数控机床发展趋势(机床行业深度报告:多因素共振,国产机床有望迎来新一轮上行周期)
Posted
篇首语:一身转战三千里,一剑曾百万师。本文由小常识网(cha138.com)小编为大家整理,主要介绍了数控机床发展趋势(机床行业深度报告:多因素共振,国产机床有望迎来新一轮上行周期)相关的知识,希望对你有一定的参考价值。
数控机床发展趋势(机床行业深度报告:多因素共振,国产机床有望迎来新一轮上行周期)
(报告出品方/作者:东北证券,刘军、韦松岭)
1. 工业母机:制造业转型升级要求机床向中高端发展
1.1. 机床行业简介
机床又被称为“工业母机”,是用于制造机器的机器。由于机器设备都是需要通过机 床对金属或其他材料的坯料进行加工制造出来的,因而机床又被称为“工业母机”, 是一个国家所有制造的精度、效率、品质的总起点。国家的工业制造能力就是依靠 机床这样的先导性产业、机器来保障和提升的,当前我国制造业要转型升级,机床 作为最基础的加工机器也必须要向中高端发展。 机床种类众多,狭义的机床即指金属切削机床。机床种类众多,按加工方式的差异 可划分为金属切削机床、金属成形机床、木工机床和其他机床。金属切削机床是我 国机床工具行业的重要组成部分,其数量最多、使用最广泛,因此狭义的机床即指 金属切削机床。
我国是全球第一大机床消费国和生产国,2020 年金属切削机床市场规模近千亿。自 建国以来,我国机床行业伴随着制造业的发展而快速崛起,2002 年和 2009 年我国 先后成为全球第一大机床消费国和第一大机床生产国,并保持至今。2020 年我国金 属加工机床消费额为 213.1 亿美元(按当年汇率折合人民币约 1470 亿元),其中金 属切削机床消费额 138.7 亿美元(折合人民币 957 亿元)占比 65.1%,金属成形机 床消费额 74.4 亿美元(折合人民币 513 亿元)占比 34.9%。
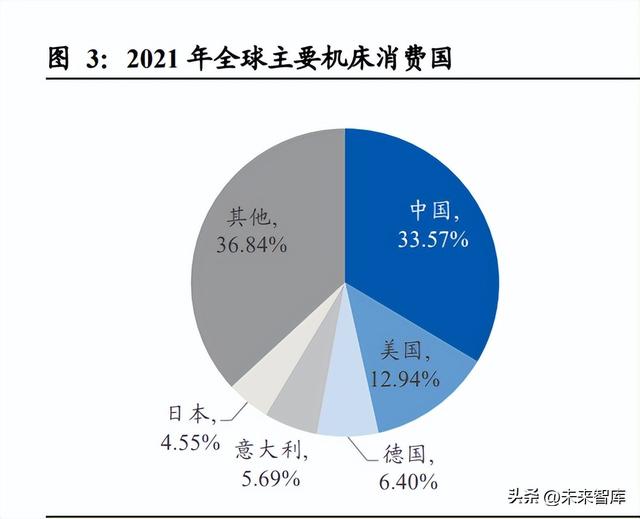
1.2. 以史为鉴:我国机床工业发展历程
由于机床“工业母机”属性,机床行业的发展除了受自身替换周期影响之外,更多 则是与我国经济发展的时代背景相关。机床的常规使用寿命为 6-10 年,主要与其使 用环境以及维护次数有关,同时通过大修也可适当延长机床的使用年限。通常在经 济发展环境较好的阶段,机床替换周期可能会由于设备的更新升级而缩短。因此在 我国机床行业 70 多年的发展历程中,机床行业的替换周期在较长时间维度来看表 现并不明显,阶段性的波动更多是与行业当时所处的经济发展背景相关。
机床的发展伴随着世界制造业的发展,由于我国在前三次工业革命中几乎没有作为 导致我国机床工业基础薄弱。世界制造业发展过程中的加工需求推动机床的诞生与 发展,原始形式的机床在 15 世纪就已出现。1774 年英国人威尔金森发明的一种炮 筒镗床被认为是世界上第一台真正意义上的机床,它解决了瓦特蒸汽机的气缸加工 问题,促进的蒸汽机的发展进而推动工业革命的发展。到 18 世纪,各种类型机床相 继出现并快速发展,为建立现代工业奠定了制造工具基础。由于我国在前三次的工 业革命中几乎没有任何作为,这也导致了我国机床工业基础先天薄弱,起步发展都 较晚。
具体来看,我国机床工业的发展主要历经以下几个阶段:
1.2.1. 1949-1958 年:起步奠基阶段
我国现代机床工业的基础源于国民经济恢复期和“一五”时期(1953-1957)。在 1949 年以前,我国并没有真正的机床工业,只在上海等地有少数工厂能够制造简易的皮 带机床。1952 年中央召开的全国第一次工具机会议才为我国机床工具行业的发展定 下基调,而同年美国已经制造出了世界上第一台数控机床。此后在苏联帮助下,我 国在三年国民经济恢复时期和“一五”期间,通过对部分机械厂的改扩建和新建, 初步建立起我国的机床行业。其中确定的 18 家骨干企业被称为“十八罗汉厂”,这 十八家国有机床厂在此后我国机床行业的发展中长期占据着主导地位。1958 年,我 国制造出第一台数控机床,仅比世界第一台数控机床晚 6 年。但需要注意的是,由 于我国产业基础较差,从实验室样机到工业大规模应用仍有极大距离。
1.2.2. 1958-1978 年:大规模建设阶段
20 世纪 50 年代末开展的三线建设中,我国机床工业得到大规模的规划建设。1958 年在中苏关系紧张的背景下,我国展开了大规模工业迁移—“三线建设”。同时,由 于国内机床工业无法满足高精度机床需求,我国也开始发展高精度精密机床。1960 年国家成立高精度精密机床规划领导小组,此后编制了 56 个高精机床品种发展规 划,制订了从样机试验到工艺攻关以至电机、轴承等配套件和原材料供应的成套措 施,并进口一批高精度机床及测试仪器装备了有关研究所及骨干厂。这也使中国的 精密机床制造上了一个台阶,形成了上海机床厂、昆明机床厂等高精度机床制造基 地。 此阶段,美国将机床产业重心放在对高精尖机床技术的研究上;德国的数控机床则 在六七十年代开始逐步领先世界;日本在 1978 年实现机床产量超过美国,并开始进 一步加强科研和高性能数控机床的发展;而我国的数控机床研制工作则受制于国内 外形势处于半封闭状态,技术更新发展有所停滞。
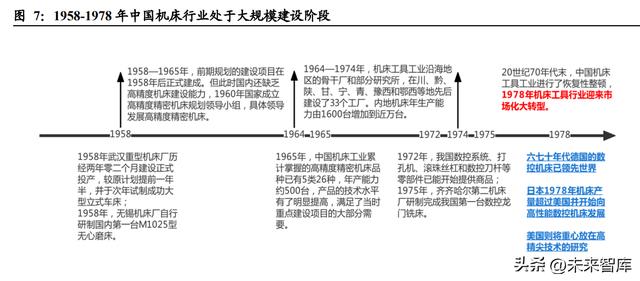
1.2.3. 1978-2000 年:市场化转型阶段
1978 年随着我国开始改革开放,中国机床工具工业也迎来了市场化大转型。1977- 1980 年我国对机床工具工业进行了恢复性整顿,以提高产品质量,为机床行业走向 市场化奠定基础。1980 年后,我国数控机床进入稳定发展期,通过引进数控系统和 主机研发技术,及与国外公司联合设计,我国制造出了自己的数控机床。1983 年一 机部提出的“扩大服务方向”的相关政策开始试行,到 20 世纪 90 年代中期,我国 机床工具行业产品全部敞开,从此走向市场化。期间,随着国家对机床工具企业技 术改造投入逐年增多,行业的产品开发和制造能力也得到了较大加强。 此阶段,西方发达国家的机床工业已经全面进入数控机床时代,而我国的机床行业 仅能生产技术相对简单的少数品类机床,数控技术发展仍处于起步阶段,中西差距 明显拉大。
1.2.4. 2001-2020 年:高速发展+转型升级新阶段
