氯化锡是什么晶体(ITO靶材的国产化漫谈)
Posted
篇首语:有上不去的天,没过不去的关。本文由小常识网(cha138.com)小编为大家整理,主要介绍了氯化锡是什么晶体(ITO靶材的国产化漫谈)相关的知识,希望对你有一定的参考价值。
氯化锡是什么晶体(ITO靶材的国产化漫谈)
一、 写在前面的话 1
二、 ITO靶材是啥东西 1
三、 ITO靶材是怎么做出来的 3
四、 ITO靶材国产化的大致历程 5
五、 ITO靶材国产化的商业、技术难点 10
一、 写在前面的话
2020年以来,特总一番如狼似虎,不顾颜面和规则的操作,各种极端手段封杀华为,让国人知道了世事险恶。缺乏自己的核心技术,碰上一个疯子,随时都有可能被扼住咽喉。
在显示行业中,有一种材料-ITO靶材,虽然经过了二十多年的国产化发展历程,但是国内产品仍然徘徊在中低端市场,艰难前行。而这个材料却是显示行业产业链的重要一环,主要原料大多数产自中国,高端产品却极大依赖日韩美。
笔者老壶,从事ITO靶材的相关行业工作多年,对ITO靶材的国产化历程、制造技术和市场略有了解,下面就说说相关的故事。
鉴于偏居一隅,信息有限,道听途说,主观臆断,文中对于整个行业的描述或有偏颇之处,时间可能模糊,人事难免偏差,数据资料全凭印象和网搜,技术细节仅是一家之言。我姑且记之,大家姑且读之,算是初级科普。本文立意,是想让广罗大众知道,ITO靶材这东西,很重要,有难度,如何来,如何用。欢迎批评,欢迎指正。有业内人士如能提供相应的更好的资料,我会酌情适时增补到文中,谢谢。
二、 ITO靶材是啥东西
ITO,是指铟锡氧化物,英文简写来源于Indium Tin Oxides,字面意思,铟锡氧的元素英文名称。
纳米ITO膜,是一种N型半导体,具有独特的既透明,又导电的特性,还能有选择的阻断一部分电子辐射、紫外线、远红外线等。
具有既透明又导电特性的材料,不止ITO一种,还有氧化锌、氧化锌铝、等,以及有可能成为下一代潮流的纳米银线等等。但是,各种材料,便宜的可能透光性差,透光性好的可能电阻率高,电阻率低的呢可能工艺难度大。综合透光率、电阻率、成本、工艺难度等因素,遂使ITO成为目前的最佳选择。
需要在各种基材,如玻璃、晶圆、塑料薄膜上形成纳米尺度的一层ITO薄膜,可以用不同的方法。低要求低成本的,可以用真空电子束蒸镀;高要求的可以用磁控溅射。这些算是物理气相沉积PVD的一种。
电子束真空蒸镀,就是在真空腔里,用电子束把ITO靶材颗粒料加热升华,然后冷凝沉积到基材上。
磁控溅射,大致就是,把ITO靶材和基材面对面摆好,接上正负电场,在氩气氛低气压下,形成的等离子体在磁场和电场控制之下,就像打靶一样轰击靶材表面,把靶材表面的物质溅射出来,沉积到对面的基材上,从而形成一层薄膜。因而得名”靶材”,英文Target。靶材还包括其他的各种高纯金属靶材、其他氧化物靶材等,如金靶、铜靶、钽靶、氧化铌、氧化锌、铜铟镓硒等等,磁控溅射形成的膜层各有功用。
ITO膜可以用在建筑玻璃、冰柜玻璃、光学视窗上,隔绝紫外线;可以用在液晶显示、OLED显示、太阳能电池板、半导体等上面用作透明电极。
而ITO靶材,就是用粉末冶金或者说类似于烧制陶瓷的方法,把ITO粉末通过成型、烧结、机加工等流程,制备成一块块规整的,黑乎乎的陶瓷板,放在磁控溅射设备里,在悲壮的生命历程中,不断地被轰击、剥离、变薄、破裂,在新的载体上走入千家万户。
