数控车床加工实训报告(数控机床 车床铣床编程方法及加工实例)
Posted
篇首语:历史和哲学负有多种永恒的责任,同时也是简单的责任。本文由小常识网(cha138.com)小编为大家整理,主要介绍了数控车床加工实训报告(数控机床 车床铣床编程方法及加工实例)相关的知识,希望对你有一定的参考价值。
数控车床加工实训报告(数控机床 车床铣床编程方法及加工实例)
一、基础知识点
- 1、从零件图开始,到获得数控机床所需控制介质的全过程称为程序编制,程序编制的方法有手工编程和自动编程。
- 2、数控机床实现插补运算较为成熟并得到广泛应用的是直线插补和圆弧插补。
- 3、自动编程根据编程信息的输入与计算机对信息的处理方式不同,分为数控语言编程(APT语言)、交互式图形编程。
- 4、数控机床由程序载体、输入装置、数控装置、伺服系统、检测装置、机床本体等部分组成。
- 5、数控机床按控制运动轨迹可分为点位控制、点位直线控制和轮廓控制等几种。按控制方式又可分为开环控制、闭环控制和半闭环控制等。
- 6、刀具主要几何角度包括前角、后角、刃倾角、主偏角和副偏角。
- 7、刀具选择的基本原则:安装调整方便、刚性好、耐用度和精度高;在满足加工要求的前提下,尽量选择较短的刀柄,以提高刀具加工的刚性。
- 8、刀具选择应考虑的主要因素有:被加工工件的材料、性能,加工工艺类别,加工工件信息,刀具能承受的切削用量和辅助因数。
- 9、铣削过程中所选用的切削用量称为铣削用量,铣削用量包括铣削宽度、铣削深度、铣削速度、进给量。
- 10、铣刀的分类方法很多,若按铣刀的结构分类,可分为整体铣刀、镶齿铣刀和机械夹固式铣刀。
- 11、加工中心是一种带刀库、自动换刀装置的数控机床。
- 12、FMC由加工中心和自动交换工件装置所组成。
- 13、切削加工时,工件材料抵抗刀具切削所产生的阻力称为切削力。
- 14、工件材料的强度和硬度较低时,前角可以选得大些;强度和硬度较高时,前角选得小些。
- 15、常用的刀具材料主要有高速钢、硬质合金钢、陶瓷、立方碳化硼、金刚石等。
- 16、影响刀具寿命的主要因素有;工件材料、刀具材料、刀具的几何参数、切削用量。
- 17、斜楔、螺旋、凸轮等机械夹紧机构的夹紧原理是利用机械摩擦的自锁来夹紧工件。
- 18、一般机床夹具主要由定位元件、夹紧元件、对刀元件、夹具体等四个部分组成。根据需要夹具还可以含有其它组成部分,如分度装置、传动装置等。
- 19、切削运动就是在切削过程中刀具与工件的相对运动,这种运动有重叠的轨迹。切削运动一般是金属切削机床通过两种以上运动单元组合而成,其一是产生切削力的运动称为主运动,剩下的运动单元保证切削工作连续进行而称为进给运动。
- 20、切削用量三要素是指切削速度、进给量、背吃刀量。
- 21、对刀点既是程序的起点,也是程序的终点。为了提高零件的加工精度,对刀点应尽量选在零件的设计基准或工艺基准上。
- 22、在数控加工中,刀具刀位点相对于工件运动的轨迹称为加工路线。
- 23、在轮廓控制中,为了保证一定的精度和编程方便,通常需要有刀具长度和半径补偿功能。
- 24、在铣削零件的内外轮廓表面时,为防止在刀具切入、切出时产生刀痕,应沿轮廓切向方向切入、切出,而不应法向方向切入、切出。
- 25、粗加工时,应选择大的背吃刀量、进给量,合理的切削速度。
- 26、精加工时,应选择较小背吃刀量、进给量,较大的切削速度。
- 27、在实际的生产中,可采用以下措施防止、抑制积屑瘤的生成。控制切削速度、降低进给量、增大刀具前角、使用切削液、减小前刀面的粗糙度、降低工件材料的塑性。
- 28、用压板夹紧工件时,螺栓应尽量靠近工件;压板的数目一般不少于两块。
