废油炼柴油设备(废油再生循环利用项目 可行性研究报告)
Posted
篇首语:追风赶月莫停留,平芜尽处是春山。本文由小常识网(cha138.com)小编为大家整理,主要介绍了废油炼柴油设备(废油再生循环利用项目 可行性研究报告)相关的知识,希望对你有一定的参考价值。
废油炼柴油设备(废油再生循环利用项目 可行性研究报告)
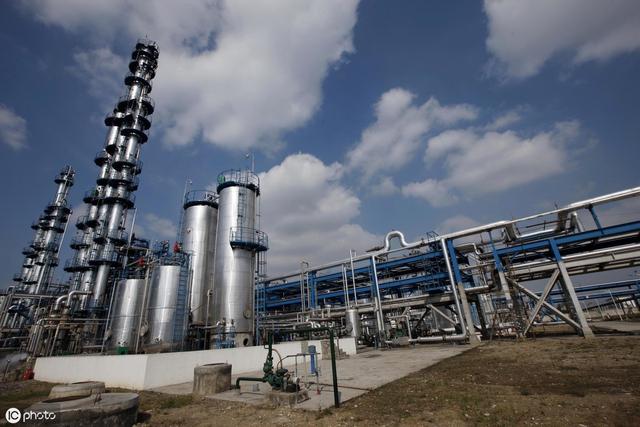
一、 市场分析:
1、废油定义:
废油主要是指:废矿物油,包括废机油、废液压油,废变压器油,废导热油、废齿轮油等等。
2、市场有多少废油?
废机油量所占比例最大:据相关部门测算,每1万辆机动车的废油产生量是180吨/年,2018年全国汽车保有量3.19亿辆,总废机油量估计达570万吨/年。
其它工业废润滑油量没有确切数据,估计不低于200万吨/年(新油需求约300万吨)。
3、市场竞争格局
过往,部分企业会将再生利用价值较大的废矿物油高价卖给非法处置企业,导致合法处置企业原料短缺,合法企业与非法企业之间存在较激烈的无序竞争。近年,国家狠抓环保,严厉打击非法处理废油的企业,对合法企业带来极大利好。
4、相关法规:
根据《国家危险废物名录》,废油属危险废物,必需按《中华人民共和国固体废物污染环境防治法》收集、贮存、处置的经营活动。在当前国家严厉的监管下,非法处理废油的企业将失去生存空间。
2017年2月4日,国家发改委发布《战略性新兴产业重点产品和服务指导目录》,将废油再生列入国家战略性新兴产业重点产品和服务指导目录主要内容,鼓励、支持合法企业发展废油再生项目。
5、技术意义:
润滑油中一般真正变质的只有百分之几,如果将这些变质的成分除去,经过一定工艺技术加工就可以生产出与天然油质量相当的高品质、高标号润滑油来。因此,在世界能源日益紧张的形势下,为了节约能源与资源,废润滑油的回收和再生利用成为需迫切解决的问题。本项目充分利用废润滑油再生还原成润滑油基础油、燃料油,既能缓解我国石油短缺而需求又日益增长的供需矛盾,又能促进环保、变废为宝、循环利用,并给企业带来良好的经济效益,具有很好的投资必要性。
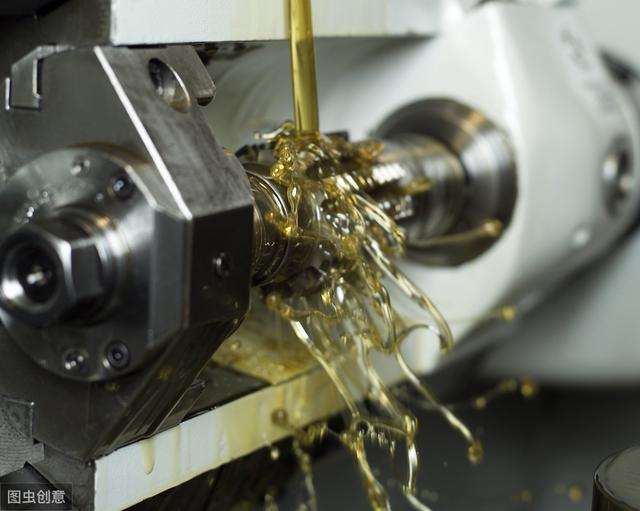
二、 方案及工艺介绍
1、 常见工艺分析
1) 物理净化法
主要包括沉降、过滤、离心分离和水洗等,这种方法严格说来不属于废油再生处理的范畴,主要是净化油,除去油中污染物,也可作为废油再生处理前的预处理。
2) 物理-化学方法
主要包括凝聚、吸附等单元操作,通过絮凝作用让油中的氧化产物形成絮状凝聚物而从油中分离出来,这种以少量的絮凝剂来代替浓硫酸的工艺,被称为絮凝工艺。这是废润滑油再生处理工艺改革中出现的一种无污染工艺,避免了使用硫酸-白土法的各种弊病,彻底根除了硫酸对环境的污染,较好地除去了油品中的氧化产物。
吸附剂的作用是将废油中的沥青、胶状物质、酸性化合物、酯及类似的产物吸附在吸附剂的表面上,用过滤的方法将吸附剂连同吸附在其表面上的物质从油中除去。在吸附过程中,通常吸附质通过孔表面边界膜,通过孔的毛细孔和整个孔内表面的扩散过程是主要的。在这一过程中,由于分子间范德华力的作用而产生吸附,从而对油脂中的色素、杂质进行吸附,而达到脱色、脱杂质的目的。
