怎么计算冲压件吨位(白车身冲压件成本控制思路与方法)
Posted
篇首语:书到用时方恨少,事非经过不知难。本文由小常识网(cha138.com)小编为大家整理,主要介绍了怎么计算冲压件吨位(白车身冲压件成本控制思路与方法)相关的知识,希望对你有一定的参考价值。
怎么计算冲压件吨位(白车身冲压件成本控制思路与方法)
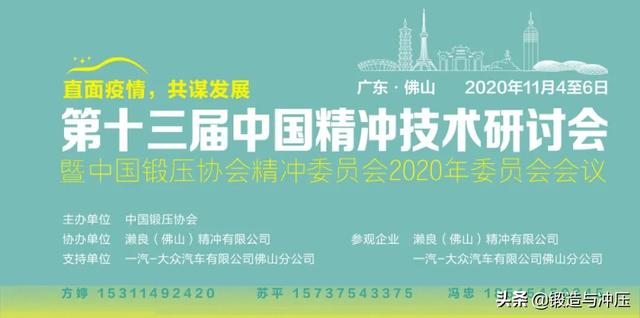
文/刘迪祥,王双枝,黄顶社 · 安徽江淮汽车集团股份有限公司
随着汽车市场竞争越来越激烈,各主机厂都开始把竞争力提升的焦点放在成本控制上。白车身成本在设计阶段就确认了95%以上,一旦进入工装实物开发阶段,工艺上改进和影响的量将很小。同步工程(简称SE)在开发时就充分考虑冲压件整个生命周期内的工艺性、成本、质量等因素,重视冲压件的工艺审查和工艺规划,用最优的工艺方法及手段开发出满足产品要求的零件。
白车身成本构成
白车身成本(图1)主要包括冲压成本和焊接成本,其中焊接成本的主要影响因素是焊点数量、焊缝长度、工装分摊及辅材等,主要由产品设计决定;冲压成本主要影响因素是原材料、生产工序及工装分摊,其中原材料成本主要受材料利用率和材料规格影响,生产成本主要受工序数量和生产吨位决定,工装分摊主要是模、夹、检具开发成本。冲压成本是影响白车身成本的关键因素(占80%),且其工艺方案冻结后成本就已经基本确定。
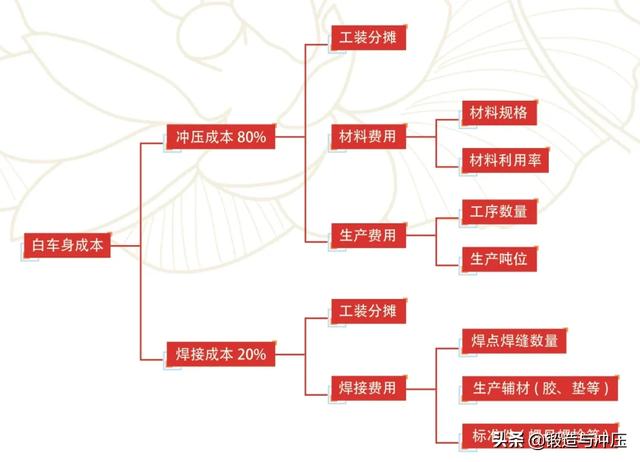
图1 白车身成本构成
冲压领域白车身成本控制的手段
冲压同步工程是在产品开发过程中实施的同步一体化设计,主要目的是提前识别产品设计和工艺设计问题,降低产品变更成本和制造风险,减少产品开发成本和生产成本,改善产品品质,缩减开发周期。其工作贯穿产品开发全过程,按产品开发阶段不同,工作侧重点不同,在产品设计阶段,主要从冲压成形性撰写产品冲压工艺可行性分析报告,反馈给产品研发部门。冲压设计阶段,主要是制定出可行的冲压工艺,具体到多少工序及各工序的冲压方向及工作内容等。在工艺验证阶段,对工艺方案进行验证和再优化,并进行相应评定和纠正及持续改进。
冲压成本控制策划
