注塑机生产的产品有毛边(塑料产品翘曲变形的成因与解决)
Posted
篇首语:出门莫恨无人随,书中车马多如簇。本文由小常识网(cha138.com)小编为大家整理,主要介绍了注塑机生产的产品有毛边(塑料产品翘曲变形的成因与解决)相关的知识,希望对你有一定的参考价值。
注塑机生产的产品有毛边(塑料产品翘曲变形的成因与解决)
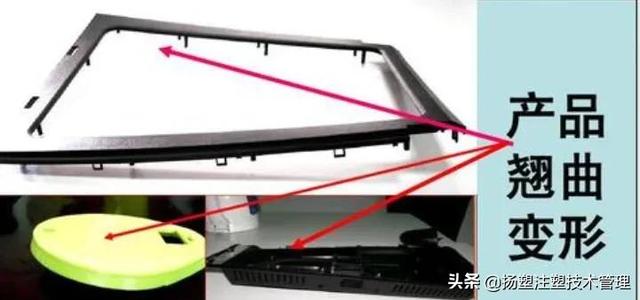
翘曲变形是薄壳塑料件注塑成型中的常见缺陷之一,因为涉及到对翘曲变形量的准确预测,而不同材料、不同形状的注塑件的翘曲变形规律差别很大。当翘曲变形量超过允许误差后,就成为成形缺陷,进而影响产品装配。对各类大量日益增加的薄壁件(壁厚小于2mm)翘曲变形做出准确预测是有效控制翘曲缺陷的前提。翘曲变形分析大都采用定性分析,从制品设计、模具设计及注塑工艺条件等方面采取措施,尽量避免发生大的翘曲变形。
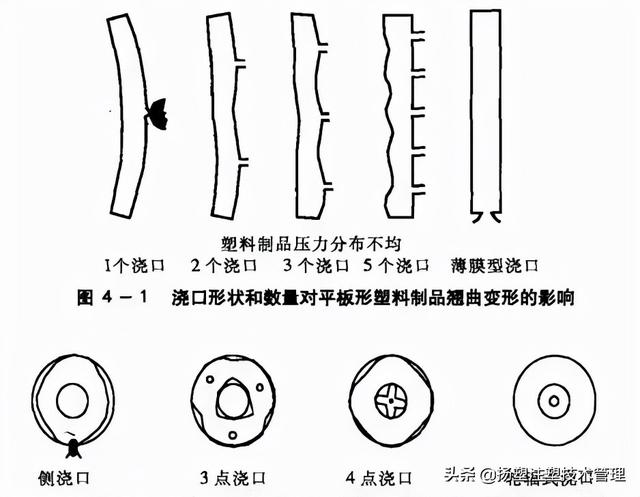
原因分析
模具方面
注塑模具浇口的位置、形式和浇口的数量将影响塑料在模具型腔内的填充状态,从而导致塑件产生变形。
流动距离越长,由冻结层与中心流动层之间流动和补缩引起的内应力越大;反之,流动距离越短,从浇口到制件流动末端的流动时间越短,充模时冻结层厚度减薄,内应力降低,翘曲变形也会因此大为减少。如果只使用一个中心浇口或一个侧浇口,因直径方向上的收缩率大于圆周方向上的收缩率,成型后的塑件会产生扭曲变形;若改用多个点浇口则可有效地防止翘曲变形。
当采用点浇进行成型时,同样由于塑料收缩的异向性,浇口的位置、数量都对塑件的变形程度有很大的影响由于采用的是30%玻璃纤维增强PA6,而得到的是重量为4.95kg的大型注塑件,因此沿四周壁流动方向上设有许多加强肋,这样,对各个浇口都能获得充分的平衡。
另外,多浇口的使用还能使塑料的流动比(L/t)缩短,从而使模腔内物料密度更趋均匀,收缩更均匀。同时,整个塑件能在较小的注塑压力下充满。而较小的注射压力可减少塑料的分子取向倾向,降低其内应力,因而可减少塑件的变形。
模具温度:模具温度对制品的内在性能和表观质量影响很大。模具温度的高低决定于塑料结晶性的有无、制品的尺寸与结构、性能要求,以及其它工艺条件(熔料温度、注射速度及注射压力、模塑周期等)
压力控制:注塑过程中压力包括塑化压力和注射压力两种,并直接影响塑料的塑化和制品质量
用实验方法研究塑料制品的翘曲变形主要体现在研究材料性质、产品的几何形状和大小、注塑成型工艺条件等对制品翘曲变形的影响。早通过设计大量的实验,获取浇口几何形状、保压参数(保压压力和保压时间)和模具的弹性对制品最终尺寸的影响。PET作为聚合物基,研究了不同材料和不同壁厚平板的翘曲特性。实验研究了33%玻璃增强纤维PA66注塑磁盘的增强比率、线性热膨胀系数的各向异性、制品厚度和翘曲之间的关系,首次提出了翘曲指数概念,采用翘曲指数研究PA66塑料制品的翘曲特性,并研究了翘曲指数、翘曲和纤维定向状态之间的关系和屈服与翘曲指数的关系。
