昆化空气压缩机油(锻造行业深度报告:锻造,从“铁马”到高端装备时代“金戈”)
Posted
篇首语:知识的价值不在于占有,而在于使用。本文由小常识网(cha138.com)小编为大家整理,主要介绍了昆化空气压缩机油(锻造行业深度报告:锻造,从“铁马”到高端装备时代“金戈”)相关的知识,希望对你有一定的参考价值。
昆化空气压缩机油(锻造行业深度报告:锻造,从“铁马”到高端装备时代“金戈”)
(报告出品方/作者:信达证券,张润毅)
1. 锻造工艺:历史时代的分割器,金戈铁马的造就者
1.1 锻造工艺源远流长
锻造工艺历史悠久,推动人类文明进入“铁器时代”。人类工具的制造能力推动历史进步, 器具和生产工艺推动着人类历史发展。
人类历史“三期论”:1836年,克里斯蒂安·于恩森·汤姆森提出了“三期论”,根据 人类制作工具的材料,将人类历史分为三个时期,即“石器时代”、“青铜时代”和 “铁器时代”。陶器虽得到广泛运用,但作为容器并非主要生产工具,未能独立“引领” 一个时代,不过制陶工艺促进了冶金、铸造、锻造等制造工艺的发展。
石器、青铜器、陶器的应用奠定了锻造工艺与铁器应用的条件。
石器使用过程中对原材料的挖掘促进金属的发现。据考古发现,约在 250 万年前,东 非出现了最初的人类,其一大特点是开始制造并使用打制石器,人类也进入了旧石器 时代。最早约在公元前 1万年,人类开始制造并使用磨制石器,并进入了新石器时代。
在采石过程中,人类发现了纯的金属。由于金、银、铜具有相对惰性的化学性质,最先被人类发现并使用。大约公元前 9000年,人类开始锻造纯银和纯铜,前期的锻造品 主要以小型装饰品为主,后期随着纯金属增多,也开始锻造一些工具,主要以纯铜为主。但在那个时代,石器依然是主导性生产工具,锻造的纯金属工具量非常少。无论 如何,锻造自然金属的活动丰富了人类对金属的认识。
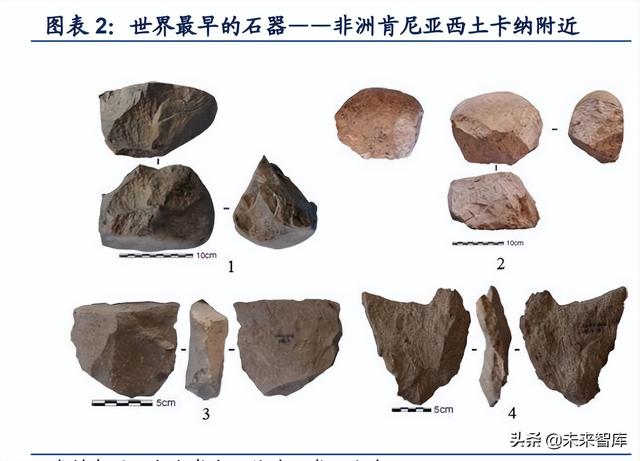
陶窑的出现提供了高温和还原性气氛,促进冶金业发展。制陶业的发展为锻造铺垫了 先决条件。早在旧石器时代,人类除了打磨石器作为工具之外,还发展出了另一项技能——制陶,伴随陶器制造所产生的陶窑,早在公元前 6000年就可以达到 900摄氏度 以上的高温,并提供了 CO 还原性气氛。人类早期使用的燃质主要是木材,在氧气不充分的环境下,木材高温燃烧所产生的气态 CO 可以将黏土中红色的氧化铁(Fe2O3) 还原成黑色的四氧化三铁(Fe3O4)。冶金的发现是一个漫长的过程,人类从用石器做 饰品到提炼出第一颗纯铜用了五六千年的时间。
钻井技术拓宽了金属采集渠道。古人为了饮水的需要,发展出了凿井技术。矿石作为 石材,一般储藏于石质山和地下岩,而凿井技术赋予了人类地下采矿的能力;冶金技 术的发展也极大提高了人类上山下地找矿的热情。
1.2 锻造优势明显,顺应装备对于轻量化&高强度的要求
锻铁强度更高、韧性更强、更经济,推进人类进入铁器时代。
锻铁强度、韧性高于青铜,更适合冷兵器的制造。铁本身的韧性与延展性高于铜,通过对高温下铁块的反复锻打,能增强其材料的强度。同等强度之下,铁器的韧性远优于青铜,青铜时代的冷兵器多做成刺戳型的短剑,而铁器时代的冷兵器开始流行用于 劈砍的刀。此外,锻造工艺对金属的延展性、韧性要求很高,作为锻造的主要材料, 铁的发现与大规模使用也促进了锻造工艺的发展。
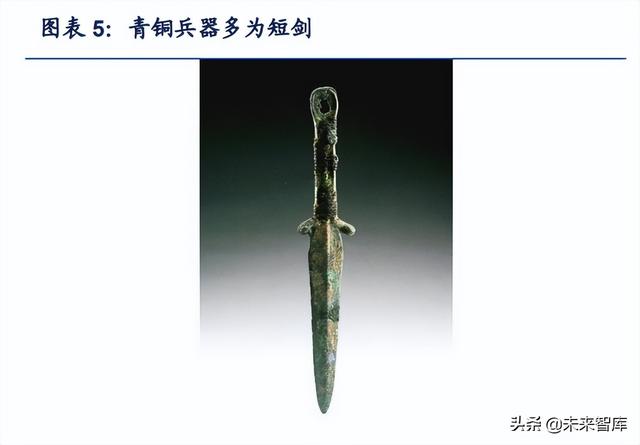
铁在地壳中铁含量相对丰度高于铜,更加经济。地壳当中铁元素丰度大于锡与铜,成 本相对低廉。由于铜本身成本较高,青铜时代,青铜主要用于礼器和兵器,而无法完全取代石器成为主要生产工具。铁器因经济性完全取代了石器成为主要生产工具,更加促进了锻造工艺的发展。
金属成型工艺分类:铸造、塑性成型、机加工、焊接、粉末冶金、金属注射成型、金属半 固态成型、3D 打印等等。其中,铸造和锻造历史最久、应用最广。
相比铸造和机加工,锻造在零件的完整性、纹理流线、零件的灵活性等方面具有优势。
塑性成型通过改变金属显微组织优化金属性能。金属材料在经过塑性变形后,不但改 变了形状和尺寸,而且其内部组织结构和性能随之发生了一系列的变化。金属材料的 显微组织会发生明显的改变,各个晶粒单中除了出现大量的滑移带、孪晶带之外,其 晶粒性转给也会发生变化,即各个晶粒将沿着变形的方向被拉长或压扁,金属内部组织结构发生了变化,进而优化金属的性能。
锻造还提供其他金属加工工艺无法比拟的结构完整性。锻造的主要原材料为金属棒料、 铸锭等。这些原材料在其冶炼、浇注和结晶过程中,不可避免的会产生气孔、缩孔和 树枝状晶等缺陷,因而,铸造工艺很难制造出能胜任需要承受冲击或交变应力的工作 环境的零部件(例如传动主轴、齿圈、连杆、轨道轮等)。锻造消除了会削弱金属零件的内部空隙和气穴。通过分散合金或非金属的偏析,锻造可提供优异的化学均匀性。 可预测的结构完整性降低了零件检查的要求,简化了热处理和机加工,并确保了在现 场负载条件下的最佳零件性能。
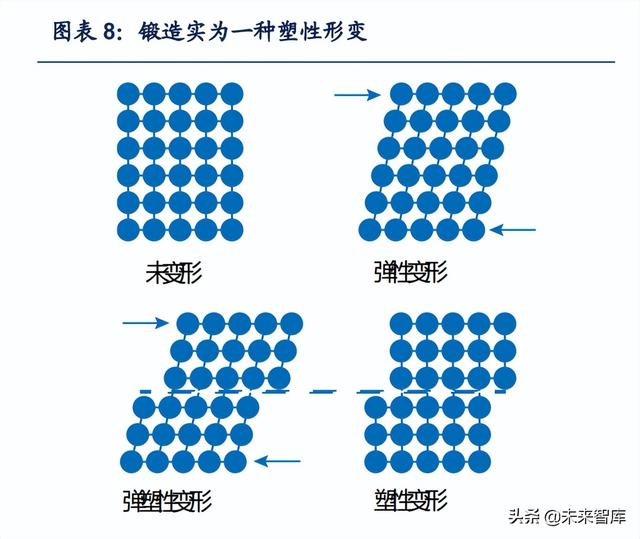
锻造的晶粒特性决定锻造件的方向韧性。通过在严格条件下使加热的金属机械变形, 锻造可以使粗大晶粒细化,得到致密的金属组织,进而得到可预测的晶粒尺寸和流动 特性。在实际操作中,通过对锻件进行预加工,可以改善铸锭的树枝状结构并消除孔 隙,提高锻件的力学性能。这种品质转化为卓越的冶金和机械品质,并在最终零件中提供更好的方向韧性。
锻造件拥有最佳的金属纹理流线。锻造是在加压设备及工(模)具的作用下,使坯料 或铸锭产生局部或全部的塑性变形,以获得一定几何尺寸、形状的零件(或毛坯)并 改善其组织和性能的加工方法。金属材料经过锻造加工后,形状、尺寸稳定性好,组 织均匀,纤维组织合理,具有最佳的综合力学性能。
2. 开刀阔斧打造重型装备,大国竞争的必要重器
2.1 锻造是工业时代兵家必争之技
近代多项理论基础为锻造技术奠基,而 1653 年帕斯卡原理的发现和提出,推动了人类锻 造设备的发展与迭代。锻造技术以塑性成形原理、金属学、摩擦学为理论基础,同时涉及 传热学、物理化学、机械运动学等相关学科,以各种工艺学,如锻造工艺学等,与其它学 科一起支撑着机器制造业。
帕斯卡原理的发现推开了大型锻造设备之门。1653 年,法国物理学家帕斯卡发现不可 压缩静止流体中任意一点受外力产生压强增值后,此压强增值瞬时间传至静止流体各 点,并据此提出了帕斯卡原理运用这一原理,可以在同一个流体系统中连接两个活塞, 通过对小活塞施加小推力,通过流体中的压力传递,就会在大活塞中产生较大的推力。 帕斯卡原理也因此运用在水压机之中,为液压锻造机的发明奠定了基础。
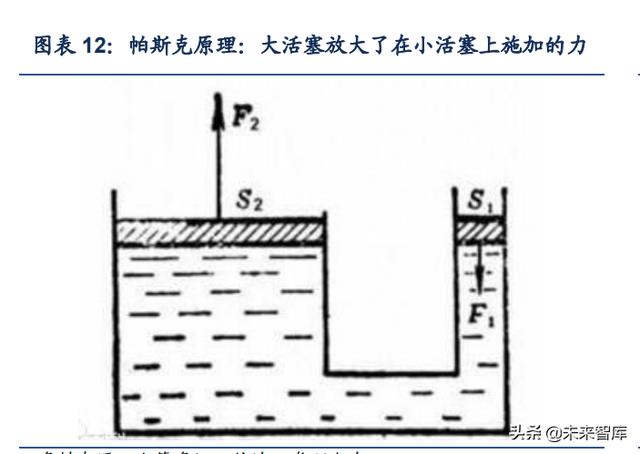
美国最先制造万吨以上锻造设备,大型锻造设备备受美、苏、德、法、捷克斯洛伐克等制 造业强国重视。
1893 年,美国伯利恒钢铁公司制造出世界首台万吨自由锻造水压机,苏、德随即跟上 步伐。20 世纪初,随着重型机械设备的发展,水压机的吨位迅速提高。在 1905 年首 次出现以油为工作介质的油压机,性能得到进一步改善。1934 年,前苏联在新克拉玛 托尔斯克重型机械厂(N M )建成了第一台 10000 吨的水压机。同年,德国研制成 功 7000 吨模锻液压机。此后,德国在 1944 年前相继制造了 30000 吨模锻水压机 1 台、 15000 吨模锻水压机 3 台。
二战结束后大国争相发展大型模锻压机。
1945 年二战结束后,美、苏两国开始意识到大型模锻压机的重要性,以战争赔偿的理 由拆走了德国的 4 台模锻液压机,美国拆走 2 台 15000 吨模锻液压机,前苏联拆走 15000 吨及 30000 吨模锻液压机各 1 台。这些设备也成为美、苏两国制造超大型模锻 压机的技术基础。1947 年,国民党政府也以战争赔偿的理由从日本拆回 5 台 1000- 3000 吨级水压机,这些水压机作为“战利品”,后来成为新中国锻造装备发展的起点。
