模锻翻转吊钳(S90级船用曲拐挤压成形试生产研究)
Posted
篇首语:男儿欲遂平生志,五经勤向窗前读。本文由小常识网(cha138.com)小编为大家整理,主要介绍了模锻翻转吊钳(S90级船用曲拐挤压成形试生产研究)相关的知识,希望对你有一定的参考价值。
模锻翻转吊钳(S90级船用曲拐挤压成形试生产研究)
曲轴是机器传递动力与运动或运动方式转换的零件,广泛用于以内燃机为动力的机器。在大型船舶中曲轴被誉为“心脏”中的部件,承担船舶发动机动力的输出,是整个机械动力系统的推动源[1-3]。大型船舶的曲轴服役中既承担巨大的载荷,又工作于潮湿、酸性的环境中,因此,其物理性能要求高,如强度、刚度以及耐磨性等;曲轴在组织上也要求严格,必须内部缺陷数量少,纤维组织分布合理。此外还要求锻件的材料利用率高,以期达到良好的制造经济效益。
当曲轴的尺寸、质量比较大时,实现其整体制造有技术与经济两方面的困难。因此,当主轴颈超过300 mm后采用组合结构,由4种零件组合而成,即输入端、曲拐、主轴颈和输出端,其中曲拐是形状复杂、质量大、数量多和承载复杂的零件,图1所示为S90级曲轴和装配前的曲拐零件,曲轴质量为19.8×103 kg。
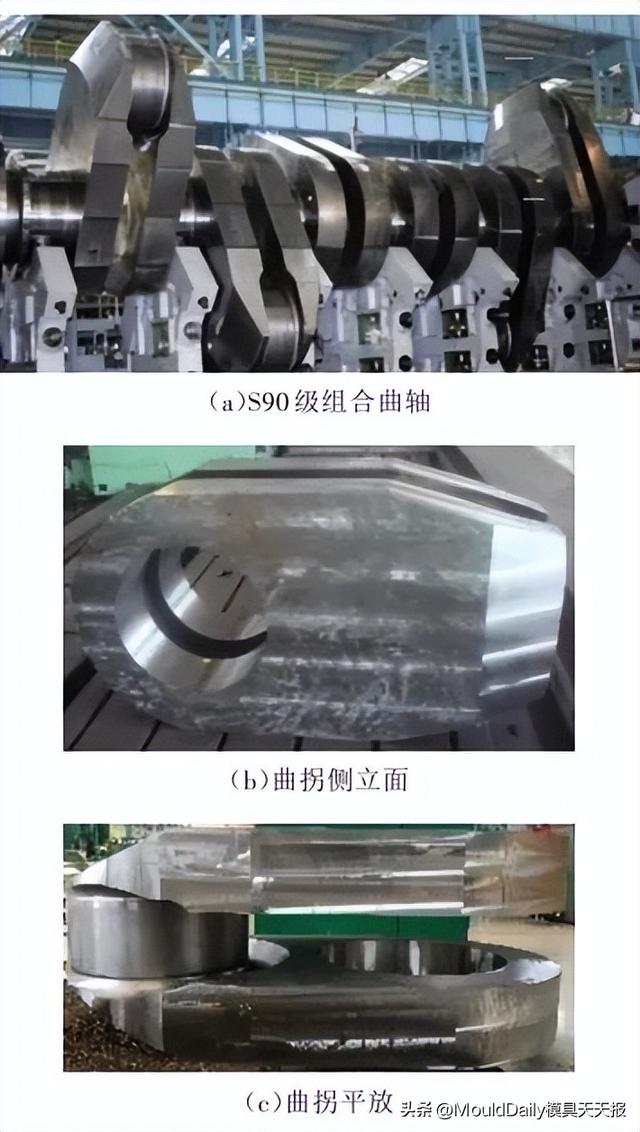
图1 S90级曲轴和装配前的曲拐零件
为保证大型船舶航行的安全性,曲拐采用冶炼铸锭、锻造制坯、切削加工和热处理的工艺进行生产,锻造起着改善铸锭组织、为切削加工提供良好形状的坯料、为热处理做好组织准备的作用,曲拐锻造工艺经历了如下发展过程。
(1)块锻法:根据曲拐的尺寸,将钢锭锻造成长方体状,然后按曲拐厚度分段切开,得到曲拐锻坯,如图2所示。其特点是锻造成形容易,不需要工装模具,锻造火次少,但金属纤维分布不合理,材料利用率低,后续加工量大,经济效益差,已被淘汰[4]。
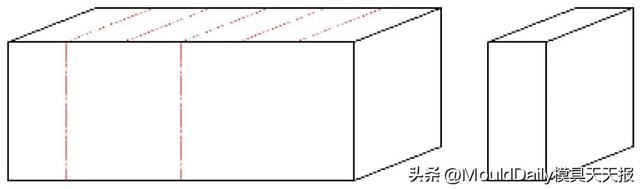
图2 曲拐块锻法