先来张ITO靶材的图:
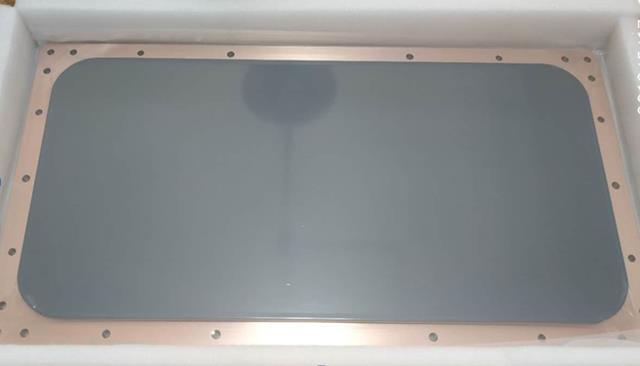
图一:ITO靶材。已经经过后处理,绑定在铜背板上,整块一体,尺寸约500*380mm。
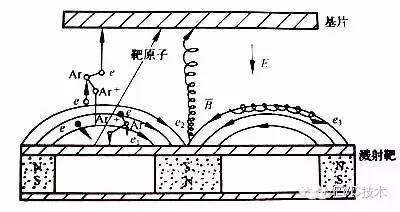
图二:磁控溅射原理
三、 ITO靶材是怎么做出来的
ITO的生产制备的工艺流程比较长,其间的每一个步骤的工艺参数和性能指标,都可能对后续的工艺过程,直至最终的靶材的磁控溅射镀膜性能,造成影响。也因此,需要考虑各个过程的N个影响因素的优化,叠加而来的诸多变化,要制备出优质的靶材,殊为不易。
比较主流的制备工艺流程如下:

图三:ITO靶材制备工艺流程
四、 ITO靶材国产化的大致历程
中国拥有世界上最丰富的的铟金属资源,现在的铟金属产量大约占世界总产量的70%,包括原生资源和再生资源。倒过来的是,国内的ITO靶材80%依赖进口,国产靶材目前仅在中低端应用市场占有一定的份额。
铟金属,属于稀散金属之一,字面意思,既稀少又分散,地壳丰度低,没有独立成矿,伴生在锌、铅、锡等矿藏中。同类的包括镓(Ga)、铟(In)、铊(Tl)、锗(Ge)、硒(Se)、碲(Te)和铼(Re)7个元素。
铟金属有不少特性,熔点157℃,放水里是熔不了的,放油锅里就能化了。
黏糊,用小刀切的话,能在刀面上糊一层,不太切得动,用来扒拉玻璃、陶瓷等,也能糊上一层,所以可以用来粘接金属与玻璃。
锡鸣,把一条铟块反复弯折,会发出嘎吱嘎吱的声音,这点,据说锡金属也一样,不过我没折腾过锡,倒是觉得折腾铟条的声音还挺有趣的。
低熔点高沸点,沸点大概两千出头,蒸气压也低。通常的铟都是4N的,也就是99.99%,要做6N(99.9999%)的铟,需要利用这一特性,对铟金属进行真空熔炼,可以把里面的蒸气压高的金属杂质除掉。以前还做过6N铟的研究,什么电解精炼、真空熔炼、区域熔炼、直拉除杂等等都尝试过。
在很久很久以前,人类还没有发明液晶显示、OLED等技术之前,用不着透明电极,所以那时候铟的用途也少,基本就是低熔点合金用来做焊丝、做消防熔断器,用来做玻璃/金属粘接剂,用来做高速轴承的润滑剂,用来做半导体磷化铟等等。像现在,有些航空航天用的光学玻璃器件的粘接,就是使用的铟丝。
中国能成为铟资源大国,那是天赋异禀。大致是在广西、湖南以及内蒙古等地的铅锌矿中,相对的富含有铟金属。以前的铅锌矿中的铟是不计入矿藏价值的,含铟的国产矿与不含铟的澳洲矿,都根据锌含量计价。后来铟金属值钱了,含铟高的锌矿就更值钱些了。
在铟的大规模应用前,湿法的铅锌矿冶炼,有一种黄铁矾法,把矿石中的锌浸取出来,剩下的矿泥渣都是废弃物,占地、扬尘、污染环境,该有的坏处都有了。后来发现,铟值钱了,而黄铁矾法把矿石中的铟都富集到矿渣中了,并且研究出了矿渣提铟的技术,突然间,漫山遍野的矿渣就变成了宝贝了。废物不一定真是废物,只是没有放到合适的位置。
其他的火法冶炼等,也能在某一工艺阶段的产物中富集铟金属。大致是,铟金属在铅锌锡矿中含量是万分之几,富集在矿渣中,可以达到千分之几,然后再用还原焙烧的的方法收集烟气粉尘,富集到百分之几,再用浸出、萃取、置换还原、电解精炼的方法得到4N的精铟。