2001-2011 年高速增长:2001 年之后,随着中国加入 WTO 开始承接全球制造业转 移,中国制造业规模在全球比重也迅速上升。这个阶段中国机床行业以每年 20-40% 的速度高速增长,机床产值产量以及消费额快速提升,并分别于 2002 年和 2009 年 达到世界第一,并保持至今。2012 年我国机床消费额达到近年顶峰,全年机床消费 额 392 亿美元,占全球机床消费额比重达 46%。 2012-2020 年结构调整转型升级:2012 年以来,受国际市场变化以及我国加快经济 转型升级影响,国内机床行业也开始由低端过渡到中高端,行业进入产量下降、结 构升级阶段。此阶段行业低端机床需求量快速下降,行业产能过剩价格竞争激烈, 中高端机床则面临欧美、日韩机床较大的竞争压力。以“十八罗汉”为代表的国有 机床企业普遍都出现经营困难的情况,难以投入足够的资金进行创新研发,产品结 构得不到更新、转型升级效果并不理想。但同时,也有例如海天精工等一批新兴的 民营机床企业抓住机遇,成立之初便定位中高端机床,在行业激烈的市场竞争中脱 颖而出。到 2020 年,国内前十大机床上市公司中已基本都是民营企业。
2. 我国机床行业规模全球第一,但“大而不强”
中国机床行业规模全球第一,但面临“大而不强”的尴尬处境。改革开放以来,我 国机床行业历经多年发展取得了巨大进步,从生产量和消费量来看都是全球第一。 但我国机床行业“大而不强”,单一国产机床企业在国际市场上并不具备竞争力。目 前国内中低端机床已基本实现国产替代,但是高端机床仍依赖进口,主要是因为机 床产业环境、技术水平仍与先进国家存在较大差距。
2.1. 中低端机床已基本实现国产替代,但与进口产品仍存在差距
可靠性差是当前国产机床普遍存在的问题。随着国内应用客户加工需求越来越复杂 多样,对机床产品的要求越来也越高,其购买关注点主要集中于可靠性、性价比、 售后服务等。根据《世界制造技术与装备市场》开展的“数控机床可靠性”调查数 据显示,精度和稳定性差是客户认为国产机床最需要解决的问题(国产机床在使用 过程中精度和稳定性下降较快);另外国产机床故障率较高,其中漏水、漏油问题尤 为明显(国产机床平均无故障运行时间仅 2000-6000 小时,德日进口机床平均无故 障运行时间 20000-30000 小时);16.5%的调查对象认为国产机床耐用度较低(平均 使用寿命短)。
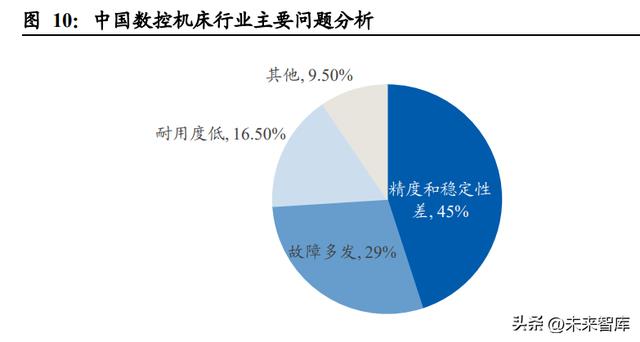
可靠性差的原因在于国产机床设计加工及装配质量差、关键零部件质量差。“数控 机床可靠性”调查数据显示,认为设计加工及装配质量差是导致国产机床可靠性差 的最大原因的占比 46%,认为是关键零部件质量差的占比 43%,另有 11%认为体现 在其他方面。同时,在对国内机床企业在提高机床可靠性时的主要障碍的分析中, 调查对象认为主要原因是企业不够重视的占比最多达 39%;认为政府及相关部门不 重视的占比为28%;认为成本高见效慢的占17.5%;认为不知道如何提高的占9.5%; 认为是其他因素的占比为 6%。
透过调查数据,设计加工及装配质量差、关键零部件质量差反映的是中国机床行业 人才短缺以及机床工业基础薄弱。相比于国外的先进技术水平来说,我国机床行业 在关键基础材料、基础零部件、先进基础工艺、产业技术基础方面仍存在较大的差 距,这是需要行业长期积累沉淀的,无法依靠短期大量的资本投入快速见效。 具体来看: (1)我国机床行业人才缺少制约了行业的发展。我国目前需要大量的三种层次数控 机床技术人才:①精通数控机床结构设计以及数控系统电气设计、能够进行数控机 床产品开发及技术创新的数控技术人才;②熟悉数控机床机械结构及数控系统软硬件知识,同时有扎实的专业理论知识并积累大量的实践经验的人才;③熟悉数控机 床的操作及加工工艺、懂得机床维护、能够进行手工或自动编程的操作人员和装配 人员。这三类人才的缺少影响了行业的发展,目前国内企业都在各尽其能培养人才, 但企业人才平台的建设更多停留在用工制度、薪酬制度等层面,聚焦解决的主要还 是企业个体层面的问题。
(2)行业基础技术能力较弱制约国产机床性能提高。由于行业技术人才短缺,我国 机床设计基础能力弱,围绕客户、行业、零件等的创新设计严重不足。目前我们虽 然在高速高精技术、复合加工技术、电主轴技术、各类功能部件等有所突破,但距 离商业化还有较长距离。这也制约了我国在卧式加工中心、各类五轴数控机床、高 度复合化数控机床、数控磨床、制齿设备等高端数控机床方面的发展。 (3)以数控系统为代表的基础及核心功能部件与国外差距较大。数控机床更多先进 功能必须通过数控系统功能体现出来,由于国产数控系统技术水平无法满足更高端 的使用需求,而国外数控系统对中国机床主机厂开放水平有限,数控系统已发展成 为制约我国机床发展的主要因素。此外,国产导轨、丝杆、主轴轴承等基础核心部 件主要差距体现在精度、稳定性和可靠性不高,得到客户认可还有较长过程。
2.2. 高档机床产业规模较小,综合技术水平亟待提高
与普通机床相比,高档数控机床具有高速、高精、多轴联动、智能、复合、网络通 信等特征。目前国内对机床档次划分还未有明确标准,我们综合行业相关上市公司 招股书披露的划分标准以及相关学术文献对数控机床技术水平划分,除了五轴联动 数控机床外,部分对性能指标要求很高的高精高速复合数控机床以及重型数控金属 切削机床也属于高档机床行列。
高档数控机床是实现我国产业升级的必需设备。以高档数控机床的代表性产品—五 轴联动数控机床为例,其主要用于加工复杂曲面,是生产飞机叶轮叶片、船用螺旋 桨、重型发电机转子、汽轮机转子、大型柴油机曲轴等高端装备部件的核心平台, 是我国实现向高端制造升级的必需设备。
国内高档数控机床产业规模还非常小,有待近一步突破。虽然近几年国产数控机床 在产品数量和品种上都取得了较大进步,同时产品技术与质量也得到较为明显的加 强。但整体来看,受限于我国机床工业基础薄弱,我国高档机床整体规模还非常小, 与我国全球第一大机床生产国和消费国的地位并不匹配。以五轴联动数控机床为例, 2016-2019 年我国金属切削机床年均消费额超千亿,而国产五轴加工中心产值仅分 别为 5.3/7.5/10.3/12.8 亿元,国产五轴机床产值仅占我国机床消费额的 1%左右。其 在我国金属切削机床产量中的占比则更小,2019 年仅占总产量的 0.21%。
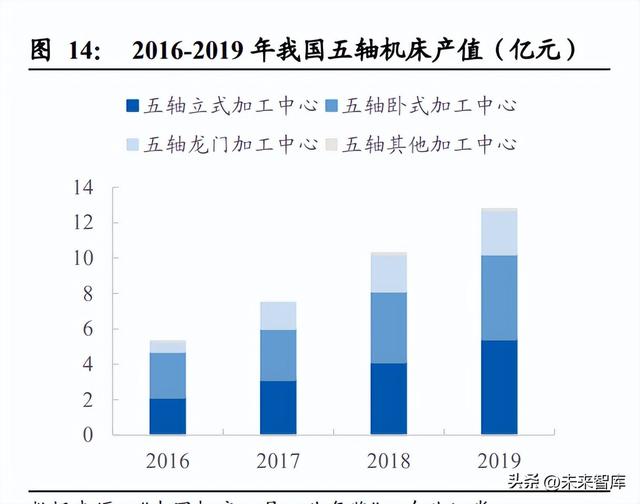
