捷米前置过滤器官网(氢燃料电池技术发展前景)
Posted
篇首语:生也有涯,知也无涯。本文由小常识网(cha138.com)小编为大家整理,主要介绍了捷米前置过滤器官网(氢燃料电池技术发展前景)相关的知识,希望对你有一定的参考价值。
捷米前置过滤器官网(氢燃料电池技术发展前景)
【能源人都在看,点击右上角加\'关注\'】
文/刘应都 郭红霞 欧阳晓平 湘潭大学材料科学与工程学院 西北核技术研究院,中国工程科学
一、前言
当前人类建立在以消耗煤炭、石油、天然气为主的不可再生能源基础之上的经济发展模式,导致了日益突出的环境污染和温室效应问题。为实现人类社会可持续发展,建立人与自然的和谐关系,发展风能、水能、太阳能、生物质能、地热能、海洋能等绿色能源,成为世界各国高度关注的课题。多数可再生能源所固有的间隙性、随机与波动性,导致了严重的弃风、弃光、弃水等现象。氢能作为可存储废弃能源并推动由传统化石能源向绿色能源转变的清洁能源,其能量密度(140MJ/kg)是石油的3倍、煤炭的4.5倍,被视为未来能源革命的颠覆性技术方向。
氢燃料电池是以氢气为燃料,通过电化学反应将燃料中的化学能直接转变为电能的发电装置,具有能量转换效率高、零排放、无噪声等优点,相应技术进步可推动氢气制备、储藏、运输等技术体系的发展升级。在新一轮能源革命驱动下,世界各国高度重视氢燃料电池技术,以支撑实现低碳、清洁发展模式。发达国家或地区积极发展“氢能经济”,制定了《全面能源战略》(美国)、《欧盟氢能战略》(欧盟)、《氢能/燃料电池战略发展路线图》(日本)等发展规划,推动燃料电池技术的研发、示范和商业化应用。
我国也积极跟进氢能相关发展战略,2001年确立了863计划中包括燃料电池在内的“三纵三横”战略;《能源技术革命创新行动计划(2016—2030)》《汽车产业中长期发展规划》(2017年)等国家政策文件均明确提出支持燃料电池汽车发展。2020年,科技部启动了国家重点研发计划“可再生能源与氢能技术”重点专项,将重点突破质子交换膜、气体扩散层碳纸、车用燃料电池催化剂批量制备技术、空压机耐久性、高可靠性电堆等共性关键技术。国家能源局将氢能及燃料电池技术列为“十四五”时期能源技术装备重点任务。
研究表明,氢能及氢燃料电池技术有望大规模应用在汽车、便携式发电和固定发电站等领域,也是航空航天飞行器、船舶推进系统的重要技术备选方案,但面临低生产成本(电解质、催化剂等基础材料)、结构紧凑性、耐久性及寿命三大挑战。
美国能源部燃料电池技术项目研究认为,燃料电池电动汽车是减少温室气体排放、降低石油使用量的最有效路径之一,随着技术进步,全过程生产成本和氢燃料成本将与其他类型车辆及燃料相当。优化系统控制策略、开发催化剂及其抗腐蚀载体等新型基础材料,是提高系统耐久性和寿命、进而促成氢燃料电池技术大规模商业化应用的有效路径。近期的综述性研究工作,报道了氢燃料电池系统在双极板、气体扩散层、催化剂、膜电极、流场设计与分析等材料或组件方面的新进展。
我国提出了将于2030年实现碳达峰、2060年实现碳中和的发展愿景。积极发展氢能,引导高碳排放制氢工艺向绿色制氢工艺转变,是能源革新发展,实现碳达峰、碳中和的重要举措。氢能将是我国能源领域的战略性新兴产业,氢燃料电池技术是实现氢能利用的先决条件。为了促进我国氢燃料电池技术产业链的全面发展,本文依托中国工程院咨询项目的支持,分析国内外氢燃料电池技术关键材料、核心组件的研发与应用现状,凝练我国发展氢燃料电池技术面临的问题,梳理未来相关技术发展方向并提出保障措施建议,以期为行业技术发展提供基础性参考。
二、氢燃料电池技术体系及发展现状
