水溶碳黑(全钒液流电池行业专题报告:沿流溯源,超“钒”脱俗)
Posted
篇首语:恢弘志士之气,不宜妄自菲薄。本文由小常识网(cha138.com)小编为大家整理,主要介绍了水溶碳黑(全钒液流电池行业专题报告:沿流溯源,超“钒”脱俗)相关的知识,希望对你有一定的参考价值。
水溶碳黑(全钒液流电池行业专题报告:沿流溯源,超“钒”脱俗)
(报告出品方/作者:国泰君安证券,庞钧文、石岩)
1. 技术详解:全钒液流电池的前世今生
随着“碳达峰,碳中和”目标提出,我国能源结构调整加快,新能源对 传统化石能源的逐步替代将是历史必然。我国幅员辽阔,拥有丰富的太 阳能、风能资源,但这些天然能源具有间歇性、波动性等特点,直接并 入电网会遇到很大困难,必须先进行平滑处理。同时,电力供给和需求 往往在时间和空间上存在错配,表现出峰谷波段,以及区域不均衡等现 象。解决上述问题的重要途径就是储能技术,尤其是电化学储能还具有 效率高、响应速度快、不受地理环境限制等优点,适用于供给侧风光发 电的平滑处理,也适用于需求侧的电能管理。相比其他电化学储能技术, 液流电池具有本征安全性和超长循环寿命,特别适用于大规模储能电站。
1.1. 基本概念与历史背景
液流电池是一种液相电化学储能装置,其活性物质完全溶解在电解液中, 通过活性元素的氧化价态变化来实现能量的存储与释放,属于一种氧化 还原电池。一般来说,液流电池需要两组氧化还原电对来构成正负极, 随着电池的充放电过程,正负极活性元素的氧化价态(电位)发生相应 变化。以早期最经典、研究最广泛的 Fe-Cr 双液流电池为例,其工作电 对为 Fe2+/3+/Cr2+/3+,正极活性物质为 FeCl2,负极活性物质为 CrCl3,电 解液基质为盐酸,正负极间用质子传导膜进行隔离(避免正负极活性物 质直接接触而发生自氧化还原反应)。电池在满充状态下放电时,正极 活性物质发生还原反应:Cr3+ + e → Cr2+,负极活性物质发生氧化反应: Fe2+ → Fe3+ + e,整体可合并为:Cr3+ + Fe2+ → Cr2+ + Fe3+,即三价 Cr 离子对二价 Fe 离子的氧化及自身的还原过程,电子从负极出发,经外 电路后到达正极。充电储能的过程则与之相反。
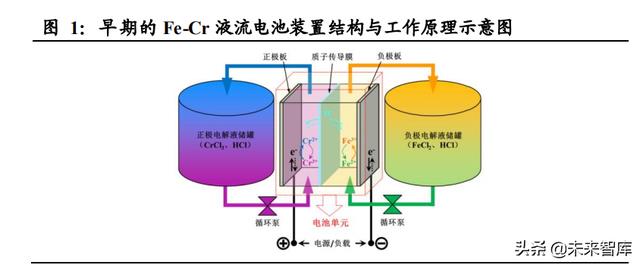
液流电池技术的起源非常悠久,跨越一个多世纪。最早可追溯到 1884 年,法国工程师 Charles Renard 发明的锌-氯液态电池,被用作军用飞艇 螺旋桨的动力源,续航时间 23 分钟,往返飞行里程 8 公里,电池整体 重 435kg,以三氧化铬和浓盐酸为氯源。该电池与今天的锌-溴液流电池 相似(但没有附加的流体驱动系统),在当时作为一次电池使用,没有 明显竞争力,随后销声匿迹。半个多世纪后的 1949 年,德国科学家 Walter Kango 发明了“液态储存电池”,并申请了正式专利,该电池以硫酸铬氯化亚铁为工作物质且存放在独立容器中,以硫酸为基质,石墨为惰性 电极,该专利被视为历史上液流电池的首个专利。此后,Kango 进一步 筛选出 6 组可用于构建液态电池的电对,以氯化钛、氯化铁、硫酸铬等过渡金属盐作为活性物质。这种液态储存电池的装置结构已初具现代液 流电池的雏形,但设计简陋,且循环性能较差,主要是由于正负极金属 离子交叉污染引起的自放电很严重,导致电压失稳和容量快速衰减,且 所用原物料的腐蚀性往往很强或具有高毒性,在成本上也不具备显著优 势,因此基本不具有商业化价值。
现代液流电池技术的进步与离子交换膜技术的发展密切相关。1950 年左 右,膜技术取得突破,人们获得了具有选择透性的离子交换膜,为现代 版液流电池技术的发展奠定了基础。1955 年,通用电器公司将聚苯乙烯 磺化修饰后得到了第一个质子交换膜(Proton Exchange Membrane, PEM),并将其作为燃料电池的电堆隔膜。PEM 只允许质子通过,阻断 其他离子透过,因此该技术很快被移植到液流电池中,作为正负极隔膜 以抑制内部自放电。到了 80 年代,通用公司与杜邦公司合作,依托后 者的全氟磺酸树脂专利技术,开发出了 Nafion 质子交换膜,并被加拿大 Ballard 公司应用到燃料电池中,使得其性能大大改善。由于全氟磺酸膜 的质子传导性能优异,还具有极强的抗氧化和酸腐蚀性,很快被引入液 流电池中,至今仍然是液流电池的主流隔膜材料。
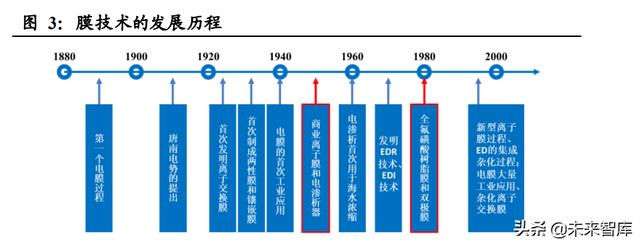
技术萌芽期(1971-1985 年): 1971 年,日本科学家 Ashimura 和 Miyake 首次提出了现代意义的液流 电池概念,通过将正负极活性物质溶解在电解液中,在惰性电极上发生 可逆氧化还原反应,以实现电能与化学能的互相转化。自 1973 年起, 美国航空航天局(NASA)开始对液流电池进行研究,用于月球基地的 太阳能储电系统,首要考虑电池的安全性、效率和运行寿命,而成本则 为次要因素。一年后,NASA 的科学家 L. H. Thaller 首次提出具有实际 意义的液流电池详细模型,以 FeCl2 和 CrCl3 作为正负极活性物质并存放 在两个外部储罐中,以盐酸作为基质,以阴离子交换膜为隔膜,以循环 泵作为液流驱动力,构成了第一款 Fe-Cr 双液流电池。此后,Fe-Cr 液流 电池在世界范围内掀起了一波研究热潮,其中美国和日本成功研发了 kW 量级、容量 10 kWh 以上的 Fe-Cr 液流电池样机,作为光伏阵列配套 设施。然而,由于 Cr3+/Cr2+半反应的可逆性较差,以及部分 Fe、Cr 离子 穿过隔膜引起交叉污染,导致工作电压不稳和容量衰减,大大降低电池 的实际使用寿命。这些问题涉及 Fe-Cr 体系的物理化学本性,当时离子 交换膜技术有限,难以妥善解决,因而 Fe-Cr 体系被逐渐淘汰。目前国 外 Fe-Cr 液流电池研发几乎停滞,仅有的美国 EnerVault 公司示范实验项 目也于 2015 年 6 月停运;国内主要是国家电投集团仍在持续研发,其 31.25kW 级 Fe-Cr 液流电堆“容和一号”已经开始量产。
