数控车床液压尾座m指令(MasterCAM车削编程,一步一步教你如何编程)
Posted
篇首语:知识是抵御一切灾祸的盾牌。本文由小常识网(cha138.com)小编为大家整理,主要介绍了数控车床液压尾座m指令(MasterCAM车削编程,一步一步教你如何编程)相关的知识,希望对你有一定的参考价值。
数控车床液压尾座m指令(MasterCAM车削编程,一步一步教你如何编程)
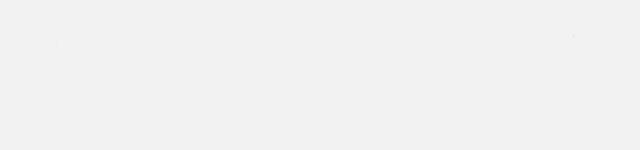
文末可下载《MasterCAM车削编程》
通过图11-1所示零件的加工,简要介绍Master CAM的车端面、粗车、精车、切槽、螺纹切削、钻孔和截断车削等自动编程过程。
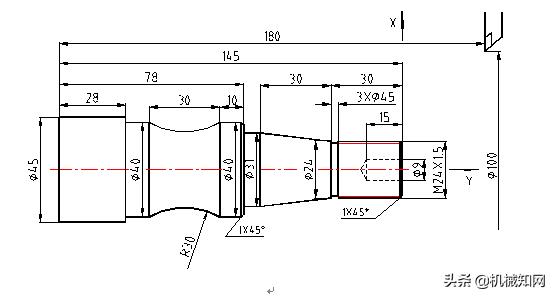
图11-1
注:⑴启动MasterCAM Lathe,按上图绘制出如图11-4所示的轮廓形状,中间连线不绘制。
⑵绘制图形时,X方向输入的坐标值为直径值;加工时,对话框中X方向的值亦为直径值。
11.1生成端面加工刀具路径
11.1.1 设置工件
1.Main Menu→Toolpaths→Job setup系统弹出如图11-2所示对话框。
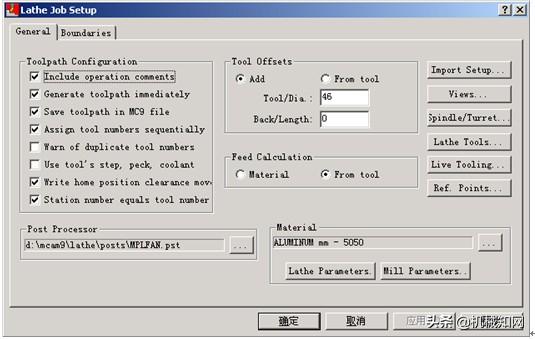
图11-2
⑴通过Tool Offsets设置刀具偏移。
⑵通过FeedCalculation设置工件材料。
⑶通过ToopathConfiguration设置刀具路径参数。
⑷通过PostProcessor设置后置处理程序。
2.选择Boundaries设置工件毛坯。见图11-3对话框。
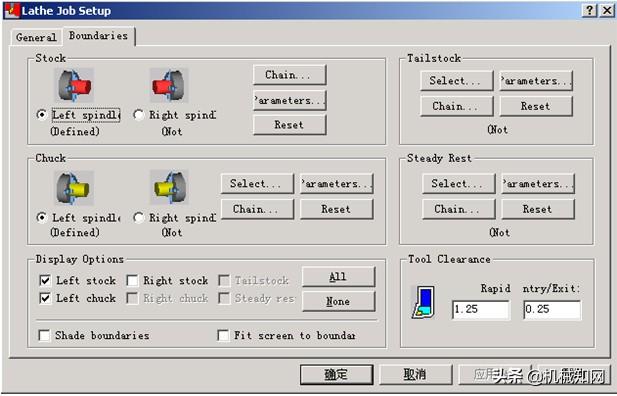
图11-3
⑴通过Stock项目设置工件毛坯大小。选择Parameters→Take from 2 point设置毛坯的左下角点为(-55,-190),右上角点为(55,10),生成虚线如图11-4所示的毛坯。
⑵通过Tailstock尾座顶尖的参数。(此例可不设置)
⑶通过Chuck设置卡盘的参数。
⑷通过Steady rest设置辅助支撑的参数。
⑸选择Ok,工件设置完成。
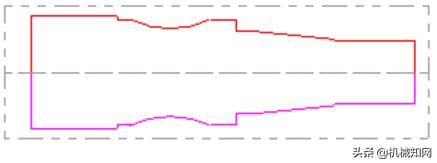
图11-4
11.1.2 生成车端面刀具路径
1.Main Menu→Toolpaths→Face系统弹出如图11-5所示的对话框。
2.在Toolparameters参数对话框中选择刀具,并设置其他参数。
3.选择对话框中的Faceparameters标签,并设置参数。见图11-6所示。Face parameters选项中各参数的含义如下:
⑴ Entry amount
Entry amount输入框用于输入刀具开始进刀时距工件表面的距离