氢燃料电池与常见的锂电池不同,系统更为复杂,主要由电堆和系统部件(空压机、增湿器、氢循环泵、氢瓶)组成。电堆是整个电池系统的核心,包括由膜电极、双极板构成的各电池单元以及集流板、端板、密封圈等。膜电极的关键材料是质子交换膜、催化剂、气体扩散层,这些部件及材料的耐久性(与其他性能)决定了电堆的使用寿命和工况适应性。近年来,氢燃料电池技术研究集中在电堆、双极板、控制技术等方面,氢燃料电池技术体系及部分相关前沿研究如图1所示。
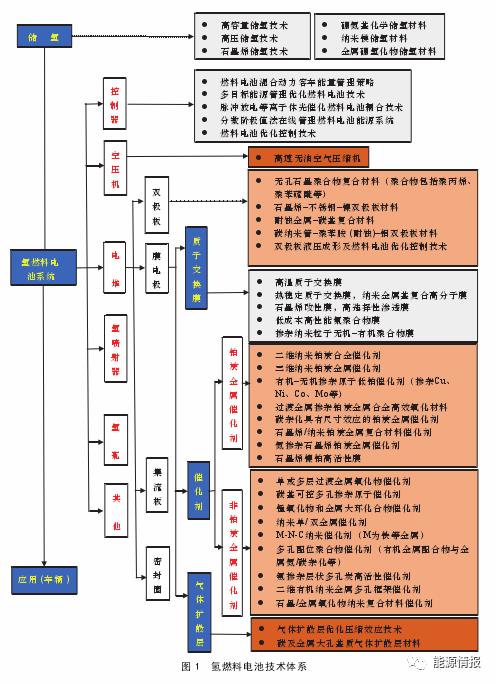
(一)膜电极组件
膜电极(MEA)是氢燃料电池系统的核心组件,通常由阴极扩散层、阴极催化剂层、电解质膜、阳极催化剂层和阳极气扩散层组成,直接决定了氢燃料电池的功率密度、耐久性和使用寿命。根据MEA内电解质的不同,常用的氢燃料电池分为碱性燃料电池(AFC)、熔融碳酸盐燃料电池(MCFC)、磷酸燃料电池(PAFC)、固体氧化物燃料电池(SOFC)、质子交换膜燃料电池(PEMFC)等。各类型燃料电池具有相应的燃料种类、质量比功率和面积比功率性能,其中质子交换膜燃料电池以启动时间短(~1min)、操作温度低(
1.质子交换膜(PEM)
全氟磺酸膜是常用的商业化PEM,属于固体聚合物电解质;利用碳氟主链的疏水性和侧链磺酸端基的亲水性,实现PEM在润湿状态下的微相分离,具有质子传导率高、耐强酸强碱等优异特性。代表性产品有美国杜邦公司的Nafion系列膜、科慕化学有限公司的NC700膜、陶氏集团的Dow膜、3M公司的PAIF膜,日本旭化成株式会社的Aciplex膜、旭硝子株式会社的Flemion膜,加拿大巴拉德动力系统公司的BAM膜,这些膜的差异在于全氟烷基醚侧链的长短、磺酸基的含量有所不同。我国武汉理工新能源有限公司、新源动力有限公司、上海神力科技有限公司、东岳集团公司已具备全氟磺酸PEM产业化的能力。
轻薄化薄膜制备是降低PEM欧姆极化的主要技术路线,膜的厚度已经从数十微米降低到数微米,但同时也带来膜的机械损伤、化学降解问题。
当前的解决思路,一是采用氟化物来部分或全部代替全氟磺酸树脂,与无机或其他非氟化物进行共混(如加拿巴拉德动力系统公司的BAM3G膜,具有非常低的磺酸基含量,工作效率高、化学稳定性和机械强度较好,价格明显低于全氟类型膜);二是采用工艺改性全氟磺酸树脂均质膜,以多孔薄膜或纤维为增强骨架,浸渍全氟磺酸树脂得到高强度、耐高温的复合膜(如美国科慕化学有限公司的NafionXL-100、戈尔公司的Gore-select膜、中国科学院大连化学物理研究所的Nafion/PTFE复合膜与碳纳米管复合增强膜等)。值得一提的是,戈尔公司掌握了5.0μm超薄质子交换膜的制备技术,2019年投产世界首条氢燃料电池车用PEM专用生产线,在日本丰田汽车公司的Mirai汽车上获得使用。此外,为了耐高温、抗无水并具有较高的高质子传导率,高温PEM、高选择性PEM、石墨烯改性膜、热稳定PEM、碱性阴离子交换膜、自增湿功能复合膜等成为近年来的研究热点。
2.电催化剂
在氢燃料电池的电堆中,电极上氢的氧化反应和氧的还原反应过程主要受催化剂控制。催化剂是影响氢燃料电池活化极化的主要因素,被视为氢燃料电池的关键材料,决定着氢燃料电池汽车的整车性能和使用经济性。催化剂选用需要考虑工作条件下的耐高温和抗腐蚀问题,常用的是担载型催化剂Pt/C(Pt纳米颗粒分散到碳粉载体上),但是Pt/C随着使用时间的延长存在Pt颗粒溶解、迁移、团聚现象,活性比表面积降低,难以满足碳载体的负载强度要求。Pt是贵金属,从商业化的角度看不宜继续作为常用催化剂成分,为了提高性能、减少用量,一般采取小粒径的Pt纳米化分散制备技术。然而,纳米Pt颗粒表面自由能高,碳载体与Pt纳米粒子之间是弱的物理相互作用;小粒径Pt颗粒会摆脱载体的束缚,迁移到较大的颗粒上被兼并而消失,大颗粒得以生存并继续增长;小粒径Pt颗粒更易发生氧化反应,以铂离子的形式扩散到大粒径铂颗粒表面而沉积,进而导致团聚。