- 29、切削用量中对切削温度影响最大的是切削速度,其次是进给量,而切削深度影响最小。
- 30、为了降低切削温度,目前采用的主要方法是切削时冲注切削液。切削液的作用包括冷却作用、润滑作用、、防锈作用和清洗作用。
- 31、切削液的种类很多,一般有:乳化液、切削油、压缩空气。粗加工与精加工追求重点不一样,故切削液的选择重点也不同。简言之:粗加工一般以乳化液为主要切削液,主要起冷却作用。而精加工以切削油为重点对象,目的是追求良好的润滑效果。
- 32、在切削塑性金属材料时,常有一些从切屑和工件上带来的金属“冷焊”在前刀面上,靠近切削刃处形成一个硬度很高的楔块,该楔块即积屑瘤。
- 33、在切削过程中,工件上形成三个表面:①待加工表面;②加工表面;③已加工表面。
- 34、数控机床中的标准坐标系采用笛卡儿直角坐标系,并规定增大刀具与工件之间距离的方向为坐标正方向。
- 35、数控机床坐标系三坐标轴X、Y、Z及其正方向用右手定则判定,X、Y、Z各轴的回转运动及其正方向+A、+B、+C分别用右手螺旋法则判断。
- 36、每个脉冲信号使机床运动部件沿坐标轴产生一个最小位移叫脉冲当量。
- 37、与机床主轴重合或平行的刀具运动坐标轴为Z轴,远离工件的刀具运动方向为Z轴正方向。
- 38、X坐标轴一般是水平的,与工件安装面平行,且垂直Z坐标轴。
- 39、粗铣平面时,因加工表面质量不均,选择铣刀时直径要小一些。精铣时,铣刀直径要大,最好能包容加工面宽度。
- 40、在数控铣床上加工整圆时,为避免工件表面产生刀痕,刀具从起始点沿圆弧表面的切线方向进入,进行圆弧铣削加工;整圆加工完毕退刀时,顺着圆弧表面的切线方向退出。
- 41、数控机床使用的刀具必须有较高的强度和耐用度。
- 42、铣削平面轮廓曲线工件时,铣刀半径应小于工件轮廓的最小凹圆半径。
- 43、走刀路线是指加工过程中,刀具刀位点相对于工件的运动轨迹和方向。
- 44、机床参考点通常设置在机床各轴靠近正向极限的位置。
- 45、机床接通电源后的回零操作是使刀具或工作台退离到机床参考点。
- 46、编程时可将重复出现的程序编程子程序,使用时可以由主程序多次重复调用。
- 47、一个完整的数控加工程序由程序名、程序体和程序结束三部分组成
- 48、使用返回参考点指令G28时,应取消刀补,否则机床无法返回参考点。
- 49、在返回动作中,用G98指定刀具返回初始平面;用G99指定刀具返回R点平面。
- 50、加工中心孔加工刀具 有钻孔刀具、扩孔刀具、镗孔刀具、铰孔刀具等。
二、程序指令
1、FANUC车床指令
G代码


M代码
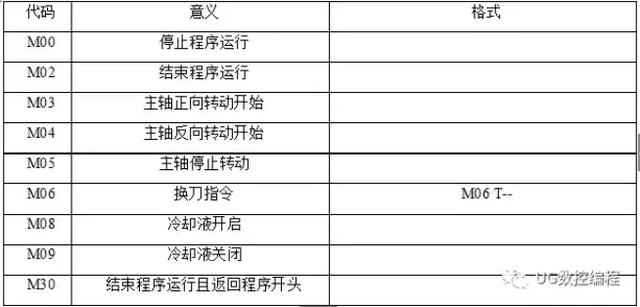
2、铣床和加工中心指令
数控指令包括准备功能指令G功能、辅助功能指令M功能、刀具功能指令T功能、主轴功能指令S功能、进给功能指令F功能。常用指令有:
G00 定位 G00 IP…
G01 直线插补 G01 IP…F…
G02 圆弧插补CW顺时针
G03 圆弧插补CCW反时针
G04 暂停
G15 极坐标指令取消
G16 极坐标指令
G17 选择XY平面
G18 选择ZX平面
G19 选择YZ平面
G20 英寸输入
G21 毫米输入
G27 返回参考点检测 G27 IP…
G28 返回参考点 G28 IP…
G29 从参考点返回 G29 IP…
G30 返回第2、3、4、参考点 G30 IP…
G40 07 取消刀尖R补偿 G40 XU--Z(W)--I-- K--
G41 刀尖R补偿左
G42 刀尖R补偿右
G43 正向刀具长度补偿 G43 Z… H…
G44 负向刀具长度补偿 G44 Z.. .H…
G49 刀具长度补偿取消
G50 比例缩放取消
G51 比例缩放有效 G51 X.. Y.. Z…P..
