打包机加热线(轧材厂棒材线操作规程)
Posted
篇首语:善行无辙迹、善言无瑕谪。本文由小常识网(cha138.com)小编为大家整理,主要介绍了打包机加热线(轧材厂棒材线操作规程)相关的知识,希望对你有一定的参考价值。
打包机加热线(轧材厂棒材线操作规程)
⒈产品名称及执行标准
⒉工艺流程图
⒊原料工序
3.1原料验收制度
3.2原料挂吊与堆放工技术操作规程
⒋ 加热工序
4.1加热炉技术参数
4.2炉区设备主要参数
4.3上料与排钢工技术操作规程
4.4看火工技术操作规程
4.5汽化冷却工技术操作规程
4.6出钢工技术操作规程
5.轧制工序
5.1 轧制工艺技术参数
5.2 530轧机技术参数
5.3 1#530开坯操作工技术操作规程
5.4 530开坯机轧钢工、调整工技术操作规程
5.5 粗、中轧机技术参数
5.6 粗、中轧轧钢工调整工艺技术操作规程
5.7 2#主控台操作工技术操作规程
5.8 精轧机技术参数
5.9 精轧调整工工艺技术操作规程
5.10精轧区域技术参数
6. 集卷技术参数
5 集卷操作规程
6 PF线技术参数
7 PF线操作规程
8 打包机技术参数
9 打包工操作规程
10 卸卷技术参数
11 卸卷操作规程
⒈产品名称及执行标准
1.1产品名称:φ6.5—φ12热轧盘条;
牌号:Q195、Q2155、Q235、HPB235、HPB335、HPB400、HPB400E
1.2产品名称及执行标准:以下产品材质按国标执行,尺寸公差要求摘录如下:
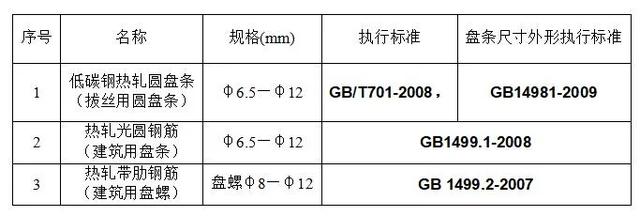
φ6.5—φ12 低碳钢热轧圆盘条(拔丝用圆盘条)产品尺寸允许偏差(GB/T14981-2009)
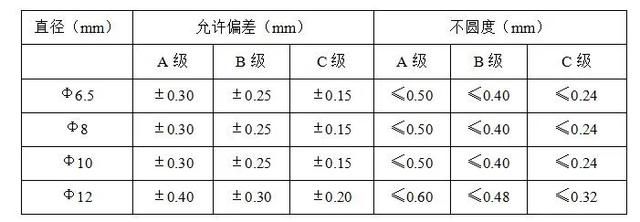
φ6.5—φ12热轧光圆钢筋(建筑用盘条)产品尺寸允许偏差:(GB1499.1-2008)
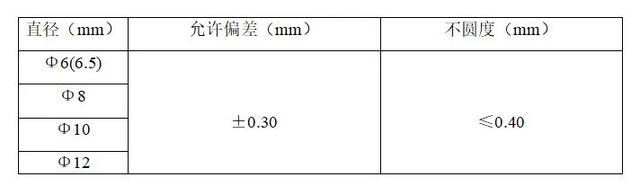
表面质量:盘条应将头尾有害缺陷切除。盘条的截面不应有缩孔、分层及夹杂,盘条表面应光滑,不应有裂纹、折叠、耳子、结疤,允许有压痕及局部的凸块、划痕、麻面,其深度或高度(从实际尺寸算起)B级和C级精度不应大于0.10mm,A级精度不得大于0.20mm热轧带肋钢筋(建筑用盘螺)产品尺寸允许偏差(GB 1499.2-2007)
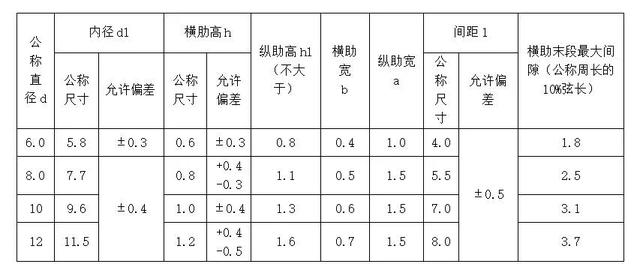
⒉工艺流程图
原料——检验——上料——入炉——加热(质量控制点)——出钢——530轧机——卡断剪——450×4轧机—1#飞剪——350×4轧机——2#飞剪——转辙器——侧活套——碎断剪 ——2#卡断剪——精轧机——水冷段——缓冷段——夹送辊——吐丝机——热检(质量控制点)——散卷冷却——集卷——PF线——打包——卸卷——挂牌入库
3. 原料工序
3.1原料验收技术标准
3.1.1连铸坯横截面为方形,边长及允许偏差为150/5cm,对角线之差不得大于7cm.。
3.1.2连铸坯长度为5700-6000mm.
