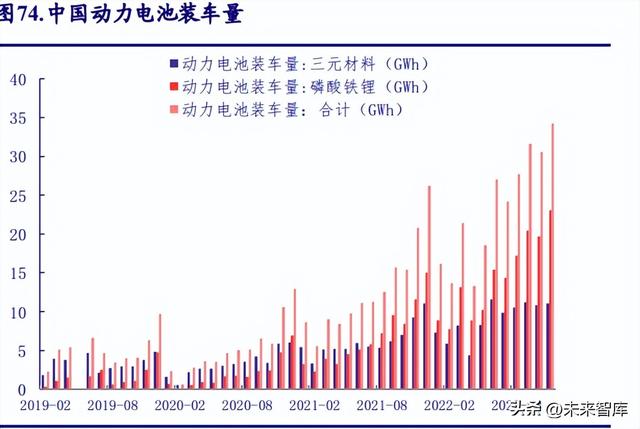
(2)动力电池扩产增速放缓,关注锂电技术变革带来的设备机遇
国内电池新增产能增长放缓,海外扩产仍在加速。从全球主流动力电池厂商产能规划来 看,2023-2025 年,国内预计将新增电池产能 843.8/680.5/439.0GWh,同比+17.28%/-19.35%/- 35.49%,产能扩张速度逐步放缓。同时,海外电池厂产能仍将保持较快增长,叠加国内电池企 业 出 海 建 厂 , 2023-2025 年 海 外 产 能 预 计 将 新 增 233.2/368.5/481.0GWh , 同 比 +58.86%/58.02%/30.53%。
2、4680 引领多环节技术变革,焊接设备充分受益
(1)特斯拉发布 4680 大圆柱电池,实现电芯降本增效
圆柱、方形、软包是动力电池封装的三种方式。相比方形和软包电池,圆柱电池优势在于: 第一,成组接触面较大,安全性佳。其弧形表面在充分接触时仍存在较大间隙,一定程度上抑 制了电池之间热量传递,且圆柱电池单体能量低,密封性较好,不易发生漏液现象,因此圆柱 电池在安全性方面优势明显。此外,圆柱电池一致性高,可以一定程度上避免由于电池不一致 导致的过充、过放和局部过热的危险。第二,材料兼容性强。为提高电池能量密度,高镍正极 材料和硅碳负极材料被应用到电池材料体系,但高镍材料较差的热稳定性和硅碳材料较高的 体积膨胀率对动力电池的安全性带来了考验。圆柱电池结构体强度更高,对硅碳负极脱胀的容 忍度较高,且圆柱电池的热失控传播阻断特性可以在一定程度上弥补高镍材料热稳定性差的 缺点,因此在应用高镍材料和硅碳负极材料方面,圆柱电池优势明显。
(2)电池厂布局 4680 产能,2023 年有望量产
海内外车企纷纷布局 4680,电池厂 2023 年有望实现量产。特斯拉 4680 电池将率先用于 Model Y 系列车型。2022 年 9 月,宝马集团宣布将从 2025 年起率先在其“新世代”车型中使 用全新圆柱电芯,已向宁德时代和亿纬锂能两家合作伙伴授予价值超过百亿欧元(约合人民币 700 亿元)的电芯生产需求合同,并还将寻找合作伙伴在北美自由贸易区建设电芯工厂为其供 应新型圆柱电池。戴姆勒、Rivian、小鹏、蔚来、江淮、一汽等国内外车企也逐步布局 4680 车 型。下游需求增长,各电池厂商纷纷布局 4680 产能。
(3)46 系列电池引领涂布+焊接工艺技术革新,设备环节率先受益
4680 电池主打“大电芯+全极耳+高镍高硅+CTC”,相比 18/21 系电池主要具备三点优 势:1)改进材料体系/结构硅基负极:能够提供更高的能量密度和倍率性能,能量密度提升 10%- 20%;2)使用新型电解液:添加新型锂盐,提高电解液窗口和充放电电压;3)无极耳/全极耳 设计:阻抗更小,提高电极和充电倍率,可承受 4C 以上高倍率电流,充电快。根据特斯拉披 露的数据,4680 电池在成本端较 21 体系圆柱电池综合降本 56%。 就设备环节而言,46 系列电池的新结构对辊压、涂布、极耳分切、焊接、揉平、注液等 工艺均提出了全新挑战。其中,干法涂布和全极耳激光焊接是技术变革的两大核心环节。相比 于传统湿法涂布,干法涂布不使用溶剂,工艺简单,节省制浆、混料、干燥等环节设备成本; 生产速度可提升至原来的七倍。另一方面,干法涂布避免了锂与混有锂金属的碳在有溶剂情况 下无法很好地融合,导致第一次循环容量损失的问题,还可将正极材料厚度从 55μm 提升至 60μm,提升活跃电极材料比,从而使能量密度提升 5%的同时保证功率密度。
