广东领创模架科技有限公司(汽车行业一体压铸深度研究报告:新趋势,汽车制造大变革)
Posted
篇首语:天赋如同自然花木,要用学习来修剪本文由小常识网(cha138.com)小编为大家整理,主要介绍了广东领创模架科技有限公司(汽车行业一体压铸深度研究报告:新趋势,汽车制造大变革)相关的知识,希望对你有一定的参考价值。
广东领创模架科技有限公司(汽车行业一体压铸深度研究报告:新趋势,汽车制造大变革)
(报告出品方/作者:信达证券,陆嘉敏、曹子杰)
一、汽车轻量化大势所趋,铝合金材料优势突出
1.1 政策直接推动+电动化要求,汽车轻量化大势所趋
1.1.1 政策要求推动汽车轻量化
政策直接推动汽车轻量化发展,纯电动车减重需求更为迫切。2020 年汽车工业协会发布《节 能与新能源汽车技术路线图 2.0》,要求燃油乘用车整车轻量化系数于 2025、2030、2035 年 降低 10%、18%、25%,纯电动乘用车整车轻量化系数降低 15%、25%、35%,客车整车轻量化 系数降低 5%、10%、15%。汽车轻量化的公式为 = × × 103,其中 L 为车身轻量化系数, m 为白车身骨架重量(不包含四门两盖及前后挡风玻璃),kTG为白车身静态扭转刚度,A 为白 车身四轮的正投影面积(即轮距×轴距)。由于白车身静态扭转刚度和白车身四轮的正投影 面积难以大幅度降低,因此整车轻量化系数的降低主要取决于白车身骨架重量的降低,其中 政策对纯电动乘用车的要求最高,纯电动乘用车减重需求最为迫切。
政策要求燃油车节能减排,也间接推动汽车轻量化发展。2020 年汽车工业协会发布《节能 与新能源汽车技术路线图 2.0》要求货车油耗于 2025、2030、2035 年较 2019 年降低 8%-10%、 10%-15%、15%-20%,客车油耗降低 10%-15%、15%-20%、20%-25%;乘用车总体新车平均油耗 在 2025、2030、2035 年分别为 4.6L/km、3.2L/km、2.0L/km,其中传统乘用车新车为 5.6L/km、 4.8L/km、4.0L/km,混动乘用车新车为 5.3L/km、4.5L/km、4.0L/km。这一方面是要求节能 与新能源汽车的占比提高,汽车工业协会的目标是节能汽车与新能源汽车在 2035 年各占 50%;另一方面也是要求汽车本身节能减排,由于汽车轻量化能够显著降低汽车油耗,因此 间接推动了汽车轻量化的发展。
1.1.2 轻量化帮助燃油车节能减排,助力电动车提升续航里程
燃油车减重能够降低油耗,电动车减重则可以增加续航里程。汽车行驶过程中会受到加速+ 爬坡阻力、滚动阻力和空气阻力,分别占汽车受到阻力的 35%、40%和 25%,其中加速+爬坡阻力、滚动阻力与车身重量成正相关。对于燃油车来说,整车减重 10%可以降低 6%-8%的燃 油消耗、降低 4%的排放、减少 5%的制动距离、减少 6%的转向力、提升 8%的百公里加速度; 对于电动车来说,根据《电动汽车—能量消耗率和续驶里程—试验方法》和汽车功率平衡方 程式,可知其消耗的功率 P 与汽车重量 m 正相关,而续航里程 S 则与汽车重量 m 负相关,数 据表明电动车减少 2kg 可以提升 1.5%的续航里程,减重 150kg 则可以提升 12%的续航里程。
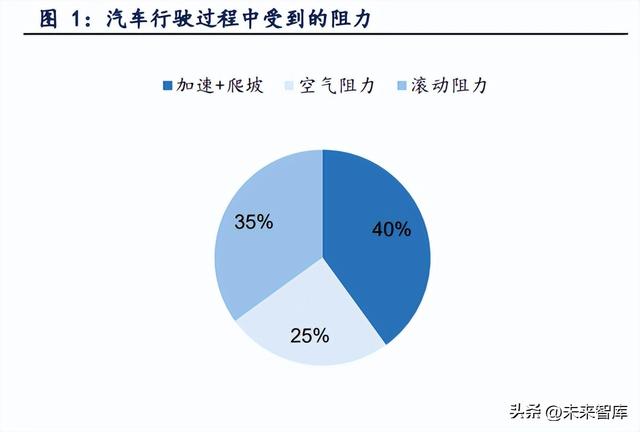
1.1.3 电动车的“里程焦虑”加速了轻量化进程
电动车电池系统更重,“里程焦虑”推动汽车轻量化。传统的燃油车发动机的重量较轻,最 常用的 4 缸发动机的重量在 90-160kg,6 缸发动机的重量在 140-200kg,8 缸发动机的重量 在 180-320kg。以宝马 3 系为例,其采用四缸发动机,整备质量为 1587kg,发动机系统的重 量占比约为 5.7%-10.1%。根据最新的 2022 年第 8 批《新能源汽车推广应用推荐车型目录》 的数据,电动车电池的重量在 209-669kg,电池重量占比在 15.1%-28.3%之间,并且随着电 动车续航里程的提高,电池重量和整备重量有提高的趋势。在“里程焦虑”背景下,电动车 对轻量化的需求更为迫切,减重也是提高电动车续航里程、降低电池成本的重要途经。
1.2 铝合金是汽车轻量化的关键材料
材料轻量化的效果最显著,是汽车轻量化的主要方法。汽车轻量化的方法分为结构轻量化、 工艺轻量化和材料轻量化。结构轻量化是指通过符合要求强度的最优结构实现材料使用的最 小化;工艺轻量化是指使用比现有材料更精细的加工来减少材料的使用量;材料轻量化是指 用轻量化材质来代替现有钢材,或者使用部分结合的方式实现轻量化。一般汽车中各材料的 使用比例为:钢铁占 64%,高分子及复合材料占 9%,铝占 8%,弹性材料占 4%,玻璃占 3%, 铜占 2%,其他材料占 10%。分结构来看,以钢材为主材的动力总成、车身、底盘以及悬挂部 分重量占比超过整车的 70%。因此,材料轻量化是效率最高、效果最显著的轻量化方式。
铝合金、镁合金、碳纤维密度远低于钢,是常见的轻量化材料。汽车常用的材料有钢、铝合 金、镁合金和碳纤维,其中钢是汽车的主要材料,但是其密度高、重量大,需要使用轻量化 材料替代。铝的密度大约为钢的三分之一,具有导热率高、耐腐蚀好、加工性能优良等优点, 并且铝合金比钢更能吸收碰撞能,大约是钢的 2 倍,能够有效提高汽车的碰撞安全性;镁的 密度为铝的三分之二,钢的四分之一,是实际应用中质量最轻的有色金属材料,具有很高的 比强度和比刚度,还具有阻尼减震、散热性好和容易回收等优点;碳纤维材料的密度较铝更 低,具有耐腐蚀、比强度和比刚度高等优点。
铝合金密度小,价格较低,适合作为汽车轻量化的替代材料。传统汽车使用普通钢,轻量化 的替代材料主要有高强度钢、铝合金、镁合金、金属+碳纤维和碳纤维,其中碳纤维价格过 高,使用量较少。价格上,2022 年 10 月 10 日我国镁锭、铸造铝合金、螺纹钢的价格分别 为 27000、20300、4090 元/吨,铝的价格约为生铁的 5.0 倍,镁的价格约为生铁的 6.7 倍。 结合大众、奥迪等欧洲品牌的轻量化技术路线来看,使用铝合金能够降低车身 40%的重量, 镁合金能够降低车身 49%的重量。我们认为铝、镁均适合作为汽车轻量化的替代材料,其中 铝的价格较低,轻量化比率完全符合汽车工业协会 2035 年的要求,是一种性价比较高的选 择。