(2)环锻法:采用中空钢锭或冲孔的锻坯进行扩孔,再锻成扁方环,从中间切断成形为U型坯料,得到2个曲拐锻件,如图3所示。其特点是材料利用率能提高,减少了后续切削的工作量,金属纤维连续、分布合理,但锻件成形工序多且复杂,工装模具更换多,效率低,所以应用较少。
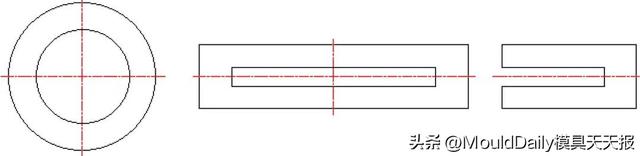
图3 曲拐环锻法
(a)冲 孔 (b)锻扁方环 (c)环切断
(3)弯锻法:其是目前国内外应用最多的方法,将钢锭锻成曲拐展开的形状,然后弯曲成形,压平修整得到锻件,如图4所示。其特点是金属纤维连续分布合理,工装模具简单,操作方便,成形容易,但在曲拐销处容易产生折叠、超宽、缺料等缺陷,且锻件材料利用率低,目前多用于小批量生产。
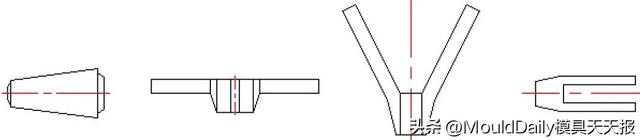
图4 曲拐弯锻法
(a)制 坯 (b)弯 曲 (c)压 平 (d)锻 件
(4)台模锻法:钢锭先锻成长方形截面的毛坯,然后放入浅凹模中成形曲拐颈端,再从上端沿对称面将坯料切开,放倒拔长两臂并精整,如图5所示。其主要缺点:①施压工序多,需采用3种凸模顺序施压,更换凸模频繁、时间长,降低了生产效率;②生产的锻件尺寸精度差,材料利用率低,后续加工量大,技术与经济效益较差。
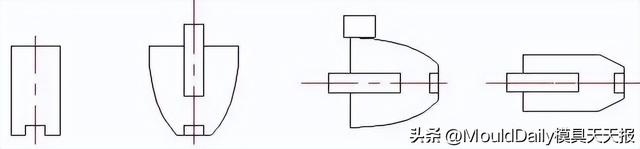
图5 曲拐台模锻法
(a)上、下两端压凹 (b)压曲拐颈端成形 (c)曲臂拔长 (d)曲臂精整
鉴于国内外曲拐锻造技术的不完善和机械制造业的生产与发展对其巨大的需求,现研究一种新的挤压技术生产曲拐。
曲拐挤压成形技术

01
曲拐锻造难点
组合曲轴用于大型船舶及其它大型机器,对其需求虽有一定的数量,但远少于用于普通车辆的小尺寸曲轴的数量。就大型船舶制造需求的组合曲轴,约需500~800根,相应曲拐的数量为4 000~ 6 000个,其曲拐的质量在10×103 kg以上,实现曲拐近净锻造存在以下难点。