焊接工艺难度、数量升级,关注激光焊接设备投资机会。全极耳极片端面与集流盘的面焊 增加了焊接工序和焊接量,对激光焊接工艺要求大大提高。焊接数量方面,从传统两个极耳的 点焊到 4680 全极耳的面焊,焊点数量相比 21700 提高五倍以上,单 GWh 电池产线增加了 5 台焊接设备,相比方形电池激光焊接工序从 5 道增加至 7 道。焊接难度方面,面焊的激光强度 和焦距不轻易控制,激光焊接工艺不稳定可能会导致焊穿烧到电芯内部或者没有焊接到位,一 般需要使用连续激光器。4680 产线单 GWh 需配置焊接设备数量增加,叠加工艺技术要求提升 带来的焊接设备价值量的增加,将充分利好激光焊接设备厂商。
3、复合铜箔产业化前夜已至,2025 年设备市场空间超百亿
(1)安全性+低成本+轻量化驱动复合铜箔产业化发展
典型锂离子电池结构主要包括正极、负极、电解液和隔膜四部分。锂电池充电时,加在电 池两极的电势迫使正极的嵌锂化合物释放出锂离子,通过隔膜后嵌入片层结构的石墨负极中; 放电时锂离子则从片层结构的石墨中析出,重新和正极的嵌锂化合物结合,锂离子实现移动, 产生电流。铜箔在动力电池成本中占比 9%,为提升电池能量密度和安全性,并进一步降低成 本,锂电铜箔正在向高密度、轻薄化、高抗拉强度、高延伸率等方向发展。
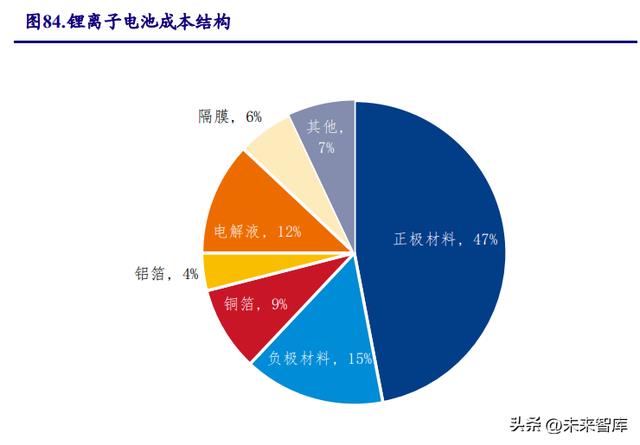
1)高安全性:传统技术仅能对内短路起到延缓作用,而且以牺牲电池能量密度为代价。 而复合集流体中间的高分子基材具有阻燃特性,其金属导电层较薄,短路时会如保险丝般熔断, 在热失控前快速融化,电池损坏仅局限于刺穿位点形成“点断路”。
2)高比能:复合集流体中间层采用轻量化高分子材料,重量比纯金属集流体降低 50%- 80%。复合铜箔中铜厚度相比 6μm 铜箔减少 66.67%,复合铝箔中铝厚度相比 10μm 铝箔减 少 80%。金属用量的节省部分用 PET 等材料进行替代后,保障安全性的同时重量更轻,产品 综合性能更优。随着重量占比降低、电池内活性物质占比增加,能量密度可提升 5%-10%。
3)长寿命:高分子材料围绕电池内活性物质层形成层状环形海绵结构,在充放电过程中, 可吸收极片活性物质层锂离子嵌入脱出产生的膨胀-收缩应力,从而保持极片界面长期完整性, 使循环寿命提升 5%。
4)低成本:PET 铜箔规模化成本显著低于传统铜箔。以 6μm 铜箔为例,其单位材料成 本为 3.73 元/平方米;而 6.5 微米 PET 铜箔的铜箔厚度为 2μm,单位总成本为 1.3 元/平方米, 低于铜箔的单位成本,材料成本优势明显。传统铜箔的原材料成本占比约 83%,而复合铜箔原 材料成本占比约 31%,且受产业化初期影响设备成本占比高达 50%,复合铜箔生产通过规模 效应降低成本的空间更大。在技术完备条件下,复合铜箔大规模量产后有望实现 4.5 元每平米 以下,相较传统铜箔有望实现降低 40%的制造成本。