为此,人们研制出了Pt与过渡金属合金催化剂、Pt核壳催化剂、Pt单原子层催化剂,这些催化剂最显著的变化是利用了Pt纳米颗粒在几何空间分布上的调整来减少Pt用量、提高Pt利用率,提高了质量比活性、面积比活性,增强了抗Pt溶解能力。通过碳载体掺杂氮、氧、硼等杂质原子,增强Pt颗粒与多种过渡金属(如Co、Ni、Mn、Fe、Cu等)的表面附着力,在提升耐久性的同时也利于增强含Pt催化剂的抗迁移及团聚能力。
为了进一步减少Pt用量,无Pt的单/多层过渡金属氧化物催化剂、纳米单/双金属催化剂、碳基可控掺杂原子催化剂、M-N-C纳米催化剂、石墨烯负载多相催化剂、纳米金属多孔框架催化剂等成为领域研究热点;但这些新型催化剂在氢燃料电池实际工况下的综合性能,如稳定性、耐腐蚀性、氧还原反应催化活性、质量比活性、面积比活性等,还需要继续验证。美国3M公司基于超薄层薄膜催化技术研制的Pt/Ir(Ta)催化剂,已实现在阴极、阳极平均低至0.09mg/cm2的铂用量,催化功率密度达到9.4kW/g(150kPa反应气压)、11.6kW/g(250kPa反应气压)。德国大众汽车集团牵头研制的PtCo/高表面积碳(HSC)也取得重要进展,催化功率密度、散热能力均超过了美国能源部制定的规划目标值(2016—2020年)。后续,减少铂基催化剂用量、提高功率密度(催化活性)及基于此目标的MEA优化制备,仍是降低氢燃料电池系统商用成本的重要途径。
3.气体扩散层
在氢燃料电池的电堆中,空气与氢气通入到阴、阳极上的催化剂层还需要穿越气体扩散层(GDL)。GDL由微孔层、支撑层组成,起到电流传导、散热、水管理、反应物供给的作用,因此需要良好的导电性、高化学稳定性、热稳定性,还应有合适的孔结构、柔韧性、表面平整性、高机械强度;这些性能对催化剂层的电催化活性、电堆能量转换至关重要,是GDL结构和材料性能的体现。微孔层通常由碳黑、憎水剂构成,厚度为10~100μm,用于改善基底孔隙结构、降低基底与催化层之间的接触电阻、引导反应气体快速通过扩散层并均匀分布到催化剂层表面、排走反应生成的水以防止“水淹”发生。因编织碳布、无纺布碳纸具有很高的孔隙率、足够的导电性,在酸性环境中也有良好的稳定性,故支撑层材料主要是多孔的碳纤维纸、碳纤维织布、碳纤维无纺布、碳黑纸。碳纤维纸的平均孔径约为10.0μm,孔隙率为0.7~0.8,制造工艺成熟、性能稳定、成本相对较低,是支撑层材料的首选;在应用前需进行疏水处理,确保GDL具有适当的水传输特性,通常是将其浸入到疏水剂(如PTFE)的水分散溶液中,当内部结构被完全浸透后转移至高温环境中进行干燥处理,从而形成耐用的疏水涂层。为进一步提高碳纤维纸的导电性,可能还会进行额外的碳化、石墨化过程。
在功能角度看,GDL均匀地将反应气体从流场引导至催化剂层,确保组件的机械完整性,并以一定的速度排除阴极上的反应产物(水),防止阴极催化剂层发生“水淹”,也避免因失水过多导致阴极组件干燥而降低各离子的传导率。因此,发生在GDL上的过程有:热转移过程、气态输运过程、两相流过程、电子输运过程、表面液滴动力学过程等。GDL是燃料电池的水管理“中心”,通过对水的有效管理,提高燃料电池的稳定性、经济性;燃料电池对水的控制可以通过水管理系统的增湿器或自增湿PEM来部分实现,但主要还靠GDL的作用。