(1)难以采用常规的模锻工艺。通常小尺寸曲轴的生产是采用专用模锻生产线,如机械压力机热模锻、液压螺旋压力机模锻以及锤上模锻生产线,既能较好地满足产品技术要求,又满足大批量生产,且投资不大。然而曲拐质量大,所需生产线设备的压力大,投资大,又因产量少,设备开动率低,导致技术与经济的综合效益差。目前还没有曲拐模锻专用生产线,其锻造都是在通用锻压设备上进行,如大型自由锻液压机或挤压液压机,这给提高曲拐锻件的尺寸精度和生产效率造成了困难。
(2)曲拐的尺寸大形状复杂。由图1可知,曲拐不仅尺寸大,而且形状复杂,加热保温时间长,表面氧化严重,粘连的氧化皮易造成表面局部凹坑而缺料;通用锻压设备难以成形复杂的形状,这使实现曲拐的小余量锻造更加困难,也是目前曲拐锻件材料利用率低的原因之一,目前曲拐锻件与交货零件的质量比为2.1∶1,即锻件材料利用率不到50%。
(3)实现高生产效率和低能耗困难。通常电站用锻件的价格高于船用锻件的价格,如转子价格是曲拐的近2倍,但曲拐的形状要比转子复杂,其锻造成形需要的火次多,中间需更换的工具与辅具多,实现高生产效率和低能耗困难。
02
曲拐挤压成形方式选择
1.2.1 曲拐的形状特点与成形方式选择
由图1(a)、(b)可知,大型曲拐由两曲臂和连杆颈组成,曲臂与曲轴主轴颈连接的一端称为曲拐的主轴颈端,因服役与组装的需求,此端为半圆形,并开有大的主轴孔;另一端与连杆颈制为一体,常称为连杆颈端,因对称关系,曲拐成U形,为减小旋转运动的质量,此端设计为近似锥状截面;曲臂的中间段接近矩形厚板,间距较窄,通常小于两臂的壁厚[8]。
基于大型曲拐的形状特点,采用挤压方式成形比较合适,其原因:①除两端外,两臂外形和其间距都近似为等截面,且长度较长,适合挤压成形;②连杆颈和两臂间距可一次挤压成形;③两端部的形状可借助挤压凸模与凹模两端施压成形。
1.2.2 曲拐形状及挤压工序的制定
由于曲拐的尺寸质量大,目前没有合适的轧制坯料,只能采用冶炼、铸锭、锻制坯的生产工艺,具体工艺流程:冶炼→铸锭→加热→自由锻制坯→加热→表面清理→挤压成形→热处理→切削加工。挤压前的坯料形状为长方体形,如图6(a)所示,形状简单,便于自由锻制坯,也便于挤压前的表面清理。