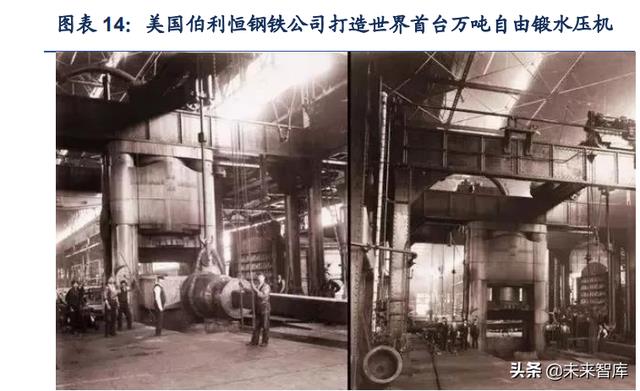
二战结束后各国锻造设备得到快速发展,1950 年,美国开始实施“空军重型压机计划” (The Air F r e e vy Press Pr gr m),决定由联邦政府出资建造两台世界最大的 45000 吨和两台 31500 吨模锻压机。1955 年,美国梅斯塔(MESTA)重型机器厂为 美国铝业(A )建造了 1 台 45000 吨模锻压机和 1 台 31500 吨模锻压机。同年, 美国劳威(LOEWY)公司也为威曼高登(Wym n-G rd n)建成了 1 台 45000 吨模锻压机和 1 台 31500 吨模锻压机。这 4 台大型模锻压机为美国后来称霸世界航空工业 奠定了雄厚的基础。
这个时候捷克斯洛伐克还是以共和国的形式存在的,还没有解体为两个独立的国家, 1956 年,他们成功地在 S ODA 厂投产了 1 台 12000 吨的模锻液压机。后来我国大跃 进时期,为促进重工业发展,从捷克斯洛伐克进口了 1 台 12000 吨的自由锻造水压机, 安装在当时还在筹建中的德阳第二重型机械厂。
前苏联为发展航空工业大力推进锻造业发展。
自 1957 年起,至 1964 年止,前苏联为发展航空航天工业,先后建造了 6 台万吨级以 上的模锻液压机,其中包括2台当时世界最大的75000吨级的模锻液压机、3台30000 吨级的模锻液压机和 1 台 15000 吨级的模锻液压机,这 6 台的主要建造商是新克拉马 托重型机器厂( M3)、乌拉尔重机厂(Y3TM)和新西伯利亚重机厂。
其中新克拉马托重型机器厂( M3),为前苏联建造了两台世界最大的 7.5 万吨级模 锻液压机,分别安装在古比雪夫铝厂和上萨尔达钛厂。这两台当时世界最大的巨型机 器,总高 34.7 米,长 13.6 米,宽 13.3 米,基础深入地下 21.9 米,总重 20500 吨。 工作台尺寸 16 米×3.5 米,采用 12 缸 8 柱上传动,模具空间净高 4.5 米,滑块行程 2000mm。它们是前苏联航空工业体系的国宝级装备,1991 年前苏联解体后,被俄罗 斯继承。该厂现在是俄罗斯最大的钛合金产品制造商——上萨尔达冶金生产联合公司 (VSMPO-AVISMA)。
法国错失锻造发展机遇,航空制造业发展受到影响,必须向别国采购锻压机或者锻压零件。
法国于 1953 年分别在伊索公司和 Cr ut-L ire 公司,建造了两台 2 万吨级模锻水压 机,用于制造航空铝合金锻件,但却一直没有超过 40000 吨的大型模锻压机。1976 年, 法国奥伯杜瓦(Aubet&Duv )特钢公司,向乌克兰新克拉马托重型机器厂( M3), 购买了一台 6.5 万吨模锻水压机,用于生产钛合金模锻件和航空铝合金模锻件。
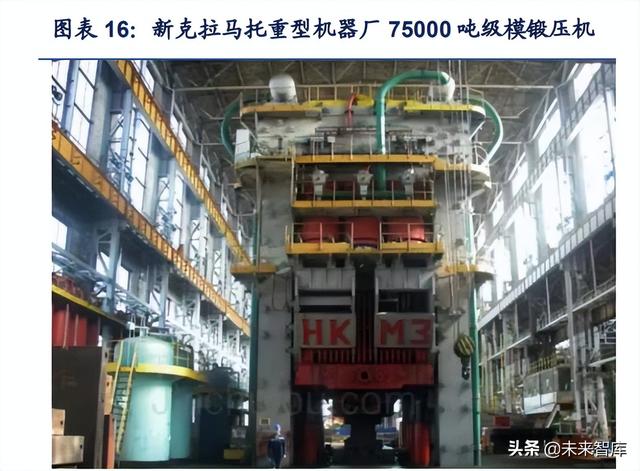
2005 年,法国奥伯杜瓦公司,又从德国辛北尔康普集团(Siempe k mp,1883 年成 立),订购了一台 4 万吨级模锻液压机。但是受限于加工能力,欧洲空中客车公司制造 A380 大型客机时,用的起落架钛合金构件,仍然需要送到俄罗斯的 7.5 万吨级模锻机 上去加工。A380 客机的两个六轮三轴小车式主起落架,承重超过 590 吨,要求寿命达 到 60000 个起落架次;采用 Ti-1023 钛合金锻造,长度达 4.255 米,重达 3210 公斤。 这是目前世界最重的航空钛合金模锻件。
新世纪美国仍为航空航天先进锻造做努力。
2005 年,美国铝业收购了俄罗斯萨马拉冶金厂的 75000 吨级模锻液压机,萨马拉冶金 厂就是前苏联解体前的古比雪夫铝厂。2001 年,美国加州舒尔茨钢厂就成功建造了 1 台 40000 吨级的模锻压机。然而这并不能满足快速发展的美国航空工业。
投资 1.1亿美元翻新 1955年在俄亥俄州克利夫兰工厂建成的 45000吨模锻压机。2015 年,位于美国洛杉矶市的韦伯金属公司(Weber Met s)向德国西马克集团梅尔公司订 购了 1 台 60000 吨级 540MN 下拉式液压模锻机。
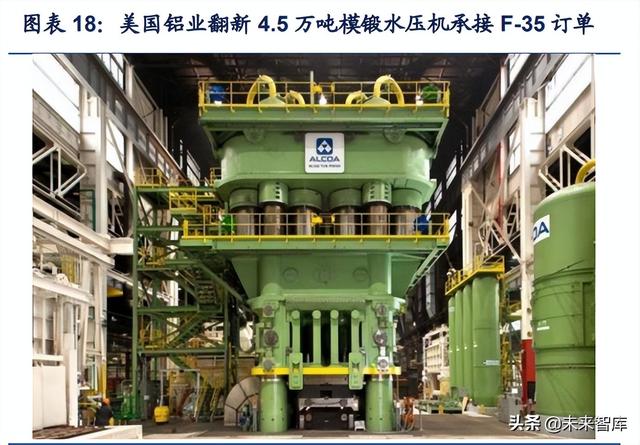
2.2 我国锻造工业发展定位高,发展快
我国锻造工业起步较晚,锻造工艺及设备制造工艺经历了数十年的发展。从修复安装 日本战后陪产 20MN 自由锻造机,到目前在精密模锻、等温模锻领域达到世界领先, 历经艰辛。自建国至今,我国自由锤锻呈现从蒸汽动力向电业驱动的动力转型,自由 锻造液压机逐渐快速化、联动化;模锻锤从气动逐渐转向电液驱动,螺旋压力机日渐 离合器式电动化,模锻液压机得到了长足发展,为精密模锻和等温模锻的发展创造了 国际竞争优势。
1967 年,中国第一重型机器厂建成亚洲最大的 30000 吨级模锻水压机,装备重庆西 南铝加工厂(冶金部 112 厂)。该机于 1973 年 9 月投产,并服役至今,对于提高我国 特种高强度合金锻件加工能力,做出重要贡献,被誉为中国工业“四大国宝”之一。
停滞 40 年后迎来新一轮快速发展。
我国自 1973 年投产第 1 台 30000 吨级的模锻压机后,停滞了将近 40 年,2003 年, 中国工程院师昌绪院士,组织了由全国 31 个企事业单位,包括航空、机械、冶金、教 育等部门的五位院士和 17 位专家,组成了《发展我国大型锻压装备研究——建设 8 万 吨模锻液压机及其配套设备》咨询组,再次向国家建议:在“十一五”期间建造一台 8 万吨级模锻液压机,和一台 1.5 万吨难变形合金挤压机,以使我国尽快获得钛合金、 高温合金、超高强度合金钢大型整体精化模锻件的制造能力。
2007 年 11 月 15 日,国家发改委最终批复,同意中国二重集团,联合中南大学、燕山 大学、西安重型机械研究院等单位,设计制造 8 万吨级模锻压机,项目总投资 15.17 亿元,其中企业自筹 3.03 亿元,申请国家拨款 4 亿元,申请银行贷款 8 亿元。规划年 产航空、电力、石化等钛 铝合金模锻件 1.5 万件,重约 1.34 万吨。
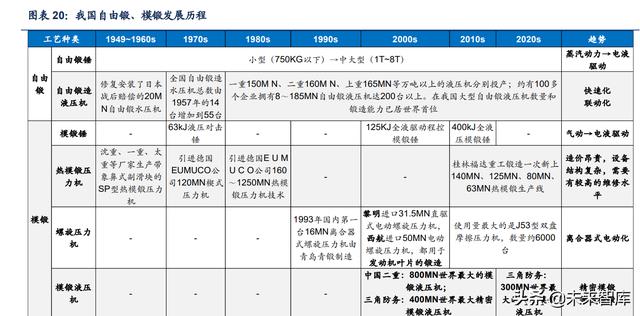
2010 年前后我国爆发式地研制了多台大型压机,仅 2012 年建成的就有 30000 吨(昆 仑重工)、40000 吨(三角航空)、80000 吨(德阳二重)模锻压机各一台。
2012 年 3 月 3 日,中国首台 40000 吨级模锻液压机,在西安阎良三角航空科技有限责 任公司进行热试车,并顺利锻造出首个大型盘类件产品。该机是目前世界最大的单缸 模锻液压机,采用钢丝缠绕预应力结构。(报告来源:未来智库)
我国锻造设备跻身世界一流。
2013 年,德阳二重自主研制世界最大的 8 万吨级模锻液压机投产,一举打破了前苏联 保持了 51 年的世界纪录,实现了我国锻造产品从高端向顶级的跨越,关键大型锻件受 制于国外的时代彻底结束。这台 8 万吨级模锻液压机,地上高 27 米、地下 15 米,总 高 42 米,设备总重 2.2 万吨,2018 年,C919 大飞机的最大、最复杂的关键承力锻件 ——主起外筒实现国产化,就是这台 80000 吨级的模锻液压机完成的。
目前世界上拥有 4 万吨级以上模锻压机的国家,只有中国、美国、俄罗斯和法国。巨 型模锻液压机,是象征重工业实力的国宝级战略装备,是衡量一个国家工业实力和军 工能力的重要标志,世界上能研制的国家屈指可数。
我国拥有超前的模锻液压机技术储备。清华大学已研发出 16 万吨模锻液压机,是俄 罗斯 7.5 万吨压机的 2 倍多、美国 4.5 万吨的 3.5 倍多。
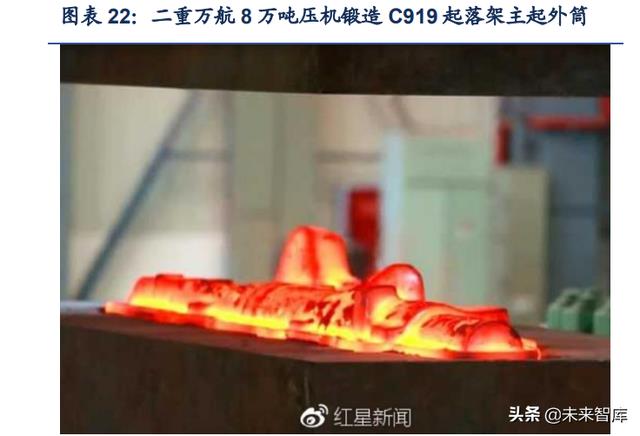