G52 局部坐标系设定 G52 IP…
G53 选择机床坐标系 G53 IP…
G54 选择工件坐标系1
G55 选择工件坐标系2
G56 选择工件坐标系3
G57 选择工件坐标系4
G58 选择工件坐标系5
G59 选择工件坐标系6
G68 坐标旋转/三维坐标转换 G68X…Y…R…
G69 坐标旋转取消/三维坐标转换取消
G73 排屑钻孔循环 G73 X… Y… Z…R… Q… F… K…
G74 左旋攻丝循环 G74 X… Y… Z…R… P… F… K…
G76 精镗循环 G76 X… Y… Z…R… Q…P… F… K…
G80 固定循环取消/外部操作功能取消
G81 钻孔循环、锪镗循环或外部操作功能 G81 X… Y… Z… R… F… K…
G82 钻孔循环或反镗循环 G82 X… Y… Z… R…P… F… K…
G83 排屑钻孔循环 G83 X… Y… Z… R…Q… F… K…
G84 攻丝循环 G84 X… Y… Z… R…P…Q… F… K…
G85 镗孔循环 G85 X… Y… Z… R… F… K…
G86 镗孔循环 G86 X… Y… Z… R… F… K…
G87 反镗循环 G87 X… Y… Z… R…Q… P….F… K…
G88 镗孔循环 G88 X… Y… Z… R…P….F… K…
G89 镗孔循环 G89 X… Y… Z… R…P….F… K…
G90 绝对值编程 G90 IP…
G91 增量值编程 G91 IP…
G92 设定工件坐标系或最大主轴速度钳制 G92 IP…
G94 每分进给 G94 F…
G95 每转进给 G95 F…
G96 恒表面速度控制 G96 S…
G97 恒表面速度控制取消 G97 S…
G98 固定循环返回到初始点
G99 固定循环返回到R点M00 程序停止
M02 程序结束
M03 主轴顺时针旋转
M04 主轴逆时针旋转
M05 主轴停止
M08 冷却液打开
M09 冷却液关闭
M30 程序结束并返回
M98 调用子程序 例如 :M98P0032007;调用O2007子程序3次
M99 子程序结束
三、编程举例
1、车床
实验题1:

毛坯:60*200
T0101:外圆车刀,Tool 2,刀片:三角形
N10T0101G99S600M03;换1号刀,加刀补,每转进给速度,主轴正转,转速600r/min
N20G00X80Z100;车刀快速移动至X80,Z100
N30Z4;车刀移动至Z4处
N40G73U10W2R4;粗车循环,X向切除的总余量10mm半径值,Z方向切除的总余量为2mm,粗车循环的次数为4
N50G73P60Q150U2W0.2F1;加工轮廓从60行开始,150行结束,X加工余量2,Z加工余量0.2,进给率1mm/转
N60G00X0;开始车轮廓,快速至X0
N70G01Z0;直线插补到Z0
N80G03X40Z-20R20;逆时针圆弧插补
N90G01X50;直线插补
N100W-20;直线插补
N110G02U0W-25R20;顺时针圆弧插补
N120G01W-10;直线插补
N130G03U0W-24R20;逆时针圆弧插补
N140G01W-10;直线插补
N150X65;直线插补,轮廓结束
N160G70P60Q150F1;精车循环
N170G00Z100;快速移动至Z100
N180M30;程序结束并返回程序起点
实验题2:

毛坯:100*200
T0101:外圆车刀,Tool 1刀片:三角形
T0202:割刀,刀片宽度3,Tool 6
T0303:螺纹刀,Tool 3
N10 T0101 G99 S1000 M03换1号刀,加刀补,每转进给速度,主轴正转,转速1000r/min
N20 G00 X102.0 Z100.0快速移动
N30Z2.0快速移动Z2,循环起点