⑵ Roughstepover
当选中Roughstepover输入框前面的复选框时,按该输入框设置的进刀量生成端面车削粗车刀具路径。
⑶ Finish stepover
当选中Fini9hstepover输入框前面的复选框时,按该输入框设置的进刀量生成端面车削精车刀具路径。
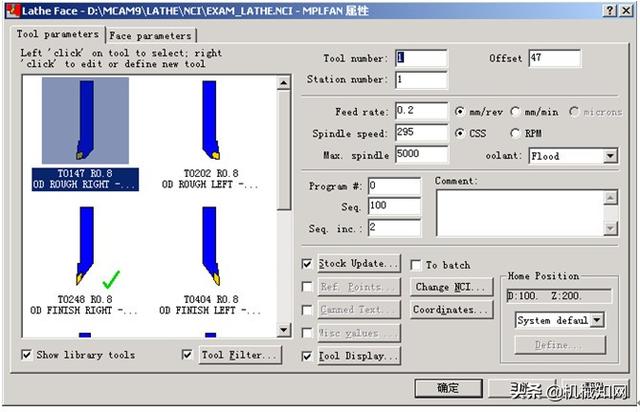
图11-5
⑷ Number of finish
设置端面车削精车加工的次数。
⑸ Overcut amount
该输入框用于输入在生成刀具路径时,实际车削区域超出由矩形定义的加工区域的距离。
⑹ Retract amount
该输入框用于输入退刀量,当选中Rapid retract复选框时快速退刀。
⑺ Stock to leave
该输入框用于输入加工后的预留量。
⑻ Cut away from center
当选中该复选框时,从距工件旋转轴较近的位置开始向外加工,否则从外向内加工,
4.选择SelectPoint,确定加工区域。
5.选择Ok,退出Face参数设置。生成如图图11-7所示的刀具路径。
11.2生成轮廓粗车加工刀具路径
接着前面的例子介绍轮廓粗车加工刀具路径的生成。
1.Main Menu→Toolpaths→Rough→Chain。选取所加工的外圆柱表面,如图11-8所示。然后选择Done。
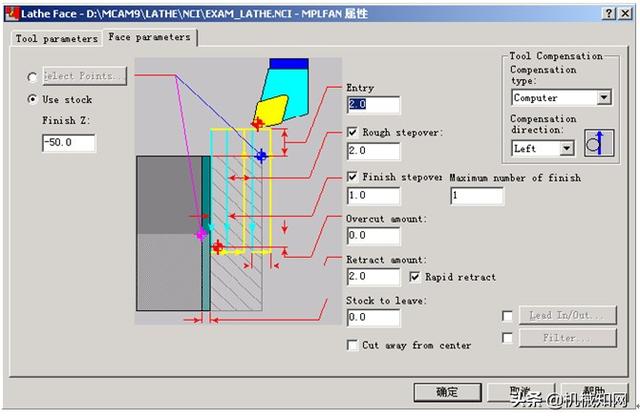
图11-6
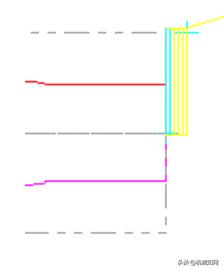
图11-7
2.系统弹出Toolparameters参数对话框和Roughparameters参数对话框。
3.Toolparameters参数对话框。见如图11-9所示。在Tool parameters参数对话框中选择刀具,并设置其他参数。
4.选择对话框中的Roughparameters标签,并设置参数。见图11-10所示,Rough parameters选项中各参数的含义如下:
⑴ Overlap amout
当选中该复选框时,相邻粗车削之间设置有重叠量。重叠距离由该复选框下面的输人框设置。若为设置进刀重叠,则将在工件外形留下有凹凸不平的扇形,Master CAM通过设置重叠量,使得粗车加工留下的材料都有一样的厚度。当设置了重叠量时,每次车削的退刀量等于设置的切削探度与重叠量之和。
⑵ Rough
Rough输入框用来设置每次车削加工的切削深度。切削深度的距离是以垂直于切削方向来计算的。当选中Equsl steps复选框时,将最大切削深度设置为刀具允许的最大值。
⑶ Stock to leave X
Stock to leave X输入框用于输入在X轴方向上的预留量。
⑷ Stock to leave Z
