旧电机漆包线怎么利用(新能源汽车扁线电机专题报告:百倍市场空间,尽享双重红利)
Posted
篇首语:知识是工具,而不是目的。本文由小常识网(cha138.com)小编为大家整理,主要介绍了旧电机漆包线怎么利用(新能源汽车扁线电机专题报告:百倍市场空间,尽享双重红利)相关的知识,希望对你有一定的参考价值。
旧电机漆包线怎么利用(新能源汽车扁线电机专题报告:百倍市场空间,尽享双重红利)
(报告出品方/作者:德邦证券,马天一)
1. 百倍市场空间,20 年综合渗透率不足 1%
1.1. 线材升级,带来扁线电机新事物
扁线应用于永磁同步电机的铜线绕组当中。以绝大部分新能源汽车采用的永 磁同步电机为例,电机结构包括定子组件、转子组件、基座、端盖以及其他辅助标 准件。定子组件包含了定子铁芯、铜线绕组、引出线和绝缘材料,一般与电机壳体 固定。铜线绕组又区分为传统圆线绕组以及新型扁线绕组。转子组件包含转子铁 芯、永磁体、转轴、轴承等部件,和输出转轴相连,带动齿轮驱动车辆行驶。
电机的发展始终围绕整车需求,扁线电机对传统圆线电机有碾压性的技术优 势。新能源汽车目前处于快速发展时期,产品质量快速提升,消费者对整车性能 要求越来越高。整车对电驱系统的主要需求包括:高效率,高功率密度,优秀 NVH, 高集成性和低成本;扁线电机在这 5 个技术指标上均碾压传统圆线电机。
电机绕组导线横截面积为四边形,与传统圆线电机差异明显。在扁线电机的 定子组件制造过程中,需要把绕组做成发卡形状,通过插入方式安装入定子,故 这种扁线电机又被称为发卡电机。(报告来源:未来智库)
1.2. 渗透率展望,百倍市场空间
扁线电机渗透率快速提升。2021 年特斯拉换装国产扁线电机,带动渗透率大 幅提升,扁线电机的趋势已经确定。
众多潜在爆款车型使用扁线电机,预计 2025 年渗透率将快速提升至 95%。 2021 年上海车展中,扁线电机大放异彩,众多高端车型均搭载扁线电机。比亚迪的 DMI 车型和 e++平台全系都是扁线电机,大众 MEB、蔚来 ET7、智己 L7、极 氪 001 等明星车型采用的都是扁线电机。
预估 2025 年新能源汽车全球销量 2367 万辆。根据《新能源汽车产业发展规 划(2021-2035 年)》,目标到 2025 年新能源汽车销售渗透率达到 20%左右,到 2035 年纯电动汽车成为新销售车辆的主流;根据新能源汽车近年来的产销状况, 我们在此基础上预计中国新能源汽车销量 2025 年达到 896 万辆(渗透率 30%), 全球销量 2367 万辆。
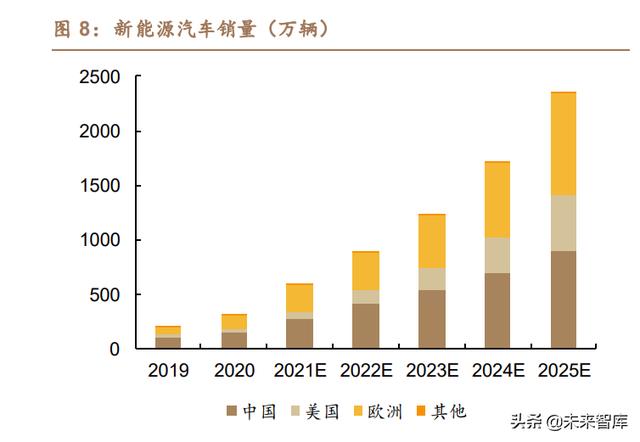
扁线未来有百倍市场空间。根据测算,2020 年扁线电机的渗透率约为 10%, 叠加新能源汽车渗透率约 5.4%,扁线的综合渗透率不到 1%。未来新能源汽车取 代传统燃油车,扁线电机取代传统圆线电机,扁线有百倍的市场空间。
1.3. 行业发展驱动力,扁线电机的五大优势
优势一:高能量转换效率带来电池成本节约。 扁线电机能大幅度提升转换效率,降低电池成本。根据上汽绿芯频道评估, 在 WLTC 工况,扁线电机比传统圆线电机的转换效率高 1.12%;在全域平均下, 两者效率值相差 2%;在市区工况(低速大扭矩),两者效率值相差 10%。按照典 型的续航 500km 的 A 级轿车(搭载 60kwh 电池包和 150kw 电机)计算,WLTC 工况下,搭载扁线电机的电池成本节约 672 元,市区工况下,电池成本节约 6000 元。
单车千元级别的成本节约对车企意义重大。以蔚来汽车为例,2021Q1 单车 毛利 8417元,单车净利仅-2239元。在新能源车和动力电池成本仍然偏高的情况, 如何降低成本是车企的永恒追求,提高电机工作效率则是降本的有效途径之一。
铜耗降低带来扁线电机转换效率高于圆线。电机损耗的能源中,有 65%来自 于铜耗,20%来自于铁耗,10%来自于风摩损耗,5%来自于杂散损耗。而铜耗来 自于电流通过铜线时的电阻发热 Q=I2R,当槽满率越高时,相同功率电机所需要 的铜线更短,进而内阻降低,发热减少,铜耗降低。
从理论上来说,圆线的槽满率一般在约 40%左右,而扁线则可以提升至 70%。 由于圆线的截面为圆形,不可避免在导线间存在不规则缝隙,而扁线间的间隙更 小,槽满率更高。
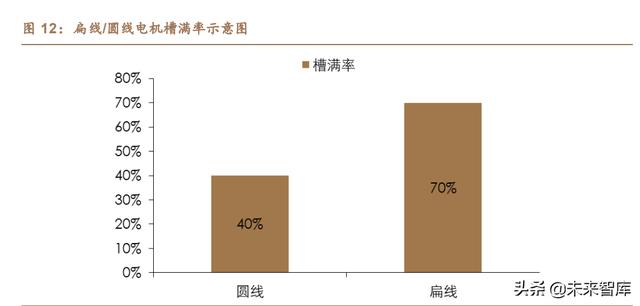
扁线电机的高效率区间比圆线电机高出许多,圆线电机的高效区一般要求是 效率>85%的区间占比不低于 85%,被称为“双 85”。而扁线电机的效率>90%的 区间占比不低于 90%,被称为“双 90”。 电机的效率与转速和扭矩相关,市区工况中出现的频繁启停工况属于低转速 高扭矩工况,而这正是圆线电机的低效率区间,而扁线电机在该工况下的转换效 率更高。
优势二:散热性好,提升高温动力性。 扁线电机散热性能好,温升相对圆线电机降低 10%。因扁线相对圆线更为紧 密的接触,散热性提升,研究发现高槽满率下绕组间的导热能力是低槽满率的 150%。绕组在热传导能力上具有各向异性,轴向的热传导能力是径向方向的 100 倍。更低的温升条件下,整车可以实现更好的加速性能。
优势三:高功率密度,整车动力更强劲。 电机的功率与铜含量成正相关,根据上汽绿芯频道评估,扁线电机槽满率提 升,相同体积下铜线填充量增加 20-30%,输出功率有望提升 20-30%,整车动力 更强劲。 国家政策层面倡导高电机功率密度。“十三五”规划中提出,新能源乘用车电 机功率密度应满足 4.0kw/kg,高于当前圆线电机约 3.5kw/kg 的水平。在圆线电机 功率密度提升进入困难模式的当前,发展扁线电机是必然之路,根据摩恩电气的 公告显示,当前领先企业的扁线电机的功率密度约 4.5kw/kg。
优势四:电磁噪音低,整车更安静。 扁线电机导线的应力比较大,刚性比较大,电枢具备更好的刚度,对电枢噪 音具有抑制作用;可以取相对较小的槽口尺寸,有效降低齿槽力矩,进一步降低 电机电磁噪音。
优势五:小体积带来高集成效率,契合多合一电驱发展趋势。 因扁线更高的槽满率,同功率电机铜线用量和对应定子较少,体积有望下降 30%。此外,扁线电机因更为先进绕线方式带来更易裁剪的电机端部,与圆线电 机相比减少 15-20%的端部尺寸,空间进一步降低,实现电机小型化和轻量化。