(2)产业化进程不断加速,核心设备 2025 年市场空间超百亿
从产业链上下游布局来看,复合铜箔产业化趋势较为明朗,2023 年有望实现量产。东威 科技作为目前国内唯一可量产电镀设备的企业,将保持较强的先发优势。目前,东威科技已先 后与客户 D、客户 L 签订 5 亿元和 10 亿元双边夹卷式水平镀膜设备订单,与宝明科技签订 2.13 亿元双边夹卷式水平镀膜设备订单,并于 12 月 9 日与胜利精密签订战略合作框架协议, 将分别在 2023 年上半年和下半年交付 10 台、30 台新型高速高效水平夹持式复合铜箔电镀设 备。产能方面,明年产能计划不低于 100 台,规划在 100-300 台左右;目前在手订单已接近 300 台,现有订单均将在 24 年底完成。东威科技将在巴城镇投资建设昆山东威新能源设备扩能项 目,预计年产销 300 台(套)卷式水平膜材电镀设备和 150 台(套)磁控溅射卷绕镀膜设备。 预计 2025 年磁控溅射+电镀设备市场空间合计达到 110 亿元。根据主流电池厂商产能规 划,假设 2022-2025 年,复合铜箔在新增电池市场中渗透率为 0.5%/8%/15%/25%。按单 GWh 需 2 台磁控溅射设备和 3 台电镀设备,单台价格分别为 1400 万元/1000 万元,随着效率和良 率的提升,单 GWh 所需设备数量逐步减少。则到 2025 年,磁控溅射设备和电镀设备市场规 模将分别达到 54.7 亿元和 55.2 亿元。
4、换电风起重卡先行,设备厂商率先受益
(1)补能需求+政策导向,推动换电市场快速发展
随着新能源汽车渗透率的快速提升,新能源汽车的补能需求也大幅提高。目前,新能源汽 车补能方式主要有充电和换电两种。充电补能分为慢充与快充两种形式,分别对应交流充电桩 与直流充电桩。交流充电桩功率较低,电池需要 8-10 小时才能充满。直流充电桩功率较高, 电池在半个小时内就可充满 80%,但是直流充电对电池损耗较大。换电模式为直接更换电池进 行补能,通过换电站对大量电池集中储存、集中充电,于站内为新能源汽车提供电池更换服务, 按换电方式可分为底盘换电、侧方换电和分箱换电。
在政策推动和新能源汽车市场的飞速发展下,我国乘用车换电站数量快速增加。截至 2022 年 11 月,我国已建成乘用车换电站数量从 2021 年 1 月的 562 座,增长至 1902 座,环比增加 4.11%。从市场格局来看,蔚来、奥动新能源和伯坦科技为主要的换电站建设企业,其中蔚来 的市场份额达到 65.51%。

目前,包括干线物流车、渣土车、牵引车、矿卡等在内的各类用车场景均在大力发展换电 模式,相关产品及商业化逐步被市场验证,换电重卡在新能源重卡中的占比飞速提升。2022 年 10 月,换电重卡销量 966 辆,在新能源重卡中占比高达 56.10%,新能源重卡渗透率仍较低, 仅有 3.57%,但未来换电重卡市场确定性明朗,有望持续快速发展。
(2)换电站布局进程加速,设备市场空间巨大