3. 我国锻造工业体系完整、发展快、壁垒高
3.1 我国现已形成较为完整的锻造工业体系
我国锻造工业体系较为完善。我国锻造工业体系目前已经基本满足国内经济建设、国防建 设、基础设施建设的需要,行业继续保持全球最大的锻造行业发展规模,并已具备支撑 “走出去”战略布局的能力。我国锻造工业现已覆盖航空、航天、航海、风电、石化、汽 车、医疗、重型设备等等多个领域。
锻造行业的上游行业主要为各类金属材料冶炼企业,如碳钢、不锈钢、合金钢、高温 合金、钛合金、铝合金等,上游原材料的供应能力和技术水平直接影响锻造行业的发 展水平。
锻造行业的下游行业为各类装备制造企业,应用领域非常广泛。如航空、航天、船舶、 电力(风电、核电、水电、火电)、石化、铁路及其他机械行业。
我国锻造企业数量众多,中低端竞争激烈而高端锻造一片蓝海。大部分锻造企业主要 从事普通碳钢、合金钢、不锈钢材料等锻件的生产,对高温合金、钛合金、铝合金、 镁合金等特种合金材料的加工能力整体不足、产品技术含量及附加值相对较低、工艺 水平相对落后。
3.2 我国锻造“十三五”期间发展迅速
我国锻造工业在“十三五”期间的迅速发展得益于全球经济与技术的发展。全球经济的发 展,尤其是互联网、数字化和信息化技术的发展,带来了锻造行业格局的大变化;我国节 能环保要求的日益深入,航空航天、高端装备、新能源汽车、轨道交通等领域轻量化高效 化发展日新月异,锻造原材料从普通钢材向高强度钢材发展,从黑色金属向有色金属发展,锻造工艺取得很大进步。
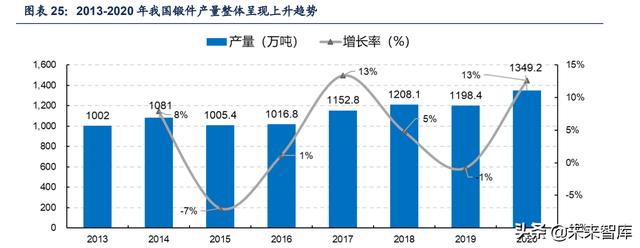
“十三五”期间我国锻造产量逐年增长。自2015年后,我国锻件产量整体呈现持续增 长趋势,到 2019 年达到 1198.4 万吨,同比增长 5.04%;2020 年中国锻件产量达到 1349.2 万吨,同比增长 12.58%。从锻件产量看,目前我国已经成为全球第一的锻造 大国并持续领先。
“十三五”期间我国模锻件产量年复合增长率达 8.08%。我国模锻件产量自 2017 年 起增速开始下滑,2019 年我国模锻件产量出现下降,而 2020 年模锻件产量又以 14% 的增速一路飙升至 885 万吨。
“十三五”期间我国汽车模锻件产量年复合增长率达 6.78%。汽车模锻件是我国模锻 行业主要生产产品,2017-2019 年我国汽车模锻件产量与汽车产量走势保持一致,均 呈下降态势,2020 年开始回升,并创下 2015 年以来新高,2020 年汽车模锻件产量为 584 万吨,较 2019 年的 489 万吨同比增长 19.4%,占模锻件总产量的 66.0%。
相比于 2016 年及以前,汽车模锻件在模锻件中的占比有所下降。由 2016 年的 72%降 至 2020 年的 66%,相应的结构空间被航空、航天等大型部件的高端模锻所替代。
我国自由锻产量于 2016 年显著下降,2017-2020 年间年复合增长率 8.7%。2020 年我 国自由锻件产量达到 464.2 万吨,较 2019 年同比增长 10%。
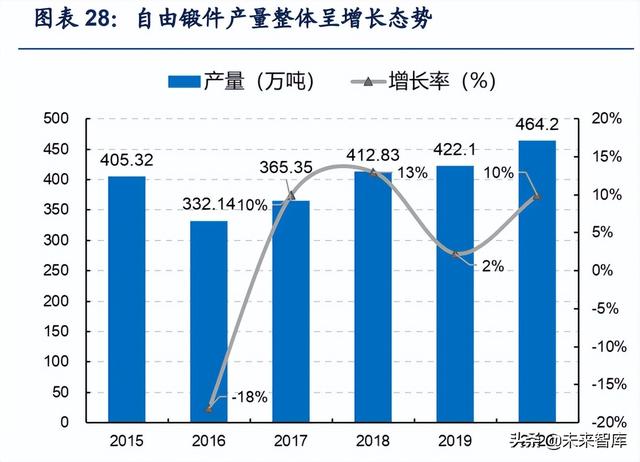
随着国防军工与航空航天事业的发展,我国环锻件的市场需求持续增加,2017-2020 年间年复合增长率 14.4%。2020 年实现 124.7 万吨产量,较 2019 年同比增长 62%, 占自由锻件产量比例为 27%。环锻属于高端锻造工艺,主要应用于航空发动机、航天 装备,随着我国军用飞机和发动机的列装、民用航空发动机国产化以及航天事业的快 速发展,未来我国环锻件市场有望提速发展。
我国锻造产品登入国际一流。如民用核电大型锻件、大飞机的起落架、承力框、燃气 轮机涡轮盘锻件、快堆支撑环锻件、核电锻造泵壳的国产化等等,展示了“十三五” 期间锻造行业发展的实际水平。
锻造设备大型化、自动化、数字化和信息化充分得到发展。如大型电动螺旋压力机、 大型热模锻压机、大型模锻液压机、大型摩擦压力机及大型辗环机、大型自由锻液压 机数量不断增加,生产线周边配套装备的自动化程度明显上升。
“十三五”期间,锻造在工艺技术及装备技术方面取得了较大的突破。面对激烈的全 球化市场竞争,企业管理的内涵已从生产能力的提升转向以提质、增效、降本为主的 内生动力变革。产品、工艺技术、模具和装备技术都产生了较大的突破。锻造产品实 现多元化、复合化,产品结构实现整体化、模块化;工艺技术上实现了材料高强化、 轻量化、多样化,正在向“控形”、“控性”、冲锻结合等复合化工艺发展;模具和装备 技术正朝着自动化、数字化、信息化方向发展。
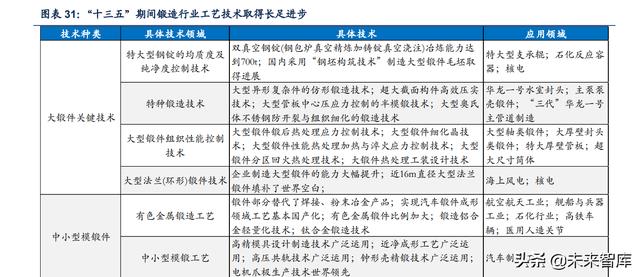
3.3 政策红利赋予锻造工业超高定位
基于锻造行业在国民经济中的基础地位,改革开放以来,政府和行业主管部门在政策上均 给予了大力支持。由于锻造工业介于产业链的中间位置,面向的是高端装备制造业,其上 游的高端材料行业和下游的高端装备制造业均享受多项国家政策支持,这些政策促进了整 个行业多向、协同发展。
2006 年,国务院发布《国家中长期科学和技术发展纲要(2006 年-2020 年)》,提出 “开发大型及特殊零部件成形及加工技术”。
2011 年,国务院发布《工业转型升级“十二五”规划》明确“加强铸、锻、焊、热处理 和表面处理等基础工艺研究”、“推进精密工模具的创新发展”;国家发改委、科技部、 工信部、商务部、国家知识产权局联合发布《当前优先发展的高技术产业化重点领域 指南(2011 年度)》,将大型构建的锻造列为需要优先发展的高技术产业重点领域。
2015 年,中国锻压协会发布《锻造行业“十三五”发展纲要》,提出配合航空发动机 和燃气轮机等下游产业发展的规划,聚焦提升基础材料、核心基础零部件(元器件)、 先进基础工艺、产业基础基础的“四基”提升计划。
2016 年,质检总局、国家标准委、工信部联合发布《装备制造业标准化和质量提升规 划》,强调研究制定金属成型、金属加工、热处理、锻压、铸造、焊接、表面工程等基 础工艺标准,提升可靠性和寿命指标。同年国务院发布《“十三五”国家战略性新兴产 业发展规划》,提出掌握铝锂合金、复合材料等加工制造核心技术。
2021 年,中国锻压协会发布《中国锻造行业“十四五”发展纲要》,提出重点发展基 础核心技术,如基础材料、基础核心零部件、核心软件等,解决制约行业发展的瓶颈 问题,增强板、补短板。
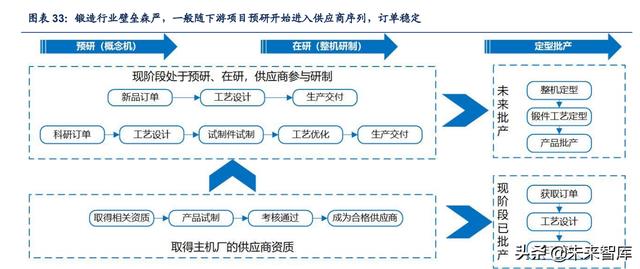
上下游政策传导效应显著。作为高端制造工艺,锻造行业处于高端原材料与高端装备制造 业的中游,上游的原材料发展政策、下游国防军工、航空、航天、船舶、电力(风电、核 电、火电)、石化、汽车等制造业均为决定国民经济发展水平的重点高端制造行业,相关政 策均认可和强调了锻造行业的基础和决定性地位。 国防军工行业推出政策鼓励民间资本进入国防军工行业。随着军民结合、寓军于民的武器 装备科研生产体系建设进一步推进,锻造行业市场空间进一步打开。
3.4 锻造行业具有高壁垒,强者恒强
锻造行业高壁垒一:市场壁垒
高端装备制造业长周期呈现“定制化”色彩,成就锻造行业的市场壁垒。锻件产品有多规格、 多品种、定制化的特点,锻件行业的发展与下游客户的定制需求密不可分,因此,需要与 主要客户建立相对稳定的合作伙伴关系。
民用领域壁垒在于进入下游主机厂合格供应商目录。一方面,在与客户确立合作关系 前,客户对供应商考核程序复杂,考察周期较长,对产品品质、产品规格、供应时间 等均有特定要求;另一方面,双方一旦确立合作关系,则该合作关系一般会相对稳定, 其它同类厂商进入存在一定难度。
军工领域壁垒受技术、型号、质控、稳定性等诸多方面影响。一种新装备的推出需要 经过锻件产品制造商、部件制造商、研究院所、主机厂等长时间的设计、研究、试验、 验证、改型等程序,并经军方检验后方能最终定型生产;同时,军工客户对各供应商 提供的产品的质量、技术等要求极高,为保证产品的一致性和稳定性,一旦确认一种装备的供应关系,通常该装备的供应关系会长期且稳定。因此,本行业的后进入者将 面临着一定的品牌和市场壁垒。
