弹簧生产工艺流程(轮轴复合挤压生产工艺分析)
Posted
篇首语:精神的浩瀚,想象的活跃,心灵的勤奋,就是天才。本文由小常识网(cha138.com)小编为大家整理,主要介绍了弹簧生产工艺流程(轮轴复合挤压生产工艺分析)相关的知识,希望对你有一定的参考价值。
弹簧生产工艺流程(轮轴复合挤压生产工艺分析)
文/赵艳凤,吴兵,张永俊·柳州方盛精密锻造有限公司
叉车是工业搬运车辆,随着经济的快速发展,其应用深入到了运输业、仓储业、港口、机场、车站及批发零售业等各行各业。随着搬运货物的重量越来越大,对叉车零部件的要求也越来越高,其零件的复杂性也越来越高。
轮轴外形及尺寸
本文提到的轮轴为某品牌公司叉车用,该零部件为出口产品,原来其同类产品尾部轴杆为机加工后装配使用(图1),现需改为一体式锻造加工成形(图2),增加了产品的锻造成形难度。
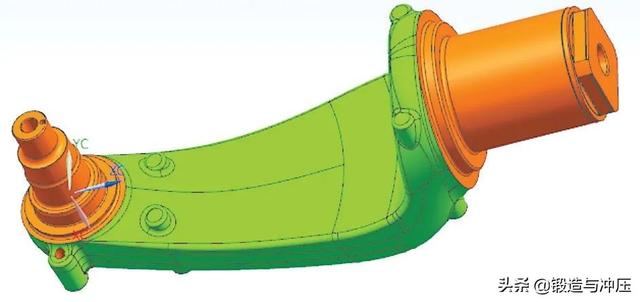
图1 轮轴机加工3D 数模
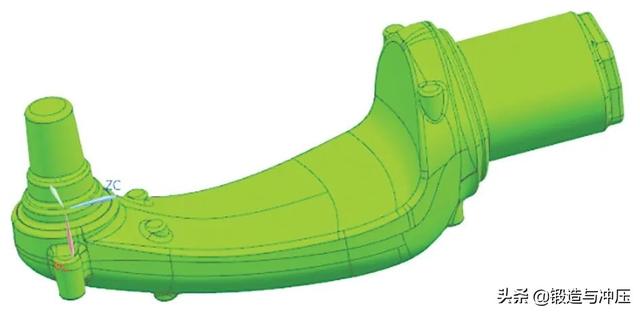
图2 轮轴锻件3D 数模
如图3 所示的轮轴锻件图,锻件尾部101.5mm高度的轴杆需要整体锻造出来,增加了锻造成形难度,生产过程中轴杆容易充不满,因此本产品在设计时采用了复合挤压的工艺进行锻造成形。
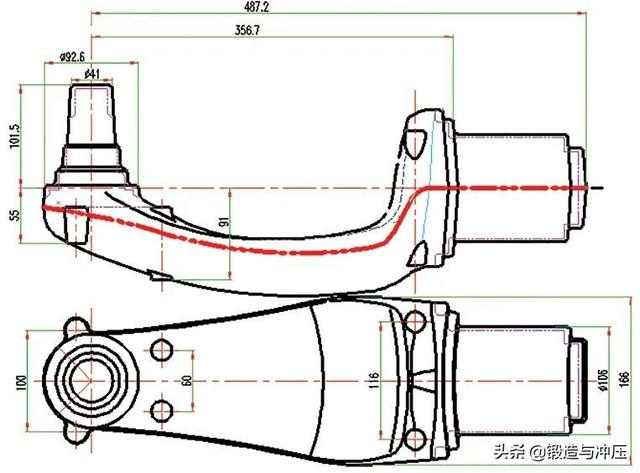
图3 轮轴锻件2D 图
工艺分析
主设备选择
轮轴锻件重37.7kg,材质为42CrMo,锻件复杂系数S3,根据投影面积计算需要成形力为60016kN,由于叉车类产品零件相对汽车类产品零件需求量较小,结合公司设备状况,选择6300t 摩擦压力机作为主设备进行生产,630t 压力机进行切边。