这里另外提一下,铟金属的价格波动,也算得上是波澜壮阔的。老壶对各个时间节点的铟价,还有挺深的印象,就不查资料了。大约在02年时,铟价从一千多下跌,最便宜的时候,低到500元/公斤,老祖宗留下来的东西卖了个成本价。后面铟价一路暴涨,06年的时候,最高曾达到6000元/公斤.09年的时候,买过2500元/公斤的。后来云南泛亚囤积铟锭,买过4200元/公斤的。去年19年,买过1150元的,买过1450元的。散了散了,想炒铟锭发财的都是憨憨,多费劲,炒股的是大个憨憨,这二十多年,投机啥都不如买房买地,能贷款融资,能收房租补贴。所以,我一路以来,特别敬佩在ITO靶材行业投资的大老板,肯投资实业的,真有家国情怀的。
国内的ITO靶材的研发,大致始于上世纪90年代,掐指一算,也有二十多年了,按照目前的市场状况,算是进展缓慢,步履艰难,对不起党国。这里面有技术的原因,有商业竞争的原因,有资金投入和政府重视的原因,后文中会略说一二。不管何种借口,目前只能占领农村,半包围城市,赚着卖白菜的钱,吃着高价的泡菜,国内的攻城狮们还需要加油。
最早呢,国内产业化的ITO靶材,大致是在2000年之后,山东的一家企业用真空热压法做出来的,业内的人估计知道这个历史的不少。
前一节中描述的工艺流程中,没有提到这个真空热压法,已经被淘汰了。就是把ITO粉末放入石墨模具中,在真空热压炉里,升温到1500℃左右,同时在模具上加上大约10Mpa的压强。这个方法做出来的靶材,相对密度低,尺寸小,产量低,成本高,只能算是解决了有无的问题。老壶之前在的企业,正好也有真空热压炉,也做过实验,做出来的ITO靶材尺寸大约是120~150mm见方,相对密度96%左右。
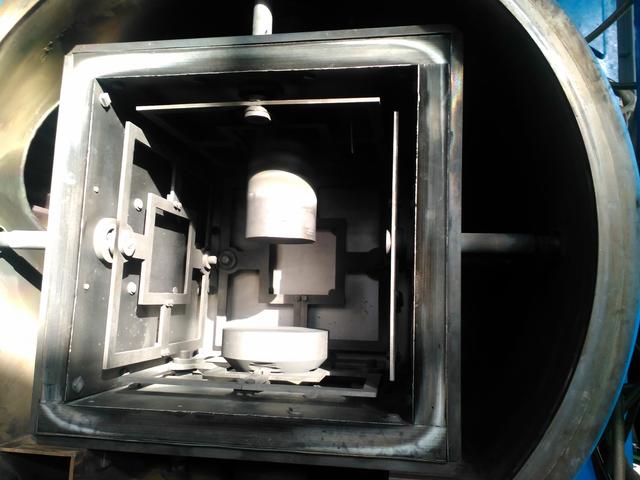
图四:真空热压炉的炉膛
这里提一下,90::10的ITO靶材,理论密度是7.15,实际密度除以理论密度就是相对密度,越高越好,很重要的指标,对应用性能影响很大。现在ITO靶材的密度不做到99.5%以上都不好意思出门说。
当时国内就知道ITO靶材很重要,研究ITO靶材的院所、公司也很多,投入很大的也不少,很多都死在路上了。大约在05年的时候,广东一家企业,名字很洋气的,用了一种新的方法,高压氧气氛烧结。把ITO粉末用模具压成薄型的坯料,这个压强大约是15Mpa;再放入冷等静压机里进一步压缩致密,这个压强大约是250MPa;然后脱胶,放入高压氧气氛烧结炉里烧结,得到ITO靶材烧结坯,氧压大致是0.5Mpa。
这里题外说一下冷等静压机,一个耐高压的筒体,用预应力钢丝缠绕,能升压到200Mpa以上。使用时,筒体里充满液体,素坯用乳胶袋包好放入,素坯的各个方向都承受相等的压力,故名之等静压。对应的还有更高端的热等静压,还要加热到1000℃以上。1Mpa压强呢,大约等于100米水深,200Mpa就相当于20000米水深了,压强比马里亚纳海沟的最深处还要高。当时流传着这么一个传说,200Mpa之下,常见的微生物、寄生虫等等生命,无不齑粉乎。所以,如果把牛肉生、鱼生等等,用冷等静压机压一下再食用,想想,原汁原味,鲜活色美,而无卫生之忧,真的很完美呀。可惜的是,有条件去做,却一直没有实践一下。有哪位做餐饮行业的,如果想创新出一条美食之路,可以一起讨论一下,说不定网红、潮流都是有可能的。 说到乳胶袋,嗯哼,有一段时间做小样品,就让车间的师傅去买了好几次大家最常见的生活用小型的乳胶的袋型产品,以至于药店的人看着师傅说,用量挺大的呀,秒懂的老司机可以去面壁三分钟了。