国内主流厂商大力推广扁线电机实现体积下降。上汽 ER6 的 8 层 hair-pin 扁 线电驱动系统,比上一代圆线电驱动系统体积下降 50%。目前华为的七合一电驱 包括:BCU 制动控制单元、PDU 电源分配单元、DCDC 低压直流电源转换器、 MCU 微控制单元、OBC 车载充电器、电机、减速器。
1.4. 扁线电机应用的障碍正在逐个化解
扁线拥有许多传统绕组不可比拟的优点,但同时扁线电机也有部分劣势,但 总体而言瑕不掩瑜。随着技术的发展和渗透率的逐渐提升,扁线电机应用的障碍 正在被逐个化解。
应用障碍一:“趋肤效应”、“邻近效应”明显,交流阻抗增大,高转速时转换 效率降低。趋肤效应指当导体中有交流电或者交变电磁场时,导体内部的电流分 布不均匀,且电流集中在导体的“皮肤”部分的一种现象。邻近效应指相互靠近的导 体,通有交变电流时,每一根导体都处于自身电流产生的磁场中,同时还处于其 他导体中电流产生的磁场中,这使得每个导体中电流分布都会受到邻近导体影响 而不均匀现象。“趋肤效应”、“邻近效应”都会增加交流阻抗,交流阻抗增大,高 转速时转换效率降低。
“趋肤效应”并不影响扁线电机渗透率的快速提升,但工程师也已经有改善 方案:1)提高扁线的宽高比,间接增加扁线的比表面积;2)减小导线尺寸,间 接增加扁线的比表面积,但这同时也会降低槽满率,需要综合评估;3)采用多档 变速箱,降低电机转速,代表车型为保时捷 Taycan;4)3D 打印铜线,导体尺寸 和横截面可以任意变化,给了绕组设计极大的自由空间,该方案导致导体内的电 分离结构,所述电分离结构用于限制涡流路径,因此电流密度被“强制”到剩余的 导体横截面上,此外借助于 3D 打印可以实现任意连接的几何形状,不需要传统 的绕组接头焊接工艺,该方案短期内无法实现量产。
应用障碍二:非标准化;不同车企的设计方案不一样,而定子是电机设计的 核心,定子尺寸定型后,导线的线型、尺寸任意一点发生改变,都需要定制昂贵的 工装模具,兼容性低,系列化难度高。 同一车企或电机企业的设计系列化趋势初现,以上汽 E2 架构为例,在设计 之初就考虑了共线生产,三款不同功率的电机(150kw,180kw,250kw)适用于 该架构上的所有车型,最大程度上实现模块化。第三方电机的壮大也会改善系列 化难度,扁线电机的技术门槛和初始投资门槛远高于传统圆线电机,技术基础较弱的车企只能广泛依赖于第三方电机厂商,第三方电机厂商的电机型号有限,也 会成为市场上的主流产品。
应用障碍三:扁线电机生产线投资额是圆线的 2-5 倍。扁线电机对产品的一 致性要求高,技术难度大,需要投入精度较高的自动化伺服设备、焊接设备、HairPin 线成形设备和工装模具等。 汽车电动化和电机扁线化的趋势已经确定,扁线电机逐渐成为资本宠儿。方 正电机的年产 100 万台新能源汽车驱动电机项目,总投资 5 亿元人民币,项目达 产后可新增销售收入 25 亿。
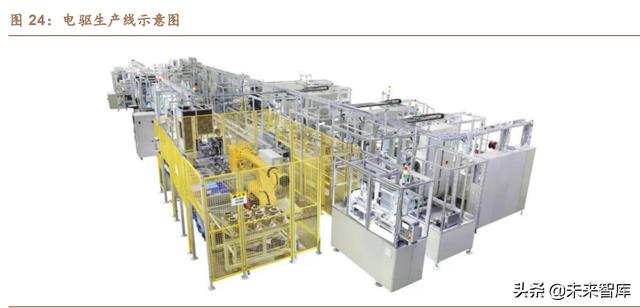
应用障碍 4:对扁线要求高,扁线成本高、技术难度大。扁线的加工难度增 大。1)从圆形切换到矩形形状,导致铜线生产加工工艺更加复杂。2)涂覆难度增 大,扁平线 R 角处的漆膜涂覆非常困难,很难保证此处绝缘层的均匀性;绝缘涂 层在烘干后会产生收缩,扁线是非均匀收缩,容易变形,需要改良使得 R 角处的 涂覆厚度更厚;3)扁线弯折成发卡后,R 角处应力集中,容易导致涂覆层破损; 4)对扁线的精度要求高,扁线截面积大、匝数少,单根导线不一致对整体性能的 影响显著增大,对扁线的一致性要求高,复杂的加工成本使得扁线成本更高,也使得扁线加工企业享受更高的技术溢价;5)新能源汽车所使用的漆包线直接关系 到整车运行稳定性,对电磁线厂家的质量控制流程、研发与工艺设计能力提出了 很高的要求,需要对拉丝和包漆速度、拉丝与包漆的协调、拉丝模具配置、张力控 制、涂漆模具配置、烘焙温度、绝缘漆粘度、工作环境等多个控制点的合理设计、 严格控制。
扁线的最大成本是原材料无氧铜杆,加工费在电机中的价值量并不高。稳定 地供给合格的产品是与车企合作的关键,在原材料是主要成本的情况下,车企寻 求加工费更低的供应商的动力并不高。
2. 竞争格局:电动车扁线化带来集中度提升
2.1. 电磁线行业格局分散,竞争激烈
扁线属于电磁线的一种。电磁线种类丰富,根据导体形状分为圆线、扁线以 及异型线。
电磁线市场竞争激烈,集中度很低。由于技术门槛低,下游客户分散,长尾 效应显著。精达股份市占率第一,达到 11.23%,其次是长城科技(7.06%),冠城 大通(3.85%),金杯电工仅占 1.21% 电磁线下游应用场景丰富,主要包括家用电器、电力设备、工业电机、汽车、 电动工具等。其中,家用电器、电力设备、工业电机合计占比达到 82 %,是最为 主要的下游需求。家电业务经过多年的高速发展,已经步入稳定阶段,2019 年至 今的行业增速基本维持在个位数。
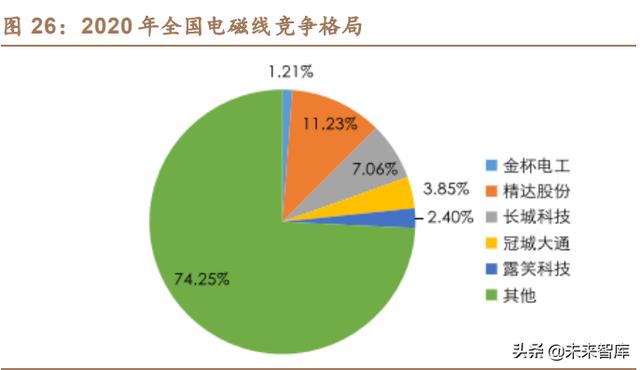
2.2. 扁线行业属于蓝海市场,目前仅四家公司量产
目前仅四家公司实现新能源汽车用扁线的量产:精达股份、长城科技、冠城 大通和金杯电工。四家公司都拥有丰富的电磁线研发生产经验,在电磁线激烈的 市场竞争中不断做大做强,属于电磁线领域的头部企业。
新能源扁线都被归类到电磁线业务当中。1)精达股份:电磁线业务占比 68.5%, 贡献公司主要收入;2)长城科技:电磁线业务占比 98.2%,是市场上最纯正的电 磁线企业;3)冠城大通:房地产占比 55.8%,电磁线占比 41.2%。4)金杯电工: 电磁线仅占 15.4%,电气装备用电线 38.5%,特种电线电缆 26.2%,电力电缆 11.8%。
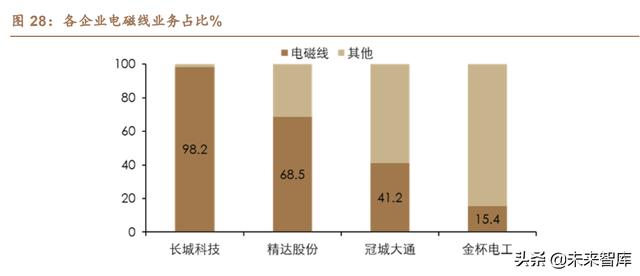
行业内公司营收差异较大,营收增长率基本保持一致。20 年精达股份电磁线 营业收入 85.2 亿,长城科技 61.6 亿,冠城大通 36.6 亿,金杯电工 12.0 亿。营 业增速方面,2015 年宏观经济出现下行压力,家电行业整体下滑,电磁线营收明 显降低。2017 年家电下乡政策实施,各企业电磁线营收增长明显。2019 增长降 低至个位数,2020 年铜价上涨,营业收入明显增长。(报告来源:未来智库)