研发示范期(1986-2000 年): 经过十余年的探索,绝大多数的液流电池候选材料体系由于各种难以克 服的缺陷而被先后淘汰,最终进入实用化示范阶段的主要是锌-溴液流电 池和全钒液流电池。其中,锌-溴液流电池是一种单侧沉积型液流电池, 优点是能量密度较高且原料成本较低,但液溴的挥发性、高毒性、强腐 蚀性和易渗透性以及锌枝晶析出使电池的实际容量、循环寿命和安全性 大打折扣。相比之下,全钒液流电池虽在能量密度上不及锌-溴液流电池, 但其他方面的表现更具有快速商业化的潜力。自 1984 年起,澳大利亚 新南威尔士大学(UNSW)的 Maria Skyllas-Kazacos 等人开始对全钒液 流电池进行系统性研究,具体涉及电极过程动力学机理、电极材料的制 作与改性、离子交换膜的优化、电解液的配方等。他们设计的全钒液流 电池活性材料为不同价态钒离子的硫酸盐,基质采用硫酸溶液。该团队 于 1986 年首次申请了全钒液流电池的专利,1988 年正式授权,并开始 建造 1kW 级的试验电堆,能量效率达 72~88%。随后,UNSW 将该技术 转售澳大利亚墨尔本的尖峰矿业公司(Pinnacle)。1993 年,UNSW 与泰 国石膏制品公司(Thai Gypsum Products)合作,尝试将钒电池应用于太 阳能屋。1994 年,全钒液流电池被应用于高尔夫车和潜艇上的备用电源。 UNSW 的研究成果是全钒液流电池史上的一个里程碑,这标志着该技术 开始从实验室走向产业化。
商业化初期(2001 年至今): 进入 21 世纪后,全钒液流电池开始真正走向商业化,前期主要以美国 和日本企业为代表。2001 年,Vanteck 公司收购了 Pinnacle 公司 59%的 股份,获得核心专利权,次年更名为钒电池储能系统技术开发公司(VRB Power System),该公司在 2004 年进一步收购 Reliable Power 公司,从而 控制整个北美地区的全钒液流电池市场,主要从事钒电池的技术开发与 授权转让,成为当时全球最大的全钒液流电池公司。同时,在 2000 年 至 2002 年间,日本 SEI 公司建成了多个全钒液流电池储能系统并将其 用于办公楼、工厂供电,以及风力发电场和高尔夫球场光伏阵列的配套 设施。2005 年,SEI 公司在北海道苫前町建立了 4MW/6MWh 全钒液流 电池储能系统,作为 36MW 风电站的调频调幅配套设施,这是当时全球 最大的全钒液流储能电池工程示范系统。此后,2008 年金融危机爆发, 对全钒液流电池产业也造成了一定程度的冲击。SEI 公司一度暂停了液 流电池项目的开发,直到 2011 才恢复商业化运作。
1.2. 工作原理与核心材料
全钒液流电池,商业简称“钒电池”,就是指液流电池的正负极电解液 活性物质全部都采用钒化合物。全钒液流电池的正负极氧化还原电对为 VO2+/VO2 + -V3+/V2+,活性材料为不同价态钒离子的硫酸盐,电解液基质 采用硫酸水溶液。电池在满充状态下放电时,正极的活性物质发生还原 反应:VO2 + + e → VO2+,标准电位+1.004 V;负极的活性物质发生氧化 反应:V2+ → V3+ + e,标准电位-0.255 V。全电池反应整体上可合并为: VO2 + + V2+ → VO2+ + V3+,开路电压 1.259 V,即五价的钒酰离子将二价 的水合钒离子的氧化为三价的水合钒离子,而自身被还原为四价的钒氧 离子的过程,电子从负极出发,经外电路后到达正极。充电储能的过程 则与之相反。在实际运行时,由于过电位等复杂因素,全钒液流电池的 开路电压一般为 1.5~1.6 V。
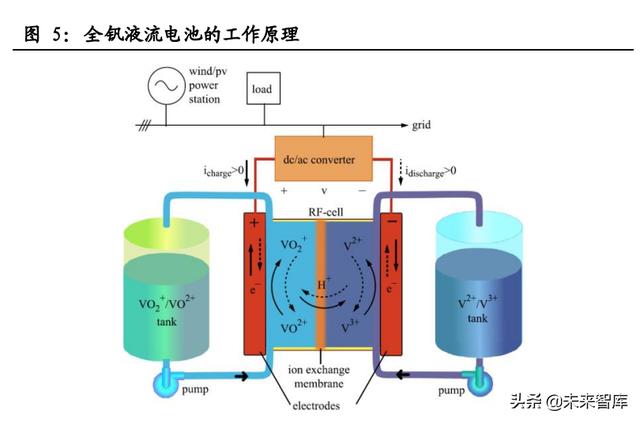
目前,全钒体系是双液流电池中最成熟的方案。所有双液流电池在电堆 结构上大同小异,主要差别在于活性物质不同,这是决定理论能量密度 的核心要素。从电化学理论上讲,只要有两组电势差不同的电对,即可 用它们的变价化合物作为正负极活性物质组成液流电池。然而,在实际 电池制作时还需考虑更多因素,例如活性物质的稳定性、溶解度、电极 反应可逆性、电化学窗口匹配性等等。真正进入商业化阶段时,还涉及 到安全性、成本、效率、寿命、环保等约束条件,是一个多学科交叉的 复杂系统工程。多年以来,围绕这些复杂因素,科研人员对液流电池展 开大量研究,累积了丰富的实验数据。在经过大浪淘沙般的筛选后,全 钒液流电池成为现阶段最有可能率先实现大规模商业化应用的液流电 池方案。全钒液流电池的整个系统由能量单元、功率单元、输运系统、 控制系统、附加设施等部分组成,其中能量单元和功率单元是核心模块。
1.2.1. 电解液材料:能量单元的核心要素
全钒液流电池的正负极电解液是其真正的储能介质,是能量单元的核心, 一般由活性物质、基质、添加剂三部分组成。电解液中活性物质的浓度 以及溶液总量(体积)从根本上决定了整个电池系统的能量密度、储能 容量上限;电解液的热稳定性决定了电池的工作温区和可靠性。
活性物质:钒硫酸盐 全钒液流电池的电解液活性物质为钒硫酸盐,其中钒元素是活性元素。 之所以选择钒作为核心工作元素,是因为钒的基态电子组态为[Ar]3d24S2, 具有丰富多变的氧化价态,+2、+3、+4、+5 价都能在酸性水溶液环境 中稳定存在,并且正负极的还原电位恰好与水的电化学窗口适配。此外, 不同价态的水合钒离子特征光谱迥异,易于辨识:二价钒为紫色、三价 钒为深绿色、四价钒为蓝色、五价钒为黄色,可以用 UV-Vis 光谱进行 浓度定量分析,从而对电解液的荷电状态(SOC)进行实时监测。不同 价 态 钒 的 硫 酸 盐 作 为 活 性 物 质 , 正 负 极 氧 化 还 原 电 对 : VO2 + /VO2+ -V3+/V2+,正极反应:VO2 + + e ⇌ VO2+,负极反应:V2+ ⇌ V3+ + e,全电池反应:VO2 + + V2+ ⇌ VO2+ + V3+。在理想情况下,未充电的 原始电解液正负极活性离子分别为 VO2+和 V3+,二者比例应该为 1:1, 以满足化学计量比要求,使活性物质被充分利用。
基质:硫酸水溶液 全钒液流电池的电解液基质一般为硫酸水溶液,其作用是维持电解液的 低 pH,抑制钒离子的水解,并增加电解液的电导率,降低欧姆极化。 采用硫酸水溶液的主要原因在于硫酸根离子的化学惰性较强,不容易被 氧化或还原,因此副反应相对较少。同时,硫酸没有挥发性,其水溶液 的蒸汽压较低,因此系统内压一般变化不大。尽管硫酸作为支撑电解液 的基质,对能量储存虽没有直接贡献,但是其含量会直接影响电解液的 放电容量和能量效率。随着硫酸浓度上升,电解液粘度增大,导致液流 阻力增大,浓差极化效应加剧,导致放电末期的电压突降,总放电容量 较少;电解液整体电导率增大,欧姆极化效应减轻,因此能量效率提升。 综合考虑,电解液中的硫酸浓度一般控制在 2~3mol/L 为宜。

添加剂:有机及无机络合剂 为了增加电解液中钒离子的溶解度和稳定性,一般还需加向其中入少量 的添加剂,起到抑制固体沉淀析出的作用。电解液添加剂的种类繁多, 分为有机物和无机物两大类。有机添加剂一般为多齿配体,带有羟基、 巯基、氨基等配位官能团,能与钒离子形成较稳定的络合物,抑制 V2O5 固体的成核长大,同时还起到分散剂的作用,降低粒子的表面能,抑制了胶粒的聚沉。常见的有机添加剂包括:氨基酸、多元醇、氨基磺酸以 及一些表面活性剂和水溶性高分子聚合物等。无机添加剂一般为盐类, 其中的阴离子或阳离子能与钒离子形成配位键,例如磷酸盐、铵盐等, 其作用机制也是抑制 V2O5 固体的成核长大,从而稳定电解液。添加剂 的用量视具体种类和电解液浓度而定,一般在 1~3%,过量使用会阻碍 离子传输机制,增大电解液的欧姆极化效应,降低系统能量效率。(报告来源:未来智库)