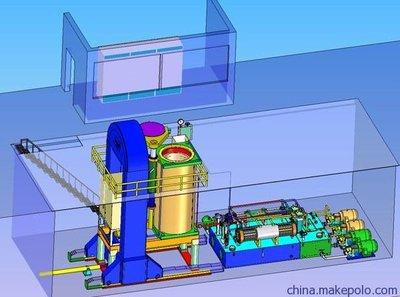
图五:冷等静压机的模样
高压氧气氛烧结比热压法要好多了,产品尺寸容易放大,产量大,成本较低,靶材密度高,工艺调整好了,能烧出99.5%以上的靶材。缺点是设备复杂,需要密封耐高压的,尺寸也受到限制,而且1500℃往上的温度,炉里都是高压纯氧,那是真心的害怕,胆颤心惊的过了不少年。每年的泄压安全阀都是准时准点去做年检的,最好不出事故,万一出了事故,责任轻点,也可以少坐几年牢不是。
这种方法,大约能做出500mm见方的靶材,尺寸大型化方面已经提升了一大步。国内有些年头的ITO靶材企业,基本都走过高压氧气氛烧结的技术发展阶段。
再后来,借鉴国外的技术,国内的企业开始尝试常压气氛烧结。特殊设计的非密闭常压,或者密闭的微压炉子,加热方式、气流组织,在不同的烧结工艺段通入空气、氩气、氧气等进行烧结。其中烧结炉的设计和气流的组织很重要,笔者借鉴韩国的炉子,对气流的组织方法做了大的改进和创新,效果还是很不错的,具有烧结炉设计和制造实力的业内企业,需要的话可以探讨一下。
目前,常压气氛烧结是国际、国内在烧结工艺段的主流。这种方法,因为不用考虑耐压容器的问题,炉子比较容易放大,能烧结出更大的靶材,每炉次的产能也可以更大,从大的方向来说,应该是烧结工艺的终极方法了。
国外现在用常压气氛烧结,能烧出长度大于2000mm的靶材了,国内目前的最大尺寸应该在1000mm左右,或者1300mm以内,这方面国内还有挺长一段路要走。尺寸的放大,不仅仅是一加一的问题,首先素坯的成型,就需要更大的模具,更大的压力机,更大的冷等静压机,更大的烧结炉,还有尺寸放大后工艺参数的变化,对烧结出来的靶材产品的性能的影响。后面会说一下另一种素坯成型的方法-注浆法,在成型工艺阶段,更有利于尺寸大型化。
这里说一下,ITO靶材的尺寸为什么要做这么大。大家经常能看到 国内的某知名龙头液晶显示企业某东方的新闻,在哪哪哪又建了一条4.5代线、8.5代线,世代越高,玻璃基板(或者柔性的塑料基材)的尺寸越大,相应的ITO靶材模组的尺寸也越大。本来呢,ITO靶材是绑定在铜背板上的,一小块一小块的拼凑出来也不是不行,可是拼缝越多,磁控溅射出来的基板的缺陷概率就越大。所以,最理想的是一块大的铜背板上,只有一块大的ITO靶材,没有拼缝。你想想,十多年前,家里铺地板砖,都用的300mm见方的瓷砖,现在都是800起步,1000的也很常见,道理是一样一样的。
回头说一下,素坯的成型方法。最古老的真空热压法,成型烧结是同时进行,没有这方面的 烦恼。模压、冷压成型,随着尺寸的放大,工艺和技术上的问题也多了起来。
比如说,我要做一块800*400mm的素坯,面积是3200CM2,按照30Mpa压强设计模压工艺,就需要1000吨的压力机了。而尺寸再放大,模具的的设计和加工也成了问题,整体成型的模具,尺寸一米多,就要找国内大型的机械加工企业了,再放大尺寸,就要考虑分体模具了。之前用过的冷等静压机,筒体内尺寸是φ800*1800,有效利用尺寸大概能有1200*500,已经是一个重型设备了,再放大估计难度不小。