金杯电工近年毛利率提升显著,其他三家基本保持稳定。金杯电工因为高附 加值的高压特种线占比增加,近几年来毛利率不断提升,20 年达到 16.58%,领 先于行业内其他公司。2020年精达股份电磁线业务毛利9.7%,长城科技为7.9%, 冠城大通为 8.3%。
加工费整体呈下降趋势。精达股份 2020 年电磁线加工费约 6 元/kg,高于竞 争对手长城科技和冠城大通,部分原因是精达股份高加工费的铝线占比更高。长 城科技 2020 年加工费为 3.7 元/kg,冠城大通 19 年电磁线加工费约 5.3 元/kg。
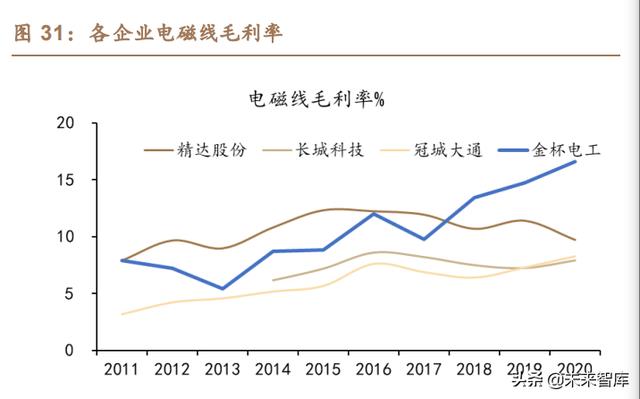
2.3. 新能源扁线产能及出货量:精达扩产最快
精达股份扩产速度最快,充分享受渗透率提升红利,预计 21 年形成产能 1.9 万吨/年,22 年形成产能 4.5 万吨/年。2019 年发行可转债募集 7.87 亿元,其中 3.3 亿元投向新能源产业及汽车电机用扁平电磁线项目,新建新能源扁线产能 3 万 吨/年。21H1 新能源扁线出货 2045 吨,其中 Q2 出货约 1248 吨,环比提升 56%, 展望全年预计出货超过 5000 吨,进入规模化放量期,良率进一步提升。
金杯电工扩产速度稍慢,23 年达到 2 万吨/年,25 年达到 5 万吨/年。2021 年 7 月公告投资 7.11 亿元新建新能源汽车电机专用电磁线产能 5 万吨/年。21H1 新能源扁线出货 700-800 吨,全年出货有望达到 2000 吨。
冠城大通电磁线子公司大通新材已经提交了 IPO 申请材料,IPO 项目包括年 产 8 万吨漆包线绿色智能技术改造项目。招股说明书显示,2020 年 1-6 月新能源 扁线出货 860 吨。
长城科技已公告产能 5.2 万吨。IPO 项目中包含 0.7 万吨新能源汽车用特种 电磁线项目,8 月 26 日公告定增 15 亿,其中 8.3 亿元用于 4.5 万吨新能源汽车 扁线。21H1 新能源汽车用扁线产量突破 1300 吨,并继续保持快速增长。
2.4. 研发及专利对比:精达和金杯领先
金杯电工和精达股份专利数量最多。扁线技术含量高,前期投入大,根据公 告资料显示,截止至 2020 年金杯电工专利数量 227 个,精达股份 214 个,长城 科技 118 个,冠城大通 30 个。
金杯电工研发人员数量远超同行。截止至 2020 年,金杯电工研发人员 668 人,长城科技 106 位,精达股份 396 位,冠城大通 114 位。
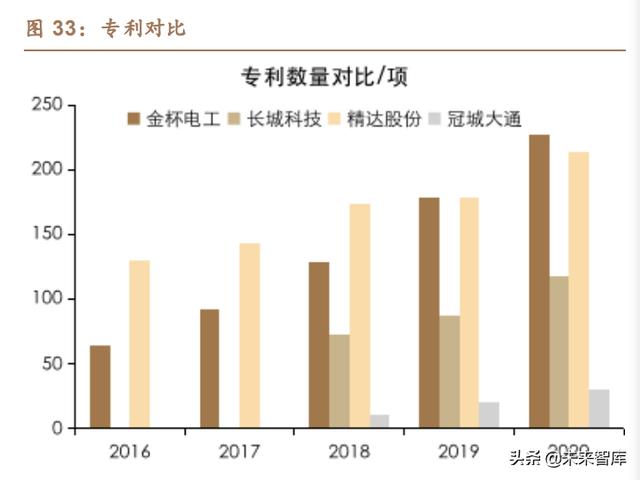
金杯电工、精达股份近三年研发费用投入较高,长城科技研发投入增速很快。 扁线技术含量高,前期投入大,早期高强度研发投入,现阶段充分享受技术溢价。
金杯电工研发费用高于同行。长城科技、精达股份、冠城大通 20 年研发费用 占营收比例分别为 2.42%、1.21%、1.18%,金杯电工 20 年研发费用占营收比例 为 3.26%,金杯专注于研发更好更新的技术,五年来研发费用/营收比例均超过 3%, 领先于同行。
3. 铜杆加工:新能源车扁线对原材料铜杆要求高
3.1. 无氧铜杆的综合性能更优异
部分车企要求以无氧铜杆制备新能源汽车扁线。扁线原材料铜杆分为低氧杆 和无氧杆,氧含量低于 450PPM 为低氧铜杆,氧含量低于 20PPM为无氧铜杆。 二者皆应用在电磁线领域。
无氧铜杆的韧性、加工性、电阻率和外观皆优于其他铜杆。1)普通铜杆中往 往有相当部分的氧化铜杂质,会对材料的韧性产生负面影响,而品质优良的无氧 铜杆中几乎没有杂质的存在,具有优良的韧性;2)优良的无氧铜杆组织均匀、晶 体粗大,不但克服了普通铜杆中最常见的多孔性缺陷,还拥有着在所有线径里最 为优越的可拉性。与无氧铜杆相比,普通铜杆有着难以拉制低于 0.5mm 以下细丝 的缺点,因此无氧铜杆有着更优异的加工性;3)用无氧杆制作的扁线电阻更小, 应用于电机时,发热的情况优于低氧杆。4)此外,无氧铜杆的外观光洁,表面圆 整,没有毛刺、裂纹、起皮及夹杂缺陷,而低氧杆因为氧含量的原因,在焊接过程 中,容易产生飞溅,而无氧杆却没有此类现象,因此,无氧杆更加受到扁线电机制 造厂家的欢迎。
铜杆的生产方式有连铸连轧法、上引连铸法、浸涂成型法和回线轧制法。不 同生产工艺所生产的铜杆含氧量、外观电导率等有所不同,主流的生产工艺为浸 涂法和上引法。
1、浸涂成型法:铜杆含氧量 20ppm 以下,铜杆圈重 3.5~10 吨。浸涂成型 利用冷铜杆吸热能力,用一根较细冷纯铜芯杆(或称种子杆),垂直通过一只能保 持一定液位高低铜水池,使铜水与该移动种子杆表面铜熔合在一起,并逐步凝固 结合成较粗铸造状态铜杆,然后经冷却、热轧、冷却、绕制成圈,整个过程封闭、 有惰性气体保护下进行。
2、上引冷轧法:铜杆含氧量 10ppm 以下,铜杆圈重 2 吨。它是利用一种管 式铜套(即石墨结晶器)其下端伸入并浸没在熔化铜液面下,上端与真空泵连通, 开始时将结晶器内空气抽出,真空作用下,使管内产生负压,铜液虹吸引向上,并 在引升器附近很快凝固成光亮铸锭。
两种生产工艺各有优劣。上引冷轧法设备投资小,厂房布置灵活,可在同一 机器上生产不同规格、品种的铜材,但难以实现规模化,适合小型企业;浸涂成型 法生产效率高,过程机械化,适合大型企业规模生产。
3.2. 自制铜杆有成本优势
富通昭和线缆杭州有限公司是重要的无氧铜杆生产商之一,公司成立于 2011 年,目前富通集团股份有限公司持股 51%,昭和电线电缆系统株式会社持股 49%。 采用浸涂法生产各种规模的无氧铜杆。
自制无氧铜杆节约成本。国内扁线生产商大部分外购无氧铜杆,少部分自制。 常规无氧铜杆的采购成本与电解铜的价格差异在 900 元左右,而新能源车使用的 无氧铜杆要求更高,价格差异更大。而采用上引法生产无氧铜杆的加工费在 500 元左右,自制无氧铜杆有利于降低成本。
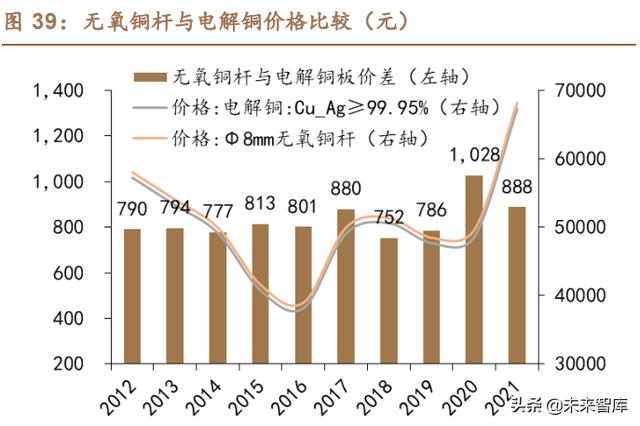
3.3. 自制铜杆能实现废铜再利用,进一步降低成本 漆包线生产过程中,不可避免的存在部分废品,自制铜杆有助于实现废铜再 利用,进一步降低成本。在上引法生产程序中增加精炼工序,利用上引法工频炉 溶炼生产过程中产生的废铜线,一样可以生产出优质铜杆,品质上也能达到下游 对电阻率的需求。当电解铜与废铜价差涨至一定程度时,利用废铜重新制杆的成 本优势将体现,下图显示的是不含税的价差,可以看到随着铜价的攀升,电解铜 与废铜价差体现出废铜再利用优势明显。