Stock to leave Z输入框用于输入在Z轴方向上的预留量。
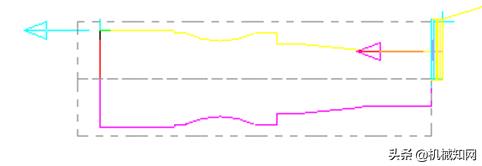
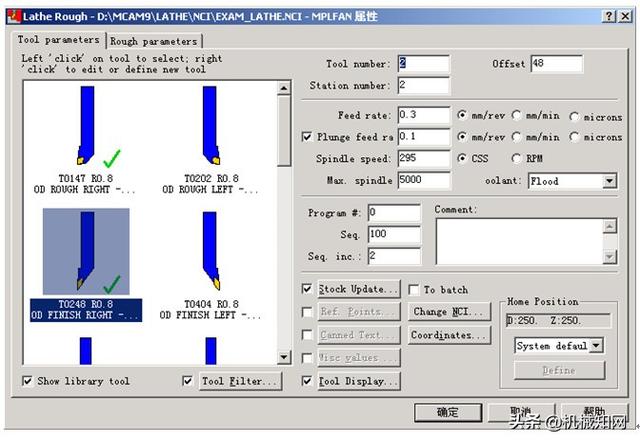
图11-9
⑸
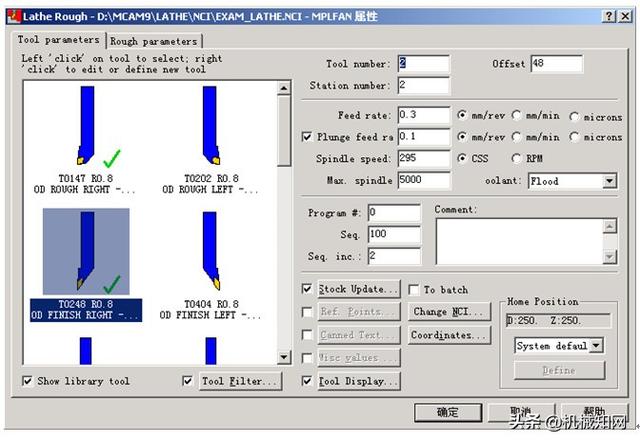
图11-9
Entry
Entry输入框用于输入刀具开始进刀时距工件表面的距离。
⑹ Cutting Method
Cutting Method框用于设置粗切加工的模式。Master CAM中提供两种选样:One-way(单向切削)和Zig-zag(双向切削)。在单向切削中,刀具在工件的一个方向切削后立即退刀,并以快速移向另一方向,接着下刀进行下一次切削加工。而双向切削,刀具在工件的两个方向进行切削加工,只有刀具为双向刀具才能进行双向切削。
⑺ Rough Direction/Angle
Rough Direction/Angle栏用于设置粗切方向和粗切角度。Master CAM提供了4种加工方向:
·OD(外径):在工件外部直径方向上切削。
·ID(内径):在工件内部直径方向上切削。
·Face(前端面):在工件的前端面方向进行切削
·Back(后端面):在工件的后端面方向进行切削。
粗切角度可以被设置为介于0至360之间的任意数值,一般情况下,外径或内径车削都是采用0°粗切角,端面车削则采用90°粗切角。
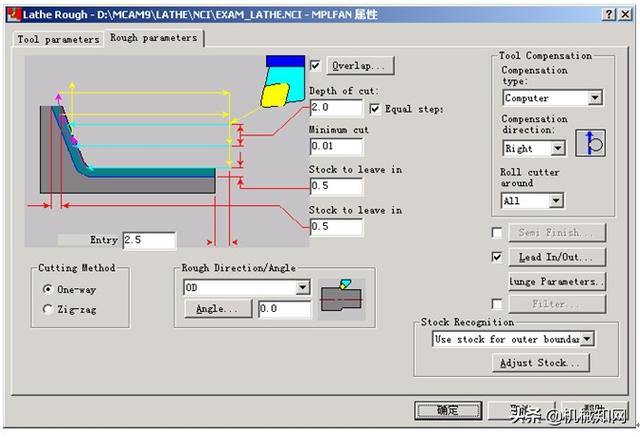
图11-10
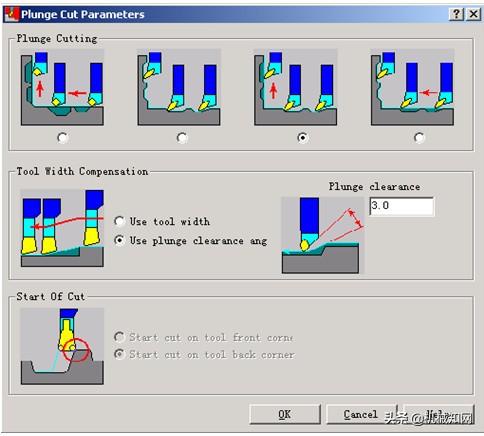
图11-11
⑻ Tool Compensation 刀具偏移方式设置。
⑼ Lead In/Out 添加进刀/退刀刀具路径设置。
⑽ Plunge parameters
设置底切参数。弹击Plunge parameters按钮,系统弹出图11-11所示的Plunge cut parameters对话框。该对话框用来设置在粗车加工中是否允许底切,若允许底切,则设置底切参数。
当选择Plunge Cutting栏中的Do not allow tool to plunge alongcut单选按钮时,切削加工跳过所有的底切部分,这时需要生成另外的刀具路径进行底切部分的切削加工。
当选择Plunge Cutting栏中的Allow tool to plunge along cut单选按钮时,系统可以进行底部分的加工,这时系统激活Tool WidthCompensation栏。
当选择Tool Width Compensation栏中的Use plunge clearance angle单选按钮时,激活Plunge clearance输入框,系统按Plunge clearance输入框输入的角度在底切部分进刀。