而注浆成型法,则是把ITO粉体配置成浆料,通过注浆模具去掉水分,形成素坯。像我们日常中接触到马桶、卫生洁具,多是用注浆法成型的,陶瓷行业的人就比较熟悉了。之前对注浆法的研究,最大的做到了900mm,就技术难点而言与模压冷压的方法各有不同,再往上大型化的话,也还有需要技术突破的地方,总的来说比模压冷压法容易不少。
ITO靶材制备注浆法工艺,国内的研究应该是才起步,研究和应用的企业不多。这里,有注浆法本身工艺难度的问题,技术细节上与陶瓷工业上用的工艺有较大区别,也有紧迫性和必要性的问题。没有研发出大的烧结炉,也就用不着大的素坯,也就不着急琢磨注浆法,模压冷压工艺用熟了还能凑合。但是,注浆法不需要模压和冷压,今后的靶材尺寸大型化还是离不开注浆法的,业内企业应该未雨绸缪。
五、 ITO靶材国产化的商业、技术难点
前面不少地方都提到,ITO靶材的国产化,起步也不算晚,参与的企业,投入的资金也不算少,可是这么多年下来,国内企业还是受气小媳妇,拿不下高端市场,赚不了钱。这里面有商业上的原因,也有技术上的原因。
先说商业上的,主要有几个方面。
首先是ITO靶材的研发,原材料价格高,设备投入大。铟金属都是按公斤计的,和银子的价格差不多,目前大约2元/克,2000元/公斤,200万/吨,最贵的时候600万/吨。这里说个小故事,当年老壶开着一辆十万的小车,需要把ITO粉拉到距离二十多公里外的另一个厂区,最多的时候拉过200公斤,值个100万,比我连人带车都值钱,开的那是小心翼翼。而ITO靶材的研发,看了前面的内容也知道,技术工艺路线也是在进化的。尺寸越来越大,研发材料费用越来越高,设备买了一波,要不尺寸小了,要不性能不够了,要不技术方向变了,还要再买一波。如果不能尽快实现量产并且实现盈利,慢慢地失血,没有雄厚的背景支持是顶不住的。
其次是市场推广方面,从下游厂家的角度来说,ITO靶材的费用大概占到液晶面板成本的10%左右,与用日韩靶材相比,用国产靶材省不了几个钱,但是靶材质量不好,有可能成批次的产出面板产品都是残次品,风险比较大。所以高端面板企业对于国产靶材的引入非常慎重,周期很长,所以国内靶材企业只能在中低端市场挣扎,缺少试错的机会,缺少自我循环发展的环境。当然,最近美国对中国的疯狂的技术封锁,使得国内显示企业对关键材料的国产化和引入,有了更开放的心态,对国内靶材企业是一个长期利好。
还有,国外的靶材生产企业也在若有若无的对国内企业进行打压。比方说,国内的靶材企业,现在铟价1200左右,最终的靶材成品,我估算的成本要到2000元左右。可是呢,国外的高端大尺寸靶材,能在国内卖到3500元左右,生产过程中的边角碎料,根据尺寸大小不同,能卖到2000~2500元.那么国内的靶材,在中低端市场只能卖到1800~2200元,没有利润空间,没有良性循环,如果没有资金和政策支持,大多数只能挣扎着倒在前进的路上,坚持不到研发出高端产品的胜利日子。这种存在着技术和资金两道门槛的行业,存在着马太效应,赢者通吃。
另有一个很好的古老的栗子,当年的柯达胶卷,在国内只卖20元一个,在俄罗斯能卖50元一个,因为国内当时有乐凯,有公元。然后,胶卷行业都被数码相机干掉了。当然也有可能,以后ITO靶材行业,不管国内还是国外的,都被新的技术干掉了,比如什么纳米银线等等。