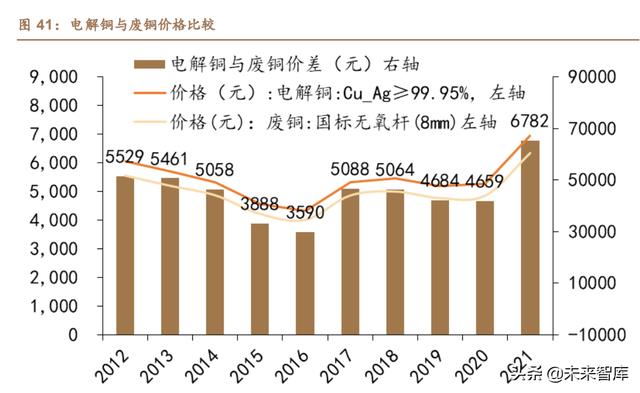
4. 铜扁线加工:拉丝、挤压、精轧三条技术路线
新能源汽车扁铜线制作方法有三种:连续挤压、拉丝成形、精轧成形。扁铜 线尺寸的加工要求宽高比大,尺寸要求精度高。目前的主流工艺路线为拉丝成形、 精轧成形。
4.1. 连续挤压:生产效率低,应用较少
连续挤压技术的工作原理:模腔位于挤压轮侧面,坯料在旋转挤压轮的带动 下进入挤压腔内,在轮槽摩擦力的作用下,坯料温度升高压力加大,达到一定值 后便从模孔中挤出,形成产品。
铜扁线连续挤压工作流程:一根上引法生产的无氧铜杆,在表面清洁的条件 下,由坯料放线盘放出,经过矫直后直接送入连续挤压机。坯料进入挤压轮轮槽 时,在槽壁的摩擦力作用下被曳引到由挤压轮和模腔形成的挤压腔内,由于挡料 块阻止了铜杆继续前进,在摩擦力产生的高压和高温作用下,金属通过模口挤出 形成铜扁线型材。通过挤压机后挤压成铜扁线产品,但此时温度较高,所以在挤 压机的产品出口处有防氧化装置和冷却系统。最后经由计米、涂油和摆臂等装置 由收排线机收卷成盘。
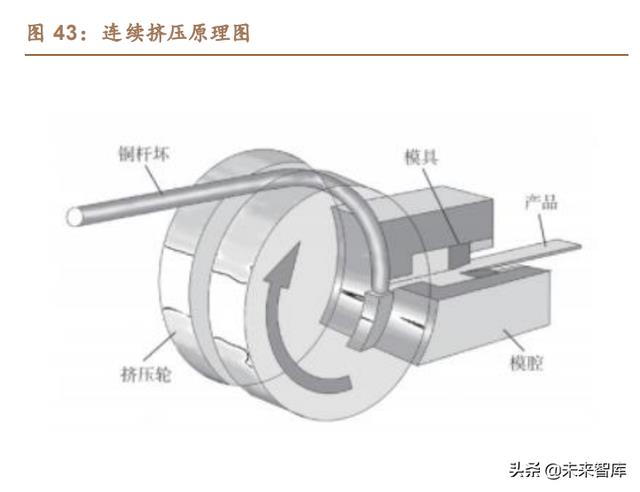
连续挤压技术的优点:1)采用连续挤压生产铜扁线, 铜坯料在挤压模口前 的温度可达 600℃以上,压力高达 1000MPa 以上,而且为三向压应力。在这种 高温、高压条件下,铜坯料的原始内部缺陷,如气孔等可以在连续挤压过程中消 除。2)由于连续挤压铜扁线仅需一道工序即可将铜盘条直接挤压成铜扁线成品, 使得铜扁线表面不会产生毛刺等表面缺陷,铜扁线具有良好的表面质量。3)由于 采用单一的坯料,仅需要简单更换模具就可以生产各种规格的铜扁线产品,且不 需要退火,因此生产周期非常短,可实现“当天交货”,而不需要库存和准备各种规 格的坯料,大大缩短了生产周期,减少资金的占用,提高了材料利用率和成品率, 特别适合于多品种、小批量的铜扁线的生产。4)模具材料和结构可保证产品具有 较高的尺寸精度,不仅可以达到国家标准的要求,而且保证了同批产品具有相同 的尺寸。5)整条生产线采用的先进计算机控制系统,生产过程可自动监测和运行, 实现了自动化生产,降低了操作工人的劳动强度。 连续挤压工艺因生产效率低,目前并未广泛应用于新能源车扁线领域。(报告来源:未来智库)
4.2. 拉丝成形: 主流工艺路线,生产精度依赖于模具
拉丝成形工艺原理:拉丝工艺是一种金属压力加工过程,在外力作用下使金 属强行通过模具,金属发生塑性变形,横截面积被压缩、长度增加,并获得所要求 的横截面形状和尺寸的加工方法。
拉丝工艺流程:1)穿线:将导线从卷线盘放出,依次穿过放线架、各级拉丝 模具、退火设备、收线铁轴。穿拉丝模具时用配套设备将导线打磨,使线径变小易 于穿过拉丝机各级模孔。2)拉丝:指将线胚通过多级模孔,在一定压力作用下, 发生塑性变形,使截面变小而长度增加的过程,由拉丝机塔轮轴带动逐级拉拔。 拉丝过程中拉丝液起润滑、冷却和清洗作用。3)拉丝后须进行连续退火,使在冷 拉过程中因晶格变化而变硬的导线经一定温度加热,消除内部应力及缺陷,提高 延伸率,使之恢复到拉丝前的物理及机械性能,有利于后续工序的进行。4)收线、 检验:将各线径规格的导线定尺复绕于收线铁盘上,作为漆包规格线或拉丝过程 线,每轴规格线全检外观、尺寸,过程线另检伸长率。
拉丝工艺的的优点:1)拉制可以得到尺寸精确、表面光洁及断面形状复杂的 制品。2)拉制品的生产长度可以很长,直径可以很小,并且在整个长度上断面完 全一致。3)拉制能提高产品的机械性能。
4.3. 精轧成形:设备昂贵,不依赖模具,生产精度高
精轧机的工作原理:电机提供动能,液压传动系统改变力矩和动力,通过轧 辊和行程运动来对工件进行重复的压轧,最终达到所需要的尺寸和形状。轧机广 泛应用于钢铁、有色等行业。
精轧机的优势:先进的精轧工艺具有提升传统拉丝和挤压两种工艺的优点, 克服两种传统工艺的不足。精轧机生产的裸线完全可以做到:1)裸线通过轧辊轧 制而成,外观质量可以达到镜面;2)导体金相组织结构均匀,导电率优于国标, 机械性能良好;3)裸线尺寸根据设定偏差自动调节,尺寸精确控制在±0.01mm 以 内,具有记忆和锁定功能,批次间不存在产品尺寸影响电阻平衡,不依赖模具,适 用范围广;4)生产过程运行平稳、噪音低、振动小、生产效率高、设备能耗低、 自动化程度高;使用该设备生产的产品质量完全能满足高档电磁线质量要求。
4.4. 三种工艺对比:拉丝为主流但依赖模具,精轧设备昂贵但性能更优
“连续挤压法”和“拉丝法”依靠模具成型,模具的尺寸均一性对扁线绕组 电阻有着极大影响,从而影响扁线性能,模具存在磨损必须定期更换。“连续挤压 法”和“拉丝法”有一个共同的特点:型都是通过模具来保障的。连续挤压法区别 拉丝法的地方为模具的工作温度在 450~550℃之间,无法用聚晶模(人工钻石模) 来进行生产。由于不能用聚晶材质作为挤压模具,每一个挤压模具的生产重量都 不会超过 58 吨(拉丝法聚晶模寿命一般在 80-100 吨)。
扁线定制化程度高,对模具迭代速度要求高。扁线因有长宽两个尺寸维度,具备高度定制化特性,而圆线仅有半径一个参数,标准化程度更高。拉丝模具是 拉丝机的核心零部件且必须定期更换,保证不同批次模具的一致性是保证产品质 量的关键,自产模具有利于提高产品质量。精达股份模具子公司聚芯智造成立于 08 年,已申请新三板挂牌,是公司的核心资产,主要为内部配套模具,保证公司 产品质量稳定,也有部分模具产品出口。目前公司持股 84.51%,员工持股平台持 股 15.49%,已实现核心管理层绑定。金杯电工也有模具加工中心,实现模具自制。
模具使用过程中存在磨损,导体尺寸不一致会对绕组的电阻平衡造成影响, 模具必须定期更换,且模具一致性要求高。虽然聚晶模具表面硬度高,但在长期 的使用过程中模具依旧存在磨损,模具的孔径尺寸会缓慢变大,造成导体尺寸变 化,进而影响导体电阻。车用电机对扁线的每米电阻差异率要求较高,进而对模 具精度要求更高。
