数控车床送两次料怎么编(你知道如何高速铣削加工薄壁件?)
Posted
篇首语:总有一些人路过你的人生,微不足道又无比重要。本文由小常识网(cha138.com)小编为大家整理,主要介绍了数控车床送两次料怎么编(你知道如何高速铣削加工薄壁件?)相关的知识,希望对你有一定的参考价值。
数控车床送两次料怎么编(你知道如何高速铣削加工薄壁件?)
薄壁件多指壁厚与轮廓尺寸之比不超过1∶20的工件,有薄壁箱型、薄壁筒型及薄板型等多种结构,具有空间占用比较小、质量轻等优势,被大量使用在航空航天、精密仪器等多个领域[1]。目前国内外主要采用数控技术、加工中心及高速加工方法加工薄壁件,特别是高速铣削的加工方式被广为采用,以此来满足薄壁件的高加工精度要求,以及提升工作效率。通过加工工艺方案分析及判定,减小高速切削过程中薄壁件的变形,最终满足工件成形技术要求。
本文针对薄壁件的特点、结构要求及工艺路线等进行理论分析,阐述薄壁件加工技术难点和工艺方案,重点使用数控车床和加工中心设备,以高速铣削方式达到零件的结构及精度要求。
01
影响薄壁件变形的多种因素及解决措施
(1)工件本身的结构及材料 汽车工业及航空航天领域存在大量回转类、板框类和曲面类工件,不同结构工件的强度、刚度存在差异。材料不同、力学性能不同,切削加工性就会产生很大的差异。
(2)夹具 工装夹具的结构和夹紧力对薄壁零件变形影响很大。工件若受夹紧力不均,则形位会发生变化,从而影响加工精度。预防措施一是采用圆弧形卡爪,将点接触变为面接触,增加接触面积;二是采用开口套,将卡爪的点受力转化成开口套的面夹紧,使得受力均匀,变形均匀;三是采取可溶性胶灌注,在工件内注入可溶性胶,之后夹紧[2]。
(3)工艺参数 根据工件图样选择相应的刀具,匹配合理的进给速度、转速及切削深度。可以采用高速切削技术来降低加工时的切削力,以减少变形。由于随着吃刀量的增大,切削力增大,工件的振动也会增大,因此在加工薄壁件时,应选择较小的吃刀量,以减少振动,从而保证加工精度[3]。
(4)其他影响因素 主要是工件受热变形。若冷却性能不理想,切削过程中刀具及工件摩擦产生的热量也会导致工件变形,从而降低加工精度。
02
工件结构
图1所示工件材质为LY12CZ铝合金,外圆直径514mm,厚度7mm。外圆直径大、厚度薄,属于典型的薄壁零件。外圆上有加工环槽,且环槽尺寸较长,圆周端面上均布12个加工孔和4个支耳,工件刚性差,装夹和加工过程中极易发生变形。同时零件的平面度有较高的要求,沟槽及外表面的表面粗糙度要求也较高,使得工件加工难度较大,如加工工艺路线选择不当,则加工精度无法控制,工件质量得不到保证。
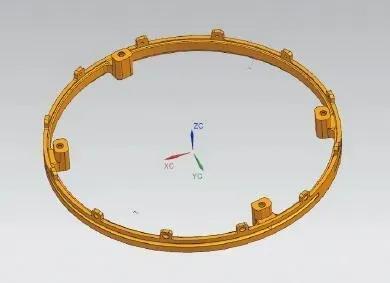
图一工件
工艺分析
(1)结构分析 工件为环形零件,结构整体规则,圆周上小孔均匀分布,支耳对称分布,沟槽沿圆周均匀分布,无异形面,无复杂结构,工件结构规整简单。
(2)材料分析 零件材料牌号为LY12CZ,属于含镁铜基铝合金,材料强度较高,在退火、淬火状态下有较好的性能,切削性能尚可。
(3)精度要求 该工件重点要求平面度≤0.05mm,要求环形槽表面粗糙度值Ra=1.6mm,其他表面粗糙度值Ra=3.2mm,其余皆为自由公差,精度要求并不苛刻。
(4)成形分析 工件为环形回转类零件,可采取车削和铣削方式达到成形零件的结构及精度要求,重点使用设备为数控车床和加工中心。
(5)工艺难点 工件本身结构简单,精度较易控制。由于工件壁薄,外圆尺寸大(直径达514mm),加工过程中极易产生变形,如不采取可靠的变形控制措施,则容易出现不合格品,所以工艺成形的难点在于变形的控制。可通过控制工件的变形,在工装和加工设备的保证下,加工出合格成品。
04
工艺方案
4.1 方案一
主要工序如下。
(1)数控车一 来料质检后,胀夹零件内孔,下料。
(2)数控车二 时效处理后,端面见光,保证平面度及外圆公差。
(3)加工中心铣削一 车削好的端面及外圆定位,粗开内腔及支耳圆周正面,预留余量,并保证总厚度。
