插片镀金电镀(光伏电镀铜行业分析:即将开启产业化进程,从0到1设备商率先受益)
Posted
篇首语:吾生也有涯,而知也无涯。本文由小常识网(cha138.com)小编为大家整理,主要介绍了插片镀金电镀(光伏电镀铜行业分析:即将开启产业化进程,从0到1设备商率先受益)相关的知识,希望对你有一定的参考价值。
插片镀金电镀(光伏电镀铜行业分析:即将开启产业化进程,从0到1设备商率先受益)
(报告出品方/作者:东吴证券,周尔双,刘晓旭)
1.电镀铜助力HJT降本增效,产业化进程即将进入加速期
1.1.HJT亟需降低银浆成本,电镀铜为HJT独有的降本方式
HJT 降本为规模扩产关键,银浆降本为重要手段。2021 年以来电池技术路线由 PERC 向更高效率的 HJT、TOPCon 等 N 型技术转变,其中 TOPCon 的扩产规模高于 HJT,我们预计 2022 年 TOPCon 新增扩产超 130GW、HJT 约 30GW,主要系 HJT 的总 成本仍偏高,根据我们的测算,2022 年底硅料 240 元/KG、M6 硅片 4.5 元/片时,TOPCon 总成本约为 0.85 元/W、HJT 总成本约为 0.91 元/W。降本成为 HJT 规模扩产的关键,而 银浆成本在 HJT 总成本中占比最高,根据我们的测算,银浆成本占总成本比重约 11%, 因此降低银浆成本、少银&去银化极为关键。
银浆降本手段主要分为两大类,电镀铜为“终极”去银化降本手段: (1)栅线图形的优化,通过栅线变细从而节约银浆耗量,例如 MBB(多主栅),逐 步由 12BB 向 SMBB、0BB(即无主栅技术,去掉主栅仅保留细栅); (2)浆料银含量的降低,使用贱金属替代贵金属,例如银包铜可利用铜替代部分 银,通过将银覆盖在铜粉颗粒的表面来减少银用量,而电镀铜则可利用铜替代全部银, 实现去银化,彻底解决 HJT 用银问题,同时与其它降银手段相比,电镀铜由于栅线更细 降低遮光面积,能够进一步提升效率,进一步降低单位成本。从降本&增效两个维度考 虑,电镀铜是去银化的终极手段。

电镀铜技术更适用于 HJT,为 HJT 独有的降本项: (1)PERC:无需使用电镀铜,因单面用银、银浆耗量少,电镀铜带来的非硅成本 下降极为有限。 (2)XBC:PN 结和电极均处于电池背面,不需要考虑遮光损失,栅线图形也不需 要特别精细,但 XBC 工艺复杂,需要多次掩膜和刻蚀,电镀铜进一步增加其复杂程度。 (3)TOPCon:①电镀铜要求低温工艺,与 TOPCon 高温工艺不适配,高温下铜容 易氧化失效;②TOPCon 电极直接与硅片接触,缺少 TCO 薄膜阻挡,铜易扩散到硅中, 带来可靠性问题,但可以通过激光在非导电层上开槽再镀镍、烧结后进行电镀铜,镍层 能够提供部分阻挡;③TOPCon 设备和工艺成本低,电镀铜带来的非硅成本降低有限。
(4)HJT:①低温工艺符合电镀铜工艺要求;②HJT 电极与 TCO 薄膜接触,不与 硅片直接接触,能够避免铜污染硅片内部;③HJT 双面用银且低温银浆耗量更大、价格 更高,因此 HJT 银浆降本需求更迫切,故电镀铜降低 HJT 非硅成本效果最明显,更适 用于 HJT 技术——根据我们的测算,假设电镀铜量产后带来 0.5%提效、电镀液等耗材 成本 0.03 元/W、电镀设备价值量 1 亿元/GW,则 PERC/TOPCon/HJT 三种技术路线应 用电镀铜后带来的非硅成本降低幅度分别为 2%/12%/21%。
1.2.电镀铜同时实现降本&增效,耗材&设备国产化推动降本加速进行时
降低电池正面遮光损失、减小栅线的电阻损耗、改善电极与 TCO 接触、低成本电 极制备是电池金属化工艺的发展方向,电镀铜既能够通过更低的电阻、更高的栅线高宽 比来提高转换效率,也能够通过低价铜完全替代高价银实现降本,有望成为去银化的降 本提效终极技术。