当选择Tool Width Compensation栏中的Use tool width单选按钮时,激活Start of Cut栏。这时系统根据刀具的宽度及Start of Cut栏中的设置进行底切部分的加工。
当在Start of Cut栏选中Start cut on tool front comer单选按钮时,系统用刀具的前角点刀底切加工。
当在Start of Cut栏选中Start cut on tool back comer单选按钮时,系统用刀具的后角点刀底切加工。通常这时刀具应设置为前后均可加工,否则将会引起工件或刀具的损坏。
5.确定。生成如图11-12所示的刀具路径。
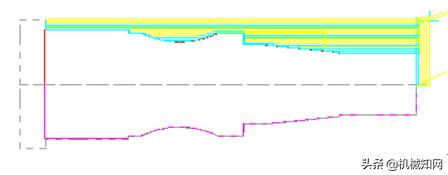
图11-12
11.3生成精车加工刀具路径
精车是沿工件的外侧、内侧或端面外形做一次或多次的车削。一般用于精车加工的工件在进行精车加工前因进行粗车加工。要生成精车加工刀具路径,除了要设置共有的刀具参数外,同样还要设置一组精车加工刀具路径特有的参数。精车加工参数在图所示的Finish parameters选项卡中进行设置。下面接着前面的例子来介绍生成精车加工刀具路径及NC文件的方法。
1.Main Menu→Toolpaths→Finish→Chain。选择与精加工的外圆柱表面,如图11-13所示。然后选择Done。
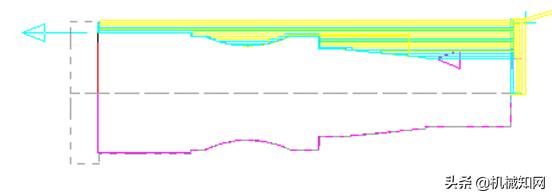
图11-13
2.系统弹出Toolparameters参数对话框和Finishparameters参数对话框。在Toolparameters参数对话框中选择刀具,并设置其他参数,如图11-14所示。
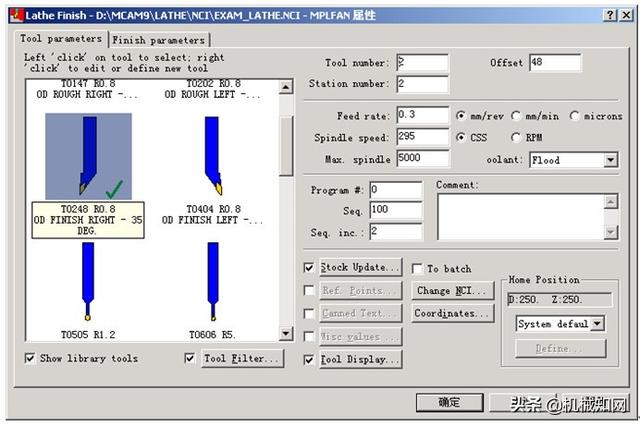
图11-14
3.选择对话框中的Finashparameters标签,并设置参数。Finishparameters选项卡中各参数与Roughparameters选项卡中的参数基本相同,如图11-15所示。Finish prameters选项卡中增加的Number of finish输入框用来设置精车加工的次数。精车加工的次数应设置为粗车加工预留量除以Finish stopover输入框中输入的精车加工进刀量。
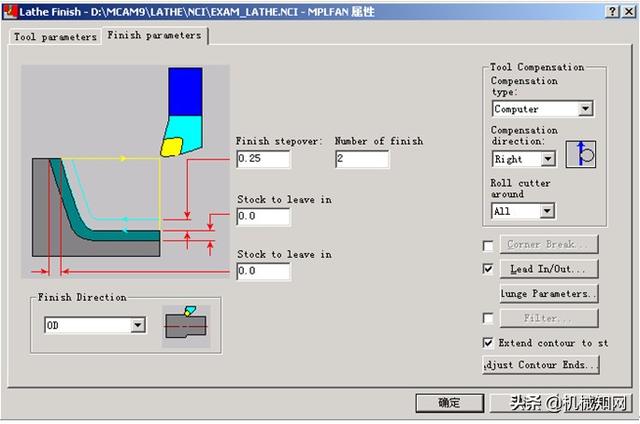
图11-15
4.确定。生成如图11-16所示的刀具路径。
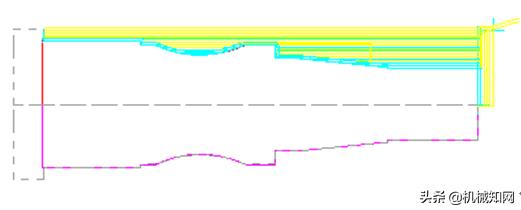
图11-16
11.4生成切槽加工刀具路径
加工如图11-17所示的退刀槽。
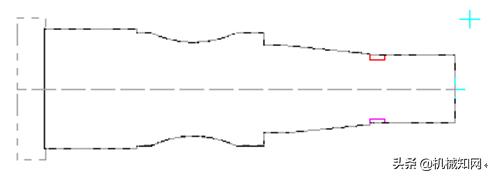