(4)加工中心铣削二 内腔轮廓、厚度及外圆依次加工到位后,铣削环槽及外圆倒角到位,以外圆定位,再加工支耳螺纹到位。
(5)四轴加工中心铣削 外圆分中找正,圆周内孔及环槽清根到位。
(6)钳工序 倒钝锐边,去毛刺。
4.2 方案二
主要工序如下。
(1)数控车一 来料质检后,胀夹零件内孔,下料。
(2)数控车二 时效处理后,端面见光,保证平面度及外圆公差。
(3)加工中心铣削一 车削好的端面及外圆定位,粗开内腔及支耳圆周正面开粗,预留余量,并保证总厚度。加工完成后,每件用三坐标测量仪标记零件变形位置和变形量。
(4)加工中心铣削二 时效处理后,正面铣预留余量,并保证平面度。
(5)加工中心铣削三 以铣好平面定位,正面铣内腔及工艺支耳,预留余量,翻面开粗内腔及工艺支耳,预留余量,加工后用三坐标测量仪重点检测外圆及平面度,标记零件变形位置,若变形量大于要求,则全批次加工本序。
(6)加工中心铣削四 外圆定位,铣削内腔工艺支耳、外圆及表面到余量尺寸,翻面正面内腔开粗及工艺支耳加工到余量尺寸,加工后用三坐标测量仪重点检测外圆及平面度,标记零件变形位置,若变形量大于要求,则全批次加工本序。
(7)线切割 线切割去除两处工艺凸台,与内腔相接平,
(8)加工中心铣削五 外圆定位,铣削内腔轮廓、工艺支耳、外圆及表面,预留余量,用三坐标测量仪重点检测外圆及平面度,标记零件变形位置,根据变形量确认是否增加热处理工序。
(9)加工中心铣削六 外圆定位,先加工零件内腔轮廓到位,换压板加工外圆和厚度到位,T形刀加工圆周半环槽到位,外圆倒角加工到位,正面支耳加工到位,并进行首件检测。
(10)四轴加工中心铣削 外圆分中找正,圆周内孔及环槽清根到位。
(11)钳工序 倒钝锐边,去毛刺。
05
工艺方案比较
方案一下料后,一次性时效处理,端面见光,精度一次性到位,并以此端面为基准,加工后续外圆和内腔,通过粗、精两次加工达到工件成形。该方案工艺简单,能保证端面的平面度,加工速度快,但加工过程中工件变形不易控制,无过程监控,容易出现质量瑕疵,达不到尺寸及精度要求。
方案二前三道工序与方案一相同,第五道工序外圆及内腔开粗后,保留加工余量,并用三坐标测量仪检测工件变形量,通过时效处理、预留富余加工余量反复加工,以及使用三坐标测量仪进行外圆和平面度的过程检测,确保工件成形合格率。
方案一工艺流程简单,加工成本低,加工效率高,但工件变形过程控制手段缺失,易产生因工件变形而引起的不合格品;方案二工艺流程科学合理,采取变形控制措施,严格控制工件加工过程中的变形,有效解决了因工件变形而引起的产品不良问题,但是加工成本高。
由于方案二从根本上解决了工件变形、质量问题,优于方案一,因此采用方案二进行该薄壁件的加工更符合技术要求。
过程检验控制
加工过程中,对工件加工工序的过程检验是必不可少的程序,需要使用专业的检具和量具来完成零件尺寸和精度的检测。方案一没有采取相应的检测手段来测量工件的变形,主要依靠主观经验进行判断;方案二重点通过三坐标测量仪来检测工件的重要变形数据指标,使用客观科学的数据说话,对变形的位置、变形量进行精确掌握和分析,为判定下一步工序操作提供有力证据,从而可采取相应的措施,消除变形引起的偏差,加工出合格的零件。
07变形的控制
从影响薄壁件变形因素的角度入手,主要从以下几个方面进行变形控制。
(1)装夹方式 使用软卡爪胀夹内孔,避免车削过程中工件变形带来的尺寸偏差,同时在工件内腔左右两处留工艺凸台(见图2),凸台形状与支耳一致,便于零件装夹,减少零件变形。
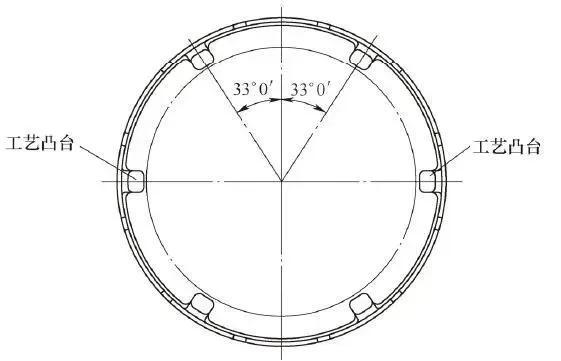
图2 工艺凸台
(2)降低工件残余应力 LY12CZ铝合金材料在加工过程中会产生内应力释放,从而产生材料变形。由于采用退火处理方式难以控制变形,因此采用在200℃保温12h、空冷的时效处理方式,消除加工残余应力,减少工件变形。