预研机制促成长期定制化上下游模式。航空装备研制周期长,为了保证产品的稳定性 和一致性,以及控制研制周期,主机厂通常与供应商紧密合作,一般自项目预研起, 就展开了同供应商长达数十年的合作。待项目进入批产阶段后,供应商的销售模式会 保持“订单→生产”的模式,通常会获得主机厂的预付款,呈现“定制化”色彩。
锻造企业一般侧重某一领域,同时向其他领域延伸。国内不同的锻造企业在主要方向 上术业有专攻。如三角防务偏重于航空航天锻件,技术上偏向于模锻和自由锻;派克 新材和航宇科技则在技术上偏向于辗环,业务范围包括船舶锻件、电力锻件、航空锻 件、航天锻件、石化锻件;通裕重工则主营电力锻件,包括风电、火电和核电。
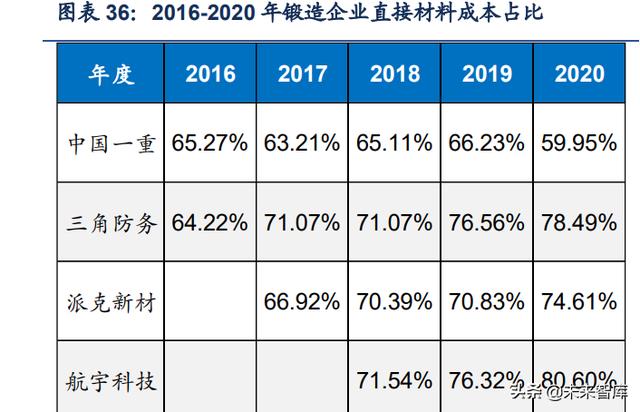
锻造行业高壁垒二:设备和资金壁垒
先进锻造设备建设周期长,建设成本高昂。我国历史上曾依赖进口,现已具备自主研发大 型模锻液压机的能力,代表设备有三角防务的 400MN 大型模锻液压机、300MN 等温模锻 液压机。辗制环形锻件、大型自由锻件对设备要求较高,如锻压机、辗环机等大型设备, 进口设备单位价值往往过亿,对资金要求较高。
原材料成本占比高,材料周转占用大量资金。原材料采购及生产经营周转需占用大量流动 资金,因此,涉足本行业的企业必须具备强大的资金实力或筹资能力,对新进入者形成较 高的资金壁垒。2016-2020 年间,三角防务、派克新材、航宇科技三家锻造企业直接材料 占主营业务成本 70%-80%;而从事机械加工,包含锻造业务的中国一重,其直接材料成本 也占据了主营业务成本的 65%左右。
锻造行业高壁垒三:生产技术壁垒
锻造行业生产技术壁垒高。锻件产品有多规格、多品种、定制化的特点,先进的生产设备、 精细的质量管理、生产经验的长期积累是锻件制造商得以长期发展的重要保障。为保证产 品的一致性、稳定性、可靠性及先进性,企业需要大量专业研发人员及熟练技术员工,而 这些专业技术人才的培养及其技术的掌握需要企业长时间的积累。因而,锻造行业具有一 定的生产经验及人才壁垒。
原材料必须选择难变形材料。高性能、长寿命、高可靠性,是航空航天等领域高端装 备锻件制造追求的永恒目标,以满足高温、高压、高转速、交变负载等极端服役条件。 采用轻质、高强度、耐高温等航空难变形金属材料,比如高温合金、钛合金、铝合金、 高强度钢等,是实现这一目标的重要途径。
材料的特殊性为锻造带来诸多难点。由于高温合金、钛合金、铝合金、高强度钢等材 料合金化程度高、成分复杂,在实际加工当中存在诸多难点:1)塑性差,锻造过程容 易开裂,需要严格控制变形程度;2)变形抗力高、流动性差,需要大载荷设备;3) 锻造温度范围窄,易产生混晶、组织不均匀问题,增加锻造火次和操作难度;4)形程度、变形速率和应力应变状态等较为敏感,锻造过程难以控制;5)组织状态复杂多样, 且对工艺条件较为敏感,组织性能难以控制。
难变形材料锻造难度大,对锻造工艺和热处理工艺都有非常严格的要求。生产过程必 须严格控制各项工艺参数,形成配套完整的控制体系和控制规范,才能使产品的性能 指标达到使用要求。因此锻造企业取得这些工艺参数和形成有效的控制体系,不但需 要具备深厚的材料和锻造理论知识,而且需要进行大量的反复计算分析、工程试验验 证和长期的工程实践。经过验证的成熟生产工艺是该行业的主要技术壁垒之一。
锻造行业高壁垒四:军工配套企业资质壁垒
军工配套企业具有较高的资质要求,对新进者形成较高的壁垒。国家对于民营企业参与军 工产品供应有更加严格的资质要求,需要取得《武器装备科研生产许可证》、《保密资格单 位证书》、《装备承制单位资格证书》等资质,且民营企业需经过军方对其产品性能、质量 控制、技术水平、研发能力等进行一系列综合评估且达到要求后,才能与军工企业进行合 作为其提供产品。
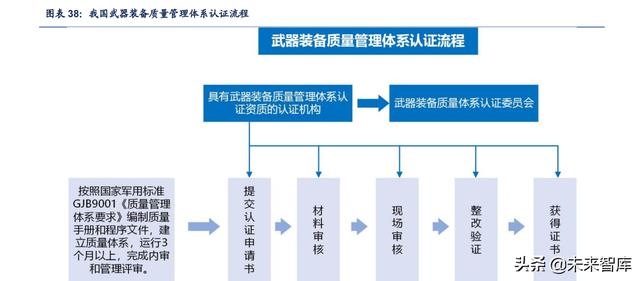
从取得资质到业绩起量,一般需要经过 4-6 年的周期。因军工行业存在预研机制,锻造企 业需要参与装备研制的全周期,经历漫长的试制或小批量生产阶段,从取得资质、参与预 研到批产交付、业绩起量,一般需要经过 4-6 年的周期。
4. 我国锻造行业市场广阔,航空航天锻造将带来千亿级市场
4.1 我国航空锻造迎来最佳放量时期,催生千亿市场
飞机被称为“工业之花”和“技术发展的火车头”,产业链长,覆盖面广。为保持国家经济 活力、提高公众生活质量和国家安全水平、带动相关行业发展具有重要作用。
锻件是飞机的关键部件。锻件制成的零件重量约占飞机机体结构重量的 20%~35%和 发动机结构重量的 30%~45%,是决定飞机和发动机的可靠性、寿命和经济性的重要 因素之一。航空发动机的涡轮盘、后轴颈(空心轴)、叶片,机身的肋筋板、支架、机 翼梁、吊挂,起落架的活塞杆、外筒等都是涉及飞机安全的重要锻件。由于航空锻件 所用材料以及零件工作环境的特殊性,航空锻造成为技术含量最高、质量控制要求最 严的行业。在装备的特殊部位应用不可取代。
飞机机身中的锻件主要集中在主结构承力件上。包括承力框、梁框架、起落架、机翼、 垂尾等主结构件;风挡、舱门边缘、机载武器吊挂等等需要长期承受交变应力的部件。 航空发动机价值约占军用飞机的 25%、民用飞机的 22%。
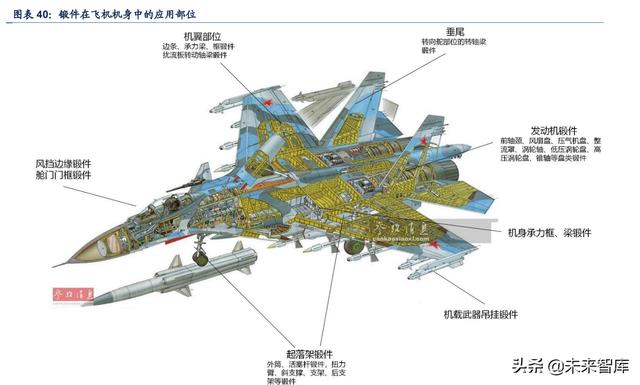
立鼎产业研究《飞机机体材料结构发展阶段及航空零部件制造价值占比分析》一文指 出:军用飞机和民用飞机因为用途的显著不同,各组成部分价值占比差别较大。对于 军用飞机,动力系统占整机价值比最高,达 25%,航电系统次之,机体结构占比约为 20%;对于民机,机体结构占整机比超过 1 3,达到 36%,动力系统次之,航电和机 电系统合计占 30%。
证券导报在《中航重机:华丽转身整机制造商 钢筋铁骨锻造者》一文中指出:按价值 计算,锻件在飞机构件中价值占比约 6%~9%,在飞机发动机中价值占比约 15%-20%。
航空锻造驱动因素一:军用飞机进入放量生产列装阶段,航空锻造市场迎来黄金时期。
从数量上看,我国军机总量与美俄存在较大差距,军机增补空间很大。截至2021年, 美国拥有军机数量为 13246 架,占比 25%,数量位居世界第一;其次是俄罗斯,数量 达到 4173 架,占比 8%。我国拥有军机数量为 3285 架,占比为 6%。横向对标美、 俄,我国军机总数占比分别为:24.80%、78.72%。未来为应对日益白热化的国际竞 争,军机增补空间很大。
从代际上看,我国军机亟需迭代升级。美国和俄罗斯均已淘汰第二代战斗机,完成了 向第三代、第四代战斗机的转型。而中国目前正在逐步淘汰二代机、向三代机转型的 过程当中,仍有大量二代机在服役。
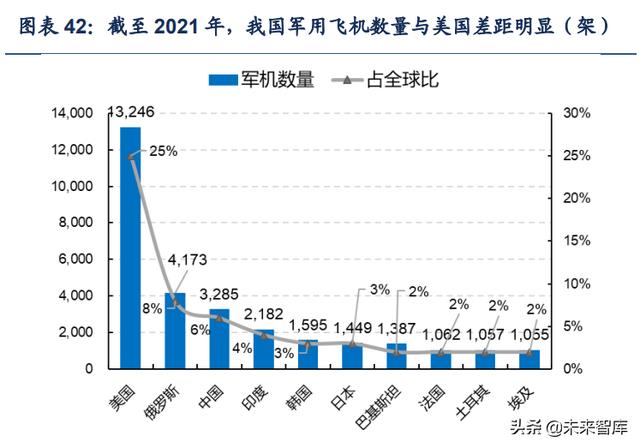
航空发动机作为飞机的心脏,对材料具有超高要求,成为航空锻造新增长极。
航空发动机对制造工艺要求很高。高性能航空发动机追求的是在极有限的自身重量与 工作空间、极恶劣的工作条件下保证长期稳定的服役性能,其制造技术要求极高,是 一种极端制造情形。
轻量化结构、难变形原材料、复杂型面薄壁零件对航空发动机制造工艺提出高要求。 为达到高的推重比性能要求,航空发动机大量采用复杂的整体轻量结构,如空心叶片、 宽弦叶片、整体叶盘等,以做到最大程度的减重;同时高性能的钛合金、高温合金以 及复合材料也大量应用,而这些材料都属于典型的难加工材料;另外航空发动机关重 件多属于复杂型面薄壁零件,对加工精度和表面质量的要求极高。