GDL的厚度、表面预处理会影响传热和传质阻力,是整个氢燃料电池系统浓差极化、欧姆极化的主要源头之一;通常以减小GDL厚度的方式来降低浓差极化、欧姆极化,但也可能导致GDL机械强度不足。因此,研制亲疏水性合理、表面平整、孔隙率均匀且高强度的GDL材料,是氢燃料电池关键技术。对GDL的研究,除了材料制备,还有关于压缩、冻融、气流、水溶造成的机械降解以及燃料电池启动、关闭及“氢气饥饿”时的碳腐蚀造成的化学降解等的性能退化研究。此外,为促进GDL材料设计与开发,研究者利用中子照相技术、X-ray电子计算机断层描绘技术、光学可视化技术、荧光显微术等手段来可视化GDL材料结构和表面水的流动状态,并利用随机模型法、两相流模型数字化重构GDL宏观形貌(孔隙)结构;为研究GDL气–液两相流行为,较多运用双流体模型、多相混合模型、格点Boltzmann方法、孔隙网络模型、流体体积(VOF)法等。
GDL技术状态成熟,但面临挑战是大电流密度下水气通畅传质的技术问题和大批量生产问题,生产成本依然居高不下;商业稳定供应的企业主要有加拿大巴拉德动力系统公司、德国SGL集团、日本东丽株式会社和美国E-TEK公司。日本东丽株式会社早在1971年开始进行碳纤维产品生产,是全球碳纤维产品的最大供应商,其他公司主要以该公司的碳产品为基础材料。
(二)双极板
氢燃料电池中的双极板(BPs)又称流场板,起到分隔反应气体、除热、排出化学反应产物(水)的作用;需满足电导率高、导热性和气体致密性好、机械和耐腐蚀性能优良等要求。基于当前生产能力,BPs占整个氢燃料电池电堆近60%的质量、超过10%的成本。根据基体材料种类的不同,BPs可分为石墨BPs、金属BPs、复合材料BPs。石墨BPs具有优异的导电性和抗腐蚀能力,技术最为成熟,是BPs商业应用最为广泛的碳质材料,但机械强度差、厚度难以缩小,在紧凑型、抗冲击场景下的应用较为困难。因此,更具性能和成本优势的金属BPs成为了发展热点,如主流的金属BPs厚度不大于0.2mm,体积和质量明显减少,电堆功率密度显著增加,兼具延展性良好、导电和导热特性优、断裂韧性高等特点;当前,主流的氢燃料电池汽车公司(如本田、丰田、通用等品牌)都采用了金属BPs产品。
也要注意到,金属BPs耐腐蚀性较差,在酸性环境中金属易溶解,浸出的离子可能会毒化膜电极组件;随着金属离子溶解度的增加,欧姆电阻增加,氢燃料电池输出功率降低。为解决耐腐蚀问题,一方面可在金属BPs表面涂覆耐腐蚀的涂层材料,如贵金属、金属化合物、碳类膜(类金刚石、石墨、聚苯胺)等;另一方面是研制复合材料BPs。复合材料BPs由耐腐蚀的热固性树脂、热塑性树脂聚合物材料、导电填料组成,导电填料颗粒可细分为金属基复合材料、碳基复合材料(如石墨、碳纤维、炭黑、碳纳米管等)。新型聚合物/碳复合材料BPs成本低、耐腐蚀性好、质量轻,是金属BPs、纯石墨PBs的替代品。为了降低BPs的生产成本以满足实际需求,发展和应用了液压成形、压印、蚀刻、高速绝热、模制、机械加工等制造方法。BPs供应商主要有美国Graftech国际有限公司、步高石墨有限公司,日本藤仓工业株式会社,德国Dana公司,瑞典Cellimpact公司,英国Bac2公司,加拿大巴拉德动力系统公司等。
(三)氢燃料电池系统部件