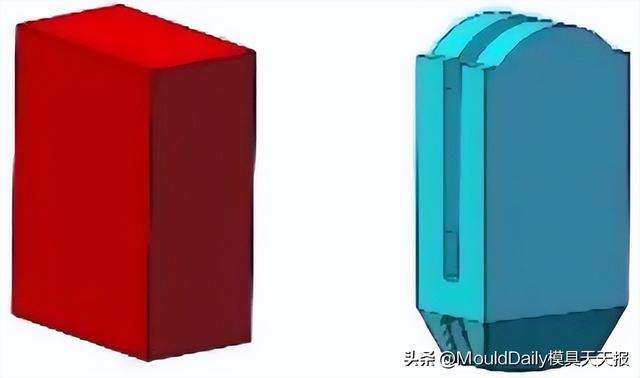
图6 曲拐的挤压成形
(a)坯料形状 (b)挤压后曲拐形状
由图1可知,曲拐的主轴孔径较大,受设备的运动自由度少和孔局部壁薄的限制,直接锻造困难,留待后续切削加工制造。若采用挤压成形不仅可节省材料,而且可减少相应的切削加工量,挤压后的曲拐如图6(b)所示。
03
曲拐挤压模的结构与工艺过程
曲拐挤压模结构
图7所示为曲拐挤压模结构,由挤压凸模、挤压筒和挤压凹模构成
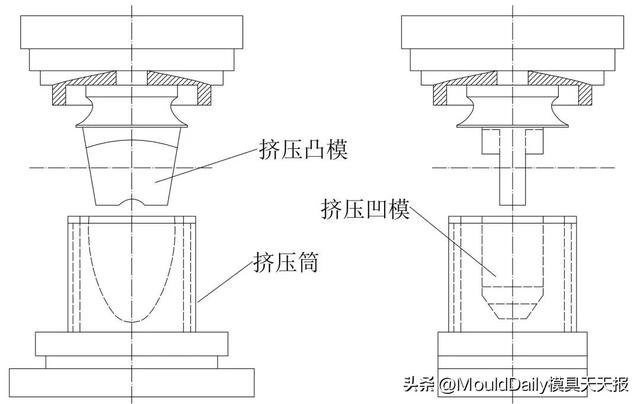
图7 曲拐挤压模结构
曲拐挤压成形过程
(1)挤压模位于挤压机动梁与移动工作台之间,挤压筒固定在移动工作台上,挤压凸模固定在动梁下面,挤压模中心线与挤压机中线重合。为便于将坯料放入挤压凹模内,挤压前需将挤压凹模随挤压筒从挤压机正下方移出。曲拐的挤压坯料质量为10×103 kg以上,加热后的坯料需用吊钳夹置放入凹模,如图8所示。
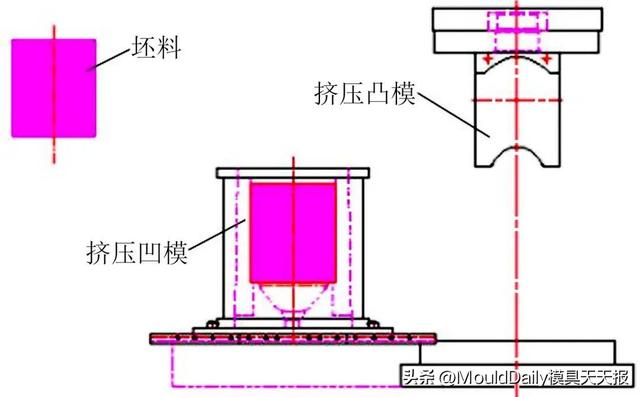
图8 移出挤压筒放置坯料
(2)坯料放入凹模后,需将凹模随挤压筒移到挤压机的工作位置,挤压模中心线与挤压机中线重合。挤压机动梁带动挤压凸模下行进行挤压,直至挤压凸模到规定的位置,完成曲拐的挤压成形,如图9所示。
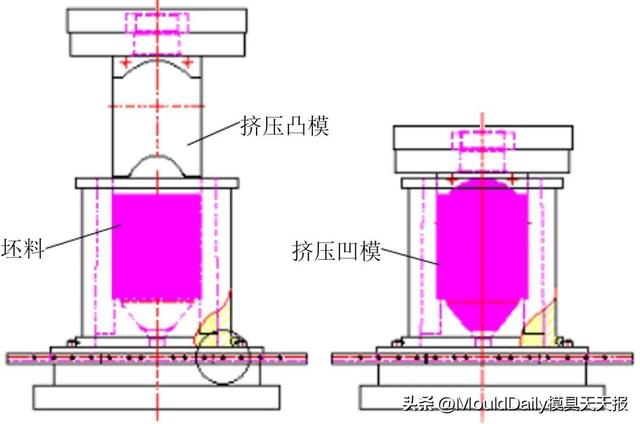
图9 移入挤压筒并挤压成形
(3)完成曲拐的挤压成形后,为减少模具受热回火和取出挤压成形的曲拐,挤压凸模在挤压机动梁带动下,迅速退回,脱离挤压凹模,如图10所示。
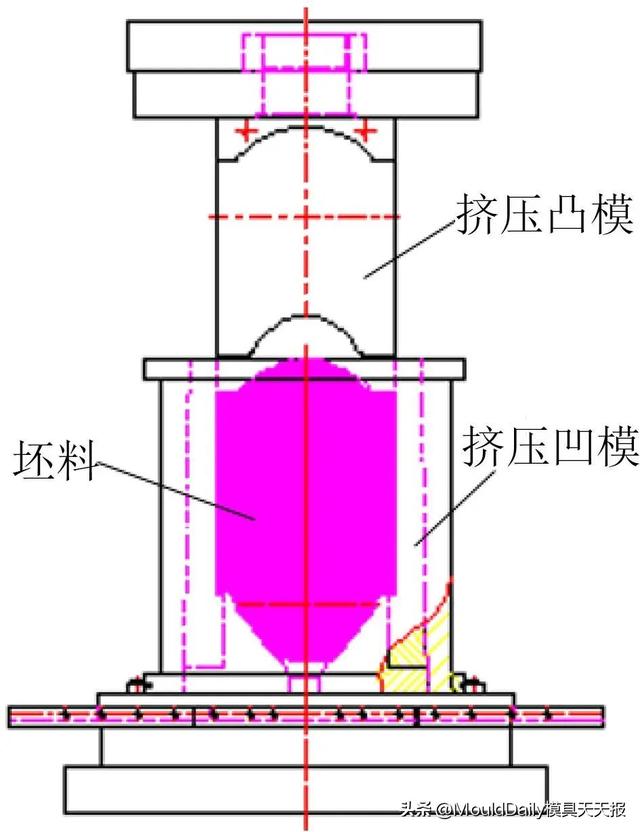
图10 挤压凸模退出
(4)挤压凸模退出后,挤压机的下顶出机构将成形的曲拐顶出,挤压凹模随挤压筒从挤压位置移出,再利用吊钳将挤压成形曲拐取走,如图11所示。随后进行下一次的曲拐挤压成形,如此循环完成曲拐挤压生产。
