智能数字显示控制仪显示LL(用于多组分增材制造零件的材料分割和数字重建的原位激光轮廓术)
Posted
篇首语:生活只有在平淡无味的人看来才是空虚而平淡无味的。本文由小常识网(cha138.com)小编为大家整理,主要介绍了智能数字显示控制仪显示LL(用于多组分增材制造零件的材料分割和数字重建的原位激光轮廓术)相关的知识,希望对你有一定的参考价值。
智能数字显示控制仪显示LL(用于多组分增材制造零件的材料分割和数字重建的原位激光轮廓术)
长三角G60激光联盟导读
据悉,本文提出了一种基于激光轮廓术的逐层原位表征技术,作为数字重建多材料零件的方法。
摘要
除了生产几何复杂零件的能力外,增材制造还提供了一个独特的机会,在部件制造过程中收集有关部件的数据。然而,在原位对零件的形态和成分进行表征的努力有限。在本文中,我们提出了一种基于激光轮廓术的逐层原位表征技术,作为数字重建多材料零件的方法。激光轮廓仪收集的数据产生高度图和灰度图像,使用专用软件进行体素化,以体积重建零件。还使用X射线计算机断层扫描(CT)对同一部件进行了分析,该CT无法分辨部件内的不同组成区域,但捕获了细丝形态。然后将零件一分为二,将数字重建与实际零件形态和组成进行比较。总体而言,数字重建与CT和二等分图像一致。数字重建和CT/二等分图像之间的偏差可能是图像分割设置或数据收集后的材料移动的结果。此处演示的现场表征方法为实时过程监控奠定了基础,并为“天生合格”的增材制造零件铺平了道路。
1.介绍
在过去的几十年中,增材制造导致了具有越来越复杂几何形状的零件制造的范式转变。虽然增材制造包括熔丝制造(FFF,通常用于聚合物)和粉末床熔合(用于金属)等技术,但最通用的技术可能是直接墨水书写(DIW)。DIW技术使用可流动材料,该材料以规定速率通过移动喷嘴挤出。DIW在制造具有不同和/或不同化学性质的建筑部件方面特别有兴趣。
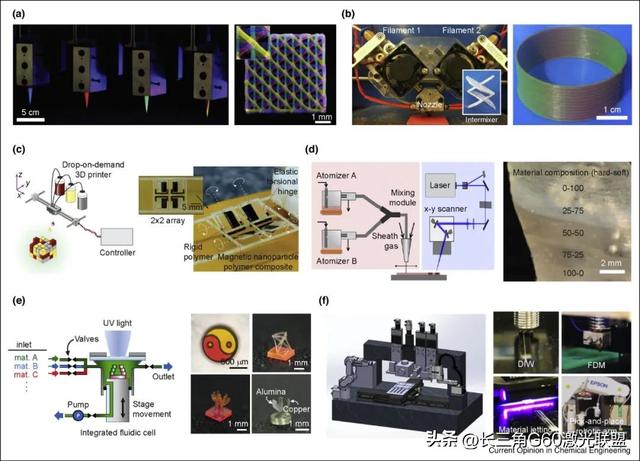
MMAM技术的最新进展。(a)使用多个喷嘴的多材料DIW。(b)使用双挤压头的多材料FDM,可通过单个喷嘴打印两条长丝。(c)基于MJ的MMAM,通过机器视觉系统提高打印分辨率。(d)使用气溶胶喷射系统的SLA。(e)使用动态流体控制的基于DLP的快速MMAM。(f)结合DIW、FDM、MJ和,以及两种互补技术(机械臂和光子固化系统)。
考虑到增材制造在零件制造过程中提供了对零件的本地可视访问,最近的一些研究集中于增材制造过程的现场监控。Grasso等人的一篇综述文章详细介绍了现场收集金属增材制造工艺数据的多种方法。他们将金属增材制造的现场监测的不同“水平”分类为0到4,包括(0)制造装置测量,(1)零件的分层测量,(2)构建路径后不久的副产品测量,(3)构建位置的零件测量,以及(4)体积层测量。虽然本文(DIW)中介绍的制造过程与Grasso等人(粉末床融合)中考虑的制造过程不同,但他们的文章正确地捕捉了创建现场过程监控方法时需要考虑的不同复杂程度。