为了维持电堆的正常工作,氢燃料电池系统还需要氢气供应系统、水管理系统、空气系统等外部辅助子系统的协同配合,对应的系统部件有氢循环泵、氢瓶、增湿器、空气压缩机。燃料电池在工作状态下会产生大量的水,过低的水含量会产生“干膜”现象,阻碍质子传输;过高的水含量会产生“水淹”现象,阻碍多孔介质中气体的扩散,导致电堆输出电压偏低。从阴极侧穿透到阳极的杂质气体(N2)不断积累,阻碍氢气与催化剂层的接触,造成局部“氢气饥饿”而引起化学腐蚀。因此,水的平衡对PEM氢燃料电池的电堆寿命具有重要意义,解决途径是在电堆中引入氢气循环设备(循环泵、喷射器)来实现气体吹扫、氢气重复利用、加湿氢气等功能。
氢气循环泵可根据工况条件实时控制氢气流量,提高氢气利用效率,但在涉氢、涉水的环境下易发生“氢脆”现象,在低温下的结冰现象可能导致系统无法正常工作;因此,氢循环泵需要具有耐水性强、输出压强稳定、无油的性能,制备难度较大,制造成本昂贵。为此发展出了单引射器、双引射器方案,前者在高/低负载、系统启停、系统变载等工况下不易保持工作流的稳定性,后者能适应不同工况但结构复杂、控制难度大。还有一些引射器与氢循环泵并联、引射器加旁通氢循环泵方案,也有着鲜明的优缺点。2010年,美国技术咨询公司提出了一种氢循环系统设计方案,利用回流的尾气对注入氢气加湿(无需阳极增湿器),这代表了未来氢循环设备的发展方向。
氢燃料电池系统中的空气压缩机,可提供与电堆功率密度相匹配的氧化剂(空气),压比高、体积小、噪声低、功率大、无油、结构紧凑,常见的车载燃料电池空压机有离心式、螺杆式、涡旋式等类型。目前使用较多的是螺杆式空气压缩机,但离心式空气压缩机因密闭性好、结构紧凑、振动小、能量转换效率高等特点,较具应用前景。
在空气压缩机的关键部件中,轴承、电机是瓶颈技术,低成本、耐摩擦的涂层材料也是开发重点。美国通用电气公司、联合技术公司、普拉格能源公司,德国Xcellsis公司,加拿大巴拉德动力系统公司,日本丰田汽车公司等都拥有商业化的空气压缩机产品系列。
(四)系统控制策略
氢燃料电池系统的寿命或耐久性,与系统控制策略密切相关[21~23]。氢燃料电池汽车在启动时需要实时开启动力电源以获得足够的压力和反应气体;而在怠速或停止运转时,为了吹扫电堆内未反应完全的气体和产生的水,也需要开启动力电源,规避“水淹”“氢脆”、化学腐蚀等情况的出现。因此,在氢燃料电池汽车的启动/停止、怠速、高/低负载等随机性变化的工况条件下,应基于现有系统构造、燃料电池衰减机理,优化控制策略来确保负载正常工作,进而维持氢燃料电池系统燃料(氢气、空气)供应流的均匀性、稳定性、热能与水平衡。近年来,在氢燃料电池系统(如PEMFC)控制方面发展或应用了诸如模糊逻辑控制、神经网络控制、模糊逻辑–比例积分微分控制(FLC-PID)等方法,操作简单、低成本、不增加计算负担,是优化控制策略的前瞻方向。
三、我国氢燃料电池技术研发进展及重点发展方向(一)关键材料及组件研发进展
近年来,我国的氢燃料电池技术基础研究较为活跃,在一些技术方向具备了与发达国家“比肩”的条件;但整体来看,所掌握的核心技术水平、综合技术体系尚不及具有领先地位的国家,如我国在1998年才出现首个氢燃料电池发明专利,目前相关核心专利数仅占世界的1%左右。先发国家在氢燃料电池系统、组件、控制技术、电极等方面发展相对均衡,一些国际性企业在燃料电池系统、电池组件与加工、控制技术等方面居于世界领先地位(见图2、图3)。
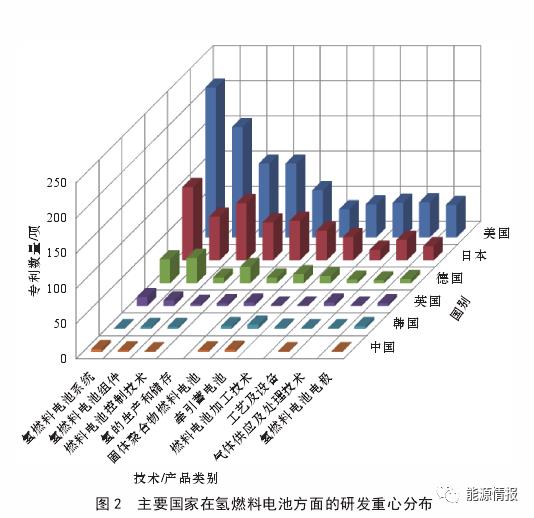