图11-17
1.Main Menu→Toolpaths→Groove→3 line→Ok→选择欲加工的槽→End here→Done。系统将弹出如图11-18所示的对话框。
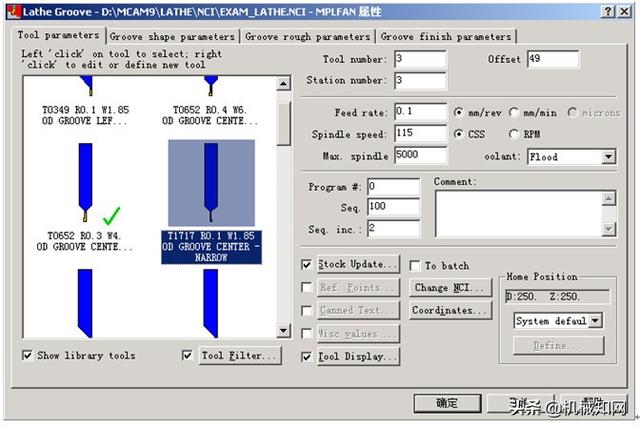
图11-18
2.Tool parameters参数对话框中选择刀具,并设置其他参数。
3.Groove shape parameters参数对话框中设置槽的形状。
4.Groove rough parameters参数对话框中设置槽的粗加工参数。
5.Groove finish parameters参数对话框中设置槽的精加工参数。
6.Ok。生成如图11-19所示的刀具路径。
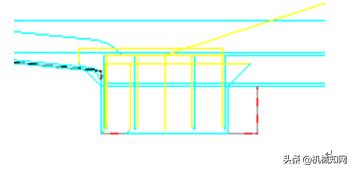
图11-19
11.5生成螺纹加工刀具路径
接着前面的例子来介绍生成螺纹加工刀具路径及NC文件的方法。
1.Main Menu→Toolpaths→Next menu→Thread。系统将弹出如图11-20所示的对话框。
2.在Toolparameters参数对话框中选择刀具,并设置其他参数。
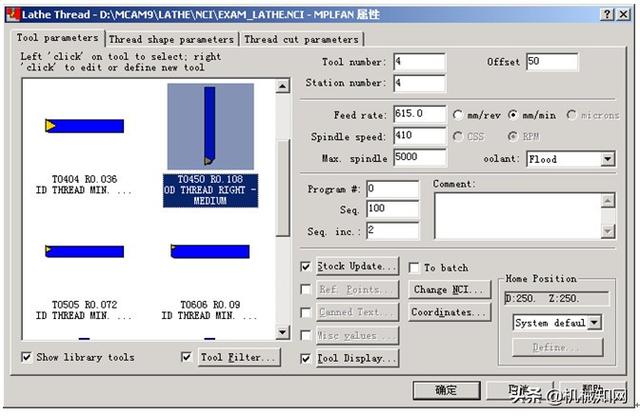
图11-20
3.在Thread shapeparameters参数对话框中定义螺纹参数。
见如图11-21所示,各参数的意义:
⑴ Lead
Lead输入框用来设置螺纹的螺距。由两种表示方法,当选择threads/mm单选按钮时,输入框中的输入值表示为每毫米长度上螺纹的个数;当选择mm/threads单选按钮时,输入框中的输入值表示为螺纹的螺距。
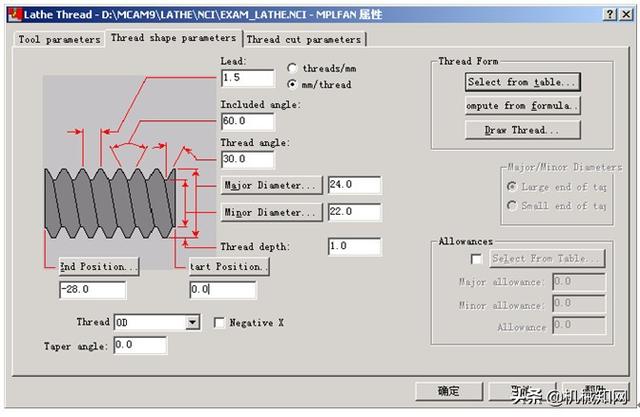
图11-21
⑵ Included angle和Thread angle
Included angle输入框用来设置螺纹两条边间的夹角,Thread angle输入框用来设置螺纹一条边与螺纹轴垂线的夹角。Thread angle的设置值应小于Included angle的设置值,对于一般螺纹,Included angle值为Thread angle值的2倍。
⑶ Major Diameter、Minor Diameter和Thread depth
Major Diameter输入框用于设置螺纹牙顶的直径;Minor Diameter输入框用于设置螺纹牙底的直径;Thread depth输入框用于设置螺纹的螺牙高度。
⑷ Start Position和End Position
Start Position输入框用于设置螺纹起点的Z坐标;End Position输入框用于设置螺纹终点的Z坐标。系统通过这两个值定义螺纹的长度。
⑸ Thread