精密锻造在航空发动机制造中至关重要。贾丽等在《航空发动机零部件精密制造技术》 一文中指出:目前航空发动机的零部件锻件毛坯占毛坯总重量的 50%以上,精密锻造 技术在航空发动机制造企业获得了重视并被广泛采用。精密锻压技术制造的发动机零 部件的毛坯,具有精确的毛坯外形,可以实现小切削余量甚至无切削余量的空心涡轮 叶片、整体涡轮以及其他部件的加工制造。随着等温模锻、超塑性等温模锻等先进的 锻造技术的发展应用,航空发动机制造企业已经可以制造无偏析超细晶粒毛坯,并批 量生产无余量精锻叶片。
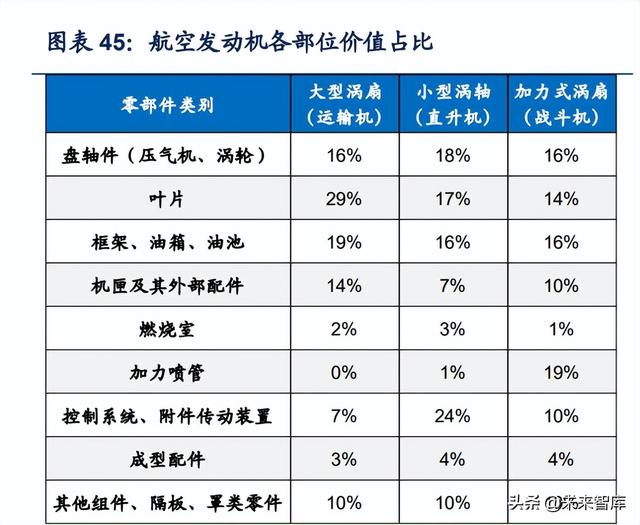
航空发动机环锻件主要包括航空发动机环锻件和航空发动机机匣。其中,航空发动机 环锻件包括除机匣外的其他环形锻件,主要包括封严环、支承环、风扇法兰环、固定 环、压缩机级间挡圈、燃烧室喷管外壁环件、涡轮导向环、整流环等;机匣包括风扇 机匣、压气机机匣、燃烧室外机匣、高压涡轮机匣、低压涡轮机匣等。
锻件在航空发动机中具有核心地位。前瞻产业研究院发布的《2013-2017 年中国航空发动 机行业市场前瞻与投资战略规划分析报告》一文中分析了军用飞机航空发动机中各部位的 价值占比,其中,大量使用锻件的盘轴件、叶片、框架、机匣、燃烧室、传动装置等占据了整个发动机价值的 70%以上,由此可见,锻件在航空发动机中具有核心地位。
发动机属于消耗品,在全生命周期内大约翻修 4 次。其性能、耗油量与翻修次数有关,航 空发动机翻修次数影响翻修成本。
推力的衰减和油耗的增加是发动机翻修的主要原因。航空发动机翻修令航空发动机的 零部件因长期处于高温、高压的工作环境当中,随着使用时间的增长,部分零件会出 现疲劳破裂失效,发动机的性能也因此衰减,发动机耗油量也因此提升。寿命期内, 发动机性能衰减应满足 GJB241A-2010《航空涡轮喷气和涡轮风扇发动机通用规范》 相关要求,推力衰减量不超过 5%,耗油率增加量不超过 5%。当发动机性能衰减到此 红线时,应返厂进行翻修,一般发动机翻修可以使其性能得到恢复。
发动机翻修可以使性能恢复,但翻修次数越多,可靠性恢复越有限。在首个翻修期内, 早期故障多,平均故障发生时间(MTBF)较短,每个翻修期内,大修后可靠性恢得 到恢复(MTBF 增加),但随着使用时间的增加 MTBF 又逐步下降。在全生命周期中, 每次大修的间隔时间逐渐缩短,大修逐渐频繁,每次大修后 MTBF 逐渐缩短。
航空发动机一般最多可以翻修 4 次。董红联等在《航空发动机寿命控制体系和寿命评定方法》一文中描述了研究发动机性能、耗油量与翻修次数关系的试验。试验选取 35 台不同翻修次数的发动机进行性能复验,发现随着修理次数的增加,发动机性能衰减 速率逐渐加快,并预测发动机使用至第五次大修时,其性能和耗油量已不满足 GJB 241-2020 的要求。即发动机在全生命周期中最多只能翻修 4 次。而在航空发动机实际 运行当中,更要参考翻修成本增加带来的经济性问题,原则上发动机大修成本不应超 过新机采购费用的 50%。
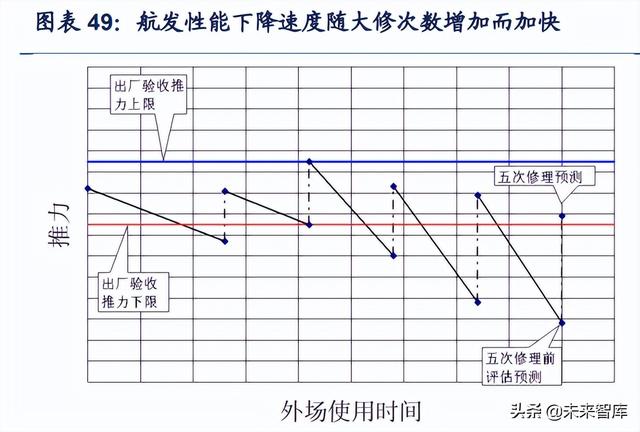
大修换件率随大修次数逐渐增加,具体情况为:首次大修为 9.8%,二次大修为 11.91%,三次大修为 12.38%,四次大修为 14.74%。换件率、试车合格率是评估修理 损伤和修理经济性的重要指标。发动机盘、轴、叶片、机匣等锻造件均为影响使用安 全且价值量较高的重要零件。根据现有的空军值班和训练计划,假设我国军机平均每年执飞 240-300 小时,以 240 小时 年计算战斗机的执飞时间,以 120 小时估计其他机型的执飞时间,可以估计航空 发动机的日历寿命。(报告来源:未来智库)
航空锻造驱动因素二:国产大飞机牵引民机零部件锻造行业腾飞。
截至 2020 年底, 民航全行业运输飞机期末在册数为 3903 架,其中:客运飞机 3717 架,分别是宽体 458 架、窄体 3058 架、支线 201 架;货运飞机 186 架。截至目前,我国自主研制的 90 座级支线客机——ARJ21-700 已经交付运营 66 架;190 座级干线客机 C919 订单已 达 815 架;280 座级远程干线客机 CR929 已经完成项目研制 G3 转阶段。
根据中国 GDP 年均 增长速度预测,中国的旅客周转量年均增长率为 5.7%,机队年均增长率为 5.2%。未 来二十年,中国航空市场将接收 50 座级以上客机 9,084 架,价值约 1.4 万亿美元(以2020 年目录价格为基础)。其中 50 座级以上涡扇支线客机 953 架,120 座级以上单通 道喷气客机 6,295 架,250 座级以上双通道喷气客机 1,836 架。到 2040 年,中国的机 队规模将达到 9,957 架,占全球客机机队比例 22%,成为全球最大的单一航空市场。
民用航空发动机寿命一般长于军用航空发动机。计量民用航发一般有两种方法,其一 是发动机循环次数,其二是发动机小时寿命。本文以发动机小时寿命作为测算依据。 未来窄体干线客机将是飞机增长的主力,新一代航空发动机的首次翻修间隔时间可以 达到 15000-20000 小时,远长于军用航空发动机。而主流航空公司,如国航、东航、 南航,其飞机日利用率可以达到约 10 小时,平均每架机每年执飞约 3650 小时。我们 据此估计民航发动机的日历翻修间隔为 4.11 年-5.48 年,航发 OEM 一般规定大修间隔 为 5 年。
航空锻造驱动因素三:我国民用航空转包业务步入快速发展期,正在向第一梯队拔升。
航空“转包”生产是全球航空飞机及发动机制造商普遍采用的一种基于“主制造商-供应商” 的供应链合作模式,随着我国技术和工艺水平的提升,叠加国际航空制造巨头降本的需要, 我国民用航空转包业务步入快速发展期。 国际航空工业转包大体分三大梯队,我国尚处第二梯队,正在向第一梯队拔升。
我国的航空工业外贸转包生产始于 1980年,先后与美国波音、欧洲空客、加拿大庞巴 迪、巴西航空工业等世界先进飞机制造公司以及美国 GE 公司、英国罗罗公司、美国 普惠公司等发动机制造公司简历了工业合作关系,开展了广泛的航空零部件外贸转包 生产,项目涉及机头、机翼、机身、尾段、舱门、发动机环锻件、机匣、叶片等等多 种产品。而目前,中国航空转包业务处于高速发展时期。
国际航空工业转包业务大体分为三大梯队,我国处于第二梯队,主要面向机体结构件 和航发零件的制造、部件的装配。第一梯队主要面向设计开发、工程制造和大部件集 成,技术难度复杂,附加值高,参与者以美国、欧洲、日本为代表;第二梯队主要面 向机体结构件制造、航发零件的制造及部件的装配,技术难度和附加值居中,参与者 以我国、韩国、墨西哥、突尼斯为代表;第三梯队主要面向零件组件供应,技术难度 和附加值低,参与者以俄罗斯、印度、马来西亚为代表。
我国航空工业外贸转包正在向第一梯队拔升。随着2017年空客(天津)总装有限公司 的成立和 2018年波音(舟山)交付中心的落成,我国航空工业外贸转包正式吹响了向 全球第一梯队拔升的号角,开始由零部件转包迈向总装、交付的新台阶。
我国航空工业转包业务交付金额逐年上升。据《中国民用航空工业年鉴 2020》统计, 2019 年我国民用航空产品转包生产交付金额 25.6 亿美元,同比增加 40.5%,其中飞机零 部件 14.4 亿美元,同比增长 36.0%;发动机零部件 7.0 亿美元,同比增长 2.5%;民用航 空机载系统和设备零部件 1.0 亿美元,同比增长 11.2 倍;其他民用航空产品及零部件 3.2 亿美元,同比增长 3.4倍。转包生产新增订单 22.3亿美元,同比增长 1.1%;储备订单 46.8 亿美元,同比减少 13.5%。
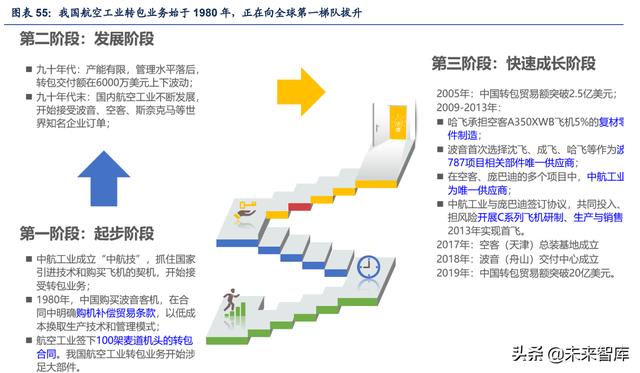
中航工业和中国航发为承接航空国际转包业务主力,民营企业参与广泛,发展势头迅猛, 相关参与方均取得国际航空/航发巨头合格供应商资质。