精轧成形不依赖模具,铜扁线尺寸精度较高。精轧法进行导体加工,尺寸控 制是一个离散量,不是使用模具成型时的趋势量。轧制成型过程是尺寸反馈给计 算单元,传动机构调整轧辊间距纠正尺寸,尺寸在一个很小的范围内变化,结合 SPC 等控制方法,绕组扁线的导体尺寸精度提高。
精轧机的设备成本远高于拉丝机,目前只有金杯电工以精轧的技术路线为主。 金杯电工精轧机来自于 REDEX group,REDEX是法国知名的设备供应商,在扁 线精轧机领域处于行业领导者的地位。采购国外设备时间周期较长,扩产速度较 慢。
5. 绝缘涂覆:电磁线核心工艺,各家技术积累集中体现
5.1. 绝缘材料简介:车规级对耐热性能要求高
绝缘膜性能优劣对扁线性能有决定性影响。漆包扁线由裸导线和包覆在其外 的绝缘漆膜两部分组成,通过涂线后绕成线圈再浸涂粘结树脂使各匝导线粘结在 一起,绝缘漆性能的优劣、工艺裕度的大小和质量的稳定都会影响扁线的性能。
电动汽车驱动电机用绝缘材料和绝缘系统提出了更高的要求:1)应具有优异 的耐电晕性能(因存在高频脉冲电压、电晕腐蚀)、2)优异的电气绝缘性能(因 额定电压较民用电压 220V有所提升)、3)优异的机械性能尤其是高粘结强度(因 存在强振动)、4)高的耐热性(设计的耐热等级为≥180)、5)高导热(功率密度 大,电机发热严重)、6)耐 ATF 油或水(采用内油冷及水冷散热冷却技术)、7) 无卤阻燃(降低着火危险性)、8)耐高低温冲击(适应气温变化)等。
车规级新能源汽车用扁线对耐热性要求高,主要采用耐温≥180℃的聚酯亚 胺漆包线漆、聚酰胺酰亚胺漆包线漆、聚酰亚胺漆包线漆这三种耐高温绝缘材料 进行漆包。
聚酯亚胺漆具有较好的电气性能和机械强度,且耐热冲击和耐软化击穿。在 180 级及以上复合涂层漆包线制造中作为底漆涂层的主要材料,在高附着和耐氟 利昂的家用电器中得到广泛应用。
聚酰胺酰亚胺漆耐热性高,不仅漆膜硬度和非软化性很大,并且对导体粘合 力较高,最先得到产业化,可在 210℃下长期使用。用于耐高温电机电气电子元 件的线圈绕组,被用作电磁线的绝缘涂层。
聚酰亚胺漆耐热性能优异,同时能够耐老化,耐高压电击穿等。其主要运用 于绝缘漆覆包电磁线,或作为耐高温涂料应用于电气行业、航空航天、石油管道 等。
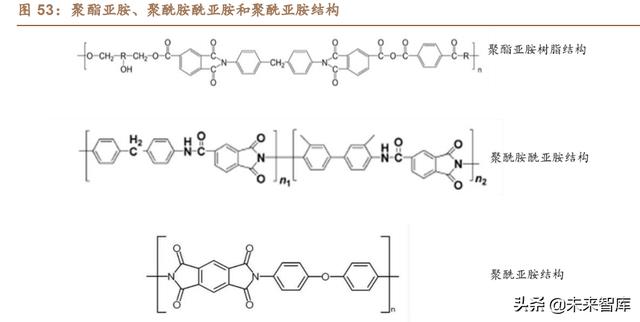
5.2. 涂覆精度依赖模具,将原有卧式涂覆设备改造成扁线立式涂覆设备难度大
绝缘涂覆设备厂商主要有三家:无锡苏意电工设备有限公司,无锡巨一同创 科技有限公司,无锡市梅达电工机械有限有限公司。
将原有卧式涂覆设备改造成扁线涂覆设备难度大,都采用新购设备方式扩产。 涂覆设备可大致分为两种,卧式涂覆设备和立式涂覆设备,其中扁线涂覆主要以 立式涂覆设备为主,在对漆膜均匀度要求不高的非车规级电磁线中,以卧式涂覆 设备为主。主要原因是卧式设备中,绝缘漆由于自身重力会向下流动,影响漆膜 均匀性。卧式涂覆设备的优点是生产能耗更低、设备成本更低,在对漆膜均匀度 要求不高的非车规级电磁线中应用广泛。
目前绕组扁线涂覆绝缘漆工艺有两种方法,其中新能源汽车用扁线基本采用 模具法:
毛毡法:利用羊毛毡的虹吸现象将漆液涂覆在扁导体表面。新能源汽车电磁 装置受到高频和车载体积的影响,宽高比更大。将绝缘涂层和载流导体很好的结 合到一起,并使 R 角漆膜厚度均匀一致,提高绕组线的 BDV(BreakdownVoltage) 值,达到绕组线绝缘层具有很均匀的介电性能。
模具法:可以提高漆液粘度,使漆液尽快从液体状态蒸发掉溶剂进入黏流态, 进一步快速加温(320~360℃)进入玻璃态,绝缘层快速完成了交联固化,减少从液 态到黏流态的流平时间,抑制 r 角处绝缘漆受液体表面张力影响的流平,从而达 到使绝缘层分布均匀体现最好的介电性能。
R 角的存在使得扁线的涂覆难度更高。漆包圆线上漆时,漆液经过模具涂覆 到圆形截面的导体上是两个同心圆,圆线的上漆时液体表面张力均匀,只需保障 圆线的导体圆度,漆包圆线的绝缘层就非常均匀。扁线的涂漆过程中受其矩形截 面及漆液表面张力影响,漆液在液体湿润性作用下,在 r 角和直线段相切位置的 漆液更容易被直线面拉走,形成不均匀的漆膜,造成 r 角部分涂覆绝缘漆困难,使 漆膜的介电性能出现薄弱点。
漆模具主要由两部分构成,涂漆区和定位区。在涂漆区镶有用耐磨材料制成 的模芯,在模芯的内形结构中又可分为缩减区和定量区。缩减区的作用是去除多 余的漆液,定量区的作用是控制每道涂漆的挂漆量,以满足涂漆工艺要求。涂漆 模具定位区的作用是保证涂漆模具轴心与导线同轴,避免偏心和涂漆不均,同时 使回漆远离模架,避免漆液溢流到模具上部,影响涂漆质量。
5.3. 偏心度:各家技术积累的体现
偏心度是漆包线的关键指标,对漆包线各方面性能都会有影响,也是各家技 术积累的体现。漆膜分布的不均匀性常以偏心度来表示,其值即为垂直于圆导体 某一截面上的最大漆膜厚度与最小漆膜厚度之比。一般的检测方式取漆包线任意 N 个点,测量每个点的绝缘层厚度,偏心度=绝缘厚度最大值/绝缘厚度最小值。
漆膜偏心度过大对电气性能有影响,导致击穿电压值分散性大。漆包线击穿 电压是漆包线在工作条件下经受电压负荷的能力。漆包线漆膜的特性及漆膜厚度 和击穿电压的关系是:V∝t,其中:V为击穿电压值,t 为漆包线漆膜厚度,击穿 电压测试是先将漆包线扭绞制样然后测试电压值,如果漆包线漆膜偏心,同一截 面上四周漆膜厚度不均匀,当漆包线漆膜较薄面绞合在一起,这时虽然漆膜达到一定的厚度,但在此处的绝缘容易被击穿,反之则击穿电压值很高。因此,漆包线 漆膜偏心度大给漆包线耐压性带来了较为明显的影响,导致了漆包线击穿电压值 分散性大。
漆膜偏心度过大对漆膜连续性影响。漆膜连续性检测方法是测量一定长度下 漆包线漆膜的针孔数。影响漆包线绝缘连续性的因素较多,漆膜偏心是其中之一, 漆包线漆膜偏心导致漆包线绝缘层厚薄不均。当涂漆不均匀,特别是第一道漆膜 涂得太薄处易使导体氧化,影响漆膜附着性,太厚处又会使漆膜内部的溶剂挥发 不充分,交联度差,漆膜的弹性差和附着性能下降,易造成脱漆现象而影响漆膜 连续性产生针孔。
漆膜偏心度对漆包线机械性能的影响。漆包线漆膜的耐刮性能反映的是漆膜 抗机械刮伤的强度,当漆膜涂覆不均时,在漆膜薄的地方易产生铜线的氧化,而 氧化层使漆膜的附着力大大下降,这样漆包线在做耐刮试验的时候,漆膜会被刮 针成块地撕破、带走,而形成短路,造成较低的耐刮数据;在漆膜较厚的地方,如 上述又会因漆膜的弹性差和附着性能下降而影响漆膜的耐刮性。漆包线漆膜偏心 度大对漆包线耐刮性能影响尤为明显的是漆包线三个面(漆包圆线每次旋转 120°,共旋转两次)的往复刮漆次数相差很大。