从技术方面来说,ITO靶材的工艺路线很长,里面的技术方向有很多分支,每一条道路,要去试错,都要付出代价。也许有国外技术可以借鉴,但是研发出来也需要时间和成本,有N多的工艺细节、参数、设备、工装需要去琢磨。
ITO靶材的性能和质量,通常用的可以数据化的表征的指标和手段,主要是尺寸、相对密度、电阻率、杂质含量。
尺寸,那是越大越好,从最早做出300*200mm的欣喜,到现在国内能做出1000mm左右的,也是在不断进步,但是和国外高端产品的1500mm以上相比还是差距很大。因为尺寸大型化,不仅仅是能做出大尺寸的素坯,在烧结过程中,越大的靶材越容易裂,平整度越难保证,均匀性越难保证,难度的增加不是直线型的,而是指数型的。
相对密度、电阻率和杂质含量这方面,国内的靶材都基本都能达到99.5%以上,1.3*10^-4Ω.cm左右,4N纯度,问题不大。
还有一些不常用的表征手段,比如XRD晶体分析、SEM晶粒分析、膨胀系数、机械强度等等,也经常用在研发过程中的工艺参数分析和选择。
不过,ITO靶材的质量好坏,上面说的都不算,只能作参考或者说是入门基础,很令人失望吧。就像公司HR招人,不是985的都扔一边去了,985的还要看各科成绩、获奖项目、社会实践,然后人招来了能不能干事还要另说。靶材好用不好用,还是要上产线,镀膜出来的生产效率、膜层均匀性、坏点数量、刻蚀性能等等,还有很重要的一项,中毒速度和程度。
这里说的靶材中毒,是行业内的一种通俗的说法。正常理解,靶材表面各处,被溅射消耗的速率应该是一致的,最终靶材应该越来越薄,直至穿透,靶材表面应该还是光滑而均匀的。
但是由于靶材内部的不均匀,存在杂质、颗粒、晶粒异常等原因,形成绝缘的孤岛。就像洪水冲刷之下,如果泥沙里有一块石头,就会逐渐被孤立出来。这些绝缘的孤岛有可能会越变越多,连成一片,影响溅射,引发电弧,造成镀膜缺陷。
所以,靶材的那些可以表征的数据再好,上了产线也可能中毒很厉害。而国产的靶材普遍比国外靶材中毒严重。
话说回来,溅射的性能与磁控溅射设备的参数调整也有很大关系,真空度、氧分压、氩分压、电压、电流、间距都要调试,吃惯了国外的粮草,再吃国内的粮草,总要有个适应过程,就是每一次适应的代价比较大,所以下游厂家也不乐意老换粮草。
行业内有一句话,我不怕你的靶材质量差,就怕你的靶材质量时好时差。质量性能不稳定,就算用在低端场景,也是很头疼的。
说到技术,靶材的整个工艺过程其实就是一个逐渐致密化的过程。从煅烧出来的ITO粉末开始,比表面积大约50,粒径大约200nm,振实密度大约1.9。然后经过模压,密度大约达到3.5,再经过冷压,密度大约达到4.2,注浆法的素坯密度可以达到4.4左右。最后在烧结阶段达到7.15左右,相对密度99.5%。如果能采取技术措施,越是在前面的工艺过程中提高密度,最后的烧结阶段,烧结融合的动力就越大,时间就越短,晶粒生长就越少,晶粒就更细一些,第二相的生成就能更少,磁控溅射的应用性能就有可能更好一些。