在储氢方面,高压气态储氢技术在国内外获得普遍使用,低温液态储氢在国外有较大发展,而国内暂限于民用航空领域的小范围使用。液氨、甲醇、氢化物、液体有机氢载体(LOHC)储氢在国外已有成熟产品和项目应用,而国内仍处于小规模实验阶段。催化剂、GDL等关键零部件或材料处在研究与小规模生产阶段,批量化产品的可靠性、耐久性还需要长期验证,主要技术为国外公司所掌握。中山大洋电机股份有限公司、思科涡旋科技(杭州)有限公司、上海汉钟精机股份有限公司等国内企业,均处于氢气循环泵的产品研发验证阶段,部分公司已实现小批量产品供货。碳纸、碳布是制备GDL的关键材料,基础材料是碳纤维;我国碳纤维研制从20世纪80年代中期才开始,目前尚处于小规模生产阶段,生产的碳纤维很难同时满足电堆对于低电阻、高渗透性、机械强度大等的要求,与国外高性能碳纤维材料相比仍有较大差距。上海河森电气公司、上海济平新能源科技公司均有小批量的碳纸生产能力。我国已将碳纤维列为重点支持的战略性新兴产业,相关技术在产业政策扶持下有望加速发展。
石墨BPs已实现国产化,金属BPs实现小批量供货,但耐久性、可靠性有待继续检验;相关研究单位或企业有中国科学院大连化学物理研究所、武汉理工大学、新源动力股份有限公司、国鸿氢能科技有限公司、上海弘枫实业有限公司等。上海重塑能源科技有限公司、上海捷氢科技有限公司、新源动力股份有限公司等氢燃料电池电堆供应商,产品功率达到国际先进水平,建成了自动化生产线;金属BPs电堆功率密度达到3.8kW/L,可在–30℃低温条件下自启动,完成6000h实车工况耐久性测试]。安徽明天氢能科技股份有限公司、雄韬电源科技有限公司已经建成电堆自动化生产线。贵研铂业股份有限公司、中国科学院大连化学物理研究所、上海交通大学、清华大学等从事催化剂研究,其中中国科学院大连化学物理所制备的Pt3Pd/C合金催化剂已应用于燃料电池发动机。PEM已具有国产化能力,年产能可达数万平方米,但高端产品还依赖进口。空气压缩机技术起步晚,2018年实现国产化并有小批量生产,但缺少低功耗、高速、无油的空气压缩机产品。
在产业发展方面,珠江三角洲、长江三角洲、京津翼地区涌现出了数百家氢燃料电池公司;氢燃料电池商用车(客车、叉车)已实现批量生产,燃料电池乘用车尚处在应用示范阶段。国产乘用车、商用车的电堆功率与国外产品大致相当,但系统可靠性、耐久性、比功率、综合寿命方面还需工况验证。国内一些企业掌握了氢燃料电池系统研发技术,相关产品的冷启动、功率密度等性能显著提升,具有年产万台的批量化生产能力。然而与国际先进水平相比,国产电池系统核心零部件及系统的耐久性与可靠性仍存在一定差距。
(二)重点发展方向1.关键材料与核心组件的性能及产能提升
膜电极、BPs、氢气循环泵、空气压缩机、GDL等核心组件,PEM、催化剂等关键材料,均已实现小规模自主生产,为未来大规模商业化生产储备了技术基础条件。氢燃料电池系统的国产化程度已从2017年的30%提高到2020年的60%。预计到2025年,金属BPs可完全国产化,低功耗、高速、无油的空气压缩机进入小规模自主生产阶段;机械强度高、孔隙率均匀、抗碳腐蚀的碳纤维制备技术有望取得突破,大电流密度条件下的GDL水气通畅传质问题有望得到解决。
在技术应用方面,从现阶段重点发展氢燃料电池客车、卡车等商用车,逐步推广到乘用车、有轨电车、船舶、工业建筑、分布式发电等领域。随着关键材料的物理性能改进,各组件热学、力学、电化学稳定性提高,氢燃料电池系统的稳定性、综合寿命将有明显改善。预计到2035年,燃料电池系统功率密度将由当前约3.1kW/L全面提升到约4.5kW/L,乘用车、商用车电堆寿命将由当前的5000h、15000h分别增加到6000h、20000h。
2.生产成本的显著下降