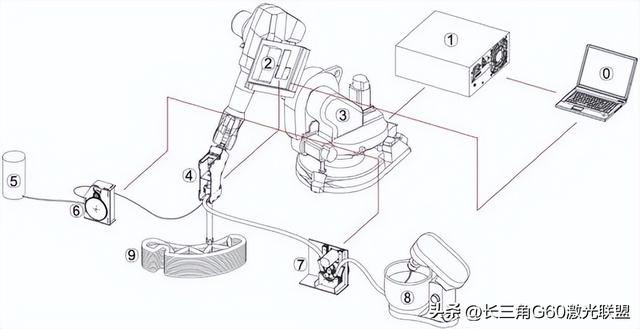
3DP设置示意图:0.系统命令;1.机器人控制器;2.打印控制器;3.机械臂;4.打印头;5.促进剂;6.用于加速剂的蠕动泵;7.用于预混合的蠕动泵;8.预混混合器;9.3D打印对象
在上述现场监测方法中,可能最容易实现的直接零件测量方法是机器视觉——一种基于图像的检查方法,已在工业中广泛用于过程监测和零件鉴定。考虑到与CT扫描相比,高分辨率相机的成本相对较低,并且区域分割和对象识别的图像处理技术不断改进,机器视觉提供了一种可访问的途径,只需对开始采集数据所需的过程进行少量修改即可对零件进行鉴定。如果在逐层基础上拍摄图像,测量技术将是1级测量方法。到目前为止,机器视觉技术已主要集成到增材制造工艺中,用于缺陷检测和可能的标记缺陷校正。
在本文中,我们描述了系统的设计和我们开发的用于产生这些重建的图像处理流水线。然后,我们将新方法用于测试,在设计零件、制造零件、图像处理技术生成的重建和X射线CT扫描之间进行并排比较。这种比较将有助于突出我们提出的技术的优点和缺点。
2.方法
2.1.材料选择和准备
本文选用的材料是为了突出逐层图像收集与传统的非原位技术(如x射线CT)相比具有的独特优势。x射线CT扫描技术可以根据材料的x射线质量衰减系数来区分材料,其衰减系数大致与密度和核截面有关。为了突出原位检测技术与CT扫描相比可能具有的优势,我们在本研究中使用的材料组成大致相同,仅在视觉上可区分。它们可以被视为具有类似x射线衰减系数但在视觉上截然不同的化学独特配方的替代品。需要注意的是,本案例研究并不是要创建一个一对一的CT扫描替代方法,而是展示一个可替代的、在线的方法,以收集零件和制造过程的数据。
2.2.多组分零件的设计
为这项研究设计了一个定制的测试件,用不同颜色材料的离散区域。主要目标是展示我们的现场数据收集和重建技术的能力,以识别在制造过程中只能通过光学访问的特征。从外观上看,测试件是一个无趣的(均匀蓝色的)立方体,一面长35毫米,但内部有嵌入的形状,用于测试重建技术的各个方面:两个45度角的环,一个球形外壳,以及LLNL的标志(图1b)。有角度的圆环(2.5 mm厚)可用于评估相对于有角度特征的垂直重建,球面(2 mm厚,25 mm内径)测试重建的能力,以分层方向分割不同直径的圆环/磁盘,LLNL标志的特点是小空间(~0.5 mm宽),这将测试处理代码解决小间隙的能力(以及打印机创建它们的能力)。如果打印机正确地生产零件,重建应包含所有三个主要特征。识别这些特征及其与实际部分比较的质量将被用来评估重建的质量。
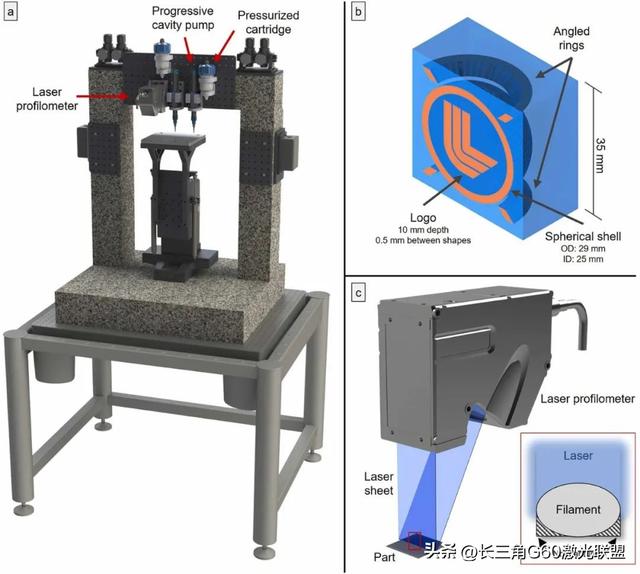