目前,我国布局换电站的玩家主要可以分为四类:1)以北汽、吉利、蔚来为代表的车企; 2)以宁德时代为代表的动力电池企业;3)以奥动新能源为代表的第三方运营商;4)以中石 化、中石油等为代表的能源央企。 蔚来换电站主要面向 C 端客户,并推出独有的 BaaS 服务。自 2017 年 ES8 起,所有电动 车均支持换电。2020 年,蔚来推出车电分离的电池租用服务(BaaS)模式,并与宁德时代、 湖北省科技投资集团以及国泰君安国际控股有限公司子公司共同投资电池资产公司。用户分 别购买电动汽车和租用电池,选择 BaaS 服务购买 75kWh 和 100kWh 的新能源汽车可分别节 省 81340 元和 140600 元,并对电池每月支付 980 元和 1680 元的租用费。蔚来自 2021 年 4 月起部署的第二代换电站,将换电时间缩短至 3 分钟内,可容纳 13 块电池。
5、汽车轻量化趋势明朗,一体压铸设备需求释放
(1)汽车轻量化加速,压铸机市场空间广阔
在全球节能减排的大趋势下,汽车轻量化已成为全球汽车工业的一致目标。《中国制造 2025》明确指出轻量化技术是汽车行业未来共同突破的重点方向。为实现“双碳”目标,我国 持续推进乘用车平均油耗下行,2020 年我国乘用车(含新能源)平均油耗已从 2016 年的 6.43L/100km 下降至 5.55L/100km。
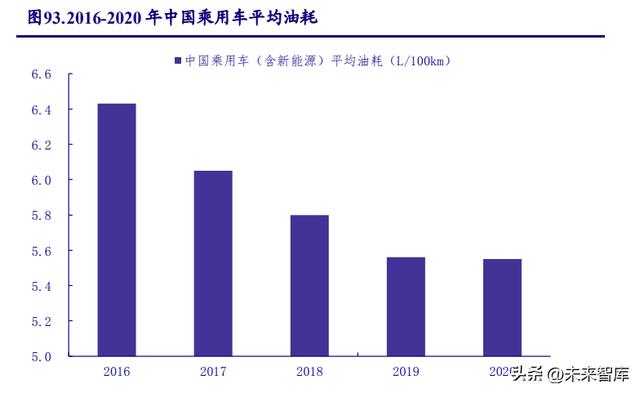
根据中国汽车工程学会发布的《节能与新能源汽车技术路线图 2.0》,我国乘用车(含新 能源)新车油耗在 2025 年、2030 年、2035 年大的目标值分别为 4.6L/100km、3.2L/100km 和 2.0L/100km。有关研究表明,汽车整车重量每减少 10%,燃油效率可提高 6-8%;重量每减少 100kg,百公里油耗可降低 0.3-0.6L,二氧化碳排放可减少约 5g/km。汽车轻量化成为实现汽车 降低油耗,节能减排的重要途径之一。
全球新能源汽车渗透率快速提高,亟需轻量化缓解里程焦虑。新能源汽车的三电(电池、 电机、电控)系统大大增加了整备质量,相比燃油车,新能源汽车往往重 10%。研究表明,纯 电动汽车整车重量每降低 10kg,续航里程可增加 2.5km。作为新能源汽车的难题,提高续航里 程一直是消费者的需求和新能源车企的目标。《节能与新能源汽车技术路线图 2.0》对纯电动 乘用车轻量化设定的目标是,至 2025 年、2030 年和 2035 年整车轻量化系数分别降低 15%、 25%和 35%。 随着下游汽车行业的飞速发展,以及汽车轻量化进程的加快,压铸机市场规模持续扩大。 压铸机主要应用于汽车(汽车动力总成配件、汽车结构件、方向盘)、摩托车、3C(计算机、通讯、 消费电子)、家电、电动工具、航空航天等高科技产业。发达国家与汽车相关的模具需求占模 具总需求量的 40%以上,目前我国与汽车相关的模具需求约占模具总需求量的 30%,其中大 部分压铸需求直接来源于汽车压铸件,2020 年我国 65%的压铸机应用于汽车和摩托车领域。 随着汽车产销规模的逐年攀升,压铸机市场飞速发展,2020 年我国压铸机市场规模达到约 170 亿元,同比增长 21.43%。
(2)特斯拉引领,车厂纷纷布局一体化压铸