机体结构件的转包业务主要集中于机体结构零件和部件的生产。参与方式逐步由提供 零件分包生产向部组件和大部段集中交付演进,空客(天津)总装基地的落成更是将 我国对航空转包项目推向了总装的环节。参与厂商有中航工业旗下的西飞、沈飞、成 飞、哈飞、昌飞、洪都和中国商飞旗下的上飞公司等。
航空发动机转包业务主要集中于轴、环件、机匣、叶片的制造。参与厂商主要是中国 航发旗下的黎阳、黎明,中航重机旗下的宏远、安大,以及民营企业航宇科技等。
航空转包承接商均取得了国际航空巨头的相关资质。机体业务参与商取得了波音、空 客、巴航工业、庞巴迪等飞机著制造商的合格供应商资质;航发业务转包参与者包括 中航重机旗下的安大锻造、宏远锻造,航宇科技,派克新材等,相关参与厂商已全部 或部分取得 GE、罗罗、赛峰、美捷特、普惠、柯林斯、霍尼韦尔、MTU 等航发巨头 的合格供应商资质。
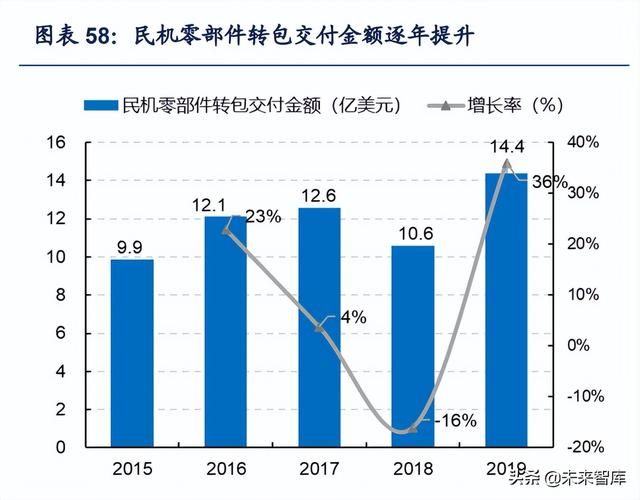
技术“内功”提升+降本“外需”扩大,未来航空锻造转包业务将更上“新台阶”。
我国航空锻造技术和工艺水平的提升拉动国际航空转包业务向国内转移。随着中国航 空零部件制造商的涌现,生产工艺和技术水平不断提高,产品质量和稳定性能够满足 国际航空发动机制造商的高品质要求。
降本的需要推动国际航空巨头扩大对我国的航空锻造业务外包。出于降低成本、提高 盈利能力的考虑,国际航空零部件转包业务仍将继续向我国转移,为我国航空锻造、 航发环锻件研制、生产企业带来更多的发展机遇。
4.2 卫星发射刺激运载火箭对航天锻件的需求
航天工业是国家战略性产业,是维护国家主权领土完整和政治安全的重要保障。航天装备 水平是代表一国航天能力的核心标志,也是衡量国家综合国力的重要标志之一。经过建国 以来几十年的努力,我国航天工业已经由最初的单纯仿制逐步发展到目前自行研制为主, 而且正向低成本、快速反应制造的方向发展,在一些领域实现了相当数量关键工艺技术的 突破,有些已接近国际先进水平。航天产业是我国少数几个水平先进、可在国际市场上与 发达国家竞争的产业之一。
运载火箭是航天发展关键装备。运载火箭作为将卫星、飞船、空间站、深空探测器等推入 预定轨道的载体,其发展与后者的发展状况紧密相关,为保证我国卫星、空间站、载人航 天与探月工程等重大航天工程的顺利推进,我国运载火箭的发展也十分迅速。截至目前, 具有自主知识产权和较强国际竞争力的“长征”系列运载火箭已成为我国运载火箭的主力, 长征系列运载火箭具备发射低、中、高不同轨道、不同类型卫星的能力,截至 2021 年 12 月 30 日,我国长征系列运载火箭已经发射 405 次。
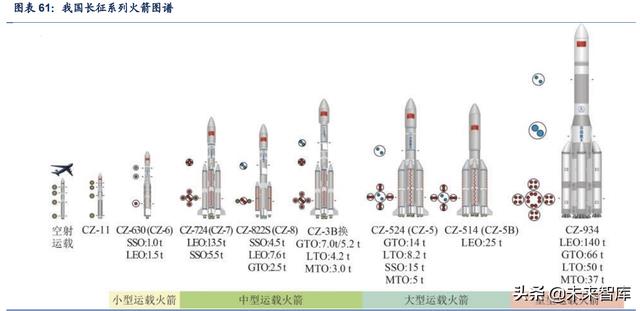
我国目前主要的运载火箭是长征系列火箭,它的技术发展起步于 20 世纪 50 年代。在国家 大力支持下,经过几代航天人的不懈努力,先后研制了长征一号、长征二号、长征三号、 长征四号等 15 个型号的长征系列运载火箭,已经初步具备了较为完整的运载能力。实现了 从常温推进剂到低温推进剂、从串联到捆绑、从一箭单星到一箭多星、从发射卫星到发射 载人飞船、从发射地球轨道卫星到发射深空探测器的跨越式发展,具备了将航天器送入任 何空间轨道的能力,在国际卫星发射服务市场中占据了一席之地,构建了具有我国独立知 识产权的长征系列运载火箭型谱。
我国运载火箭发射次数不断攀升。自2018年起,我国运载火箭轨道发射次数长期处于 世界第一,尤其在 2021 年,我国运载火箭次数呈现井喷式增长。截至 2021 年 12 月 30 日,我国已经发射火箭 55 次,比美国多 10 次,较 2020 年全年增长 41%,发射次 数占全球发射次数的 38%。
地球观测卫星占据我国在轨卫星数量 50%。根据加州大学《S te ite D t b se(2021-9- 1)》数据,截至2021年9月1日,我国在轨卫星共有467个,包括地球观测卫星(50%)、 通讯卫星(15%)、导航卫星(10%)、技术试验卫星(15%)和科学卫星(10%)。
当前导航卫星已经完成组网,我们预计:未来 10 年导航卫星到寿更换仍有 31 次发射。
我国导航卫星以“北斗”工程为代表,2020 年 6 月 23 日,北斗三号最后一颗全球组 网卫星在西昌卫星发射中心点火升空。6 月 23 日 9 时 43 分,我国在西昌卫星发射中 心用长征三号乙运载火箭,成功发射北斗系统第五十五颗导航卫星,暨北斗三号最后 一颗全球组网卫星,至此北斗三号全球卫星导航系统星座部署全面完成。
当前,拥有 45颗在轨卫星的“北斗”系统已进入稳定运营期,未来卫星到寿是新发射 的主要动因。据《UCS S te ite D t b se(2021-9-1)》数据,其中 28 颗 MEO 北斗 三号卫星均为长征三号乙火箭一箭双星发射,发射重量多为 800 千克,轨道高度约为 25000 千米;其余的 17 颗 GEO 卫星轨道高度可达 35000 千米,以 4200 千克的中大 型卫星为主。北斗卫星设计寿命多为 8 年。
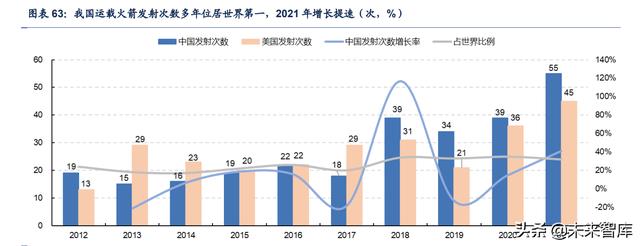
我们预计未来 10 年,目前在轨的北斗卫星均需要更换一次,则还需要 14 次 MEO 一 箭双星发射,以及 17 次 GEO 一箭一星发射,共计发射 31 次。
我国地球观测卫星发射开展如火如荼,我们预计未来 10 年将发射 386 次。
大多地球观测卫星星座运行在 LEO 轨道。根据加州大学《UCS S te ite D t b se (2021-9-1)》统计,截至 2021 年 9 月 1 日,我国地球观测卫星有 31 个在轨星座、 232 颗卫星,除高分卫星、风云卫星、宁夏卫星星座拥有 35000kmGEO 轨道卫星外, 其他卫星星座大多在 500~600 千米 LEO 轨道运行。
我们预计:未来 10 年地球观测卫星将发射 712 颗,共计发射 386 次小型运载火箭。 当前我国已推出多个地球观测卫星的发射计划,其中已有明确计划并已开展的发射计 划工 11 个,未来地球观测卫星以 LEO 轨道卫星为主,以小卫星和微小卫星为主,部 分采用小型火箭一箭多星发射方式发射。
全球卫星互联网竞争激烈,我国已发布多项通信卫星发射计划。我们预计未来 10 年将有 375 次发射。
各国“星座互联网”计划相继出台,未来卫星发射牵引运载火箭制造业增长。卫星通 信是利用卫星中的转发器作为中继站,通过转发无线电信号,实现两个或多个地球站 之间的通信。早在 2015年 1 月,Sp eX CEO 马斯克就宣布了卫星互联网服务计划, 这一项目被命名为 St r ink“星链”,计划发射超过 1.2 万颗卫星。
地球低轨卫星容量仅 6 万颗,5G 时代近地轨道成为不可复制的黄金资源。地球卫星的 轨道主要分为低中高三种,低地球轨道(LEO):又称近地轨道,距地面约 200-2000 公里的圆轨道;中地球轨道(MEO):距地面约 2000-20000 公里的圆轨道;地球同步 轨道(GEO):又称高地球轨道,距地面约 36000 公里的圆轨道。中高轨道卫星对地 面终端要求严格,且带宽有限,无法满足全球海量用户的互联容量需求;相比之下, 低轨卫星互联网星座可实现:高带宽、高性能全球覆盖、低时延、可便携式嵌入式终 端、低成本的全球互联服务。
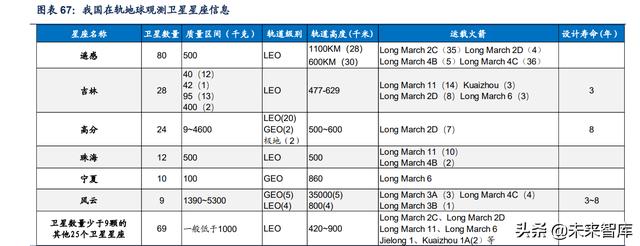
目前卫星通信的趋势从高轨向中低轨转移,各国相继推出 MEO 和 LEO 星座计划。其 中最具代表性的则是英国卫星通信公司 OneWeb、Sp e X 的 St rLink“星链”以及亚马 逊的 Pr je t uiper 星座计划等。截至 2021 年 9 月 15 日,英国 OneWeb 在轨星座卫 星总数达到 322 颗,几乎是 OneWeb 计划的整个 648 颗 LEO 卫星群的一半;而截至 2021 年 12 月 18 日,Sp e X 的 St rLink 计划已经发射 33 批,共计 1942 颗卫星, 远远超出了最初设计的 1440 颗卫星。