3.1.3连铸坯表面不得有肉眼可见的裂纹、翻皮、结疤、夹渣,深度高度大于3mm的划疤、压疤、气孔、凸块、凹块,连铸坯端面不得有缩孔、皮下气泡。
3.1.4连铸坯的弯曲度应不影响入炉。
3.1.5 连铸坯的化学成分应符合国际标准。
3.2原料挂吊与堆放工技术操作规程
3.2.1卸料时,应按验收人员指定的地点堆放整齐。
3.2.2每堆原料应为同一钢种、同一炉(批)号的原料,不得混号堆放。
3.2.3当两个或两个以上的炉(批)号原料堆放在一起时,应为同一钢号,不得混钢号堆放。
3.2.4同钢号、不同炉号的原料堆垛时,炉(批)号之间应有明显的标记,严禁隔开堆垛。
3.2.5堆垛要整齐,垛基要平稳,呈“井”字形堆放,垛高不得超过2米,垛间距离不得少于1米,钢垛离厂房边柱不得少于1.5米,钢料堆好后应在侧面做好钢号、炉(批)号标志。
3.2.6卸车挂吊时,严禁超过吊盘宽度或超重挂吊。
3.2.7原料转堆时,应按原料验收人员编制的转运单进行转运,不准擅作主张,转错钢号或炉(批)号。
3.2.8监督上料工执行按炉(批)号送钢制度。
4. 加热工序
4.1加热炉技术参数
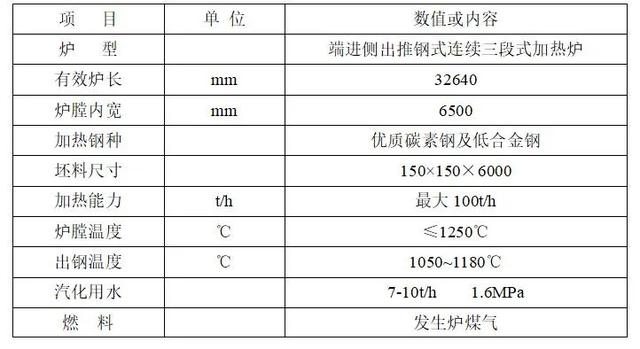
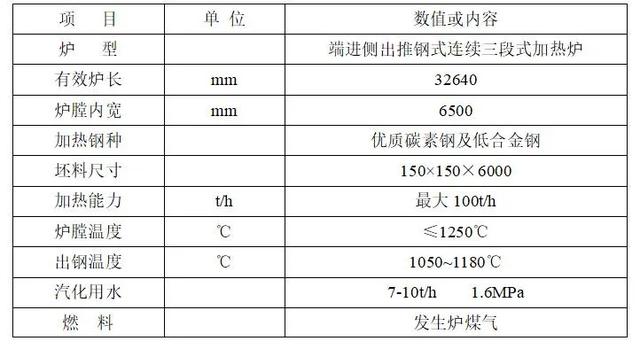
4.2炉区设备主要参数
4.2.1输送辊道技术参数:辊道辊子直径:Ф300
辊道辊子长度:1000mm(35个)+1500mm(7个)
辊道辊子间距:1000mm/1500mm
辊道辊子线速度:556mm/s
辊子数量:42个
总长度:44.3m
4.2.2推钢机技术性能:
推力:1800KN 推程:1350mm
推钢规格:150-170方坯,L=6000mm
液压缸:320/220X1800
额定压力:16MPa
工作压力:14MPa
4.2.3出钢机技术性能:
型式:压轮顶杆式
电机型式:
1)推杆顶钢用:YZR225M-6 22KW
2)水平移动用:YZR160l-6 11KW
减速机:推杆用 ZQ400—I i=15.75
水平移动 ZQ350—I i=48.75
推杆推速: 0.852m/s
横移速度: 92㎜/s
行程: 4.5m
出钢次数: 6次/分
4.2.4出炉辊道技术性能:
辊道辊子直径:Ф300
辊道辊子长度:1000mm
辊道辊子间距:772mm
棍子数量:10个
辊道辊子线速度:820 mm/s
4.3上料与排钢工技术操作规程
4.3.1必须严格执行“按炉送钢制度”,按原料验收人员指定的钢号、炉(批)号顺序上料。
4.3.2上料前,按原料输送单或原料平衡卡对照实物,核对钢号、炉(批)号、吊数、支数,当实物与卡片相符时,方可上料,若实物与卡片不符,应找原料验收人员查清原因。
4.3.3装炉前必须检查钢坯质量,不得有烂头或超长。对超长或存在烂头的钢坯,切割后进炉。对龟裂、变形、缠孔明显的应及时吊走另外堆放,不准随意挑出或不处理就进炉。把好原料进炉关。
4.3.4同一炉号的钢坯必须连续进炉,不得漏钢进炉。更换炉(批)号时,要在最后一根钢坯放置实物作为标记。
4.3.5排钢要整齐规则,对有弯曲的钢坯,应使钢坯弯曲方向朝上或面向炉前,保证钢坯在炉内走正,使钢坯两端与炉墙保持相等或大于150—200㎜的距离,以免刮炉墙。
4.3.6排钢后应将出钢信号及时发给出钢操作台,以便及时出钢。
4.3.7严格执行进炉操作规程,注意观察设备的运转情况。
4.4看火工技术操作规程
4.4.1根据不同钢种、不同原料规格及实际轧制节奏调节温度,对钢坯进行加热,保证开轧温度,避免过热、过烧、脱碳等加热缺陷出现。
4.4.2正常轧制时,严格执行规定的热工制度:
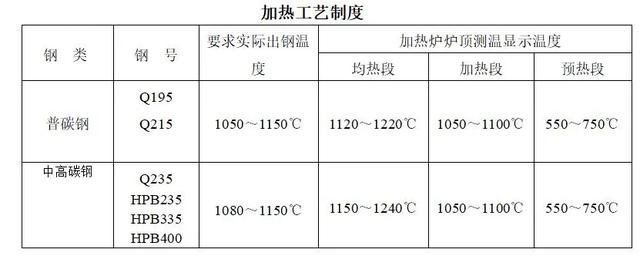
注:加热炉温度分别为均热段、加热段、预热段炉墙温度
均热段温度—指出钢槽部位炉顶热电隅温度。
加热段温度—指腰炉炉顶部位热电隅温度。
预热段温度—指炉尾炉顶部位热电隅温度。
4.4.3在正常生产时,炉温不允许大幅度波动,上下限范围为±30℃,最高炉温不得超过1320℃(极限)。
4.4.4为消除阴阳面,下加热温度应略高于上加热温度,但上、下温度差不得超过±50℃。
4.4.5根据燃烧情况和工艺要求调整煤气、风量和烟道闸门的开启度。
4.4.6正常生产时,除出钢炉门外,其它炉门、看火孔都严密关闭,防止冷空气吸入炉内。
4.4.7根据加热仪表的指示和记录进行操作,如仪表发生故障应及时通知有关人员修理。
4.4.8注意检查风、煤气、水冷系统及炉子的工作情况,发现问题及时处理。
4.4.9定期消除炉渣,清渣后及时在炉底均匀地铺加一层50—60㎜厚的镁砂。
4.4.10严格执行加热工艺技术操作规程,经常与汽化工保持联系,沟通运行情况。
4.5汽化冷却工技术操作规程
4.5.1启动操作
4.5.1.1检查汽包、水泵、抽水泵、水箱、水位压力表、安全阀、主汽阀等设备是否处于正常状态。
4.5.1.2用软水冲洗炉筋管15—20分钟,然后关紧排水阀,继续注入软水,使汽包保持正常水位,方可通知看火工点火开炉。
4.5.1.3随着炉温升高,汽包不断补水,保持汽包正常水位(汽包直径的1/2,波动为±50㎜),待汽包压力上升到所需压力时,打开主汽阀,进入正常工作状态。
4.5.2正常运行操作
4.5.2.1经常观察汽包和仪表的运行情况,注意上升管有无明显的摆动和水柱声,发现异常现象及时处理,汽化运行时,值班室不得离人。
4.5.2.2汽包工作压力控制在指定的工作压力以内,水位保持在正常的工作水位,水箱水位保持在2/3以上。
4.5.2.3安全阀每班放汽一次,定期排污阀每四小时一次。连续排污每班观察一次,并检查各阀门是否灵敏。
4.5.2.4每周开启蒸汽泵1—2次,每周检查水质一次,严禁汽包用硬水代用软水。
4.5.2.5经常检查汽包、管道的运行情况,对照汽包压力表和水位表与操作室的指度是否一致,发现问题,及时和有关人员联系、汇报并处理,特别是软水供应不及时,应及时反映当班领导,采取紧急措施。
4.5.3停炉期间的操作
4.5.3.1停炉期间,首先关闭蒸汽输出阀,尽可能保持汽包的正常工作压力。
4.5.3.2炉膛温度降至100℃时,方可停止向炉筋管内供水。
4.5.3.3经常与热工联系沟通生产、运行情况,注意本岗位的设备运转是否正常。
4.6出钢工技术操作规程
4.6.1出钢操作应严格按“按炉号送钢制度”执行,必须要得到要钢信号方可出钢,并注意观察钢坯的出炉温度,使之符合加热规程规定。
4.6.2出钢时,观察钢坯是否在出钢槽中心,以免顶出钢口炉墙发生故障,影响正常生产。
4.6.3发现炉内钢坯走斜要及时通知有关人员,查明原因,及时处理。
4.6.4要钢信号消失要立即停止出钢。
4.6.5推钢杆有弯、抬头、漏水等出钢不顺时,应立即通知有关人员检修处理。
4.6.6注意观察更炉(批)号的标记,做好出钢坯支数的记录,核实炉(批)号支数与出炉情况是否相符,并通知有关人员做好成品的隔号工作。
4.6.7生产不正常检修时,应关闭出钢口,以防冷空气吸入炉膛内,造成黑头钢,影响生产。
4.6.8常检查推钢杆内循环水的流量、压力。
5.轧制工序
5.1轧制工艺技术参数
5.2 530轧机技术参数
型式:三辊开坯轧机
轧辊公称直径:φ530×1800mm
轧辊最大直径:φ600mm
轧辊最小直径:φ530mm
轧辊轴径:φ300mm
轧辊转速:81.55r.p.m.