工艺流程
此产品属于长轴类零件,根据其各特征截面形状选择工艺流程为:下料→加热→制坯(掉头拔长)→预锻→终锻→抱紧切边→喷砂→热处理(调质)→喷砂→磁粉探伤→外观尺寸检查→机加工→尺寸检查→清洗防锈→包装出货。
根据工艺流程分析产品在设计过程中要考虑以下问题点:
⑴制坯图的确认,材料直径的选择,按照产品截面图(图4)其计算最大截面需求直径为φ165mm。根据体积相等原则或黑箱原理进行简化,简化后确认其制坯形状见图5,选择材料直径φ150mm,需掉头拔长。
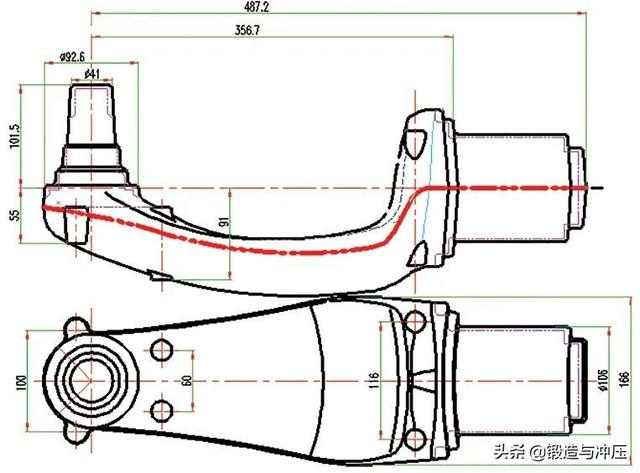
图4 产品截面图
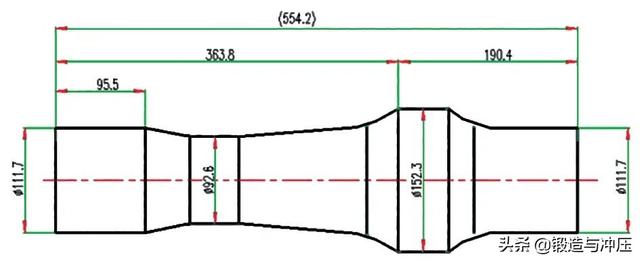
图5 制坯简图
⑵由于尾端杆部的高宽比为2.47,一次成形充满性差,需要设计预锻,并需对其预锻形状提前做预处理,同时大头耳朵处也容易充不满,需在预锻前做处理。
⑶由于四个小定位凸台要求的一致性较高,切边采用了抱紧切边方式;难点为弹簧的选择,需核算弹簧的弹力和行程,使产品在切边过程中既能确保切断又要控制切边后的变形量满足要求,同时还需对切边为斜面的斜度尺寸做处理。由于产品较重,切边后的出料工具需特别制作。
⑷产品定位问题,在设计过程中要保证每一道工序的定位稳定,确保产品在生产过程中不会因为放不正产生质量问题,特别是制坯到预锻定位方式的选择。
数值模拟分析
通过之前的简化制坯图,用下料尺寸为φ150mm×318mm 的锻坯进行数值模拟。之前考虑的问题点为对预锻大头容易不满模的处理,采取的措施主要是增加入料圆弧R 角,控制此处两侧的金属流动速度,预锻到终锻的体积配比设计为1.5%左右,模拟后此处无充不满风险。