弹簧设计(环形弹簧的制造工艺)
Posted
篇首语:一切节省,归根到底都归结为时间的节省。本文由小常识网(cha138.com)小编为大家整理,主要介绍了弹簧设计(环形弹簧的制造工艺)相关的知识,希望对你有一定的参考价值。
弹簧设计(环形弹簧的制造工艺)
1环形弹簧的结构
1.1常见环形弹簧的结构
环形弹簧通常是由端环、外环和内环组成(见图1)。主要参数为弹簧的内径 D1外径 D2和自由高度。自由高度又是由单圈环簧的高度h、数量n、环间的轴向间距δ决定。还有一个主要的参数就是圆锥半角β,当β选取较小时,弹簧刚度较小,若β<p(摩擦角,一般7°~9°),则卸载时产生自锁,即不能回弹复原。
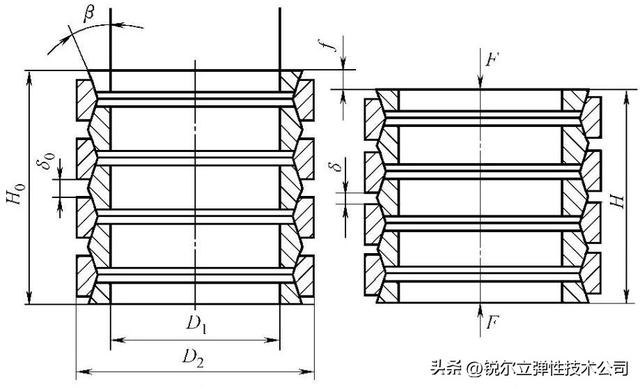
图1环形弹簧结构
a)自由状态 b)受载荷状态
D1—弹簧的内径 D2—弹簧的外径H0—弹簧的自由高度δ0—弹簧外圆环之间的轴向间距
β—弹簧圆环的圆锥半角 δ—弹簧受载荷后外圆环的轴向间距 H—弹簧受载荷后的高度
常用环形弹簧结构尺寸见表2
1.2改进型环形弹簧的结构
改进型环弹簧的内外环截面作了一些调整,即轴向外环的外径和内环的内径不是一根直线,而改成了曲线(见图2)。这样截面积就减小,重量随之减轻,但又不影响内外环的摩擦力,既节约了资源又减轻了重量;也有单外环或单内环改变截面形状的。
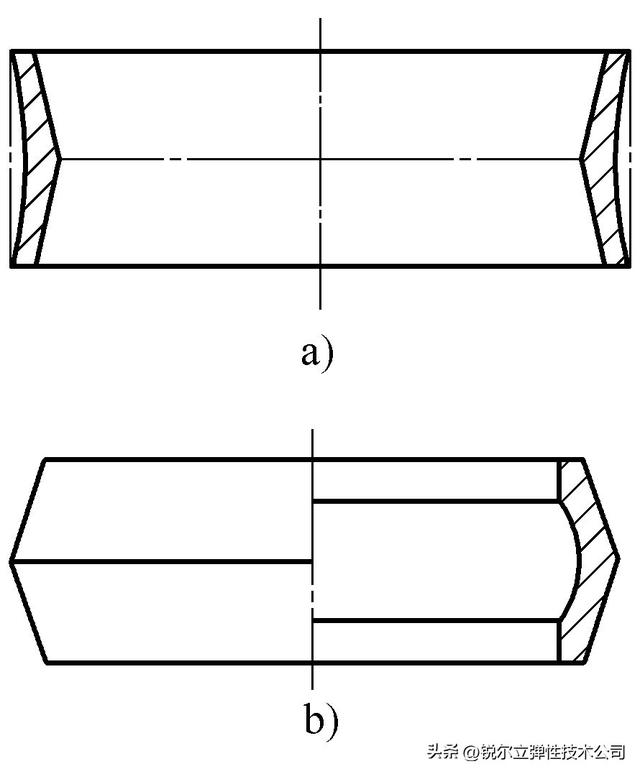
图2改进型环簧 a)外环 b)内环
2环形弹簧的制造工艺流程
环形弹簧规格繁多如表2所列,小自外径18mm,大至外径500mm左右。由于很难找到壁厚与外径相适应的无缝弹簧钢钢管,一般多用锻好的环坯进行制作,其工艺流程如图3所示。

图3环形弹簧的制造工艺流程图
2.1环形弹簧的毛坯制造
环形弹簧锻造毛坯如图4所示。环形弹簧的厚度与外径比一般很小,极易变形,为考虑成品精度,所以下料的内外径加工余量较大,一般都在单边5mm以上。锻造毛坯应成环形,按照毛坯尺寸再计算圆钢下料的长短。例如:当计算外环毛坯为 D1=499mm、d1=438.5mm、h1=82mm 的环簧毛坯选用多粗的圆钢下料,料长又为多少?