图1 (a)用于制造测试物品的自定义打印机设置。(b)试验件模型(切成两半)图像,显示感兴趣的主要特征和相关尺寸。(c)在被打印零件的第一层上扫描的激光轮廓仪的描绘。值得注意的是,在激光轮廓仪捕捉到3D扫描之前,整个层是打印出来的。红色边框显示激光轮廓仪捕获的灯丝的哪些区域。
2.3. 打印过程
多组分测试件在定制的3D打印机上通过直接墨水写入(DIW)工艺进行3D打印(图1a)。3D打印机的X轴和Y轴采用Aerotech ANT130XY组件,Z轴采用Aerotech ANT130LZS组件。三个轴由三个航空科技DP32020E伺服驱动器驱动。轴向运动和材料分配都使用Aerotech的aeroasic命令控制,后者封装在LLNL的自定义流量控制器MoSyFlow中。物料从筒体加压进入进气泵(,用于精细控制物料流量和启动/停止。打印前,测量两个喷嘴之间的X, Y和Z偏移量,并运行启动/停止校准程序,以确保使用适当的挤出时间参数,以最大限度地减少零件的缺陷。
2.4. 现场数据收集技术
通过逐层进行3D激光轮廓测量扫描,将数据收集程序纳入打印过程。Keyence LJX-8002控制器单元连接到Keyence LJX-8080线扫描轮廓仪头,该轮廓仪头使用定制夹具安装在打印机上的试验板上(图1a)。LJX-8080使用405 沿40 并使用倾斜CMOS传感器进行观察,以三角测量零件的高度(图1c)。为了收集3D数据,可以使用线性平移台以恒定速度在轮廓仪头部下方移动零件,并且可以将多个轮廓缝合在一起以形成3D表面。除了高度数据之外,还使用激光的散射强度生成灰度图像。
2.5.图像数据的后处理和部分重建
采集的高度和灰度数据的后处理在打印结束时以批处理方式完成,并涉及两个数据集的卷积。整个过程中的数据处理管道和数据转换图像如图2所示。使用自定义Python例程对高度和灰度图像进行采集数据的后处理。
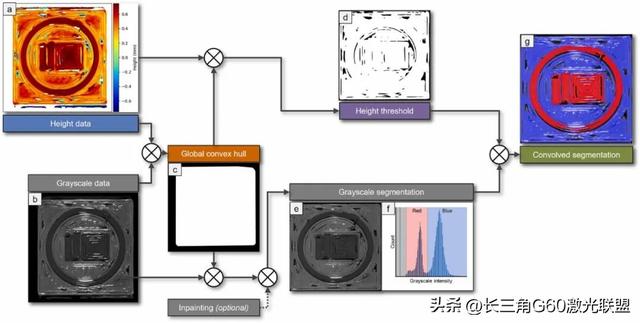
图2高度和灰度图像卷积的数据处理流程图。高度数据(a)和灰度数据(b)被阈值化并用于创建全局凸壳(c),该全局凸壳应用于每个层以裁剪图像处理区域。然后逐层地将凸壳应用于高度和灰度数据。高度数据被阈值化以创建二进制掩码(d)。灰度数据被形态学侵蚀(e),并使用由直方图(f)确定的阈值进行分割。再次卷积高度和灰度数据以获得最终层分割(g)。
逐层高度数据由激光轮廓仪以24位图像格式输出,高度值编码在颜色通道信息中。位图高度图像的RGB通道信息对15位数据进行编码——8位绿色、3位红色和4位蓝色——然后将其组合成合成值。