1.2.2. 电堆材料:功率单元的核心要素
电堆是全钒液流电池进行电化学反应的场所,决定了系统的功率特性, 电堆的性能会直接影响系统整体的性能。一个全钒液流电池电堆本质上 是由多个单电池叠合串接组成,一般以压滤机的方式进行叠合紧固,其 内部有一套或多套电解质循环系统,而电流出入端口则是统一的一套。 全钒液流单电池的主要构件包括:电极、双极板、隔膜、端板、密封件, 以及其他紧固件等。
电极: 全钒液流电池的电极并不参与电化学反应,只是作为反应的场所,活性 物质在电极表面得到或失去电子,发生还原或氧化,实现电能与化学能 之间的相互转化。电极材料的物理化学性能对全钒液流电池有重要影响: 第一,电极的导电性和催化性能直接影响电池的极化状态以及电流密度 大小,进而影响能量效率;第二,电极材料的物理化学稳定性直接影响 电池整体工作稳定性和实际寿命,因此电极材料必须有较高的化学惰性、 机械强度、导电性,最好比表面积较大。早期使用金属电极,包括金、 铅、钛等单质金属,以及钛基铂、钛基氧化铱等合金材料。但金属电极 材料存在很多缺陷,有的电化学可逆性差,有的成本过高,难以大规模、 长时间使用。之后,人们改用碳素类电极材料,例如石墨、玻碳、碳毡、 石墨毡、碳布以及碳纤维等,这类碳材料化学稳定性好,导电性好,易 制备且成本低。研究发现,玻碳电极可逆性差;石墨和碳布电极在充放 电过程中易被刻蚀损耗,而且这几种材料的比表面积小,造成电池内阻 较大,难以大电流充放电;碳纸电极比表面积虽大,稳定性也较好,但 亲水性较差,电化学活性不高。目前,最广泛使用的电极材料是碳毡或 石墨毡,它们都属于碳纤维纺织材料。
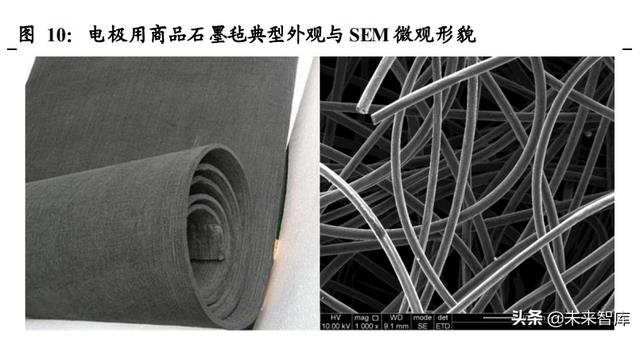
双极板: 全钒液流电池中的双极板是一种导电隔板,它与电极紧贴在一起,用来 分隔两个相邻单电池的正负极电解液、汇集电流,并对电极起支撑作用, 从而在电堆内部实现多个单电池的串联。理想的双极板材料具有:良好 的阻气和阻液性、导电性、化学惰性、机械强度。阻气和阻液的目的是 防止极板两侧的正负极电解液渗透交叉污染,这是双极板最基本的要求。 高导电性既包括双极板自身的低阻抗,还要求双极板与电极之间的接触 电阻较低,这是为了降低电池的内阻。由于双极板的两侧分别是强氧化 性和强还原性的电解液,要在这种严酷环境下长期运行,双极板材料必 须有很高的化学惰性。最后,双极板作为支撑电极,必须有较好的机械 强度和可加工性。最初使用的是金属双极板或纯石墨双极板,前者的机 械强度好但耐腐蚀性较差(金、铂等贵金属则成本过高),后者的耐腐 蚀性好但脆性大且加工成本高。目前一种方案是对石墨双极板改性,提 高机械强度和可加工性;另一种方案是采用碳塑复合双极板,将导电填 料和聚合物树脂混 制成型,具有很好的机械强度和耐腐蚀性,但是导电性有所降低(电阻率相比金属和石墨双极板提高 1~2 个数量级)。目前 而言,电极材料也是一种易损耗材料,在正常工况下的实际使用寿命大 约在两年左右,到期后需要进行更换。目前,研究者们通过热压或模压 将电极与双极板粘结成一体,能得到电化学性能好又不易刻蚀的一体化 电极-双极板。
隔膜:离子选择性透过,长寿命的关键点 。全钒液流电池中的隔膜是一种离子传导膜,位于每个单电池中央,用来 分隔单电池内部的正负极电解液,防止活性物质互相混合发生“蹿液” 而自放电,同时允许特定离子的选择性传递,保证电池内部电路导通。 隔膜性能直接影响电池的效率和寿命,一般要求:较高的离子选择性、 离子导电性、化学稳定性、机械强度。理论上可选用:阳离子交换膜、 阴离子交换膜、多孔分离膜。其中,阳/阴离子交换膜有负/正电荷基团, 可让特定类型的阳离子或阴离子透过;多孔分离膜没有荷电基团,通过 离子半径来进行筛选和截留。目前在全钒液流电池在应用最为广泛的是 质子传导膜,属于阳离子交换膜,工艺成熟,典型代表是杜邦公司生产 的 Nafion 膜,这是一类全氟磺酸树脂,化学稳定性和离子导电性很好,但离子选择性不好,成本高(500~800 美元/平方米)。之后,人们尝试 将苯磺基等离子选择性基团修饰在部分氟化聚合物碳链上,制成了部分 氟化膜,离子选择性明显提高,但化学稳定性降低,而且需要辐射工艺。 考虑到氟化树脂的昂贵,人们转而研发非氟烃类膜,一类是无孔型非氟 离子交换膜,另一类是多孔型非氟分离膜。无孔型非氟离子交换膜是在 非氟聚合物上引入离子选择性基团,例如磺化聚芳醚酮,其离子选择性 和导电性较好,但化学稳定性降低,循环几百次就被严重破坏。多孔型 非氟分离膜的典型代表是纳滤膜,表面没有荷电基团,但分布有大量的 纳米级微孔,允许半径较小的水合质子通过,不允许半径很大的水合钒 离子通过。目前,全氟磺酸树脂膜已开始国产替代,而非氟膜的应用则 方兴未艾,这对于降低电池系统的成本具有重要意义。
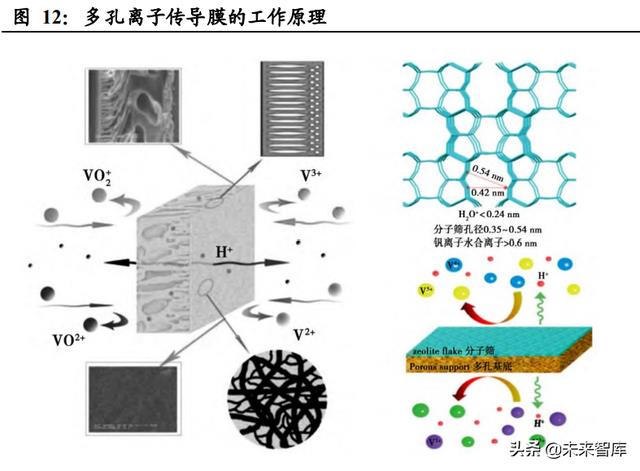
密封件: 密封性是钒电池性能的重要保障,系统全密封运行,严格避免电解液的 外漏和内漏。若发生外漏,二价水合钒离子在空气中极易被氧化而发生 容量损失,而且强腐蚀性的电解液可能破坏电堆的其他构件。若发生内漏,正负极电解液可能互混,这将直接影响电堆的性能和寿命,而且从 电堆外部不易发现漏液。由于全钒液流电池的正负极电解液具有强氧化 性和强还原性,且电解液基质又是硫酸,普通的橡胶密封材料根本无法 耐受这种环境,必须采用特殊的氟橡胶作为密封件。此外,用于密封件 的氟橡胶材料应具有适宜的硬度、拉伸强度、拉断伸长率和撕裂强度, 并且压缩塑性形变量要尽量小,还需要附加自紧固装置。然而,氟橡胶 的价格很昂贵,大约 30~40 万元/吨,而且在长期运行中仍然面临老化、 塑性变形等问题。中科院大连化物所的科研团队通过一体化激光焊技术 简化密封工艺,实现隔膜-电极-双极板的一体化,节省了氟橡胶构件, 这对于降低电堆成本具有重要意义。
1.3. 制造工艺与技术壁垒
1.3.1. 电解液材料制造:配方和工艺是关键
钒电池电解液是通过在硫酸中还原五氧化二钒制成,可利用化学法或电 解法等工艺大规模生产。早期的钒电池电解液是由硫酸氧钒(VOSO4) 溶于硫酸溶液来直接配制的,优点是操作简便,但硫酸氧钒的价格昂贵, 经济性较差,不适合规模化生产。目前,量产钒电池电解液的方法分为 化学还原法和电解法,本质都是把五价钒还原成低价。化学还原法是将 五价钒原料(如五氧化二钒、偏钒酸铵等)与硫酸溶液混合,放入还原 剂(如草酸、二氧化硫等)后加热,反应得到低价钒盐溶液。电解法是 通过在电解槽中对五价钒原料进行阴极还原,同样得到低价钒盐溶液。 化学法优点是工艺和设备简单,缺点是反应较慢,需要高温处理。电解 法的优点是可以常温大批量生产,生产效率高,缺点是需要消耗较多的 电能。初始状态的电解液中钒离子的氧化价态在 3~4 之间,输入电堆后 开始预充电,阳极的钒离子被统一氧化成+5 价,阴极的钒离子被统一还 原成+2 价,至此完成了正负极电解液价态调整,可以开始工作。