当选择OD选项时,生成外螺纹加工的刀具路径;当选择ID选项时,生成内螺纹加工的刀具路径;当选择Face/Back选项时,生成用于加工螺旋槽的刀具路径。
4.在Thread cutparameters参数对话框中定义螺纹切削参数。见如图11-22所示,各参数的意义:
⑴ Nc code format
该参数用来设置螺纹指令的形式,用于切削螺纹的NC代码有三种:G32、G92、G76。G32和G92命令一般用于切削简单螺纹,G76用于切削复合螺纹。
⑵ Determine cut depths form
该参数用来设置定义切削深度的方式。当选择Equal area单选按钮时,系统按相同的切削量来定义每次的切削深度;当选择Equal depths时,系统按统一的深度进行切削加工。
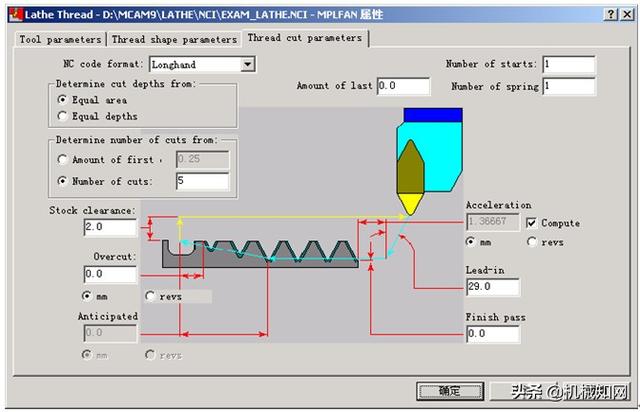
图11-22
4.Determine number of cut form
该参数用来设置定义切削次数的方式。当选择Amount of first单选按钮时,系统根据设置的第一刀切削量、最后一刀切削量(Amountof last)和螺纹深度来计算切削次数;当选择Number of cuts单选按钮时,系统根据设置的切削次数、最后一刀切削量和螺纹深度来计算切削量。
5.Ok。生成如图11-23所示的刀具路径。
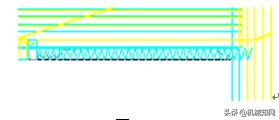
图11-23
11.6 生成钻孔加工刀具路径
MasterCAM的钻孔加工用于钻孔、镗孔或攻螺纹的刀具路径。系统提供20种钻孔形式,包括7种标准形式和13种自定义形式。要生成钻孔刀具路径,除了要设置共有的刀具参数外,同样还要设置一组钻孔刀具路径特有的参数。
下面接着前面的例子来介绍生成螺纹加工刀具路径及NC文件的方法。
1.Main Menu→Toolpaths→Drill,系统将弹出如图11-24所示的对话框。
2.在Tool parameters参数对话框中选择刀具,并设置其他参数。
3.在Simple drill– no peck参数对话框中设置孔的位置、深度及其他参数。如图11-25所示。
4.在Custom Drillparameters参数对话框中设置使用的典型钻孔循环。
5.Ok。生成如图11-26所示的刀具路径。
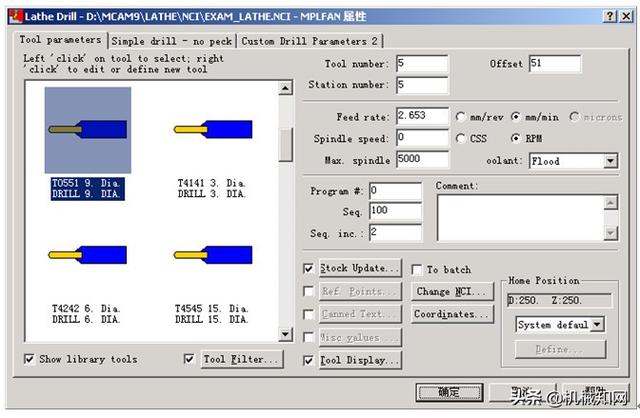
图11-24
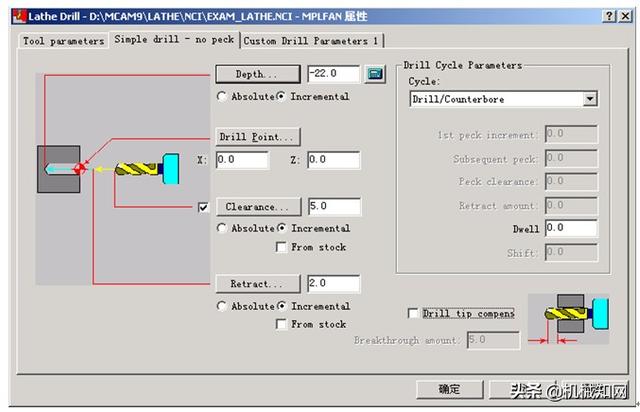
图11-25
11.7生成截断加工刀具路径
截断加工以生成一个垂直的刀具路径来切削工件,一般用于工件的切断。系统首先通过选取一个点来定义车削起始位置。然后设置共有的刀具参数,和一组截断车削刀具路径特有的参数。