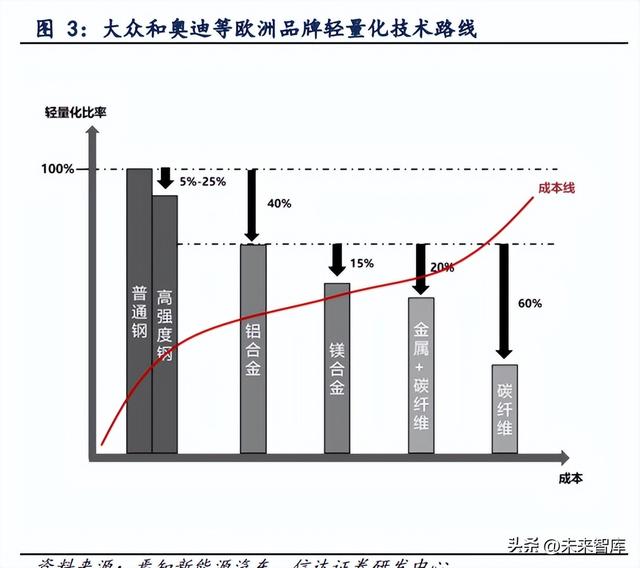
参考飞机轻量化过程,飞机轻量化经历了钢→铝→复合材料的过程。在第一阶段,飞机的结 构较为简单,主要用到的材料有木材、蒙布、金属丝、钢索等,早期飞机用木三夹板、木条 等来做飞机大梁和飞机骨架,采用亚麻布做机翼的翼面;在第二阶段,许多国家逐渐用钢管 代替木材做机身骨架,用铝板做蒙皮,制造出全金属结构飞机;在第三阶段,美国道格拉斯 公司出产的 DC-T 机发动机的防火壁和短舱上首次使用了钛材,后期钛合金开始被应用于飞 机上,主要是发展航空发动机用的高温钛合金和机体用的结构钛合金;在第四阶段,机体主 要是铝、钛、钢、复合材料结构。以铝为主;在第五阶段,机体主要是复合材料、铝、钛、 钢结构,以复合材料为主。对比飞机轻量化的发展历程,我们认为当前阶段汽车轻量化的核 心材料为铝。
纯电动车铝材渗透率快速提高,未来十年间单车用铝量翻倍增长。根据国际铝业协会的数据, 纯电动车整体单车铝用量、渗透率均高于燃油车,具体而言,2018 年纯电动车单车铝用量 为 128.4kg,整体渗透率为 31%,预计 2025 年单车铝用量为 226.8kg,整体渗透率达到 50%,2030 年单车铝用量进一步提升至 283.5kg,渗透率为 56%,细分来看,2018-2030 年底盘和 悬架、车轮和制动器、车身封闭件绝对铝用量提升较大;2018 年燃油车单车铝用量为 118.7kg, 渗透率为 24%,预计 2025 年单车铝用量为 179.8kg,渗透率达到 38%,2030 年进一步提升至 222.8kg,渗透率为 44%,细分来看,2018-2030 年车身结构、底盘和悬架绝对用铝量提升较 大。
汽车铝材市场广阔,2030 年有望达到 3292 亿元。市场规模的测算基于以下假设:1)2021 年我国新能源汽车的销量为 352 万辆,我们预计 2030 年达到 1909 万辆,年复合增速为 21%, 其中混动约为纯电动汽车销量的四分之一,燃油车销量随新能源汽车的渗透率提高而下滑, 2030 年销量为 748 万辆;2)根据国际铝业协会的统计数据,2021 年纯电动、混动、燃油车 的单车铝用量分别为 173、207、145 千克,预计 2030 年分别达到 284、265、223 千克;3) 我们预计 2022 年汽车铝材价格为 44 元/千克,整体呈波动上行的态势。波动上行是因为铝 一般由电解制成,电解是高耗能工艺,能耗双控大背景下铝产能受限,需求不断提升,因此 未来铝价中枢有望提升。综上所述可得 2021 年纯电动、混动、燃油车汽车铝材的市场规模 为 232、69、1569 亿元,2030 年分别为 2033、476、783 亿元,年复合增速分别为 27%、23%、 -7%,汽车铝材总规模从 2021 年的 1870 亿元增长至 2030 年的 3292 亿元,年复合增速为 6%。 我们认为汽车铝材市场处于蓝海市场,整个市场空间有望达到 3000 多亿元,在汽车电动化 的大背景下,纯电动车、混动车的铝材的成长性更好,2021-2030 年年复合增速有望超 20%。
二、一体化压铸新趋势,汽车车身制造迎来大变革
2.1 传统车身制造工艺难以适应铝合金用量提高的趋势
传统汽车主要使用钢材,车身制造主要由冲压、焊装、涂装以及总装四大工艺构成。冲压: 利用压机对钢板施加压力,使其模具中成型。主机厂的冲压车间主要负责生产高质量要求的 大型外覆盖件(侧围、发动机盖、翼子板、门外板等);内部的结构件由各零部件供应商负责 制造,主机厂采购。焊装:冲压好的车身板件局部加热或同时加热、加压而接合在一起形成 车身总成。涂装:对焊接完成后的车身总成进行防腐和喷漆处理,起到保护和装饰作用。总 装:将车身、发动机、变速器、仪表板、车灯、车门等构成整辆车的各零件装配起来生产出 整车。
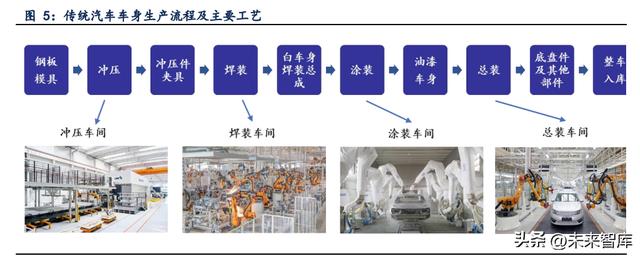
传统车身制造工艺有车身重、灵活度低、成本高、效率低、零件强度低等痛点,难以适应铝 合金用量提高的趋势。车身结构件较多,传统车身制造工序较为复杂,具体包括了发动机盖、 翼子板、车门、侧围等大型外覆盖件的冲压,并将覆盖件与结构件焊接形成白车身总成,共 计由 300-500 个零部件构成,焊接点位高达 4000-6000 个。传统车身制造工艺存在以下痛 点:1)车身重:传统工艺加工铝合金难度高,全铝车身普及受限;2)灵活度低:造型灵活度低,难以进行多零件一体成型;3)成本高:数百个零部件+数千个焊点导致设备成本(主 要指模具)、制造成本、人力成本较高;4)效率低:众多零件生产和焊接工序耗费大量时间, 生产效率低;5)零件强度低:材料本身强度低以及多零件安装焊接强度更低。
铝合金焊接复杂,现有工艺难度大,成本高。铝合金具有表面的氧化层熔点较高等特性,采 用传统熔化焊存在热输入过大引起的变形、气孔、焊接接头系数低等问题,同时由于型材的 厚度、断面都各不相同,在焊接时就产生了很多种组合,尤其在厚度差异很大时,热输入非 常难以控制,因此传统焊接工艺无法满足铝合金材料的连接要求。目前采用的解决方法一类 是发展先进焊接技术,包括主流的摩擦搅拌焊以及更加先进的激光焊,另一类是发展新型连 接技术包括冲铆技术、螺栓自拧紧技术和胶接技术,但采用新型焊接和连接技术的方案在提 高工艺难度的同时还会增加设备和时间成本。以奥迪 A8 为例,其车身结构材料中 70%为铝 合金,20%为热成型钢,镁合金和其他材料的比例不超过 2%;为使铝合金和热成型钢材等材 料实现链接,其采用了 16 种连接技术,复杂的连接工艺增加了制造难度,提高了制造成本。
2.2 一体化压铸重塑车身制造工艺
