板式换热器垫片组装(换热器盲板拆装动画+故障处理办法)
Posted
篇首语:赋料扬雄敌,诗看子建亲。本文由小常识网(cha138.com)小编为大家整理,主要介绍了板式换热器垫片组装(换热器盲板拆装动画+故障处理办法)相关的知识,希望对你有一定的参考价值。
板式换热器垫片组装(换热器盲板拆装动画+故障处理办法)
换热器装配
管式换热器常见故障原因分析及处理方法
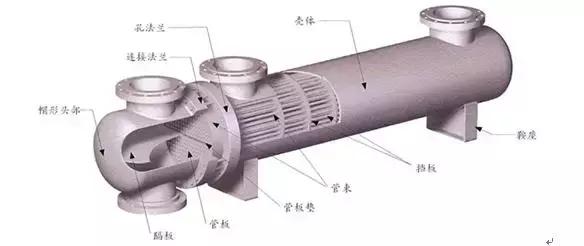
一、两种介质互串(内漏)
1 产生原因
①换热管腐蚀穿孔、开裂。
②换热管与管板胀口(焊口)裂开。
③浮头式换热器浮头法兰密封漏。
2 处理方法
①更换或堵死漏的换热管。
②换热管与管板重胀(补焊)或堵死。
③紧固螺栓或更换密封垫片。
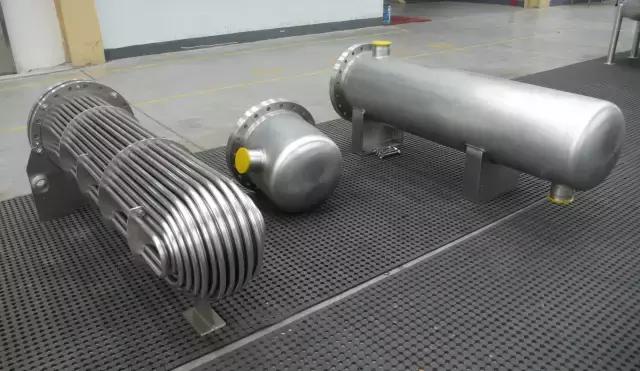
二、法兰处密封泄漏
1 产生原因
①垫圈承压不足、腐蚀、变质。
②螺栓强度不足,松动或腐蚀。
③法兰刚性不足与密封面缺陷。
④法兰不平或错位,垫片质量不好。
2 处理方法
①紧固螺栓,更换垫片。
②螺栓材质升级、紧固螺栓或更换螺栓。
③更换法兰或处理缺陷。
④重新组对或更换法兰,更换垫片。
三、传热效果差
1 产生原因
①换热管结垢。
②水质不好、油污与微生物多。
③隔板短路
2 处理方法
①化学清洗或射流清洗垢污。
②加强过滤、净化介质,加强水质管理。
③更换管箱垫片或更换隔板。
四、阻力降超过允许值
1 产生原因
壳内、管内外结垢
2 处理方法
用射流或化学清洗垢物
五、振动严重
1 产生原因
①因介质频率引起的共振。
②外部管道振动引起的共振。
2 处理方法
①改变流速或改变管束固有频率。
②加固管道,减小振动。
板式换热器常见故障原因分析及处理方法
板式换热器常见故障有串液、外漏、压降过大、供热温度不能满足要求四个方面。
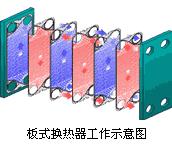
一 、串液
1 产生原因
①由于板材选择不当导致板片腐蚀产生裂纹或穿孔。
②操作条件不符合设计要求。
③板片冷冲压成型后的残余应力和装配中夹紧尺寸过小造成应力腐蚀。
④板片泄漏槽处有轻微渗漏,造成介质中有害物质浓缩腐蚀板片,形成串液。
2 处理方法
①更换有裂纹或穿孔板片,在现场用透光法查找板片裂纹。
②调整运行参数,使其达到设计条件。
③换热器维修组装时夹紧尺寸应符合要求,并不是越小越好。
④板片材料合理匹配。
二 、外漏
1 产生原因
①夹紧尺寸不到位、各处尺寸不均匀(各处尺寸偏差不应大于3 mm)或夹紧螺栓松动。
② 部分密封垫脱离密封槽,密封垫主密封面有脏物,密封垫损坏或垫片老化。
③ 板片发生变形,组装错位引起跑垫。
④在板片密封槽部位或二道密封区域有裂纹。
2 处理方法
① 在无压状态,按制造厂提供的夹紧尺寸重新夹紧设备,尺寸应均匀一致,压紧尺寸的偏差应不大于±0.2N (mm)(N 为板片总数),两压紧板间的平行度应保持在2 mm 以内。
② 在外漏部位上做好标记,然后换热器解体逐一排查解决,重新装配或更换垫片和板片。
③ 将开换热器解体,对板片变形部位进行修理或者更换板片。在没有板片备件时可将变形部位板片暂时拆除后重新组装使用。
