注塑产品pp料熔接线(「技术」注塑件熔接痕成因及改进措施)
Posted
篇首语:游手好闲地学习,并不比学习游手好闲好。本文由小常识网(cha138.com)小编为大家整理,主要介绍了注塑产品pp料熔接线(「技术」注塑件熔接痕成因及改进措施)相关的知识,希望对你有一定的参考价值。
注塑产品pp料熔接线(「技术」注塑件熔接痕成因及改进措施)
熔接痕是影响塑件质量的一个重要因素。研究发现:在相同工艺条件下,熔接痕区域的强度只有原始材料的10-92%,严重影响注塑制品的正常使用。如在汽车行业,不合格的塑件直接导致汽车质量下降,甚至危及人的生命安全。因此,研究熔接痕的形成过程、影响因素及寻找消除熔接痕的办法具有重要的现实意义。
熔接痕是影响塑件质量的一个重要因素。研究发现:在相同工艺条件下,熔接痕区域的强度只有原始材料的10-92%,严重影响注塑制品的正常使用。如在汽车行业,不合格的塑件直接导致汽车质量下降,甚至危及人的生命安全。因此,研究熔接痕的形成过程、影响因素及寻找消除熔接痕的办法具有重要的现实意义。
熔接痕的形成机理
塑料制品的“熔接痕”是指两股熔融物料相接触时形成的形态结构和力学性能完全不同于其他部分的三维区域。注塑件中最常见的熔接痕有两种基本类型:一种是因塑件结构特点或尺寸较大,为减小熔体流程和充模时间,采用两个或两个与上浇口时,从不同浇口进入型腔的熔体前锋相遇处形成的熔接痕,称为冷熔接痕;另一种是当型腔内装有型芯和嵌件时,熔体绕经这种障碍物时分为两股,绕过障碍物后两股熔体又重新汇合形成的熔接痕,称为热熔接痕。
另外,当制件壁厚过分悬殊时,流体流经型腔时所受的阻力不同,在壁厚处阻力小,流速快;而壁薄处阻力大,流速慢。由于这种流动速度的差别,使来自不同壁厚的熔体,以不同的流速相汇合,最终在汇合处形成熔接痕。
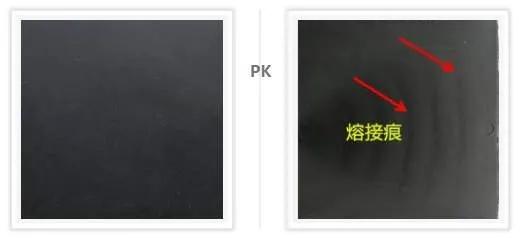
熔接痕的影响因素及改进消除的措施
由于熔接痕对塑件的质量有重要的影响,人们对其形成机理和性能评价做了大量研究,并提出了多种解决方案。
1. 注塑工艺参数对熔接痕的影响
a. 温度的影响
升高温度可以加速聚合物的松弛过程,减少分子链缠结的时间,这样更有利于物料前端分子的充分熔合、扩散和缠结,从而提高熔接痕区域的强度。实验证明:提高熔体温度有利于减少塑件表面V型口的深度,当熔体温度从220℃提高到250℃时,V型槽的深度从7μm下降至3μm。
温度对含有33%玻璃纤维增强的PA66注塑制品熔接痕拉伸能力的影响,经研究发现:有无熔接痕的试样拉伸强度都会随着熔体温度的升高而升高;温度变化对熔接痕的拉伸强度的影响并非是线性的,温度相对较低(如70℃)时,随着温度的升高,熔接痕的拉伸强度变化明显;但当温度升到一定程度时,这种变化相对平缓。
用PA66(35%玻纤增强),用ABS做实验也得到相似的结论。利用模拟发现模具温度和熔体温度对不同材料形成熔接痕强度的影响并不一样。采用实验和模拟相结合的方法发现,在注塑成型工艺参数中,熔体温度对ABS塑件熔接痕强度影响最大。
b. 注射压力和保压压力的影响
注射压力是塑料熔体充模和成型的重要因素,其作用是克服塑料熔体在料筒、喷嘴及浇注系统和型腔中流动时的阻力,给予塑料熔体足够的充模速度,能对熔体进行压实,以确保注塑制品的质量。提高注射压力有助于克服流道阻力,把压力传递到熔体前锋,使熔体在熔接痕处以高压熔合,增加熔接痕处的密度,从而使熔接痕强度得到提高。提高保压压力不仅可以给熔料分子链的运动提供更多的动能,而且能够促进两股熔体的相互结合,从而提高熔接痕区域的密度和熔接痕的强度。
c. 注射速度和注射时间的影响
