水性胶水固化剂(固化剂用量对水性环氧涂料性能的影响)
Posted
篇首语:孤独如影随形,我们不能杀死他,只能与他和解。本文由小常识网(cha138.com)小编为大家整理,主要介绍了水性胶水固化剂(固化剂用量对水性环氧涂料性能的影响)相关的知识,希望对你有一定的参考价值。
水性胶水固化剂(固化剂用量对水性环氧涂料性能的影响)
摘要:水性环氧涂料不仅具有良好的防腐性能,而且符合环保要求,可以用于工程机械涂装。由于水性环氧乳液是一个多相体系,其涂料的固化过程与溶剂型环氧涂料有所区别,特别是环氧固化剂的用量对涂膜的性能有较大影响。本文通过对不同比例的水性环氧乳液和固化剂进行研究,采用红外光谱、涂膜硬度、吸水率、耐中性盐雾试验以及电化学交流阻抗谱进行分析与表征,结果表明m(环氧乳液)∶m(固化剂)=4.5∶1时,涂料的综合性能最优。
溶剂型涂料和水性涂料不仅在溶剂的选择上有着本质的区别,在成膜过程及机理等方面也存在较大的差异。环氧乳液和固化剂分别是双组分环氧涂料的A、B组分,溶剂型环氧涂料为均相体系,随着溶剂的挥发,两组分逐渐发生交联作用,而水性环氧涂料为多相体系,一般环氧树脂以分散相的形式分散在水相中,水性环氧固化剂则溶解在水中,固化成膜过程包括水分的蒸发、乳液粒子的聚集、变形以及与固化剂相互作用形成三维空间网状结构,最终表现出较强的抗渗透性。
理论上来讲,环氧树脂的固化是一个活化氢分子与一个环氧分子作用,形成完整的三维空间结构,但是水性环氧涂料固化交联过程是以固化剂为中心,逐渐向环氧树脂微粒内部扩散,固化剂分子首先与环氧树脂分散相粒子的表面接触并发生交联固化反应,随着固化反应的进行,粒子表面的环氧树脂相对分子质量和玻璃化温度均逐渐提高,使得固化剂分子向粒子内部的扩散速度逐渐变慢,这就意味着环氧树脂分散相粒子内部进行的固化反应较其表面少,导致内部交联密度低,最终并非所有的环氧基都有机会与固化剂的活化基团作用。因此,在实际应用中需要研究水性环氧乳液与固化剂的比例对涂层性能的影响,找出最佳配比。
1·实验部分
1.1 双组分水性环氧涂料的制备
A组分的配方如表1所示。
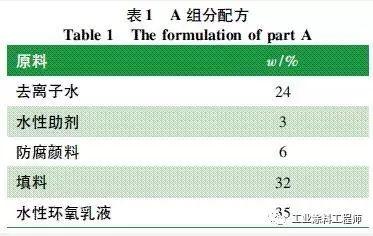
添加去离子水及部分助剂,搅拌15min左右;添加防腐颜料及填料,搅拌30~60min;添加水性环氧乳液及部分助剂,搅拌30min左右,制得A组分。水性环氧乳液和固化剂的技术指标分别如表2、表3所示。
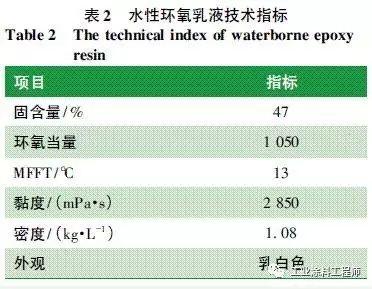
表2 水性环氧乳液技术指标
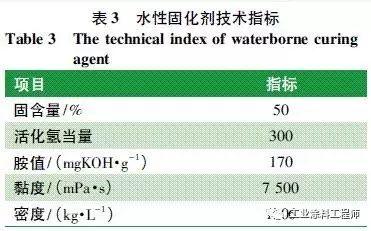
表3 水性固化剂技术指标
1.2 样品制备
环氧乳液与固化剂的比例和样品编号的对应关系如表4所示。
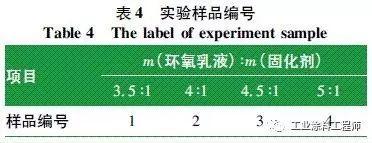