在对灰度数据应用图像校正技术后,使用多Otsu阈值方法分割处理后的图像。不同成分的阈值由用户选择以大致对应于灰度强度数据的直方图上的值的局部最小值。零件中的每个像素都分配了一个与Otsu阈值箱编号相对应的“材质标签”。对合成图像进行微小校正,以去除图像中的小孔和物体,使其低于经验确定的尺寸。然后通过逐元素乘法将合成图与高度数据卷积,使得只有高于某个高度阈值且具有有效分配的合成值的部分被包括在最终数据堆栈中。该部分最终表示为均匀间隔的体素网格数据集,每个像素指定一个指定给特定材质的值。
2.6.测试部件的X射线计算机断层扫描(CT)
还使用X射线计算机断层扫描(CT)对供试品进行了分析。CT扫描实际上是一种用于质量检查的常用技术,但是,它是本地的,在零件完成之前无法收集数据。零件热固化后,使用North Star Imaging X25 CT扫描仪以30.08的分辨率对其进行成像 μm/体素。值得注意的是,CT扫描依赖于X射线衰减的差异来分辨不同的材料,并且由于我们使用的硅酮仅颜色不同,因此不太可能在捕获的图像中看到任何成分差异。
3.结果与讨论
3.1. 测试件质量
图1b中所示的测试件是使用DOWSIL SE 1700打印的,以评估一层一层检查技术的能力,以正确重建多组分叠加制造部件的内部特征。当试图在名义上的全密度物品上进行DIW打印时,典型的情况是,材料挤压不足和过度的区域是明显的,并导致零件质量下降。图3c显示了被打印部件的外观图像。由于制造过程的逐层特性,最后的部件具有具有特征脊的均匀着色的外表面。在立方体的表面中心也有一些区域,它们是立方体外部和内部外壳外部之间的薄壁。切片软件只在那些可能没有被优化分配的区域放置了少量的材料,从而导致这些面部的颜色“渗出”。从部件的外观来看,尚不清楚内部是否保留了其沉积时的形态,但为了图像分析的目的,我们假设在收集数据后,各层没有显著变化。
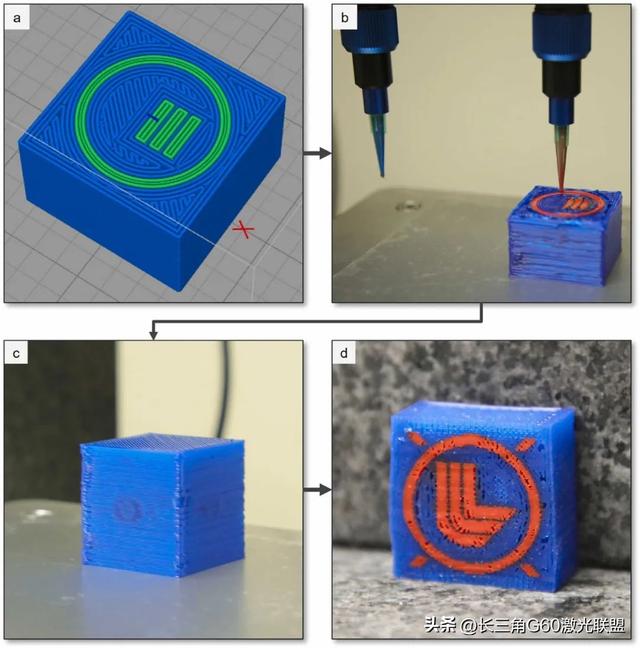
图3.(a)商业切片软件中测试零件的自上而下图像,具有完整的内部细丝形态。(b)在切片软件中显示的大致相同位置的测试打印图像。(c)打印后的最终零件外部图像。(d)在与打印品正交的方向上被平分后的零件的图像。
3.2.逐层灰度图像和高度图
原始灰度图像和转换高度图的示例如图4所示。这些图像展示了图像分析过程中必须考虑的许多关键挑战。查看图4(a1、b1、c1)的灰度图像,两种材料在具有两个分量的区域中的部分的灰度图像中是可清楚区分的,并且可以使用相对光强度容易地分割。然而,这些部分的逐层成像技术中的许多主要挑战在该图中也很清楚。
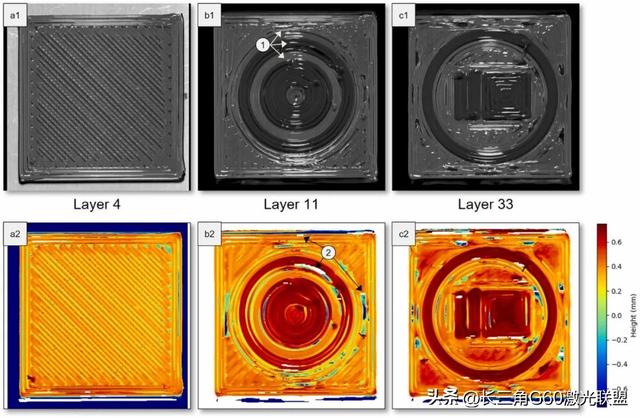
图4.激光轮廓仪在不同高度收集的逐层数据的示例图像。来自激光的表面反射在灰度图像中显示为亮/饱和区域。(a1,a2)层4图像,示出了以板为背景的单组分切片。(b1,b2)层11数据,显示了测试的两种材料之间的对比度水平。光反射的饱和示例由标签1表示。在b2的外环中可以看到裂缝中高度数据的下降(由标签2表示)。(c1,c2)层33数据,显示了图像中使分割复杂化的饱和区域的普遍性。