偏心度过高导致绝缘性能不达标,若通过提高漆膜厚度改善绝缘性能会牺牲 槽满率,如何平衡槽满率与绝缘性能是各家的工艺 knowhow。通过漆膜厚度对 槽满率影响的敏感度分析,当单边漆膜厚度由 0.08mm 增加至 0.16mm 时,槽满 率将由 70%降低至 66.3%。槽满率是电机的关键性指标,将影响电机转换效率、 散热效果、功率密度等。
5.4. R 角变小,提升槽满率,对涂覆要求更高
降低 R角弧度也有助于增加槽满率。槽满率是电机企业孜孜不倦的追求目标, 根据测算,当 R 角由 0.8mm 降低至 0.3mm 时,槽满率提升 0.9%。
降低 R 角同时对扁导线的生产工艺和绝缘漆涂覆有更高的要求。电磁线的原 材料铜杆在经过拉伸后其截面会自然形成圆形,而扁线则需要依靠专业的模具或 精轧成形,R 角越小,对设备的精度要求越高。扁线生产成为发卡状的过程中需 要弯折且 R 角处的漆膜出现拉伸,漆膜厚度降低。在“趋肤效应”的作用下,R 角越小的地方,电场强度越高,而该处的漆膜又最薄,从而成为薄弱点,R 角降 低增加了 R 角处出现电晕腐蚀的概率。实际有效的绝缘能力是由最薄处决定的, R 角越小,越能体现出企业的加工精度高。
6. 技术迭代:800V 扁线与绕组成型技术路径
6.1. 新能源电机要求明显高于工业电机
电机是电动汽车唯一的动力源,承受着复杂的运行环境及工况,造成对扁线 的质量要求远高于传统工业电机。虽然两者的分类及控制的理论和方法相同,但 用于电动汽车的电机通常要求频繁起停,快速动态响应,低速恒转矩运行且过载 能力强,转速变化范围宽,在充分满足汽车运行功能的同时还应满足行驶时的舒 适性,适应环境的能力等。电动汽车电机所用驱动器相比于工业用电机的驱动器 来说,在尺寸、工作环境、可靠性、功率密度、冷却方式等方面有较大差异,对电 动汽车电机驱动技术的基本要求总结如下:
1)严格的体积要求和重量要求:普通工业电机对于体积尺寸和重量没有这么 严格的要求,一般以满足工业目标为第一目的。电动汽车不同,尺寸和重量决定 了汽车的动力性能和驾驶体验,直接影响产品的质量。所以电动汽车电机的难点 就在于提高功率重量密度和功率体积密度,要求电机质量轻、体积小的同时追求 高功率。
2)独特的转矩特性:启动或低速时要求超高转矩,将汽车速度以最快的方式 泵升至期望速度。一般工业电机并没有这么高的启动速度要求。同时高速时需要 提供足够的功率,使得汽车可以高速巡航。
3)宽调速范围:车用电机最高转速可能是电机基速的 4 倍甚至更高。目前电 动汽车普遍只使用固定档的齿轮组,这要求电机的调速范围越宽越好。以特斯拉 的 Model S 基本款为例,电机最高转速能达到 18000 转/分钟,这对于电力电子 调速器来说是一个非常大的考验。
4)全范围转换效率要求:工业电机基本都处于额定工况中运行,固定转速、 功率、环境等。而车用电机作为汽车的唯一动力源,需要应对汽车复杂多样的运 行工况,对全范围的转换效率要求极高。
5)高安全性,任何情况下都应确保具有高度的安全性,尤其是失效模式下可 控。
6)低噪声:包括电磁噪声和音频噪声,满足车辆电磁兼容性和驾驶舒适性需 要。
6.2. 800V 的扁线技术路径:厚漆膜 VS PEEK,厚漆膜性能不佳但便宜
800V 被认为是下一代电动车必经之路,2019 年保时捷发布全球首款 800V 车型 Taycan。现代 E-GMP5、奔驰 EVA、通用第三代纯电动平台以及大众 Trinity, 都选择了 800V 电压平台。吉利 SEA浩瀚平台、广汽、奇瑞、上汽等车企都在规 划 800V 的方案,800V 成为车企新一轮竞争的制高点。
800V 的核心优势是快充性能提升明显。800V 电压平台搭配 350kW 超级充 电桩所能实现的充电速度,不仅比目前常见的 120kW 直流快充桩要快上很多,更 逐步接近传统燃油车在加油站加油的使用体验,尤其对于没有家用充电桩安装条 件、充电依赖公共充电设施的用户来说是一大利好。Taycan 支持 800V直流快充, 最大充电功率 250kw,在 22.5 分钟内能从 5%充到 80%的电量。在补能焦虑依 旧困扰电动车发展的背景下,如何比拼补能速度成为新的焦点,800V在这方面具 有得天独厚的优势。
800V能显著降低高压线束线径,减少发热,降低质量,节约线束成本。电压 等级从 400V 提高至 800V,根据最简单的 P=UI,在输出相同功率的情况下,800V 系统所传输的电流就更小,线缆线径和重量就可以降低,节省线束的成本及安装 空间。
800V平台下电晕腐蚀出现概率增加,电晕腐蚀会对电机绝缘造成重大危害。 电晕放电(coronadischarge)是指气体介质在不均匀电场中的局部自持放电,是 最常见的一种气体放电形式。通常发生在在曲率半径很小的尖端电极附近,如绕 组出槽口处、绕组绝缘层内部等。电晕即气隙放电,部分能量转换为光、热、声、 电磁等,会造成 1)热效应局部温度升高,绝缘老化等;2)机械损坏,大量带电 离子“电子和正负离子”以高能量和高速度撞击,造成绝缘层机械强度降低、局部 放电区域绝缘层出现麻点、麻坑、孔眼等绝缘失效问题;3)化学损坏,气体局部 放电形成臭氧,臭氧化学性质不稳定,易生成氧化氮,再与水蒸气反应生成硝酸, 腐蚀绝缘层。
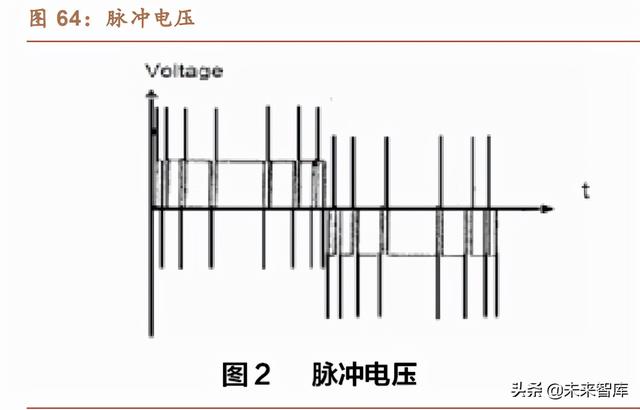
要满足 800V 的技术要求,主要通过两种技术路线:1)厚漆膜工艺,2)薄 漆膜+PEEK 膜包工艺;
提升漆膜厚度是最简单有效的途经,漆包线的绝缘性能与漆膜厚度成正比, 现在主流的新能源扁线的结构是:内层为铜扁线导体,根据扁线性能要求和使用 领域不同,铜扁线导体外涂设有二层或者三层绝缘漆膜,漆膜具体包括底漆层、 耐电晕漆层和面漆层。第一层为聚酯亚胺或者聚酰胺酰亚胺漆膜,第二层为耐电 晕漆膜,第三层为聚酰胺酰亚胺或者聚酰亚胺漆膜。
根据精达股份杨思伟的讲话,厚漆膜工艺解决电晕腐蚀主要有以下 3 条 路线:
1)提高漆包线的局部放电起始电压(PartialDischarge Inception Voltage, PDIV)值:使漆包线的 PDIV 值高于电机运行中的过冲电压,保证不会因为局 部放电而发生绝缘损耗现象。高压电机用的漆包线,通常采用介电常数低的 PI 漆膜,因为 PDIV 和介电常数呈反比关系,介电常越低 PDIV 值越高。另外还 可以增加漆膜厚度,从而达到提高 PDIV 值。目前精达股份可以做到双边膜厚 320μm,PDIV 可达 2300Vp 以上。
2)提高漆包线的耐电晕性能:过提高漆包线的耐电晕性能来增加漆膜的 寿命。它是通过延长破坏通道路径,耐电晕层可以作为放电阻挡层,降低局部 放电漆膜侵蚀;有利于空间电荷的扩散,抑制空间电荷的积聚。
3)兼顾 PDIV 和耐电晕性能:用 PI+P(A)I 耐电晕的涂层,这样漆包线不 但具有耐电晕性能同时还兼具高 PDIV 的特性,目前精达股份漆膜厚度可达 320μm,常温可以达到 2200Vp 以上。
厚漆膜工艺有以下缺陷:1)由于漆包线生产方式为多道涂覆+重复烘烤,为 使漆膜达到指定的厚度,需要对原有漆包机进行改造,将几个机头合并在一起才 能连续生产。改造后的漆包机产能下降,产品的单位能耗上升,同时排出的废气 也大量增加。2)工艺繁琐,产品需要经过三十次以上的涂覆烘烤过程,行线过长, 要调整部分工艺参数:一方面,因生产中烘烤次数过多,易造成漆膜固化过度,损 伤漆膜,从而影响产品性能,产品偏心度也比一般产品大。另一方面,产品在生产 过程中漆包线多次往复经过导轮,也必定会对漆层造成损伤,造成产品质量下滑。 3)上述超厚型漆膜的设计是出于满足驱动电机线圈耐高电压和高 PDIV 的目的, 但漆膜过厚会对其他性能产生负面影响;包括但不局限于出现漆膜柔韧性下降、 驱动电机线圈绕制过程中漆膜易开裂、不能满足某些驱动电机长期在恶劣的工作 环境(如高温环境)下使用等状况,从而给漆包线生产厂家及使用客户带来诸多困扰。
薄漆膜+聚醚醚酮(PEEK)被认为是驱动电机领域的终极绝缘方案。塑料之 王 PEEK 具有优良的综合性能,在许多特殊领域可以替代金属、陶瓷等传统材料。 该塑料的耐高温、自润滑、耐磨损、耐电晕腐蚀和抗疲劳等特性,使之成为当今最 热门的高性能工程塑料之一,它主要应用于航空航天、汽车工业、电子电气和医 疗器械等领域。
PEEK 的综合性能碾压漆包产品,电机的使用环境越严苛,PEEK 的优势越明显,PEEK的优势包括:1)耐高低温,持续使用温度达260℃,低温可耐受-100℃; 2)化学性能极为稳定,各种常见溶剂中只有硫酸可溶解破坏它;3)耐水、海水、 蒸汽,低渗透性,低吸湿性,长期放置在湿热条件下仍能保持结构及性能稳定; 4)在熔融状态下具有良好的流动性,凝固后具有优异的机械性能和尺寸稳定性, 使其可以通过挤出工艺一次性加工成型达到要求,降低了产品的加工难度和成本; 5)在较宽的频率和温度范围内保持良好的电气特性,完全满足电磁线绝缘要求; 6)无毒无污染,加工过程中产生的废料可完全回收,减少成本的同时环保清洁; 7)优异的介电强度,超高的 PDIV值;8)优异的稳定性,在长时间使用中,性能 衰减程度小。
PEEK 材料适合单层挤出,实现更高的功率密度。PEEK 多层挤出指的是挤 出到涂覆层之外,可显著提高绝缘性能;单层挤出指的是直接挤出到铜线上,无 需粘接层。单层挤出可实现更薄的导线结构,从而实现更高的导线密度, 从 而提高驱动电机的功率密度和槽满率。
PEEK 已经应用在电驱领域中,代表性产品为本田 IMMD 驱动电机,采用古 河电工提供的 HVWW 高压线,与漆包线相比,PEEK 采用挤出工艺可以获得更大 的壁厚和更好的同心度,带来的就是更高的 PDIV 值和尺寸一致性。此外由于 PEEK 耐磨性能好,铜线之间预留的安装尺寸更小,能够实现更高的紧凑度,从 而提升槽满率。
PEEK 的大规模应用主要难点:1)专利限制,2)成本高昂
1)专利限制:PEEK 应用的关键专利归日本古河电气工业株式会社所有。该发明提供一种抗变频器浪涌绝缘电线,其在无损高温下的绝缘性能的情况下可使 绝缘层厚膜化、并具有较高的局部放电起始电压与优异的耐热老化特性。其中, 在导体 1 的外周具有至少 1 层漆包烧结层 2,在漆包烧结层 2 的外侧具有至少 1 层挤出被覆树脂层 3,漆包烧结层 2 与挤出被覆树脂层 3 的合计厚度为 50μm 以 上,漆包烧结层 2 的厚度为 60μm 以下,挤出被覆树脂层 3 的厚度为 200μm 以 下,挤出被覆树脂层3在25℃~250℃的拉伸弹性模量的最小值为100MPa以上, 将漆包烧结层 2与挤出被覆树脂层3合在一起的绝缘层的相对介电常数在 25℃为 3.5 以下、在 250℃为 5.0 以下,漆包烧结层 2 在 250℃的相对介电常数(ε1')与 挤出被覆树脂层 3 在 250℃的相对介电常数(ε2')的关系满足(ε2'/ε1')>1。
挤出 被覆树脂层为热塑性树脂的层,作为形成挤出被覆树脂层的热塑性树脂,例如可 以挤出聚醚醚酮(PEEK)。若采用这些热塑性树脂,则与上述厚度、合计厚度、以 及相对介电常数、相对介电常数及在 25℃~250℃的拉伸弹性模量的最小值的比 相互作用,从而局部放电起始电压更进一步提高,低温下直至高温下的机械特性 及高温下的绝缘性能也高度地维持,而且耐热老化特性也更进一步提高。
中国企业也在研发 PEEK 相关产品。2021 年 6 月 11 日精达股份的发明专利 (一种 PEEK 电磁线的加工工艺)获得授权。该发明提供一种结构合理而使用可 靠便捷的 PEEK 电磁线的加工工艺,其工艺控制点较少且步骤简化程度高,无需 额外对漆包机进行改造,同时大幅度减少了废气废液的排放,降低能耗;按照该 发明所提供的漆包线生产工艺所加工出的 PEEK 漆包线,具备了表面硬度大、耐 刮擦、耐化学试剂、耐高温高压及能适应各种恶劣工作环境工作的优势,能满足 现有厂家及客户对 PEEK 漆包线的生产加工及使用需求。
2)成本高昂:PEEK 高昂的成本是阻碍其大规模应用的重要因素之一,PEEK 的综合性能和优势碾压其他产品,但同时采购成本高昂,预计未来将首先应用在 1)使用环境恶劣,对性能要求高的车型;2)对成本敏感度低的豪华车型。
6.3. 绕组成型技术路径: Hair-pin 占上风,长安 iDD 混动系统选择 Swinding
根据联合电子的文章,从驱动电机定子绕组技术的发展历程看,可以将其划 分为第一代径向嵌装绕组技术与第二代轴向嵌装绕组技术。