(1)增效:①电阻损耗少,导电性能更优:电镀铜栅线内部均匀、与 TCO 接触更 优(图 5 所示),有效减小电极与 PN 结的接触电阻,同时与银浆混合物相比,铜栅线为 纯铜,本身的体电阻更低,铜栅线的体电阻率约 1.8μΩ.cm,低温银浆的体电阻率约 3- 10μΩ.cm,故电阻损耗少、导电性能更优。②线宽更窄,遮光损失少:铜栅线的线宽更 窄、高宽比更高,即电极更窄、更厚,其中铜栅线的线宽约 15μm,低温银浆的线宽大 于 40μm,故电镀铜能够降低栅线遮挡造成的遮光损失、提高载流子收集几率,上述因 素共同作用使得电镀铜相较低温银浆丝网印刷可以提高 0.3-0.5pct 光电转换效率。
(2)降本:目前浆料降本手段主要为银包铜与电镀铜,我们测算对比了两种方式 的非硅成本差异,主要体现在材料和设备两方面,其中银包铜根据发展阶段分为 50%/30% 含银量,HJT 电池效率均为 25%;电镀铜分为小规模初期/规模量产,HJT 电池效率分别 为 25.3%/25.5%。
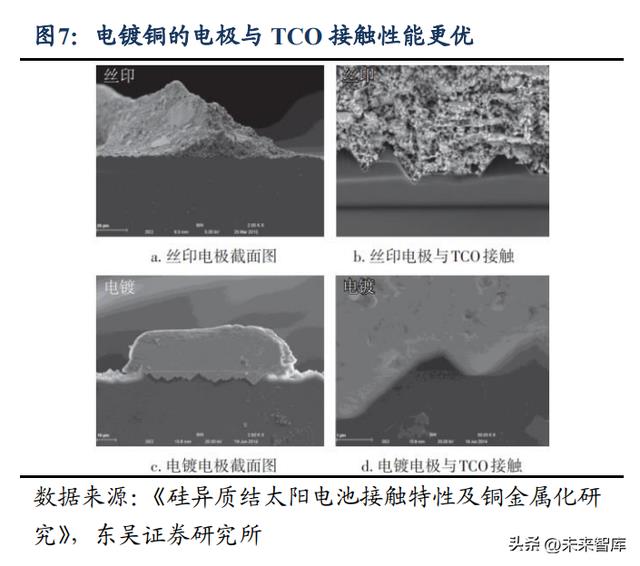
①材料成本:a.银包铜:以浆料耗量 120mg/片为基准,根据 50%/30%的含银比例及 6500 元/KG 的银浆价格测算得到成本分别为 0.05/0.03 元/W;b.电镀铜:我们估计铜耗 量约 77mg/片,结合铜价测算得到成本约为 0.0006 元/W,显著降低浆料成本,但电镀铜 额外需要配备电镀药水、掩膜材料等,目前下游需求量较少且海外供应商居多使得成本 较高,未来国产化&规模放量有望降本,我们估计小规模初期/规模量产后成本分别约 0.07/0.03 元/W,故综合来看虽然电镀铜节省了银浆成本,但额外增加的电镀药水、掩膜 材料等影响了材料降本效果。
②设备成本:a.银包铜:仍采用传统的丝印工艺,单 GW 丝印设备价值量约 4000 万 元,按照 5 年折旧期,则设备折旧成本约 0.01 元/W;b.电镀铜:当前单 GW 电镀铜设 备价值量约 2 亿元,未来有望降低至 1 亿元,按照 5 年折旧期,则设备折旧成本约 0.04/0.02 元/W。 ③材料+设备折旧成本合计:综合材料及设备折旧成本,50%/30%银包铜的边际非 硅成本约为 0.06/0.04 元/W,电镀铜目前成本约为 0.11 元/W,故与银包铜相比,电镀铜 尚不具备显著降本优势,主要系电镀药水、掩膜材料等耗材及设备折旧成本较高,未来 国产化&规模放量降本后有望降低至 0.05 元/W。
当然随着光伏下游装机量持续提升、全球银浆耗量增加可能会带来银价上涨,存在 银包铜材料成本增加的可能性,故我们认为电镀铜的产业化进程除了自身持续降本外, 也取决于其它降银手段的推进速度,同时电镀铜也是抑制银浆价格上涨的有效手段。根 据我们的测算,银价上涨 43%、银浆含税价格 9295 元/KG 时,30%银包铜的材料+设备 折旧成本为 0.051 元/W,而电镀铜工艺量产(提效 0.5%、电镀液和掩膜材料成本为 0.03 元/W、设备价值量 1 亿元/GW)的成本约为 0.051 元/W,此时电镀铜量产成本与银包铜 打平,上涨超过 43%时电镀铜成本低于银包铜,经济性凸显。
1.3.电镀铜处于导入初期,关注下游验证情况
早期电镀铜以研发线和中试线为主,没有大规模量产。2015 年日本 Kaneka 采用电 镀铜的双面异质结电池效率达到 25.1%,并计划利用该技术建立一条试生产线;2018 年 国电投建立了电镀铜中试线,2021 年初效率达到 24.5%;金石能源 2021 年推出了电镀 铜 HBC 组件,组件效率达到 23.3%,中试线效率最高超 26%;2021 年 11 月海源复材公 告与捷得宝合作建设 5GW 电镀铜 HJT 产能,首条线规划投产 600MW。