使用激光轮廓仪获取各层的高度图,并将记录的图像转换为第2.5节中讨论的高度图。原始高度图示例见图4(a2、b2、c2)。激光轮廓仪的最大测量范围为:+ /- 20.5 ,然而,已减少了兴趣区域,以减轻单层高度测量的噪声。单组分层和多组分层的高度图捕捉了零件的细丝结构,并显示了打印细丝可能没有重叠的材料间隙。然而,在多个细丝的界面处,光可能投射到两个细丝之间的区域中,而不被反射到传感器中,从而导致裂缝中的数据丢失。也有可能激光从光滑的硅酮表面的反射会被误解并捕获为单层轮廓的一部分。
有趣的是,在沉积的第一层上收集的图像明显比剩余图像亮,这可能是由于第一层接近反射金属基板。因此,第一层的高度和灰度映射与在整个打印的其余部分收集的相比相对较差。这种复杂性将在该方法的未来迭代中通过使用非反射基板或临时调整第一层轮廓仪的照明设置来解决。
3.3.体积零件重建和比较
这项工作的主要目标是证明可以在逐层基础上有效地采用现场检查方法,以创建增材制造零件的精确体积重建。受检供试品的主要特征是嵌入球形外壳内的LLNL标志以及外壳顶部和底部的两个外部角环。
测试件是用剃刀在零件的大约中间切开的,以作为这里提供的其他检查方法之间的直接比较。值得注意的是,这项工作的主要重点不是优化打印的质量,而是展示这里的检查方法能够数字重建部分和恢复主要形态特征。被等分的部分具有典型缺陷,当限定一个增材制造的部分时,这些缺陷将是主要的兴趣(特别是空洞和材料的位移)。该零件的顶部和底部几层在全密度直线填充的残余细丝之间有周期性的间隙。在部分的一些主要细丝和特征之间也有间隙,这些间隙可能可以追溯到刀具路径本身。最后一个主要缺陷可以在LLNL标志的“L”之间看到,似乎有些材料被过度挤压,弥合了不同特征之间的差距。
除了一层一层地收集图像和资料外,打印出来的测试品治愈后还会进行x射线计算机断层扫描(CT)检查。在图5c中可以看到大致相同位置的图像。尽管CT扫描可以清楚地恢复零件的纤维驱动特征(例如,孔洞、间隙),并且与测试件非常相似,但在图像中无法分辨密度匹配的材料。
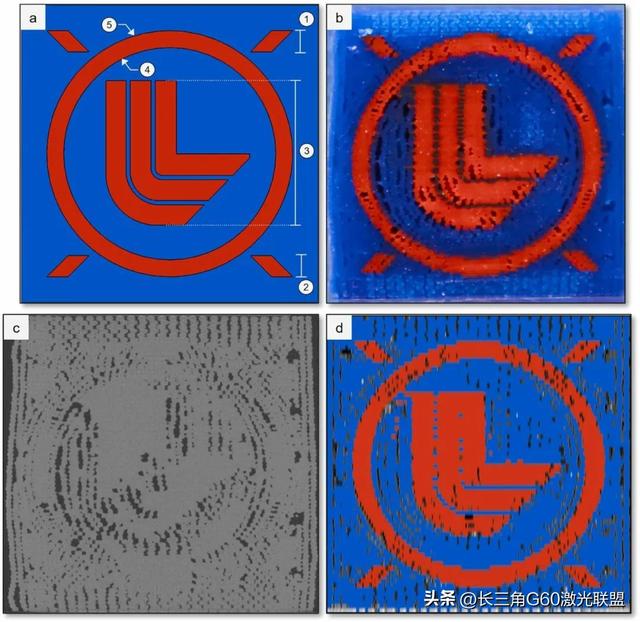
图5.3D打印的供试品的横截面图像(切片)。所有切片均来自同一部分,并在大致相同的位置拍摄。(a)显示设计意图的原始CAD模型切片。(b)用剃须刀片对分后的物理部分照片。(c)零件的X射线CT重建切片。(d)基于激光轮廓仪的零件重建切片。(a)中的标记特征用于比较3D模型、二等分零件和数字重建之间的测量尺寸。