3) 化学方法
这一方法主要包括硫酸处理,硫酸-白土处理和硫酸-碱-白土处理等。虽然采用硫酸对废油进行再生处理的效果较好,但是该工艺明显的不足是产生比较严重的二次污染,如产生大量的酸性气体二氧化硫及大量的难以处理的酸渣、酸水、白土渣等,危害操作人员身体健康、腐蚀设备、污染环境。国家已经不允许采用这种酸洗再生处理工艺。
2、 领先的废油再生处理工艺介绍
蒸馏法,是当前较为先进的废油再生处理工艺,无二次污染,但投资成本大,工艺复杂。
1)催化蒸馏法:
这里介绍一种“三级复合催化+高真空减压蒸馏+分压汽提技术”。先经复合催化剂三级催化后,再采用道尔顿的蒸汽分压原理汽提,无需进行酸碱处理或溶剂萃取,用汽提减压原理使原料油油品蒸馏全过程得以完成,水蒸气汽提对脱去废油的酸性气味,使之甜味化是非常有效的。长时间汽提能使废油中的NO2完全去除,硫含量能下降到80%以上,油品甜化后进入分馏塔,塔顶设回流装置,内回流装置中用水为回流介质,通过水流量的大小来控制塔顶温度300度以下)。整个生产过程无二次污染,无三废排放,即可产出合格的再生润滑油基础油及燃料油,此发明属国内首家使用并申请专利,并得到用户的认可。
2)技术原理
原料废润滑油经沉降脱除机械杂质后,进入化学处理釜,加入新型复合催化剂。在高真空条件下进行蒸馏,依次蒸出水、轻馏分油、各种沸程的润滑油基础油,经过冷却后回收。最后排出蒸馏残渣(可作燃料)。蒸馏过程中废润滑油采用循环加热的手段;加热热源采用导热油加热等。配有废气处理系统对真空泵排出的气体进行净化处理。蒸馏出的馏分油经过吸附剂脱色后进入储罐区。
3)技术特点
a、处理油料广泛:适用各种废润滑油(包括汽、柴机润滑油、液压油、齿轮油等几乎所有可以回收的废弃油);
b、处理过程中不会造成二次污染:此工艺产生过程中不使用酸和白土,没有产生不能利用污染环境的废物;生产过程采用燃油或燃气加热,并有废气处理装置,排出的尾气达到国家排放标准,对环境影响非常小。;
c、产品质量好:不会产生氧化变色,也没有臭味产生;
d、处理成本低;回收率高(出油率达80%-95%,因废油来源不同,出油率也不同)。
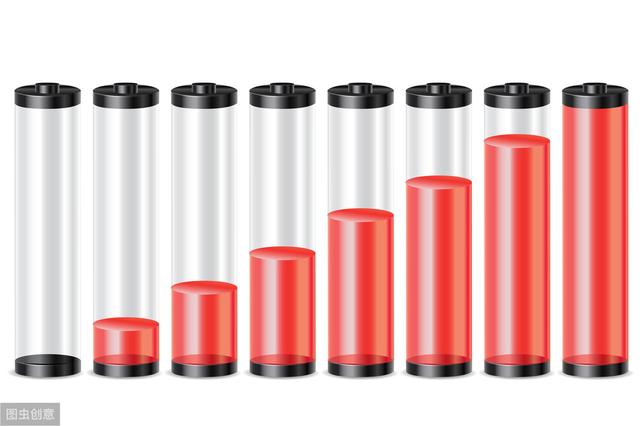
三、 生产工艺及物料平衡
1 、工艺流程及产污环节
本工艺流程为:废润滑油→预处理→沉降脱水→复合催化→减压精馏→成品基础油。
废润滑油收集后,先经离心过滤去除大颗粒固体杂质进入卸油池,再打入储罐中沉降脱水,上层含水量较低的废油进行复合催化,再通过减压蒸馏、高真空蒸馏将各馏分油分离出来,各馏分油就可以作为不同的合格的润滑油基础油。蒸馏塔底重组分可作为燃料油外卖,芳烃油外卖。
2、工艺流程简述
2.1过滤
外购的废润滑油先通过化验室化验进行严格分析,根据分析结果选择合理的处理工艺进行处理。处理前先通过过滤方式,除去大块固体杂质 S1 如废手套、废螺丝、废抹布等,废润滑油过滤后进入卸油池.