传统压铸 vs 一体压铸。传统车身制造覆盖四大工艺:1)冲压:借助压力机与模具将板材 连续冲压为小块钣金零件;2)焊装:将冲压好的车身零件用夹具定位,采用装配后焊接的方 法将其接合形成车身总成(即白车身);3)喷涂:喷涂油漆于白车身上,起到防腐蚀与装饰 的作用;4)总装:将车身、动力系统、电控系统、内外饰等各零件装配生产为整车。一体化 压铸则通过大吨位压铸机,将多个单独、分散的铝合金零部件高度集成,再一次成型压铸为 1- 2 个大型铝铸件,从而替代多个零部件先冲压再焊接在一起的方式。所需生产零部件数量骤减, 同时大幅减少焊接、涂胶环节,极大简化了车身整体生产流程。
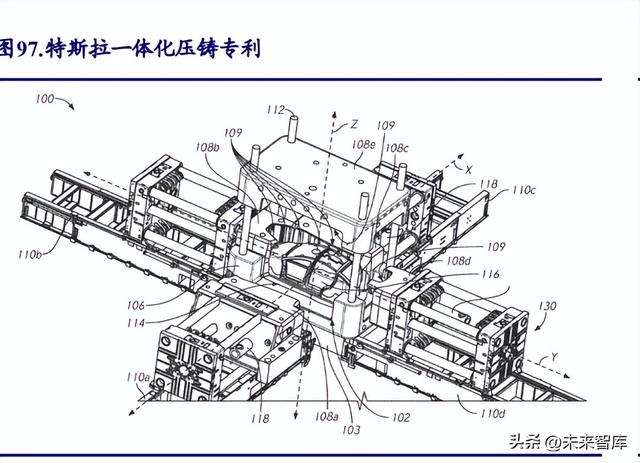
国内外车企紧跟特斯拉脚步,布局一体化压铸技术。随着一体压铸技术在 Model Y 后地 板应用的逐渐成熟,特斯拉将一体压铸逐步推广至 Model Y 前机舱、Cybertruck 后地板等其他 结构件上,其中 Cybertruck 后地板将使用 8000T 压铸机进行生产。沃尔沃、大众、蔚来等国内 外车企也纷纷布局一体化压铸产能和铝合金材料,从而实现车身轻量化。
(3)下游需求升级,压铸设备企业布局超大型压铸机
新能源车企布局一体化压铸带动超大型压铸机需求增长,压铸设备企业率先受益。作为一 体化压铸生产的核心设备,目前大型高端压铸设备供应商主要为海外企业,包括布勒、意德拉 和意特佩雷斯,其中意德拉于 2008 年被力劲科技收购。为满足新能源车企的一体化压铸需求, 国内主要压铸企业加快布局一体化压铸产能。
(五)船舶行业周期向上,订单增加推升龙头业绩
1、船舶行业:订单新增上行,行业步入新周期
近两年,世界各国经济不均衡复苏,全球航运市场和造船市场经历了超预期的回升阶段, 我国的三大造船指标在 2021 年也实现了全面增长,在国际市场份额中保持领先,绿色船舶转 型发展加速,产业链供应链韧性得到提升,船舶行业正处于周期向上的发展期。但同时收到劳 动力资源不足、综合成本波动上升等因素影响,船舶行业可谓机遇与挑战共存。 船舶制造业的景气度受供需关系影响,是较为典型的强周期行业。拉长时间周期来看,船 舶制造业近半个世纪以来,经历了多轮从复苏到繁荣最后衰退、萧条的大周期。2010-2020 年 是上一轮周期的萧条期,行业产能过剩,船舶需求下滑,并且受到金融危机影响,全球造船完 工量及手持订单量持续下滑。
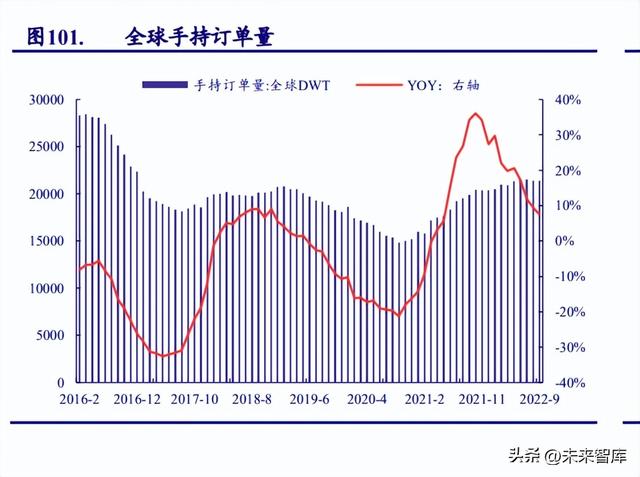
2、散货船订单大幅增长,供需紧平衡促价格提升
从 2020 年 Q3 开始,集装箱船运价指数与各类船型的新签订单量大幅上升。2021 年全球 各类新船新签订单量达 3768 万载重吨,同比约增长 126%,其中全球散货船新签订单量达 2028 万载重吨,同比增长约 114%;全球油船新签订单量达 1326 万载重吨,同比下降 30%;集装箱 船新签订单达 368 万 TEU,同比增长 343%。
从船运价格来看,集装箱船运价指数(CCFI)在 2021 年上涨了 300%以上,涨幅为历史 最高,箱船结束了持续十余年的低谷,新船订单量激增,究其原因主要是海外疫情防控的政策 放松刺激国外对中国进口需求的增长,同时全球的物流网络拥堵,需求的短期大幅增长提高了 船运成本,导致运价指数的上涨,同时也带动新造船价格指数的上升。
3、中国市场份额居世界首位,船舶行业龙头持续受益