N40G71U2.0R1.0粗加工循环,X每次切深2,退刀量1
N50 G71 P60 Q130 U1.0 W0.5 F0.1加工轮廓从60行开始,130行结束,X加工余量1mm,Z加工余量0.5mm,进给率0.1mm/转
N60G00X0精加工轮廓开始
N70 G01 Z0
N80 X30.0 C1.5
N90 Z-36.0
N100 G02 X58.0 W-30.0 R45.0
N110 G01 X80.0 R5.0
N120 W-20.0
N130X102.0轮廓结束
N140G70P60Q130F0.1精加工循环
N150 G00 X102.0 Z100.0
N160 T0202
N170G00X31.0Z-36.0车削退刀槽
N180 G01 U-4.0 F0.1
N190 U4.0
N200 G00 X102.0 Z100.0
N210 T0303换刀
N220G00X34.0Z6.01移至车螺纹的起点处
N230G92X29.2Z-35.0F3.0车螺纹深至X29.2,导程为3mm
N240 X28.6车螺纹深至X28.6
N250 X28.2车螺纹深至X28.2
N260 X28.04车螺纹深至X28.04
N270G00X34.0Z7.52移至第二次螺旋线的起点处
N280G92X29.2Z-35.0F3.0车螺纹深至X29.0,进给率取导程3
N290 X28.6
N300 X28.2
N310 X28.04
N320 G00 X102.0 Z100.0
N330 M30
实验题3:
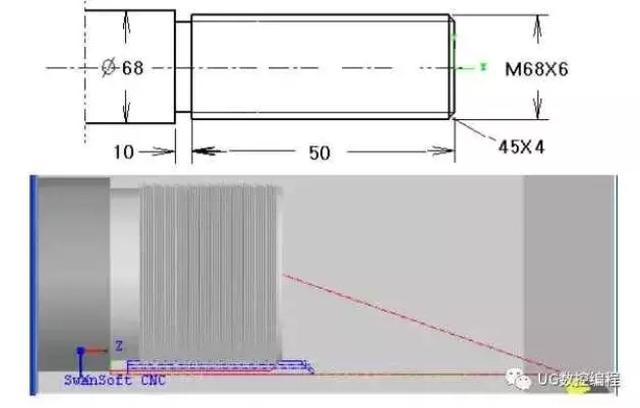
毛坯:68*200T0101:外圆车刀,Tool 1
T0202:割刀,宽度10,Tool 6
T0303:螺纹刀,Tool 3
N10T0101G99M03;
N20G00X70Z100;
N30X0Z0;车削外圆
N40G01X68C4F0.1;车C4倒角
N50Z-60;
N60G00X70;外圆结束
N70Z100;
N80T0202;换二号刀
N90G00X70Z-60;车削退刀槽
N100G01X60F0.1;
N110X70;
N120G00X70Z100;
N130T0303;换三号刀
N140G00X70Z10;循环起点
N150G76P030560Q100R0.1;复合螺纹切削循环,精加工次数3,螺纹Z向退尾长度为5,刀尖角度60,最小切深0.1,精加工余量为0.1
N160G76X60.56Z-55P3720Q1800F6;X60.56Z-55螺纹根部终点的坐标值,螺纹牙型高度为3.72mm,第一次切削深度为1.8mm,螺纹导程为6mm
N170G00X70Z100;
N180M30;
四、铣床编程
1、根据零件图,确定加工路线,选择合适刀具,进行基点计算,编写数控程序。
提示:
(1)刀具选择:φ20高速钢立铣刀、φ10高速钢立铣刀、φ12高速钢麻花钻。
(2)编写凹槽加工的子程序,然后旋转坐标系两次调用。G68/G69
(3)孔加工采用极坐标编程。G16/G15

2、其毛坯为四周已加工的铝锭,凸台外轮廓已粗铣,钻孔已完成。试编写凸台外轮廓精铣和铰孔的加工程序。
刀具:
①Ø16立铣刀 主轴:600r/min进给速度:100mm/min
②铰孔Ø8mm铰刀主轴:200r/min进给速度:24mm/min
刀具半径补偿:D01长度补偿H01
- 机械 机械制造 手工编程宏程序 CNC 数控机床数控车床 UG编程 机加工操机
文章来自网络
相关参考
这是一本学习的书,也是一本练习的册子,它把内容分为数控车床加工技能实训、数控铣床加工技能实训和数控车铣综合加工技能实训三个学习情境,每个学习情境又根据相应岗位职业能力需求,划分为数控机床操作基础模块、...