部分国产高档机床静态出厂精度与国外领先水平接近,但动态性能和精度保持还存 在差距。以五轴立式加工中心为例,科德数控、纽威数控、沈阳机床研制的一系列 五轴立式加工中心机床定位精度 5-8μm,重复定位精度 2.5-3μm 与国外第一梯队 厂商产品相当。但在动态性能和精度保持性上,国内机床和同类型的进口机床相比 还存在一定的差距。例如,国产机床精度往往下降较快;国产的数控系统、功能部 件等不能满足长期使用要求;各部件匹配度较差,部件质量及寿命问题较大;产品 环境适应性普遍不佳,受温度变化引起的精度波动较大。
国内机床企业普遍较小,行业集中度低、规模化能力弱进一步影响了国产高端机床 的研究开发。目前国内数控机床企业规模普遍较小,行业集中度相对较低,龙头企 业营收规模也仅在 30-50 亿之间,与国际一线机床厂商相比差距较大。规模化生产 研发能力弱也进一步影响了国内企业对高端机床的研发生产和制造装备的投入。
2.3. 未来我国主要金属切削机床需要达到的制造水平
目前受国外禁运等因素影响,我国还有大量高端机床需要攻克。我国高档数控机床 从建国初就长期面临严峻的“卡脖子”风险,西方国家的“巴统协定”及“瓦森纳 协定”等都对向中国出售的高端数控机床及相关的数控系统、功能部件实行不同程 度的出口管制,机床制造的关键核心技术也一直被美国、德国、日本等西方发达国 家垄断。虽然我国机床工具行业在这些年的高速发展过程中取得了巨大的进步,但 仍有大量高端机床需要攻克。 具体来看,我国五轴数控机床、大型/重型加工中心、卧式加工中心、高度复合化数 控机床、数控磨床、制齿设备等各类高端数控机床与国外同行相比还存在较大差距, 未来还需重点攻关。
3. 细分品类机床市场规模及变化趋势
金属切削机床可进一步分为车床、磨床、铣床、钻床、镗床、齿轮加工机床、螺纹 加工机床、刨床、拉床、电加工机床、切断机床和其他机床 12 类。加工中心是指具 有两种或两种以上加工方式(如车铣复合加工中心)、通过程序能从刀库自动换刀的 数控机床(按是否使用数控系统可分为数控机床和非数控机床)。 细分品类金属切削机床市场规模:目前市场对细分领域市场规模还未有明确的划分,2019 年我国金属切削机床消费额 141.6 亿美元(折合人民币 976.57 亿元),其中车 床作为金属切削机床最重要的一大分类,通常在金属切削机床中占比约为 20%-35%。 根据中国机床工具工业协会数据以及浙海德曼招股书(2019 年浙海德曼车床营收 3.45 亿元,在车床行业市占率 1.43%),预计国内车床行业市场规模在 200-250 亿元 左右(其中数控车床市场规模 100 亿元左右)。另外根据《2020 中国机床工具工业 年鉴》以及中国海关进出口数据,测算 2019 年磨床市场规模为 84.50 亿元,加工中 心市场规模 250 亿元左右(其中:立式加工中心 130 亿元左右,卧式加工中心 80 亿 元左右,龙门加工中心和其他加工中心 40 亿元左右)。
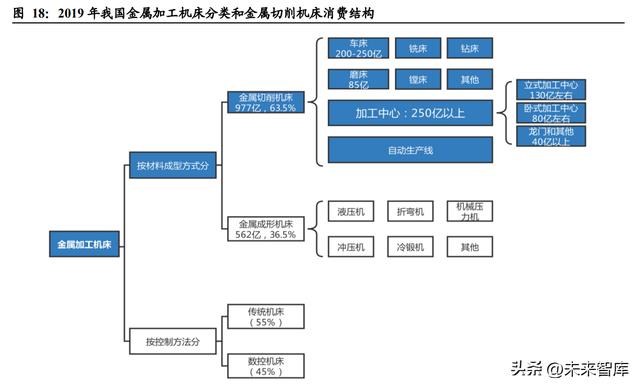
近几年以新能源汽车、光伏、风电为代表的新兴产业崛起,对高精、高速、自动 化、智能化、复合化特征的各类机床需求迅速增加,带动了我国机床市场需求结 构发生巨大变化,除了创造新的设备需求之外,也加快了制造业新旧产能的替 换,释放出与金属切削机床相关的新的需求空间。此外,疫情影响海外机床进口 也加速了我国机床国产替代的进程,国产机床在近几年迎来快速发展期。 整体来看,目前国产数控车床、立式加工中心等机床产品已经具备同国外同行 同台竞技的实力,进入主动竞争阶段,市场占有率相对较高。国产磨床、制齿 设备、卧式加工中心、龙门加工中心、各类五轴数控机床、高度复合化数控机 床等高端数控机床基本被国外品牌垄断,国产品牌占有率较低。
3.1. 数控车床:市场规模超 100 亿,目前已基本实现国产替代
车床是机械制造与修配工厂中使用最广的一类机床,在我国金属切削机床产值中占 比大约为 20-35%。车床是主要用车刀对旋转工件进行车削加工的机床,主要用于 加工轴、盘、套和其他具有回转表面的工件,在车床上还可以用钻头、铰刀、板牙 等进行相应加工。目前数控车床是我国车床行业的主流产品,国产数控车床已实现 主轴、刀塔、尾座等核心部件的自主生产,具备与国外同行竞争的实力,性价比优 势明显。 车床产销变化整体与机床行业发展趋势相似。由于车床是使用最为广泛的机床品类 之一,需求与下游制造业景气高度相关。2011-2019 年数控车床行业产量、产值整体下降,基本与我国机床行业发展趋势相似。但在市场需求总量下降的同时,也伴随 着需求结构升级的调整。在 2011-2014 年行业下行期间,车床数控化率从 2011 年的 43%提升至 2014 年的 56%(2019 年 65%左右),助力数控车床产销总体增长。此后, 随着我国经济增速放缓,机床产业结构调整力度不断加大,数控车床行业也不可避 免地处于下行周期中。
数控车床进口规模整体下降。近年数控车床进口数量整体下降,2019 年数控车床进 口数量只有 2011 年一半左右,但进口金额降幅远小于数量降幅,表明我国对进口高 端数控车床需求具备韧性,还未实现完全替代。
国内车床行业竞争相对激烈,高端数控车床进口替代持续推进。“十三五”末期与 “十二五”末期相比,国内数控车床单台均价整体小幅下降,平均价格在 16-17 万 左右的水平。在当前结构调整、产品升级大背景下,国产数控车床均价小幅下降也 体现了我国车床行业竞争仍然相对激烈。而进口数控车床在数量、金额均下降的背 景下,均价仍呈现增长趋势,表明我国数控车床在转型升级和结构调整上取得了不 错的进步,正在逐渐替代进口高端数控车床。
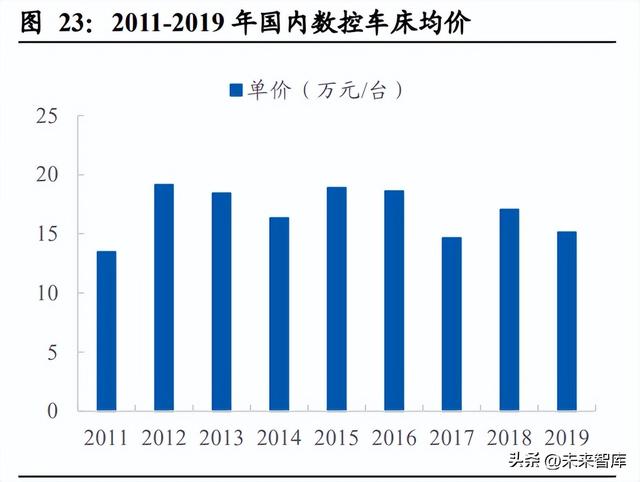
整体来看,2019 年国内数控车床市场规模 107 亿元,目前已基本实现国产替代。 2019 年国内车床市场规模 200-250 亿元,其中数控车床市场规模 107 亿元。近年由 于国内持续淘汰落后产能,中低端数控车床产销持续下降,国产数控车床产值已从 2011 年的 141 亿元快速下降至 2019 年的 63 亿元。同时,数控车床进口金额下降相 对较慢,这也导致从产值角度看近年我国数控车床进口依赖度逐渐提升。
3.2. 磨床:市场规模超 80 亿,主要依赖进口
磨床主要用于工件表面精密加工,在金属切削机床中产值占比约为 10%左右。磨 床是利用磨具和磨料(如砂轮、砂带、油石、研磨剂等)对工件表面进行磨削加 工的机床,通过磨削加工,可以使工件的形状及表面精度、光洁度达到预期要 求。根据用途和采用工艺不同,磨床可以分为平面磨床、外圆磨床、内圆磨床、 轧辊磨床、无心磨床、轴承磨床等,其中以平面磨床使用最为广泛,但轧辊磨床 和外圆磨床产值占比较高。