轧机最大轧制压力:1500KN
公称轧制速度:2.79m/s
减速速比:i=170/27=6.07
减速机低速轴需用最大输出扭矩:400KN.m
5.3 1#530开坯操作工技术操作规程
a) 操作前仔细检查设备及按扭、开关、操作手柄、信号灯、指示灯等装置是否正常。
b) 启机后检查机前辊道、升降台、机后输送辊道运转是否正常。
c) 按设备工作制度正确操作轧钢区域的设备。
d) 启动主机应先得到供油信号的正常指示,油位压力达到压力值后,方可开启主机。
e) 启动主机不得带负荷启动,未开启水闸严禁开启主机。
f) 主机在30分钟内连续启动不允许超过三次。
g) 根据主控台的信号指示情况,给出钢工发出要钢信号或停止出钢的指示。
h) 听从轧钢调整工的指挥,配合协调,掌握好轧制节奏。
i) 轧制过程中,严禁一、三道,二、四道同时过双杠,对错误的指挥有权阻止,及向上级有关领导反映。
j) 精心操作,严禁轧制低温钢、烂钢、黑头钢,控制轧钢节奏。
k) 严格执行轧钢工艺技术操作规程。
5.4 530开坯机轧钢工、调整工技术操作规程
5.4.1开坯机轧钢工、调整工负责开坯机的正常轧制,保证进入粗轧的轧件外形,及尺寸符合工艺要求的正确性。
5.4.2根据工艺设计要求,正确调整各道次的孔型高度,正确安装各道次卫板,架梁的高度,保证轧件顺利通过。
5.4.3轧制过程中,发现烂钢、裂纹等有明显缺陷的应停止轧制,及时处理,公差尺寸合格的方可送入粗轧机组。
5.4.4观察红钢的温度情况,不符合温度的钢不得入轧机,及时将低温度的钢吊离辊道严禁轧制低温钢。
5.4.5随时观察各道次的冷却水浇槽情况,严禁在无冷却水的情况下轧制,确保轧件无明显变化。
5.4.6经常检查上下调节装置是否灵活,上辊吊杆的松紧度中辊H架的稳定,及各胶瓦台的磨损情况,确保轧件无明显变化。
5.4.7观察翻钢板升降台的启动装置是否到位,保证轧件顺利通过。
5.4.8轧制中要观察,量检查轧件的外形尺寸,发现孔型磨损严重或有其它缺陷时,及时反映有关人员和部门,得到允许后及时进行更换。
5.4.9轧制过程中轧辊轴向窜动不得大于2.0mm.(毫米),如发现轴向窜动或上下跳动厉害时,应及时调节轴向调节器的松紧度,避免瓦光的磨损。
5.4.10 有关操作台密切配合,保证轧制顺利进行。
5.4.11 严格执行轧钢工艺操作规程。
5.5 粗、中轧机技术参数
5.5.1、1#450机列:
复合减速箱人字齿轮轴中心距:500mm
总速比:i=23.8277 i=23.8277
电机型号:Z560-2B 功率:619KW 转速:285-600r/min
轧辊辊身长度:800mm
注:轧机最大轧制压力:2000 KN 最大轧制力矩:2*100 KN.m
复合减速箱所需供油量:≥210L/min
设备冷却水所需供水量:≥60t/h
万向联轴节:按照QPA4651-4-0定货图定购
5.5.2、2#450机列:
总速比:i=7.4324 i=5.0
电机型号:Z560-2B 功率:619KW 转速:285-600r/min
轧辊辊身长度:800mm
注:轧机最大轧制压力:2000 KN 最大轧制力矩:2*100 KN.m
复合减速箱所需供油量:≥210L/min
设备冷却水所需供水量:≥60t/h
万向联轴节:按照QPA4651-4-0定货图定购
5.5.3 、1#350机列:
总速比:i=4.5523 i=3.36 电机型号:Z560-2B 功率:610KW 转速:450-800r/min
轧辊辊身长度:650mm
注:轧机最大轧制压力:650KN 最大轧制力矩:30KN.m
复合减速箱所需供油量:≥210L/min
设备冷却水所需供水量:≥60t/h
万向联轴节:按照QPA定货图定购
5.5.3 、2#350机列:
总速比:i=1.6111 i=1.2889 电机型号:Z560-2B 功率:610KW 转速:450-800r/min
轧辊辊身长度:650mm
注:轧机最大轧制压力:650KN 最大轧制力矩:30KN.m
复合减速箱所需供油量:≥210L/min
设备冷却水所需供水量:≥60t/h
万向联轴节:按照QPA定货图定购
5.6 粗、中轧轧钢工调整工艺技术操作规程
5.6.1粗、中轧调整工负责K21至K9轧机的正常轧制,负责保证各自的轧机轧件在外形尺寸符合工艺要求,以确保顺利进入精轧机组。
5.6.2正常轧制前,必须逐架次测辊缝、试小科,待科型确定后,方可轧制坯料。
5.6.3手动压下的压下量,根据各自的轧机型号的不同,压下量不同调整压下时,应多加注意避免出现推钢故障。
5.6.4正确调整各架次的孔型高度及孔型尺寸,细心安装各架次的进出导卫,保证轧制线一致。
5.6.5注意观察各机组之间的堆拉关系,观察科型的变化,经常与2#主控台的沟通了解,最佳的转速匹配,保证轧件的通条一致。
5.6.6经常观察各使用槽的冷却水供应情况,严禁在无冷却水的情况下轧制钢坯。
5.6.7巡回检查设备的运行情况,注意导卫装置是否松动磨损严重,发现此类情况应及时紧固,调整或及时更换,保证各道次的轧件质量。
5.6.8换辊后,根据辊径的变化,及时通知主控台调整转速,做到料过开水,以免使用槽出现裂纹。