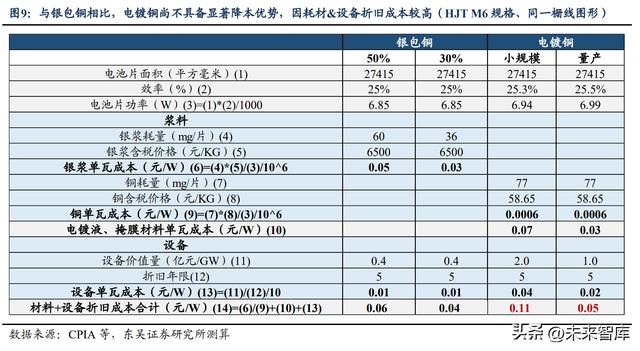
2022 年以来光伏电镀铜耗材借鉴 PCB 领域、设备借鉴半导体领域等均有所突破, 电镀铜快速导入验证。(1)耗材:以往多采用干膜+挂镀方式,但干膜成本较高,热压 到电池片上后容易带来碎片率的提升,2022 年 8 月以来掩膜突破采用湿膜(油墨)后产 业化进程加速,油墨在 PCB 的领域应用较为成熟,通过改善线宽后在光伏领域得以应 用。(2)设备:图形化与金属化设备均有进展,如芯碁微装将激光直写光刻设备由半导 体领域复制到光伏领域,迈为股份与 SunDrive 合作研发无种子层直接电镀工艺等。
电镀铜目前处在产业化初期,仍存在设备产能&环保&良率等问题,我们预计 2023 年行业进行较大规模中试,2024 年有望导入量产。(1)设备产能:目前设备产能较低, 未来设备产能进一步提升后有利于降本。(2)环保:在电镀铜工艺生产过程中,会产生 干膜或油墨、电镀液等有机污染物,且沉积抗蚀剂、曝光、抗蚀剂显影需在黄光洁净室 内进行需要进行后续处理。(3)良率:相较丝网印刷,电镀铜工序更长、更复杂,使得 良率较低。随着设备、耗材等产业链配套成熟,下游电池厂积极研发验证,我们认为 2023 年行业将进行较大规模中试,2024 年有望导入量产。
2.多种技术方案角力,电镀铜设备商优先受益
2.1.到2025年电镀铜设备市场空间达30亿元,2023-2025年CAGR达260%
电镀铜工序包括种子层制备、图形化、电镀三大环节,涌现多种设备方案。电镀铜 工艺尚未定型,各环节技术方案包括(1)种子层:设备主要采用 PVD,主要技术分歧 在于是否制备种子层、制备整面/局部种子层和种子层金属选用;(2)图形化:感光材料 分为干膜和油墨,主要技术分歧在于曝光显影环节选用掩膜类光刻/LDI 激光直写/激光 开槽;(3)电镀:主要技术分歧在于水平镀/垂直镀/光诱导电镀。
目前电镀铜设备价值量共 2 亿元/GW,预计有望下降到 1 亿元/GW 左右。以 HJT 电镀铜工艺为例,种子层制备环节,PVD 设备价值量约 5000 万元/GW,占比约为 25%; 图形化环节由于技术路线选择差异,设备价值量在 4000-6000 万元/GW 不等,占比约为 30%;电镀环节设备价值量约 5000 万元/GW,占比约为 25%,其它设备占比约为 20%。 伴随各环节技术进一步成熟及电镀铜规模化量产,我们预计设备投资额后续有望下降到 1 亿元/GW 左右。
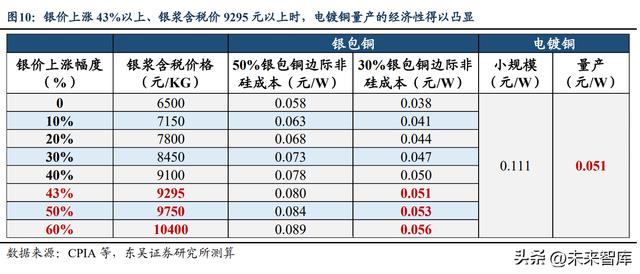
我们预计到 2025年电镀铜设备市场空间达 30亿元,2023-2025年 CAGR达 260%。 目前电镀铜仍然处于试验阶段,我们预计 2023 年年中出现 100-300MW 产线,2024 年 出现 GW 级产线。假设 2023-2025 年 HJT 在光伏电池片中分别达到 25%、35%、45%的 渗透率,电镀铜在 HJT 金属化方法中分别达到 2%、10%、25%的渗透率,我们测算到 2025 年电镀铜设备市场空间为 30 亿元,2023-2025 年 CAGR 达 260%,其中 PVD 市场 空间达到 7 亿元,图形化设备市场空间达到 9 亿元,电镀设备市场空间达到 7 亿元。
2.2.种子层制备:PVD为主流方案,2025年新增设备市场空间约7亿元