2011 年至今国内磨床产销下降幅度较大。2012 年受欧债危机、国内宏观经济增 速放缓等因素的影响,我国机床工具行业市场需求总量大幅减少。磨床行业由 于国产低端产能占比相对较大(2011 年国内磨床数控化率仅为 21.92%),供需 矛盾也相对突出,到 2019 年国内磨床产量已减少至 2011 年的 1/3 左右。
磨床进口结构也在调整升级。受市场需求大幅减少影响,2012 年起国内磨床进口数 量以及进口金额也持续减少。但进口金额的降幅小于进口数量的降幅,说明我国下 游行业对进口磨床产品结构也在调整升级。
国产磨床均价整体稳定,进口磨床均价缓慢提升。2011-2019 年国产磨床单台均价 整体稳定,大约为 15-16 万元左右。进口磨床单台均价超 100 万元,且呈缓慢提升 趋势,表明随着我国制造业转型升级,我国对进口磨床的需求也在向更高端发展。
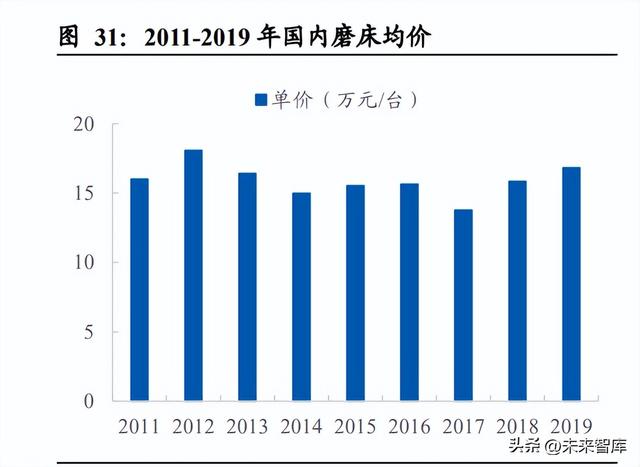
整体来看,2019 年国内磨床市场规模约为 85 亿元,磨床国产化进程缓慢,进口依 赖度维持高位。由于磨削加工对精度要求相对较高,国内下游客户较为依赖进口产 品,2011-2019 年国产磨床与进口磨床产销下降幅度基本一致,我国磨床国产化进程 缓慢,进口依赖度仍然维持在 80%左右的高水平。
细分磨床品类来看,轧辊磨床、无心磨床、轴承磨床国产化率相对较高,其他品类 磨床基本依赖进口。2019 年我国磨床需求结构中,外圆磨床、平面磨床、轴承磨床、 无心磨床、轧辊磨床、内圆磨床需求规模相对较大,分别为 17.6、13.0、6.9、5.7、 4.7、4.3 亿元,占我国磨床市场规模比重超 60%。其中仅轧辊磨床能够实现国产替 代,无心磨床和轴承磨床国产化率相对较高但也未超过 50%,其他品类磨床基本依 赖进口。
3.3. 立式加工中心:市场规模超 130 亿,目前已基本实现国产替代
立式加工中心定制化程度相对其他类型机床低,下游应用领域广泛,有大量客户属 于中小加工企业,对经济环境的变化更加敏感,因而在部分年份产销波动较大。立 式加工中心是指主轴与工作台垂直的加工中心,适用于加工板类、盘类、模具、小 型壳体等各类零部件,具备结构简单、占地面积小、功能组合多样、加工范围广、 批量加工效率高等优点,广泛应用于各个行业的零部件加工。 立式加工中心是相对较容易突破的中高端机床,目前已基本实现国产替代。立式加 工中心结构简单、定制化程度相对其他品类机床低,是相对容易突破的中高端产品。 在 2012-2016 年我国机床产业转型升级、行业产销整体下降过程中,立式加工中心 由于是率先实现国产替代的机床品类之一,产销逆势增长。2016 年后,随着下游制 造业机床需求进一步收缩,同时立式加工中心也已基本实现国产替代,国内立式加 工中心产销量也开始逐渐下滑。
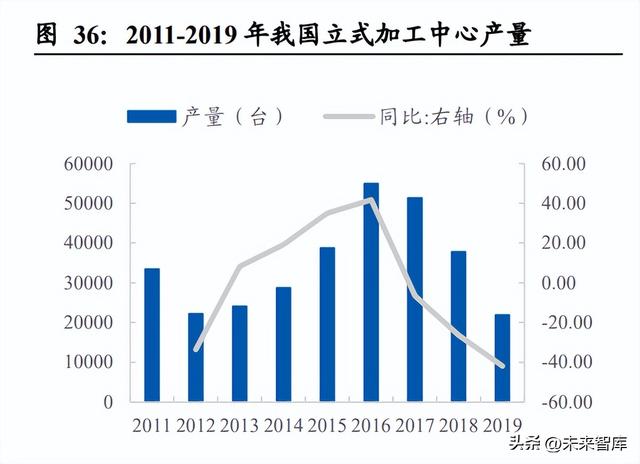
下游需求收缩以及国产替代不断推进,立式加工中心进口数量、金额持续下降。整 体来看,受我国机床供给结构升级以及下游需求收缩影响,使得以立式加工中心等为代表的中档机床进口量逐年减少。另外,由于进口机床一般存在半年以上的供货 周期,进口机床对市场低点有一定的滞后效应,因此立式加工中心进口数量以及金 额呈现较大幅度波动。
国产、进口产品均价方面,国产立式加工中心产品均价大约为 25-30 万元左右,近 年由于五轴立式加工中心等高端产品也逐渐取得突破,国产产品均价再次逐步提升。 进口立式加工中心产品均价大约为 50 万元左右,在进口数量持续下降背景下,2019 年进口产品均价有较大幅度提升,主要是因为目前国内采购的大多为较高端产品。
整体来看,2019 年我国立式加工中心市场规模大约为 134 亿元,对进口立加产品依 赖度持续下降,目前已基本实现国产替代。
3.4. 卧式加工中心:市场规模超 80 亿,主要依赖进口
卧式加工中心技术含量高,是数控机床产业发展水平的标志性产品之一。卧式加工 中心是指主轴与工作台平行的加工中心机床,适用于多工作面、形状复杂、精度要 求高的产品的批量生产,在汽车、航空航天、船舶和发电等行业被广泛应用。国产 卧式加工中心在精度、效率、智能化和可靠性等方面与国际先进产品仍有差距,目 前国内高档卧式加工中心主要依赖进口。 近年我国卧式加工中心产销规模整体稳定。2011-2019 年,受国际经济形势低迷以 及国内机床行业需求疲弱影响,我国卧式加工中心产量、产值整体下降,但近年较 为稳定。其中,2012 年国产卧加产量下降,产值同比增长约 29%,主要是下游客户 对国产高端卧式加工中心需求增加所致。
卧式加工中心进口规模持续下降,国产替代稳步推进。2011-2019 年,我国卧式加工 中心进口数量、金额整体下降,尤其是近年进口规模下降幅度大于国内,说明在机 床市场需求总量下降背景下,我国卧式加工中心国产替代也在稳步推进。
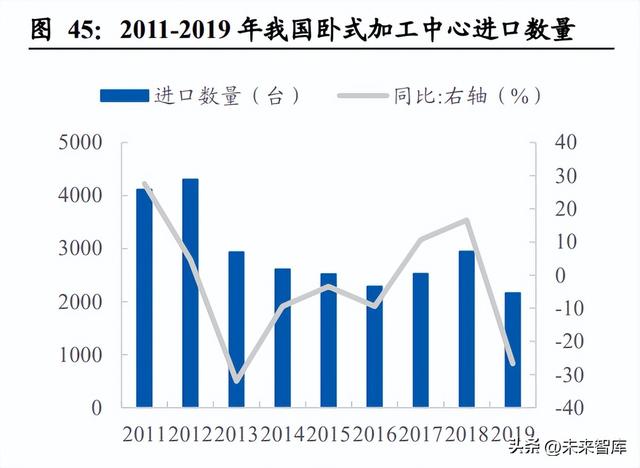
受下游产品需求结构变化影响,近年国产、进口卧式加工中心均价小幅下降。国内 卧式加工中心产品均价 150-200 万元左右,进口产品均价约 300-350 万元左右。近 年国产、进口卧式加工中心均价小幅下降,主要是以新能源汽车为代表的新兴产业 对卧式加工中心产品性能要求变化所致。
2019 年国内卧式加工中心需求规模约为 80 亿元,其中国产机床占比 23%。整体来 看,近年我国卧式加工中心国产替代稳步推进,但进度较为缓慢。
3.5. 龙门加工中心:市场规模 30-50 亿,高端产品主要依赖进口
龙门加工中心主要用于加工大型工件,国内产品具备一定竞争力。龙门加工中心主 轴与工作台垂直,整体是门式结构的大型加工中心,适用于加工大型工件和形状复 杂的工件,在航空航天、军工、高铁、模具、船舶、汽车等领域应用广泛。“十五” 以来,随着我国军工、航空航天、船舶、能源等产业对大型、重型机床需求日益增 加,国内企业纷纷通过引进技术、合作生产等方式研发生产各类型龙门加工中心, 国内龙门产品在结构性能、技术水平、产品质量等方面都取得较大进步,部分产品 具备一定市场竞争力。 近年市场对中低端龙门加工中心需求逐渐饱和,国产龙门加工中心产量、产值逐渐 下降。2012-2015 年,在国内机床行业转型升级初期,由于大型、重型机床市场竞争 相对较小,国内机床厂家纷纷转向研发生产相关机床产品,使得国内产品顺利在中 低端市场实现了进口替代。2015 年后,随着国内大型、重型机床产能饱和,在机床 市场需求持续萎缩背景下,国内龙门加工中心产量、产值也开始逐步下降。