5.6.9注意观察1#切头剪得切头、切尾长度,根据工艺要求调整,也可根据原料情况,规格品种的变化做相应调整。
5.6.10发生故障进行处理时,手势、信号要明确,精轧出故障时1#切头剪、卡断剪、事故剪应同时启动,严禁闯红灯,以防人身设备事故的发生。
5.6.11出现堆钢事故,废钢应及时清理出生产线,避免影响再生产线的正常轧制
5.6.12严格执行轧钢工艺技术操作规程
5.7 2#主控台操作工技术操作规程
5.7.1:粗.中轧技术操作规程
5.7.1.1 2#主控台是负责粗.中轧机组及1#切头剪.2#切头剪.自由活套套量的控制。侧活套套量的控制。以及其他辅助设备的开启.停止和各机架间速度匹配的控制台。
5.7.1.2操作前仔细检查各按扭.开关,及各架机组的转速情况和其他设备的工作情况.认真分析电脑画面情况.并了解上一班生产情况。如有问题及时处理,或上报有关人员处理。
5.7.1.3开启主机前应先通知油泵站.水泵站开启,得到信号指示后 ,查看供油.供水情况后,方可启动,严禁带负荷启动。
5.7.1.4熟练调节各机架间的转速及掌握自由活套的套量,南线北线走钢的情况,保证轧制能顺利进行
5.7.1.5经常观察电脑画面所显示的转速数据,作好原始记录。
5.7.1.6在轧制过程中出现异常故障,自动失控时,应改为手动调节转速与活套量的大小,和手动碎断1#剪。2#剪。发现跑钢伤及设备的情况下。应对运行的设备采取保护措施,停止运转。
5.7.1.7与各操作台始终保持工作联系,配合轧钢工的工作。
5.7.1.8严格执行“按炉送钢制度”,换炉号时应及时将新.旧炉号通知后区操作台及有关人员,以免混炉号。
5.7.1.9设备停止运行或发生停电事故时,应立即关闭主画面开关.控制器.按扭等,置于零位,并及时将情况告知相关人员和其他操作台人员,避免发生人身.设备事故。
5.7.1.10严格执行工艺技术操作规程。
5.7.2 精轧机区域技术操作规程
5.7.2.1精轧机操作对象主要是:精轧机组,南线、北线和吐丝机夹送棍的开启控制和夹送棍、吐丝机转速的匹配。
5.7.2.2启动主机时,必须分清调整工的手势,看清南线北线的工作情况,待发出开机信号后,方可开启主机按扭。
5.7.2.3精轧主操人员必须配合精轧调整工检查活套起落情况,2#飞剪及碎断功能情况及光电管检测机构的灵敏度和工作情况。
5.7.2.4精轧的线速度,在更换品种和辊径改变后,夹送棍、吐丝机的转速同时要做相应的调整,保证线速度一致。
5.7.2.5精轧操作工必须认真观察过钢情况,发生堆钢、跑钢、自动装置失控时,应采取手动,和人工碎断,以免飞钢伤人。
5.7.2.6主控台操作人员必须认真记录好电流和转速,同时记录工作情况。作好工艺原始数据的记录,对口交接班。
5.7.2.7做好工艺数据的保密工作,外来人员一律不得入内。
5.7.2.8严格执行工艺纪律和技术操作规程
5.8 精轧机技术参数
5.9精轧调整工工艺技术操作规程
5.9.1精轧机是高线车间的关键部位,技术要求工艺纪律比其它机组有明显区分,时刻保持高度警戒。
5.9.2调整工首先应准备好精轧机所需要的卡尺、样棒等专用工具,熟悉掌握各项操作要求。
5.9.3调整工在预调各架次的进口滚动导卫时,首先用样棒插入导轮之间,使两滚轮能够轻松转动松紧度正常为止。
5.9.4开机前必须检查各架次的导卫,如有松动磨损严重及时调整紧固更换为止。
5.9.5开轧前启机应先开水后启机的原则,同时检查浇槽水管通水情况及钓鱼线的松紧度,轧前关闭大罩。
5.9.6调整工一定要熟悉轧制程序表,掌握相关的红坯尺寸及辊缝的参数,以便正确调整,确保精轧机组堆拉关系。
5.9.7注意水压、油压在正常轧制下的变化情况,保证精轧机组设备的正常运转。
5.9.8安装后的进出口导卫必须保证轧制线一致,进出口不得于轧辊相接触而间隙又不能过大。
5.9.9精轧调整工应对精轧机前后的热金属检测器和检测装置,起套装置等设备进行检查,让其处在正常工作状态。
5.9.10经常与主操作人员保持工作联系,时刻掌握2#飞剪及碎断剪及其他辅助设备运转情况,发现问题及时解决。
5.9.11更换品种,辊径改变后,应及时与主操作人员沟通情况,以便及时调整轧机转速及吐前夹送辊、吐丝机转速,使盘卷顺利通过芯杆。
5.9.12正常轧制时,注意观察卡量前方来料及侧活套套量的延伸情况,常与中轧调整工保持联系,正确调整料形,保证中轧预精轧的轧制速度。
5.9.13时刻观察精轧与加送辊的速度,加持的变化、穿水压力、流量的变化,保证成品的温度控制在工艺要求的范围之内。
5.9.14调整工必须保证成品质量,按国标轧制。
5.9.15密切注意前后信号灯和工友之间的各种手势,及时处理发生的各种问题。
5.9.16为保证成品质量,要做到:一观察、二卡量、三调整原则,确保成品通条一致。
5.9.17出现成品孔后堆钢故障时,应对穿水.吐前夹送 .吐丝机同时检查,避免二次堆钢。
5.9.18保证成品出口与跑槽.穿水器.引线跑槽在同一轧制线和水平线上。
5.9.19更换品种规格时,同时对穿水引线管.及夹送辊辊缝相应调整.,保证轧制顺利。
5.9.20严禁轧制低温钢.黑头钢。
5.9.21严格执行工艺技术操作规程。
5.10 轧件尺寸的检查