实验方法研究翘曲变形,往往局限于某一特定的几何形状、特定的材料和工艺条件,并不能全面考虑诸多因素对翘曲变形的影响,而且也不能在产品设计阶段预测可能发生的翘曲变形的大小。在实际使用中,经验公式的局限性也显而易见,不仅受实验条件的影响,还与实验数据的处理方法、经验公式的应用条件等许多因素有关,并且一种经验公式只适用于与实验状况相当接近的生产过程。
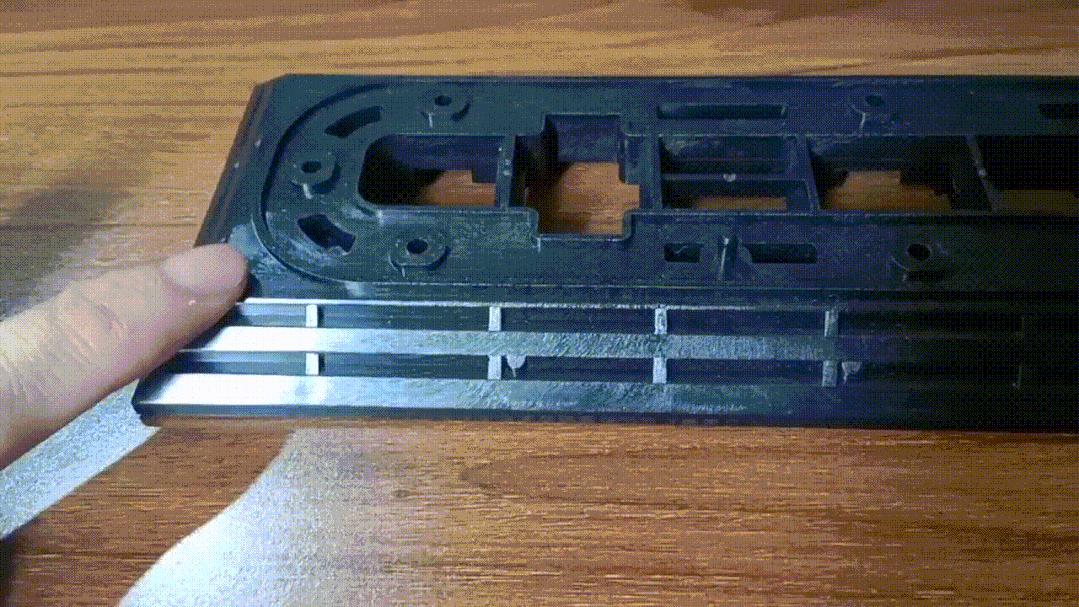
收缩/翘曲
由于翘曲变形与不均匀收缩有关,从研究不同塑料在不同工艺条件下的收缩行为入手,来分析收缩与制品翘曲的关系。在注塑流动、保压、冷却模拟的基础上,通过实验和线性回归方法,提出了预测注塑制品收缩的模型,在收缩预测的基础上,通过结构分析模拟程序计算出制品的变形。
用高收缩率的材料很难获得尺寸精度高的制品,力求高精度,应尽量应用非晶态树脂和各方向收缩一致的树脂。很多材料在改变流动速度、保压压力、保压时间、模具温度、充模时间、制品厚度等参数的条件下,测出制品的收缩。根据测试结果,将制品的收缩分为三个部分:体积收缩、分子取向引起的不均匀收缩、不平衡冷却引起的不均匀收缩。体积收缩、结晶含量、模具限制、塑料取向等的收缩预测方法,利用流动和冷却分析结果来预测收缩应变。
冷却系统的设计
在注射过程中,塑件冷却速度的不均匀也将形成塑件收缩的不均匀,这种收缩差别导致弯曲力矩的产生而使塑件发生翘曲。
如果在注射成型平板形塑件时所用的模具型腔、型芯的温度相差过大,由于贴近冷模腔面的熔体很快冷却下来,而贴近热模腔面的料层则会继续收缩,收缩的不均匀将使塑件翘曲。因此,注塑模的冷却应当注意型腔、型芯的温度趋于平衡,两者的温差不能太大。
除了考虑塑件内外表面的温度趋于平衡外,还应考虑塑件各侧的温度一致,即模具冷却时要尽量保持型腔、型芯各处温度均匀一致,使塑件各处的冷却速度均衡,从而使各处的收缩更趋均匀,有效地防止变形的产生。因此,模具上冷却水孔的布置至关重要。在管壁至型腔表面距离确定后,应尽可能使冷却水孔之间的距离小,才能保证型腔壁的温度均匀一致。
同时,由于冷却介质的温度随冷却水道长度的增加而上升,使模具的型腔、型芯沿水道产生温差。因此,要求每个冷却回路的水道长度小于2m。在大型模具中应设置数条冷却回路,一条回路的进口位于另一条回路的出口附近。对于长条形塑件,应采用冷却回路,减少冷却回路的长度,即减少模具的温差,从而保证塑件均匀冷却.