第一代绕组技术:径向嵌装绕组。径向嵌装绕组是指将铜导体绕制成型后, 沿定子铁芯齿部的极靴口将绕组从径向方向装配进铁芯槽内。从 1888 年开始,工 业电机上应用的主流绕组技术均为径向嵌装绕组,初期绕组技术以分布式圆线径 向嵌装绕组为主,1942 年又逐渐衍生出集中式圆线径向嵌装绕组,随后到 1995 年发展出集中式扁线绕组以及分布式波绕扁线绕组。
径向嵌装绕组难以适应自动化生产。径向嵌装式绕组技术由于其铁芯槽口极 靴形状的结构设计受限,会直接影响到电机的峰值/持续特性以及 NVH 性能,此 外在生产工艺上往往还需要手工介入调整,难以实现高节拍(60s 以内)的自动化 生产。
第二代绕组技术:轴向嵌装绕组。从 1958 年开始,随着绕组技术的进一步成 熟,第二代轴向嵌装绕组技术开始进入市场应用,初期的轴向嵌装绕组也主要应 用在大中型工业电机中。轴向嵌装绕组是指将半成型或者未经预成型的扁铜线导 体,沿定子铁芯的端面槽口将绕组从轴向方向装配进铁芯槽内。
轴向嵌装绕组的第一个技术分支:Hairpin 绕组。Hairpin 绕组凭借其优异的 功率,扭矩与效率性能迅速占领主流技术市场。Hairpin 绕组可以大大减少绕组嵌 装所需的装配预留空间和导体间隙,其槽满率可以达到 70%左右。
轴向嵌装绕组的第二个技术分支:I-Pin 绕组。I-Pin 绕组无需预成型且为单 槽装配,可以进一步降低绕组的装配预留空间,其槽满率可以达到 74%左右(以联合电子目前已批产的 I-pin 产品为例),具有更为优异的功率,扭矩与效率性能。 缺点是焊接工艺繁琐,端部尺寸较大。
轴向嵌装绕组的第三个技术分支:S-winding 绕组。S-winding 绕组具有众多 优势:1)成型后两头端部无需焊接,端部空间尺寸更小;2)更加优秀的 NVH性 能,减少了转矩脉动(即随着电机轴旋转而导致的转矩输出周期性增加和减少) 从而实现更平稳的运行;3)更出色的冷却效果。
2018 年博格华纳凭借性 S-winding 型绕组导线成型技术荣膺《汽车新闻》 杂志颁发的 PACE 大奖。该方案尤其适用于安装空间有限的 P2 混合动力汽车, S-winding 绕组比集成绕组定子短 30%左右,而扭矩密度提高了 50%以上。
2021 年 6 月长安汽车最新发布的蓝鲸 iDD 混合动力系统采用 S-winding 绕 组。搭载该系统的 SUV 车型 UNI-K PHEV 的匮电油耗仅为 5L/100km,其核心零 部件蓝鲸电驱变速器采用的就是 S-winding 绕组,电驱动综合效率 90%;电机控 制器最高效率超过98.5%,电机功率密度达到10kW/kg,液压系统压力高达60bar。 官方宣称,蓝鲸 iDD 系统最高传递效率达到 97%,系统综合扭矩最大可达 590 牛·米,百公里加速最快 6 秒+,最高车速可达 200km/h。
不同技术路线对生产设备及工艺的影响极大,绕组生产步骤大致分为:插头、 线成型、扭头、切平、焊接等。Hair-pin 在各步骤的生产工艺难度适中,而 S-winding 在线成型加工步骤上难度极高,但在焊接、端部高度等方面存在优势。
目前的技术路线仍然以 hair-pin 工艺技术路线为主,I-pin 以联合电子、博世 为代表,S-winding 以博格华纳为代表。
(本文仅供参考,不代表我们的任何投资建议。如需使用相关信息,请参阅报告原文。)
精选报告来源:【未来智库】「链接」。
相关参考
特种专用电机的种类有(新能源汽车扁线电机专题报告:百倍市场空间,尽享双重红利)
...物扁线应用于永磁同步电机的铜线绕组当中。以绝大部分新能源汽车采用的永磁同步电机为例,电机结构包括定子组件、转子组件、基座、端盖以及其他辅助标准件。定子组件包含了定子铁芯、铜线绕组、引出线和绝缘材料,一...
新能源汽车高速发展,带来技术革新,其中电机作为新能源汽车动力总成的关键部件,是车辆行驶中的主要执行机构,决定了整车的动力性能。新能源汽车电驱核心部件发卡电机以其独特的优势将以雨后春笋般爆发,江苏大族智...
扁线电机的定义电驱动系统作为新能源汽车的核心零部件之一,对新能源汽车的性能有着重要影响,对于新能源汽车的动力性、经济性、舒适性、安全性、可靠性、耐久性有着重要意义。而提高电驱动的技术水平和质量,需要从...
扒电机铜的机器(铜扁丝轧机,铜合金扁丝轧机,镀铜扁丝联轧机,漆包铜扁线连轧机)
...,PLC控制轧机设备电器系统,在运行过程中合理分配每个电机马达的转动频率,保证整条生产线的协调稳定运行。设备高度自动化,在运行过程中可自动调整产品尺寸,整机操作简单,容易上手,在提高生产效率的同时节省人工...
来源:科技日报把“命门”掌握在自己手中金凤前不久,随着吉利汽车、中通客车等国内知名车企的电动车下线,精进百思特电动(上海)有限公司(以下简称精进电动)牵头研发的新能源汽车高性能永磁电机已经装机超7万台。...
来源:科技日报把“命门”掌握在自己手中金凤前不久,随着吉利汽车、中通客车等国内知名车企的电动车下线,精进百思特电动(上海)有限公司(以下简称精进电动)牵头研发的新能源汽车高性能永磁电机已经装机超7万台。...
第四章:新能源汽车的驾驶特点新能源汽车的能量回收-0403能量回收的原理传统燃油车没有能量回收,燃油在发动机内燃烧,化学能转为动能驱动车辆,刹车时通过摩擦减速,将动能转为热能并释放掉。新能源汽车由于使用了电...
...、凌达压缩机、凯邦电机、新元电子(电容)、格力电工漆包线等一系列高端工业零部件。空调心脏:压缩机 压缩机,是将低压气体提升为高压气体的一种从动的流体机械,是空调的心脏
无磁界电热板与碳纤维哪个好(新能源汽车驱动电机行业研究:市场空间、发展趋势和产业链拆解)
...况:永磁同步电机主导,2025年市场规模有望达到385亿元新能源汽车驱动电机基于电磁感应现象,将电池中的电能转化为机械能,驱动新能源汽车行驶,是决定新能源汽车动力性能的核心零部件之一。主流的交流驱动电机利用定...
汽车旧发电机回收厂家(2017中资汽车及零部件产业十大海外并购)
...业务……近年来在燃油汽车禁售紧逼、国家政策重点支持新能源汽车的产业环境下,中国企业斥重金并购海外车企及零部件企业的案例已频频见诸媒体。今年以来,中国整车厂商和零部件企业在相关政策支持下,纷纷走出国门,...