冲压成本控制要进行提前策划并贯穿于整个产品开发流程,从整车到分总成到零件,都可以参照同类历史车型现状,去除不合理因素后,设定一个参考值,然后结合CAE 分析,给出达标值和挑战值,与工装开发厂家合力一起达成成本目标。在“造型设计—产品设计—工艺设计—工艺验证”各个阶段都可进行目标策划,结果总结确认及改进措施,确保设计出最优的产品、选择最佳的工艺、控制最严的验证,将降成本工作在项目运行各阶段执行落地。同步的将各阶段优秀的方案和经验进行总结和提炼,并转化为各类设计指南,指导后续项目的开发。各阶段成本控制措施及效果如表1 所示。
表1 各阶段成本控制措施及效果
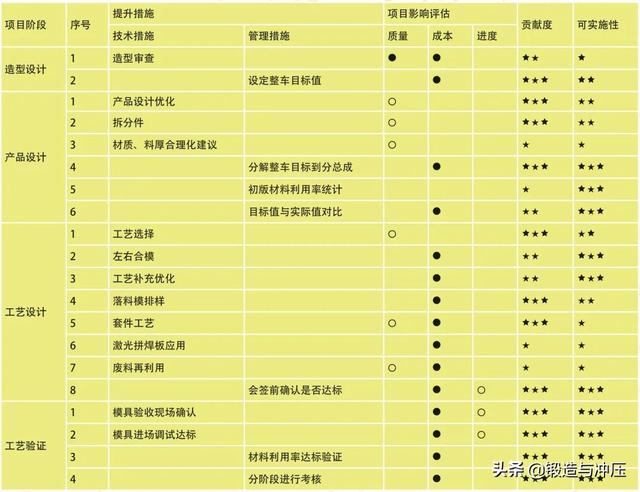
提升整车材料利用率
材料利用率直接关系到白车身成本。以某车型为例,整车材料利用率提升1 个百分点,节约板料重量约12.32 千克,按照板料市场参考价6 元/千克计算,白车身成本节约12.32 千克×6 元/千克=73.92元。提升材料利用率在造型、产品设计、工艺分析设计及试制阶段均可开展,图2 为我司某款轿车在设计阶段通过产品边界优化、拆分件合件等手段提升材料利用率,图3 是在工艺设计阶段通过优化工艺补充,优化排样、摆剪、开发侧出料落料模具,合模、激光拼焊、零件嵌套套冲、废料利用等工艺手段多途径多维度提升整车材料利用率,整车材料利用率从最初规划的55.07%,到方案冻结时提升至58.17%,挑战目标达成。在工艺验证阶段通过实物缩减料片尺寸等手段,整车材料利用率进一步提升,无天窗版达到59.14%,小天窗版58.59%,全景天窗版58.29%。

图2 产品设计阶段提升材料利用率
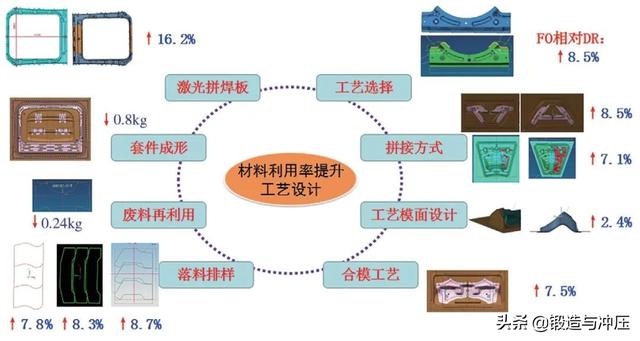
图3 工艺设计阶段提升材料利用率
降低冲压件成形吨位与工序数
冲压件的生产费用与压力机吨位选择和工序数直接相关。冲压模具工艺设计时选择的机床吨位越大,生产工序数越多,生产费用就越高。冲压设备型号的合理选择和优化及减少工序数均可降低生产成本。如我司冲压件机床设计吨位一般用CAE 理论吨位乘经验系数并参考历史车型选择成形吨位,通过成形部位放大成形R 角,修冲类模具使用波浪刀口,提升模具研合及非关键面避空,现场吨位实物验证及优化均能降低成形吨位。
整车工序比(模具数量/零件数)一定程度上可体现整车生产成本,一般整车控制在2.4 以内。在设计阶段通过零件优化减少模具复杂程度,采用多腔模具,左右合模、共模、套模等方式均可减少零件工序比。如图4 所示。