1.Main Menu→Toolpaths→Next menu→Cutoff。系统将提示选取一个点来定义车削起始位置,输入截断点的坐标为(60,-145),回车确定,系统将弹出如图11-27所示的对话框。
2.Toolparameters参数对话框中选择刀具,并设置其他参数。
3.Cutoffparameters参数对话框中设置截断车削参数,如图11-28所示。
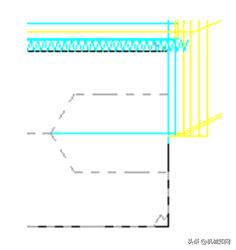
图11-26
Cutoff parameters选项卡中的大部分参数与前面介绍的参数相同,下面仅介绍截断车削特有的参数。
⑴ X Tangent Point
该参数设置截断车削的终止点的X坐标,系统的默认设置为0(将工件截断),用户可以在输入框中输入终止点的X坐标,也可以单击XTangent Point按钮在绘图区选取一点,以该选取点的X坐标作为截断车削终止点的X坐标。
⑵ Cut to
该参数设置刀具的最终切入位置。当选择Front radius单选按钮时,刀具的前角点切人至定义的深度;当选择Backradius单选按钮时,刀具的后角点切人至定义的深度。
⑶ Comer Geometry
该参数在截断车削起始点位置定义一个角的外形。当选择None单选按钮时,在起始点位置垂直切人,不生成倒角;当选择Radius选项时,按输入框设置的半径生成倒圆角;当选择Chamfer单选按钮时,按设置的参数生成倒角,其设置方法与切槽加工中切槽角点处倒角设置方法相同。
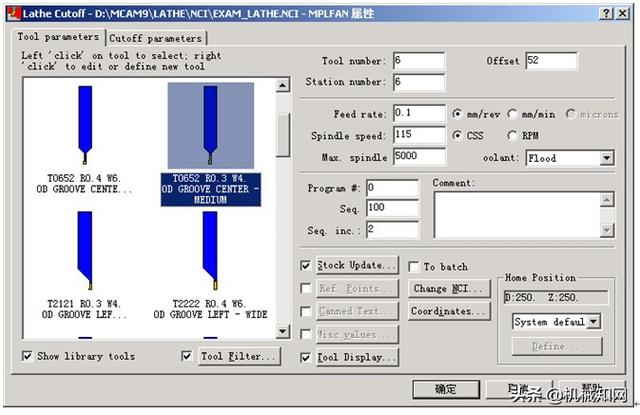
图11-27
4.Ok。生成如图11-29所示的刀具路径。
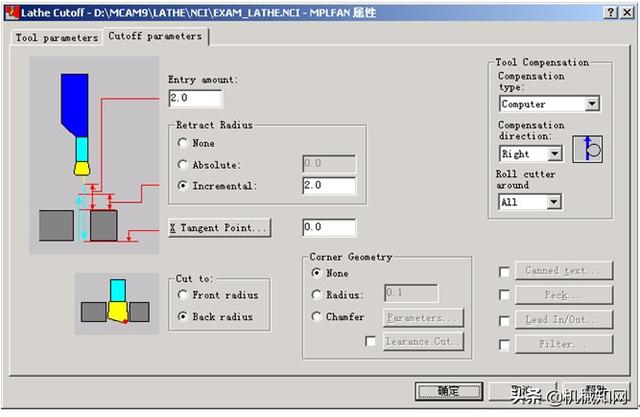
图11-28
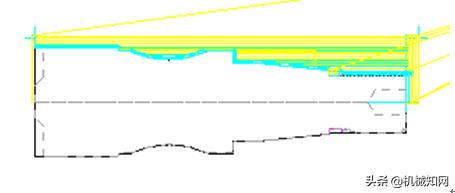
图11-29
11.8 刀具路径检查
通过Main Menu→Toolpaths→Operations或通过Main Menu→Nc utils进入刀具路径检查,操作过程与铣削加工相同。动态仿真结果如图11-30所示。
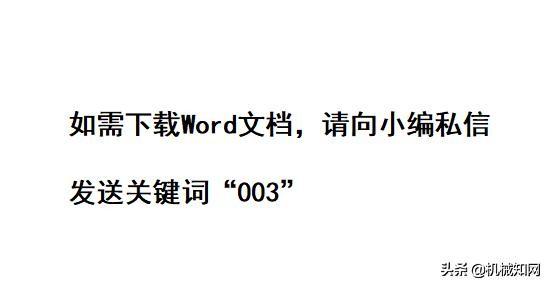
生成NC程序过程与铣削加工相同,可参考前面内容学习。
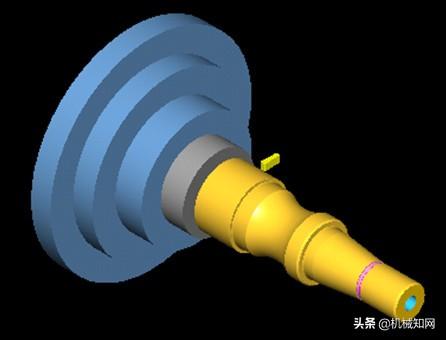
相关参考
数控车床编程常用指令(数控编程M代码大全,收集好了,超级好东西)
1、G00与G01G00运动轨迹有直线和折线两种,该指令只是用于点定位,不能用于切削加工G01按指定进给速度以直线运动方式运动到指令指定的目标点,一般用于切削加工2、G02与G03G02:顺时针圆弧插补G03:逆时针圆弧插补3、G04(延时或暂...