我们预计:未来 10 年通信卫星将发射 1423 颗,共计发射小型运载火箭 375 次。当前 我国已推出多个通信卫星的发射计划,其中已有明确计划并已开展的发射计划共 8 个, 未来地球观测卫星以 LEO 轨道卫星为主,以小卫星和微小卫星为主,部分采用小型火 箭一箭多星发射方式发射。
我们预计:导航卫星、地球观测卫星、通信卫星将刺激我国运载火箭发射需求,我国未来 10 年将分别为导航卫星、地球观测卫星和通信卫星发射运载火箭 31/386/375 次。 锻件是运载火箭的关键零部件。
火箭用锻件产品主要用于运载火箭发动机机匣、安装边、支座、法兰,运载火箭整流 罩、运载火箭外壳、卫星支架等。未来 10 年航天锻件市场规模将受益卫星发射需求的 增加。
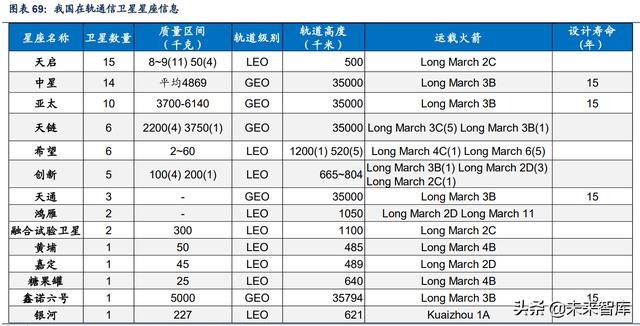
4.3 我国船舶工业于 2020 年率先复苏,即将牵引船舶锻件行业巨大市场
船舶工业是为国民经济及国防建设提供技术装备的现代综合性和军民结合的战略性产业, 是国家实施海洋强国和制造强国战略的重要支撑。新世纪以来,我国船舶工业快速发展, 已经成为世界最主要的造船大国之一。船舶工业根据用途可分为军用舰船和民用船舶两类。
船用锻件主要包括动力锻件、轴系锻件、锚系锻件和舵系锻件。其中,动力锻件主要包括 燃气轮机机匣、船用柴油机锻件、叶轮、法兰等,船用柴油机机体、机座、法兰等;轴系 锻件有推力轴、中间轴、艉轴、螺旋桨轴等;舵系锻件主要有舵杆、舵柱、舵销等;锚系 锻件主要有锚绞机用部件等。
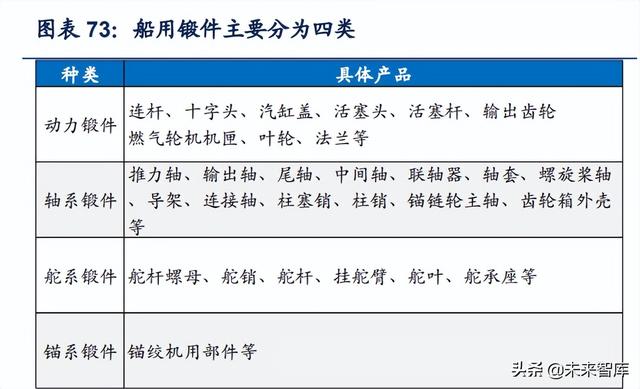
追赶美国海军,军用舰船产业有望保持高景气。
军事战略改变要求海军迅速提升实力。2015 国防部发布《中国的军事战略》白皮书, 中国海军按照近海防御、远海护卫的战略要求,逐步实现近海防御型向近海防御与远 海护卫型结合转变,构成合成、多能、高效的海上作战力量体系,提高战略威慑与反 击、海上机动作战、海上联合作战、综合防御作战和综合保障能力。
近年来海军装备建设呈现高速发展态势。根据美国国防部的报告,到2020年为止,中 国海军的舰艇数量已经超过美国,中国舰队的总规模估计为 350 艘,而美国为 293 艘。 但是在航母、驱逐舰数量和排水量等方面,我国还与美国海军有较大的差距。为补齐 与美国海军的差距,我国海军在未来较长的时间内仍处于追赶阶段,军用舰船产业也 有望持续保持高景气度,而作为军用舰船重要配套产业的锻造行业亦将受益,锻件需 求将有望保持持续增长。
世界船舶工业持续低迷,我国船舶工业率先复苏。
当前世界造船指标下挫,市场低迷形势蔓延。根据克拉克森数据,2020 年全球新船成 交 5933 万 DWT、2210 万 CGT,同比分别下降 9.2%、14.1%。完工交付 8944 万 DWT、2993 万 CGT,同比分别下降 9.5%、8.4%。截至 12 月底,手持订单已降至 1.59 亿 DWT、6993万 CGT,同比分别下降 15.3%、7.7%。自金融危机以来,全球新 船成交市场有三次极端行情分别在 2009 年、2012 年、2016 年,2020 年由于新冠疫 情引发的一系列连锁反应,市场成交再次陷入低谷。
我国船舶工业率先复苏,锻件市场需求将进一步扩大。2021 年 1-11 月,我国造船完 工量达到 3901 万载重吨,占全球比例为 47.6%;新接订单量 6004 万载重吨,占全球 比 51.8%;截至 2021 年 11 月底手持订单量 9843 万载重吨,造船三大指标均位居世 界第一。我国造船工业在全球造船低迷的背景下率先复苏。
巨大海运需求和船队规模为船舶工业发展提供稳固基石。巨大的海上货物贸易需求需 要强大的船舶工业。当前,我国已发展成为仅次于美国的全球第二大经济体,2020 年 中国进出口总值超过 32 万亿人民币,再创历史新高。我国经济发展既需要石油、天然 气、粮食、矿产等资源进口,又需要向全球提供工业制成品、基础材料等出口商品, 以上进出口货物来自或运往美洲、非洲、大洋洲、欧洲和中东等距离中国较远或陆地隔离的地区,海上运输是主要方式,离不开庞大的远洋船队支持。做强船舶工业是实 现经济稳定发展,能源、矿产等重要战略物资运输安全的重要保证。
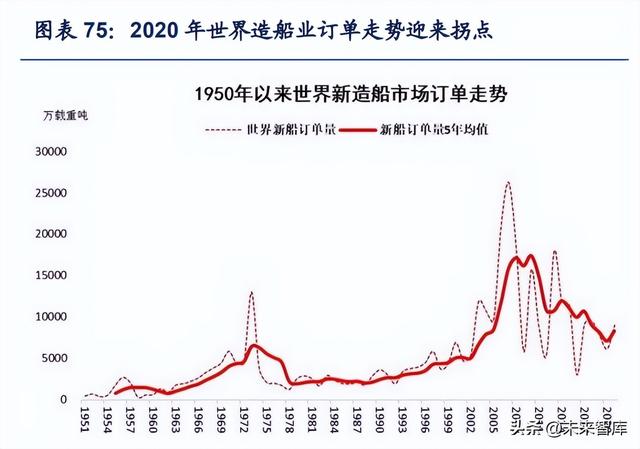
从船舶成本构成来看,人工成本占到全船成本的 30%左右、钢材等原材料占全船成本 的 25%、设计管理成本占全船的 5%、船舶配套占全船成本 40%左右。船舶配套和原 材料占整船成本相当大的比重,船舶总装制造企业成本中约 65%左右需要外购。
在推动“国内国际双循环”政策、全球疫情持续弥漫的时代背景下,我们预计:我国 造船业将率先完成复苏,拥抱低碳无碳大趋势和绿色能源船舶大蓝海,未来10年迎来 平稳的增长与发展时期,这将有效刺激船舶锻造厂商业绩增长。
4.4 “双碳背景下”,新能源发电拓宽电力锻件市场空间
“双碳”背景下,风电锻件、气电锻件不断拓宽电力锻件市场。
我国发电量不断增长,发电结构正在以新能源取代火电。2011-2020 年间,我国发电量逐 年增长,火力发电在电力结构中的占比逐年下降,从 2011 年的 85.38%降为 2020 年的 68.52%;而水电、核电、风电、太阳能发电等等清洁能源发电占比逐年提高。
我国将控制火电增长,转而以新能源发电逐步替代。
2020 年国家电网能源研究院发布了《中国能源电力发展展望》,报告认为,电源装机 总量 2035 年、2060 年将分别达到 40 亿、50 亿千瓦左右,风电和光伏发电将逐步成 为电源结构的主体,常规电源将长期在电力平衡中发挥重要作用,煤电装机预计于 2030 年前达峰,核电、水电、气电等各类电源近中期稳步发展。
《电力行业“十四五”发展规划研究》提出:“十四五”期间我国将大力发展可再生能 源,坚持集中式与分布式并举开发新能源,安全有序发展先进核电,将调峰电源作为 “十四五”气电发展的主要方向;合理控制煤电新增规模,发挥煤电托底保供和系统 调节作用,服务新能源发展。预期 2025 年,全国常规水电装机 3.7 亿千瓦,风电装机 4 亿千瓦,太阳能发电装机 5 亿千瓦,生物质发电装机 6500 万千瓦,核电装机 0.7 亿 千瓦,气电装机 1.5 亿千瓦,煤电装机规模力争控制在 12.3 亿千瓦以内。“十四五”期 间,力争完成约 2500 万千瓦煤电机组延寿。
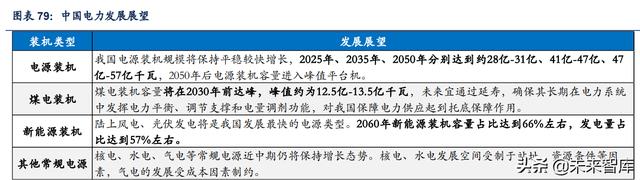
风电锻件成为锻造重要增长极。
顺应未来中国的经济社会发展,能源需求仍将保持一定的增速。为解决能源资源和环 境挑战,中国已经明确提出低碳能源发展战略和目标,风电已经开始并将继续成为实 现低碳能源战略的主力能源技术之一。根据国家发展和改革委员会能源研究所发布的 《中国风电发展路线图 2050》(2011 年发布)预测:到 2020、2030 和 2050 年,风 电装机容量将分别达到 2 亿、4 亿和 10 亿千瓦,成为中国的五大电源之一,到 2050 年满足 17%的电力需求。
我国风电行业迅猛发展。据国家能源局消息,截至 2021 年 11 月,我国风电并网装机 容量达到 30486 亿千瓦,突破 3 亿千瓦大关,较 2016 年底实现翻番,是 2020 年底欧 盟风电总装机的 1.4 倍、是美国的 2.6 倍,已连续 12 年稳居全球第一。
风电锻造主要集中于风电主轴的锻造和风电齿圈的锻造。风电主轴是风电整机的重要 零部件,风电主轴行业的发展受风电整机制造行业、风力发电行业拉动影响较大,风 电主轴的行业发展与风电整机行业的发展过程相似度较高。目前从事风电锻造的企业 有通裕重工、派克新材等。