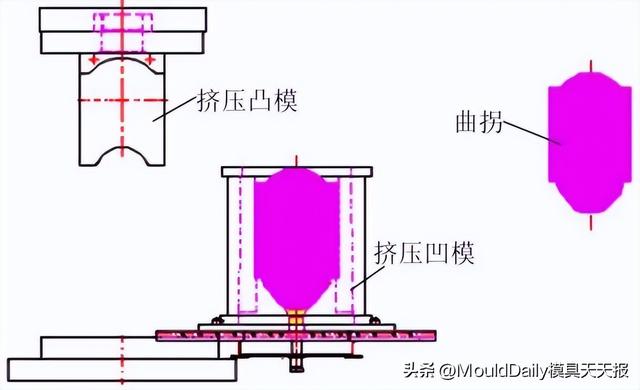
图11 取出挤压成形的曲拐
曲拐挤压成形的数值模拟研究

为验证曲拐挤压成形技术方案的可行性,了解挤压成形过程中材料的流动规律和变形分布,计算挤压成形所需的载荷,采用数值模拟方法进行研究。
01
曲拐挤压成形的数值模拟
力学模型
采用锻造商业软件forge进行数值模拟,挤压模的材料选用模具钢L6,坯料挤压变形的初始温度为1 230 ℃,模具的预热温度为350 ℃,挤压速度为30 mm/s,采用常摩擦条件,摩擦因子取0.7,模具零件与坯料间的换热系数为60 W/(m2•℃),数值模拟的力学模型如图12所示。
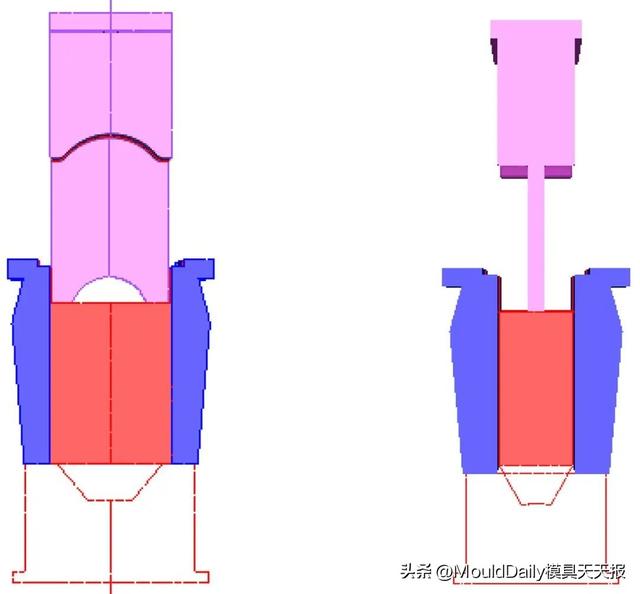
图12 数值模拟的力学模型
(a)正视图 (b)侧视图
曲拐挤压成形过程的模拟
为了解曲拐挤压成形的过程,在凸模的挤压行程中取6个行程点观察坯料的变形,分别是初始毛坯、挤压行程分别为20%、40%、60%、80%、100%。挤压坯料的成形状况如图13所示。
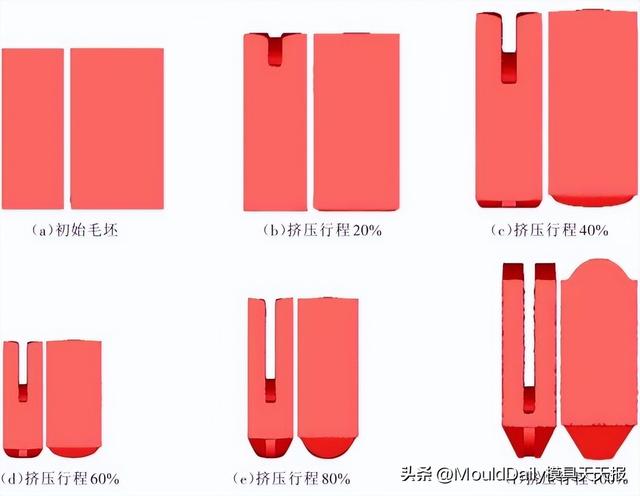
图13 曲拐挤压的坯料变形过程
数值模拟结果分析
由于曲拐的曲臂厚度大于两臂间距,因而凸模较窄,挤压成形过程分为2个阶段,其分界点约在凸模行程80%处。
在凸模完成行程的80%前,此阶段的变形主要集中在凸模下方与两臂内侧,主轴颈端的两臂内侧有一定的塌角,其是在挤压的最初阶段形成,当超过行程的20%后,塌角不再变化。此阶段主要是劈开坯料、初步形成两臂,两端的成形较少。曲拐挤压成形的载荷行程曲线如图14所示,载荷增大缓慢且较小。
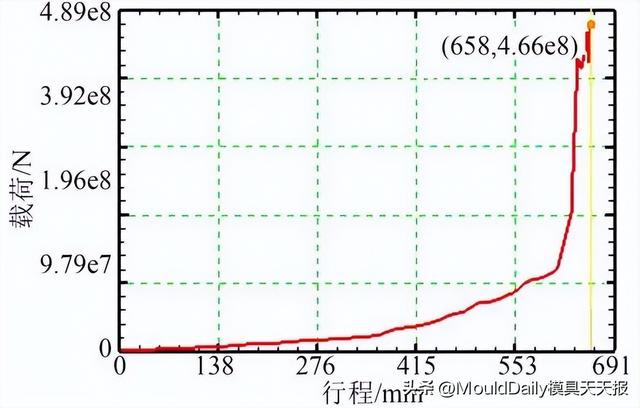
图14 曲拐挤压成形的载荷行程曲线
当超过行程的80%后,两臂顶端处的坯料开始与凸模接触并逐渐成形,此阶段的挤压载荷随行程的增加而迅速增大,迫使两端材料流向两端深处,完成整个曲拐的成形。