中小型、个性化龙门产品需求日益增多,国内企业在新品开发以及产品性能等方面 的差距使得龙门进口数量持续增长。近年随着新能源、自动化等新兴行业的发展, 使得国内对中小型、个性化龙门加工中心的需求日益增多,这也对机床企业提出了 更高的设计加工和制造要求。国产龙门与国外产品在结构、技术方面差异不大,但 国内企业在新品开发、制造工艺、精度和稳定性等方面与国外厂家仍存在较大的差 距,也使得近年我国龙门加工中心进口数量持续增长。
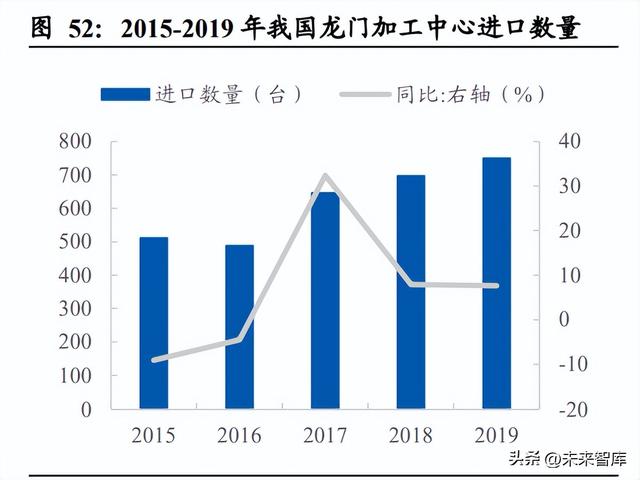
国产、进口产品均价方面,进口产品均价持续下降也一定程度上反映了国内龙门需 求结构的变化,国内产品均价持续增长则说明我国龙门加工中心正逐步向高端发展。
整体来看,2019 年国内龙门加工中心市场规模接近 40 亿,部分国产龙门加工中心 产品技术相对成熟,已具备一定市场竞争力,但定制化、高精高速等高端龙门加工 中心主要进口欧洲、日本等地区的局面还未改善。
4. 产业链:中高端机床数控系统及功能部件自主化率仍较低
机床行业上游主要供应铸件、钣焊件、精密件、功能部件、数控系统、电气元件等。 下游客户包括汽车行业、传统机械工业、模具行业、工程机械、电力设备、轨道交 通、船舶制造、航空航天、石油化工、电子信息技术工业以及其它加工工业。
铸件:机床底座、床身等基础大件使用铸件,铸件属于中间加工成品,产品价 格主要是在原材料生铁和废钢的基础上加上一定的加工费。对于高端铸件,配 方、材质、外观、性能等均会影响价格。
钣焊件:钣焊件是以冷加工工艺对钢板、铝板等金属板材进行加工,形成符合 精度要求、功能要求的形状和尺寸,用于焊接机身起内外防护作用。同时组成 功能部件的刀库支架、直角头支架以及出水系统、排屑系统等也使用钣焊件。
精密件和功能部件:精密件主要包括主轴单元和丝杠、导轨、轴承等传动部件 等。功能部件主要包括数控回转台、刀库、机械手、齿轮箱、铣头、刀架等。 目前国产中高端机床精密件和功能部件主要来自日本、德国等地区,部分采购 于国内企业或自制。
数控系统:数控系统用于数控机床,也可用于原有机床的系统升级和改造,主 要包括控制装置、驱动装置和检测装置。目前我国大型机床生产商主要从日本、 德国等技术成熟的国家采购数控系统。中高档数控机床常用数控系统品牌包括 日本发那科、德国西门子、日本三菱、德国海德汉等。
从成本结构来看:在机床生产过程中,原材料成本占比最高,为 73.9%,其次是人 工、折旧与其他制造费用,分别占比 11.9%、7.9%和 6.4%。而在原材料成本的进一 步拆分中,由铸件加工而成的底座床身等结构件占比最大,通常在 30%-40%左右,价 格受钢材影响较大;其次是数控系统占比 22%;由丝杠导轨等传动机械以及辅助动 力系统等组成的传动系统占比 20%;高速主轴和电机等组成的驱动系统占比 13%;刀 库、刀塔等占比 5%;光栅尺占比 2%。通常具备规模优势的企业,在进行原材料采购 时能够享受到和采购规模对应的折扣优惠,能有效增加公司毛利率。
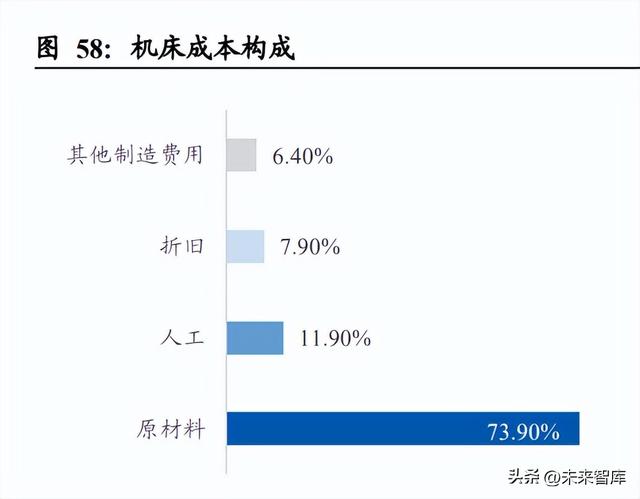
从上游市场来看,对机床行业影响较大的主要有钢铁、数控系统和功能部件三大类。 目前国内数控机床企业普遍存在数控系统以及核心部件外购情形,原因是国内工业 技术基础较差,同时国产机床企业都比较小,难以发挥规模效益优势进行自主研发, 大量部件外购也是行业主要的生产模式。
(1)钢材铸件整体对外依存度较低
目前我国钢材行业产能充足,铸件产量稳居世界第一。自 2000 年以来,我国一直保 持世界第一铸件生产大国的地位,整体来看行业产能充足。大部分国内机床公司选择将铸件及毛坯件的粗加工、半精加工等非核心工序进行外协加工,这是对机床行 业有利的一个因素。但需要注意的是,我国铸件产能结构中包含大量的小型铸造厂, 拖累了我国铸造行业的整体产能质量。国内铸造行业整体呈现大而不强的局面,行 业集中度较低,尚处于充分竞争阶段。从单位企业平均铸件产量来看,我国要低于 发达国家甚至不如印度等其他新兴经济体,应用于中高端机床部件的多种特钢材料 仍需进口,同时在熔炼、回火、退火、淬火等基础材料热处理技术也还有待提升。
(2)中高端数控系统依赖进口
数控系统行业专业化分工,市场集中度高,我国中高端数控系统市场被国外企业占 据。在当前机床行业的产业链分工中,数控系统呈现专业化以及高度集中化的特点, 全球市场主要由日本发那科、三菱以及德国西门子、海德汉等少数企业垄断。目前 国内 70%以上的数控机床的数控系统使用进口产品,其中发那科、三菱、西门子三 大龙头 2020 年合计市场份额就达 65%,广州数控凭借中低端车床数控系统跻身国 内市场前列。此外,国内机床终端客户在产品配套的数控系统的选择上也有偏好, 中高端机床终端用户更愿意购买使用发那科等国外数控系统的机床产品。
(3)中高端机床功能部件进口依赖度高
国际第一梯队机床企业为保证机床质量会自产部分核心功能部件,我国则主要依赖 外采。由于机床核心零部件的质量会直接影响到机床的性能水平(例如铸件性能和 质量直接影响设备的运行水平和可靠性;丝杠导轨和伺服电机会直接影响到机床运 动精度;数控系统以及传感器等则直接影响到机床制造的精度、效率、可靠度以及 维护成本),同时外部采购的功能部件主要为标准产品,与机床整机可能存在匹配度 较差从而影响机床性能的问题,因此国际第一梯队机床通常选择自制部分零部件。 一般主要集中在铸件、钣金件等基础大件,以及传动系统、功能部件、电气元件等 一类或几类,但因涉及门类众多,无法做到全面覆盖,各自侧重不同。如德马吉森 精机注重铸件、钣焊件、传动系统部件的自主开发生产,国内机床企业大部分核心 部件则以进口为主,这也是制约我国数控机床行业整体技术水平快速提升的原因之 一。