在上轮船舶行业的景气周期中,中国造船业三大指标份额仅占世界约 15%,而从 2022 年 10 月的数据来看,中国造船业的造船完工量、手持订单量和新船订单约占总额的比例达到 50% 左右,中国造船订单数居世界首位。2021 年 9 月,中国造船业景气指数达到峰值,三大指标 在 2021 年均有所提升。2022 年,新船订单量前 10 家企业占全国总量约 70%,在船舶行业新 周期,国内龙头企业订单有望持续增长。
中国船舶:中国船舶集团有限公司是我国船舶工业发展的国家队、主力军,坚持走自力更 生、自主创新发展道路,培育了超大型智能原油轮、液化天然气运输船、超大型集装箱船等集 研发、制造、配套为一体的世界级海洋装备先进产业集群,公司深化供给侧结构性改革,以大 型邮轮、船用低速机、智能船舶、智慧海洋等重大创新工程为牵引,发展形成了完整的海军武 器装备、科技创新和产业发展体系,打造形成强力国际竞争优势。 根据公司三季报显示,公司 2022 年三季度营收小幅增长,归母净利润大幅提升。公司 2022 年三季度营业收入为385.92亿元,同比增长0.96%,归母净利润为14.63亿元,同比增长256.35%, 公司净利率与毛利率分别达到 3.88%及 10.03%,净利率达到近几年来最高水平。
中国重工:中国重工是目前 A 股资本市场上首家获得国家国防科技工业管理部门批准的 上市公司。目前,中国重工在舰载武器装备关键技术、舰船用配套产品技术方面拥有大量高质 量科技成果和自主核心技术,产品包括舰艇用柴油机及部件、舰载武器发射装置、舰艇用导航 设备、舰艇用通讯设备、军用加固计算机、舰艇用传动装置等多种军用舰船装备。 公司 2022 年三季度营收稳步增长,但归母净利润大幅下降。公司 2022 年三季度营业收入 为 259.62 亿元,同比增长 4.49%,归母净利润为-12.52 亿元,同比下滑 2363%,预计 2022 年 底会有所改善。公司净利率与毛利率分别达到-5.07%及 5.49%,对比往年均有所下降。
中船防务:中船海洋与防务装备股份有限公司是中国船舶集团有限公司属下的大型造船 骨干企业之一,其前身是广州广船国际股份有限公司。 公司于 1993 年在上海和香港上市,是 中国第一家 A+H 股上市造船企业。014 年、2015 年,中船防务先后收购了中船龙穴造船有限公 司、中船黄埔文冲船舶有限公司,完成了对中船集团在华南地区优质造船资产的整合,实现境 内核心军工资产上市,成为集海洋防务装备、海洋运输装备、海洋开发装备和海洋科考装备四 大海洋装备于一体的大型综合性海洋与防务装备企业集团。 公司 2022 年三季度营收稳步增长,归母净利润大幅增长。公司 2022 年三季度营业收入为 72.99 亿元,同比增长 6.66%,归母净利润为 0.24 亿元,同比增长 289%,公司净利率与毛利率分别达到 0.48%及 6.67%,维持正常水平。
(本文仅供参考,不代表我们的任何投资建议。如需使用相关信息,请参阅报告原文。)
精选报告来源:【未来智库】。「链接」
相关参考
泰州线切割(机械行业策略报告:紧抓通用设备自主可控,把握专用设备景气加速)
(报告出品方:中国银河证券)一、2023年投资关键词:疫后复苏、自主可控、新技术落地(一)2022年回顾我们在2022年度机械行业策略报告《硬科技+新能源,引领装备升级新征程》中提出2022年投资关键词为“硬科技”“新能源...