提高注射速度和缩短注射时间会减少熔体前锋汇合前的流动时间,降低热损耗,并加强剪切生热,使熔体黏度下降,流动性增加,从而提高熔接痕强度。熔接痕的强度对注射时间非常敏感,会随着注射时间的缩短而增强。但是注射速度过大,容易产生湍流(熔体破裂),严重影响塑件的性能。通常注射成型时应采用先低压慢速注射,然后再根据塑件的形状来调节注射速度的方式。在实际生产中,为了缩短生产周期,避免出现湍流的情况,更多的是采用中等较高的注射速度。
注射速度影响熔体在型腔内的流动行为,也影响型腔内的压力、温度及制品的性能。注射速度大,熔体通过模具浇注系统和型腔的流速也大,物料受到剪切作用就越强烈,摩擦生热就越大,温度上升,粘度下降,物料的流程也延长,型腔压力也提高,制品熔接痕的强度也提高。
2. 模具设计对熔接痕的影响
在选定材料、设置完工艺参数之后,模具的设计就成了最关键的一步。合理的模具结构可以减少熔接痕的产生,提高熔接痕区域的强度或降低熔接痕对塑件整体性能的影响。
a. 浇注系统的设计
根据熔接痕的形成原理可知,对多个浇口充模势必形成多个分支料流,如果浇口数量为N,熔接痕的数量至少为N-1。可见浇口的数量越多,产生的熔接痕也越多,如果来自各浇口的料流前锋熔体不能很好地熔合,则会使熔接痕加重,严重影响塑件质量。
b. 排气系统和冷料井的设计
由于排气不畅而产生的残余气体在注射过程中被压缩在模腔内,不仅会烧伤制品还会导致熔接痕出现。气体在熔体充模时容易被排挤到熔体的汇合部位,在两股料流之间产生夹层,最终阻碍料流融合,不仅促使熔接痕产生而且会降低熔接痕处的强度。PS塑件在充分排气时,熔接痕处的强度为36.5MPa,而无排气时只有17.5MPa。模具充分排气或采用真空引气均利于减轻消除熔接痕。
另外,在熔接痕出现的部位开设冷料穴可使熔体前锋在冷料穴部位汇合(俗称垃圾销)。提高熔体在塑件末端汇合时的温度,不仅可以减小熔接痕的产生,而且可以增强熔接痕处的强度。
c. 温度调控系统的设计
模温越低越不利于熔体的充分熔合。模具设计时,若冷却水道离熔体汇合处太近,则接缝处的熔体因温度降低粘度升高而无法熔合,将产生明显的熔接痕。冷却系统设计不当,还会造成模具温度分配相差过大,致使塑料熔体充模时,型腔不同部位因温差导致填充速度不同,从而引起熔接痕。所以,温控系统的合理设计,会使模具温度波动分布均匀,减少熔接痕的产生。
现在实现了急冷急热注塑模具温度控制调节系统,使模具型腔表面温度能够根据注塑过程中各阶段的需求快速转换。这种急冷急热模温调节系统,其共同优点是因成型面能被急速、均匀地冷却,并能急速加热到接近或等於原料的熔融温度,因此成型的产品质量好,不易产生熔接痕、流痕等成型缺陷。
另有一种利用电池圈的磁效应迅速加热模具成型表面,然后再用冷却水冷却模具来实现模具温度控制的方法,可以提高塑件质量,避免熔接痕的产生。
d. 型腔、型芯表面粗糙度的设计
型腔、型芯的表面粗糙度也会影响塑料熔体的充模流动速度。表面粗糙度值过大,则熔体流速减慢,模具壁冷凝层加厚,料流截面减小,流动阻力增大,熔体温差扩大,分支流的熔接强度下降。加工模具时,如果型腔表面粗糙度不一致,也会因熔体充模速度不同而导致熔接痕的生成。
e. 模具结构在其他方面的改进
一种能消除有孔注塑制品外观熔接痕的模具结构,具体方法是制品在型腔内刚刚注塑充填完成时,利用镶芯对型腔内较软的物料熔体进行切割,得到制品孔。该方法可以用于表面有各种类型孔的塑料制品,可以完全消除孔处的熔接痕,从而提高产品质量。
还有一种特殊注塑机构,实际生产中,在动、定模板未锁紧时(间隙2mm)进行注塑,在注塑量为所需注塑量的70%-80%时进行二次合模。由于模具未完全闭合时没有型芯的分流作用,也就不会形成熔接痕,所以能够彻底杜绝熔接痕的产生。
3. 顺序阀针浇口技术对熔接痕的影响
在产品高度自动化的大批量生产过程中,几乎所有的大型注塑件都采用热流道系统。对于此类塑件而言,多浇口进胶可以确保型腔充填完全并提高充填效率,但这也必然会产生分支料流,从而导致熔接痕的出现。而采用按照顺序打开浇口阀针的方法,可使熔料流依次融合向型腔两端,从而解决熔接痕的问题。