(1)红外光谱测试样品制备:直接用环氧乳液与固化剂按照表4比例制备样品,搅拌均匀后,放置15~20min进行熟化,然后在氯化钠晶片上涂上薄薄的一层,固化完成后放在干燥器内干燥24h以上待用。
(2)涂层性能及电化学测试样品制备:用环氧乳液与固化剂按表4比例制备样品,放置15~20min进行熟化,然后按照GB/T1727—1992《漆膜一般制备法》进行制板,放置7d后待用。
1.3 性能测试
(1)红外光谱测试:将制备好的样品进行红外光谱测试,红外光谱分析仪型号为:NEXUS470。
(2)涂层性能测试:分别按照GB/T1730—2007《色漆和清漆摆杆阻尼试验》、HG/T3344—2012《漆膜吸水率测定法》、GB/T1733—1993《漆膜耐水性测定法》、GB/T1771—2007《色漆和清漆耐中性盐雾性能的测试》进行涂膜硬度、吸水率、耐水性及耐中性盐雾测试。
(3)电化学交流阻抗谱测试:将制好的试板浸泡于3.5%的NaCl水溶液中,浸泡30min后进行第一次交流阻抗测试,之后每隔一段时间进行一次测试(浸泡初期测试时间间隔较短,随着浸泡时间的增加,测试时间间隔可适当延长),辅助电极为铂电极,参比电极为甘汞电极,扫描频率范围为105~10-2Hz,施加在工作电极上的扰动电压为10mV,试验面积为19.6cm2。
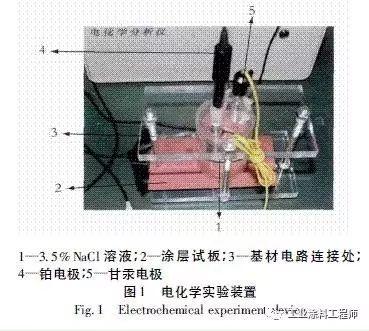
图1 电化学实验装置
2·结果与讨论
2.1 红外光谱分析
4种固化膜的红外光谱如图2所示。
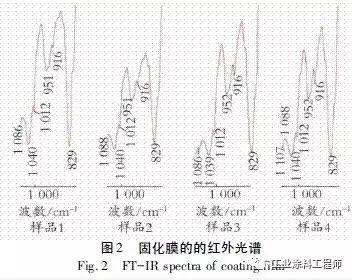
图2 固化膜的红外光谱
图2分别为4种样品固化产物的红外光谱在916cm-1处为环氧特征峰,此峰的强弱直接反映了固化反应进行的程度。水性环氧涂料随着固化剂用量的增加,树脂固化后的环氧红外峰逐渐减弱,水性环氧树脂固化更完全。
根据表2和表3提供的参数进行计算,水性环氧乳液与固化剂理论上(1个活化氢分子与1个环氧分子作用)的比例为3.7∶1,但是由图2可看出,对于水性环氧乳液即使在固化剂过量的情况下,树脂固化后仍存在环氧峰,这说明并非所有的环氧树脂都能参与固化交联反应。因此对于水性环氧乳液而言,环氧树脂很难完全参与固化反应,这是由它的成膜机理决定的。
2.2 涂层硬度的影响
4种样品涂膜的硬度如图3所示。
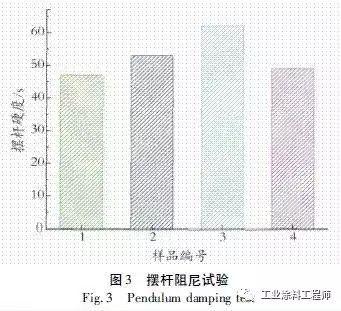
图3 摆杆阻尼试验
由图3可以看出,涂膜摆杆硬度随固化剂用量的减少先增加后减小,即固化剂过多或过少时都会降低涂膜硬度,为确保涂膜硬度较为理想,需一个合适的固化剂用量。当固化剂用量过多时,固化交联反应结束后会有固化剂剩余,而剩余的固化剂分子在涂层中相当于增塑剂的作用,会降低涂膜硬度,随着固化剂用量的减少,固化交联后剩余固化剂的量减少,增塑作用减弱,涂膜硬度增加。当固化剂用量过少时,因固化剂不足导致涂层交联密度较低,涂膜硬度又有所降低,因此,合适的固化剂用量为涂膜硬度提供了一个保证。