为了更定量地比较重建的目标和实际零件,测量了嵌入零件的五个特征:(1,2)顶部和底部角环的高度,(3)LLNL标志的高度,(4)内球面的垂直直径和水平直径,(5)外球面的垂直直径和水平直径(见图5a)。目标零件提供的尺寸(图5a)是直接从三维模型上测量的,实际零件和重建零件的尺寸(图5b,d)是用ImageJ测量的。为了考虑体素分辨率,重构的测量在垂直方向上四舍五入到最接近的0.5 mm,在水平方向上四舍五入到0.1 mm。结果显示,数字重建与实际零件之间的测量值具有较好的一致性,与目标尺寸仅略有偏差。这些值的偏差可能是由于在沉积后或固化过程中打印过程中的材料移动造成的。
尽管这一重建代表了一项重大成就,并为AM部件的实时检查提供了一条前进的道路,但它并非没有缺点。直接比较CT图像和重建时立即出现的一个主要缺点是,在获取数据后,细丝和材料可能会移动。例如,当在打印过程中向零件添加更多质量时,可能存在于下部区域中的一些细丝间隙似乎会塌陷,因为材料在热固化之前仍然是可流动的。Plott和Shih使用不同的弹性体系统对这些形态变化进行了探索,但他们的工作突出了在尝试使用进化过程中收集的数据重建零件时存在的固有困难。
未来,这可以通过使用紫外线固化材料系统来克服,因为材料将有效地冻结在原位。该方法的另一个缺点是在进行顶面拓扑测量时,在细丝的下侧丢失数据。挤出长丝具有椭圆形横截面,然而,仅捕获顶部圆形表面(见图1c)。在本文中,数字重建假设整个层高度(0.5 毫米)。有人提出,细丝沿其中心轴的相对对称性可用于更准确地恢复单个细丝形态。这项工作保留给未来的工作,因为它需要考虑跨越整个构建时间的材料转移。
3.4. Layer-wise空隙比较
虽然图5显示了CT图像、被二分部分和激光轮廓重建对嵌入特征的一致性,但我们也希望评估该部分的缺陷。由于空洞是增材制造零件中最常见的缺陷之一,也是我们的新技术唯一适合识别的缺陷,所以我们选择根据每次重建得到的空洞的位置和大小分布来比较这些技术。对给定层的CT图像采用二值标记算法,并在部分大约相同的位置进行数字重建,估计空洞面积。图6比较了零件内两个不同位置的空洞位置和尺寸分布。
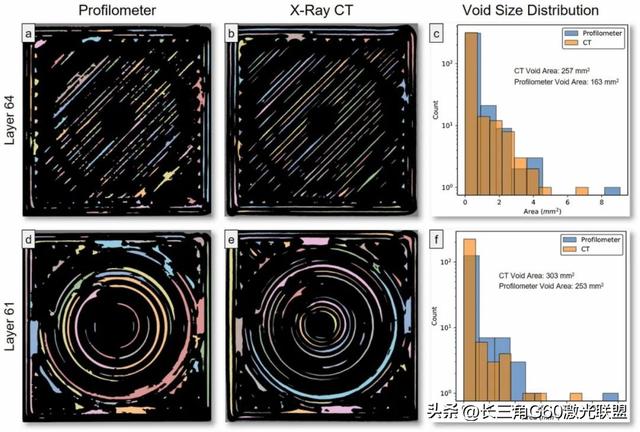
图6.供试品两个不同高度的轮廓仪(a,d)和X射线CT(b,e)数据的分层比较。图像中的形态数据显示在空隙尺寸分布图中,以及图像中估计的空隙总面积(c,f)。图中的彩色区域表示确定未沉积材料的层中的“空隙”。不同的颜色仅用于突出不同的区域,并且颜色是任意的,并且不对应于轮廓仪数据和CT数据。
特别是,与CT图像相比,基于轮廓仪的重建的分布图似乎偏向于较小的空隙区域。我们认为,这主要是由于硅酮的反射表面在重建过程中产生伪影,从而有效地将大空隙区域切割成多个较小区域。当比较图6a和b时,这种现象尤其明显,其中在图6b中连续出现的许多长对角线空隙在图6a中被分解成多个较短的空隙。图6c和图6F中还显示了基于收集方法的空隙的总面积。估计的轮廓仪空隙面积始终小于使用CT数据估计的空隙面积,尽管与单个切片的面积相比,表观差异相对较小。