首先要计算出此批毛坯体积V
根据锻造比≥2的要求选用Φ200mm弹簧圆钢,则长度应为:
考虑下料损耗及锻造损耗,实际下料为(11.5x1.2)mm=14mm
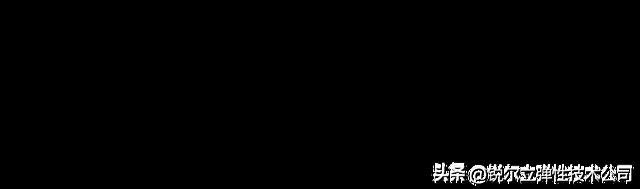
图4环形弹簧锻造毛坯a)外环毛坯b)内环毛坯
环簧毛坯锻造不像碟簧毛坯下料,一定要使锻造比大于2:1。锻造环簧毛坯可以用模锻,也可以用滚压法,犹如滚压轴承大小环。
2.2粗车
粗车内外环时,都需留有精车前的加工余量,此余量的大小视环簧尺寸大小而异。小环簧留得小,大环簧留得大,因为热处理时簧越大,变形相对也大。各向的尺寸一般在0.20~2mm之间,角度可车出也可不车出。此角度β理论上在12°~20°之间选用,一般选用 β=14°~16°,视图样而定。
2.3热处理
环簧热处理一般采用淬火、回火工艺,D2≤140mm的小环簧建议用等温热处理工艺,以获得更佳的强韧性。对于大环簧,为使热处理变形减小,可采用适当挂具。
具体热处理制度视材质而异,环形弹簧常用材料是60Si2MnA和50CrVA弹簧钢,由于环形弹簧毛坯都是经过锻造的,所以必须进行淬火回火处理。
淬火就是把钢加热到临界温度 AC3或Ac以上保温一段时间,使其完成奥氏体化再以适当温度冷却,从而获得马氏体或贝氏体组织的热处理方法。上述两种钢种的加热和冷却时的临界点见表1。
表1环形弹簧常用弹簧钢加热和冷却时的临界点(单位:℃ )
钢种 | 钢号 | Ac1 | Ac2 | Ar1 | Ar3 | M3 |
硅锰弹簧钢 | 60Si2MnA | 755 | 810 | 700 | 770 | 260 |
铬钒钢 | 50CrVA | 740 | 810 | 688 | 746 | 300 |
因此,60Si2MnA淬火温度选用(850~880)℃入池淬火;50CrVA淬火温度选用830~850℃入池淬火。淬火炉选用盐浴炉为佳。淬后硬度应为>58~60HRC。
环形弹簧回火是将淬火后的环形弹簧重新加热到低于 Ac1的某个选定温度,并保温一段时间,然后以适宜的冷却速度冷却,其目的是获得所需的力学性能,稳定环形弹簧的组织和尺寸以及消除内应力。环形弹簧回火后的硬度一般为45~50HRC。
环形弹簧淬火时宜在盐浴炉中进行,可以不用夹具,因为淬火尺寸已经考虑到淬回火后的粗加工所需余量。回火可在井式炉中进行,回火后应立即在水中冷却,回火温度选用400~500℃,回火保温时间视环形弹簧最大厚度考虑。t≤10m)mm的保温时间不低于60min,t≥10mm的保温时间不低于90min。
环形弹簧淬火后应立即回火,以避免由于内应力过大而产生裂纹,淬火与回火之间的时间相隔不宜超过4h。
2.4精车
环形弹簧热处理后进入精车工序,精车最好在数控车床上进行。可以保证圆环的圆锥半角。β是圆环的重要几何参数,它决定环形弹簧的刚度。β小,刚度小,若 β<p (摩擦角)将产生自锁,即不能回弹;β大,刚度大,按照图样精车此角。
2.5强压处理
环形弹簧必须进行强压处理,处理时应将内环、外环和端环按图样要求配制,弹簧试验时,变形量
式中 n-环形弹簧圆锥接触面对数;
δ0-弹簧外圆环间的轴向间距;
δmin-弹簧圆环间在工作极限位置应保留的最小间距。
弹簧圆环间在工作极限位置应保留的最小间距,一般应使 δmin≥1mm,直径较大或加工精度较低时,最小间距应取大些。一般精度较低时可取 δmin≈D/50;精度较高时取 δmin≈D/100。强压时,两侧应置放限高块。
2.6特性测试
环形弹簧的各部几何尺寸检验合格后,都必须测试其力学性能。测试前各接触面需加入润滑剂,常用的润滑剂为石墨、固态MoS2或其他润滑脂。其力学性能不但与几何尺寸有关,更与摩擦面的加工工艺有关,接触面未经精加工,在重载条件下摩擦系数 fu=0.16、p=9°;接触面经精加工在重载荷条件下摩擦系数 fu=0.15、p=8°30';当接触面经精加工在轻载荷条件下摩擦系数 fu=0.12、ρ=7°。图5给出了不同条件下,环形弹簧的特性曲线。
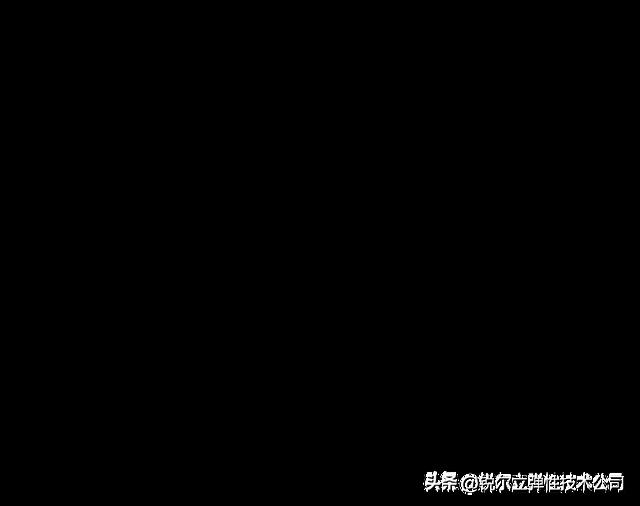
图5环形弹簧的特性曲线
环形弹簧在一个加载和卸载循环中的特性曲线为OABO,如果没有摩擦力的作用下,则应为OC,卸载时,特性曲线由B点开始,而不是由E点,这是由于摩擦使弹簧弹性滞后引起的特性曲线。由于环形弹簧有其较大摩擦功的损耗,所以OA加载曲线测到位后卸载会有不同的曲线,这主要决定于环间摩擦系数所致。