工业基础薄弱产业链短板突出,中高端机床关键配套件发展滞后仍然依赖进口。功 能部件产业发展的滞后已成为数控机床发展中公认的瓶颈,目前国产可替代的核心 部件已经逐渐发展成熟,部分主机厂已逐步使用国产核心部件进行境外品牌替代。 但由于技术水平仍存在一定差距,若全部采用国产核心部件,对于主机厂而言,其 高端数控机床的精度水平、精度的稳定性、精度的保持性都会受到影响,进而影响 高端数控机床的销售情况,因此目前我国的中高端机床关键配套部件主要依赖进口。 2019 年我国功能部件产值 13.7 亿元,从细分结构上看,产值占比最高的是数控机床 功能部件生产产值 7.7 亿元,其中滚珠丝杠副产值 2.7 亿元、滚动导轨副和直线导 轨副产值 1.8 亿元、电主轴和机械主轴产值 1 亿元。而进口方面,2019 年我国功能 部件进口总额达 15.3 亿美元,其中,机床零部件进口额 9.0 亿美元(折合人民币 62.41 亿元),进口规模是国产配套零部件产值的 8.1 倍。
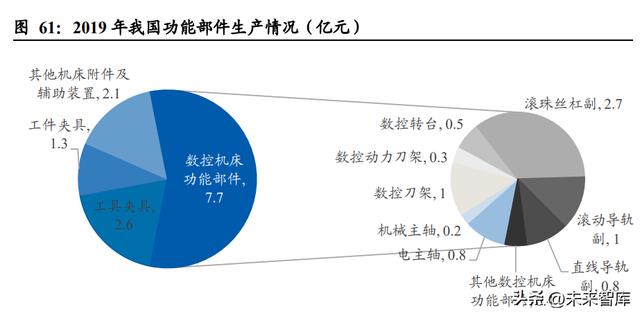
5. 多因素驱动,国产机床有望迎来新一轮上行周期
自2020年以来,中央和地方各级政府密集出台了多项刺激经济发展的政策措施, 我国机床工具行业 2020 年下半年开始走出下行通道,复苏趋势明显。同时,受 全球疫情影响,海外机床企业供应链受阻,导致国内企业购买海外设备交期延 长、售后服务也难以实现,也给了国内机床进入下游企业的机会。在存量替换周 期以及下游产业升级数控化率提升的背景下,国产机床行业近十年的下行走势 有望扭转,迎来新一轮上行周期。
5.1. 需求端
我国是全球第一制造业大国,出口景气叠加内需消费复苏,带动制造业投资高速增 长。2004-2020 年我国制造业产值年均复合增速 12.05%,占全球制造业比重也从 7.53% 上升到 28.37%,已连续多年成为全球第一制造业大国。出口方面,2021 年以来,受 到海外疫情和全球经济复苏拉动,国内中间品制造业、专用和通用设备等出口强劲, 成为投资增长的最重要动力。内需方面,2020 年以来国内居民收入呈现恢复式增长, 带动下游消费制造业投资增长,2022 年 1~9 月,全国固定资产投资同比增长 10.10%。 预计后续随着国内疫情防控政策放松,以及相关经济刺激政策生效,下游客户对机 床等专用和通用设备的需求也将增加。
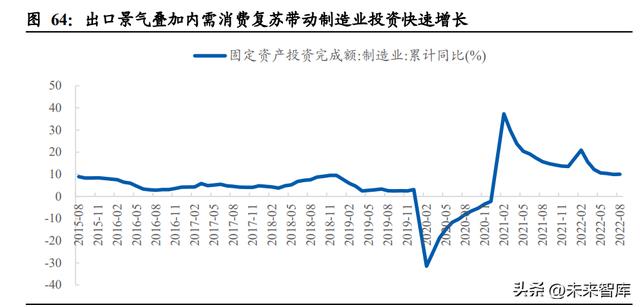
目前正值机床 8-10 年更新替换周期,下游机床更新替换需求有望增加。2000-2011 年国内金属切削机床产量快速增长,并在 2011 年达到历史最高的 88.68 万台。通常 机床的设计使用寿命约为 8-10 年,经历多年高强度使用后,加工精度和稳定性均会 出现下降,同时许多传统机床也无法适应当前高速、高精、高效的加工需求。虽然 机床的更新替换受多种因素影响,但若按传统的 8-10 年使用寿命计算,目前正值新 一轮机床更新替换需求释放的高峰,尤其是目前我国很多传统机床处于超期服役状 态,随着行业景气度提升,更新替换需求有望得到进一步释放。
制造业升级促进机床数控化率提升,加快存量机床更新迭代。目前我国机床数控化 率仅为 45%左右,远低于日本、欧美地区制造业发达国家水平。同时,随着自动化、 新能源汽车、航空航天、模具等下游行业的发展,对于机床的性能要求也产生了一 些变化,也加快了存量机床的迭代升级。例如,传统燃油车对于机床的精度性能要 求相对较高,但新能源车则对机床智能化、高效率、降成本等方面有较高要求。
全球疫情影响进口机床交付及售后服务,国产机床面临较好发展机遇,我国金属切 削机床贸易逆差有望缩小。2021 年我国金属切削机床进口额 62.4 亿美元,同比增 长 27.35%,出口额 36.5 亿美元,同比增长 32.73%,从贸易差额上看,金属切削机 床贸易逆差较大为 25.9 亿美元,而金属成形机床为顺差 4.5 亿美元。受全球疫情影 响,进口机床在订单交付、技术及售后人员的流动与服务方面受阻,使得国产机床 获得了国内下游客户更多的试用机会,正面临较好的进口替代机遇,未来我国金属 切削机床贸易逆差有望进一步缩小。
国产机床在发展中国家性价比优势突出,国产机床出海潜力巨大。2021 年我国金属 切削机床出口 36.5 亿美元,同比增长 32.7%。虽然目前国产机床畅销日本、欧美等 机床产业发达的地区难度相对较大,但在部分发展中国家和地区性价比优势明显。 近年国产机床在越南、印度、土耳其、墨西哥等地的销售增长迅速(以中低端机床 为主,出口均价仅为 0.03 万美元左右),随着国内机床企业纷纷加大海外渠道布局 力度,国产机床出海潜力巨大。
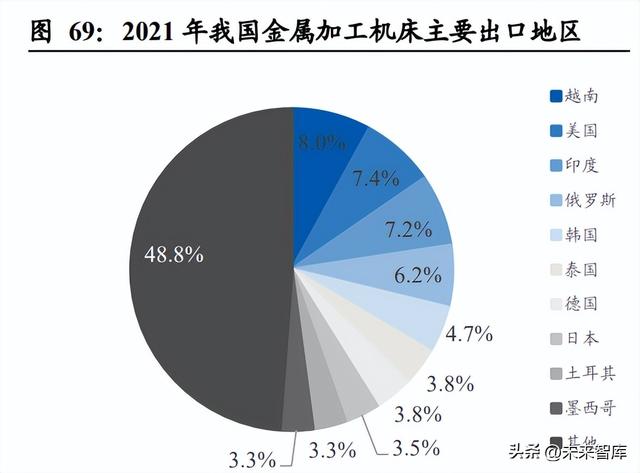
5.2. 供给端
机床国产替代持续推进,中低端机床基本实现自给,高端机床还有广阔替代空间。 2010-2021 年我国机床行业进口金额以及进口依赖度整体下降,2021 年国内机床消 费额 277.6 亿美元、进口金额 74.6 亿美元,进口依赖度 26.87%,较 2010 年的 33.08% 下降明显。但需要注意的是,目前实现国产替代的主要是中低端机床产品,高端机 床依然主要依赖进口,国产替代进度缓慢。目前我国高端机床国产化率仅不到10%, 整体替代空间广阔。
产业结构调整升级过程中“国退民进”,民营机床接力国企成为国产替代生力军。在 近十年的机床产业结构调整升级过程中,国有机床企业因产值连年递减,经营情况 较差。外资企业销售规模则在国产替代大背景下整体下滑。国内民营机床企业由于 没有历史包袱,设立之初期便定位中高端产品,在近十年行业下行周期中营收逆势 增长,市场份额不断扩大,成为实现我国机床国产替代的生力军。近年也是民营机 床企业上市高峰期,通过上市募资投建新产能以及加大产品研发投入,也进一步巩 固了行业地位。
机床作为“工业母机”受国家高度关注,出台相关政策支撑行业快速发展。机床作 为“工业母机”,是智能制造装备的重要基础,其发展水平高低是我国从制造大国到 制造强国转变的关键指标。当前,国家及各地方政府对智能装备、数控机床等产业 都表现出高度的重视,制定并实施了一系列促进行业发展的法规及产业政策。
数控系统、功能部件等已初具规模,为行业发展提供坚实保障。虽然目前我国中高 档数控系统以及主轴、丝杠、导轨等零部件主要依赖进口,但国内机床工具产业在 中低端机床零部件的国产化方面已经取得较大成效,对未来我国机床工业的发展形 成强有力支撑。根据《中国制造 2025》重点领域技术路线图,2020 年国产标准型、 智能型数控系统国内市占率已分别达到 60%、10%,主轴、丝杠、导轨等功能部件 国内市占率 50%左右。预计到 2025 年,标准型、智能型数控系统国内市占率将分 别达到 80%、30%。主轴、丝杠、导轨等中高档功能部件国内市场占有率达到 80%。