电解液 是全钒液流电池 系统总成本中占 比最大的部分( 一般为 30%~50%)。尽管电解液的基本原料都是五氧化二钒,属于同质化产品, 但由于不同厂家采用的电解液生产路线和添加剂各不相同,因此制得的 电解液性能和成本也有较大差异。在性能方面,主要是电解液配方具有 独特性,特别是浓度、酸度和添加剂等,企业都以专利形式进行保护。 同时,不同企业技术的差异会造成电解液杂质含量的差异,也会反映在 电池性能上。此外,不同生产工艺的加工成本不同。目前电解液的市场 价格大约为 1500 元/kW·h,储存 1kW·h 电能大约需要 10kg 五氧化二钒, 因此电解液形式的五氧化二钒价格约 15 万元/吨。目前市售五氧化二钒 现货价格约为 10 万元/吨,因此五氧化二钒加工成电解液的单位成本约 为 5 万元/吨。换言之,电解液成本的 2/3 来自于五氧化二钒,1/3 来自 于加工费用。由于五氧化二钒本身是从钒渣、石煤中提取的,如果将电 解液的工艺起点直接从钒渣、石煤等原材料开始,跳过五氧化二钒环节, 那么就能缩短整个制造流程,从而大幅降低电解液成本,而这要求企业 具有相当大的产能规模,并且对上游具有相当强的掌控力。
1.3.2. 电堆材料与装配:材料复杂,装配精密
1.3.2.1. 电堆核心材料:电极、双极板、隔膜
电极:碳基纺织材料。 电极材料常用碳毡或石墨毡。碳毡是有机高分子纤维毛毯经过预氧化、 惰性气氛碳化等热处理工艺制得的,石墨毡则是将碳毡进一步在 2000℃ 以上的高温下进行石墨化处理制得。这类碳纤维电极具有很大的比表面 积,化学稳定性和导电性也很好,但在长期使用时容易发生氧化脱落, 因此还需要对其进行改性处理,包括材料本征处理、金属化处理和氧化 处理等,或与惰性高分子基体共制成复合材料(但电导率会降低)。
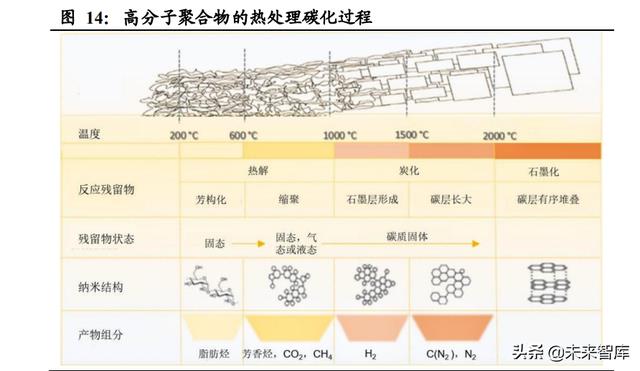
双极板:碳塑复合材料 。碳塑复合双极板在目前的全钒液流电堆中应用最广泛。碳塑复合双极板 的加工性能、结构强度等明显优于无孔硬石墨板;阻液性能明显优于柔 性石墨板;抗腐蚀性远强于普通金属双极板,而且制造工艺简单,成本 低廉。碳塑复合双极板的原料包括聚合物基体和导电填料。其中聚合物基体一般为 PE、PP、PVC 等惰性塑料或者环氧树脂等;导电填料分为 两部分,主要导电填料主要为石墨粉,次要导电填料可以选择炭黑、碳 纤维等无定形碳,混合后经过模压、注塑等方式加工成型。导电填料在 聚合物基体内部构成三维导电网络,同时一定程度上提高了机械强度。
隔膜:全氟磺酸树脂 。全氟磺酸树脂膜是目前全钒液流电堆中应用最多的隔膜。从分子结构看, 全氟磺酸树脂的主体骨架为聚四氟乙烯结构,支链端基为磺酸基团的全 氟乙烯基醚结构,合成路线:四氟乙烯与全氟醚磺酰氟在引发剂作用下 共聚,再经过水解和酸化。全氟磺酸树脂的合成难度尚可,更大的困难 在于后续加工成膜环节,关键在于降低加工损耗,并制造出厚度均匀、 性能优异的膜,而核心的熔融挤出压延成型技术长期被美国杜邦公司所 垄断,国产膜容易出现“针眼”等缺陷而难以满足使用要求,所以只能 依赖进口,这是导致全氟磺酸树脂膜价格昂贵的重要原因。目前,全氟磺酸树脂的加工成型技术分为:熔融挤出法、凝胶挤出法、溶液浇筑法、 流延法等。近年来,国内逐步开始推进全氟磺酸树脂膜的国产替代,并 取得了显著成果,代表性企业有东岳集团和江苏科润。
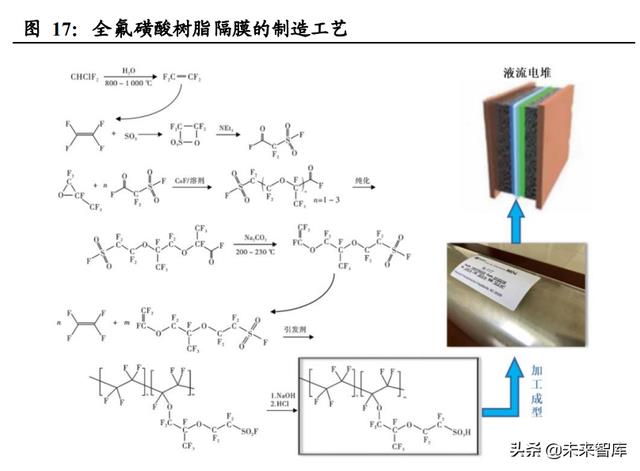
1.3.2.2. 电堆装配:叠合紧固,要求较高
全钒液流电堆的装配设计对技术要求较高。从电堆的整体布局和单电池 结构来看,全钒液流电池与质子交换膜燃料电池也有很多相似之处,但 钒电池系统并不需要使用贵金属催化剂,也不存在介质储存困难的问题。 事实上,很多优秀的液流电池研发团队都有丰富的氢燃料电池电堆研究 经验,例如中科院大连化物所。全钒液流的电堆装配与氢燃料电堆完全 一致,都是以压滤机的方式进行叠合紧固,这种组装方式看似简单,实 际具有较高的技术要求。首先,叠合紧固会对电极产生压缩,改变电极 孔结构,很考验双极板的耐压性能;其次,电极与双极板之间是硬接触, 即依靠一定的压紧力来降低界面接触电阻,如果贴合不良则会降低电堆 的电压效率;同时,电堆的防漏要求很高,漏液漏气不仅造成容量衰减, 还可能造成安全事故。
2. 横向比较:钒电 vs 锂电、钠电、钠硫
液流电池的构造与锂离子电池等普通二次电池截然不同。首先,液流电 池的电极采用的是惰性材料,正负电极本身不参与电化学反应,而实际 参与反应的活性物质具有独立的能量储存单元,在循环泵作用下沿传质 线路在电堆内部和外部储罐之间形成闭环,向电极及时供应活性物质, 并将反应产物快速抽离,从而避免了浓差极化和热累积效应。换言之, 液流电堆单元只是一个发生电化学反应的场所,活性物质在空间分布上 与之分离,这意味着两层含义:其一,电池的功率特性与容量大小相对 独立,因而在设计和应用上可以有很大的灵活性;其二,活性物质由外 置的储罐单独存放,便于运行维护和安全管理,这正是液流电池相比于 其他二次电池技术的安全性、灵活性等优势的根源。此外,液流电池的 活性物质一般是完全溶解在电解液中构成均相体系,而不像锂离子电池 那样附着在集流体上,因此没有复杂的固态相变,没有机械应变等破坏 因素,这是液流电池循环寿命远长于其他二次电池技术的根源。(报告来源:未来智库)
2.1. 钒电 vs 锂电:性能特点截然相反,应用场景迥然不同
全钒液流电池与锂离子电池的性能特点截然相反,二者的应用场景相差 甚远,其实并不在同一赛道。首先,从(质量)能量密度看,全钒液流 电池比锂离子电池低得多。目前,锂离子电池体系中最低的磷酸铁锂电 池是全钒液流电池最大值的 3 倍以上。如果再算上附加设施,那么储存 相同水平的能量时,整个全钒液流电池系统的体积约为锂离子电池的 3~5 倍。因此,目前的水系全钒液流电池几乎不可能用于车载动力电池 或小型消费电子领域。规模化静态储能对能量密度要求不高,对占地面 积等空间因素的容忍性较大,因而成为全钒液流电池的主要应用场景。
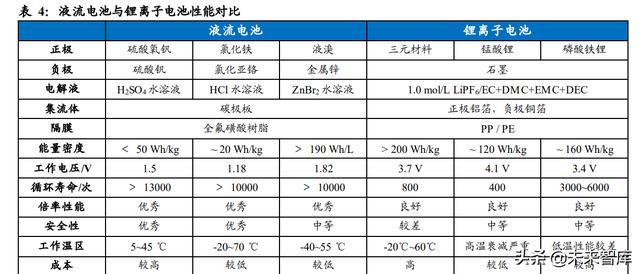
2.2. 钒电 vs 钠电:优缺点呈高度互补,或并立于储能市场