顶出系统的设计也直接影响塑件的变形。如果顶出系统布置不平衡,将造成顶出力的不平衡而使塑件变形。因此,在设计顶出系统时应力求与脱模阻力相平衡。另外,顶出杆的截面积不能太小,以防塑件单位面积受力过大(尤其在脱模温度太高时)而使塑件产生变形。顶杆的布置应尽量靠近脱模阻力大的部位。在不影响塑件质量(包括使用要求、尺寸精度与外观等)的前提下,应尽可能多设顶杆以减少塑件的总体变形。
用软质塑料来生产大型深腔薄壁的塑件时,由于脱模阻力较大,而材料又较软,如果完全采用单一的机械式顶出方式,将使塑件产生变形,甚至顶穿或产生折叠而造成塑件报废,如改用多元件联合或气(液)压与机械式顶出相结合的方式效果会更好。
残余热应力对制品翘曲变形的影响:
在注射成型过程中,残余热应力是引起翘曲变形的一个重要因素,而且对注塑制品的质量有较大的影响。由于残余热应力对制品翘曲变形的影响非常复杂,模具设计者可以借助于注塑CAE软件进行分析和预测。
塑料熔体在成型过程中,由于取向、收缩的不均匀,导致内应力的不均匀,所以制品出模后,在不均匀内应力的作用下,发生翘曲变形。因此,许多学者从力学角度分析、计算制品的内应力和翘曲。在国外一些文献中,翘曲被看成是不均匀收缩产生的残余应力造成的。
在注塑成型冷却阶段,当温度高于玻璃化转变温度时,塑料是粘弹性流体,并伴有应力松弛现象:当温度低于玻璃化转变温度时,塑料变成固态。塑料在冷却过程中的这种液一固相转变和应力松弛,对准确预测制品残余应力和残余变形很有影响。
冷却阶段塑料由液态变为固态的相转换和应力松弛行为。对未固化的区域,塑料呈现粘性行为,用粘性流体模型描述,对己固化的区域,塑料呈粘弹行为,用标准线性固体模型来描述,采用粘-弹相转换模型和二维有限单元法来预测热残余应力和相应的翘曲变形。
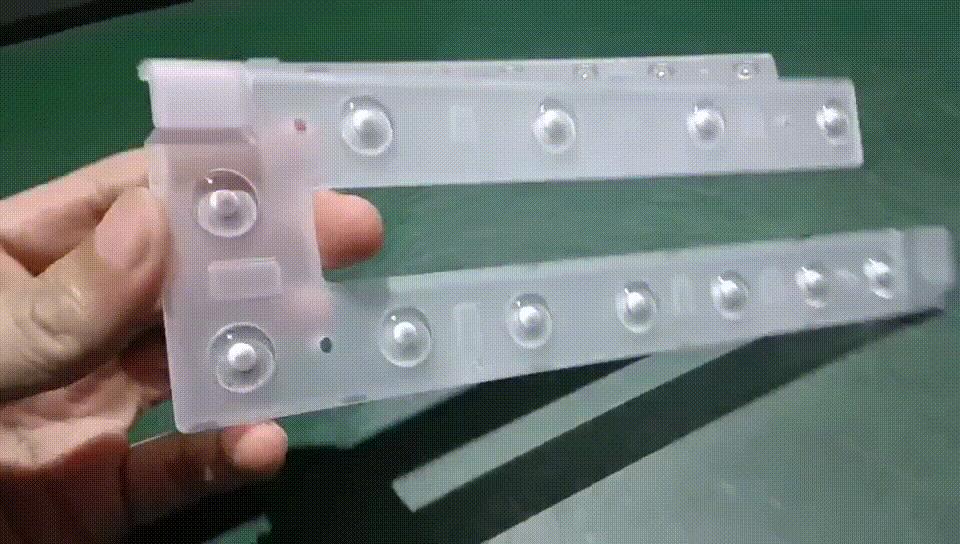
塑化阶段对制品翘曲变形的影响:
塑化阶段即玻璃态的料粒转化为粘流态,提供充模所需的熔体。在这个过程中,聚合物的温度在轴向、径向(相对螺杆而言)的温差会使塑料产生应力;另外,注射机的注射压力、速率等参数会极大地影响充填时分子的取向程度,进而引起翘曲变形。
注射的初期使用低速,模腔充填时使用高速,充填接近终了时再使用低速注射的方法。通过注射速度的控制和调整,可以防止和改善制品外观如毛边、喷射痕、银条或焦痕等各种不良现象。
多级注射控制程序可以根据流道的结构、浇口的形式及注塑件结构的不同,来合理设定多段注射压力、注射速度、保压压力和熔胶方式,有利于提高塑化效果、提高产品质量、降低不良率及延长模具/机器寿命。
通过多级程序控制注塑成型机的油压、螺杆位置、螺杆转速,能谋求改善成型件的外观不良,改善缩水、翘曲和毛边的对应措施,减少各模每次注射成型件的尺寸不均。
通过多级程序控制注塑成型机的油压、螺杆位置、螺杆转速,能谋求改善成型件的外观不良,改善缩水、翘曲和毛边的对应措施,减少各模每次注射成型件的尺寸不均一。