汽车铝合金加工工艺分为铸造和形变,其中铝铸件的用量最高。铸造铝合金是指将铝合金加 热至熔融状态,流入模具中冷却成型后加工成汽车零部件;形变铝合金是指通过冲压、弯曲、 轧制、挤压(非挤压铸造)等工艺使其组织、形状发生变化的铝合金。实际应用中铸造铝合金 一般用于结构更加复杂的部件,例如发动机气缸、汽车摇臂、轮毂、变速箱壳体等耐久性要 求高、结构更为复杂的位置,形变铝合金则适用于结构较为简单、对机械性能要求更高的汽 车部位。根据《铝合金在新能源汽车工业的应用现状及展望》的统计数据,2017 年我国铸造 铝合金约占汽车铝合金市场份额的 77%,形变铝合金的市场份额则为 23%。
铝合金压铸具有产品质量好、生产效率高、经济效果优良的优势。压铸是铸造工艺中最成熟、 效率最高的制造技术之一,目前在汽车铸件中占比超 70%。产品质量好:铝铸件尺寸精度高, 表面光洁度好,强度和硬度较高,强度一般比砂型铸造提高 25-30%,但延伸率降低约 70%, 尺寸稳定,互换性好,并且可压铸铝薄壁复杂的铸件。生产效率高:铝铸件的压铸模使用次数多且适用于大批量生产,例如国产 JⅢ3 型卧式冷空压铸铝机平均八小时可压铸铝 600- 700 次,小型热室压铸铝机平均每八小时可压铸铝 3000-7000 次。经济效果优良:由于压铸 铝件尺寸精确,表泛光洁等优点,一般不再进行机械加工而直接使用,或加工量很小,所以 既提高了金属利用率,又降低了加工设备的用量和人员工时。
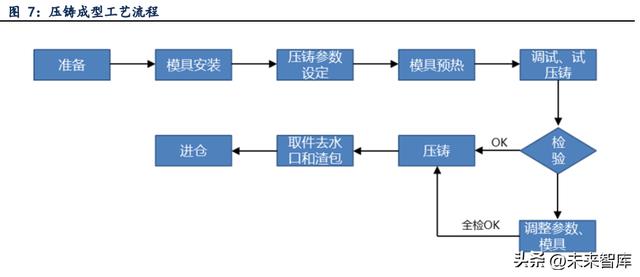
高压压铸是生产铝铸件的常用工艺,流程可分为合模、配汤、 射出、开模、产品顶出等, 是指将液态或半固态金属或合金,或含有增强物相的液态金属或合金,在高压下以较高的 速度填充入压铸型的型腔内,并使金属或合金在压力下凝固形成铸件的铸造方法。压铸时 常用的压力为 4~500MPa,金属充填速度为 0.5—120m/s。金属液的充型时间极短,约 0.01—0.2 秒(须视铸件的大小而不同)内即可填满型腔,高压、高速是压铸法与其他铸 造方法的根本区别,也是重要特点。
高压压铸铝铸件力学性能较弱,业内有降低压力、降低速度、减少空气含量三种技术升级 路线。高压压铸工艺具有成型精密、生产效率高等优点,但由于高速压射时模具型腔中的 气体不能被有效排除,会形成气孔缺陷,导致铸件力学性能相对较弱。为了满足汽车零部 件的性能与质量要求,业内产生了降低压力、降低速度或者减少空气含量三种主要技术升 级路径,其中低压/差压压铸通过降低填充压力以提高铸件内部质量,设备操作难度增加, 工艺效率有待提升;超低速压铸可降低工艺压射速度,但生产效率大幅降低,且会对后续 清理工作带来困难;真空压铸减少型腔中空气含量,设备成本较高,对工艺技术要求高。
一体化压铸采用超高真空高压压铸工艺,能够实现多个铝合金零件的一体化成型。一体化压 铸是指采用特大吨位压铸机,将多个单独、分散的零部件高度集成,压铸一次成型为几个大 型铝铸件,从而替代多个零部件先冲压再焊接或铆接组合的方式。一体化压铸是对传统压铸 工艺的全方位升级:(1)生产效率高:大型压铸机一次压铸加工时间通常在 80-90 秒,每小 时能够完成 40-45 个铸件生产,每天生产铸件数接近 1000 个,而传统加工流程需要 1-2 小 时,优势明显;2)材料回收利用率高:废料回收可直接融化,重新铸造,回收利用率约 95%; 3)维护成本较低:无需排查每个零部件的制造状态,节约大量人力和时间;4)品控进一步 提升:零部件数量减少使得误差累计大幅减少。
一体化压铸能够显著降低传统铝合金加工工艺的连接成本。根据信公咨询数据,传统钢制车 身的重量约为 350-350kg,当前钢材价格约为 8 元/kg,预计全钢车身材料成本为 2800-3600 元,白车身焊接点以 3000 个进行计算,每个焊接点焊接成本 0.2 元,连接成本 600 元,合 计成本在 3400-4200 元;以铝合金用料多的奥迪 A8 做测算,假设钢铝混合车身、全铝车身 的重量分别为 280、200-250kg,当前铝合金的单价为 20 元/kg,每个焊接点焊接成本为 0.65 元,以此推算出钢铝混合冲焊车身、全铝冲焊车身、一体化压铸铝合金车身的综合成本分别 为 5666、5950-6950、4195-5195 元,一体化压铸铝合金车身工艺通过减少焊接点显著降低 了加工成本。
2.3 特斯拉引领,产业链上下游积极布局
2.3.1 特斯拉引领一体化压铸工艺发展
采用一体化压铸技术的 Model Y 实现了降本增效。特斯拉率先于 2020 年采用一体化压铸技 术,其 Model Y 将采用一体式压铸后底板总成,具有以下优势:(1)总重量下降 30%,制造 成本下降 40%;(2)零件数量较 model 3 减少 79 个,焊接点由 700-800 个降低至 50 个;(3) 不需要进行热处理,制造时间由 1-2 小时缩短至 3-5 分钟。2022 年 Model Y 实现将 171 个 独立零件已简化成 2 个大型压铸单体零件,工厂所需机器人数量也减少到一半左右。
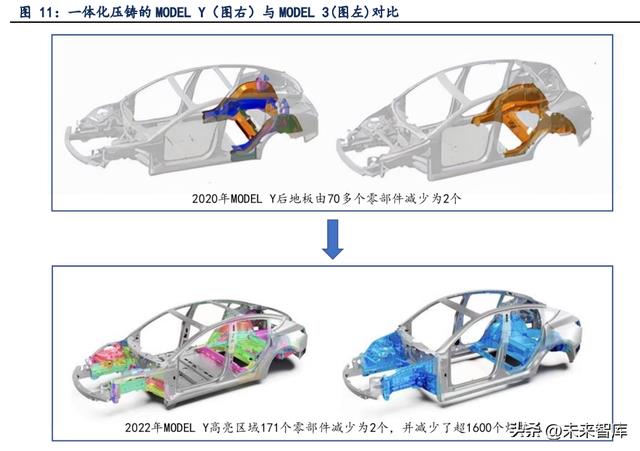
一体化压铸最新进展:一体式前后车身与电池包形成的三合一底盘。特斯拉 Model Y 可使 用第三代 4680 电芯采用全新的一体式底盘电池包,一体化压铸的前后车身与电池包形成了 三合一底盘,新结构拥有很高的结构强度和刚度,并且在电芯布置得更为集中之后还降低了 车辆的转动惯量,更有利于操控和转向响应。此外三合一底盘实现了 10%的轻量化,提高了 14%的续航潜力,并减少了 370 个车身零部件。
2.3.2 产业链上下游积极布局