但是杆顶端局部充不满的现象依然存在,根据模拟结果进行修正,主要是增加入料圆角及此处的桥部宽度,让金属更容易流进型腔,预锻到终锻的体积配比设计为2%左右。由于未模拟制坯过程,因此坯料模拟温度设定为1100℃,终锻后模拟成形力为58600kN,上下模温度设置为200℃。预锻模拟的成形结果如图6 所示,终锻模拟的成形结果如图7 所示,可以看出模拟过程中预锻和终锻都能充满型腔,数模锁定后待现场实际生产验证。
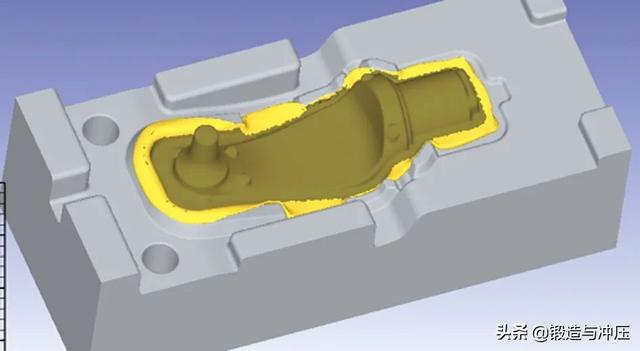
图6 预锻成形模拟
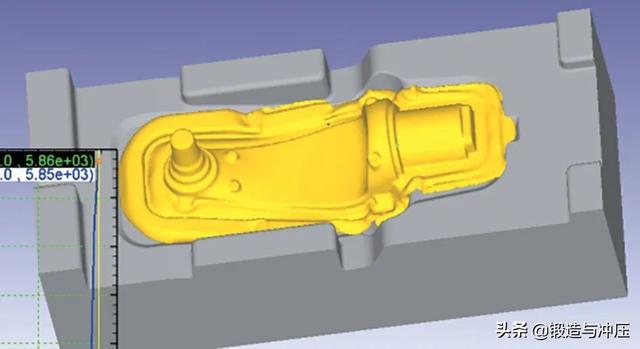
图7 终锻成形模拟
锻件生产过程验证
由于模拟参数与现场实际会有差异,生产中制坯采用空气锤2 道掉头拔料,验证其尺寸满足设计要求,用6300t 摩擦压力机进行预锻、终锻,由于提前设计了摆料定位,产品在生产过程中定位稳定,预锻锻打2 锤,终锻锻打2 锤。实际生产中坯料见图8,预锻件见图9,终锻件见图10,样件生产过程中由于量少且过程监控严格未发现不良问题。但是进入小批量试生产时,在生产过程中发现轴杆局部充不满情况依然存在,如图11 所示,不良品占比达到15%,通过现场分析确认原因如下:
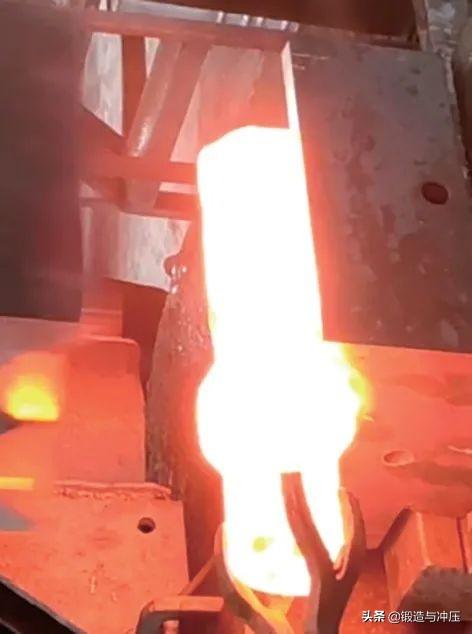
图8 制坯
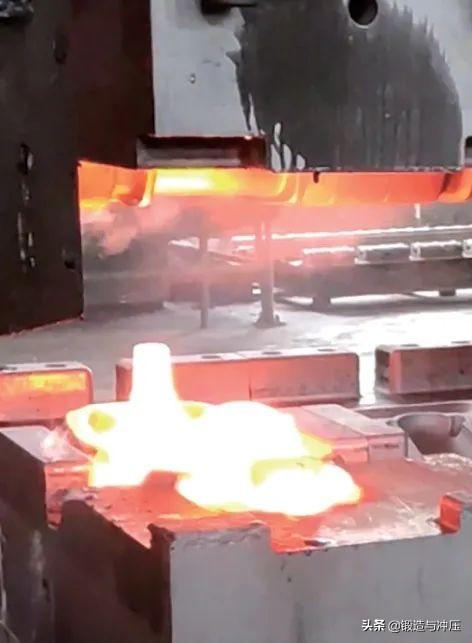
图9 预锻
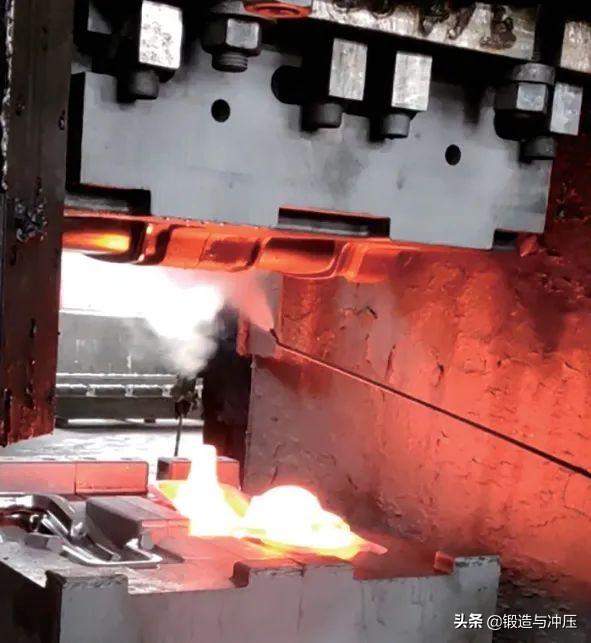
图10 终锻
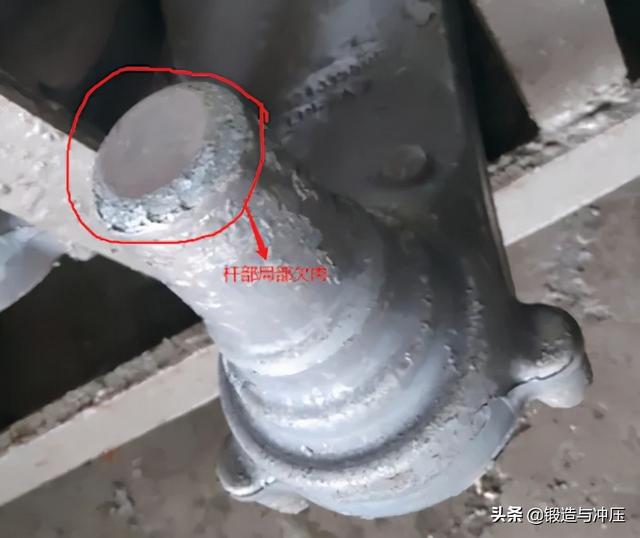
图11 杆部局部欠肉
⑴采用空气锤掉头拔料过程中工人节拍不稳定,制坯后局部产品温度会偏低;