制备种子层的主要作用为提升栅线与 TCO 层之间的导电性和附着力。由于 HJT 电 池电极接触透明导电薄膜(TCO 层),会存在电镀金属与 TCO 层之间吸附力较差的问 题,通常借鉴半导体行业的方案,在电镀金属与 TCO 层之间制备整面“种子层”、掩膜电 镀后去除掩膜蚀刻未电镀部分种子层来解决附着力的问题,但应用于光伏行业的大规模 生产需要解决几个问题:(1)步骤较多导致的良率较低和成本较高;(2)种子层蚀刻溶 液会一定程度刻蚀 TCO 层,增加量产工艺难度和废液处理成本;(3)制备铜种子层后 薄膜的透过率发生降低,进而导致光电转换效率降低等。
HJT 电池可以选择制备种子层(整面或局部)或不制备种子层直接电镀。(1)整面 制备种子层:如捷德宝的方案为整面制备种子层;(2)局部制备种子层:如太阳井拥有 局部制备种子层的专利,保障电镀电极与 TCO 层高附着力,同时省去种子层刻蚀步骤; (3)无种子层直接电镀:如迈为股份 2022 年 9 月联合澳大利亚金属化技术公司 SunDrive 研制出转换效率高达 26.41%的 HJT 电池(M6 尺寸),SunDrive 即为无种子层直接电镀 工艺。
种子层制备所需设备为 PVD,设备价值量约 5000 万元/GW。制备种子层的方法通 常是物理气相沉积法(PVD),将具有透明导电薄膜的基片放置在镀膜载板表面进入腔 室上镀膜,可采用 PVD 溅射法、PVD 蒸镀法或 PVD 离子镀法,沉积包括铜、镍、银、 铝的单一膜层或复合膜层,沉积厚度为 5‑500nm。PVD 方案优势在于(1)便于控制工 艺温度在 200℃左右;(2)技术成熟,可共用沉积 TCO 膜层的 PVD 或新增 PVD 设备实 现。其它制备方法包括 RPD、印刷等。 我们预计到 2025 年电镀铜新增 PVD 设备市场空间为 7 亿元,迈为有望首先受益。 相较于 RPD 设备,迈为股份 PVD 设备具备产能较高、靶材利用率较高、成本较低等优 势,且与 RPD 转换效率差距逐步缩小。伴随 PVD 逐渐成为种子层制备主流设备,我们 认为迈为股份有望首先受益。
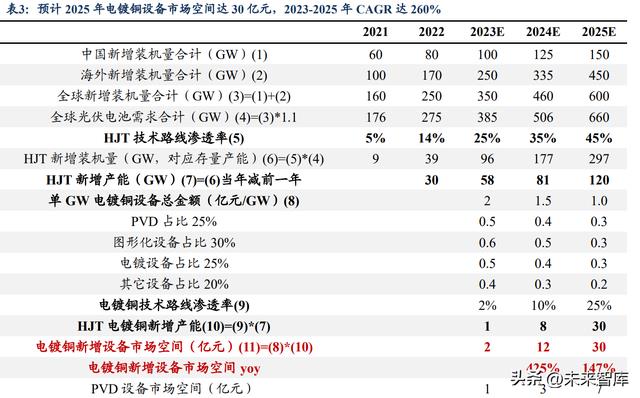
2.3.图形化:“油墨+掩膜类光刻”经济性强,2025年新增设备市场空间约9亿元
图形化环节分为掩膜、曝光、显影工序。掩膜即在电池片上涂覆感光材料,曝光指 在烘干后的电池片上留下待电镀区域图形(或需掩模版,该掩模版与感光材料不同),显 影指去除电池片表面待电镀区域的感光材料,最终形成电镀需要的图形化开口。 掩膜工序中,油墨正在成为主流感光材料,优势在于低成本和细线宽。感光材料分 为干膜和湿膜(油墨),主要作用为阻挡和蚀刻,且电镀栅线的线宽取决于掩膜的精度。 干膜是 PCB 行业的成熟耗材,应用于光伏电镀铜的劣势在于(1)成本较高;(2)需要 热压贴到电池片上,容易造成碎片率的提升;(3)栅线难以做细,只能达到 30 微米。油 墨的优势在于更低的成本和更细的线宽,经技术突破现已能满足电镀铜 10 微米线宽要 求。涂覆感光材料可以采用层压、喷墨打印、丝网印刷、超声喷涂、滚压涂布等方式, 其中油墨印刷应用较为普遍。
曝光显影可以通过掩膜类光刻、LDI 激光直写、激光开槽或喷墨打印实现。曝光工 序可采取(1)掩膜类光刻:需要通过掩模版把图形转移到涂覆感光材料的电池片上,按 曝光光源可分为激光光源和紫外 LED 光源。(2)LDI 激光直写:计算机控制的高精度 光束聚焦投影至涂覆有感光材料的基材表面上完成曝光。(3)激光开槽:替代曝光显影, 直接打开掩膜实现图形化。(4)喷墨打印:使用蚀刻机喷墨打印刻蚀剂以完成开槽,线 宽通常在 25 微米内。