需要注意的是,比较这些数据集本身就很困难,而且可能会部分扭曲结果。CT数据是在材料固化后收集的,有证据表明材料可能在沉积过程后或固化过程中发生了位移。这些图像和数据的配准也很困难,因为收集方法产生的图像分辨率不同,而且对象的空间方向有显著不同。数据收集时间和方法的差异可能导致了估计的孔隙大小分布图和面积的明显差异。相信在未来的研究中,可以用真正的原位x射线CT扫描方法对这两种方法进行更直接的比较。分析整体孔隙大小形态和分布也很有意义,然而,本文中提供的数据的分辨率使得这种分析的计算成本很高,因此我们选择将重点放在分层分析上进行比较。分层分析也更类似于人类或自主流程操作员将监测和利用的实时决策。
4. 结论
一种基于激光轮廓测量的分层原位表征技术已被应用于直接墨写制备具有密度匹配、视觉上不同材料的多材料部件。该检测技术产生了高度图和灰度图像,然后使用定制的卷积分割程序分析,以数字重建零件。高度数据和灰度图像的结合使该技术能够在使用的材料在视觉上明显时识别空洞(缺少材料)和材料类型。相比之下,非原位x射线CT能够识别空洞,但无法区分两种材料,因为它们的衰减相似。此外,基于轮廓仪的重构完全来源于制造过程中收集的数据,原则上可以实时计算和分析,以便在飞行中检测缺陷。将两种技术与文章的物理截面进行比较,结果显示非常一致。
基于轮廓仪的(实时)重建和x线CT之间也有显著的偏差。成像伪影导致基于轮廓仪的技术比CT识别更多的小空洞。我们还观察到打印后与材料沉降有关的偏差,这是慢固化油墨配方工作时不可避免的挑战。正因为如此,如果需要精确的答案,基于轮廓仪的重建方法显然不能替代x射线CT分析。然而,基于轮廓仪的重建可以在对生产时间影响最小的情况下进行,并生成可用于在线决策的信息,这是x射线CT技术无法做到的。只要感兴趣的材料或区域在视觉上可区分,这种方法也可能适用于其他形式的增材制造。因此,我们认为该技术值得进一步开发,并可能在生产环境的过程健康监测和简化部分验收中找到未来的应用。
来源:In situ laser profilometry for material segmentation and digital reconstruction of a multicomponent additively manufactured part, Additive Manufacturing, doi.org/10.1016/j.addma.2022.102896
参考文献:Additive Manufacturing Technologies, Springer Internationa, Publishing, Cham (2021), 10.1007/978-3-030-56127-7
长三角G60激光联盟陈长军原创作品!