⑵锻造过程中此处模具温度低,材料进入型腔后温度容易下降,且此处离人较远,容易润滑不足。
根据分析结果对产品工艺过程进行了调整:
⑴通过修改制坯,增加尾部此处的配料尺寸,直径从φ111.7mm 修改为φ112.5mm,同时减少中间材料直径,确保用料总体不变;
⑵预锻杆部此处R 角继续加大,由原来的R40mm 加大到R50mm;
⑶预锻到终锻的配比由原来的2%修改到3%;
⑷同时重点控制工人拔料节拍,热模时预锻模及终锻模杆部的模具温度需大于200℃,锻造过程中需确保此处的模具冷却及润滑。
调整后产品生产基本能满足要求,切边采用抱紧切边(图12),其优点为变形量小,4 个定位点在抱紧过程有整形的功能,落差尺寸稳定性好,同时修正过原斜面形状后切边行程较短且切边外观质量更好,合格的热锻件成品如图13 所示。
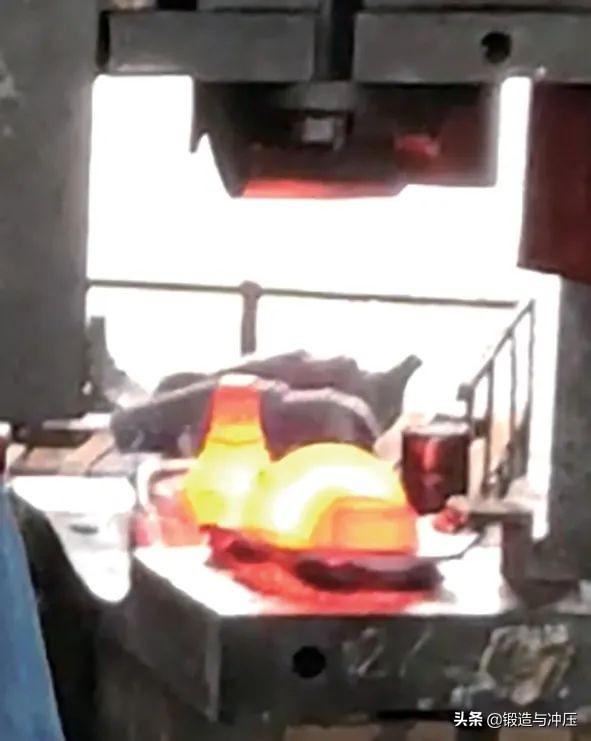
图12 抱紧切边
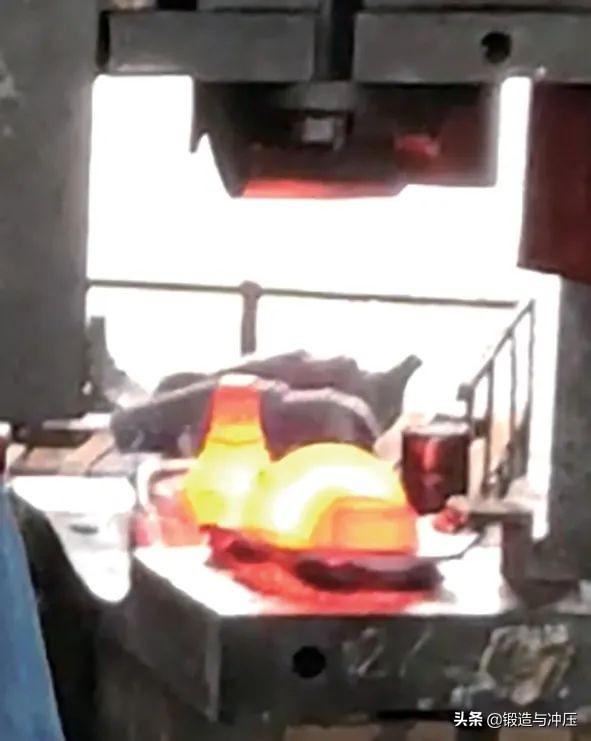
图13 热锻件成品
由于锻件增加了尾部杆身,热处理调质时锻件更容易变形,初期试制时未能引起足够重视。待锻件热处理完成后用三维扫描仪对成品进行扫描(图14),与3D 数模对比时才发现热处理变形量局部较大,无法满足成品要求,随后通过调整装框及淬火入水方式得以解决。锻件成品见图15。
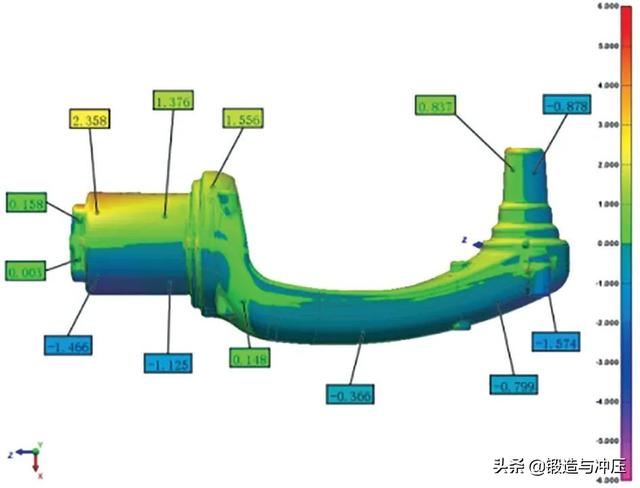
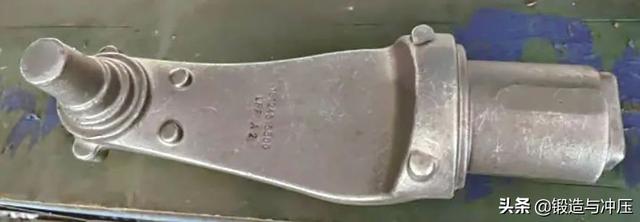
图15 锻件成品
结束语
