数控车床主轴转速有30转跳动(车削出现“暗影”是怎么回事?)
Posted
篇首语:本文由小常识网(cha138.com)小编为大家整理,主要介绍了数控车床主轴转速有30转跳动(车削出现“暗影”是怎么回事?)相关的知识,希望对你有一定的参考价值。
数控车床主轴转速有30转跳动(车削出现“暗影”是怎么回事?)
大家好,我是数控狗ROVER
导读
一些对接触面有着较高电气性能要求的工件,如插针,表面高光车削后需要进行镀2μm铜底或铝底,然后镀镍底6~8μm,最后镀银至少5μm的电镀处理。电镀后,工件表面可看到宽度不规则明暗相间的条纹,客户称之为“暗影”现象。由于暗影对加工精度没有造成直接的影响,所以没有引起足够重视,现在为了提高高光车削的加工效果,满足客户工件电镀处理后的外观和电气性能需求,该问题亟待解决。那么,暗影究竟是什么原因造成的呢?本文从切削实验、切削力测试、主轴动态回转误差测试三个方面来分析。
暗影的描述

车削刀纹是车削后的加工表面上余留的加工痕迹组成的宏观形貌。在高光车削中,工件材质主要为紫铜和铝,常用刀尖圆角半径为0.4mm的金刚石刀片。车削后工件外圆表面粗糙度值均可达到Ra =0.8μm以内(见图1),裸眼观察外观光滑明亮。
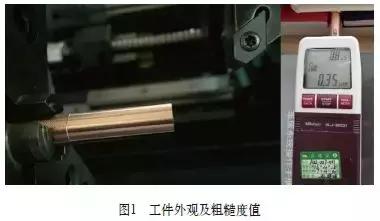
工件是否存在暗影现象无法通用直接观察或用粗糙度值衡量,用高倍放大镜观察外表面,能看到条状纹理, 类似粗车刀纹,无暗影工件明暗条纹宽度基本均匀一致(见图2),有暗影工件可观察到宽度不规则的明暗条纹,暗影处条纹较宽(见图3)。
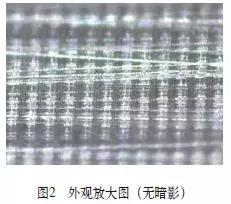
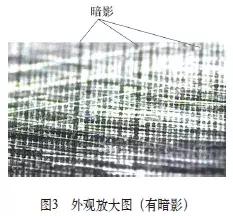
使用三维轮廓仪检测工件外表面可以发现暗影在微观上是由于车刀纹的凸峰和凹谷宽窄不均及波峰波谷值浮动较大,主要表现在凹谷比较宽而产生暗影现象(见图4、图5)。
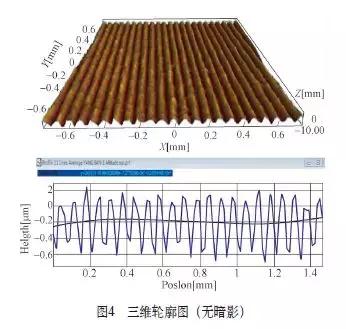
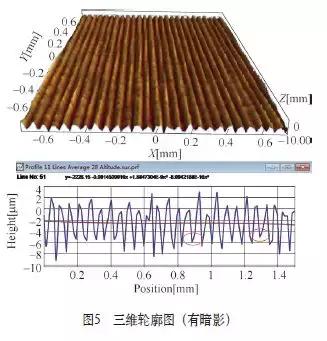
暗影产生原因分析