一体化压铸产业链的上游为压铸机、材料与模具厂商,中游为铝合金压铸厂,下游为主机厂。 一体化压铸有两种业务模式,一种是自研模式:主机厂直接采购压铸机、材料和模具等物料, 自建工厂生产压铸件,代表车企有特斯拉、小鹏和沃尔沃;另一种为采购模式:主机厂直接 向压铸厂商采购压铸件,由压铸厂商采购相关的物料,生产压铸件后交付给主机厂,代表车 企有高合、蔚来、理想。当前自研模式的代表企业特斯拉已经开始与压铸厂商接触,长期来 看,由于主机厂自建厂房与产线成本较高,并且汽车销量可能会成为产能利用率的压制因 素,因此采购模式有望成为长期主流。
大型压铸机是汽车实现一体化压铸的基础。一般来说一体化压铸所需要的压铸机锁模力都 在 6000T 以上,当前全球能生产 6000T 压铸机的企业有海外的意德拉集团(力劲科技全资 子公司)和瑞士布朗集团,国内的力劲科技、海天金属和伊之密。更大吨位的压铸机意味着 压铸件的尺寸和结构可以进一步突破,目前特斯拉、力劲科技、广东鸿图、海天金属等企业均在研发 12000T 以上的压铸机。2022 年 9 月,力劲科技与广东鸿图发布 12000T 超大型智 能压铸单元,这是迄今为止全球最大吨位的压铸机,有望助力整车级别一体化压铸件。
模具是一体化压铸的核心工具,壁垒较高。模具是为强迫金属或非金属成型的工具,可以分 为成型部分、浇注系统、模架部分、排溢系统、温控系统等部分,是工业生产中必不可少的 工艺装备,模具生产得到的零部件具有高效率、高一致性、低耗能耗材、精度/复杂度较高的 特点。模具制作的难点在于模具设计和原材料的选取,大型一体化压铸要求模具高精密度, 这提高了模具制作的难度。一般压铸厂商不具备大型压铸模具的设计能力,通过外部采购来 满足需求,目前我国的大型压铸模具厂商主要有广州型腔、宁波臻至、宁波赛维达、文灿雄 邦、合力科技和重庆广澄模具,此外德国著名模具公司肖弗勒模具集团也于浙江建厂。
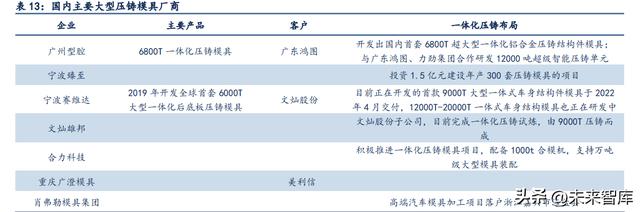
免热处理合金材料能够提高一体化压铸的良品率,从而降低成本。铝合金的热处理分为铸锭 均匀化退火、回复再结晶退火、固溶(淬火)热处理、时效、形变热处理,传统铝合金需要 通过热处理提高铝合金的强度、塑性、韧性、耐蚀性、疲劳性等综合性能。一体化压铸的大 型铝合金部件对精度要求较高,热处理过程易引起汽车零部件尺寸变形及表面缺陷,虽然通 过矫正工艺可以改善一定的尺寸精度,但会降低良品率,导致成本急剧上升,因此免热处理 铝合金材料是大型一体化压铸结构件的关键。国外免热处理铝合金材料厂商主要有美国铝 业、德国莱茵菲尔德和特斯拉,国内厂商正在积极研发,目前立中集团、上海交大、广东鸿 图、湖北新金洋已研制成功。
中游压铸厂商纷纷布局一体化压铸,文灿、鸿图、拓普等较为领先。文灿股份、广东鸿图、 拓普集团、旭升股份等中游压铸厂商分别采购大型压铸机,其中文灿股份、广东鸿图、拓普 集团在经验积累和订单获取上具有先发优势,三者与车企建立合作并开始试制一体化压铸件。 此外,文灿股份多个已经获得定点的一体化压铸产品均试制成功,包括半片式后地板、一体 式后地板、前舱和上车体一体化大铸件,后续产品将进入到小批量交样过程中,公司预计在 今年 4 季度开始贡献收入。
特斯拉、蔚来、小鹏、理想、高合、沃尔沃、长城等车企已布局汽车一体化压铸领域。新势 力方面:目前特斯拉采用一体化压铸后地板的 Model Y 已正式交付,国内蔚来采用一体化压 铸后副车架的 ET5 即将交付,小鹏、理想、高合、与华为深度合作的赛力斯汽车的一体化压 铸已提上日程,估计在 2023 年将陆续上车,此外小米汽车搭载一体化压铸的车型有望于 2024 年实现量产;传统车企方面:包括大众、沃尔沃在内的国外传统车企在一体化压铸布局时间线比较长,预计在 2025 年左右才能实现量产,国内车企中,长安、长城已开始了项目的招 投标,估计未来两三年内将实现量产。
2.4 一体压铸工艺尚有待发展成熟,长期市场空间广阔
一体化压铸的壁垒在于:(1)工艺壁垒:填充流程很长,易出现填充不足、冷格、压铸缺陷、 毛坯变形,工艺的好坏决定了良品率的高低;(2)资金壁垒:大型设备采购价格较高, 7000T/9000T/12000T 的压铸机单价约为 7000/9000/12000 万元,需要大量生产降低边际成 本,回收设备成本周期长;(3)材料壁垒:免热处理材料技术复杂,国产材料厂商大多难以 满足材料的强度和可加工性,并且非热处理材料也有劣势,没有固溶等过程,要靠压铸本身 得到良好性能,还要兼顾强度、韧性、延伸率,对铝液纯净度、含气量、成分配比、真空度、 温度、参数、冷却润滑工艺等都要求较高。 一体化压铸较传统工艺也存在一些劣势:(1)售后维修成本较高:由于零件一体化成型,可修复性降低,维修成本提高,所以目前生产的多为不易碰撞部位;(2)运输成本高:大型一 体化压铸件没有小件灵活,运输成本高,需要就近建厂、就近供货,因此需要与主机厂签订 长期合作协议。(3)折旧成本高,大型一体化压铸设备成本高,如果配套车型销量低将会产 生较高的折旧成本。 因此,现阶段一体化压铸工艺将主要应用于非关键、不易损坏的底盘部件,未来随技术成熟, 应用范围有望逐步拓宽,从一体化压铸的难度来看,实现先后顺序可能是后地板、前地板、 中地板、结构件。虽然仍有良品率、工艺、产能等问题需要克服,但我们认为一体化压铸是 汽车车身加工工艺的未来重要发展趋势,先进入厂商有望形成卡位优势,在未来收获较大的 行业红利,此外,考虑到大型一体化压铸件或对车身部分中小压铸件形成替代,未及时布局 一体化压铸的技术的厂商长期或面临被市场淘汰的风险。
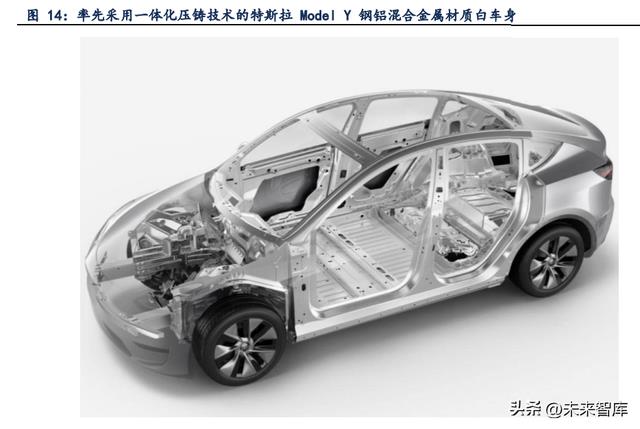
一体化压铸设备市场份额快速增长,2025 年有望超百亿,年复合增速为 136%。我们采用信 公咨询的统计数据,假设:(1)根据 2021 年及截至 2022 年 9 月各大新能源厂商销量数据, 预测出 2022 年的销量,并在 2022 年-2025 年以每年 30%的销量增速增长,在 2026 年-2030 年以每年 20%的销量增速增长;(2)后地板、前地板、中地板分别对应 7000、9000、12000T 的压铸机,单价分别为 7000、9000、12000 万元;(3)一台大型一体化压铸机的年产能为 10 万个压铸件,再结合产能利用率的爬坡以及压铸件数量需求,从而计算出各家新能源车企对 压铸机的需求。以此测算 2021 年一体化压铸设备的市场规模为 3.5 亿元,2025、2030 年分 别达到 108.9、652.9 亿元,年复合增速分别为 136%、79%。