而要使晶粒直径更小,更均匀和一致,甚至要追溯到更早一些的工艺过程:共沉淀。在氯化铟锡溶液中加入氨水进行共沉淀,涉及到晶粒形成的粒径、粒径一致性、团聚性等,需要调整的参数有溶液浓度、溶液温度、氨水浓度、滴加速率、搅拌速度、反应时间、陈化时间等等。仅仅这些参数的优化选择,就算按正交试验的方法来设计,都要做很多实验,而且这还只是在ITO粉体阶段,用比表面、粒度分布、振实密度等数据来表征,更麻烦的是还要往后做,从成型到烧结到溅射,这些最前面的参数都有可能影响。所以通常只能实验一部分参数范围,差不多了就固定下来,往后做。这就有点碰运气了,好在科学发展史上也不缺乏因为运气好的才取得成功的,做的人多了,总会有那么一两个逮到老鼠的,自我安慰一下。
再往下,沉淀后的浆料的清洗,因为引入了氯离子,要把它尽量清除掉,需要反复的洗涤。洗涤的工艺方法也有很多种选择,从自然沉降过滤到板框压滤机,到陶瓷膜清洗机。洗的次数少了,氯离子除不尽,洗的多了接近终点时,浆料就是一种胶体,如果自然静置,可能一周时间都还是混混沌沌的,大家可以参考一下生石灰洗成石灰膏,差不多类似的。
再往下,氢氧化铟锡粉体煅烧,时间和温度的选择,温度高了晶粒太大,温度低了晶粒太小,都会影响成型密度和烧结,影响溅射性能。而且如果用注浆法,对煅烧出来的ITO粉体的粒径和团聚的二次粒径有更高的要求,才能调制出合适的注浆浆料,需要进行二次煅烧。
再往下,如果是模压冷压路线,粉体需要造粒,加入粘接剂和表面活性剂,尽量在烧结前提高素坯的密度,这里面有很多技术细节需要雕琢。如果是注浆成型路线,模具的制造、浆料调制、注浆压力控制、坯料的转移、干燥,也有很多实验要做。
再往下,有了大尺寸的素坯,还造好了大型的烧结炉,素坯都是低强度很娇贵的,小心翼翼的装炉,烧结温度通常在1550℃到1600℃之间,从室温RT一路小心升温,调控气氛、压力、流量,这里需要实验的参数选择也很多,历经几十个小时,再慢慢的等待炉子降温,历经几十个小时。
大概做一炉烧结实验吧,需要5~10天,一台炉子一个月能做4~6次实验。打开炉子,怀着忐忑的心情,首先看烧结坯是完整的,还是破裂了。不幸的是,越是大尺寸的靶材,越容易破裂,而破裂原因还可能你一时半会根本就分析不出来,可能需要你倒腾到最前面的工艺进行优化。而且就算优化好的工艺参数,可能十次烧结实验里,有八次是正常的,就有那么一两次可能是破裂了,而且还是裂的稀碎,四仰八叉的,或者是严重变形、密度异常等等,还是找不到原因。
前面一切正常了,烧结坯出来还需要测试密度是否合格,电阻率是否合格,平整度是否合格。对大尺寸靶材而言,平整度也是非常重要的,靶材制造成本中的很大一部分就是平整度原因产生的。比如靶材的目标厚度是8mm,那么设计烧结坯厚度是10mm左右,两面各磨掉1mm就能出平整面。如果靶材不平整,可能需要设计烧结坯厚度到11mm,材料成本就增加了10%。越大的靶材,需要预留的磨削厚度就越大,造成的浪费就越大。
大尺寸靶材,还需要买大型的平面磨床,大型的电火花线切割机,大型的超声波清洗机,大型的绑定加热台,设备的投入也是直线上升,由量变到质变的过程。
我想,中国人的聪明才智,不输于世界上的任何国家任何人种。有了资金的支持,有了下游企业的试错机会,有了时间和经验的积淀,总有一天,国产的高端ITO靶材会市场化、白菜化,会占领国内市场,期望的就是这一天早点到来。望行业内的同仁们共勉之。
相关参考
溅射靶材为什么要绑定背靶呢?溅射靶材主要应用于电子信息行业,如集成电路、信息存储、液晶显示、激光存储器、电子控制器件等。也可用于玻璃镀膜、耐磨材料、耐高温腐蚀、高档装饰用品等行业领域。背靶bondIng指用焊...