④ 重新组装拆开的板片时,应清洁板面,防止污物粘附着于垫片密封面。
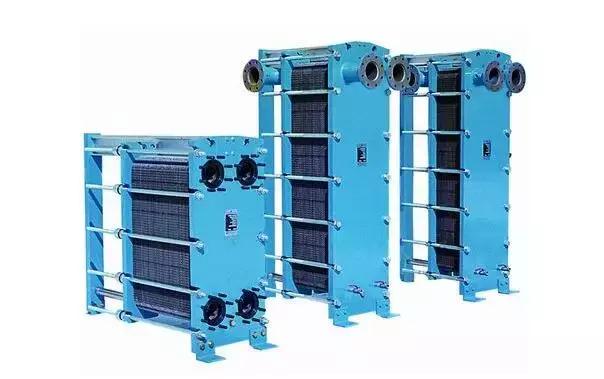
三 压降过大
1 产生原因
①运行系统管路未进行正常吹洗,特别是新安装系统管路中许多脏物(如焊渣等)进入板式换热器的内部,由于板式换热器流道截面积较窄,换热器内的沉淀物和悬浮物聚集在角孔处和导流区内,导致该处的流道面积大为减小,造成压力主要损失在此部位。
② 板式换热器首次选型时面积偏小,造成板间流速过高而压降偏大。
③ 板式换热器运行一段时间后,因板片表面结垢引起压降过大。
2 处理方法
①清除换热器流道中的脏物或板片结垢,对于新运行的系统,根据实际 情况每周清洗一次。
②二次循环水最好采用经过软化处理后的软水,一般要求水中悬浮物质量浓度不大于5 mg/L、杂质直径不大于3 mm、pH≥ 7。
当水温不大于95℃时,Ca 、Mg 浓度应不大于2 mmol/L;
当水温大于95℃ 时,Ca 、Mg 浓度应不大于0.3 mmol/L、溶解氧质量浓度应不大于0.1 mg/L。
③对于集中供热系统,可以采用一次向二次补水的方法。
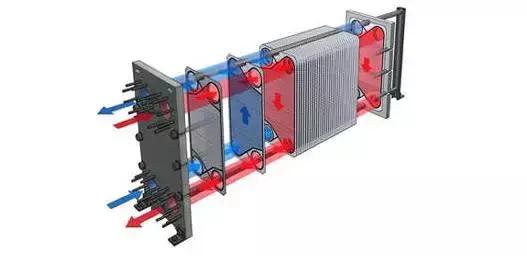
四 供热温度不能满足要求
1 产生原因
①一次侧介质流量不足,导致热侧温差大,压降小。
②冷侧温度低,并且冷、热末端温度低。
③并联运行的多台板式换热器流量分配不均。
④换热器内部结垢严重。
2 处理方法
① 增加热源的流量或加大热源介质管路直径。
② 平衡并联运行的多台板式换热器的流量。
③拆开板式换热器清洗板片表面结垢。
列管式换热器管束故障及法兰盘泄露
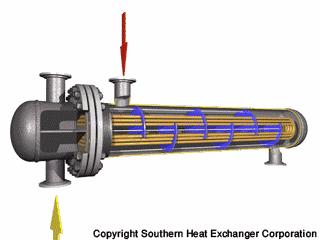
一、管束故障
1 、管束的腐蚀、磨损造成管束泄露或者管束内结垢造成堵塞引起故障
冷却水中含有铁、钙、镁等金属离子及阴离子和有机物,活性离子会使冷却水的腐蚀性增强,其中金属离子的存在引起氢或氧的去极化反应从而导致管束腐蚀。同时,由于冷却水中含有Ca2+、Mg2+离子,长时间在高温下易结垢而堵塞管束。
为了提高传热效果,防止管束腐蚀或堵塞,采取了以下几种方法:
(1)对冷却水进行添加阻垢剂并定期清洗。
例如对煤气冷却器的冷却水采用离子静电处理器或投加阻垢缓蚀剂和杀菌灭藻剂,去除污垢,降低冷却水的硬度,从而减小管束结垢程度。
(2)保持管内流体流速稳定。
如果流速增大,则导热系数变大,但磨损也会相应增大。民生煤化对地下水泵进行了变频改造,使地下水管网压力比较稳定,提高了热交换器换热效果和降低了管束腐蚀。
(3)选用耐腐蚀性材料(不锈钢、铜)或增加管束壁厚的方式。
(4)当管的端部磨损时,可在入口200mm长度内接入合成树脂等保护管束。
2、振动造成的故障
造成振动的原因包括:
由泵、压缩机的振动引起管束的振动;由旋转机械产生的脉动;
流入管束的高速流体(高压水、蒸汽等)对管束的冲击。
降低管束的振动常采用以下方法:
(1)尽量减少开停车次数。
(2)在流体的入口处,安装调整槽,减小管束的振动。
(3)减小挡板间距,使管束的振幅减小。
(4)尽量减小管束通过挡板的孔径。
二、法兰盘泄漏入