顺序阀针法浇口技术是近年来开发的一种注塑成型新技术,其理论模型由美国Moldflow公司率先提出,而美国GE公司首先在薄壁件生产中对其进行了商业应用。顺序阀针浇注技术是在原来热流道浇口处加上一个可以控制开、关的阀门装置,注塑浇口的开、关根据具体要求决定其工作方式。注塑模具浇注系统采用阀针式浇注控制後,可以通过浇口控制熔体的流动方向和流量,达到消除或减少熔接痕的目的。
浇口的开启或者关闭由液压缸或者汽缸驱动,在热流道中浇口与顶杆的连接是一根圆柱顶针。采用顺序阀针浇口技术成型制品时,一般分为四个步骤,在整个过程中一个浇口最多可以经过两次开、关:(1)注塑开始,打开模具中间浇口,向型腔内注入熔体,继而向两侧分流;(2)当熔体刚好流经两侧浇口时,关闭中间浇口,同时打开两侧浇口;(3) 当熔体充满整个型腔,开始补缩、保压时,打开所有浇口;(4) 保压结束前,关闭所有浇口,冷却制品,开模取件。
顺序浇口技术具有以下几个特点:消除大型塑件熔接痕;降低成型压力及相关残余应力;缩短成型周期;注射压力和保压压力带来的影响相互独立,喷嘴的闭启就可调整型腔的压力。在成型大型塑件时,传统的同步多点进胶,虽然能使熔体充满整个型腔,但是由于熔接痕的存在,很难使产品质量达到理想的要求。经生产实践证明,顺序阀针浇口技术切实有效地解决了注塑中的熔接痕问题。
4. 其他改善熔接痕强度的方法
要消除或者减少熔接痕的影响,提高熔接痕的强度,还可从选择基体树脂和助剂等入手。由于熔接痕处往往存在应力集中,所以可以用热处理的方法为注塑制品消除或减小在成型过程中形成的内应力,改善制品的力学性能。对于无定型塑料其处理方法是在高于玻璃化温度10-15℃、惰性气氛条件下,在加入适当液体或热空气的烘箱中放置一定时间;对于半结晶型塑料,要在低于熔点温度50-80℃的相似条件下放置一定时间,通常以40-50min/mm为宜,然后再将塑料冷却到室温。此外,研究者们还尝试了双推冲模法和振动辅助注塑成型法来减少熔接痕的产生。
a. 双推充模法
双推充模法是研究人员在研究材料自增强技术时,提出的一种成型方法。该系统由左注射系统、右注射系统和具有两个浇口的模具组成。开始时,两个浇口同时充模,当型腔被充满时,会在中间形成平面状的熔接痕区域。这时,控制系统驱动未固化的物料左右运动。由于靠近模壁处剪切应力大、凝固早,所以物料移动困难,于是熔接痕形成V型结构。
然后,物料在左右两个控制系统的作用下左右移动,如此反复几次,熔接痕所在地面便形成了犬牙交错状态,从而提高了两股料流的结合强度,改善了熔接痕的力学性能。与上述方法相似的是Bevis发明的双柱塞推料法,工作时,活塞的往复运动带动了充满模腔内的熔体的往复运动,达到了双推充模法的预期效果。
b. 振动辅助注塑成型
振动辅助注塑成型是借助外加力场(包括机械振动、声波振动和超声波振动等)对原料进行塑化和加工,从而使塑件的整体性能得到大幅度提高的一种新型高聚物成型方法。其作用机理是通过局部加振,使聚合物产生脉动。这种方法主要是利用电磁振动使物料在料筒内塑化更加完全,有较低的充模粘度,而且容易排除气体,有利于熔接痕强度的提高。
熔接痕的存在不仅会引起塑件表面的质量问题,还会影响塑件的强度。熔接对于大多数塑件而言是难以避免的,但是通过对塑件结构及模具结构进行改善,实行主动控制,可以消除或大大降低熔接痕的影响,使塑件外观及力学性能满足设计要求和使用要求。此外,原料自身的结晶度、松弛时间等性质也是影响熔接产生的重要原因,选择合适的树脂对于消除或减少熔接痕也有重要意义。
相关参考
熔接痕熔接线融合线(注塑最头疼的问题——熔接痕(Weld Lines)缺陷分析及排除方法)
...陷中,熔接痕是最为普遍的,除少数几何形状非常简单的注塑件外,发生在大多数注塑件上(形状通常为一条线或V形槽),尤其是需要使用多浇口模具和嵌件的大型复杂品。熔接痕不仅使得塑件的外观质量受到影响,而且使塑...