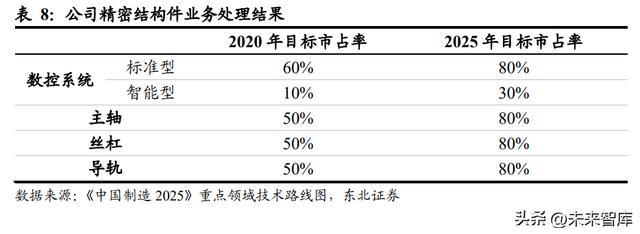
6. 整机重点公司分析
6.1. 海天精工
国内民营机床龙头,龙门加工中心产品得到下游客户广泛认可。海天精工成立于 2002 年,2016 年挂牌上市,主要产品包含龙门加工中心、立式加工中心、卧式加工 中心、数控车床等,广泛应用于航空航天、汽车、模具制造、工程机械、通用制造 等行业。公司成立以来一直致力于高端数控机床的研发、生产和销售,是目前国内 通用机床销售收入最高的民营企业,龙门加工中心产品得到下游客户高度认可。
大型机床稳定增长,中小机型快速放量。公司中大型龙门加工中心行业领先,市场 占有率连续多年保持国内细分品类第一。近年公司大型机床产销稳定增长,保持行 业领先地位,同时产品多元化战略也开始见效,立式加工中心等中小机型机床快速 上量,收入占比迅速提高。
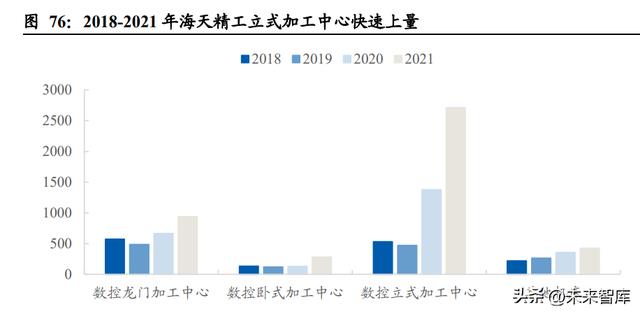
航空航天、军工领域销售占比达 20%,主要下游行业景气延续。公司以龙门加工中 心起家,产品技术水平、开发设计和应用经验、制造经验行业领先,目前已具备较 好的品牌效应。中大型龙门加工中心主要用于加工大型零部件,下游包括航空航天、 风电、船舶军工、工程机械等。2020 年公司在航空航天、军工领域销售占比高达 20%, 销售规模国内领先。此外,公司在近年景气度相对较高的新能源车和模具行业销售 占比也分别达到 10%。在目前机床国产替代持续推进背景下,公司下游主要行业景 气度相对其他传统制造业较高,随着公司规模扩张竞争力不断增强,公司长期成长 可期。
综合竞争能力突出,各项财务指标表现优异。近年随着产销规模扩大、产能利用率 迅速提升,公司营收利润迅速增长。2016-2021 年公司营收 CAGR 为 22.05%,归母 净利润 CAGR 达 42.56%。盈利能力方面,公司费用控制良好,近年净利率持续提 高,ROE、ROA 水平处于行业较高水平,同时在现金流等方面表现优秀,综合竞争 优势明显。
6.2. 纽威数控
国内领先的数控机床领先企业,产品系列齐全致力于提供全套切削技术解决方案。 纽威数控前身苏州纽威机械,是从事工业阀门业务的纽威股份的兄弟公司,2006 年纽威机床研究院成立标志公司开始进入通用机床制造领域。公司自设立以来一直致 力于中高档数控机床的生产销售以及提供全套切削技术解决方案,产品系列齐全, 拥有 7 大系列 200 多种型号机床产品,广泛应用于汽车、工程机械、模具、阀门、 自动化装备、航空、通用设备等行业,目前已在 40 多个国家建立销售网络,产品出 口近 60 多个国家和地区。
下游应用领域广泛,通用制造和汽车行业销售占比最高。2020 年公司下游客户结构 中,通用设备行业占比 38.54%,产品主要用于铸件、钣金件、齿轮、轴承、紧固件 等各种通用基础零部件的加工;汽车行业占比 21.67%,工程机械行业占比 7.74%; 模具行业占比 4.11%。
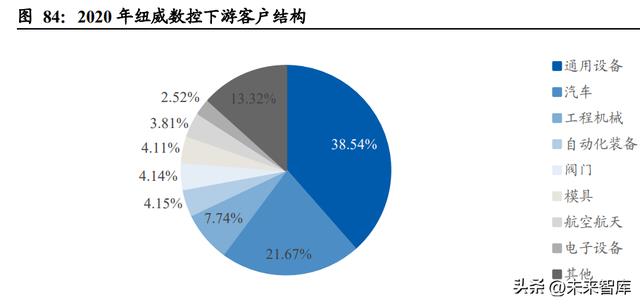
产品以中大型机床为主,大型加工中心和卧式数控机床贡献近 70%收入。按照产品 规格、行程及主轴方向,公司产品可分为大型加工中心(主要为龙门加工中心和大 型镗铣床)、卧式数控机床(主要为卧式加工中心和卧式车床)和立式数控机床(主 要为立式加工中心和立式车床),2021 年大型加工中心和卧式数控机床销售占比达 68.39%,立式数控机床由于立式加工中心市场需求下降收入占比有所萎缩。
部分机床技术实力已达到国际先进水平,竞争优势明显。公司在我国数控金属切削 机床细分行业排名前列,部分高端机床产品技术已达到国际先进水平,例如高效型 卧式加工中心具备高性能、高效率的特点,主要应用于发动机缸体、缸盖、减速箱 壳体、自动生产线加工等行业。产品已成功进入国内大型内燃机龙头企业,并实现 发动机缸体缸盖的量产,打破了该领域一直被国外厂家垄断的局面。
营收利润高速增长,盈利能力不断提高。近年公司营收利润高速增长,营业收入从 2017 年的 6.36 亿元增长至 17.13 亿元,CAGR 为 17.13%;归母净利润从 2017 年的 0.21 亿元增长至 2021 年的 1.69 亿元,CAGR 高达 68.43%。由于产销规模不断扩大, 产能利用率持续提高,公司规模效应显现,各项费用率持续下降,盈利能力不断提 高。
6.3. 国盛智科
结构件起家,纵向一体化发展的智能制造解决方案提供商。国盛智科成立于 1999 年, 早期主要是为赫斯基、德马吉森精机等国内外数控机床厂商进行精密钣焊件和铸件等装备部件的定制化研发生产,此后逐渐过渡到机床本体的制造。公司在进行装备 部件以及机床 OEM 生产的同时,也为后续向数控机床业务转型打下坚实基础。目 前,公司已形成铸件和精密钣焊件、数控机床、智能自动化生产线为主的三大系列 产品。
数控机床相关产品已成为公司核心业务,高档数控机床收入占比持续提升。目前公 司已形成数控机床及自动化生产线为主、装备部件为辅的业务结构,数控机床相关 产品收入占比超 80%。公司数控机床产品可拆分为高档数控机床(主要包括五轴联 动数控加工中心、五面体龙门、卧式镗铣加工中心、大型龙门、精密卧加、车铣复 合加工中心等)和中档数控机床(主要包括立加、小型龙门、数控车床等),近年公 司致力于高档数控机床的研发、生产和销售,高档机床销售占比持续提升,2021 年 公司高档机床收入占比已达 39.16%。
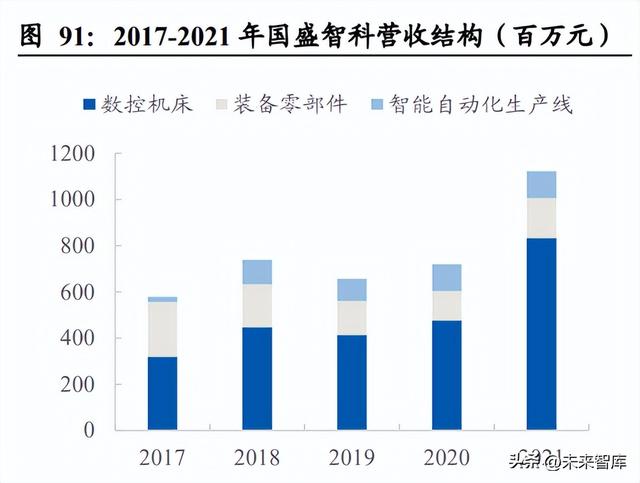
公司数控机床下游应用广泛,模具行业产品、渠道优势明显。公司数控机床下游应 用领域为机械设备、模具、汽车、工业阀门、石油化工等行业,2019 年公司在模具 领域收入占比为 24.35%,较同业可比公司较高。主要是因为 2011-2015 年公司在进 行机床 OEM 生产销售时台州区域客户为重要服务群体,随着公司业务由机床本体 向数控机床发展,公司也逐渐将台州区域客户发展为渠道经销商。台州作为中国“模 具之都”,模具产业发达,客户需求也进一步反馈至公司产品研发生产与渠道建设, 模具行业也逐渐发展成公司优势领域。