轧件尺寸的检查包括轧件高度、轧件宽度及轧件形状。
5.10.1机组末架出口轧件尺寸的检查
轧件的高度尺寸可通过测量切头(尾)直接获得准确的尺寸。
轧件的宽度尺寸因头尾自由轧制无张力,同时温度偏低,一般测头尾尺寸时,尺寸均较大,仅供参考。为获取较准确的轧件宽度尺寸,可让主控台操作工利用飞剪碎断功能切取一段较长轧件,并测量远离尾部的宽度尺寸。为避免堆钢事故的发生,应尽量少使用“碎断功能”,可以采用轧件头部多切几次来获取准确的尺寸钢样。
测量冷轧件尺寸时应乘上1.013倍(热膨胀系数)为轧件热尺寸。
5.10.2中间道次轧件尺寸的测量
由于粗轧机轧速低,可用外卡钳在线测量运动中的热轧件。
可以用木片烙印运动中的热轧件,根据烙印的形状,观察轧件在孔型中充满程度,从而估算出轧件宽度。
调整工在生产过程中逐步积累观察轧机辊缝的能力,从而判断轧件充满程度,堆拉状态。
5.10.3轧件高度尺寸及宽度尺寸的调整
开坯轧机末架轧件尺寸精度控制范围 -1.0mm~+1.5mm。
中轧机末架轧件尺寸精度控制范围 -0.5mm~+0.5mm。
机组末架轧件高度尺寸超差两种情况和原因。
第一种是轧件中间高度尺寸与头尾尺寸变化不大,在正常范围内波动,只是在轧件通条长度上普遍过大或过小,此种情况与张力关系不大,而产生的原因与各道次高度尺寸有关,应着重调整各道轧件的高度尺寸,即调整辊缝。
第二种是轧件头尾尺寸合适,而中间尺寸过小。由其轧件宽度尺寸过小,此种情况与轧件高度设定关系不大,而主要是机架间存在张力有关,应着重调整张力,使机架间达到理想的张力状态。
轧件高度尺寸与辊缝调节
换辊换槽后,引起高度尺寸变化的主要原因是孔型磨损。因轧槽磨损而使孔型高度尺寸增加。轧件高度尺寸增大,要保证轧件的设定尺寸,就必须采用辊缝补偿调节,以保证各道次轧件尺寸的相对稳定。
d、机架间张力的判断及调节
机架间张力的大小可直接由主控台通过电机负荷电流的变化来判断。当轧件咬入第一架轧机后,电流值为a值。若轧件咬入第二架轧机后电流值保持不变,则无张力。当电流值发生变化,如小于(或大于)a值,则表明一、二架之间存在拉钢(或堆钢)。
台下可以通过观察辊缝宽窄变化来判断机架间拉钢或堆钢轧制。
调节张力的主要方法是调整轧机的转速,严禁又调转速,同时又调辊缝,两项调整同时进行将造成调整的混乱。
调整张力应首先从第一架开始,逐架向后调整。
中轧机一拖二机架间张力由工艺设定,只能采用辊缝调整补偿,相邻机组调节张力采用调整转速。
调整工要加强与主控台信息联系,上下协调配合。
5.10.4 预精轧、精轧机轧制过程的调整操作
5.10.5 预精轧、精轧调整工接班后应立即备好所用工具,仔细查看上班生产记录,了解上班生产质量及设备运行状况。
5.10.6观察预精轧机立活套起套状态及精轧机各轧机间的堆拉状态。
5.10.7 对上班精轧成品头部、中部等取样,同时对预精轧末架轧机来料进行取样观察和测量。并要将测量数据做好记录,为本班精轧机调整做好工艺准备。
5.10.8调整工应认真检查各架轧机入口、出口导卫情况,如有松动或磨损严重,应立即紧固或更换,预调整滚动导卫时,也可用样板或试棒捅入两滚轮之间孔型,使两滚轮转动而又不紧为止。
5.10.9检查轧辊,导卫冷却水系统(水量、水压)等是否正常,如发现异常情况,应及时向轧钢班长报告,及时组织处理。
5.10.10 精轧机调整工是全轧线的总调整工,粗轧、中轧、预精轧调整工必须服从总调整工的指挥,确实做到粗轧满足中轧,中轧满足预精轧,预精轧满足精轧,确保轧线工艺顺行。
5.10.11 开轧后,精轧工取第一根钢的头部第二圈后一段样,中间一段样进行测量,第一根钢受钢温、调速影响较大,一般仅供参考。但可以预测精轧机微调整的方向。如发现倒钢、耳子、折叠等现象,应立即亮红灯进行调整。
观察第一根钢预精轧立活套起套状态及精轧机各机架间的堆拉关系。
前五根钢要求逐根取样,一般要求头部+中部,中部+尾部,头部+尾部,中部等,应视第二根检查或具体情况而定。
根据成品尺寸的检测状况对精轧机、预精轧及上游轧机进行辊缝调整或进行速度调整。
开轧正常后,半小时内要求十分钟取样一次,并视具体情况决定取样部位。
正常过钢后精轧取样规定,每小时取样一次,一般取样部位为头尾各一样,长度200~300㎜;更换成品入口导卫后取样一次,取样部位为头、尾部;机架收料后,取样1~2次;发现成品尺寸有波动时,取样次数视具体情况而定;精轧操作工间隔1小时到打包处检查成品外观、头、尾、尺寸状态等情况。
5.10.12 正常过钢时,调整工要注意观察水平活套的运行状态,及来料红坯尺寸、温度,并与预精轧、中轧调整工及时联系。
5.10.12 注意观察精轧机、夹送辊、吐丝机之间的堆拉状态及吐丝机吐圈情况,有异常情况及时调整。
5.4.13 精轧机如果发生堆钢,要求记录机架的红坯尺寸。
5.4.14 精轧对成品质量的责任。
Φ6.5线材:Φ6.5(-0.3+0.1)成品尺寸按Φ6.4控制;
Φ8.0线材:Φ8.0(-0.3+0.1)成品尺寸按Φ8.0控制;
Φ10线材:Φ10(-0.3+0.1)成品尺寸按Φ10控制椭圆度应小于0.4㎜。
注:成品机架:Φ6.5-K1 Φ8-K1甩18、19架;