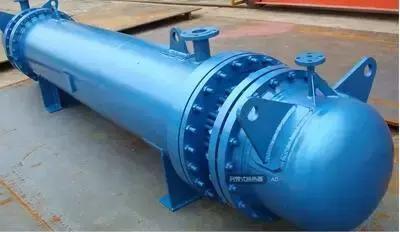
法兰盘的泄漏是由于温度升高,紧固螺栓受热伸长,在紧固部位产生间隙造成的。
因此,在换热器投入使用后,需要对法兰螺栓重新紧固。
换热器内的流体多为有毒、高压、高温物质,一旦发生泄漏容易引发中毒和火灾事故,
在日常工作中应特别注意以下几点:
尽量减少密封垫使用数量和采用金属密封垫;
采用以内压力紧固垫片的方法;
采用易紧固的作业方法。
相关参考
板式换热器板片装反了(板式热交换器的板片发生错位的原因及处理方法,国信工业设备)
...交换器的板片发生错位的原因及处理方法:一般引起板式换热器错位的原因无外乎是多程组合、长期使用的,同时介质流量和压力变化较大,这个时候,板式换热器无法抵住压力,会引起板片变形,密封垫片滑离垫片槽。可将损...
板式换热器由于换热效率高、热损失小、结构紧凑轻巧、占地面积小、使用寿命长等特点而被广泛的应用,但是大家在使用的过程中难免会出现一些问题,今天就和大家分享一下板式换热器常见故障的处理方法。常见的故障一般...
板式换热器在化工、石油和供热等行业中的应用较为广泛。但板式换热器的选择过程十分复杂,且需要优化供热系统。因此,本文主要分析了节能设计在板式换热器供热系统中的具体应用方法,并分别对供热系统的工作原理、系...
(一)运行状况偏离工艺要求1、新投产的板式换热器如果达不到工艺要求,应仔细检查原始设计参数、设计计算、组装等是否正确,然后决定是否应增加或者减少换热面积,以及改变流程组合。2、若板式换热器开始运行是正常的...
手动紧固扳手(拆装板换扳手 板式换热器电动液压工具 板换液压扳手拆卸)
派力重工换热设备拆卸设备移动灵活手动板换扳手板式换热器因具有坚固,工作效率高等优势被广泛的应用在生活、生产中,每一种应用都有它不可替代的作用,板式换热器主要由传热板片、密封垫片、两端压板、固定封头、活...
第1节板式换热器的安装板式换热器由其结构特点所决定,它的安装比较方便和灵活。以下对板式换热器的额零件组装和系统安装方面需注意的事项加以说明。一、板式换热器的零件组装关于板式换热器的零件组装,无论是制造...
板式换热器拆卸专用工具(板框式换热器液压扳手 板式换热器拆装扳手)
产品简介板式换热器液压扳手是可拆板式换热器高效的拆装工具,适用于板式换热器制造厂及使用单位对可拆板式换热器的拆装。与工人拆装相比,只需两个人,拆装效率可提高6倍以上。板式换热器液压扳手由泵站、夹紧油缸...
板式换热器液压扳手是可拆板式换热器高效的拆装工具,适用于板式换热器制造厂及使用单位对可拆板式换热器的拆装。与工人拆装相比,只需两个小时,拆装效率可提高6倍以上。板式换热器液压扳手由泵站、夹紧油缸、高压...
板式换热器具有传热系数高、压降小、结构紧凑、质量轻、占用空间小、面积和流程组合方便、零件通用性强、可选择材料广以及容易实现规模化生产等特点,已被广泛应用于食品、机械、冶金、石油化工和船舶等领域,并成为...
板式换热器具有传热系数高、压降小、结构紧凑、质量轻、占用空间小、面积和流程组合方便、零件通用性强、可选择材料广以及容易实现规模化生产等特点,已被广泛应用于食品、机械、冶金、石油化工和船舶等领域,并成为...