溅射靶材为什么要绑定背靶呢?溅射靶材主要应用于电子信息行业,如集成电路、信息存储、液晶显示、激光存储器、电子控制器件等。也可用于玻璃镀膜、耐磨材料、耐高温腐蚀、高档装饰用品等行业领域。背靶bondIng指用焊...
氧化镍靶材(靶材行业深度研究报告:国产替代+技术革新,高端靶材需求强劲)
(报告出品方/作者:东方证券,刘洋)一、金属靶材为薄膜沉积核心材料,广泛用于平板显示器、半导体、光伏电池、记录媒体等领域(一)分类方式:按应用可分为半导体靶材、平板显示靶材、太阳能电池靶材、记录存储靶...
爱发科(靶材行业深度研究报告:国产替代+技术革新,高端靶材需求强劲)
(报告出品方/作者:东方证券,刘洋)一、金属靶材为薄膜沉积核心材料,广泛用于平板显示器、半导体、光伏电池、记录媒体等领域(一)分类方式:按应用可分为半导体靶材、平板显示靶材、太阳能电池靶材、记录存储靶...
爱发科(靶材行业深度研究报告:国产替代+技术革新,高端靶材需求强劲)
(报告出品方/作者:东方证券,刘洋)一、金属靶材为薄膜沉积核心材料,广泛用于平板显示器、半导体、光伏电池、记录媒体等领域(一)分类方式:按应用可分为半导体靶材、平板显示靶材、太阳能电池靶材、记录存储靶...
晶体管与场效应管(金属氧化物半导体场效应管(MOSFET)漫谈)
场效应管是一种被广泛地运用在模拟电路和数字电路中的晶体管。场效应管分为两种,一种是金属氧化物半导体场效应管即MOSFET,另一种为结型场效应管JFET。这一次我们将重点放在金属氧化物半导体场效应管上。MOSFET是上个世...
氧化铋靶材(东兴证券:引领变革 特斯拉国产化加速 关注产业链投资价值)
投资摘要特斯拉——汽车行业变革引领者,技术优势构成核心竞争力:全球新能源汽车销售量从2011年的5.1万辆增长至2018年的201.8万辆,7年时间销量增长近40倍。预计2022年全球新能源汽车销量将达到600万辆,相比2018年约增长2倍...
《AI先锋周刊》是—家关注人工智能学术研究、产业生态链、技术落地、边缘应用等维度的先锋电子新媒体。欢迎广大热爱AI的同道中人阅读、评论、转发、投稿,记得点击“关注”,随时获取全球AI最新讯息。来源:方正证券、...
...与整合,随后经过千人研发团队的钻研,将多项技术成功国产化。去年6月,汉能首批铜铟镓(CIG)靶材在MiaS
氟碳类(半导体材料行业深度研究:晶圆厂迎扩产潮,大国利剑国产替代前景)
...多样,广泛应用于晶圆制造和封装工艺半导体材料是制作晶体管、集成电路、电力电子器件、光电子器件的重要材料。按照工艺的不同,可分为晶圆制造材料和封装材料。其中,晶圆制造材料主要包括硅片、特种气体、掩膜版、...