氢燃料电池系统的成本必然随着技术进步、生产规模的扩大而下降,预计未来10年生产成本将降低至目前的50%。燃料电池系统各部件的成本构成,若按照年产量为5×105套、净功率为80kW/套计算,可建立分析模型:膜电极成本占比为27%,BPs成本占比为12.4%,空气循环子系统(含空气压缩机、质量监控传感器、温度传感器、过滤器等)成本占比为25.8%,冷却回路(含高低温回路、空气预冷器、电子组件等)成本占11.2%,其他成本占23.6%。双极板和催化剂分别占整个电池电堆成本的28%和41%,而气体扩散层、电解质膜、膜电极骨架三者成本大体相当,约占电堆成本的6%~8%;各部件在系统成本中的占有比例随着生产规模和各自的技术水平而变化。该分析结果虽具有模型依赖性并建立在丰田Mirai车型数据及一些前提假设基础上,但揭示了未来提高氢燃料电池电堆功率密度、降低氢燃料电池系统制造成本的途径。应重点发展低成本、低Pt或无Pt的电催化剂,低成本、轻薄型、高性能复合材料BPs,尽快发布产业政策和技术规范,在条件成熟区域扩大燃料电池系统生产规模。
美国能源部计划在2025年实现氢燃料电池系统(功率为80kW)成本目标40美元/kW,为远期的30美元/kW目标奠定基础,进而达到与内燃机汽车的生产成本可比性。按照我国现有的技术储备条件,根据中国氢能联盟《中国氢能源及燃料电池产业白皮书》(2019年、2020年)预测,2035年我国氢燃料电池系统的生产成本将降至当前的1/5(约800元/kW);到2050年降低至300元/kW[26];届时燃料电池汽车拥有量将超过3×107辆,加氢站数量达到1×104座,氢能消耗占终端总能源消耗的10%。虽然不排除因我国研究机构与企业之间的深度协作而带来技术快速提升,到2035年氢燃料电池汽车成本将具有与内燃机汽车同等的竞争力[27]并基本接近国外先进水平,但就目前的技术状态而言,需着力提升氢燃料电池电堆材料制备和部件制造技术,大幅度降低相关系统的生产成本。
四、对策建议(一)强化制氢技术攻关,降低氢气燃料使用成本
降低氢燃料成本有利于氢燃料电池技术的推广应用,而大规模的氢燃料电池技术利用将进一步降低相关系统的成本。建议切实推动与氢燃料电池技术产业链配套的制氢、储运氢[28,29]、加氢站的发展,稳步降低氢气燃料使用成本;重点发展并应用碳捕获与封存技术,通过风能、水能、太阳能、生物质能等可再生能源,传统谷电能实施大规模绿色制氢;对标当前国际先进水平的2~3mg/cm2催化剂Pt载量、3.7美元/kg产氢成本的指标,重点采用PEM电解槽制氢技术路线,积极发展高温固体氧化物电解水制氢技术。
(二)加快关键材料和核心组件的技术攻关与转化应用
为进一步降低氢能的生产和利用成本,无论是氢燃料电池还是电解水制氢,需要大力开展碳纤维纸/布、PEM、催化剂、GDL、BPs等关键材料或核心组件的制备技术研究与转化应用。建议构建“研究机构/实验室–企业–产业园”的协同创新机制,鼓励原创的突破性研究成果进入企业开展“先行先试”,及早接受市场考验;在有条件的地区建设氢能产业园区,注重产业集群建设以形成规模化效应,从而促进氢燃料电池系统及氢气成本的技术性下降;支持自主研发企业的产品进驻氢能产业园区进行培育示范,国家级实验平台应侧重支持企业进行产品论证和工况测试。多渠道、全方位引入社会资本参与加氢站、储运氢基础设施建设,通过项目试点和示范运营,助推氢燃料电池全产业链的稳健发展。
(三)科学制定产业规划,构建政策保障体系