(3)使用合理的工艺参数 高速切削过程中,为减小切削力,减小工件变形,尽量使用小的轴向切削深度,可以选择较大的径向切削深度,甚至可以大于刀具的半径。径向切削深度大于刀具半径时,随着切削用量增加,加工效率提高,而切削力最大值却保持在一个稳定值。切削速度的变化并不会影响薄壁件的几何结构尺寸,在主轴转速允许的前提下,可以尽量选择大的切削速度。
(4)其他因素的控制 薄壁件变形不仅受切削工艺参数的影响,还受走刀路径、机械振动和冷却方式等综合因素的影响。在走刀路径上,应以尽量减少工件最小刚度部位上的作用力为原则,可以采用对称加工或阶梯式加工的路径;在切削液方面,应加强加工中心的日常检查,查看冷却循环系统是否正常工作,切削液使用是否得当,参数设置是否合理。从而降低工件加工变形,保护刀具,延长刀具的使用寿命。
薄壁件的加工是公认的难题,且薄壁件有向极薄化方向发展的趋势,加工过程中主要是防止薄壁件发生变形而影响加工精度。通过制定合理的加工工艺路线,改善装夹夹具,选择科学的走刀路径及工艺参数,可以有效地降低薄壁件的变形,保证工件加工精度,提升加工效率。
相关参考
数控铣床编程教学视频(在数控铣床加工中,分享薄壁椭圆的加工经验)
...椭圆加工。通过完成该零件的仿真加工,掌握椭圆的数控铣削编程与加工方法。从本次任务图可知,该椭圆旋转了45°,铣床中有专门的旋转指令G68,在编程时可按照未旋转之前的进行编程,加一个旋转指令即可,因此编程十分...
如果你真的想做一件事情,那么就算障碍重重,你也会想尽一切办法去办到它。但若是你不是真心地想要去完成一件事情,那么纵使前方道路平坦,你也会想尽一切理由阻止自己向前。人生就要活得漂亮,走得铿锵。自己不奋斗...
数控加工机械基础知识(数控加工技术的基础知识(九)-- 高速加工技术)
高速切削加工工艺规划安全、高效和高质量是高速切削的主要目标。高速加工按目的分为两种情况:以实现单位时间最大去除量为目的的高速加工和以实现单位时间最大加工表面为目的的高速加工。前者用于粗加工,后者用于精...
...误差,以检验加工中心的几何特性。第二种试件用于检测两次间隔面铣削过程中是否存在接刀痕,用于评价机
数控车床对刀视频(「UG编程干货」模具零件数控铣削加工 从建模到编程了解一下)
2.1分析零件通过图形分析可知:(1)零件涉及曲面、钻孔等造型方法。(2)零件可以通过建立草图、拉伸、修剪体、镜像、扫掠等常用命令进行造型(3)为了保证加工精度,所以在三轴数控铣床上分两次次装夹完成,采用四边...
摩擦专用石墨粉(石墨高速加工用什么刀具(含铣削、车削、孔加工刀具))
...技术的发展,石墨材料的制造工艺不断完善,市场上石墨高速铣削机床应运而生,能满足不同加工需求的石墨材料层出不穷,数控电火花加工机床的石墨放电性能也有了全面的提升。石墨因具有较高的高温强度、低热膨胀系数、...
数控铣床刀补怎么使用(FANUC数控铣床编程实例2-铣削矩形零件平面二)
...能一次走刀加工完成。行间距取2/3倍的刀具直径,即8mm,两次刀轨间,刀具切过的重叠宽度则为4mm。刀具下刀点仍然是位于工件左侧之外,且刀具侧刃与工件有一定安全距离,Y位置要使刀具外沿超出工件下边缘一定宽度。刀轨...
数控铣削加工中刀具补偿的作用(玩数控不懂“刀具补偿”,你如何闯荡江湖?)
...工轮廓和编程轨迹完全一致,从而实现“刀具补偿”。01数控车床用刀具的交换功能1.刀具的交换指令格式一:T0101;该指令为FANUC系统转刀指令,前面的T01表示换1号刀,后面的01表示使用1号刀具补偿。刀具号与刀补号可以相同,...
数控车床常用的刀具有哪些(数控加工中心铣削过程中常用的刀具)
我们知道数控加工中心区别是数控铣床的一大特征就是有无刀库。加工中心一般具有机械手刀库内有16或24把刀具,可以在加工过程中完成自动换刀。不同的加工工序需要不同的刀具种类,但都用于切削金属材料,所以加工中心...
我们知道数控加工中心区别是数控铣床的一大特征就是有无刀库。加工中心一般具有机械手刀库内有16或24把刀具,可以在加工过程中完成自动换刀。不同的加工工序需要不同的刀具种类,但都用于切削金属材料,所以加工中心...