相关参考
水位显示器显示LL(部分实用的电气符号,电路图里看到别不认识它们,需要的收藏吧)
电流表PA电流表电压表PV电压表有功电度表PJ无功电度表PJR频率表PF相位表PPA最大需量表(负荷监控仪)PM功率因数表PPF有功功率表PW无功功率表PR无功电流表PAR声信号HA光信号HS各种颜色的指示灯指示灯HL红色灯HR绿色灯HG黄色灯HY蓝色...
过程分析仪表的选型过程分析仪器仪表又称在线分析仪器仪表,是用于工业生产流程中对物质的成分及性质进行自动分析与测量仪器仪表的总称,重点为燃烧控制、废气安全回收、流程工艺控制、质量监测所需的自动化分析产品...
桑乐太阳能温度显示LL(2020工伤预防记者团进企业|山东桑乐集团有限公司紧绷安全弦)
编者按:幸福生活,需要劳动来创造;安全生产,则是劳动的前提。为提高社会及职工对预防工伤、安全生产的知晓度,通过宣传使广大职工树立安全生产意识,减少工伤事故,由济南市人社局等部门联合主办,齐鲁晚报·齐鲁壹...
PLC液位控制仪随着国家的经济的快速发展,对于能源的需求的不断增大,全国各地都建造了大大小小的罐区,用于储存各类油、气等燃料资源。这些燃料包括了石油,成品油(柴油、汽油),液化石油气,液化天然气等等。以前...
控制实验装置(智能操控装置和开关状态显示仪各自有哪些功能?谁更值得拥有?)
...面普遍存在的运行工况无法实时监测,指示元件集成度,智能化程度低等问题,智能操控装置和开关状态显示仪应用在高压开关柜中,极大地提高了高压开关柜操控的集成度和智能化。它们之间有什么区别?为什么同样的开关柜...
燃料喷嘴温度剃度(金属增材制造行业深度研究:从“0~1”迈向“1~N”)
...泰证券,李聪、朱雨时、田莫充)科普篇:从“零”拆解增材制造,多重路径齐头并进多维度优势凸显,增材制造为传统制造的重要补充增材制造技术,也称为“3D打印”技术(AdditiveManufacturing,AM),与传统的加工工业的核心...
燃料喷嘴温度剃度(金属增材制造行业深度研究:从“0~1”迈向“1~N”)
...泰证券,李聪、朱雨时、田莫充)科普篇:从“零”拆解增材制造,多重路径齐头并进多维度优势凸显,增材制造为传统制造的重要补充增材制造技术,也称为“3D打印”技术(AdditiveManufacturing,AM),与传统的加工工业的核心...
PLC液位控制仪随着国家的经济的快速发展,对于能源的需求的不断增大,全国各地都建造了大大小小的罐区,用于储存各类油、气等燃料资源。这些燃料包括了石油,成品油(柴油、汽油),液化石油气,液化天然气等等。以前...
PLC液位控制仪随着国家的经济的快速发展,对于能源的需求的不断增大,全国各地都建造了大大小小的罐区,用于储存各类油、气等燃料资源。这些燃料包括了石油,成品油(柴油、汽油),液化石油气,液化天然气等等。以前...
PLC液位控制仪随着国家的经济的快速发展,对于能源的需求的不断增大,全国各地都建造了大大小小的罐区,用于储存各类油、气等燃料资源。这些燃料包括了石油,成品油(柴油、汽油),液化石油气,液化天然气等等。以前...