02
曲拐挤压成形的载荷计算
曲拐挤压成形载荷的计算是选择设备的依据,借助载荷-挤压行程的变化曲线可分析毛坯材料填充模腔的过程。由图14可知,数值模拟计算的最大挤压成形载荷为466 MN,挤压生产试验显示的最大值为420 MN,两者相差不大。
曲拐挤压成形的生产试验
曲拐挤压成形的生产试验包括钢水冶炼、铸锭、钢锭加热、自由锻制坯、坯料加热、坯料表面清理、挤压成形、锻后热处理等全部技术过程。现进行曲拐的挤压成形试验,试验件是S90曲拐,零件交货质量为16.7×103 kg,挤压后曲拐坯的质量为 27×103 kg,挤压后曲拐坯质量是交货零件的1.61倍。挤压机的工程载荷为500 MN,挤压过程中液压系统显示挤压力为420 MN。曲拐挤压成形的主要工艺过程如图15所示。

图15 曲拐挤压生产试验
生产试验后,对挤压成形的曲拐进行尺寸测量,满足曲拐的后序机械加工的尺寸要求,试验设备系统显示,最大挤压载荷为420 MN。说明采用挤压成形方式进行曲拐生产可行。但在大批量生产中需注意以下环节。
(1)挤压前坯料的形状尺寸精度控制。挤压前坯料的形状尺寸精度是影响曲拐挤压成形结果和挤压顺利进行的重要因素,当其精度过低时会导致2种不利结果:一是坯料尺寸大或形状不规范,加热后难以放入挤压筒内,导致无法进行挤压;二是坯料尺寸小或形状不规范,坯料与挤压筒间隙大且不均匀,挤压成形的曲拐两臂长短不一,壁厚差别大。
(2)去除坯料的表面氧化皮。曲拐质量大,挤压前加热、保温时间长,出炉后表面有一层厚的氧化皮,若没有去除干净,会造成局部尺寸缺少而不合格,同时损伤模具。
(3)适当提高加热温度。曲拐两端形状是最后成形,此时端部材料的温度降低较明显,变形流动困难,端部难以成形饱满,也导致挤压载荷提升剧烈,适当提高加热温度可缓解或消除上述现象。
▍原文作者:张彦娟 1,2孙统辉 1,2任杰 3张瑞华 1,2
▍作者单位:1. 洛阳中重铸锻有限责任公司; 2. 中信重工机械股份有限公司; 3. 上海电机学院
相关参考
视频加载中...