全钒液流电池与钠离子电池具有很强的互补性,前者适用于大中型规模 储能,后者适用于小型灵活储能。液流电池是一种液相(水相体系为主) 的电化学储能装置,其特点在于活性工作物质溶解在电解液中,通过改 变活性物质的氧化价态实现能量的存储与释放,典型代表有全钒液流电 池、铁铬液流电池、锌溴液流电池等。液流电池的最大优势在于其水相 体系的本征安全性,以及超长的循环寿命,特别适用于中大型的电化学 储能设施,但缺点则是能量密度低、工作温区窄,因此很难小型化或应 用于高寒地区。相比之下,钠离子电池的能量密度约是液流电池的 3 倍 以上,可耐受-40℃的低温,但由于其基本原理和结构与锂离子电池完全 相同(都属于离子嵌脱型二次电池,都使用易燃的有机电解液),本征 安全性和循环寿命不及液流电池。未来,钠离子电池和液流电池将有望 在储能领域实现分层次优势互补。例如,户用和移动式小型储能设备对 能量密度要求较高,适合使用钠离子电池;大中型的电化学储能电站对 安全性的要求较高,适合使用液流电池。
2.3. 钒电 vs 钠硫:能量密度不是根本,安全问题一票否决
钠硫电池的能量密度虽然远高于液流电池,但是安全性缺乏保障,已经 被国内外多个国家否决。钠硫电池诞生于 20 世纪 60 年代,国外的产业 化探索超过半个世纪,优点是能量密度高、功率密度高、库仑效率高、 寿命长、成本较低,曾一度占据国外电化学储能技术的主流,典型代表 是日本 NGK 公司。然而,钠硫电池的致命缺点是安全性能差,正负极 分别使用单质硫和金属钠,仅用脆性陶瓷隔膜分离,运行温度在 300℃以上,一旦隔膜破损会发生爆炸反应。自 2011 年以后,钠硫电池研发和 应用在国外处于停滞状态,国内也出台政策明确否决了钠硫电池在中大 规模储能领域的应用。相比之下,全钒液流电池虽然在能量密度上无法 与钠硫电池抗衡,但作为中大规模储能设备,其安全性方面的巨大优势 足以弥补其不足之处。
3. 产业现状:技术完备,只欠东风
当前,全钒液流电池技术已经完备,但产业链尚未健全,需求尚未打开, 产能正在蓄力发展,规模效应尚未显现。我们认为,全钒液流电池产业 在未来的 3 年内可能仍将处于导入期向成长期过渡的阶段,并预计将在 “十四五”末期迎来爆发式增长。
3.1. 产业结构:链条较长,复杂度高
全钒液流电池产业链也包含上游、中游、下游三个部分,但是比锂离子 电池更复杂,涉及多个行业。上游:原材料供给、电解液配制、电堆材 料加工,主要原材料包括五氧化二钒、硫酸、碳材料、聚合物材料等, 以及各类辅材,涉及基础化工、钢铁冶炼、有色金属等产业,其中钒矿 及其加工业处于核心地位,是电解液原料五氧化二钒的来源。中游:电 堆装配、控制系统、其他设备和附件等,其中电堆装配和控制系统的技 术壁垒最高,涉及各类耗材和电子元器件。下游:终端应用市场,主要 为各类储能用户,包括发电侧、电网侧、用电侧。
3.1.1. 上游:钒矿及钒加工、电堆材料制造
(1)钒矿及钒加工:与钢铁行业强关联
由于钒的离子半径与同价态的铁、钛、铝、磷等非常接近,容易发生同晶 掺杂替换,因此自然界中的钒一般与这些元素伴生。此外,由于化合价态 的多变,钒离子还可以在化合物的晶格中替换钼、铬、钨、铌、锰、铜等元 素。因此,钒是一种亲石元素,一般以分散状态存在于矿石中,其自然分布 特点是:储量大,分布广,含量低。在自然界中,很少有高品位的钒矿,目 前已知的 70 多种含钒矿物中,钒含量较高的矿物只有少数几种,主要是: 绿硫钒矿、钒铅锌矿、钒铜铅矿、钒铅矿、钾钒铀矿、钒云母。这些富钒矿 区大都在非洲、美洲等地,而且储量也非常有限,例如曾经是钒原料主要来 源的秘鲁的绿硫钒矿已经被开采殆尽。二战后,钒的主要来源之一是钒铀矿 提铀过程中的副产物,这得益于原子能工业的快速发展,其主要原料是钾钒 铀矿(K2(UO2)2(VO4)2·3H2O),它是一种钾铀酰的钒酸盐水合物,主要产于 美国、澳大利亚等地。到了 70 年代后,钒的富集工艺得到进一步改善,人 们可以从一些低品位的矿石中富集和提取钒,这些矿石多为含钒的铁矿,或 者含钒碳质页岩,这大大拓宽了钒的获取渠道。
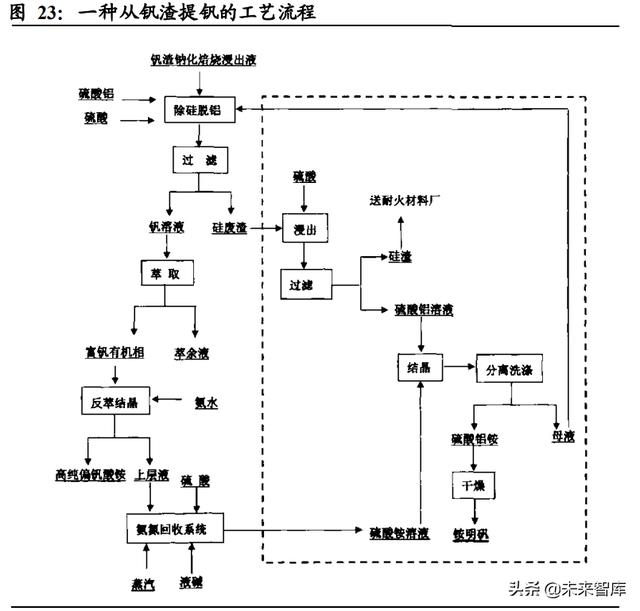
含钒碳质页岩是我国钒资源的主要构成部分,占我国钒总储量的 87%。 碳质页岩也称“石煤”,属于沉积矿,由古代富钒的菌类、藻类以及浮 游生物等残骸沉积变质形成。石煤虽然也称为“煤”,但热值一般在 4184 kJ/kg(仅相当于普通燃煤热值的 1/5),碳含量仅 10~15 %,灰分含量却 高达 70~88 %,故而得名“石煤”。石煤中化学元素极为丰富,除碳以外, 灰分含钙、硅、铝、钒、钼、银、镓、铯、钾、铬、砷、汞、铅、镉等 20 多种元素。钒在石煤中以钒云母、含钒高岭土、含钒电气石、含钒石 榴石等物相存在,整体钒含量(以五氧化二钒计)一般为 0.13~1.2 %, 品味较低。多数石煤在提钒时需先进行氧化焙烧,主要是为了脱碳,并 将低价态的钒氧化为五价,该步骤的产热可用于发电或供暖。然后再与 钠盐或钙盐混合后二次焙烧,将钒转化为钒酸盐,也可直接将一次焙烧 产物酸浸处理。我国的石煤提钒工业起步于 70 年代末期,经过 30 多年 的发展,在钒产业中已具有重要地位,但传统工艺转化率低、污染严重, 河南、湖北、重庆、陕西、新疆、贵州等存在石煤提钒产业的省份对新 建企业大多采取禁止采用加盐(含低盐)焙烧提钒技术的产业政策。目前, 我国急需发展高效、绿色的石煤提钒新工艺,充分利用该资源。
含钒固态废弃物是除了矿石钒以外的重要钒资源,尤其是某些地区的燃 油烟灰,以及工业废弃钒催化剂等都可以用来提取钒。例如,委内瑞拉、 俄罗斯等地的原油中钒含量相对较高,其燃油烟灰中含有 4.4~19.2 %的 钒,最高的可达 40 %,而且总量基数大,具有重要的回收价值。由于烟 灰是燃烧产物,其中的钒元素已经全部被氧化为五价,无需再进行焙烧 预氧化,一般碾碎后直接用氢氧化钠水溶液加热浸泡,即可使钒转变为 钒酸钠进入水相,滤渣中残余钒可进一步用盐酸浸取富集,再萃取分离。 这种湿法浸取工艺可提取烟灰中 90 %以上钒,且纯度较高。此外,废弃 钒催化剂也是重要的钒资源,回收后既避免污染,又节约资源。主要的 钒催化剂包括:接触法制硫酸催化剂、烟气脱硝催化剂和石油化工合成 中的各种钒催化剂,既可采用氢氧化钠转化为钒酸盐回收,也可以还原 酸化后制成硫酸氧钒回收。由于钒矿属不可再生资源,含钒固废的回收 和循环利用具有深远意义。
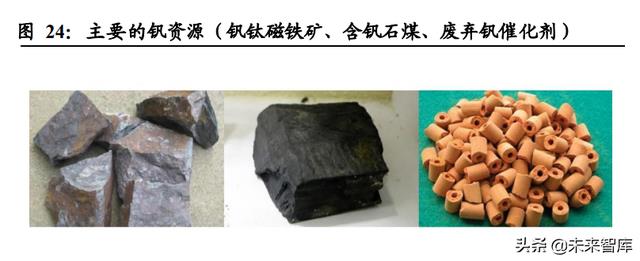
(2)电堆材料制造:发展空间大,技术壁垒高
全钒液流电池的电堆材料包括:电极、双极板、隔膜、密封件等几种关 键材料,其原料多为碳材料以及高分子聚合物材料等,与有机化工产业 密切相关。由于各个厂家的选材和工艺不尽相同,电堆材料的成本及性 能也存在差异性。此外,现有电堆材料的技术和工艺尚有较大的改进空 间,相关研发工作仍在不断进行中 ,逐步实现国产替代。