一体化压铸部件空间广阔,2025 市场规模有望达到近 500 亿元。根据信公咨询统计数据, 新能源汽车一体化压铸后地板、前地板、中地板的重量分别为 50-60、110、70kg,按照 50- 60 元/kg 的定价模式,单车价值量分别约为 3000、6000、3850 元。结合此前假设,测算出 2021 年一体化压铸部件的市场规模为 2.9 亿元,预计 2025 年、2030 年分别达到 476.4、 2021.1 亿元,年复合增速分别为 258%、225%。
三、投资分析
3.1 中游压铸厂商积极布局,业绩释放在即
3.1.1 文灿股份:一体化压铸即将量产,有望于四季度开始贡献收入
国内领先的汽车铝合金铸件研发制造企业,已实现全球化布局。公司成立于 1998 年,总部 在南海区里水镇,2020 年完成了对法国百炼集团的收购,在江苏南通、无锡、天津、大连、 武汉及墨西哥、匈牙利、塞尔维亚、法国等地设有 17 个生产基地。公司掌握高压铸造、低 压铸造和重力铸造等工艺方式,主要从事汽车铝合金精密铸件产品的研发、生产和销售,致 力于为全球汽车客户提供轻量化与高安全性的产品。
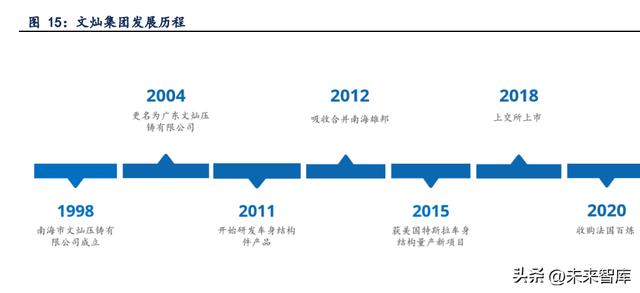
百炼集团整合著有成效,新能源业务驱动公司业绩增长。2017-2021 年公司营业收入由 15.57亿元增加至 41.12 亿元,年复合增速达 27%;受汽车行业低迷影响 2019 年归母净利润仅为 0.71 亿元,此后随着行业景气度提升,叠加新能源产品的快速放量,公司业绩企稳回升。 2022 年 H1 公司实现营业收入 24.42 亿元,同比+20.15%,归母净利润 1.36 亿元,同比 +85.82%;主要原因系客户缺芯缓解,公司销售订单得到恢复,收入带来增长,且新能源汽 车客户和新能源汽车产品收入占比提高,带动公司毛利增长。
公司与国内外知名汽车整车厂商及一级零部件供应商建立了稳固的合作关系,如大众、奔驰、 宝马、奥迪、雷诺等国际知名整车厂商,特斯拉、蔚来汽车、理想汽车、小鹏汽车、广汽新 能源等新能源汽车厂商,比亚迪、吉利、长城汽车、赛力斯等国内知名整车厂商,以及采埃 孚、博世、大陆、麦格纳、法雷奥、本特勒等全球知名一级汽车零部件供应商。此外,公司 在 2021 年还与亿纬锂能、欣旺达及阳光电源等知名电池厂商建立了合作关系。
一体化压铸即将实现量产,有望于 Q4 开始贡献收入。2022 年上半年,天津工厂和南通工厂 9000T 压铸机已完成新势力客户定点的大型一体化产品试制,这是公司继 2021 年 11 月 6000T 压铸设备上首次完成半片式后地板的试制后,时隔不到半年内再次在一体化铸件领 域取得突破,充分彰显公司在大型一体化产品领域的先发优势。公司目前已经获得产品定点 的一体化压铸产品均取得了产品试制成功,包括半片式后地板、一体式后地板、前总成项目 和上车体一体化大铸件,后续产品将进入到小批量交样过程中,公司预计在 2022 年第四季 度开始贡献收入。
3.1.2 广东鸿图:积极研发相关技术,一体化压铸进度较快
铝压铸龙头,聚焦主业并积极拓展业务。公司成立于 2000 年,专注于精密铝合金压铸件的 设计和生产制造,产品主要用于汽车、通讯和机电行业。公司先后于 2011 年和 2013 年分别 在南通和武汉成立两家压铸子公司,2016 年收购宝龙汽车 60%股权,实现从汽车零部件延伸 至整车、新能源汽车等领域的产业战略布局;2017 年购买宁波四维尔 100%股权,产品线延 伸至汽车内外饰件领域。
低点已过,业绩有望触底反弹。受汽车行业低迷影响 2019 年公司归母净利润达到低点,此 后触底反弹。2022 年 H1 公司实现营业收入约 29 亿元,同比-2.35%,变动原因为长春四维 尔于 2021 年 5 月完成股权转让,若 2021 年同期数据同步剔除长春四维尔影响,则同比 +6.14%。其中,汽车类压铸件产品实现营业收入 20.83 亿元,同比增长 10.38%。2022 年 1 月,压铸板块成功下线国产最大尺寸 6800T 超大型一体化铝合金压铸结构件,并率先布局全 球首台最大吨位 12000T 压铸装备及产品的开发与导入工作。
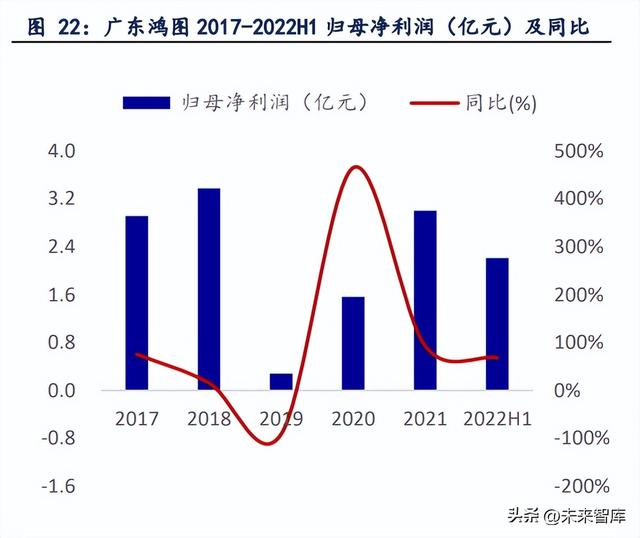
技术研发获新突破,一体化压铸成型技术国内领先。公司具备强大的技术研发自主保障能力, 专利、标准、技术奖项处于行业第一,掌握一体化压铸产品从结构同步设计、材料、模具设 计与制造,生产过程控制、精密加工、装配全流程工艺技术。2022 年 H1 公司研发投入约 1.33 亿元,同比增长 11.64%。2022 年 5 月,公司表示其自主研发的免热处理铝合金材料已获得 国家授权发明专利,该专利材料性能及使用成本对比国内外同类产品均处于领先水平,并已应用于一体化压铸产品开发试制。
一体化压铸进度较快,顺利收到客户定点。2022 年 1 月,公司开发的 6800T 新能源汽车超 大型一体化铝合金后地板压铸结构件产品成功试制,一体化结构件的试制成功标志着本公司 成为国内首家掌握超大型一体化铝合金结构件压铸生产技术的民族品牌企业,攻克了超大型 一体化压铸的产品设计、新材料开发、工艺设计、装备制造等难题,实现了超大型一体化压 铸技术的国产自主可控;同时还将向力劲科技集团采购包括 2 套 12000T 压铸单元在内的 8 套大型及超大型智能压铸单元。2022 年 6 月收到小鹏汽车发出的定点开发通知,公司成为 其某车型底盘一体化结构件产品的供应商。
3.1.3 旭升股份:深耕铝压铸零部件,多维度布局一体化压铸