2.2沉降脱水
通过油泵将卸油池内的废润滑油送输入储油罐,在储油罐内进行沉降。然后将上层油层部分用泵抽出来用于下一工序,同时将含油废水抽出来进入油水分离器处理,罐底为油泥。根据类比同类型的润滑油生产厂家,该过程分离出的油、水及杂质约为 3.2%。该工序产生固废油泥 S2、含油废水 W1,经沉淀预处理后的润滑油进入原料油罐以备下一步处理。
2.3复合催化
用釜式固定床催化裂化装置加工原料油,即把原料油装入蒸馏釜中加热,使油气化。在釜顶设有催化塔,塔内设有多层催化剂床填装催化剂。当被加热的油气穿过催化塔中催化剂床层后,再冷凝冷却为液体。所得的油品,即达到了减粘、降凝、降密度、脱色、除臭的目的。
2.4高真空精馏
初步处理后的废润滑油加热到 330-350℃后输入蒸馏塔蒸馏,得到不同馏分的基础油,此工序产生不凝气 G1和 残渣角油S2。
3、产污环节
本项目主要生产装置产污环节如下,主要有:
3.1废气
生产装置废气产生节点为:①高真空蒸馏产生的不凝气(G1):主要污染物为烃类,进入瓦斯管网送至燃烧炉燃烧;②气提产生的不凝气(G2):主要污染物为烃类、甲基吡咯烷酮,进入瓦斯管网送至燃烧炉燃烧;③燃烧炉烟气:燃烧炉主要用于各蒸馏塔进料加热,其产生的污染物主要为天然气燃烧产生的少量的 SO2、NOx 和烟尘,以及废气燃烧产生的 CO2、NOx,废气通过 1 根 20m 高排气筒(1#)排放;食堂油烟废气:经油烟净化器处理后高空排放。
3.2废水
生产装置废水产生节点为:预处理单元原料沉降罐产生的含油污水(W1),蒸馏产生含油污水(W2)。以及精制过程中,精制沉降过程产生的含油废水(W3)。
3.3固废
生产装置固废产生节点为:过滤产生的滤渣(S1)、预处理产生的油泥(S2)。
4、物料平衡
4.1整体物料平衡
日产200吨废油再生项目整体物料平衡入表1所示,
4.2工艺水平衡
项目工艺水平衡详见表2;
产品精制工艺水平衡详见表3;
4.3 建设项目水平衡
4.3.1项目用水情况
项目用水环节包含:生活用水、循环冷却补水、设备及地面冲洗用水、绿化用水等。用水为自来水,取自供水管网。产品精制汽提工序需要加入蒸汽,蒸汽消耗量为 395t/a,蒸汽来自园区蒸汽管网。
1)生活用水
项目建成后劳动定员 58 人,厂内设置食堂,职工均为附近居民。根据《建筑给水排水设计规范》(GB50015-2009)相关规定,生活用水量以人均 150L/d 计,则项目建成后生活用水量为 2784m3/a。
2)冷却系统补水
项目建成后循环水量为 100m³/h,补水量按循环量的 2.0%计,则年补充水量为15360t。
3)场地及设备冲洗用水
项目装置占地面积 650m2(假定),按照 2L/(m2 •d)系数计算,则年用水量为 416 m3,由循环冷却排水供给;由建设方提供资料,本项目生产线连续生产,设备无需清洗,只有在检修期会有部分设备清洗,耗水量约为 1 套生产装置 60m3/a。项目建成后,全厂设备、地面冲洗用水量为 536 m3/a,其中地面冲洗水采用循环统溢流水,设备冲洗采用新鲜水补充。
4)绿化用水
建设项目绿化面积为725m2,用水按2L/m2·d,一年以160天计,则年用水量为237.5t,由循环冷却排水供给。根据上述分析可知,项目建成后年新鲜用水量总计 9132m3,水源来自来水管网。
4.3.2项目排水情况
拟建项目排水实行清污分流。清洁雨水经雨水管线排放。生活污水经化粪池处理后同生产废水一排入厂内污水处理站处理。经污水站处理后排入污水处理厂。
1)工艺废水
项目建成后全厂工艺废水量约为 1864t/a,其中 COD 167381mg/L,石油类45594mg/L。
2)设备及地面冲洗水包括各生产装置、罐区及场地冲洗水等,由于项目为连续生产,设备一般不冲洗,项目建成后每年共约需冲洗水 536t/a,排放量约为 428.8t/a,进厂区污水站处理。