轮轴采用的复合挤压工艺很早就已经开始有应用了,现在许多产品在生产过程中都会用到。想要在设计过程中少走弯路,需在新产品开发设计评估阶段,通过工作经验及同类产品质量数据系统在分析初期能较好的识别出问题点,提前对问题点进行预处理,同时通过数值的模拟来验证前期规划的合理性,数值模拟可以把一些未考虑全面的问题在实际生产前暴露出来,并能提前进行修正。但是现场生产实际情况比较复杂,数值模拟无法做到100%模拟现场,因此在实际生产过程中要更仔细的观察寻找变异点,需根据实际生产情况调整设计工艺,确保量产稳定性。同时现代化技术的发展,产品开发过程中3D 建模+数值模拟+现场实际生产+三维数据扫描对比等数字化的建设,会更快更好的推进新产品开发及生产过程中工艺的改善。
——文章选自:《锻造与冲压》2022年第1期
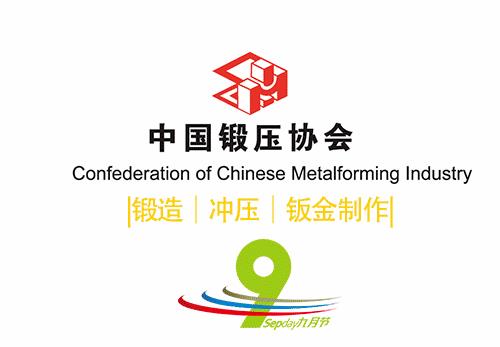
相关参考
...种和数量迅速增长。目前,世界各国建成了上千条铝型材生产线,其工艺装备、生产工艺和模具的设计与制造均已基本定型,具有标准化、系列化的特点。(1)铝型材绝大多数采用6063-T5/T6铝合金生产,这是因为6063铝合金质轻,...
...闭式挤压工艺,对于成形深筒形的件并不擅长,并且实际生产中还面临脱模困难的问题。传统的接套体成形方案采用开式模锻先锻造出两端无孔、底座填实的锻件,然后通过机加工进行生产。考虑到所用材料为30CrMnMoTiA(803A)(...
液压机温控怎么拆卸(「原创」一种热挤压半轴套管成形液压机研发)
...挤压半轴套管成形液压机研发的必要性,在分析现有生产工艺流程模式下成形设备不足的基础上阐述了用于热挤压半轴套管成形液压机的优势。之后阐述了热挤压半轴套管液压机设计的关键技术,包括主机参数特点及设计优化、...
液压机温控怎么拆卸(「原创」一种热挤压半轴套管成形液压机研发)