数控床身铣床精度检测实训报告(数控加工中心|关于机床精度的介绍)
...?我们今天就来聊一聊所谓的“精度”是什么?一、工件加工精度我们用车床加工出来的工件要测量一下加工后的几何尺寸(尺寸、形状和表面相互位置)与理想几何参数的符合程度,即工件加工精度。精度的高低用误差的大小...
数控铣床实训总结300字(数控铣床编程操作,四个实例助你快速入门)
数控铣床是在一般铣床的基础上发展起来的一种自动加工设备,两者的加工工艺基本相同,结构也有些相似。数控铣床有分为不带刀库和带刀库两大类。其中带刀库的数控铣床又称为加工中心。下面我们就来看看数控铣床编程实...
实例一:毛坯为70㎜×70㎜×18㎜板材,六面已粗加工过,要求数控铣出如图3-23所示的槽,工件资料为45钢。1.依据图样要求、毛坯及前道工序加工状况,确认工艺方案及加工道路1)以已加工过的底面为定位基准,用通用台虎钳夹...
时间如逝,一转眼操作数控车床已有十年,十年的摸爬滚打让我积累了数控车床的一些加工技巧与心得,与各位同仁交流。 因加工零件的更换频繁及工厂条件受限,十年来我们都是自己编程,自己对刀,自己调试及完成零件的...
数控加工与编程实训报告(CNC数控加工中心编程好学吗?多年数控编程工程师指点迷津)
编程对加工中心来说中重要性不言而喻,不少打算在加工中心行业发展或者没有接触过加工中心操作的朋友心中都有这样的疑虑?加工中心编程难不难?好学不好学?目前加工中心编程分为两种,手工编程和软件编程。 手工编...
在数控车床上可以车削米制、英寸制、模数和径节制四种标准螺纹,无论车削哪一种螺纹,车床主轴与刀具之间必须保持严格的运动关系:即主轴每转一转(即工件转一转),刀具应均匀地移动一个(工件的)导程的距离。以下...
数控机床没有程序是不能运动的。需要专业人员利用专业软件工具,根据产品的形状编制程序。UG编程就是指数控机床的程序编制。无锡品文UG编程培训机构,CNC数控加工编程培训UGCAM主要由5个模块组成,即交互工艺参数输入模块...
数控车床g98编程实例(FANUC数控铣床编程实例18-复杂凹十字台加工)
下图零件是在方形零件上方加工六棱凸台,再在凸台上加工二层凹槽。可以使用φ13立铣刀加工这些特征,另外的三个孔可以使用钻头和铰刀加工。工步1:铣削棱柱凸台走刀轨迹如下参考程序T3M6G90G54G40G43H3G00Z100M03S2500M08G00X70Y23G00Z...
数控车床动力头编程实例(数控铣床搞定曲轴、凸轮轴粗加工的奥秘、高招与绝对细节经验)
曲轴和凸轮轴是发动机重要运动部件,其传统工艺采用车床对主轴颈、连杆颈和凸轮进行粗加工。由于工件结构特殊和切削量大且不均匀,工件受力大而容易弯曲变形,所以加工精度难以保证,影响后续加工质量,同时存在设备...