3)冷却循环溢流水项目循环水量为 10m3/h,为了保证工艺循环水的水质,项需定期排放循环水池中的水,弃水量约为补水量的 30%,则循环弃水量为 4608m3/a。属于清净下水,根据类比该废水中主要污染因子 COD 产生浓度约为 30mg/L, SS 浓度约为 40mg/L,部分用于地面冲洗(416m3/a)、绿化用(475m3/a),其余直接排入雨水管网(3717m3/a)。
4)生活污水项目职工 58 人,生活用水量以人均 150L/d 计,年生产 320d,则公司生活用水量为 2784t/a,排水系数取 0.8,则年生活废水排放量为 2227t。
5)初期雨水
由于罐装、泄漏等原因,储罐区、装置区初期雨水中 COD 浓度一般在200~1000mg/L,平均为 600mg/L,SS200mg/L、石油类 50mg/L。这部分雨水计入排污总量,后期雨水及厂区其它雨水通过雨水管网直接排放。
地面径流雨水产生量按下式计算:
q=15.873(1+0.78lgP)/(t+10)0.91(l/s.104m2)
式中:Q—径流雨水量(m3);
g—重力加速度,取 0.98;
P—暴雨强度重现期,取 2 年;
t—降雨历时,取 10min。
经计算初期雨水量约为 184.75t/a,COD 产生量为 0.087t/a,SS 产生量为 0.029t/a。
4.4大气污染源强分析
有组织废气主要是生产装置产生的不凝气、燃烧炉燃烧天然气产生的废气及
食堂油烟,主要成分为 SO2、NOx、非甲烷总烃、烟尘及食堂油烟。
(1) 工艺废气
项目产生的工艺废气主要为脱水、初馏、减压蒸馏、高真空蒸馏产生的不凝气,主要成分为非甲烷总烃.项目废气产生情况为①脱水产生的不凝气(G1),主要成分为非甲烷总烃,产生量为 13.727t/a;②初馏产生的不凝气(G2),主要成分为非甲烷总烃,产生量为0.631t/a;③减压蒸馏产生的不凝气(G3),主要成分为非甲烷总烃,产生量为 46.378t/a;④高真空蒸馏产生的不凝气(G4),主要成分为非甲烷总烃,产生量为 52.175t/a;⑤汽提不凝气,主要为非甲烷总烃、甲基吡咯烷酮,产生量为 18.472t/a;
(2) 燃烧炉烟气
本项目设置 1 台 260 万大卡/小时燃烧炉,天然气热值按 8000 大卡计,热效率85%,则燃烧炉天然气耗量约为 295 万 Nm3/a。
本项目天然气燃料燃烧产污系数主要参照《环境影响评价工程师职业资
格登记培训教材 社会区域类》(中国环境科学出版社出版)中油、气燃料的污染物排放因子,每燃1000立方米天然气排放烟尘0.14kg,SO2 0.18kg,NOx1.76kg,具体数值见表4。
(3) 食堂油烟
本项目预设职工食堂一座,仅供内部职工就餐用,食堂厨房基准灶头1个,属于中型规模。食物在炸、煎、煮、炒等烹饪、加工过程中将挥发出油脂、有机质及热分解或裂解产物,从而产生油烟废气。厨房油烟中的主要危害成分为醛、酮、烃、脂肪酸、醇、芳香族化合物、酮、内酯、杂环化合物等。
根据调查,居民人均食用油用量约10kg/a,油烟产生量按耗油量的4%计,则人均产生量为0.4kg/a。本项目建成后职工定员58人,则油烟产生量约23.2kg/a,产生浓度约6.0mg/m3。建议对油烟采用静电式油烟净化器净化后,通过排烟管集中达标排放。油烟净化器设计净化效率≥70%,则油烟年排放量约6.96kg,排放浓度约1.8 mg/m3。
食堂采用电、天然气作为能源,项目建成后天然气用量约 2160Nm3/a,使用量较小,因此,对此部分液化气燃烧产生的废气污染物亦不进行定量统计分析。
(4)、无组织排放
(1)罐区“大、小”呼吸排放的废气
① 小呼吸排放量
小呼吸排放是由于温度和大气压力的变化引起蒸气的膨胀和收缩而产生的蒸气
排出,它出现在罐内液面无任何变化的情况,是非人为干扰的自然排放方式。
固定顶罐的呼吸排放可用下式估算其污染物的排放量:
LB = 0.191×M(P/(100910-P))0.68×D1.73×H0.51×ϫT0.45×FP×C×KC
式中:LB — 固定顶罐的呼吸排放量(kg/a);
M — 储罐内蒸气的分子量,各类油按轻质油中较小值计,分子量为 220;