法兰液压机(热模锻液压机(1000吨2000吨3000吨压力机))
热模锻液压机(1000吨2000吨3000吨压力机),选用框架式结构,热锻一次成型,热模锻,是锻造工艺技术的一种,一般是指将金属毛坯加热至高于材料再结晶温度后,利用模具将金属毛坯塑性成形为锻件形状和尺寸的精密锻造方法...
法兰液压机(热模锻液压机(1000吨2000吨3000吨压力机))
热模锻液压机(1000吨2000吨3000吨压力机),选用框架式结构,热锻一次成型,热模锻,是锻造工艺技术的一种,一般是指将金属毛坯加热至高于材料再结晶温度后,利用模具将金属毛坯塑性成形为锻件形状和尺寸的精密锻造方法...
液压机类型及型号(热模锻液压机(1000吨2000吨3000吨压力机))
热模锻液压机(1000吨2000吨3000吨压力机),选用框架式结构,热锻一次成型,热模锻,是锻造工艺技术的一种,一般是指将金属毛坯加热至高于材料再结晶温度后,利用模具将金属毛坯塑性成形为锻件形状和尺寸的精密锻造方法...
液压机类型及型号(热模锻液压机(1000吨2000吨3000吨压力机))
热模锻液压机(1000吨2000吨3000吨压力机),选用框架式结构,热锻一次成型,热模锻,是锻造工艺技术的一种,一般是指将金属毛坯加热至高于材料再结晶温度后,利用模具将金属毛坯塑性成形为锻件形状和尺寸的精密锻造方法...
材料成形方法是零件设计的重要内容,也是制造者们极度关心的问题,更是材料加工过程中的关键因素,今天就带大家来看看金属成形工艺。01铸造液态金属浇注到与零件形状、尺寸相适应的铸型型腔中,待其冷却凝固,以获得...
压铸(注意压铸不是压力铸造的简称)是一种金属铸造工艺,其特点是利用模具腔对融化的金属施加高压。模具通常是用强度更高的合金加工而成的,这个过程有些类似注塑成型。砂模铸造就是用砂子制造铸模。砂模铸造需要在...
来源:新材料在线 锻造在中国有着悠久的历史,它是以手工作坊的生产方式延续下来的。大概是在20世纪初。它才逐渐以机械工业化的生产方式出现在铁路、兵工、造船等行业中。这种转变的主要标志就是使用了锻造能力强大的...
来源:新材料在线 锻造在中国有着悠久的历史,它是以手工作坊的生产方式延续下来的。大概是在20世纪初。它才逐渐以机械工业化的生产方式出现在铁路、兵工、造船等行业中。这种转变的主要标志就是使用了锻造能力强大的...
意大利数控立车(大连重工(002204SZ):控股子公司拟购置一台二手55米数控曲拐立车)
...大型曲轴市场拓展,董事会同意下属控股子公司大连华锐船用曲轴有限公司投资不超过450万元购置一台二手φ5.5米数控曲拐立车(含基础、安装和恢复使用等费用)。本文源自格隆汇