(1)切削实验
在同一工件的不同位置,使用相同的车削参数:转速3 500r/min,切削深度0.1mm,进给量0.06mm/r进行加工,大部分暗影都具有可重复性(见图6),说明暗影与X 轴、Z轴运动位置无关。
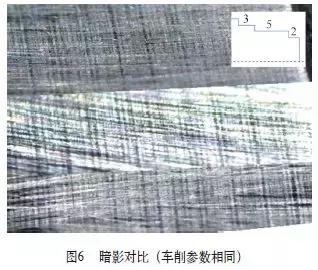
转速和切屑深度不变,只改变进给量进行车削,把暗影图片按进给量比例关系缩放,大部分暗影均可重合(见图7),说明暗影发生的位置与进给量关联性不大,可能与转速有关。
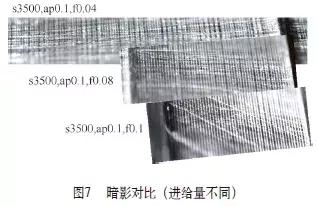
只改变切削深度, 其它车削参数不变,分别选取a p=0.06mm、0.1 mm、0.2 mm、0.3 mm进行车削, 暗影只有条纹颜色深浅的区别,大部分暗影均可重合,说明暗影发生与切屑深度无关。
(2)切削力测试 使用B&K
公司7700 Pulse数据采集分析系统对出现暗影机床的切削力进行分析诊断。按照车削参数:转速240~4 000r/min区间,间隔100r/m i n,切削深度0.1mm,进给量分别为0.05mm/r、0.1mm/r、0.15mm/r进行测试。
随着主轴转速的增加,在其他参数不变时,工件去除率逐渐增大,载荷也应该增大,但实测切削力除了进给量为0.05mm/r时小幅增大以外,其余都是在转速升高时略有减小(见图8),说明在高转速车削时存在让刀、跳动,导致切削量不足,从而切削力没有按照正常趋势发展。
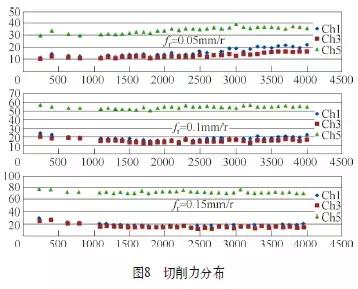
从每一个切削参数对应的切削力信号也能发现,切削信号在稳定切削力基础上有类似正弦信号叠加,说明存在动态车削力,并且从信号波形可发现叠加信号不单纯为一个(见图9)。切削力的频谱包含众多频率,主要是转速的倍频,说明引起信号波动的原因跟转速有关,可断定为主轴系统回转缺陷引起的。因此,暗影问题可认为是主轴系统回转故障。
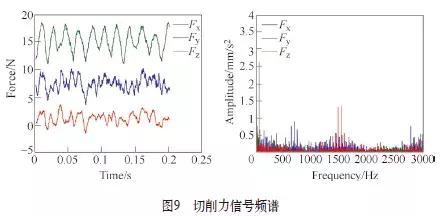
当转速为1 200r/min时选取不同进给量的切削力信号均表现的较为稳定,可见即便是加工质量相对良好的切削状态下,切削信号也包含与转速有关的频率成分(见图10),从而也可以验证进给量和切削深度两个参数不是产生暗影现象的原因。

转速1 700~2 300r/min区间振动几乎可以忽略不计,能检测到转频,但不明显,对切削力信号的干扰也不显著(见图11)。

图12和图13为较高转速区间的信号,可见随着转速提高,切削力频谱幅值显著增大,说明暗影不是因为高转速精加工时才会出现,而是与主轴系统本身有关,始终存在,只是在高转速切削时能量较大,更能激发出明显的暗影现象。


(3)主轴动态回转误差测试
由上述实验和分析可知,暗影现象的出现主要是由于主轴的动态回转缺陷造成的,因此设计如图14所示的实验对主轴动态回转误差进行测试,找出主轴动态回转误差与暗影的关系。由于车床主轴的动态特性需在高速旋转状态下进行测量,所以适宜采用高精度非接触式的测量仪器,故选用激光位移传感器进行测量。
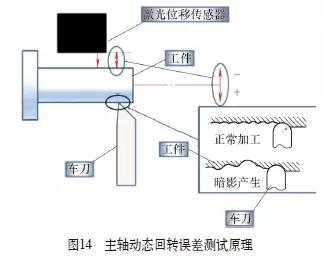
通过测量结果可发现位移波峰值变化频率与暗影出现频率较为一致,激光位移传感器的信号特征和暗影的产生及程度成正相关。当主轴动态回转误差值为1~2μm时,无暗影现象产生(见图15)。
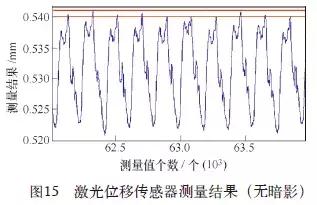
结语

综上所述, 主轴的动态回转误差是产生暗影现象的主要原因。暗影是由刀尖和工件在工件径向方向上的微位移产生的,因此, 暗影可定义为在车削过程中, 因刀具系统相对主轴系统的动态位移所造成的刀具偏离工件,从而在加工表面形成异常的加工纹理。当主轴动态回转误差值小于2μm时无暗影现象产生。
转载于金属加工
相关参考