充模及冷却阶段对制品翘曲变形的影响:
熔融态的塑料在注射压力的作用下,充入模具型腔并在型腔内冷却、凝固的过程是注射成型的关键环节。在这个过程中,温度、压力、速度三者相互耦合作用,对塑件的质量和生产效率均有极大的影响。较高的压力和流速会产生高剪切速率,从而引起平行于流动方向和垂直于流动方向的分子取向的差异,同时产生“冻结效应”。“冻结效应”将产生冻结应力,形成塑件的内应力。温度对翘曲变形的影响体现在以下几个方面。
- A. 塑件上、下表面温差会引起热应力和热变形;
- B. 塑件不同区域之间的温度差将引起不同区域间的不均匀收缩;
- C. 不同的温度状态会影响塑料件的收缩率。
脱模阶段对制品翘曲变形的影响:
塑件在脱离型腔并冷却至室温的过程中多为玻璃态聚合物。脱模力不平衡、推出机构运动不平稳或脱模顶出面积不当很容易使制品变形。同时,在充模和冷却阶段冻结在塑件内的应力由于失去外界的约束,将会以变形的形式释放出来,从而导致翘曲变形。
真三维方法来计算残余应力和最终形状(收缩和翘曲)。他们考虑了保压阶段的影响,将制品分成三层,由三维网格来分析残余应力和变形。,提出了在保压阶段以后所引起的残余应力和变形的数值模拟模型。计算残余应力时,采用了热粘弹模型(包含体积松弛)。其采用的有限单元法是基于由平面单元集合而成的壳层理论,该理论正适用于形状复杂的薄壁注塑制品。
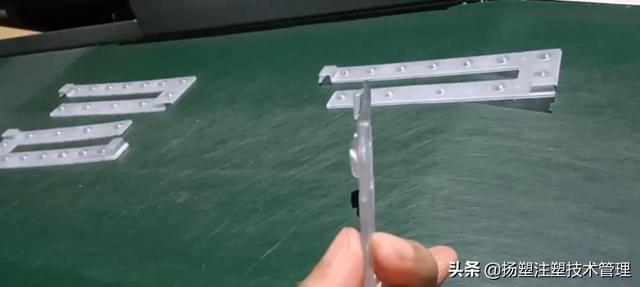
注塑制品收缩对翘曲变形的影响解决办法:
注塑制品翘曲变形的直接原因在于塑件的不均匀收缩。如果在模具设计阶段不考虑填充过程中收缩的影响,则制品的几何形状会与设计要求相差很大,严重的变形会致使制品报废。除填充阶段会引起变形外,模具上下壁面的温度差也将引起塑件上下表面收缩的差异,从而产生翘曲变形。
对翘曲分析而言,收缩本身并不重要,重要的是收缩上的差异。在注塑成型过程中,熔融塑料在注射充模阶段由于聚合物分子沿流动方向的排列使塑料在流动方向上的收缩率比垂直方向的收缩率大,而使注塑件产生翘曲变形。一般均匀收缩只引起塑料件体积上的变化,只有不均匀收缩才会引起翘曲变形。结晶型塑料在流动方向与垂直方向上的收缩率之差较非结晶型塑料大,而且其收缩率也较非结晶型塑料大,结晶型塑料大的收缩率与其收缩的异向性叠加后导致结晶型塑料件翘曲变形的倾向较非结晶型塑料大得多。
对制品几何形状分析的基础上选择的多级注塑工艺:由于制品的型腔较深而壁又较薄,使模具型腔形成长而窄的流道,熔体流经这个部位时必须很快地通过,否则易冷却凝固,会导致充不满模腔的危险,在此应设定高速注射。但是高速注射会给熔体带来很大的动能,熔体流到底时会产生很大的惯性冲击,导致能量损失和溢边现象,这时须使熔体减缓流速,降低充模压力而要维持通常所说的保压压力(二次压力,后续压力)使熔体在浇口凝固之前向模腔内补充熔体的收缩,这就对注塑过程提出多级注射速度与压力的要求。