我们预计到 2025 年电镀铜新增图形化设备市场空间约为 9 亿元,相关标的包括迈 为股份、芯碁微装、帝尔激光。按技术路线来看,(1)掩膜类光刻:我们看好经济性更 强的“油墨+掩膜类光刻”技术路线,迈为股份有望凭借丝网印刷相关技术积淀实现技 术突破。(2)LDI 激光直写:芯碁微装下游验证进展较快,与头部电池片厂商如隆基、 通威进行技术交流。(3)激光开槽:帝尔激光布局电镀铜激光开槽设备,目前已获得 GW 级 BC 电镀铜订单。
2.4.电镀:看好水平镀技术突破,2025年新增设备市场空间约7亿元
电镀原理为在掩膜的图形化开口处通过电镀形式沉积金属铜,形成铜电极。电镀是一种湿法沉积过程,可以通过调控电流密度大小来控制金属阳离子沉积速率,通过控制总电荷量、电镀面积和电镀时间控制金属层厚度。但电镀过程中需要外加电源,需要设置电极夹点,容易造成电池片隐裂,并且在电镀后,夹点区域被铜覆盖,一定程度上减小了电池的有效工作面积。
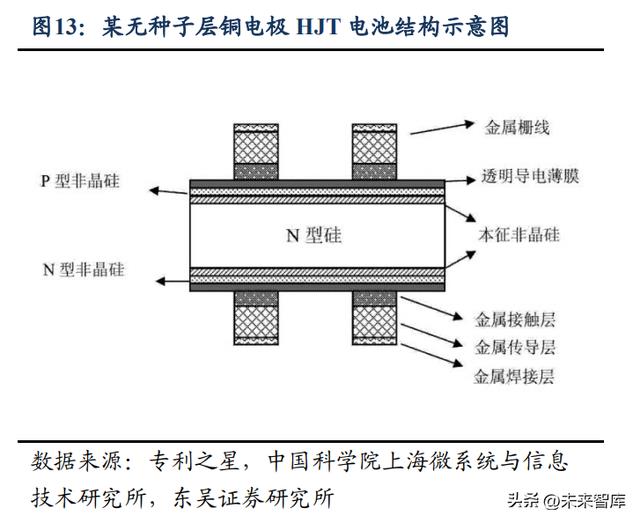
电镀环节主要包括水平镀、垂直镀、光诱导电镀等。(1)水平镀:硅片通过滚轮水 平进入电镀机,上下两层导电的毛刷与硅片图形化留下的沟槽接触,实现长铜。(2)垂 直镀:通过夹具夹爪夹着硅片上预留好的夹点进入电镀机,长铜原理和水平镀一致,区 别为自动化程度较低,主要包括垂直升降式电镀和垂直连续式电镀,垂直连续镀能够不 使用挂具。(3)光诱导电镀:将电池片通过滚轮传输进行光照,光照面通过电极线与电 镀液导通,形成闭合回路以完成金属沉积。其原理为:光线照射到电池片表面,电池片 内产生光生载流子,在内建电场的作用下被分离成电子和空穴,分别向n型掺杂硅层面、 p 型掺杂硅层面处移动,电子发生还原反应,溶液中的金属离子由此被消耗,生成的金 属被沉积到电池片表面。
我们看好水平镀技术突破,有望满足光伏电镀铜大产能低成本量产条件。根据罗博特科专利说明书,虽然垂直镀成熟度水平较高,但其主要缺陷在于自动化水平较低带来 的产能低下,难以满足光伏大产能需求;且电镀槽体较大、耗材用量较多、电镀均匀性 有待提升。相较而言,水平镀药水用量小,自动化水平高,且产能较高,碎片率低;但 制程难度较高,电池表面空洞、接触稳定性、电池片损伤等问题有待攻克。目前已有厂 商转向水平镀与垂直镀结合的电镀技术,我们看好水平镀技术突破,提升电镀环节生产 节拍和生产良率,进一步推动电镀铜技术的广泛应用。
我们预计到 2025 年电镀铜新增电镀设备市场空间约 7 亿元,相关标的包括迈为股 份、罗博特科、东威科技。(1)迈为股份:与启威星合作开发水平电镀设备,启威星湿 法工艺积累深厚,已布局水平电镀设备及生产线、电镀夹具、药液浓度控制等方面专利; (2)罗博特科:布局 4 种电镀技术方案,2023 年 1 月公开的发明专利宣布实现双面电 镀、单线产能 14000 整片/小时、破片率<0.02%。(3)东威科技:专注于垂直镀,2022 年 12 月发布垂直连续电镀第三代设备,宣布电镀产能达 8000 片/小时,预计 2023 年上 半年发货;2023 年 1 月公告与国家电投及其子公司合作协议,将提供一台样机用于验证 测试。
3.本土重点公司介绍
3.1.迈为股份:光伏异质结设备领军者,积极布局电镀铜工艺
HJT 设备龙头,前瞻布局铜电镀技术。迈为股份为 HJT 整线设备龙头,积极布局 电镀铜技术,2021 年 9 月与澳大利亚 SunDrive 合作使用无种子层直接铜电镀工艺实现 了 M6 尺寸 HJT 电池片 25.54%转换效率,2022 年 8 月进一步提升至 26.41%,创造了新 的世界纪录,目前迈为自主研发图形化环节设备,与启威星等合作布局电镀环节设备, 我们预计 2023 年进行中试,2024 年有望正式对外提供整线。 (1)已有的 PVD 技术可适用于种子层制备:HJT 种子层和 TCO 薄膜沉积可使用 同一台 PVD 设备(需要增加腔体数量)或直接增加一台 PVD 设备(靶材需更换为铜或 铜合金等种子层材料),公司自主研发 PVD 镀膜设备的技术经验可延伸至 HJT 电镀铜 工艺。