建议研究制定有关氢能、氢燃料电池技术的中长期发展规划,做好系统的顶层设计。关键技术的突破与创新,稳定的专业人才队伍是关键,建议在2021—2035年周期内持续设立氢燃料电池国家级专项课题,提供稳定的经费支持,鼓励氢能及氢燃料电池研究队伍倾力投入研究。合理保持对氢燃料电池产业链的投入,从土地、税收、技术标准等诸多方面给予积极支持,鼓励和引导氢燃料电池企业从事研发与产业化应用活动。有关技术标准体系的构建,是引导企业安全有序开展研发和市场活动的重要前提,建议系统研究制定加氢站等基础设施的安全标准建设文件,车辆、船舶、发电站等应用场景下氢燃料电池系统的技术和检测标准,出台法规文件缩短加氢站及氢燃料电池项目从审批、建设到运营的时间历程。
免责声明:以上内容转载自能源情报,所发内容不代表本平台立场。
全国能源信息平台联系电话:010-65367702,邮箱:hz@people-energy.com.cn,地址:北京市朝阳区金台西路2号人民日报社
相关参考
小伙伴们对电动汽车都非常熟悉,又对燃料电池的关键技术非常好奇,那我们一张图来说明其关键技术1.储氢和运氢技术2.燃料电池的电堆:膜电极(质子交换膜/催化剂/气体扩散层)+双极板+集流板+密封圈3.核心零件:控制器+空...
受到政策红利的推动,近年来氢燃料电池行业快速发展,在多家知名电堆生产商的大力支持与配合下,恒大新材的电堆粘接与密封胶业绩也得到了翻倍的增长,市场影响力及品牌知名度得到了大幅度提升。“作为国内最早参与氢...
受到政策红利的推动,近年来氢燃料电池行业快速发展,在多家知名电堆生产商的大力支持与配合下,恒大新材的电堆粘接与密封胶业绩也得到了翻倍的增长,市场影响力及品牌知名度得到了大幅度提升。“作为国内最早参与氢...
...油和柴油,无论是目前主流的动力电池路线、发展中的氢燃料电池路线都是如此。除了这两者之外,还有另外一种路线:水氢技术路线即甲醇燃料现场即时制氢与燃料电池发电高度集成路线,实际上在国内已经悄无声息的发展了...
...油和柴油,无论是目前主流的动力电池路线、发展中的氢燃料电池路线都是如此。除了这两者之外,还有另外一种路线:水氢技术路线即甲醇燃料现场即时制氢与燃料电池发电高度集成路线,实际上在国内已经悄无声息的发展了...
浙江润丰能源怎么样(燃料电池站上产业风口 2025年氢燃料电池或迎第一个拐点)
...角加\'关注\'】8月16日,氢能源概念再掀涨停潮,而作为燃料电池龙头的全柴动力(600218)今日再次涨停,股价再创新高,达成7天4板,大洋电机(002249)也已4天3板。据公司互动透露,全柴动力氢燃料电池业务目前处于研发试制...
浙江润丰能源怎么样(燃料电池站上产业风口 2025年氢燃料电池或迎第一个拐点)
...角加\'关注\'】8月16日,氢能源概念再掀涨停潮,而作为燃料电池龙头的全柴动力(600218)今日再次涨停,股价再创新高,达成7天4板,大洋电机(002249)也已4天3板。据公司互动透露,全柴动力氢燃料电池业务目前处于研发试制...
...的本田汽车与五十铃汽车1月15日表示,双方将联合研究氢燃料电池作为重型卡车动力的应用。两家公司希望将这种零排放技术应用在体积更大的车型上,从而扩大燃料电池的使用范围。两家公司表示,作为这个为期两年的合作的...
氢的环保优点(北京冬奥会重用氢燃料汽车,氢燃料电池的春天是否真的来了?)
...不少行业的发展,比如在本次北京冬奥会上被重用的“氢燃料电池汽车”。据了解,本次北京冬奥会总共运行超1000辆氢能源汽车,包括来自丰田、吉利、北汽、宇通、福田等车企的氢燃料电池大巴、小轿车、特种车等,并配备30...
日本宣布停止氢燃料电池研发(开启保守攻坚战,大众未来十年弃氢从电)
...争力,尤其是对于乘用车来说,油箱会占用机舱空间,氢燃料更加适配商用车,而非乘用车。