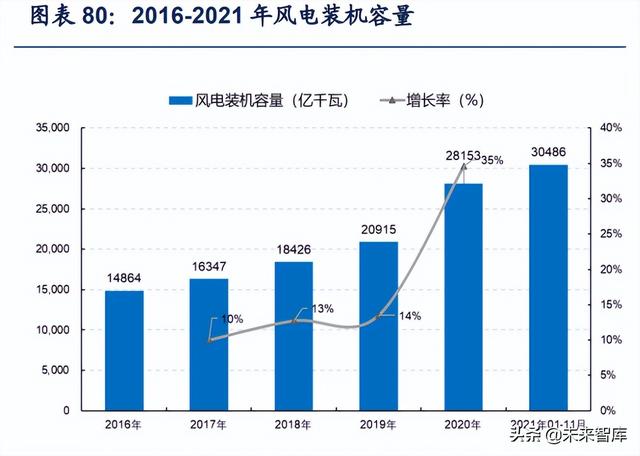
未来 5 年中我国火电达将实现达峰,气电锻件将拓宽锻件市场。
火电当前仍是我国发电主体。截至 2021 年 11 月,全国发电装机容量 23.2 亿千瓦。其 中,非化石能源装机装机容量 10.7亿千瓦;水电 3.9亿千瓦;火电 12.9亿千瓦(其中, 燃煤发电 11.0亿千瓦,燃气发电10704万千瓦);生物质发电 3598万千瓦,核电 5326 万千瓦,风电 3.0 亿千瓦,太阳能发电 2.9 亿千瓦。(报告来源:未来智库)
5. 锻造行业重点公司分析
5.1 中航重机:高端装备锻造龙头,技术优势转化竞争优势
坚持强军主责,突出航空主业,中航重机生产经营活动主要涉及锻铸、液压环控等业务。 锻造业务涉及国内外航空、航天、电力、船舶、铁路、工程机械、石油、汽车等诸多行业; 铸造业务主要为汽车、工程机械等领域配套泵、阀、减速机等液压铸件,叉车零部件、管 道阀门以及航空等铸件。液压产品主要包括高压柱塞泵及马达;热交换器业务主要研制生 产列管式、板翅式、环形散热器、胀接装配式、套管式热交换器及铜质、铝质、不锈钢等 多种材质、多种形式的热交换器及环控附件。
中航重机航空锻造业务相对全面,模锻、自由锻和环锻齐头并进。截至目前,中航重机旗 下参控股公司共有 20 家。锻造领域的核心子公司有贵州安大、陕西宏远、江西景航,其中, 贵州安大业务以环锻为主,陕西宏远业务以模锻、盘轴锻为主,江西景航则以中小型精密 锻铸件为主;液压环控领域的核心子公司有力源液压和贵州永红,其中力源液压以高压柱 塞泵及马达为主,贵州永红以热交换机为主。
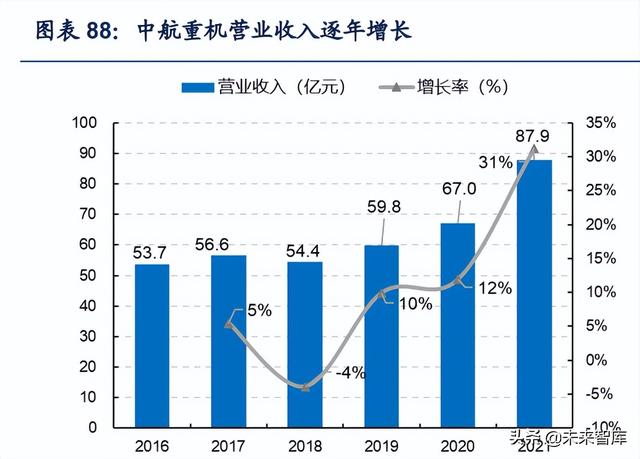
突出主业,锻造产品占比逐年增长,经营效率逐年提高。中航重机 2016-2021 年锻造产品 营业收入占比自 65%提升到了 75%;由于剥离了低效资产,相应地,公司毛利率和归母净 利率近年来稳步提升,2021 年毛利率达到 28.3%,归母净利率达到 10.1%。
5.2 派克新材:业务范围广泛,业绩增长稳定
专注高端锻造,产品应用广泛。发行人是一家专业从事金属锻件的研发、生产和销售的高 新技术企业。发行人主营产品涵盖辗制环形锻件、自由锻件、精密模锻件等各类金属锻件, 可应用于航空、航天、船舶、电力、石化以及其他各类机械等多个行业领域。 公司工艺能力覆盖广。公司拥有包括锻造工艺、热处理工艺、机加工艺、性能检测等在内 的完整锻件制造流程,可加工普通碳钢、合金钢、不锈钢以及高温合金、铝合金、钛合金、 镁合金等特种合金,具备跨行业、多规格、大中小批量等多种类型业务的承接能力。 公司主要产品可以分为航空锻件、航天锻件、船舶锻件、电力锻件、石化锻件、其他锻件。
业绩持续平稳增长。2016 年至今,派克新材营业收入、归母净利润持续稳定增长,2021 年营业收入已达 17.3 亿元,同比增长 69%,归母净利润达到 3.0 亿元,同比增长 82%。
航空航天锻件业务占比逐年增长,经营效率逐年提升。公司航空航天锻件营收占比逐年提 升,2016-2021 年由 7%扩大到 41%;毛利率与归母净利率逐年提升,2021 年毛利率达到 29.0%,归母净利率达到 17.5%。
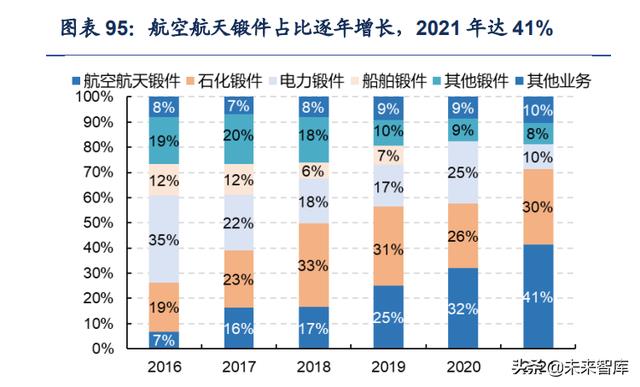
5.3 三角防务:400MN 模锻机打造大型飞机钢筋铁骨
“三航”站位决定超高起点,服务新型号持续带来订单。公司主营业务为航空、航天、船舶 等领域的锻件产品的研制、生产、销售和服务。在航空领域,为我国军用和民用航空飞行 器提供包括关键的结构件和发动机盘件在内的各类大型模锻件和自由锻件,也是占比最大 的业务类型。三角防务目前已进入航空、航天、船舶等领域的各大主机厂供应商名录。特 别是在航空领域,产品目前已应用于新一代战斗机、新一代运输机及新一代直升机。
直升机结构件主要包括发动机系统锻件、传动箱系统锻件、桨毂系统锻件、机身结构 锻件、起落架锻件和武器吊挂系统锻件,主要涉及钛合金、超高强度钢和铝合金的锻 造。
航发和燃气轮机盘类件主要包括前颈轴、风扇盘、压气机盘、整流罩、涡轮轴、低压 涡轮盘、高压涡轮盘、锥轴等盘类锻件,主要涉及高温合金、钛合金、超高强度钢、 不锈钢等材料的锻造。
业绩增速持续拔升,锻造市场持续掘金者。三角防务 2016 年间营业收入持续增长,2021 年预计达到 12.3 亿元,归母净利润预计达到 4.4 亿元;归母净利率近年来持续稳定在 30% 以上,2021 年预计将达到 35%。
公司以模锻件为主,模锻件营收占比常年稳定在 80%以上,并逐年提升,2020 年占比为 87%。 公司经营效率逐年提升。2016-2021 年,公司毛利率与净利率逐年提升,2020 年公司毛利 率达到 45.0%,归母净利率达到 33.2%。
(本文仅供参考,不代表我们的任何投资建议。如需使用相关信息,请参阅报告原文。)
精选报告来源:【未来智库】。未来智库 - 官方网站
相关参考
...设备,需要机器设备的地方就需要机床。机床通过铸造、锻造、焊接、冲压、挤压等方式,对精度要求较高和表面粗糙度要求较细的零件进行加工,从而生产设备。制造业是一个国家经济发展的支柱产业,机床行业的强大与否正...
模具毛边冷焊机(电气百科:锻造安全、锻造与锻造设备、铸造行业、锻造钢制工件)
电气百科:锻造安全技术概述、锻造与锻造设备、铸造行业现状及常见缺陷修补方法、锻造钢制工件的常用下料方法电气百科:锻造安全技术概述锻造是金属压力加工的方法之一,它是机械制造生产中的一个重要环节。根据锻造...
ws蓄热式烧嘴燃烧的使用原理有哪些呢?下面坜合博小编就给大家来分解一下。WS蓄热式烧嘴系統至少包括两个烧嘴,两个蓄热器,一个热能回收系统以及相应的控制装置。其工作原理是一种通过蓄热球从窑炉烟气中回收热量来...
ws蓄热式烧嘴燃烧的使用原理有哪些呢?下面坜合博小编就给大家来分解一下。WS蓄热式烧嘴系統至少包括两个烧嘴,两个蓄热器,一个热能回收系统以及相应的控制装置。其工作原理是一种通过蓄热球从窑炉烟气中回收热量来...
温锻和热锻有什么区别(精密锻造、汽车零件锻造…聊聊锻造界的那些事—智造人才网)
锻造行业是打造重型装备、先进装备的基础,是大国间较量的必争之技。现代锻造业经过上百年的发展历程,已经形成系统且先进的锻造工艺和锻造技术。受益政策支持、技术研发与市场推动,我国锻造行业规模位居全球首位,...
温锻和热锻有什么区别(精密锻造、汽车零件锻造…聊聊锻造界的那些事—智造人才网)
锻造行业是打造重型装备、先进装备的基础,是大国间较量的必争之技。现代锻造业经过上百年的发展历程,已经形成系统且先进的锻造工艺和锻造技术。受益政策支持、技术研发与市场推动,我国锻造行业规模位居全球首位,...
文/颜建斌·东风锻造有限公司瞿良·东风汽车集团股份有限公司一辆汽车上采用“冷温锻”近净成形工艺制造的零件品种(包括复杂程度、重量大小、精度高低)和零件数量的多少,体现了汽车先进制造技术的水平。我国目前一辆...
文/颜建斌·东风锻造有限公司瞿良·东风汽车集团股份有限公司一辆汽车上采用“冷温锻”近净成形工艺制造的零件品种(包括复杂程度、重量大小、精度高低)和零件数量的多少,体现了汽车先进制造技术的水平。我国目前一辆...
想学锻造刀剑(机械制造工艺基础知识,金属加工工艺锻造技术,锻造生产工艺过程)
一、锻造生产工艺过程1.下料下料方法:剪切法、锯割法、砂轮切割法、冷折法和气割法等2.锻件的加热加热目的:提高金属的塑性和降低其变形抗力,即提高金属的可锻性3.锻造将坯料在力的作用下发生塑性变形,从而改变...
电液锻——高效、节能、环保!电液锤在我国发展迅速,具有我国自主知识产权的8~12t液压自由锻锤已研制成功并投入使用,在国际上尚属首创。1、概念以液压油为工作介质,利用液压传动来带动锤头作上下运动,完成锻压工...