营收规模不断扩大,盈利能力企稳回升。2017-2021 年,公司营业收入 CAGR 为 18.02%,归母净利润 CAGR 为 21.10%。利润率方面,2017-2021 年毛利率略有下降, 主要是公司将业务重心转移至数控机床业务,毛利率较高的装备零部件业务占比下 降所致(2017 年装备零部件毛利率 40.01%,收入占比 40.43%);净利率企稳回升, 主要是随着数控机床产销规模不断扩大,规模效应下公司费用率整体下降。
6.4. 创世纪
原主营 3C 精密结构件业务,目前是 3C 及立式加工中心细分领域龙头。公司前身 东莞劲胜塑胶制品有限公司,2010年5月挂牌上市,成为东莞首家创业板上市公司。2013 年 8 月正式投产消费电子产品金属精密结构件项目,全面进军金属结构件领 域。2015 年 11 月公司收购深圳创世纪 100%股权,进入高端数控机床行业。2017 年 公司 3C 领域数控机床销量已位居全国前列,2018 年由于国内宏观经济下行,人力 成本和融资难度上升,以及大客户三星转移消费电子业务到东南亚,公司经历 28.66 亿元巨亏,之后开始整合剥离消费电子产品金属结构件业务。目前公司精密结构件 业务整合剥离基本完成,高端智能装备业务成为公司核心业务。
历史问题出清,公司开启发展新纪元。2020 年底公司消费电子产品精密结构件业务 就已基本剥离完毕:①资产端:剩余固定资产 1.58 亿,应收账款 1.38 亿,长期股权 投资 0.19 亿元以及存货 0.13 亿元。剩余资产基本都属于有盈利能力,或已足额计 提减值、或预计可变现净值高于成本的资产,资产占比较小且未来将持续减少,对 公司整体将不构成显著影响;②人员端:截至 2020 年底公司精密结构件业务相关的 员工人数为 44 人(2018 年底为 9503 人),占公司总人数的比例约为 1.84%,剩余 人员公司也将在合法合规基础上继续推进转移与安置;③业务层面:2021 年后公司 不再专门从事精密结构件业务的经营。
公司机床按应用领域可分为 3C 机床和通用机床两个方向。在 3c 领域,公司产品销 量和市场份额排名行业前列,2021 年 3C 钻攻机出货量超 10000 台,累计出货量已 超 80000 台,行业地位领先,目前已进入替代发那科、兄弟公司等国际一线巨头的 阶段。公司通用机床业务立足于中高端数控机床,2021 年出货约 15000 万台(主要 以立式加工中心为主,2021 年出货超 10000 台),规模优势明显。近年公司也在持 续扩张数控机床品类,龙门、卧加、数控车床、精雕机等产品也在快速上量。
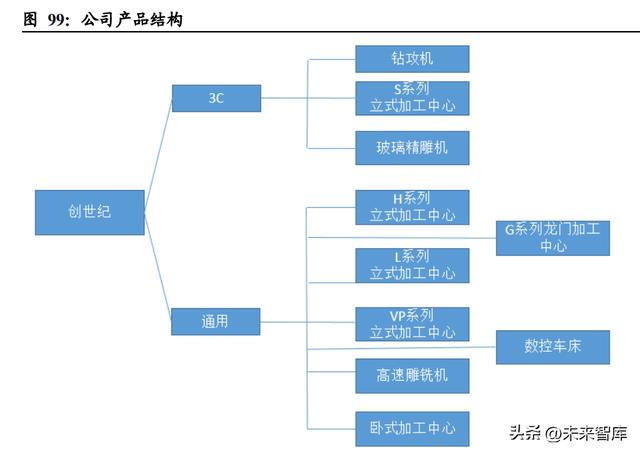
依托 3C 机床规模优势,快速推进数控机床平台建设。在原有 3C 机床规模优势基础 上,近年公司苏州、宜宾、东莞、湖州四大产业基地也先后投产,进一步巩固行业 产能规模的领先地位,经营模式护城河深厚。较大的规模体量也使得公司得以通过 向进口品牌供应商进行战略采购或规模化集采,实现降低成本、质量保证、交付保 障等关键目标,提高公司产品性价比和综合竞争力。
业务剥离影响短期营收利润,2021 年已实现营收利润正增长。近年受精密结构件业 务剥离影响,公司营收利润波动较大,随着公司历史问题基本处理完毕,预计后续 公司营收利润将获得更加稳定的发展。2021 年公司实现营业收入 52.62 亿元,同比 增长 53.60%;归母净利润 5.00 亿元,同比增长 171.71%。
核心财务指标向好:①2021 年财务费用率较 2020 年下降 4.58 个百分点;②销售毛 利率、销售净利率自 2018 年以来持续提升;③ROE、ROA 改善明显整体向上;④ 经营活动现金流持续增长,偿债能力较好。
(本文仅供参考,不代表我们的任何投资建议。如需使用相关信息,请参阅报告原文。)
精选报告来源:【未来智库】。「链接」
相关参考
普通木工车床价格(机床行业深度报告:多因素共振,国产机床有望迎来新一轮上行周期)
...韦松岭)1.工业母机:制造业转型升级要求机床向中高端发展1.1.机床行业简介机床又被称为“工业母机”,是用于制造机器的机器。由于机器设备都是需要通过机床对金属或其他材料的坯料进行加工制造出来的,因而机床又被称...
提高酒店服务质量的意义(酒店行业深度研究:三因素共振,酒店行业迎资产整合浪潮)
...出的轻资产模式变化带来的利润率和ROE水平趋势性提升的发展规律进行了详细阐述。本文将从更长周期视角,对全
数控机床的应用及发展趋势(中国数控刀具行业现状深度调研与发展战略预测报告)
数控又称为切削工具,是机械制造中用于的工具,是指机械制造中用于切削加工的工具,主要由数控刀片、刀垫、夹紧元件以及刀体组成。数控刀具凭借着规格多样、切削速度快、加工周期短等特点广泛应用于汽车制造、工业模...
...床?机床被称为工业母机,即生产机器的机器。人类社会发展到今天,上天入地,五洋捉鳖,每一个方面都需要用到机器设备,需要机器设备的地方就需要机床。机床通过铸造、锻造、焊接、冲压、挤压等方式,对精度要求较高...
数控机床的发展趋势(全国各省市数控机床行业“十四五”发展思路汇总分析)
中商情报网讯:高端数控机床装备是国家工业和国防安全的重要支撑,是制造强国建设的重中之重。中国经济迈向高质量发展,对产品质量的要求越来越高,对数控机床的要求也越来越高。为支持数控机床产业创新发展,中国十...
...期、产量峰值等与机床存量、宏观经济景气度、主要下游发展情况、政策支持相关。1)一般机床更新周期约为10年,工作强度等会影响其使用年限。根据观研天下2022年10月19日发布的报告,机床是机械制造业中的耐用消费品,一...
...床线束管等各类汽车波纹管、空调滴水管。1、影响行业发展的有利因素(1)汽车行业可持续发展及政策扶持的产业环境综合分析我国汽车保有量、人均可支配收入水平以及近年来汽车工业的发展趋势,我国的汽车消费市场已进入...
浙江机床静压主轴多少钱(金属粉末行业深度报告:高端材料,千亿市场)
...制品的工艺方法。因此,金属粉末是伴随着粉末冶金技术发展起来的,金属粉末的应用领域
浙江机床静压主轴多少钱(金属粉末行业深度报告:高端材料,千亿市场)
...制品的工艺方法。因此,金属粉末是伴随着粉末冶金技术发展起来的,金属粉末的应用领域
...成。在新颁布的国家“十二五”规划中,明确提出将重点发展高端装备制造业的信息化、自动化、智能化水平,而这显然离不开精密机床行业的有力支持。其实数控端面铣机床行业在我国的发展不是那么顺利的,随着我国经济和...