公司成长可以分为四个阶段:初创阶段(2003-2007)、巩固阶段(2008-2011)、转型发展阶 段(2012-2015)、加速扩张阶段(2016 至今)。 1)初创阶段和巩固阶段期间,公司的主要业务是铝压铸工业件。公司成立于 2003 年,开始 从事模具加工业务,成立初期就为公司的主要客户海天塑机提供注塑机零配件,2005 年开 始为上海艾热性能泵有限公司提供泵头、泵体等产品,并在巩固阶段与这些主要客户建立了 长期合作关系。 2)转型发展阶段开始,公司进军新能源汽车市场。公司在此阶段逐步转型新能源车铝压铸 零部件,2013 年开始与特斯拉合作,逐步成为特斯拉的一级供应商,从个别零件起步,逐步 生产变速箱、电池组件等特斯拉的核心零部件,并开始供应装配完毕的油泵等部件。2016 年 开始新能源汽车迎来快速增长,特斯拉业绩进入高速通道,公司的产能、业绩也快速增长。 目前公司已经成为了汽车精密铝合金零部件龙头之一。
公司产品以新能源汽车零部件为主,工业、模具类为辅。公司目前产品分为三个部分,汽车 类、工业类、模具类。汽车类产品覆盖新能源车传动系统、悬挂系统、电气系统、电池系统、 液压系统等核心系统零部件;工业类产品包括清洗机配件、电机配件、注塑机配件等;模具 类产品主要是铝压铸产品的壳体,公司拥有自主设计模具的技术。
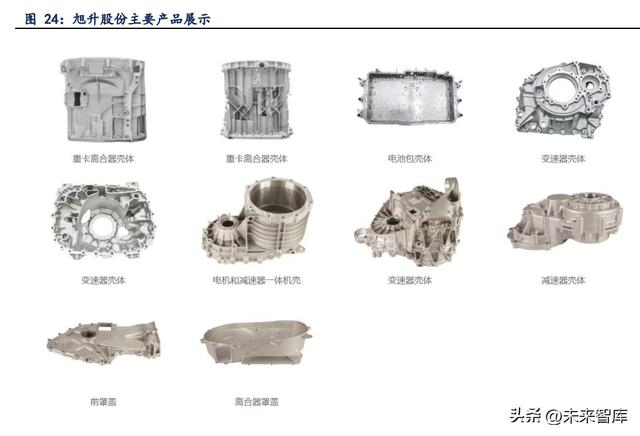
公司业绩进入高速增长阶段。2019-2021年,公司营业收入从10.97亿元增长至30.23亿元, 整体保持快速增长的趋势,年复合增速为40.20%。2019-2021年及2022H1,公司归母净利分 别为2.07、3.33、4.13、2.75 亿元,同比增长-29.66%、61.10%、24.16%、30.28%。在全球 绿色低碳转型的政策环境下,特斯拉、长城等国内外主要新能源汽车厂商的产销有望进一步 提升,汽车零部件企业将随之受益,公司业务规模有望进一步扩大。
全球化客户体系加深现有业务领域的优势地位。公司客户资源已覆盖了“北美、欧洲、亚太” 三大全球新能源汽车的主要消费地区。除公司早期客户特斯拉外,在新能源领域声望较高的 车企大多成为了公司的客户,业务合作随着公司产能建设进度而不断深化,包括 Rivian、 Lucid、Polaris(北极星)、比亚迪、长城汽车、蔚来、理想、小鹏、零跑等。此外,采埃 孚、法雷奥、西门子、宁德时代、赛科利、亿纬锂能等一级零部件供应商亦是公司的重要客 户。
多维度布局一体化压铸。公司密切关注一体化压铸的发展动态,认可一体压铸未来的发展趋 势,也已经做了一些前期准备工作,公司已做好材料、模具、设备配套设施等的储备;但是 目前一体化压铸还处于前期阶段,在产品验收标准的确认、产品产量的稳定性、由主体厂自 制还是交由供应商供货模式等商务条款还需确认。公司会在充分的商业条款落地以后择时快 速切入。截至 2022 年上半年,公司已积累了大吨位压铸机(4400T)的使用经验、大吨位模 具的设计与制造能力,并积极与主机厂进行沟通交流。随着大吨位压铸机(8000T 及以上) 的采购到位和方案的落地,将快速推动公司一体化压铸的进展。
3.1.4 拓普集团:车身底盘多域 Tier0.5 平台型供应商,进军一体化压铸领域
国内 NVH 领域龙头,进军一体化压铸领域。1983 年创立,总部位于中国宁波,在汽车行业 中专注笃行近 40 年。早期主要从事汽车 NVH 业务,2000 年成立第一家 NVH 研发中心,2015 年在上交所上市,2016 年公司在巴西设立首家海外工厂,开启全球化产业布局,2021 年, 公司橡胶减震产品实现营收 33.47 亿元,同比+30.73%,同时公司于 2021 年进入车身一体式 铸造领域。
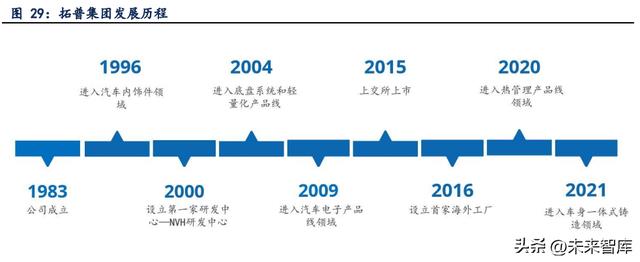
公司产品线丰富,实现全球化产业布局。公司主要产品包括汽车 NVH 减震系统、内外饰系 统、轻量化车身、智能座舱部件、热管理系统、底盘系统、空气悬架、智能驾驶系统共八大 业务板块;除汽车业务外,公司积极布局机器人产业,公司的运动执行器包括电机、电控及 减速机构等部件,样品已获得客户的认可,后续发展潜力较大。公司已在全球设立 5 家研发 中心,40 家以上子公司,60 家以上制造工厂。
“内饰+NVH”是主要收入来源,底盘系统成长性较好。公司 2022 年 H1 实现营业收入 67.94 亿元,同比+38.18%;实现归母净利润 7.08 亿元,同比+53.97%;其中,内饰功能件和减震 器分别实现营业收入 21.50 亿元、18.33 亿元,毛利率贡献率分别为 17.21%、23.37%。近 年来,底盘系统增长速度较快,2022 年上半年实现营业收入 17.84 亿元,较上年增长 100. 47%。
与力劲集团、华人运通战略合作,布局一体化压铸。2022 年 2 月 25 日,拓普集团与华人运 通 7200T 一体式后舱下线仪式在拓普集团杭州湾制造基地举行,该超大型结构件采用力劲 7200T 超大型智能压铸单元一体化压铸成型,长、宽分别近 1700mm 和 1500mm,实现了 15%- 20%的减重效果,随着一体化超大压铸后舱的顺利下线,标志着拓普集团成为了国内首个量 产超大型一体化铝合金结构件制造技术的汽车零部件供应商。2021 年,拓普集团已签约采 购 21 台套力劲大型智能压铸装备,包括 6 台套 7200 吨、10 台套 4500 吨和 5 台套 2000 吨 的智能压铸单元,主要用于新能源汽车超大型结构件,如前机舱、后车体及电池壳体等产品 的生产制造。
3.1.5 爱柯迪:国内领先的汽车铝合金精密压铸件专业供应商
国内领先的汽车铝合金精密压铸件专业供应商。成立于 2003 年,主要从事汽车铝合金精密 压铸件的研发、生产及销售,营业收入中 90%以上来自汽车类压铸件。公司聚焦汽车轻量化、 节能环保、新能源、电动化、自动驾驶方向。2014 年公司在墨西哥注册成立子公司 IKDFAEZA, 启动建立第一个海外生产基地,2017 年上交所上市。