...挤压半轴套管成形液压机研发的必要性,在分析现有生产工艺流程模式下成形设备不足的基础上阐述了用于热挤压半轴套管成形液压机的优势。之后阐述了热挤压半轴套管液压机设计的关键技术,包括主机参数特点及设计优化、...
涡卷发条弹簧在冲击、振动或长期交应力下使用,所以要求弹簧钢有高的抗拉强度、弹性极限、高的疲劳强度。在工艺上要求弹簧钢有一定的淬透性、不易脱碳、表面质量好等。弹簧细分碳素弹簧钢即含碳量WC在0.6%-0.9%范围内的...
...即PU按照层数划分:三层:加膜复合;二层:不加膜复合生产原理复合设备核心组成部分为上胶装置与复合装置。面布(薄膜)经过上胶装置时,通过上胶压辊挤压,雕刻辊胶眼里的胶水被迫转
目前,我国大多数饲料厂均采用环模制粒生产水产饲料。通过环模制粒生产的硬颗粒饲料沉入水底10~20min即溃散,采食性差,部分残留在水域环境中,对水质污染严重;而挤压膨化饲料经过高温、高压,是一种低污染、浪费...
摘要:文章首先分析了复合钢板压力容器生产前的准备工作,并对加工过程中所应用到的各项技术方法和安全措施进行探讨,总结出加工中的注意事项,避免在加工制造过程中,有影响到复合板材料质量安全的问题出现。关键词...
摘要:文章首先分析了复合钢板压力容器生产前的准备工作,并对加工过程中所应用到的各项技术方法和安全措施进行探讨,总结出加工中的注意事项,避免在加工制造过程中,有影响到复合板材料质量安全的问题出现。关键词...
挤压机铝棒温度(技术丨车体6082铝合金型材的T4热处理生产工艺)
(内容来源于:有色金属结构材料,关注查看更多详情)6082和6061同属Al-Mg-Si系可热处理强化铝合金,挤压加工、锻造性能好,阳极氧化性、抗蚀性好。具有良好的可成型性、可焊接性、可机械加工性,同时具有中等强度,在退...