双极板以石墨为主要原料,制成改性石墨双极板或碳塑复合双极板。其 中,石墨双极板是用石墨粉与树脂或沥青混合后,在石墨化炉中经 2500~2700℃高温一体石墨化处理而得,再经过切割和打磨制得。石墨 双极板具有致密度高,电阻率低的优点,但制造过程耗时久,成本高, 而且材料脆性大,在压制紧固时容易发生碎裂,因此不适合大功率、大 规模的电堆,仅适合小型电堆。目前,大功率电堆中使用的多为碳塑复 合双极板,一般采用导电碳粉(如:石墨粉、炭黑、碳纤维等)与热塑 性烃类聚合物(如:PE、PP、PVC 等)混合后加入阻滞剂、脱模剂, 然后以注塑或模压的方法加工成型。
隔膜材料最初是采用全氟质子交换膜,之后可能转向非氟离子传导膜。 全氟质子交换膜最早用于氯碱工业,成功实现产业化,之后又广泛应用 于氢燃料电池。相比燃料电池隔膜,全钒液流电池隔膜不仅要求有很高 的化学稳定性和机械强度,而且要有较好的离子选择透性。目前,国内 的东岳集团等企业已具备自主生产全氟磺酸树脂膜的能力,但液流电池 用的高质量 Nafion 膜仍需进口,价格非常昂贵,例如 Nafion 115 的价格 过去为 700 美元/平方米,这是因为磺基氟代烃类聚合物的成型技术长期 被美国杜邦公司垄断。此外,Nafion 膜的离子选择性差强人意。另一条 路线是采用非氟离子传导膜,即非离子交换性隔膜,该技术是我国自主 发展的方向,以中国科学院大连化学物理研究所为代表的科研团队已经 取得了重要成果,具有核心知识产权。
3.1.2. 中游:电堆整机装配、控制系统
电堆整机装配:技术壁垒高,研发周期长
全钒液流电堆的装配技术壁垒较高。全钒液流的电堆装配与氢燃料电堆 完全一致,都以压滤机的方式进行叠合紧固,业内很多优秀的液流电池 研发团队都有多年的氢燃料电池电堆研发经验,例如中科院大连化物所。 压滤机叠合紧固会对电极和双极板产生压应力,压力过大可能导致板材 发生塑性变形甚至断裂;压力不足则会导致电极与双极板之间贴合不良, 使接触电阻增大,降低电堆的电压效率,还可能会导致漏液漏气,造成 系统容量衰减,甚至无法工作。一般来说,电堆的功率规模越大,内部 材料的工作面积就越大,其叠合装配的工艺难度也就越大。在现行技术 框架下,具有大规模全钒液流电堆生产能力的企业数量并不多,而电堆 主体结构经过多年发展,很难做大幅改动,因此这些头部企业具有先发 优势,并通过不断优化升级,长期保持领先优势。
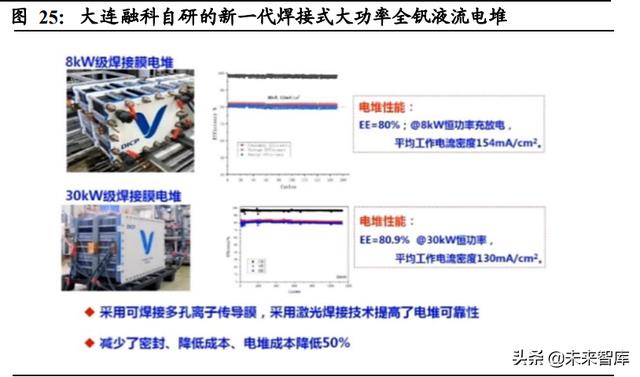
控制系统:成熟度较高,自研或外包
控制系统包括 PCS、BMS、EMS 等,所需硬件装置是电力电子行业的 基本元件,相关产业都比较成熟,可通过与相关企业合作,定制化生产。 电解液输运系统由管路、循环泵、变频器、控制阀件、传感器、换热器 等部件构成,这些装置在化工生产领域较为常见,可直接采购相应零件 自行加工,或者外包设计。其他设施还包括消防装置、建筑材料等等, 占全钒液流电池系统总成本比例较低,利润空间相对较小。
3.1.3. 下游:储能——发电侧、电网侧、用电侧
产业链下游为各类储能用户,按照电力产业链的主体结构,其自上而下 可分为:发电侧、电网侧、用电侧。在不同的接入方式下,储能设备的 电能容量、建设规范、验收标准、运行模式也各不相同。目前,产业化 的储能技术主要包括抽水储能和电化学储能,后者又主要包括:锂离子 电池、铅蓄电池、液流电池和其他电池技术。据中国储能网的数据统计 显示,截至 2020 年底,国内储能累计装机容量中,抽水储能占 89%, 比 2019 年比例下降了四个百分点;电化学储能占 11%,其中 89%是锂 离子电池,铅蓄电池占比约 10%,液流电池只有 0.7%左右。在 2020 年 新增的电化学储能中,锂离子电池占了 97%,但考虑到安全性等因素, 未来锂离子电池储能的增量可能将下降,整个市场的增量可能会逐步转 向液流电池,尤其是技术最为成熟的全钒液流电池。(报告来源:未来智库)
3.2. 主要企业:市场集中度较高,中国企业占鳌头
我国的全钒液流电池研究和产业化世界领先,国内钒电池企业分为两类: 一类是科研院所自研技术转化创建的初创型企业,以大连融科为代表; 另一类是吸收合并国外技术,再优化升级的企业,以北京普能为代表。 国外的全钒液流电池相关企业大都规模较小,主要分布在日本、北美和 欧洲。全钒液流电池产业链复杂度较高,其中核心环节是材料端和设备 端,材料端主要包括电解液材料和电堆材料,设备端主要包括整机装配和控制系统。
3.2.1. 材料端:电解液材料、电堆材料
(1)电解液材料
全钒液流电池的电解液材料核心是钒化合物。电解液制造分为两个步骤, 首先是核心前驱体的生产,即钒化学品(五氧化二钒、偏钒酸铵等), 目前拥有相关技术和量产能力的基本为大型钒提炼及加工企业;尔后是 将前驱体转化为电解液,目前掌握钒电解液制造的全球龙头企业是大连 博融新材料公司,全球市场占有率在 80%以上。
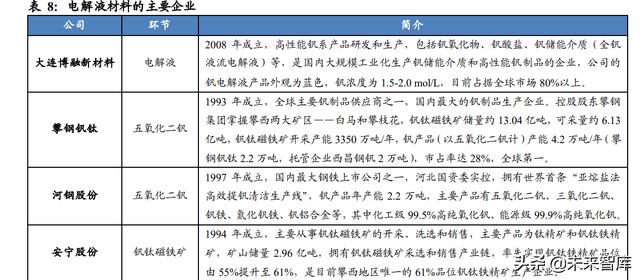
(2)电堆材料
全钒液流电池的电堆材料与氢燃料电堆相似度很高。当前全钒液流电池 还没有大规模应用,因此几家代表性企业主要依靠自研自产或外协加工 的方式生产电极材料,以供自用。未来一旦市场需求放量,则大概率会 供不应求。由于全钒液流电堆材料中的电极、双极板、隔膜等材料与氢 燃料电池的相应构件几乎相同,因此目前从事氢燃料电堆材料研发和生 产的企业,未来较容易转型成为钒电池的电堆材料供货商,应予以关注。
3.2.2. 设备端:电堆整机制造、控制系统制造
我国的钒电池企业大致分为两类:一类是科研院所自研技术转化创建的初创型企业,多以校企合作模式开展,以大连融科为代表;另一类则是 通过吸收合并或控股的方式,获得相应技术参与竞争的企业,以北京普 能为代表。主要企业有:武汉南瑞、上海电气、四川伟力得、上海神力 科技等,各自拥有核心技术,普遍研发时间超过 10 年。
4. 未来发展:提高性能,降低成本
全钒液流电池具有其他电化学储能技术无法替代的本征安全和长寿命, 阻碍大规模商用的主要原因是:性能单一导致应用场景局限,初始成本 过高导致经济性不足。未来全钒液流电池的发展方向主要在于提升电池 性能以拓展应用场景,以及降低系统的初始投资成本。
4.1. 当前痛点:能量密度低、工作温区窄、初始成本高
(1)全钒液流电池能量密度较低:应用场景有限
目前水系硫酸基全钒液流电池的能量密度仅有 20~50W·h/kg,不足磷酸 铁锂电池的 1/3。相对较低的能量密度意味着储存相同水平的能量,全 钒液流电池需要比锂离子电池更大的重量和体积,导致其实际应用场景 很有限,只能用于静态储能装置,而难以应用于车载电力系统或便携式 电子产品。事实上,锂离子电池能快速产业化和降低成本的重要应用就 是应用场景丰富,既能用于消费电子,也能用于汽车动力电池,所以一 旦技术基本成熟,需求端可以很快放量,规模效应得以显现。
(2)全钒液流电池工作温区较窄:需附加温控系统