Φ10-K3甩18、19架
头部带耳子不得超过2圈,尾部带耳子不得超过1.5圈。
成品不允许出现单边耳子和因充填过满而出现微带耳子。
成品不允许有严重的周期性压痕。
成品不允许有折叠、裂痕、耳子、结疤、分层及夹杂等缺陷。
不允许有大面积或局部严重翘皮,当发现时,应及时通知相关人员,确认是否上游轧机挂丝造成的,确认后要立即组织处理,消除缺陷。如果是原料问题,检查员应对产品进行跟踪监控,并做好原始记录。
交接班或检修等停工,开机前必须认真检查,机间导卫引线导管等是否有障碍物。
6. 集卷技术参数
集卷圈径 850—1250mm
集卷重量 2×1060Kg
双芯棒翻转周期 120s
双芯棒有效长度 3570mm
盘条托盘行程 3480mm
托举油缸(共3个) φ80/45×570
双芯棒旋转角度 180º
双芯棒旋转中心线倾斜角 45º
7. 集卷操作规程
7.1操作人员必须熟悉各操作按钮功能,操作熟练准确。
7.2操作人员必须熟练掌握机械设备运转的先后秩序及设备连锁原理及目的。
7.3开机前检查设备、液、气、电控是否正常,并对设备进行空负荷状态下的自动运行试验不少于次。设备上好挂有“检修”牌或前一工位没有信号灯,禁止试车。
7.4双芯棒操作顺序:
A 芯棒处于竖直位(B芯棒处于水平位)→接收托板上升到顶部→关上仓门→集卷头摆臂摆出(鼻锥落下)→拨托爪收回(盘条落下)→开始收料→接收托架缓慢下降→接受托板走到底位→集卷头摆臂摆进(线卷收集完毕、鼻锥提升)→托爪闭合→打开仓门→A芯棒旋转到水平位(B芯棒处于垂直位)结束一个收集过程
7.5系统工作中,操作人员要兼顾生产线前后工位的工作情况,注意工位之间的相互协调与配合。
7.6正常情况下,集卷站处于自动工作状态,操作人员应密切注意设备的动作情况和顺序,在设备出现误动作的情况下,应及时采取有效的措施,防止设备事故的发生。
7.7生产结束时,确认散冷辊道停机后,方可关机,关闭操作台电源及工作信号灯。
7.8下班断开操作台所有电源,打扫卫生。
7.9生产过程中,如有特殊情况,应先按急停按钮,保护设备,并上报有关部门组织检查。
8. PF线技术参数
9. PF线操作规程
9.1、操作本系统的工作人员应经过专门培训,并对系统各部位的位置、功能、操作方法、急停应急措施等有详细的了解和认识;
9.2、操作设备前应仔细检查系统周围及系统运行通道内有无妨碍系统运行的障碍物存在,对检修后的设备还必须对各部位进行检查,在确认链条无卡阻、各气动系统正常、各信号联锁无误后方可启动设备;
9.3、一般情况下,系统应置于自动状态,只有在打捆工位或系统出现需人为处理的情况下,才将系统操作置于手动;
9.4、无论系统处于何种状态,设备操作人员必须精力集中,对设备的运行状况进行密切监视,确保系统的安全运行;
9.5、手动对设备进行操作时,应严密监视物料运行工况,并与设备周围的作业人员作好配合;
9.6、系统各部位均设有紧急停车按钮,操作人员在紧急情况下,应使用最近的紧急停车按钮,以防事故的发生;
9.7、系统检修或停机时间较长时,操作人员应切断系统电源、收回各机旁操作箱钥匙,并通知电器维护人员在总电源刀闸上挂牌警示;
9.8、系统操作箱应经常保持清洁,严禁将潮湿物品置于操作箱等电器设备上;
9.9、系统出现严重的故障报警、系统故障时应及时通知专业维修人员进行处理。
10、打捆机技术性能:
盘卷圈径 850—1250mm
打捆重量 2×1020Kg
最大压紧力:384KN
压紧力:90——180KN
盘卷温度:350℃-450℃
设备最大开口度:4700mm
打捆头电机减速机:X90L-4,5-4-1.25 功率:1.5Kw
转速:1500r.p.m. 减速比:
11、打捆机操作规程
11.1设备使用前应检查液压执行元件、管路、接头是否有泄露点,系统压力是否在规定的范围内。
11.2检查各滚轮、转轴部位的润滑是否良好,运行轨道范围内无妨碍设备运行的障碍物。
11.3将操作手柄置于手动位置,分别对升降、压紧、桥臂、打捆头装置等进行空负荷动作试验三次以上,确认无误后投入自动状态。
11.4对自动状态下的设备进行空负荷动作试验,所有动作程序应与实际工况相同,且打捆机与其他设备的连锁、信号交换系统正常、准确。
11.5一切正常后,方可发出允许进钩信号,并提醒打捆操作人员注意安全。
11.6工作中,设备操作人员应与打捆操作人员密切配合,监视好设备运行。
11.7凡本设备运行及与打捆机配合使用设备在运行中出现的不正常动作和异常噪音,操作人员应采取相应措施,及时通知相关维修人员进行处理。
11.8设备运行中严禁任何人进行设备维护和设备的参数调整。
11.9保持设备及其周围的清洁卫生。
12、卸卷机技术性能:
盘卷尺寸:Φ850/Φ1250mm
单个盘卷重量:2040Kg
盘卷托架盛卷数量:2卷
卸卷周期:84s
小车速度:V升=100mm/s V降=200mm/s V压紧=200mm/s V松开=200mm/s V横移=12-24m/min
升降液压缸:Φ80×600 行程:600mm
推板气缸:Φ140×1050 最大行程1050mm
配用电动机: 型号:YD100L- 功率:1.5Kw
转速:1500r.p.m.