(2)丝印图形化技术积累与类光刻具备协同性:迈为图形化技术积累丰富,丝印 网板与掩膜版有一定相通性,①掩膜曝光 vsLDI 路线:掩膜曝光设备价值量仅为 LDI 设 备的 1/2 甚至 1/3,经济性优势突出,LDI 设备不仅稳定性较差,激光还可能损伤 HJT 电 池的钝化层。②油墨(湿膜)vs 干膜:油墨已于 2022 年 8-9 月实现线宽突破,能够满 足电镀铜对于栅线线宽的要求(<10 微米),而干膜还未达到相应水准。 (3)与启威星等合作电镀环节:垂直电镀产能有限且难以提升,因此迈为倾向于 选择生产效率更高、产能更大的水平电镀方案,铜电镀的布局由迈为参股公司江苏启威 星进行。启威星通过引进日本 YAC 的制绒清洗技术,为迈为 HJT 整线提供配套清洗制 绒设备,具有多年湿法技术的积累和对 HJT 工艺需求的深刻理解。目前启威星电镀设备 处于研发阶段,并已经有电池行业的客户在进行试用。
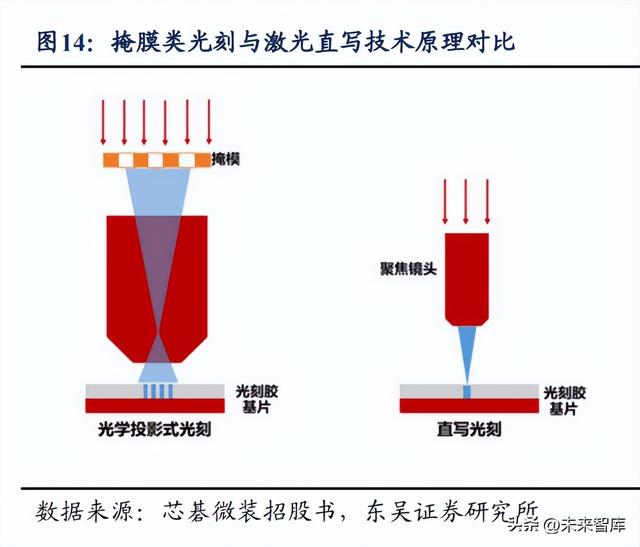
3.2.太阳井(未上市):领跑异质结电镀铜整线设备,自主研发实力构筑技术护城河
科研实力夯实发展基石,吸引通威两轮投资。苏州太阳井新能源有限公司创立于 2017 年,致力于研发、生产异质结电池铜制程整套解决方案。公司由澳大利亚新南威尔 士大学光伏专业海归博士团队带领,年研发投入额超千万元,掌握异质结太阳能电池领 域多项核心技术,目前已申请国内外专利 70 余项,其中近 30 项专利已获得授权。受益于 双碳政策,公司迎来快速发展期,先后获得光伏行业龙头企业通威股份的两轮战略投资。
开发低成本镀铜技术,降本增效优势明显。通过实现低成本图形化掩膜技术与 TCO 直接镀铜技术突破,公司成功开发出低成本铜制程异质结太阳能电池金属化技术,可显 著降低生产成本、提升生产效率及良率,进而大幅提升产品的竞争力。在此技术的基础 上,公司建成世界首条 250MW 级别量产生产线,目前正处于量产验证及组件扩产阶段, 预计 2024 年前可实现产业大规模应用,届时电池效率可提升至 24.8%。
3.3.罗博特科:光伏自动化设备龙头,首创新型异质结电池铜电镀装备
光伏自动化设备龙头,积极布局 TOPCon、HJT 等方向。罗博特科自 2011 年成立 以来深耕光伏自动化设备,突出的技术实力确保公司在薄片化趋势下的 TOPcon 市场中 仍占据龙头地位并得到下游客户的广泛认可,公司客户包括天合光能、通威太阳能和 SunPower 等国内外知名的大型光伏厂商。同时公司也在 HJT 领域积极布局,2015 年杭 州赛昂成功实现铜电镀 HJT 量产化应用时,罗博特科便为其提供自动化设备,积累了相 关技术经验。目前公司关于 HJT 技术路径的自动化技术和产品已迭代至第三代,处于行 业领先水平。
完成新型异质结电池铜电镀装备交付,成功切入铜电镀业务领域。区别于传统的垂 直升降式电镀、垂直连续电镀、水平电镀技术方案,公司独创了全新的量产型铜电镀方 案,从源头上解决了目前生产中产能低、运营成本高等痛点,这种插片式太阳能电池片 铜电极电镀装置及方法已在申请专利。目前公司提供的电镀铜方案主要是基于 HJT 路 线,其在 TOPCon 方向上的延展性应用也在考虑范围内。公司已于 2022 年 12 月完成了 业界首创新型异质结电池铜电镀装备交付,后续将与合作客户(传统玩家)一起完成设 备的安装调试及工艺测试与优化工作,并将持续加快推进该业务领域的量产化进程。 2023 年 1 月公告与国家电投在铜栅线异质结电池 VDI 电镀解决方案达成战略合作。