目前水系硫酸基全钒液流电池的理想工作温区是 5~45℃,在此温度区间 以外需要温控调节。由于水系硫酸基钒盐溶液的热力学不稳定性,目前 全钒液流电池电解液对温度的要求较为严格,直接暴露于高温和低温下 都会导致系统无法正常工作。负极的低价钒离子在低温下容易结晶析出, 正极的五价钒离子在高温下容易聚合成五氧化二钒固体析出,以上两种 情况都会导致电解液容量衰减,还会使电堆流道阻力变大,使浓差极化 加剧,严重时甚至会毁坏电堆。因此,一般需要对全钒液流电池的电解 液进行温度控制和反馈调节,这样平均会损耗约 5%的内部能量,而且 增加了附加设备,使全系统的能量密度更低、体积更大。
(3)全钒液流电池初始成本较高:初始经济性不足
目前全钒液流电池的初始投资成本大约为 3000 元/kW·h,明显高于其他 成熟的储能技术,初始经济性不足。现阶段,全钒液流电池的核心成本 在于电解液和电堆材料,二者共占系统成本的 70%左右,在短期内很难 大幅降低。尽管全钒液流电池残值高、寿命长,因此在全生命周期内的 平均成本很低,但先决条件是产业链要打通,并形成“生产-使用-回收” 的闭环,而产业化的推进又需要先降低初始成本,提高下游需求方对于 该技术的接受度,这就造成了一个悖论。由于初始投资经济性不足,而 技术研发需要庞大的资金长期维持,企业没有积极性也没能力继续研发 推广,最终只能放弃研发而将技术打包卖出,这是国外钒电池研究多年 却一直不温不火的主要原因。
4.2. 技术展望:材料改进,系统优化
4.2.1. 电解液体系改进:能量密度更高,使用成本更低
(1)提高电解液浓度和稳定性:盐酸基全钒液流电池
提升电解液浓度和稳定性是增加系统能量密度,拓宽工作温区的关键。 传统的硫酸基全钒液流电池能量密度低、工作温区窄,本质是因为硫酸盐的溶解度难以提升,而且溶液的热稳定性差。为改善硫酸基钒电解液 的性能,常用方案是添加络合稳定剂,但迄今为止还没有一种添加剂能 兼顾正极电解液的高温稳定性和负极电解液的低温稳定性。钒离子有空 置的 3d 电子轨道,而氯离子作为一种弱场配体,能对钒离子进行有效 络合,从而提高钒盐溶解度和稳定性。基于这个思路,美国太平洋西北 国家实验室(PNNL)的科研团队于 2011 年率先开发了“硫酸+盐酸”的 混酸体系钒电解液,而后又开发了纯盐酸基钒电解液。其中,混酸体系 的钒离子浓度达到 2.5mol/L,能量密度较原硫酸基钒电池提升 70%,工 作温区-5~50℃;全盐酸基钒电解液的钒离子浓度达到 5mol/L,能量密 度较硫酸基钒电池提升 1 倍,工作温区-20~60℃。由于盐酸体系的蒸汽 压较高,且在过充情况下容易释放氯气,而当时的电堆系统材料较难满 足要求,因此该技术没能进入大规模商用化。
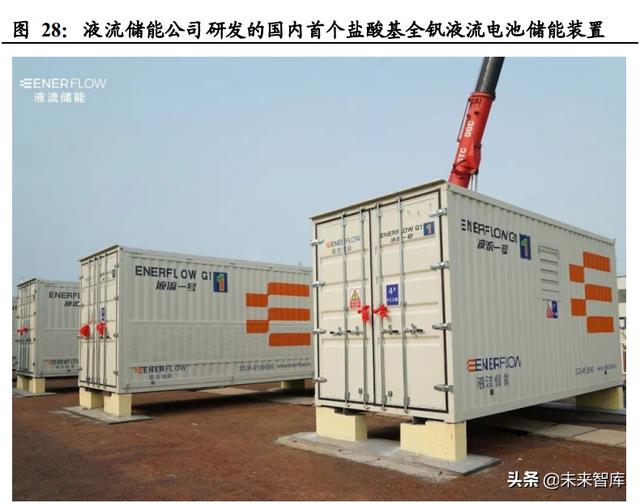
(2)拓宽电解液的电化学窗口:有机非水系液流电池
有机非水系电解液能大幅提升工作电压,从而提高钒电池的能量密度。 无论是传统的硫酸基钒电池,或是改进的盐酸基钒电池,其电解液都属 于水系溶液。正负极活性物质种类的选择受制于水的电化学窗口,正极 物质的电位不能高于水的析氧电位,负极物质的电位不能低于水的析氢 电位,因此水系全钒液流电池的正负极工作电压较低,而电池能量密度 与工作电压成正比,所以只有突破水系环境才能实现能量密度的跃升。 非水系的有机溶剂电解液有两个巨大优势:1)可选择的活性物质种类 大大增加,可以选择钒以外的其他轻质的廉价金属离子甚至是化合物, 进而提高比容量,降低成本;2)工作电压显著提升,这对于提高液流 电池的能量密度有重要帮助。然而,有机非水系液流电池也有很多缺点: 循环寿命较短,能量效率较低,以及有机溶剂的毒性和易燃性等。总体 而言,有机非水系电解液是实现液流电池小型化的重要方向,但可能会 在安全性方面打一些折扣,现阶段距离实际应用还有很远的距离。
(3)使用廉价金属做活性元素:全铁液流电池
使用铁等廉价金属替代钒作为活性元素,从源头降低电解液成本。全钒 液流电池的电解液成本占据系统总成本的 30~50%,其根本原因是钒的 价格昂贵。如果用一些廉价的金属替代钒作为活性元素,就能从根本上 降低电解液成本,典型代表是水系全铁液流电池,正负极氧化还原电对 为 Fe2+/Fe3+ -Fe0 /Fe2+,活性材料为氯化亚铁,基质为盐酸水溶液。电池 在满充状态下放电时,正极的活性物质发生还原反应:Fe3+ + e →Fe2+, 标准电位+0.77 V;负极的活性物质发生氧化反应:Fe0 → Fe2+ + e,标准 电位-0.44 V。全电池反应整体可合并为:Fe3+ + 1/2Fe0 → 3/2Fe2+,开路 电压 1.21 V,即三价铁离子与零价单质铁归中反应,变成二价亚铁离子 的过程,电子从负极出发,经外电路后到达正极。充电储能的过程则与 之相反。由于电解液为强酸环境,而亚铁离子的还原电位低于氢离子, 全铁液流电池的负极在充电时往往伴随严重的析氢反应,导致溶液 pH 升高,使亚铁离子发生水解,析出糊状氢氧化物。同时,全铁液流电池 属于“液-沉积”型液流电池,负极在充电时沉积出固体单质金属铁,当 沉积不均匀时就会形成尖锐的铁枝晶,容易刺穿隔膜,导致内短路。
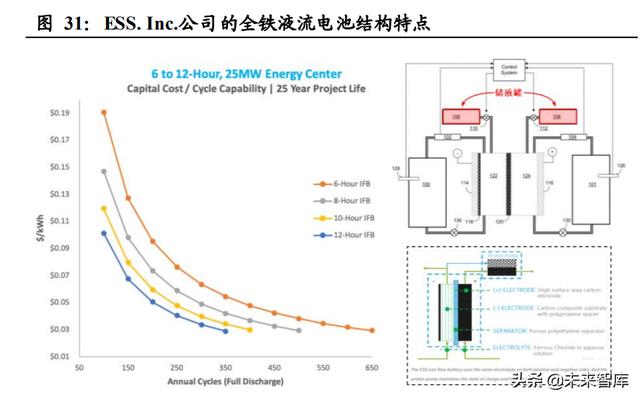
4.2.2. 离子传导膜改进:非氟多孔滤膜,替代全氟树脂
全氟磺酸树脂隔膜成本高,离子选择性较差,非氟多孔膜是未来重要的 替代方案。目前,以 Nafion 117 为代表的全氟磺酸树脂仍然是最常用的 钒电池隔膜,其稳定性、电导率都很好,但是成本过高,且离子选择性 较差。未来主要发展方向是开发新型隔膜,对全氟磺酸树脂膜进行替代, 其中一个有希望的方案是开发非氟多孔滤膜,也是目前液流电池膜材料 的研究热点,我国在该领域的研究处于世界前列。中国科学院大连化学 物理研究所的张华民团队原创提出“不含离子交换基团”离子筛分传导 机理,开发出稳定性、离子选择性较好的非氟多孔膜。不过,目前多数 非氟多孔膜的电导率相对全氟磺酸树脂膜较低,导致内阻偏大,有待于 进一步研究和改良。(报告来源:未来智库)
4.2.3. 全系统结构优化:小型钒电模组,面向户用储能
通过高效整合各个模块,制造集成度较高的小型化钒电模组,有望作为 户用灵活储能装置。由于全钒液流电池的本征安全性,可用于人员密集 的住宅区,例如户用储能系统。然而,一般的全钒液流电池系统的体积 庞大,限制了它在户用储能端的应用。为此,国内外部分企业开始探索 小型钒电模组,主要是通过提高电堆的功率密度实现电堆的小型化,再 整合各个模块,提高集成度,从而减小系统的总体积。目前,小型化的 全钒液流电池可做到与家用冰箱的尺寸相近,可以作为工商业生产以及 家庭用电的应急储备设施,已经出现了一些成型的产品。例如,国内的 大连融科储能技术发展有限公司推出的 ReFlexTM 系列,以及德国 Voltstorage 公司推出的全钒液流电池模块,每个小电池模块储能时长为 4h,可以独立工作,也可通过多个模块串联提高电堆功率。这种小型化 钒电模组拓宽了应用场景,为全钒液流电池的产业化注入了新的活力。