熔接痕熔接线融合线(注塑最头疼的问题——熔接痕(Weld Lines)缺陷分析及排除方法)
...陷中,熔接痕是最为普遍的,除少数几何形状非常简单的注塑件外,发生在大多数注塑件上(形状通常为一条线或V形槽),尤其是需要使用多浇口模具和嵌件的大型复杂品。熔接痕不仅使得塑件的外观质量受到影响,而且使塑...
在加工塑料制品中容易出现痕迹如何判断这接痕是熔接痕。熔接痕产生的主要原因是塑胶在模腔内的交汇处会产生熔接线,熔接线是不可避免的,可采用用增大流速,温度,压力等方法降低熔接线的明显度以达到需要的表面要求...
在加工塑料制品中容易出现痕迹如何判断这接痕是熔接痕。熔接痕产生的主要原因是塑胶在模腔内的交汇处会产生熔接线,熔接线是不可避免的,可采用用增大流速,温度,压力等方法降低熔接线的明显度以达到需要的表面要求...
注塑产品熔接痕的解决办法(金属嵌件注塑出现喷流纹要怎么处理)
金属嵌件注塑件在注塑时出现产品不良的情况有很多种,包括溢边、填充不足、气泡、龟裂、喷流纹和熔接痕等等。金属冲压厂家也都在实际生产过程中总结了经验,能够针对不同的问题,做出正确合适的措施。此文主要讲注塑...
注塑产品熔接痕的解决办法(金属嵌件注塑出现喷流纹要怎么处理)
金属嵌件注塑件在注塑时出现产品不良的情况有很多种,包括溢边、填充不足、气泡、龟裂、喷流纹和熔接痕等等。金属冲压厂家也都在实际生产过程中总结了经验,能够针对不同的问题,做出正确合适的措施。此文主要讲注塑...
注塑熔接痕形成原因(注塑最头疼的问题——熔接痕(Weld Lines)缺陷分析及排除方法)
...陷中,熔接痕是最为普遍的,除少数几何形状非常简单的注塑件外,发生在大多数注塑件上(形状通常为一条线或V形槽),尤其是需要使用多浇口模具和嵌件的大型复杂品。熔接痕不仅使得塑件的外观质量受到影响,而且使塑...
注塑熔接痕形成原因(注塑最头疼的问题——熔接痕(Weld Lines)缺陷分析及排除方法)
...陷中,熔接痕是最为普遍的,除少数几何形状非常简单的注塑件外,发生在大多数注塑件上(形状通常为一条线或V形槽),尤其是需要使用多浇口模具和嵌件的大型复杂品。熔接痕不仅使得塑件的外观质量受到影响,而且使塑...
...时,因不能完全熔合而产生的接缝。1.2熔接痕产生的机理注塑成型充填时,熔料在模腔中的流动,一般模腔壁面的温度都比塑料的熔点低,所以熔料从进入模腔的时刻起便开始冷却,在与模壁接触的一层熔体构成了不移动的外壳...
...时,因不能完全熔合而产生的接缝。1.2熔接痕产生的机理注塑成型充填时,熔料在模腔中的流动,一般模腔壁面的温度都比塑料的熔点低,所以熔料从进入模腔的时刻起便开始冷却,在与模壁接触的一层熔体构成了不移动的外壳...