P — 在大量液体状态下,真实的蒸气压力(Pa),轻质油蒸汽压为 600 帕;
D — 罐的直径(m),本项目废润滑油、重馏分、中馏分、轻馏分、燃料油储罐
直径分别为 9.1m、8m、8m、8m、8m;
H — 平均蒸气空间高度(m),本次环评取 0.3m;
ϫT — 一天之内的平均温度差(℃);
FP — 涂层因子(无量纲),根据油漆状况取值在 1~1.5 之间,本次环评取 1.0;
C —用于小直径罐的调节因子(无量纲);直径在 0~9m 之间的罐体,C = 1 -0.0123(D-9)2;罐径大于 9m 的 C = 1;
KC — 产品因子(石油原油 KC 取 0.65,其他的有机液体取 1.0)
② 大呼吸排放量
大呼吸排放是由于人为的装料与卸料而产生的损失。因装料的结果,罐内压力
超过释放压力时,蒸气从罐内压出;而卸料损失发生于液面排出,空气被抽入罐体
内,因空气变成有机蒸气饱和的气体而膨胀,因而超过蒸气空间容纳的能力。
可由下式估算固定顶罐的工作排放:
LW = 4.188 × 10-7 × M × P × KN × KC
式中:LW — 固定顶罐的工作损失(kg/m3 投入量)
KN — 周转因子(无量纲),取值按年周转次数(K)确定。
K ≤ 36,KN = 1
36 < K ≤ 220,KN = 11.467×K-0.7026 K > 220,KN = 0.26
KC — 产品因子,有机液体取 1.0
M — 储罐内蒸气的分子量,各类油按轻质油中较小值计,分子量为 220。
③装卸及管线输送和装置的无组织排放废气
主要指本项目油品装卸及加工过程中管线和装置各类阀门跑、冒、滴、漏现象引起的无组织排放废气,以非甲烷总烃计,根据建设单位多年从事化工行业的经验,在生产过程中一旦发生管线或装置阀门跑、冒、滴、漏现象,均应立即进行修复以保证项目的经济效益,一般来说因跑、冒、滴、漏损失的量极小,约占项目年加工量的 0.001%,根据本项目年加工量,建成后全厂产生量约为 0.6 t/a。
项目工艺废气进入燃烧炉燃烧,其处理效率为 99%,废气中主要含有非甲烷总烃和甲基吡咯烷酮,非甲烷总烃的燃烧产物为 CO2、H2O,甲基吡咯烷酮含有氮元素,其燃烧产物为 CO2、H2O、NOx,根据工程分析可知,项目工艺废气中含有甲基吡咯烷酮的量为 105.635t/a,其中含氮量为 105.635/99.13*14=14.919t/a,按照燃烧效率 99%计算,则转化为氮氧化物的量为 14.919*0.99=14.77t/a,按照 30%氮转化为 NO,70% 氮转化为 NO2 计算,则进入燃烧炉燃烧后烟气中 NOx 总量为14.77/14*0.3*30+14.77/14*0.7*46=43.466t/a。
工艺废气进入燃烧炉燃烧情况见表 5。
项目有组织排放及处理方式情况如表6。
4.5废水污染源强分析
项目废水主要来源于工艺废水、设备及地面冲洗废水、生活污水、初期雨水等。
项目建成后全厂污水产生总量约为 5099t/a,入污水站处理达标后排入污水处
理厂;循环水弃水作为清下水排入雨水管网。根据水平衡分析结果及相类似企业实际
情况,全厂废水产生、排放情况表 7。
4.6噪声污染源强分析
项目建成运营后噪声设备较多,主要为:燃烧炉、冷却器、冷却塔、空压
机、风机以及大功率机泵等,噪声强度在 70~100dB(A)之间。企业拟对高噪
声设备安装隔声罩,采取防振降噪措施,降低生产噪声对周围环境的影响。项目
主要生产设备的噪声源强见表8
从上表可知,项目产生的噪声源均为间断性声源,噪声的产生具有一定的突
发性。
本项目噪声源主要为各机械设备。评价中建议项目单位对噪声设备采取如下
治理措施:
(1) 设备选型:建议在满足生产要求的前提下,尽量选用低噪声设备;
(2) 合理布局:将高噪声设备尽量布置在厂区中间,远离厂界,通过距离
衰减减轻噪声对周围环境的影响;
(3)项目在厂区内部、项目边界等处尽可能加强绿化,合理配置绿化植物,
四周种植树木花草可有效降低噪声强度。
(4)加强管理:平时加强对各噪声设备的保养、检修与润滑,保证设备良