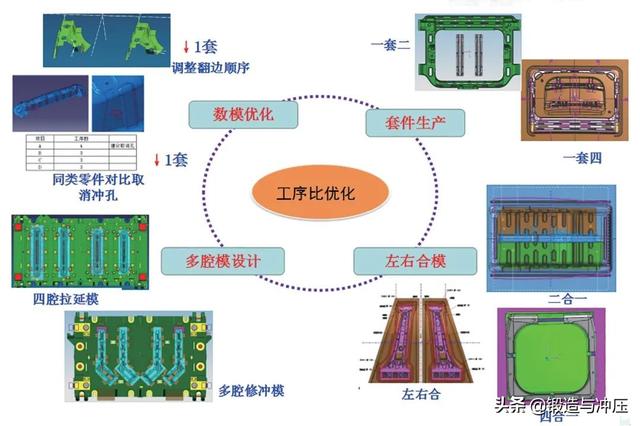
图4 工序比优化
减少工装开发投入成本
冲件模具开发费用是占比最大的研发投入,约占一半以上,而铸造模开发又占到所有模具开发费用的80%。预期产量不大的车型,非关键铸造模件可采用半工装方案,仅开发成形类模具,修冲类模具使用激光切割的方案,待车型上量,再开发修冲类工装。对于确定不开发全工装的车型,零件一次成形可以不考虑修冲角度,能进一步减少翻整类模具的开发,半工装方案一般可节省工装费用的35%~70%。但激光切割生产费用会相应增加,我司半工装方案的盈亏平衡点约为10000 台。对于生命周期超过10000 台但又非主销车型,可通过降低设计标准,如减少模板厚度,降低镶块材质和标准件要求,开发简易模具等,均可以减少工装开发投入成本,即减少工装分摊和冲压件成本。简易工装方案见图5。
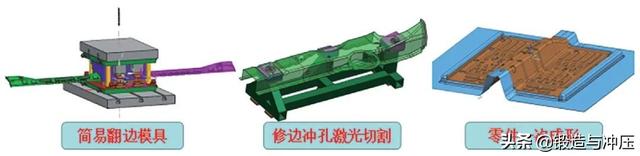
图5 简易工装方案
零件选材优化
零件选材优化也是技术降本的方案之一,在设计阶段要加强车体BOM 材质审查,尽量减少板料规格和特殊规格的板料,便于集中规模采购及议价。另外,同规格料片中,一般1.5mm 料厚板料最便宜,锌铁合金板B340LAD 相较其他材质要便宜,汽车用板材常规料厚范围见图6。可根据市场价格信息,在不影响整车性能以及零件成形性的前提下,对冲压件材质进行优化。同时可加大新材料、新技术的应用,激光拼焊板、热成形件较成熟,铝合金、充液胀形零件正逐步研究和应用,新技术的应用不仅能提升白车身的强度,也能有效技术降本。
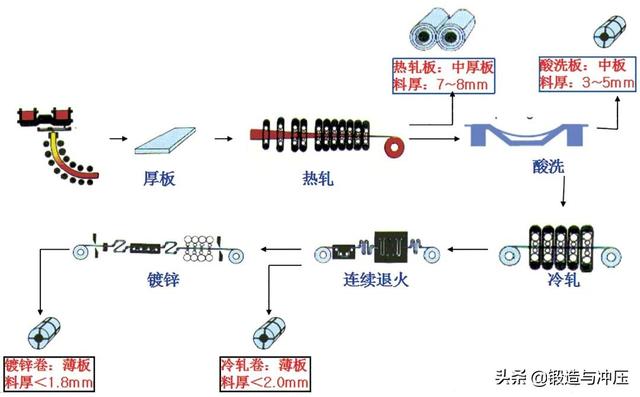
图6 汽车用板材常规料厚范围
结论
同步工程阶段作为控制白车身成本的最重要阶段,在产品设计冻结之前进行的工艺方案规划将决定后续的工装成本以及生产成本,因此从产品的工艺性、设备的合理性以及工装开发的精益性展开成本控制活动十分必要。凡事预则立,不预则废。冲压件成本控制在产品设计阶段可实施空间大,贡献度高,利用历史车型大数据库比对,通过系统策划,设计改良,工艺优化,过程确认,评定纠正可以持续改进。
——来源:《锻造与冲压》2020年第16期
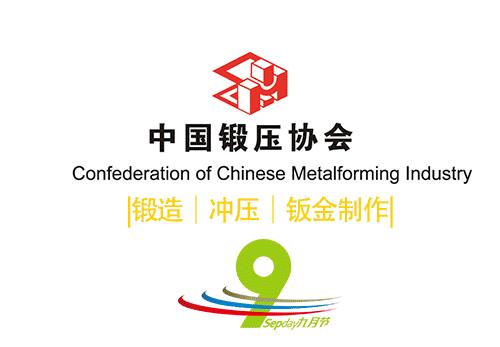
相关参考