表2是常用环形弹簧结构尺寸,可供设计、制造时参考。
表2常用环形弹簧结构尺寸
序号 | 结构尺寸/mm | 弹簧特性 | 导向件尺寸/mm | 一只内环和一只外环的质量/kg | |||||
D2 | D1 | h | δ0 | F/kN | F/mm | 外导向 | 内导向 | ||
1 | 18.1 | 14.8 | 3.6 | 0.8 | 5 | 0.4 | 18.7 | 13.9 | 0.002 |
2 | 25.0 | 20.8 | 5.0 | 1.2 | 9 | 0.6 | 25.9 | 20.1 | 0.004 |
3 | 32.0 | 27.0 | 6.4 | 1.6 | 14 | 0.8 | 33.1 | 26.1 | 0.007 |
4 | 38.0 | 31.7 | 7.6 | 1.8 | 20 | 0.9 | 39.3 | 30.6 | 0.012 |
5 | 42.2 | 34.6 | 8.4 | 2.0 | 26 | 1.0 | 43.6 | 33.4 | 0.018 |
6 | 48.2 | 39.4 | 9.6 | 2.2 | 34 | 1.1 | 49.8 | 38.1 | 0.026 |
7 | 55.0 | 46.0 | 11.0 | 2.6 | 40 | 1.3 | 56.7 | 44.5 | 0.035 |
8 | 63.0 | 51.9 | 12.6 | 2.8 | 54 | 1.4 | 64.9 | 50.3 | 0.056 |
9 | 70.0 | 58.2 | 14.0 | 3.2 | 65 | 1.6 | 72.1 | 56.4 | 0.074 |
10 | 80.0 | 67.0 | 16.0 | 3.6 | 83 | 1.8 | 83 | 64 | 0.105 |
11 | 90.0 | 75.5 | 18.0 | 4.0 | 100 | 2.0 | 93 | 73 | 0.145 |
12 | 100.0 | 84.0 | 20.0 | 4.4 | 125 | 2.2 | 103 | 81 | 0.203 |
13 | 124.0 | 102.0 | 24.8 | 5.2 | 200 | 2.6 | 128 | 98 | 0.408 |
14 | 130.0 | 111.5 | 24.8 | 5.2 | 160 | 2.6 | 134 | 108 | 0.376 |
15 | 140.0 | 116.0 | 28.0 | 6.0 | 250 | 3.0 | 144 | 112 | 0.568 |
16 | 166.0 | 140.0 | 32.0 | 7.6 | 400 | 3.8 | 170 | 136 | 0.869 |
17 | 194.0 | 155.0 | 38.0 | 8.8 | 600 | 4.4 | 199 | 150 | 1.676 |
18 | 198.0 | 162.0 | 37.0 | 7.8 | 510 | 3.9 | 203 | 157 | 1.570 |
19 | 220.0 | 174.0 | 44.0 | 8.8 | 720 | 4.4 | 225 | 169 | 2.537 |
20 | 262.0 | 208.0 | 42.0 | 9.6 | 860 | 4.8 | 268 | 202 | 3.451 |
21 | 300.0 | 250.0 | 60.0 | 11.6 | 1000 | 5.8 | 306 | 245 | 5.51 |
22 | 320.0 | 263.0 | 64.0 | 12.4 | 1200 | 6.2 | 326 | 258 | 7.06 |
23 | 350.0 | 288.0 | 70.0 | 13.2 | 1400 | 6.6 | 356 | 283 | 9.18 |
24 | 400.0 | 330.0 | 80.0 | 15.6 | 1800 | 7.6 | 407 | 324 | 13.56 |
25 | 489.0 | 428.5 | 78.0 | 24.0 | 2000 | 7.9 | 498 | 420 | 22.000 |
相关参考