好运转,减轻运行噪声强度。
采取以上降噪措施后,项目厂界噪声可满足《工业企业厂界环境噪声排放标
准》(GB12348-2008)表 1 中的 3 类区标准,达标排放。
4.7 固废污染源强分析
项目产生的废物有滤渣、油泥、废水处理废油、生活垃圾等。生活垃圾产生
量以每人 0.5kg/d 估算,全年 320 天,全厂定员 58 人,共产生生活垃圾 9.28t/a。
项目固废产生情况汇总见表9。
4.8污染物排放汇总
项目建成后各种污染物产生量、削减量、排放量统计汇总见表 10。
5 安全生产
本工艺采取原料预处理、汽化分馏分离等目前国内外较先进的工艺技术,全过程在减压封闭的环境下进行物理分离,没有化学反应,摒弃同行业酸碱白土后段落后工艺,杜绝了废原料对环境的二次污染,所有废料都可循环利用,使固、液、气的排放严格控制在国家标准之内。利用自身的副产品作燃料,节约生产成本。真正做到了环保节能,科技再生。
6.环境保护
废气:原料在生产过程中会产生部分不可液化的气体,主要成分是C1-C4的烷烃类气体,经循环净化系统冷凝回收后,通过尾气安全回收装置,既消除了环境的污染,又节约了大量燃料。
废水、废油脱轻工艺的废水及生产过程的滴漏含油污水,统一有组织的收集,经过沉降、暴气、隔滤、收集漂浮费油入原料罐,污水进行投入表面活性剂进行进一步化学处理絮凝,然后通过砂滤、活性炭,除杂脱臭,末端泵压100目滤纸过滤后的用作生产过程中循环冷却降温水,没有任何污染,原料中的废水量很小,一般在3%左右,经水处理设备处理后可用于冷却水循环使用。
由此可见,生产中的三废都可以全部妥善解决,不会对环境造成污染,可达到良好的环保效果。综上所述,本工艺很好的满足了安全、环保、节能、高效等方面的要求,用最小的投资取得最大的效益。
7.危险废物贮存设施的安全防护与监测
7.1、危险废物贮存设施都必须按GB15562.2-1995的规定设置警示标志。
7.2、危险废物贮存设施周围应设置围墙或其它防护栅栏。
7.3、危险废物贮存设施应配备通讯设备、照明设施、安全防护服装及工具,并设有应急防护设施。
7.4、危险废物贮存设施内清理出来的泄漏物,一律按危险废物处理。
7.5、按国家污染源管理要求对危险废物贮存设施进行监测
7.节能技术措施
1、工艺、新技术采取的节能措施及其节能效果
(1)设备均选用国家推荐的高效节能产品。工艺过程采用管壳式集束换热系统,对生产过程大于80℃的液体热源全流程进行换热,逐步梯次提升工艺热工况要求。选用高效、节能的生产设备,以提高生产效率,从而减少设备数量、缩短加工周期。提高设备功效。
(2)采用了先进的生产工艺和生产设备,提高原材料的利用率,减少原材料的浪费。
2、变电系统的节电措施
(1)为了降低低压电气线路过长造成的电能消耗,在用电车间就近设变配电室,以减小低压电器线路长度。
(2)在高压开关柜和低压开关柜内采用节能高效、分断能力高的断路器,保证电力的正常运行,减少停电事故。
(3)处理设备等均选用国内节能产品,对负荷变化较大的电机采用变频调速,使其实际功率与负荷相适应,达到降低能耗、提高工作品质的作用。
(4)在灯具选择中,采用节能型光源。
3、节水措施
所有用水器具都应选用节水型产品,严格控制各用水点的水压和水量,避免管网跑、冒、滴、漏和流速过大或静压过高而造成的水资源浪费。
四、 投资分析
1、 选址及规模:根据环保要求,需要选址化工园区,面积约600~1500平米;计划设计年处理量3~5万吨以上,并拥有相当市场竞争优势。
2、 投资分析:
2.1 设备投资约400万元;
2.2 基础建设及其它投资约200万元;
蒸馏设备主要部件清单表(单台/套) 见表11
储油罐等清单表(单台/套) 见表12
3、 投资收益:
3.1.废油再生基础油产品质量/收率
3.1.1.主产品基础油的收率视原料废润滑油的情况而定,一般最好的为废液压油、4S店废机油,最差的为海运船舶柴油机油。
3.1.2.采用本工艺技术生产的产品收率(按原料不含水计算)如下:
A)轻质工业燃料油: 5~10%