泰州线切割(机械行业策略报告:紧抓通用设备自主可控,把握专用设备景气加速)
(报告出品方:中国银河证券)一、2023年投资关键词:疫后复苏、自主可控、新技术落地(一)2022年回顾我们在2022年度机械行业策略报告《硬科技+新能源,引领装备升级新征程》中提出2022年投资关键词为“硬科技”“新能源...
法那科陶瓷轮(机械行业策略报告:紧抓通用设备自主可控,把握专用设备景气加速)
(报告出品方:中国银河证券)一、2023年投资关键词:疫后复苏、自主可控、新技术落地(一)2022年回顾我们在2022年度机械行业策略报告《硬科技+新能源,引领装备升级新征程》中提出2022年投资关键词为“硬科技”“新能源...
法那科陶瓷轮(机械行业策略报告:紧抓通用设备自主可控,把握专用设备景气加速)
(报告出品方:中国银河证券)一、2023年投资关键词:疫后复苏、自主可控、新技术落地(一)2022年回顾我们在2022年度机械行业策略报告《硬科技+新能源,引领装备升级新征程》中提出2022年投资关键词为“硬科技”“新能源...
机械及行业设备(机械设备行业专题报告:掘金三方向,产业趋势、自主可控、新基建)
获取报告请登录未来智库www.vzkoo.com。1、3C设备:苹果再迎“大年”,5G换机潮来临1.3C设备:苹果再迎“大年”,5G换机潮来临1.1.3C整体行业景气度一般,手机有回暖迹象目前受海外疫情影响,苹果产业链订单有所延迟、并有部分...
...中长期贷款)会领先资本开支。1)机床覆盖下游汽车、机械制造、3C电子、模具等广泛的制造业领域,其需求变动与下游资本开支密切相关。2011年企业新增中长期贷款增速触底,2012年开始
...中长期贷款)会领先资本开支。1)机床覆盖下游汽车、机械制造、3C电子、模具等广泛的制造业领域,其需求变动与下游资本开支密切相关。2011年企业新增中长期贷款增速触底,2012年开始
方形动力卷绕机(机械设备行业深度报告:聚焦高景气板块,把握自主可控机会)
(报告出品方/作者:首创证券,曲小溪)1光伏设备:需求共振+技术迭代,未来设备端高景气延续1.1光伏装机超预期,行业高景气延续光伏装机量高增长,行业景气度延续。国内方面,2022年1-9月国内光伏新增装机52.6GW,同比增10...
沃尔沃发电机耗材(机械设备行业深度报告:聚焦高景气板块,把握自主可控机会)
(报告出品方/作者:首创证券,曲小溪)1光伏设备:需求共振+技术迭代,未来设备端高景气延续1.1光伏装机超预期,行业高景气延续光伏装机量高增长,行业景气度延续。国内方面,2022年1-9月国内光伏新增装机52.6GW,同比增10...
...专业队伍。经过多年的努力,先后向市场推出了:快走丝线切割机床系列、中走丝线切割机床系列、慢走丝线切割机床系列、电火花成形机