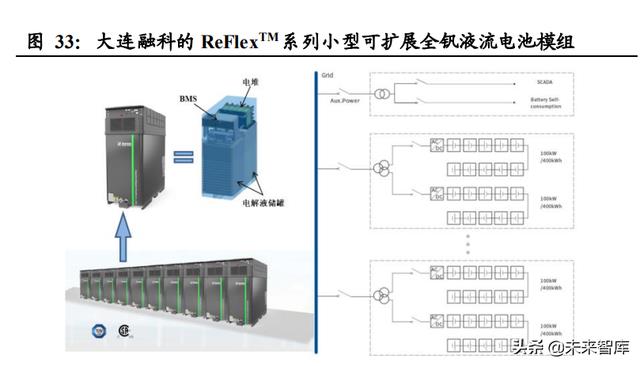
4.3. 发展速度:长期靠技术,短期靠模式,近期靠政策
液流电池技术不是新生事物,与锂离子电池技术在几乎同时诞生,在 70~80 年代一度曾是储能电池的主流方向,而那时的锂离子电池还处于 萌芽阶段,因为金属氧化物电极材料才刚刚出现,性能和成本上都不及 全钒液流电池。当时的国际环境大背景是美苏“太空竞赛”与两次石油 危机,而全钒液流电池恰好诞生于此期间。作为一种可靠的储能技术, 全钒液流电池受到了美国、日本等国家重点扶持,在此期间飞速发展。 可见,新技术的早期发展依赖政府支持,背后具有政治因素和战略目的。
(1)技术进步是最核心生命力:简化电解液工艺,提高倍率和容量
简化电解液工艺:直接从钒渣生产电解液
全钒液流电解液的制备通常以五氧化二钒为初始原料,而五氧化二钒本 身是从钒渣中提取的,若直接从钒渣开始生产电解液,电解液的加工成 本可以进一步降低。从钒渣提取五氧化二钒经历了液相富集和固相析出 的过程,而五氧化二钒在制成电解液时又从固相变回液相,如果从钒渣 提钒工艺中间的液相环节直接获取五价钒硫酸盐溶液,进行还原或电解 处理,可以缩短电解液的制造流程。该方案与钒渣处理绑定,只有具备 较大产能规模的上游钒矿加工企业才能做到。
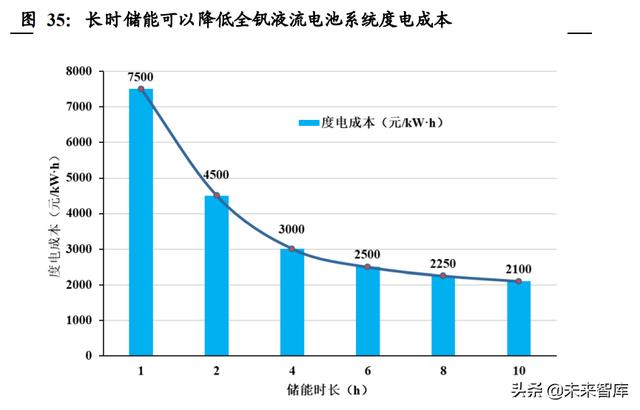
(2)商业模式是产业化快车道:上下游一体化,电解液金融化
纵向一体化
回顾锂离子电池产业的发展,很多锂电龙头都运用了纵向一体化模式, 例如宁德时代采用收购及签署战略性长期协议的方式,与上游矿产企业 绑定,稳定了锂、钴等正极材料必需金属的供应。买入原料后,由前躯 体厂商代工生产三元前躯体,保障原材料供应以及压低原料成本。同时 为降低原材料供应风险,成立合资公司用于研发生产碳酸锂、氢氧化锂 以及三元、磷酸铁锂等正极材料。纵向一体化在锂离子电池产业的成功 运用,对于全钒液流电池产业具有重要的借鉴意义,供应链的专门化不 仅能有效降低采购成本,减轻钒价格波动影响,还能显著提升生产效率。 尤其是开发设计电解液、电堆、配套辅助材料和控制系统等环节,通过 专门化原料供应、工艺设备和生产经验的积累,能提高并稳定产品的良 率,进而建立标准化生产工艺,产生规模效应。目前,已有部分钒电池 企业与上游钒材料企业进行了战略合作,典型的如大连融科与攀钢钒钛。
(3)政策指令是最强的催化剂:大规模储能,安全是底线
政策鼓励液流电池等电化学储能技术发展。随着国家“双碳”目标确立, 能源结构调整加快,新能源发电的装机量不断增加,与之相应的储能需 求也日渐攀升。根据国家发改委、能源局《关于加快推动新型储能发展 的指导意见》,2025 年我国新型储能装机规模将达到 30GW 以上,储能 装机需求将快速增长。目前,很多地方政府都对新增的新能源发电项目 做了配储比例的要求。相比于抽水蓄能,电化学储能电站建造周期短, 而且没有地理条件限制,其渗透率逐渐提升。同时,政府也出台了一系 列的政策,鼓励发展新型储能技术。2022 年 2 月,国家发改委和国家能 源局联合发布《“十四五”新型储能发展实施方案》,将百兆瓦级液流电 池技术纳入“十四五”新型储能核心技术装备攻关重点方向之一。6 月, 两部门又联合发布《关于进一步推动新型储能参与电力市场和调度运用 的通知》,明确了新型储能作为独立储能的市场地位。这些政策的出台 对电化学储能产业具有重要促进作用。
(本文仅供参考,不代表我们的任何投资建议。如需使用相关信息,请参阅报告原文。)
精选报告来源:【未来智库】。未来智库 - 官方网站
相关参考
氟橡胶流动分散剂(全钒液流电池行业专题报告:沿流溯源,超“钒”脱俗)
...品方/作者:国泰君安证券,庞钧文、石岩)1.技术详解:全钒液流电池的前世今生随着“碳达峰,碳中和”目标提出,我国能源结构调整加快,新能源对传统化石能源的逐步替代将是历史必然。我国幅员辽阔,拥有丰富的太阳能...
水溶液钛酸钾电池(全钒液流电池行业研究报告:钒电池长时储能空间广阔)
(报告出品方/作者:光大证券,王招华、方驭涛)1、钒电池优点:安全性高、全生命周期成本低、资源自主可控1.1、安全性高、易扩容是最大优点全钒液流电池,是一种以金属钒离子为活性物质的液态氧化还原可再生电池。全...
承德耐磨自蔓延(全钒液流电池行业研究报告:钒电池长时储能空间广阔)
...成本低、资源自主可控1.1、安全性高、易扩容是最大优点全钒液流电池,是一种以金属钒离子为活性物质的液态氧化还原可再生电池。全钒液流电池是以+4、+5价态的钒离子溶液作为正极的活性物质,以+2、+3价态的钒离子溶液作...
日池9九速飞轮(全钒液流电池行业研究报告:钒电池长时储能空间广阔)
...成本低、资源自主可控1.1、安全性高、易扩容是最大优点全钒液流电池,是一种以金属钒离子为活性物质的液态氧化还原可再生电池。全钒液流电池是以+4、+5价态的钒离子溶液作为正极的活性物质,以+2、+3价态的钒离子溶液作...
液态锂离子蓄电池(锂离子电池和液流电池的工作原理以及优缺点对比)
...,占地多安全性易燃易爆,有机溶剂电解液无燃爆风险,水溶液电解液放电时长1-4小时,功率与储量比例固定,>4小时越长越贵4-12小时,功率与储量可
液态锂离子蓄电池(锂离子电池和液流电池的工作原理以及优缺点对比)
...,占地多安全性易燃易爆,有机溶剂电解液无燃爆风险,水溶液电解液放电时长1-4小时,功率与储量比例固定,>4小时越长越贵4-12小时,功率与储量可
熔盐发电于光伏发电比较(中国首家,HJT+钙钛矿幕墙发电+熔盐储热+液流储电”示范项目)
...国际领先地位,拥有最多的中试和量产线业绩。也参股了全钒液流电池公司德海艾科,公司自身也在积极拓展熔盐储能业务的多场景应用,谢谢。近
熔盐发电于光伏发电比较(中国首家,HJT+钙钛矿幕墙发电+熔盐储热+液流储电”示范项目)
...国际领先地位,拥有最多的中试和量产线业绩。也参股了全钒液流电池公司德海艾科,公司自身也在积极拓展熔盐储能业务的多场景应用,谢谢。近
清大电池(燃料电池行业专题报告:重卡、叉车引领未来燃料电池市场)
获取报告请登录未来智库www.vzkoo.com。1、全球进入燃料电池汽车加速布局阶段,我国以商用车为主1.1燃料电池汽车是燃料电池的主要应用早在20世纪60年代,燃料电池就已成功应用于航天飞行领域,后期随着燃料电池技术水平的提...
清大电池(燃料电池行业专题报告:重卡、叉车引领未来燃料电池市场)
获取报告请登录未来智库www.vzkoo.com。1、全球进入燃料电池汽车加速布局阶段,我国以商用车为主1.1燃料电池汽车是燃料电池的主要应用早在20世纪60年代,燃料电池就已成功应用于航天飞行领域,后期随着燃料电池技术水平的提...