2.3 涂层吸水率和耐水性的影响
涂膜的吸水率和耐水性对涂层的防腐性能有很大影响,涂层的吸水率越大,耐水性越差,防腐性能越差。4种样品涂膜的吸水率如图4所示。
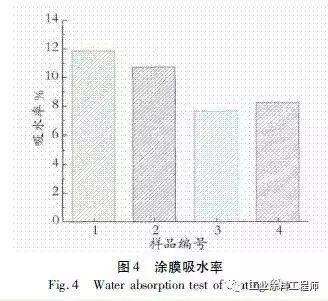
图4 涂膜吸水率
由图4可以看出,涂膜吸水率随着固剂化用量的减少,先减小后增大。当固化剂用量过大时,固化后的涂层中有剩余的固化剂,水性环氧涂料所使用的固化剂具有很强的亲水性,涂膜吸水率较大,随着固化剂用量的减少,吸水率降低。但当固化剂用量过少时,本可以发生交联固化的环氧基团未能发生交联反应,导致树脂交联密度下降,涂层的致密性不够,吸水率增加。当m(环氧乳液)∶m(固化剂)=4.5∶1时,涂膜吸水率相对最低,在此比例下水性环氧涂料中的环氧树脂和固化剂能够最大程度地交联固化,并且剩余的亲水性固化剂也控制在一定程度,吸水率最低。涂膜耐水性测试结果如表5所示。
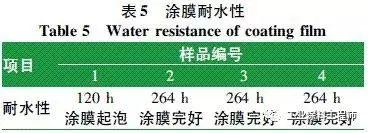
由表5可以看出,当固化剂用量过多时,涂膜耐水性较差,在浸泡120h的时候,涂膜表面呈现较为密集的小泡,这说明涂层中剩余的未参加固化反应的固化剂对耐水性影响比较大。其他比例下,涂膜耐水时间均超过了264h,能够满足一般工业涂料的耐水性要求。
2.4 涂层耐中性盐雾的影响
涂层耐中性盐雾试验结果如表6和图5所示。
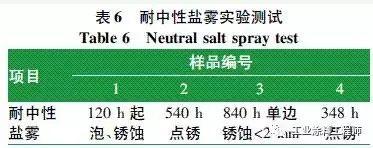
表6 耐中性盐雾实验测试
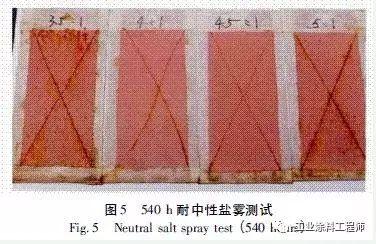
图5 540h耐中性盐雾测试
由表6及图5可以看出,当固化剂用量不同时,耐盐雾时间和现象有所不同,随着固化剂用量的增大,耐盐雾时间先增加再减小。当固化剂的用量较少时,本可以发生交联反应的环氧基团因固化剂用量不足而未能参与反应,涂层交联密度低,水汽容易渗透至涂层底部,耐中性盐雾时间较短,试板会较早出现一些锈蚀点。当固化剂值用量过多时,涂层交联固化后会有部分剩余的固化剂,固化剂具有较强的亲水性,为水汽渗入涂层内部提供的通道,因此耐中性盐雾时间较短,板面也会较早出现一些气泡和锈蚀点。当m(环氧乳液)∶m(固化剂)=4.5∶1时,耐中性盐雾时间最长,且板面无起泡、锈点等现象。
2.5 电化学交流阻抗谱
图6是不同固化剂用量下,试板在3.5%的NaCl水溶液中浸泡30d后的波特图。
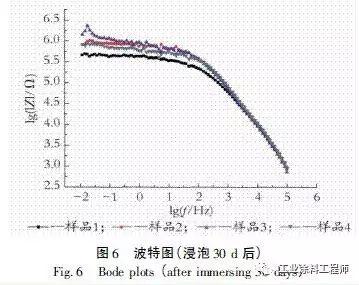
图6 波特图