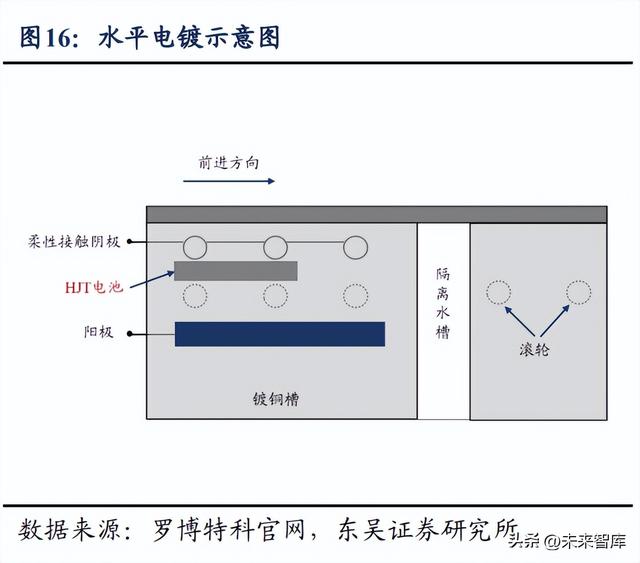
3.4.东威科技:PCB电镀设备龙头,光伏电镀铜领域成功突破
PCB 电镀设备龙头,垂直连续电镀设备技术水平国际领先。公司产品包括 PCB 电 镀专用设备(VCP、水平化铜、水平镀等),五金表面处理专用设备,以及面向新能源动 力电池负极材料专用设备、光伏领域专用设备、真空溅射专用设备等。其中垂直连续电 镀设备(VCP)为公司主要收入来源。垂直连续电镀设备技术水平国际领先,电镀均匀 性、贯孔率(TP)等关键指标上处于行业领先水平。
积极拓展光伏电镀设备,实现客户突破。公司第二代光伏垂直连续硅片电镀设备于 2022 年初交付客户,经客户反馈均匀性、破片率等重要指标均达到要求,目前已完成客 户验收。2022 年 12 月,公司发布垂直连续电镀第三代设备,宣布电镀产能达 8000 片/ 小时,预计 2023 年上半年发货;2023 年 1 月公告与国家电投及其子公司合作协议,将 提供一台样机用于铜栅线异质结电池垂直连续电镀解决方案的验证测试。
3.5.捷得宝(未上市):光伏电池电镀铜先行者,整线设备积累深厚
光伏电池电镀铜先行者,团队技术背景卓越。捷得宝科技股份有限公司、苏州捷得 宝机电设备有限公司分别成立于 2012 年、2015 年,致力于光伏电池电镀铜解决方案, 布局相关设备工艺专利超过 20 项。团队技术背景卓越,主要人员来自于应用材料,其 中总经理单伶宝先生曾任应用材料事业部总经理、保利协鑫光电GCL光电事业部总裁。 自研油墨掩膜+水平镀,HJT 整线设备积累深厚。公司自研图形化一体机和电镀一 体机,水平电镀产能可达 7500 片/小时,可应用于 HJT 和 TOPCon 电池片,客户认可度较高。早在 2018 年,公司完成南昌国电投的 120MW HJT 电镀产线交钥匙工程。2021 年,公司与海源复材签订协议,提供前期 600MW 设备,包括 PECVD、电镀铜相关设 备,制绒设备与国内厂商合作。
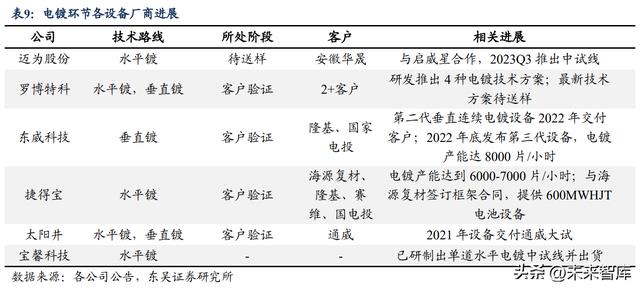
3.6.芯綦微装:国内激光直写设备龙头,拟定增加码电镀铜应用
国内激光直写设备龙头,下游验证进展领先。公司主要产品为微纳级别直接成像设 备与直写光刻设备,产品广泛应用于半导体、显示及 PCB 行业,市占率不断上升。公司 直写光刻技术不断取得突破,已将应用于 IC 载板产业化生产的直写光刻设备线路层曝 光精度(最小线宽)由 8 微米提升至 6 微米。根据公司定增预案,在新能源光伏领域, 公司已经与下游知名电池片厂商进行了技术探讨。
拟定增加码电镀铜应用,设备研发进展加速。根据公司定增预案,公司预计投资总 计 3.18 亿元建设现代化的直写光刻设备生产基地,推动直写光刻设备在新能源光伏等 领域的应用。根据公司定增回复函,公司拟投入 4200 万元规划一条电镀铜中试实验线; 截至 2022 年 12 月,公司已实现实验室条件下满足 5 微米以下线宽的铜栅线曝光需求的 直写光刻设备产业化;同时提供量产线实现最小15微米的铜栅线直写曝光方案,产能 达到 6000 片/小时、对位精度±10 微米,可以应用于HJT,并支持210mm 的整片和双 半片光伏电池的制造。
3.7.苏大维格:依托光刻机先进制造能力,进军电镀铜图形化领域
苏大维格是国内领先的微纳结构产品制造和技术服务商。通过自主研发光刻机,公 司建立微纳光学研发与生产制造的基础技术平台体系,目前已形成公共安全和新型印材、 消费电子新材料、反光材料、高端智能装备四大事业群。根据公司 2022 年半年报,微 纳光学产品贡献 6.4 亿元营业收入,占比 73.2%;反光材料贡献 2.3 亿元营业收入,占比 25.6%;设备贡献 0.2 亿元营业收入,占比 0.3%。