(B)重质工业燃料油: 8~15%
(C)基础油: 70~85%
3.1.3.产品质量符合:中石油(Q/SY44-2009)润滑油基础油之HVI类标准。
3.2.生产成本核算
3. 2.1蒸馏部分能源成本
将1吨油加热到350℃变成蒸汽所需热量计算:
显热Q1=1000公斤×(350℃-18℃)×0.5千卡/公斤℃=166000千卡
潜热Q2=1000公斤×250千卡/公斤=250000千卡
总的热量消耗Q=Q1+Q2=416000千卡
3.2.2.天然气加热成本
A.天然气的热转换率为80%,每立方天然气的最大热量是
Q=8500千卡/立方×80%=6800千卡/立方
B.1吨油的耗液化气量为
416000千卡÷6800千卡/立方=61立方
C.工业用天然气的价格为4.3元/立方,则
每吨油费用:61立方×4.3元/立方=262.3元
3.2.3.电加热成本
设备系统动力电机等总功率160KW/h
工业电价为0.8元/度,则
每小时用电量:160X0.8元/度=128元
3.2.4.其他公用工程及人工成本
每天其他公用工程费用500元,
人工成本:200*4*3=2400元
每天处理100吨,则每吨均摊成本为(2400+500)÷100=29元
3.2.5.废油原料成本
进厂每一吨废油成本收购价1800-2000元左右
(注:其实大部分废油是不要钱,因为需要有危险废物处置单位开联单的)
3.2.6.催化剂成本
每一吨基础油催化剂成本约270元左右
3.2.7.生产1吨油总成本
1. 每吨油费用:61立方×4.3元/立方=262.3元+ 每小时用电量:160X0.8元/度=128元+每天处理100吨,则每吨均摊人工成本为(2400+500)÷100=29元+进厂每一吨废油成本收购价1800-2000元左右+每一吨基础油消耗催化剂270元
=2689元/吨
基础油销售:4800-5000元左右X85%=4080元
燃料柴油:4000-4500元左右X15%=600元
日利润:4080+600-2689=1991元/吨/每天成品X85吨X1991=利润16.9万/天
月利润:16.9万/天×25天=422.5万元
年利润:422.5万元/月×10个月=4225万元
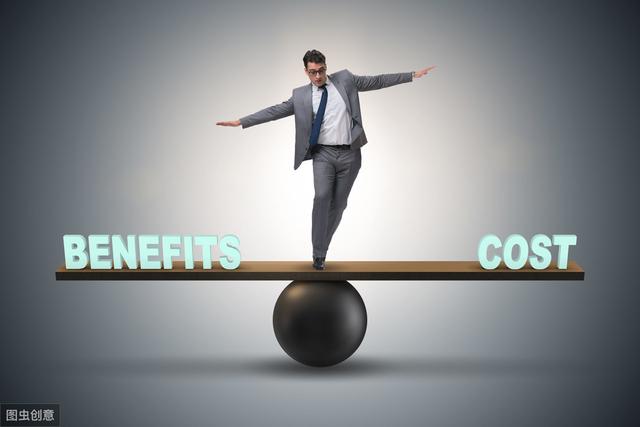
五、风险分析
1)技术风险
本项目处理的主要废油包括废矿物油、蒸馏残渣等,需要专业的工艺设计及技术支持,如果处理不当,可能会造成环境污染。项目工艺设备设计合理,制造工艺先进,自动化程度高,安全设施完备。
2)环境风险
项目废油处理过程中会产生一定量的废水、废气、固体废弃物等,需要采取适当的环境保护措施。
a废水:油品在处理过程中,会产生一些有弱酸性的废水。通过加入弱碱液中和后,把中性废水经过三级过滤,达到无害化后,排到专用的蒸发处理器(其热源采用主体处理器的烟道余热)蒸发。
b废气:主要是生产过程中产生的废气。通过两级安全装置水封和燃气喷嘴充分燃烧,
既消除了大气污染,又节约了大量的燃料。
c固废:原材料通过催化蒸馏后,会有一些固体残渣,约占原料重量的1%左右,其
主要组分是沥青。在市场上可以作为生产沥青销售。不影响环境。
3)征地风险:项目占地为工业园的土地,性质为工业用地,当地政府对项目持支持态度,征地风险较小
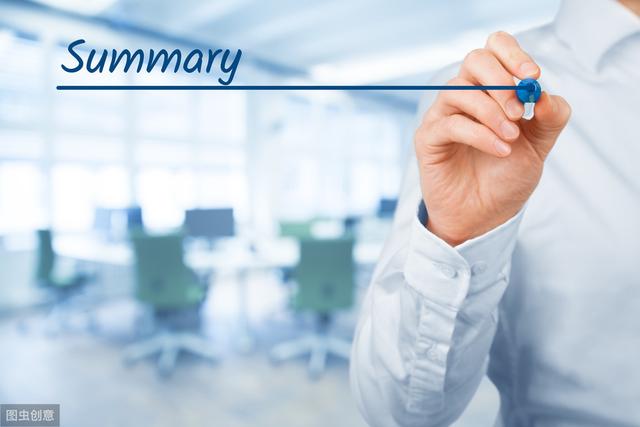
六、结论建议
根据以上分析计算表明:利用废机油炼油“变废为宝,利国利民”,在技术上先进可行,既可以节约能源、变废为宝,又可以减少其对环境的污染,废油再生循环利用具有良好的经济效益、社会效益和环境效益,符合国家相关产业政策和当地经济发展的要求。定位准确,市场广阔,工艺技术成熟、设备先进、收集、贮存、处置均有保证,综合评价,该建设项目是可行的。
在项目建设准备、建设、建成验收、项目投入阶段,做好控制预算、进度、成本、质量控制,同时注意环境保护、节能及文明安全施工、竣工验收、加强管理,使项目发挥最大效益。
编写:刘均佳 377808491@qq.