公司产品从中小铝合金压铸件向中大件新能源汽车、智能化产品拓展。主要产品以中小型零 部件为主,具有产品数量较多,品种繁多,多批次、多家客户工厂发运等特点。根据爱柯迪 智能制造科技产业园环评信息的产品方案显示,新能源汽车车身部件的规格为 40 千克,新能源汽车电池系统单元产品的规格为 10 千克,较公司传统中小件产品的规格有较大增加。 据公司招股书,公司传统产品结构中占比最高的是 100-200 克,其次是 200-300 克,然后是 100 克以下,公司预计 300 克以下产品占比合计接近 60%。
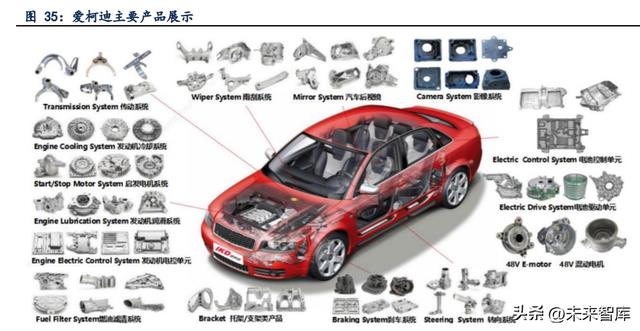
新能源汽车+智能驾驶带动公司整体业绩增长。公司 2022 年 H1 实现营业收入 18.33 亿元, 同比+16.66%;实现归母净利润 2.13 亿元,同比+7.51%;其中,汽车类压铸件实现营业收入 16.87 亿元,占总营业收入 92%以上。公司明确“新能源汽车+智能驾驶”的产品定位,新能 源汽车市场占有率稳定提升,新能源汽车用产品销售收入同比增长约 200%,智能驾驶系统 项目(激光雷达、视觉系统、中控系统等)快速增长。
募集资金购置大吨位压铸机,积极布局一体化压铸。2022 年 9 月,公司发行可转换公司债 券募集资金 15.7 亿元,用于爱柯迪智能制造科技产业园项目。该项目拟购置 45 台压铸机, 其中拟购 1000T 以上压铸机 35 台,包括 2 台 8400T、2 台 6100T 和 4 台 4400T。
3.1.6 泉峰汽车:国内优质铝压铸供应商,全面布局一体化压铸
国内优质铝压铸供应商,注重全球化布局。公司成立于 2012 年,总部位于江苏南京,主要 从事汽车关键零部件的研发、生产、销售,以及部分洗衣机零部件产品,2019 年于上交所挂 牌上市。公司注重全球化布局,2017 年在辽宁大连设有研发中心和生产基地,分别在 2020 年、2021 年于安徽马鞍山和天津设立分公司,2022 年匈牙利工厂主体工程基本完成,公司 预计 2023 上半年开始逐步投产。
“新能源+传动”双核心业务。公司产品种类众多,重点专注于技术含量较高的汽车热交 换系统、汽车传动系统、汽车引擎系统、刹车与转向系统零部件以及新能源汽车零部件的 研发与制造。2021 年,公司核心业务新能源汽车零部件业务和传动零部件业务依然保持 快速增长,新能源汽车零部件及汽车传动零部件销售分别实现营收 5.65 亿元、3.24 亿元, 同比增长分别达到 43.25%、36.09%。
受疫情影响业绩短期承压。2022 年 H1 公司实现营业收入 7.42 亿元,同比-7.86%;实现归 属于上市公司股东的净利润-0.21 亿元,同比-126.76%。原因在于:(1)3 月中下旬以来吉 林、上海等地区新冠疫情的多点爆发,对公司的生产造成比较严重的冲击;(2)为推动诸多 新项目的如期量产、在新能源汽车零部件业务上抢占先机,研发投入持续增加、产能进一步 扩张,研发费用与固定成本大幅增长;(3)受到芯片短缺、动力电池原材料价格上涨等影响。
全面布局一体化压铸。1)设备:公司目前规划的主要大型压铸机都放在安徽马鞍山生产基 地,其将成为公司压铸一体化的生产中心。截至 2022 上半年,一台 4400T 的压铸机已经投 入使用,另有 4000T、4200T 正在调试安装;原本的 6100T 和 8000T 压铸机受疫情影响,到厂时间预计推迟到 2022 年年底。2)模具:公司正在进行 5000-8000T 压铸机用模具的设计 和研发。3)材料:公司在免热处理压铸材料应用上也取得了一定的进展,相关的技术已经 成功应用在一体化托盘的生产上。
3.2 产业链上下游迎来发展机遇,享受行业高速增长红利
3.2.1 力劲科技:全球最大的压铸机制造商
2022 财年公司收入规模提升,压铸机业务是主要收入来源。公司成立于 1979 年,公司总部 位于中国香港,2006 年在香港成功上市,主营业务为设计、制造及销售压铸机、注塑机和数 控加工中心(CNC)。2022 财年(截至 2022 年 3 月 31 日止 12 个月)实现营业收入 53.63 亿 港元,同比+33.4%,其中压铸机业务实现的营收连续 5 年占比 50%以上,是公司主要收入来 源;实现净利润 5.07 亿元,同比+82%。
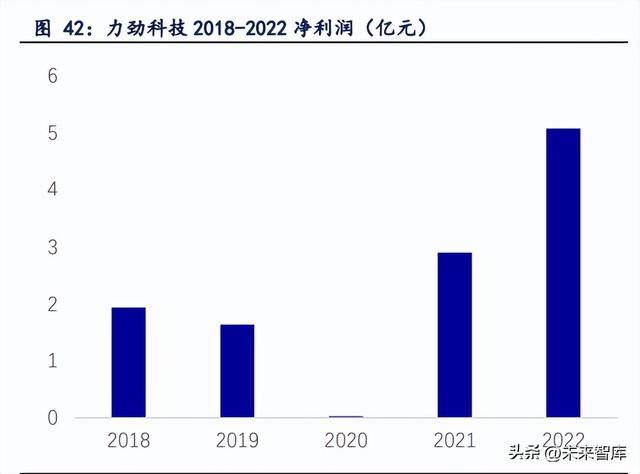
联合多家企业共同推动一体化压铸发展。2022 年 9 月,公司举办“12000T 超大型智能压铸 单元发布仪式”,正式发布全球首台最大吨位 12000T 超级智能压铸单元,该压铸单元由力 劲与广东鸿图联合研发,目前已完成样件试产,有望领导全球迈向大型汽车结构件“一体化 压铸”态势,助推国家铸造高质量发展。2022 年 5 月,文灿集团向力劲集团继续采购 9 台 压铸机(包括 7000T 2 台、4500T 2 台、3500T 3 台、2800T 2 台),继续深化双方战略合作 关系。
3.2.2 伊之密:模压成型设备行业领军企业
国内领先的注塑机与压铸机厂商。2002 年公司成立,总部在中国广东,2015 年于深交所创 业板上市,专注模压成型装备制造领域,是一家集设计、研发、生产、销售及服务为一体的 装备供应商,主要产品有注塑机、压铸机、橡胶注射机及相关配套产品等。2022 年 H1 公司 实现营业总收入 19.20 亿元,同比+13.04%,其中注塑机和压铸机产品营收分别为 14.39 亿 元、2.91 亿元;归母净利润为 2.4 亿元,同比-9.10%。
超重型压铸机厂房建设即将完工,与客户合作顺利推进。2022 年 5 月,公司超重型压铸机 厂房动工,公司预计今年 10 月竣工,厂房建成后,公司预计可满足 2 万吨超大型压铸机交 付,具备年生产重型和超大型压铸机 60-80 台的能力,远期规划年产能可达 100 台。截至 2022 上半年,公司已完成 6000 吨、7000 吨、8000 吨及 9000 吨超大型压铸机研发,9000 吨 超大型压铸机已与一汽完成签约,并已完成设备的总装,正在进行厂内测试,公司预计在 2022 下半年可交付客户使用;7000 吨压铸机已中标中国长安车身一体化压铸项目。