依托光刻机先进制造能力,进军电镀铜图形化领域。公司成功开发多个系列覆盖纳 米级和微米级的光刻机设备,设备精度满足光伏电镀铜要求。根据公司 2021 年年报, 在光刻机关键器件方面,公司向上海微电子提供了其半导体领域投影式光刻机用的定位 光栅部件,充分证明公司光刻机方面先进制造能力。根据公司 2021 年年报及 2022 年半 年报,公司积极拓展光刻机设备在太阳能光伏电池铜电镀方案图形化方面的应用。
(本文仅供参考,不代表我们的任何投资建议。如需使用相关信息,请参阅报告原文。)
精选报告来源:【未来智库】「链接」
相关参考
抗电镀油墨(从东威科技的暴涨,看HJT铜电镀降本的可行性多少)
HJT产业化阻力:光伏银浆成本高昂HJT效率改进难抵光伏辅材银浆成本高。银浆是HJT光伏电池的关键原材料,是由高纯度(99%)的银粉、玻璃氧化物、有机材料等所组成的机械混合物的粘稠状浆料,应用在HJT电池生产的最后一步主...
昆山丝印器材(依托电镀设备实现横纵向延伸,东威科技:受益锂电复合铜箔产业化)
(报告出品方/分析师:东吴证券周尔双刘晓旭)1.东威科技:依托电镀设备实现横纵向延伸,拓展锂电、光伏领域迎新增长极1.1.电镀龙头设备商,拓展光伏、锂电新领域东威科技依托电镀设备实现横纵向延伸,拓展锂电、光伏...
无锡覆铜板分切刀(PCB电镀设备龙头,东威科技:复合铜箔产业化,开启新成长曲线)
(报告出品方/分析师:广发证券代川朱宇航范方舟)一、东威科技:PCB电镀设备龙头,围绕工艺拓场景(一)立足PCB电镀设备,围绕电镀工艺拓展锂电镀膜、光伏镀铜设备东威科技是PCB电镀设备龙头,围绕电镀铜工艺,拓展锂...
批全铜龙头(市场爆炒新技术:光伏电镀铜VDI技术龙头估值还有多大空间)
核心要点:1)电镀铜的优势:电池转换效率的提升和节约银浆成本。2)电镀铜设备:电镀铜设备可兼容异质结、Topcon,只要用铜电镀一定有图形转移技术,一定会买曝光机、油墨印刷机等。只要用铜电镀,就绕不开芯碁微装的...
氧化电镀电源(深圳高频电镀电源应用于哪些产业 高频电镀电源有什么特点)
我们都知道,现在的高频电镀电源都是用于镀金、银、镉、铜、锌、锡及合金等不同材料的镀液中,而且高频电镀电源与传统整流器相比有着独特的特点,比如说电源体积小,重量轻,效,控制精度高。那么高频电镀电源应用于...
...电镀-→二级逆流漂洗-→镀镍-→二级水洗-→浸柠檬酸-→镀金-→回收-→2-3级纯水洗-→烘干;其中的
今晚九点半盗窃金饰后到金器店销赃买卖双方均被抓侦查中发现老板收购的“金粉”可能来路也不正……“今后我一定加强对电镀材料的管理和对员工的法治教育,坚决杜绝此类情况再次发生……”2月21日,在江苏省丹阳市检察...
...将电镀工艺分为镀铬、镀铜、镀镉、镀锡、镀锌、镀镍、镀金、镀银共8大类。接下来,小编将为大家详细介绍电镀工艺8大分类的原理和特点。浪声手持式镀层分析仪镀铬铬是一种微带天蓝色的银白色金属。它有很强的钝化性能...
...离磨料线锯3.2固结磨粒线锯3.3树脂结合剂固结磨粒线锯3.4电镀固结磨粒线锯3.5金刚石线锯4.金属钨丝第二章光伏行业各环节概况1.光伏产业链概述2.光伏产业链主要材料产销情况2.1多晶硅2.2硅片2.3晶硅电池片2.4晶硅组件2.5光伏市场...
电镀废水的来源一般为:(1)镀件清洗水;(2)废电镀液;(3)其他废水,包括冲刷车间地面,刷洗极板洗水,通风设备冷凝水,以及由于镀槽渗漏或操作管理不当造成的“跑、冒、滴、漏”的各种槽液和排水;(4)设备冷却水,冷却水...