com
相关参考
...多万吨。相关专家说,润滑油市场需要资源的循环利用。废油回收利用既是环境保护,又是循环经济发展和资源综合利用的重要组成部分。以废润滑油为例,油品报废只是其中部分烃类(约10%~25%)变质,其余大部分烃类组成...
废油炼柴油(用于生物柴油?重庆这家酒店垃圾桶回收废油到底怎么回事?)
...、震惊!近日,一段重庆某酒店工作人员从垃圾桶中回收废油的视频在网上流传,让众多网友质疑是在提取潲水油,为此感到震惊和愤怒!对此,重庆长寿区市场监督管理局经过调查发通报称:经核实,两名餐饮店工作人员为长...
一、废油污染来源润滑油从机械诞生后就与之如影随行,不可缺少。随着机械化程度的增加,润滑油的使用量也随之增加,同时也产生了大量废旧润滑油。废旧润滑油中正在变质的只有3%左右,其主体仍是好的基础油。润滑油在...
【能源人都在看,点击右上角加\'关注\'】油质超标!废油处理!一直是令发电企业烦恼不已的难题看着那数以百吨计的电力用油变成劣化油发电企业:心疼!看着因为油质劣化导致机组各项性能下降,引发种种设备故障,甚至...
废油再生设备(餐饮废油变身航空燃料中国实现生物航煤绿色国际货运首飞)
...以可再生资源为原料生产的航空煤油,原料主要包括餐饮废油、动植物油脂、农林废弃物等。与传统石油基航空煤油相比,全生命周期二氧化碳排放最高可减排50%以上。2009年,中国石化成功开发出具有自主知
采用电磁加热技术,将废机油投放到高温常压电磁加热裂解釜中,加入催化剂后对废机油加热进行催化裂解和净化提取,馏出油蒸气,分解出油分,油分冷凝为混合油,再经沉淀过滤化学处理,混合油逐步净化为初级柴油,废机...
济南柴油发电机组(废油可作生物柴油使用 济南首家“无废”餐厅这样实现无废处理)
齐鲁网·闪电新闻2月16日讯在济南新旧动能转换起步区,有一家“无废”餐厅,不仅利用“按克称重、智能结算”系统实现了从源头减少食物浪费,而且餐厅目前使用的餐厨处理设备可以通过杂物分拣、固液分离、油水分离等实...
济南柴油发电机组(废油可作生物柴油使用 济南首家“无废”餐厅这样实现无废处理)
齐鲁网·闪电新闻2月16日讯在济南新旧动能转换起步区,有一家“无废”餐厅,不仅利用“按克称重、智能结算”系统实现了从源头减少食物浪费,而且餐厅目前使用的餐厨处理设备可以通过杂物分拣、固液分离、油水分离等实...
机器运转一定时间后,换下来的油,一般习惯称为“废油”,针对液压油废油过滤进行回用,可减少原油采购成本及环保成本。液压油废油过滤技术可通过特利尔物理净化技术实现工业废油在线净化循环再利用。液压油站主油箱...
机器运转一定时间后,换下来的油,一般习惯称为“废油”,针对液压油废油过滤进行回用,可减少原油采购成本及环保成本。液压油废油过滤技术可通过特利尔物理净化技术实现工业废油在线净化循环再利用。液压油站主油箱...