由图6可以看出,在不同频率下,交流阻抗值的变化规律基本为一条平滑的曲线,且从高频到低频,交流阻抗值先迅速增大,后平缓增加直至基本平稳,其中样品3交流阻抗最高,样品1交流阻抗最低。当固化剂用量适当时,水性环氧树脂的交联密度达到一定程度,并且过剩的固化剂最少,这时交流阻抗值最高;当固化剂用量较多时,涂层中剩余大量的固化剂,亲水性的固化剂会导致交流阻抗值大大降低。
图7是不同固化剂用量下,|Z|0.01(频率为0.01Hz时的交流阻抗值)随时间变化曲线。
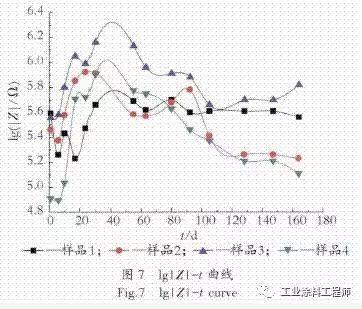
图7 曲线
由图7可以看出,随浸泡时间的增加,|Z|0.01的基本变化趋势为先略微降低,再升高,又降低。在试板浸泡初期,由于涂层的微孔为盐水渗入内部提供了输送管道,盐水通过这些管道慢慢向涂层内部渗透,导致|Z|0.01稍微降低。随着浸泡时间的增加,防腐颜料开始发挥其钝化作用,在涂层与钢材的界面形成钝化层,|Z|0.01开始增加。随着浸泡时间的进一步增加,腐蚀进一步扩展,逐渐破坏钝化层,导致|Z|0.01降低。
对比不同固化剂用量下的|Z|0.01随时间变化曲线,可以看出在浸泡初期,样品1的|Z|0.01降幅最大,即当固化剂过量最多时,由于固化剂的强亲水性,促进了盐水向涂层内部渗透。另外在浸泡初期,样品4的|Z|0.01值较低,即当固化剂用量较少时,涂层平均交联密度较低,抗渗透能力低。纵观图7,样品3在整个浸泡过程中|Z|0.01相对于其他样品一直处于最高值,这也进一步说明当m(环氧乳液)∶m(固化剂)=4.5∶1的情况下,耐腐蚀性能最优。
图8为m(环氧乳液)∶m(固化剂)=4.5∶1时,不同浸泡时间下的奈奎斯特图。
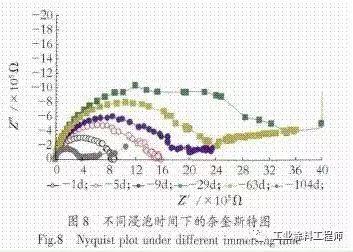
图8 不同浸泡时间下的奈奎斯特图
由图8可以看出,浸泡时间分别为1d和5d时,Nyquist图为一个半圆,随着浸泡时间的增加,Nyquist图上开始出现2个半圆的趋势,且高频端半径[11]随浸泡时间的增加先增加后减小。这是因为当浸泡时间在5d以内时,电化学腐蚀现象尚未发生,因此,Nyquist图为一个半圆,即一个时间常数,但是由于盐水迅速渗入涂层内部,交流阻抗降低,导致Nyquist图高频端半径较小。随着浸泡时间的增加,均开始出现两个时间常数,即微观电化学腐蚀已经开始发生。由于防腐颜料的钝化作用,形成致密的钝化层,导致交流阻抗增加,Nyquist图高频端半径开始增大。随着浸泡时间的进一步增加,钝化层遭到破坏,曲线直径开始变小。
3·结语
红外光谱证明即使在固化剂过量的情况下,水性环氧的固化产物中仍有环氧基团存在。通过对涂膜硬度、耐中性盐雾和电化学交流阻抗谱分析,水性环氧涂料在固化剂不过量的情况下涂膜的性能随固化剂的用量增大而提高,在固化剂过量的情况下涂膜的性能随着固化剂用量的增大而下降,当m(环氧乳液)∶m(固化剂)=4.5∶1时涂膜各项性能最优。
注:文章转自工业涂料工程师,版权归原作者所有。
相关参考