减速机: 型号:BW-22-43 减速比:43
13、卸卷机操作规程:
13.1本设备正常工作时为自动工作状态,进入卸卷工位的盘卷按照预先设定的程序进行工作。
13.2卸卷程序为:盘卷进入卸卷工位→小车自等待位后退到接卷位→升降装置升起将盘条托离C型钩→行走小车将盘卷送至卸卷位→升降装置下降落卷→行走小车后退至等待位→检测元件发讯允许C型钩进出。
13.3盘卷高度小于600mm时,自动卸卷功能失效,此时应手动操作,将进入工位的盘卷卸下。
13.4设备正常工作前,应检查气动和液压执行元件、管路、接头是否有泄露点,系统压力是否在规定的范围内。
13.5检查链条及各滚轮、转轴部位的润滑是否良好,运行轨道范围内无妨碍设备运行的障碍物。
13.6将操作手柄置于手动位置,分别对升降、推进、小车行走装置等进行空负荷动作试验三次以上,确认无误后投入自动状态。
13.7对自动状态下的设备进行空负荷动作试验,所有动作程序应与实际工况相同,且卸卷机与其他设备的连锁、信号交换系统正常、准确。
13.8一切正常后,方可发出允许进钩信号。
13.9工作中,设备操作人员应监视好设备运行状况,并对C型钩在前后轨道的数量进行合理分配,以免影响生产。
13.10凡本设备运行及与卸卷机配合使用设备在运行中出现的不正常动作和异常噪音,操作人员应采取相应措施,及时通知相关维修人员进行处理。
13.11设备运行中严禁任何人进行设备维护和设备的参数调整。
13.12保持设备及其周围的清洁卫生。
更多精彩内容,尽在【云轧钢】公众号。
相关参考
⒈产品名称及执行标准⒉工艺流程图⒊原料工序3.1原料验收制度3.2原料挂吊与堆放工技术操作规程⒋加热工序4.1加热炉技术参数4.2炉区设备主要参数4.3上料与排钢工技术操作规程4.4看火工技术操作规程4.5汽化冷却工技术操作规程...
1、冷床1.1.作用:对轧后倍尺进行加速、制动、并送入冷床冷却、编组,保证冷床上的倍尺平直且一端对齐。1.2.设备组成及特点冷床区输入辊道长200米,输入辊子数量146个,间距1.2米,线速度3~23米/秒,辊道电机变频调速;输...
...发挥生产潜能,增强企业经济效益的目的。1概述三钢棒材厂始建于1992年,1995年底开始投入生产,设计年产∮12-40mm螺纹钢筋和光面圆钢30万吨,生产原料为150*150*8000mm连铸小方坯,采用热装
三、概念题1、连轧——一根轧件同时通过几架轧机,并保持在单位时间内轧件通过各轧机的体积相等的轧制为连轧。2、轴承寿命——轴承在一定转速下的工作小时数称为轴承寿命。3、全连续轧制(无头轧制)——全连续轧制就...
...发挥生产潜能,增强企业经济效益的目的。1概述三钢棒材厂始建于1992年,1995年底开始投入生产,设计年产∮12-40mm螺纹钢筋和光面圆钢30万吨,生产原料为150*150*8000mm连铸小方坯,采用热装
摘要:介绍了攀钢金属制品有限公司棒材生产线提高定尺率的生产实践,通过控制加热炉氧化烧损、负偏差精度及切分规格线差控制、倍尺剪切精度提升、齐头棍道改进、各规格钢坯定长等措施,棒材定尺率由最初平均约96%〜97%...
电焊工安全技术操作规程 第1条:电焊、气割,严格遵守”十不烧”规程操作。 第2条:操作前应检查所有工具、电焊机、电源开关及线路是否良好,金属外壳应有安全可靠接地或接零,进出线应有完整的防护罩,进出线端应用...
一、万能试验机操作规程1、接通总开关电源。2、估计测量范围,将摆铊挂在摆杆上,并调整缓冲阀手柄,对准标线。3、开动油泵电机,拧开送油阀,使试台升高10mm,然后关闭油阀。4、开动油泵电机,调整指针对准刻度盘零点...
成都海尔电器维修(海尔洗衣机全国服务热线电话2022已更新(24小时售后服务热线))
海尔洗衣机全国服务热线:400-1535-118(客服中心)在维修操作过程中,严格按维修*及操作规程执行,确保维修质量。在收费方面,严格按照发展和会颁布的《家用电器维修服务明码标价规定》结合行业协会规定,并严格执行。...
...全生产规程、制度和安全技术措施或擅自变更安全工艺和操作程序,指挥者使用未经安全培训的劳动者或无专门资质认证的人员;生产经营管理人员指挥工人在安全防护设施或设备有缺陷、隐患未解决的条件下冒险作业;生产经...