数控车床棒料怎么使用(总结篇:数控车削编程指令大全与实例介绍,内容简单详细)
1)绝对坐标编程常用代码X和Z表示;增量坐标编程时用U和W表示,可按绝对坐标、增量坐标或两者混合编程。--般不用G90、G91指令。2)由于车削常用的毛坯为棒料或锻件,加工余量较大,可充分利用各种固定循环功能,达到多次循环...
虽然现在CAM编程已相当普遍,但手工编程仍将在想当一段时间内有广泛的应用市场,所以本文所述的数控车削编程技巧还很有实际意义的。文中所列的原则、指令、技巧及注意事项都是作者通过实践得出并验证过的,所以很有实...
数控车床的组成及工作原理(数控车床加工实例工艺分析及编程(华中数控))
...指令及子程序的编程技巧。2、通过对零件的加工,了解数控车床的工作原理。3、了解典型零件的数控车削加工工艺。二、仪器与设备(1)配备华中世纪星数控系统的CK6032卧式车床一台。(2)尼龙棒(或塑料棒)一根(50—60mm,毛坯外形...
数控机床车削编程(数控车床车60度的顶尖编程,程序步骤很详细)
死顶尖也好,活顶尖也罢,通常都是常用件或标准件,市场上均可购买到!如果你想自己去制作一个死顶尖,个人观点,那个60°的尖不论是编程还是加工是最没技术含量的地方,如果编程,如图所示,按照三角函数关系,即可...
数控车床结构数控车床按结构分类卧式数控车床卧式数控车床主轴水平置的为卧式数控车床(最为常见的类型,除大型车床外基本都是卧式车床)立式数控车床立式车床立式车床主轴垂直水平面。立式车床主要用于大型重型工件,...
数控车床加工螺纹编程(数控车床的螺纹加工指令,复合循环指令你都知道吗?不知道的我教)
大家好,我是木子,今天给大家带来,数控车床基础的螺纹车削编程教学,话不多说,上干货螺纹车削加工指令一、螺纹加工方法在数控车床上加工螺纹的进刀方式通常有直进法和斜进法,如图所示。直进法使刀具双侧刃切削,...
数控车床在车削加工(数控车削编程综合实例大全完整版领取速来分享给自学者)
...大家的支持!喜欢我的作品记得多多关注+点赞+转发哦!数控车床的分类数控车床的基本功能数控车床的基本编程方法螺纹车削加工指令循环编程需要的朋友们下方留言《车削》最好是私信老师,即可领取哦!
数控车床自动编程(数控车削编程综合实例大全完整版领取速来分享给自学者)
...大家的支持!喜欢我的作品记得多多关注+点赞+转发哦!数控车床的分类数控车床的基本功能数控车床的基本编程方法螺纹车削加工指令循环编程需要的朋友们下方留言《车削》最好是私信老师,即可领取哦!
木工数控车床如何编程(数控车削编程教学来啦提升技术必学的干货)
...编程教学》里面涵盖的内容也是十分丰富,我会给大家从数控车床概述、床数控系统的基本功能、基本编程方法、加工指令、编程综合实例等给大家讲解,有需要学习的朋友们都可以给我留言哦,我就把完整版资料分享给你~大...