3.2.3 立中集团:全球领先的再生铝合金、汽车轻量化产品和新材料制造商
全球领先的再生铝合金、汽车轻量化产品和新材料制造商。公司成立于 1984 年,总部位于 河北保定,2015 年在深交所创业板挂牌上市,是专业从事铝合金及铝合金高端应用的国际 化企业集团,公司主要产品包括再生铸造铝合金,免热处理合金、铝合金车轮和转向节,新 能源汽车电机壳,功能中间合金新材料,精密模具,自动熔炼装备和锂钠电池新材料等,2022 年 H1 公司实现营业收入 100.52 亿元,同比+16.00%;归母净利润 2.77 亿元,同比+0.54%。
持续推进免热处理合金材料的市场推广。公司从 2016 年开始立项免热处理合金项目的研发, 于 2020 年申请并相继获得了国家发明专利证书,打破了国外在该领域的产品垄断和技术封 锁,并逐步实现了该材料的市场化应用和推广;2022 年 5 月,公司与文灿集团签署了《战略合作框架协议》,在新能源汽车的大型一体化车身结构件、一体化铸造电池盒箱体等产品 的材料开发和工艺应用领域建立了战略合作关系。
3.2.4 合力科技:国内领先的大型高端精密模具及零部件供应商
国内领先的大型高端精密模具及零部件供应商。公司成立于 2000 年,总部位于浙江宁波, 公司主要从事汽车用铸造模具、压铸模具、热冲压模具、铝合金部品和汽车制动系统的研发、 设计、制造和销售。公司主要产品为汽车用发动机模具、变速箱壳体模具、新能源汽车电池 盒模具、电机模具等大型精密模具,2017 年于上交所上市。2022H1 公司实现营业收入 3.12 亿元,同比-11.14%;归母净利润 0.28 亿元,同比-23.9%。
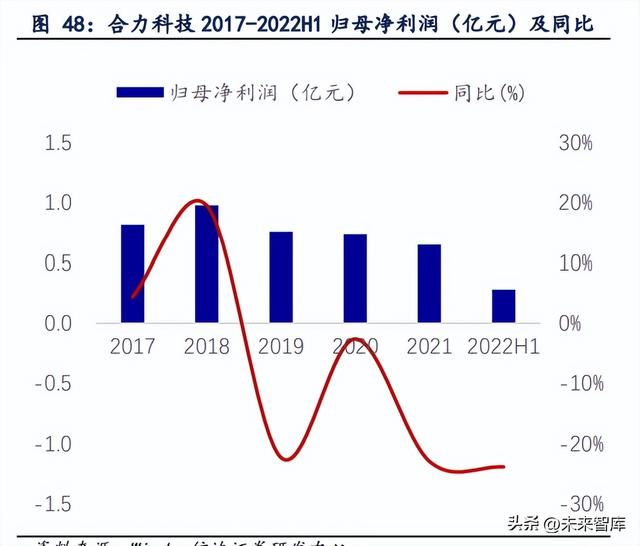
募集资金推进大型一体化压铸模具项目建设。2022 年合力科技拟通过非公开发行股票方式 募集不超过 8.05 亿元的资金,用于大型一体化模具及精密铝合金部品智能制造项目以及补 充流动资金。公司本次大型一体化模具及精密铝合金部品智能制造项目将在浙江省象山县滨 海工业园区内购置的土地上新建厂房,并对部分已有厂房进行升级改造,打造业内领先的智 能化生产基地,项目达产后将新增 75 套中大型一体化模具的产能。
(本文仅供参考,不代表我们的任何投资建议。如需使用相关信息,请参阅报告原文。)
精选报告来源:【未来智库】。系统发生错误
相关参考
海天注塑机怎么调润滑时间(汽车行业一体压铸深度研究报告:新趋势,汽车制造大变革)
(报告出品方/作者:信达证券,陆嘉敏、曹子杰)一、汽车轻量化大势所趋,铝合金材料优势突出1.1政策直接推动+电动化要求,汽车轻量化大势所趋1.1.1政策要求推动汽车轻量化政策直接推动汽车轻量化发展,纯电动车减重需...
海天注塑机怎么调润滑时间(汽车行业一体压铸深度研究报告:新趋势,汽车制造大变革)
(报告出品方/作者:信达证券,陆嘉敏、曹子杰)一、汽车轻量化大势所趋,铝合金材料优势突出1.1政策直接推动+电动化要求,汽车轻量化大势所趋1.1.1政策要求推动汽车轻量化政策直接推动汽车轻量化发展,纯电动车减重需...
热室压铸机(力劲科技研究报告:一体化压铸放量,超大型压铸机龙头启航)
...学清)1.力劲科技:全球超大型压铸机龙头力劲科技集团有限公司于1979年成立,于2006年在香港联交所主板成功上市,是全球最大的压铸机制造商之一。公司总部位于中国香港,并在深圳、中山、宁波、上海、阜新等地设立十余...
热室压铸机(力劲科技研究报告:一体化压铸放量,超大型压铸机龙头启航)
...学清)1.力劲科技:全球超大型压铸机龙头力劲科技集团有限公司于1979年成立,于2006年在香港联交所主板成功上市,是全球最大的压铸机制造商之一。公司总部位于中国香港,并在深圳、中山、宁波、上海、阜新等地设立十余...
悬挂式冷铆机厂(汽车一体压铸行业深度报告:汽车制造革新,一体压铸蓄势待发)
...作者:中银证券,朱朋)轻量降本提效凸显,特斯拉引领一体压铸风潮一体压铸推动汽车制造工艺革新传统汽车制造包括冲压、焊装、涂装、总装四大工艺。冲压是运用中小型压力机和模具,将板材等原材料加工为所需形状和尺...
成都模具零部件(成都博俊汽车零部件 模具基地产品定位为高压铸铝和一体化压铸产品)
近日,江苏博俊工业科技股份有限公司(以下简称“博俊科技”)在投资者互动平台表示,成都博俊科技有限公司(以下简称:“成都博俊”)产品定位为高压铸铝和一体化压铸产品,厂房正在建设收尾中,目前部分设备已与供应商...
挡泥板模具生产(汽车行业一体化压铸研究报告:应时而生,方兴未已)
...渗透率不断提高轻量化是一种有效的节能减排技术。全球汽车行业的节能减排政策逐渐趋严,油耗、排放标准不断提高。轻量化技术作为一种重要的汽车节能减排途径,在满足汽车安全性和成本控制的条件下实现汽车减重。同时...
1.1模具为“工业之母”,制造业带动行业稳健增长模具为强迫金属或非金属成型的工具,是工业生产中必不可少的工艺装备。模具生产得到的零部件具有高效率、高一致性、低耗能耗材、精度/复杂度较高的特点。模具行业为技...
注塑机主板线路图(天风研究:国内一体化压铸市场空间到2025年预计将达300亿以上规模,关注两条主线)
【核心观点】一体化压铸是什么?压铸技术是一种特种铸造技术,目前压铸铝合金制品在汽车用铝中约占54%~70%。一体化压铸技术是压铸技术的新变革,通过将原本设计中需要组装的多个独立的零件经重新设计,并使用超大...
注塑机主板线路图(天风研究:国内一体化压铸市场空间到2025年预计将达300亿以上规模,关注两条主线)
【核心观点】一体化压铸是什么?压铸技术是一种特种铸造技术,目前压铸铝合金制品在汽车用铝中约占54%~70%。一体化压铸技术是压铸技术的新变革,通过将原本设计中需要组装的多个独立的零件经重新设计,并使用超大...