残余热应力使制品翘曲变形的解决方法:
流体表面的速度应该是常数。应采用快速射胶防止射胶过程中熔体冻结。射胶速度设置应考虑到在临界区域(如流道)快速充填的同时在入水口位减慢速度。射胶速度应该保证模腔填满后立即停止以防止出现过填充、飞边及残余应力。
相关参考
经过多年的经验积累总结出以下不良缺陷:注塑不满、凹陷、熔合缝、料流纹、光泽不好、气孔、黑点、溢边、翘曲变形、脱模不好、云彩、流道断裂、唱片沟纹、光环、麻点气、烧焦、冷料、喷射纹、银纹、飞边、须状斑纹、...
经过多年的经验积累总结出以下不良缺陷:注塑不满、凹陷、熔合缝、料流纹、光泽不好、气孔、黑点、溢边、翘曲变形、脱模不好、云彩、流道断裂、唱片沟纹、光环、麻点气、烧焦、冷料、喷射纹、银纹、飞边、须状斑纹、...
主要对生产注塑产品的各种塑胶制品的缺陷检查与试验方法,适用于一般注塑制品的检查,本标准仅供常规检测用,特殊要求以partspec为准。常见质量缺陷有:缺料、缩印、熔接痕、料流纹(流痕)、光泽不好(阴阳面、色差)...
主要对生产注塑产品的各种塑胶制品的缺陷检查与试验方法,适用于一般注塑制品的检查,本标准仅供常规检测用,特殊要求以partspec为准。常见质量缺陷有:缺料、缩印、熔接痕、料流纹(流痕)、光泽不好(阴阳面、色差)...
主要对生产注塑产品的各种塑胶制品的缺陷检查与试验方法,适用于一般注塑制品的检查,本标准仅供常规检测用,特殊要求以partspec为准。常见质量缺陷有:缺料、缩印、熔接痕、料流纹(流痕)、光泽不好(阴阳面、色差)...
主要对生产注塑产品的各种塑胶制品的缺陷检查与试验方法,适用于一般注塑制品的检查,本标准仅供常规检测用,特殊要求以partspec为准。常见质量缺陷有:缺料、缩印、熔接痕、料流纹(流痕)、光泽不好(阴阳面、色差)...
...腔、薄壁、壁厚不均),工艺参数不合理(保压、顺序阀),注塑机(吨位偏小,注塑压力不够)2.变形:弯曲、扭曲、翘曲、不平原因:1、保压压力过大,内应力大,出模后24h内变形大。2、冷却不均匀,导致翘曲。3、浇口位置不合
...腔、薄壁、壁厚不均),工艺参数不合理(保压、顺序阀),注塑机(吨位偏小,注塑压力不够)2.变形:弯曲、扭曲、翘曲、不平原因:1、保压压力过大,内应力大,出模后24h内变形大。2、冷却不均匀,导致翘曲。3、浇口位置不合
...腔、薄壁、壁厚不均),工艺参数不合理(保压、顺序阀),注塑机(吨位偏小,注塑压力不够)2.变形:弯曲、扭曲、翘曲、不平原因:1、保压压力过大,内应力大,出模后24h内变形大。2、冷却不均匀,导致翘曲。3、浇口位置不合
关于作者:钟元,2011年出版书籍《面向制造和装配的产品设计指南》(DFMA)。2019年11月即将出版《面向成本的产品设计:降本设计之道》(DFC)。如果觉得文章不错,请关注“降本设计”头条号,获取更多原创产品设计知识,...